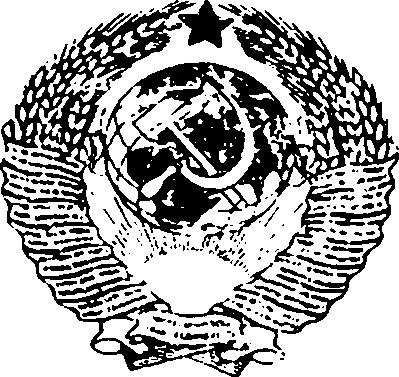
ГОСУДАРСТВЕННЫЙ СТАНДАРТ СОЮЗА ССР
ОПРАВЫ КОРРИГИРУЮЩИХ очков
ОБЩИЕ ТЕХНИЧЕСКИЕ ТРЕБОВАНИЯ И МЕТОДЫ ИСПЫТАНИИ
ГОСТ 18491 — 90
(СТ СЭВ 4780-84)
Издание официальное
15 коп. БЗ 3-90/195
Е
ГОСУДАРСТВЕННЫЙ КОМИТЕТ СССР ПО УПРАВЛЕНИЮ КАЧЕСТВОМ ПРОДУКЦИИ И СТАНДАРТАМ Москва
УДК 681.7.072.42:006.354
Группа П46
ГОСУДАРСТВЕННЫЙ
СТАНДАРТ
СОЮЗА «■интян
ССР
ОПРАВЫ КОРРИГИРУЮЩИХ ОЧКОВ
ГОСТ
18491—90
(СТ СЭВ 4780—84)
Общие технические требования и методы испытаний
Spectacle frames for corrective eye glasses. General technical requirements and test methods
ОКП 94 4260
Дата введения 01.07.91
Настоящий стандарт распространяется на оправы корригирующих очков (далее — оправы).
Оправы предназначены для внутреннего рынка и для экспорта в страны с умеренным и тропическим климатом.
Оправы изготовляют в климатическом исполнении B1.I по ГОСТ 15150.
Стандарт не распространяется на лорнеты, пенсне и безобод-ковые оправы.
Номенклатура и применяемость показателей качества приведены в приложении 1.
Термины и определения, применяемые в настоящем стандарте» и их пояснения приведены в приложении 2.
Основные принципы проектирования оправ приведены в приложении 3.
Соответствие требований ГОСТ 18491 требованиям СТ СЭВ 4780 приведено в приложении 4.
1. ТИПЫ И ОСНОВНЫЕ РАЗМЕРЫ
1.1. Оправы подразделяют на типы, указанные в табл. 1.
Таблица J
Обозначение тмиа оправы | Наименование типа | Вил и обозначение заушника |
оп | Оправа корригирующих очков пластмассовая | Жесткие Ж |
ом | Оправа корригирующих очков металлическая | Жесткие Ж; эластичные Э |
ок | Оправа корригирующих очков комбинированная | То же |
Издание официальное Перепечатка воспрещена
★ Е
© Издательство стандартов, 1990
1.2. Размеры оправ должны соответствовать указанным на черт. 1, 2 и в табл. 2.
Черт. 1
Примечание. Черт. 1—7 не определяют конструкцию оправы, а служат только для пояснения основных размеров.
