ФЕДЕРАЛЬНОЕ АГЕНТСТВО
ПО ТЕХНИЧЕСКОМУ РЕГУЛИРОВАНИЮ И МЕТРОЛОГИИ
ГОСТР 54571— 2023
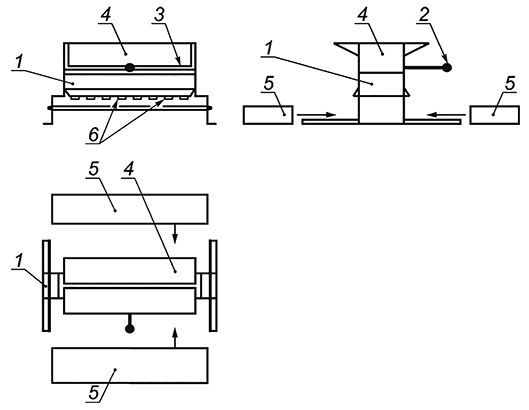
НАЦИОНАЛЬНЫЙ СТАНДАРТ РОССИЙСКОЙ ФЕДЕРАЦИИ
ПРОПАНТЫ МАГНЕЗИАЛЬНО-КВАРЦЕВЫЕ
Технические условия
(ISO 13503-2:2006+Amd.1:2009, NEQ)
Издание официальное
Москва Российский институт стандартизации 2023
Предисловие
1 РАЗРАБОТАН Обществом с ограниченной ответственностью «Научно-технический центр «Огнеупоры» (ООО НТЦ «Огнеупоры»)
2 ВНЕСЕН Техническим комитетом по стандартизации ТК 009 «Огнеупоры»
3 УТВЕРЖДЕН И ВВЕДЕН В ДЕЙСТВИЕ Приказом Федерального агентства по техническому регулированию и метрологии от 13 июля 2023 г. № 513-ст
4 Настоящий стандарт разработан с учетом основных нормативных положений международного стандарта ИСО 13503-2:2006 «Промышленность нефтяная и газовая. Растворы и материалы для вскрытия продуктивного пласта. Часть 2. Измерения свойств расклинивающих наполнителей, используемых для гидравлического разрыва пласта и заполнения скважинного фильтра гравием» (ISO 13503-2:2006 «Petroleum and natural gas industries — Completion fluids and materials — Part 2: Measurement of properties of proppants used in hydraulic fracturing and gravel-packing operations», NEQ), включая техническую поправку Arnd.1:2009
5 ВЗАМЕН ГОСТ Р 54571—2011
Правила применения настоящего стандарта установлены в статье 26 Федерального закона от 29 июня 2015 г. № 162-ФЗ «О стандартизации в Российской Федерации». Информация об изменениях к настоящему стандарту публикуется в ежегодном (по состоянию на 1 января текущего года) информационном указателе «Национальные стандарты», а официальный текст изменений и поправок — в ежемесячном информационном указателе «Национальные стандарты». В случае пересмотра (замены) или отмены настоящего стандарта соответствующее уведомление будет опубликовано в ближайшем выпуске ежемесячного информационного указателя «Национальные стандарты». Соответствующая информация, уведомление и тексты размещаются также в информационной системе общего пользования — на официальном сайте Федерального агентства по техническому регулированию и метрологии в сети Интернет (www.rst.gov.ru)
© Оформление. ФГБУ «Институт стандартизации», 2023
Настоящий стандарт не может быть полностью или частично воспроизведен, тиражирован и распространен в качестве официального издания без разрешения Федерального агентства по техническому регулированию и метрологии
Содержание
1 Область применения
2 Нормативные ссылки
3 Термины и определения
4 Классификация
5 Технические требования
6 Требования безопасности и охраны окружающей среды
7 Правила приемки
8 Методы испытаний
9 Требования к погрешности измерений
10 Транспортирование и хранение
Приложение А (справочное) Основные требования, предъявляемые к ситам для испытаний
Приложение Б (справочное) Соответствие номеров сит настоящего стандарта обозначениям сит по ГОСТ Р 51568
Библиография
НАЦИОНАЛЬНЫЙ СТАНДАРТ РОССИЙСКОЙ ФЕДЕРАЦИИ
ПРОПАНТЫ МАГНЕЗИАЛЬНО-КВАРЦЕВЫЕ
Технические условия
Magnesial-quarts proppants.