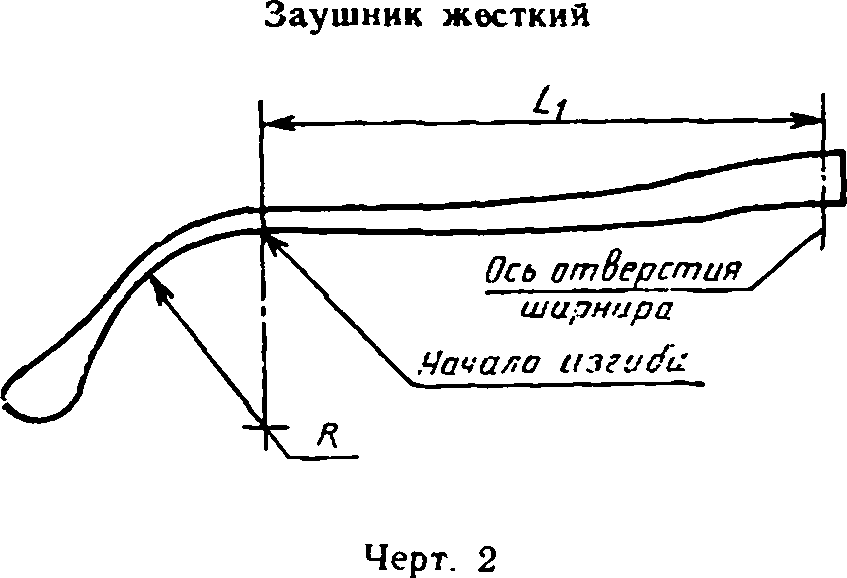
Таблица 2
Размер | Диапазон номинальных значений | Шаг |
а | От 34 до 60 | 1 |
Ь | » 10 > 28 | 1 |
L, | > 55 > 115 | 5 |
1.3. Условное обозначение оправы должно содержать:
слово «Оправа»;
обозначение типа оправы;
расстояние а между вертикальными касательными к фацетной канавке ободка;
минимальное расстояние b между вертикальными касательными к фацетным канавкам ободков (указывается через дефис);
вид заушника;
размер Li заушника (указывается через дефис);
наименование или шифр модели оправы (указывается через дефис);
обозначение технических условий.
Пример условного обозначения пластмассовой оправы с размерами а = 50 мм, &=16 мм, жесткими заушниками с размером Li = 90 мм, шифр модели 2.189:
Оправа ОП50-16 Ж-90 2.189 ТУ 25—1910001—87
2. ТЕХНИЧЕСКИЕ ТРЕБОВАНИЯ
2.1. Оправы должны изготовляться в соответствии с требованиями настоящего стандарта, по ГОСТ 23256 для класса Г, по рабочим чертежам и техническим условиям, утвержденным в установленном порядке.
2.2. Углы у, у! и глубины S, Si фацетных канавок (черт. 3) для пластмассовых и металлических ободков должны быть равны соответственно:
у — от 80 до 110°; S — от 0,5 до 1,2 мм;
Yi — от 90 до 110°; S( —от 0,3 до 1,0 мм.
2.3. Заушники, установленные под углом менее 90° к горизонтально расположенной рамке, не должны опускаться под действием собственного веса.
2.4. Заушники должны поворачиваться на оси шарниров плавно, без заеданий.
2.5. На поверхности оправы, кроме фацетных канавок, не должно быть острых кромок и заусенцев.
2.6. На наружной поверхности оправ и поверхностей, сопряженных с ней, кроме фацетных канавок и мест сопряжения рамок с заушниками, не должно быть видимых невооруженным глазом раковин, царапин, наплывов припоя и других дефектов, ухудшающих их внешний вид. На поверхности металлической оправы, изготовленной из проволоки по ГОСТ 5220, допускается незначительное наличие точек диаметром не более 0,3 мм и раковин размером не более 0,3 мм в количестве не более 5 шт., на внутренней поверхности волосовин длиной не более 10 мм в количестве не более 2 шт.
2.7. В пластмассовых деталях и склеенных соединениях оправ не должно быть более 3 пузырей на 1 см2 диаметром от 0,15 до 0,25 мм на каждой детали.
Допускается наличие посторонних включений размером до 0,5 мм в количестве 1 шт. на оправу.
В пластмассовых рамках, получаемых методом литья под давлением, допускается наличие следов спаев потоков расплава полимерного материала в виде волосовин с внутренней стороны рамки.
2.8. Соединения деталей оправ должны быть прочными и выдерживать следующие усилия:
неразъемные соединения—(50±5) Н ((5±0,5) кгс); наконечники заушников с металлической частью, опоры для носа—(20±2) Н ((2±0,2) кгс).
2.9. Для изготовления оправ должны применяться материалы, разрешенные к применению Министерством здравоохранения СССР.
Примечание. Коэффициент светопропускания бесцветного прозрачного литьевого материала и число расцветок окрашенного в массе литьевого и листового этрола должны соответствовать нормативно-технической документации на них.
2.10. Металлические детали оправ из коррозионных материалов должны иметь защитно-декоративные покрытия по ГОСТ 9.301 и устанавливаться в технических условиях на оправы конкретной модели.
Допускается отсутствие защитно-декоративных покрытий на металлических деталях, облицованных пластмассой, а также на шарнирах, винтах, заклепках, изготовленных из нейзильбера.
2.11. Оправы, упакованные в транспортную тару, должны быть устойчивы к воздействию транспортной тряски с максимальным ускорением 30 м/с2 и частотой от 2 до 3 Гц.
2.12. 90%-ная наработка до отказа должна составлять не менее 15 385 качаний заушника;
средняя наработка на отказ шарнира должна составлять не менее 25 000 качаний заушника.
2.13. 90%-ный срок службы оправ должен быть не менее 1,8 года при наработке не более 15 000 качаний заушника.
Полный средний срок службы оправ должен быть не менее 3 лет при количестве качаний заушника не более 30 000.
2.14. Оправы при эксплуатации должны быть устойчивы к воздействию климатических факторов для исполнения В1.1 по ГОСТ 15150.
2.15. Виды современных методов декоративной отделки должны регламентироваться в технической документации на конкретную модель оправы.
2.16. В технических условиях на оправы конкретной модели должны быть дополнительно установлены требования к:
виду заушников;
размерам заушников;
материалу оправы;
номеру или шрифту расцветки (виду покрытия);
массе оправы;
маркировке.
3. МЕТОДЫ ИСПЫТАНИЯ
3.1. Проверку основных размеров оправы (пп. 1.2, 2.2) проводят универсальными измерительными инструментами: штангенциркулем по ГОСТ 166; угломером с нониусом по ГОСТ 5378; калибрами для метрической резьбы по ГОСТ 24997, а также специальными шаблонами и приспособлениями, обеспечивающими необходимую точность измерения.
Проверку размеров а и b (п. 1.2) проводят путем измерения светового проема и глубины фацетной канавки.
Проверку размеров фацетной канавки (п. 2.2) проводят путем контроля технологической оснастки и инструмента, обеспечивающих выполнение соответствующих размеров.
3.2. Проверку требований пп. 2.5—2.7 (кроме наличия пузырей и включений), 2.10, 2.15 проводят внешним осмотром без применения увеличительных средств.
Проверку требований пп. 2.6 и 2.10 проводят путем сличения оправы с контрольными образцами, утвержденными в установленном порядке. Проверку наличия пузырей (п. 2.7) проводят с помощью лупы с увеличением 10х по ГОСТ 25706.
3.3. Проверку удержания заушника шарниром (п. 2.3) проводят следующим образом: каждый заушник устанавливают под любым углом менее 90° к рамке, расположенной горизонтально. При этом заушник не должен опускаться под действием собственного веса.
3.4. Проверку плавности перемещения заушника (п. 2.4) проводят путем легкого встряхивания оправы. При этом заушник, установленный под любым углом менее 90° горизонтально расположенной к рамке оправы, должен повернуться на оси шарнира.
3.5. Проверку прочности соединений деталей оправ (п. 2.8) проводят испытанием на отрыв одного элемента конструкции от другого. При приложении усилий, указанных в п. 3.8, направленных с учетом эксплуатационных нагрузок, в течение 1 мин соединение не должно разрушаться.
Проверку прочности соединения наконечника заушника с металлической частью и опоры для носа, надетой на держатель, проводят приложением к концу заушника или опоры, закрепленных в зажимном приспособлении, усилия, направленного вдоль металлической части заушника или опоры, в течение 1 мин. По окончании испытания допускается смещение наконечника — не более 2 мм, опоры — не более 1 мм.
Проверку прочности соединения приклеенных опор для носа с рамкой оправы проводят приложением статической нагрузки к опорной поверхности опоры для носа в направлении, перпендикулярном к ней, в течение 1 мин. При этом соединение не должно разрушаться.
3.6. Проверку устойчивости оправ к воздействию транспортной тряски (п. 2.11) проводят на стенде имитации транспортирования, обеспечивающем перегрузки с погрешностью от минус 10 до плюс 25%.
При испытаниях оправ в транспортной упаковке их жестко крепят в центре платформы без дополнительной амортизации.
Режим испытаний:
частота — от 2 до 3 Гц;
максимальное ускорение — 30 м/с2; продолжительность—1 ч.
После испытаний оправа не должна иметь повреждений.
3.7. Проверку безотказности (п. 2.12) проводят в соответствии с ГОСТ 23256 на четырех образцах по коду В3-1 на стенде, обес-печивающе*м плавное перемещение заушника от угла 60°±5° к плоскости рамки до угла, превышающего максимальный угол раскрытия заушника (до упора) на 3°—4°, и обратно.
Усилие при качании прикладывают к заушнику на расстоянии от 35 до 90 мм от оси шарнира.
За отказ принимают несоответствие требованиям пп. 2.3 и 2.4 (отвинчивание винтов шарниров в пределах пол-оборота не является отказом). Перед испытанием шарнирные соединения допускается смазывать индустриальным маслом общего назначения И12-А по ГОСТ 20799 или другим, соответствующим ему по техническим характеристикам. По окончании испытаний следует произвести подтяжку винтов до первоначального положения.
Для оправ с однотипными шарнирами допускается проводить испытания на одной модели оправ.
3.8. Проверку долговечности (п. 2.13) проводят по методике п. 3.7 на трех образцах оправ при отсутствии предельного состояния или пяти образцах — при допустимом одном предельном состоянии. На каждом шарнирном соединении должно быть проведено не менее 30 000 качаний.
За критерий предельного состояния принимают поломку шарнирного соединения.
3,9. Проверку устойчивости оправ к воздействию климатических факторов внешней среды (п. 2.14) проводят в камерах тепла и холода, обеспечивающих поддержание температуры с погрешностью ±3СС следующим образом:
на тепло- и холодоустойчивость — выдержкой оправ в камерах тепла и холода при температурах, равных соответственно плюс 45°C и минус 60°C; время выдержки в каждой камере 1 ч с момента достижения номинального режима;
на смену температур — путем воздействия на оправы трех непрерывно следующих друг за другом циклов; в каждом цикле оправы помещают в камеру тепла, температуру которой заранее доводят до плюс 45 °C и выдерживают в течение 1 ч, затем оправы выдерживают при температуре плюс 20 СС в течение 1 ч и вновь переносят в камеру холода, температуру которой доводят до минус 60 СС и выдерживают в течение 1 ч, затем оправы выдерживают при температуре плюс 20 °C в течение 1 ч.
Допускается объединять испытания на тепло- и холодоустойчивость и на смену температур;
на влагоустойчивость — выдержкой оправ без транспортной тары в камере влажности, обеспечивающей поддержание температуры и влажности с погрешностью ±3%, относительная влажность в камере должна быть равна верхнему номинальному значению, время выдержки оправ с момента достижения номинального режима — 2 сут.
При испытаниях номинальные значения климатических факторов следует устанавливать по ГОСТ 15150.
Допускается проводить испытания очковых оправ со вставленными линзами или их имитаторами.
После каждого вида испытаний не должно быть нарушений целостности оправ и их защитно-декоративных покрытий, замеченных при осмотре без применения увеличительных средств.
С. 8 ГОСТ 13491—90
ПРИЛОЖЕНИЕ 1 Обязательное
1.1. Расстояние между вертикальными касательными к основанию фацетной канавки ободка, мм
1.2. Минимальное расстояние между вертикальными касательными к основанию фацетной канавки ободков, мм
1.3. Минимальное расстояние между горизонтальными касательными к фацетной канавке ободков, мм
1.4. Радиус изгиба рамки, мм
1.5. Размеры фацетной канавки, ? и мм
1.6. Показатель прочности соединений деталей оправ, Н (кгс)
1.7. Вид материала
а | Основные раз меры очковой оправы | + |
b | То же | + |
h | > | |
R | + | |
— | Профиль фацет | •F |
ной канавки | ||
— | + | |
+ |
И-
НОМЕНКЛАТУРА И ПРИМЕНЯЕМОСТЬ ПОКАЗАТЕЛЕЙ КАЧЕСТВА ОПРАВ КОРРИГИРУЮЩИХ ОЧКОВ
Таблица 3
Применяемость в | ||||
Наименование показателя качества | Обозначение показателя качества | Наименование характеризуемого свойства | настоящем стандарте | ТУ |
1. Основные показатели назначения
2. Показатели надежности
2.1. Средняя | наработка на | Безотказность | + | |
отказ, цикл 2.2. 90%-ная | наработка до | То же | + | |
отказа, цикл 2.3. Полный | средний срок | Дол говеч ность | + | |
службы, лет 2.4. 90%-ный | срок службы | То же | ||
лет |
3. Эргономические показатели
Продолжение табл. 3
Наименование показателя качества | Обозначение показателя качества | Наименование характеризуемого свойства | Применяемость в | |
настоящем стандарте | ТУ | |||
3.3. Плавность перемещения заушника | — | То же Положение за- | + | — |
3.4. Угол между заушниками, | — | 4- | — | |
расположенными до упора, и | ушника относи- | |||
прямой, проходящей через оси | тельно рамки в | |||
шарнира | горизонтальной поверхности | |||
3.5. Наклон опорных поверх- | —- | Расположение | 4- | — |
костей, соприкасающихся с но- | опорных поверх- | |||
сом, ....° и мм | ностей | |||
3.6. Угол, определяющий по- | — | Положение зауш- | 4* | — |
ложение заушника относитель- | ника относитель- | |||
но рамки | но рамки | |||
3.7. Масса оправы, г | —- | — | ||
4. Эстетические показатели | ||||
4.1. Качество поверхности | — | — | 4- | — |
оправы | ||||
4.1.1. Наличие на поверхно- | — | — | — | |
сти оправ острых кромок, заусенцев, царапин, точек, ухудшающих внешний вид. Наличие в пластмассовых деталях пузырей | ||||
4.1.2. Качество защитно-де- | — | — | 4- | |
коративных покрытий 4.1.3. Наличие современных методов декоративной отделки поверхности | — | — | + |
5. Показатели устойчивости к внешним воздействиям
5.1. Устойчивость к климати | — | 4- | — | |
ческим воздействиям при эксплуатации 5.2. Устойчивость к воздей | 4- | |||
ствию транспортной тряски |
Примечания;
1. В табл. 3 знак <4-> означает применяемость; знак «—> — неприменяе-мость; знак «±> — ограниченное применение соответствующих показателей качества продукции.
2. В зависимости от назначения условий применения и конструктивных особенностей конкретных оправ допускается дополнительно использовать показатели, не указанные в табл. 3.
ПРИЛОЖЕНИЕ 2
Справочное
ТЕРМИНЫ И ИХ ПОЯСНЕНИЯ, ПРИМЕНЯЕМЫЕ В СТАНДАРТЕ
Таблица 4
Термин | Поясвение |
Оправа | Устройство для фиксации линз в заданном |
Рамка | положении Часть оправы, обеспечивающая монтаж и фик- |
Ободок | сацию линз в заданном положении Часть рамки, содержащая фацетную канав- |
Опорная поверхность для | ку для монтажа линзы Часть оправы, соприкасающаяся с носом |
носа | |
Канавка фацетная | Канавка V-образного профиля |
Световой проем | Пространство, ограниченное ободком |
Заушник | Часть оправы, обеспечивающая заданное по- |
Заушник жесткий | ложение очков Заушник, жесткий по всей длине |
Заушник эластичный | Заушник, заканчивающийся упругой частью |
Стержень армирующий | Металлический сердечник пластмассового зауш- |
Шарнир | ника Часть оправы, соединяющая рамку и заушник, |
Размер а | и обеспечивающая его перемещение относительно рамки Расстояние между вертикальными касательны- |
Размер b | ми к основанию фацетной канавки ободка Минимальное расстояние между вертйкальными |
Размер | касательными к основаниям фацетных канавок ободков Длина заушника от оси шарнира до начала |
Внутренняя поверхность | изгиба Поверхность, обращенная к лицу |
оправы | Линия, перпендикулярная к плоскости ободка |
Прямая OOi | |
Наконечник заушника | и проходящая через центр пересечения горизонтальной и вертикальной осей ободка Пластмассовая деталь, одеваемая на металли- |
ческий заушник, с целью обеспечения удобства при пользовании оправой |
ПРИЛОЖЕНИЕ 3 Справочное
ОСНОВНЫЕ ПРИНЦИПЫ ПРОЕКТИРОВАНИЯ ОЧКОВЫХ ОПРАВ
1. Рамки оправ должны быть изогнуты в соответствии с черт. 4. При этом OR выбирается из диапазона 90—160 мм, /?1 —из диапазона 200—400 мм; предельные отклонения — ±10% номинального значения.
Черт. 4
Допускается в пластмассовых рамках изгибать каждый световой проем или (и) всю рамку по радиусу цилиндра.
При этом значение угла а между заушниками, раскрытыми до упора, и прямой, проходящей через оси шарниров, выбирается из диапазона 85°—100°.
Рамки пластмассовых оправ толщиной не более 5,5 мм в сечении А—А допускается не изгибать. При этом значение угла а выбирается из диапазона 85е—110°.
Рамки оправ, световой проем которых имеет форму круга, изгибу не подлежат. При этом угол а должен быть 9У—95°.
2. Основные размеры для построения поверхностей, соприкасающихся с носом, выбираются в соответствии с антропологическими данными, указанными на черт. 5: ф— от 15° до 40°, 9 — от 20°’до ЗУ, I — не менее 3 мм, Д=/+5 мм, b — от 10 до 28 мм.
3. Размеры, определяющие положение заушника относительно рамки оправы, указаны на черт. 6.
4. Жесткие заушники рекомендуется изгибать в соответствии с черт. 7. Значение размеров выбирается из диапазонов:
— от 160 до 450 мм;
R2— от 20 до 30 мм;
т— от 20 до 30 мм;
п — от 5 до 10 мм.
3.1. Длина заушника
32. Удержание шарнирным соединением от опускания заушника, установленного под любым углом менее 90° к горизонтально расположенной рамке под действием собственного веса
__ | + |
Качество креп | + |
ления заушника | |
к рамке |
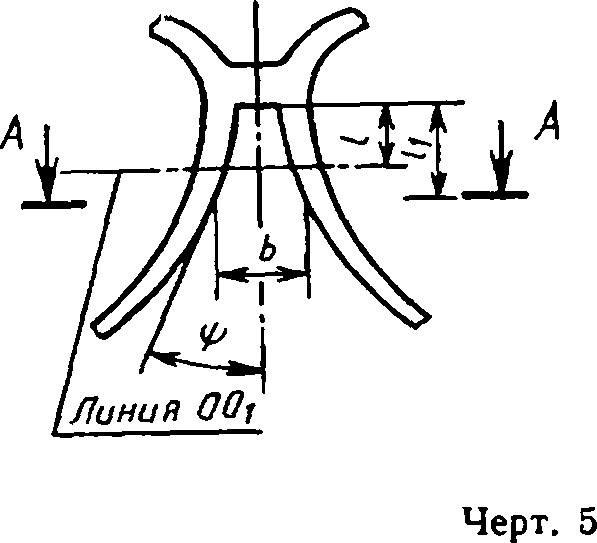
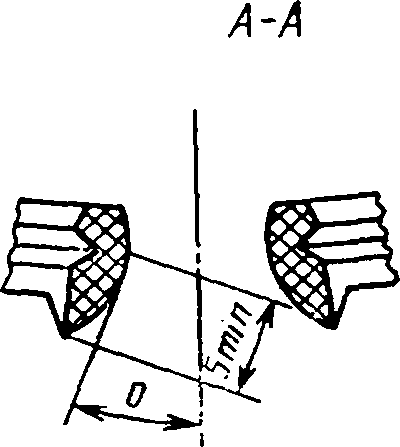
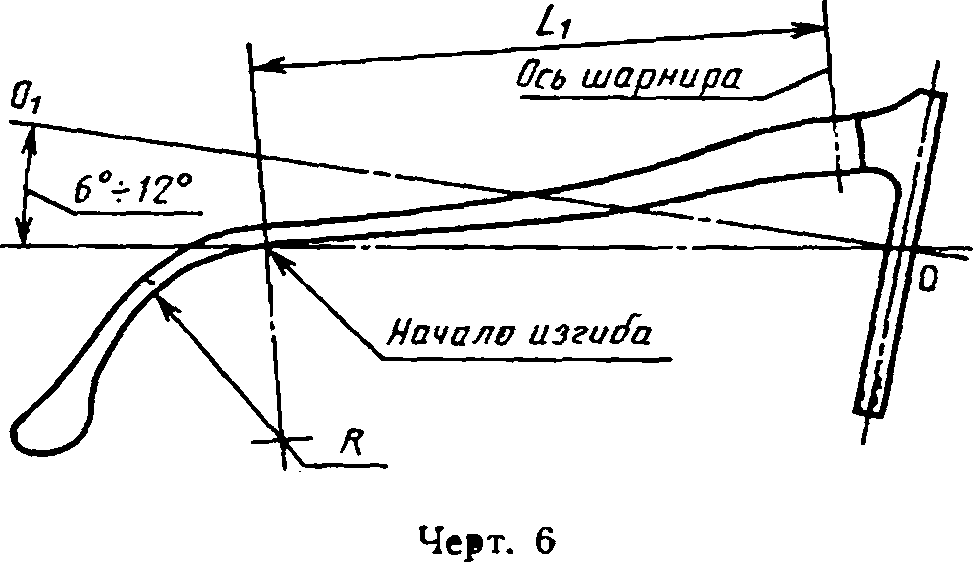

Черт. 7
ПРИЛОЖЕНИЕ 4
Справочное
СООТВЕТСТВИЕ ТРЕБОВАНИЙ ГОСТ 18491—90 ТРЕБОВАНИЯМ СТ СЭВ 4780—84
Таблица 5
Номер «ункта ГОСТ 18491—90
Номер пункта, раздела
СТ СЭВ 4780—84
1.2
2.2
2.3
2.4
2.5
2.6
2.7
2.8
2.9
2.10
2-11
2.12
3.1
3.3
3.4
3.2
3.5
3.2
3.6
3.7
Разд. 1
2.2
2.6
2.13
2.10
2.10
2.11
2.14
2.17
2.12
2.15
2.16
.3.1
3.2
3.5
3.4
3.6
3.4
3.7
3.3
ИНФОРМАЦИОННЫЕ ДАННЫЕ
1. РАЗРАБОТЧИКИ
Э. А. Атласов (руководитель разработки), В. Т. Воронов, Л. М. Бабчиницер, В. И. Терновская
2. УТВЕРЖДЕН И ВВЕДЕН В ДЕЙСТВИЕ Постановлением Государственного комитета СССР по управлению качеством продукции и стандартам от 30.03.90 № 694
3. Срок первой проверки — 1996 г. Периодичность проверки — 5 лет
4. Стандарт полностью соответствует СТ СЭВ 4780—84
5. ВЗАМЕН ГОСТ 18491—79, ГОСТ 4.308—85
6. ССЫЛОЧНЫЕ НОРМАТИВНО-ТЕХНИЧЕСКИЕ ДОКУМЕНТЫ
Обозначение НТД, на который дана ссылка
Номер пункта
ГОСТ 9.301—86
2.10
ГОСТ 166—80
3.1
ГОСТ 5220—78
2.6
ГОСТ 5378—88
3.1
ГОСТ 15150—69
Вводная часть,
2.14
ГОСТ 20799—88
3.7
ГОСТ 23256—86
2.1, 3.7
ГОСТ 24997—81
3.1
ГОСТ 25706—83
3.2
Редактор Л. Д. Курочкина Технический редактор В. Н. Малькова Корректор В. С. Черная
Сдано в наб. 18.04-90 Подп. к печ. 16.07.90 1,0 усл. п. л. 1,0 усл. кр.-огг. 0,83 уч.-изд. л. Тираж 4000 экз. Цена 15 к.
Ордена «Знак Почета» Издательство стандартов, 123557, Москва, ГСП, Новопресяенский пер.» 3
Тип. «Московский печатник». Москва, Лялин пер., 6. Зак. 1815