Specifications
Дата введения — 2024—01—01
1 Область применения
Настоящий стандарт распространяется на магнезиально-кварцевые пропанты и магнезиальнокварцевые пропанты с полимерным покрытием (далее — пропанты), предназначенные для использования при добыче нефти методом гидравлического разрыва пласта и заполнения скважинного фильтра гравием.
2 Нормативные ссылки
В настоящем стандарте использованы нормативные ссылки на следующие стандарты:
ГОСТ 12.1.005 Система стандартов безопасности труда. Общие санитарно-гигиенические требования к воздуху рабочей зоны
ГОСТ 12.1.007 Система стандартов безопасности труда. Вредные вещества. Классификация и общие требования безопасности
ГОСТ 12.3.009 Система стандартов безопасности труда. Работы погрузочно-разгрузочные. Общие требования безопасности
ГОСТ 12.4.028 Система стандартов безопасности труда. Респираторы ШБ-1 «Лепесток». Технические условия
ГОСТ 12.4.041 Система стандартов безопасности труда. Средства индивидуальной защиты органов дыхания фильтрующие. Общие технические требования
ГОСТ 12.4.253 (EN 166:2002) Система стандартов безопасности труда. Средства индивидуальной защиты глаз и лица. Общие технические требования
ГОСТ 17.0.0.01 Система стандартов в области охраны природы и улучшения использования природных ресурсов. Основные положения
ГОСТ 1381 Уротропин технический. Технические условия
ГОСТ 1770 (ИСО 1042—83, ИСО 4788—80) Посуда мерная лабораторная стеклянная. Цилиндры, мензурки, колбы, пробирки. Общие технические условия
ГОСТ 2211 Огнеупоры и огнеупорное сырье. Методы определения истинной плотности
ГОСТ 2642.0 Огнеупоры и огнеупорное сырье. Общие требования к методам анализа
ГОСТ 2642.3 Огнеупоры и огнеупорное сырье. Методы определения оксида кремния (IV)
ГОСТ 2642.8 Огнеупоры и огнеупорное сырье. Методы определения оксида магния
ГОСТ 3118 Реактивы. Кислота соляная. Технические условия
ГОСТ 3134 Уайт-спирит. Технические условия
ГОСТ 5841 Реактивы. Гидразин сернокислый
ГОСТ 9546 Реактивы. Аммоний фтористый кислый. Технические условия
ГОСТ 10227 Топлива для реактивных двигателей. Технические условия
Издание официальное
ГОСТ 22524 Пикнометры стеклянные. Технические условия
ГОСТ 24717 Огнеупоры и огнеупорное сырье. Маркировка, упаковка, транспортирование и хранение
ГОСТ 25336 Посуда и оборудование лабораторные стеклянные. Типы, основные параметры и размеры
ГОСТ 29169 (ИСО 648—77) Посуда лабораторная стеклянная. Пипетки с одной отметкой
ГОСТ 30108 Материалы и изделия строительные. Определение удельной эффективной активности естественных радионуклидов
ГОСТ Р 51568 (ИСО 3310-1—90) Сита лабораторные из металлической проволочной сетки. Технические условия
ГОСТ Р 52667 Огнеупоры неформованные. Правила приемки и методы отбора проб
ГОСТ Р 52918 Огнеупоры. Термины и определения
ГОСТ Р 53228 Весы неавтоматического действия. Часть 1. Метрологические и технические требования. Испытания
ГОСТ Р 58144 Вода дистиллированная. Технические условия
ГОСТ Р 58577 Правила установления нормативов допустимых выбросов загрязняющих веществ проектируемыми и действующими хозяйствующими субъектами и методы определения этих нормативов
ГОСТ Р ИСО 3534-1 Статистические методы. Словарь и условные обозначения. Часть 1. Общие статистические термины и термины, используемые в теории вероятностей
ГОСТ Р ИСО 5725-1 Точность (правильность и прецизионность) методов и результатов измерений. Часть 1. Основные положения и определения
Примечание — При пользовании настоящим стандартом целесообразно проверить действие ссылочных стандартов в информационной системе общего пользования — на официальном сайте Федерального агентства по техническому регулированию и метрологии в сети Интернет или по ежегодному информационному указателю «Национальные стандарты», который опубликован по состоянию на 1 января текущего года, и по выпускам ежемесячного информационного указателя «Национальные стандарты» за текущий год. Если заменен ссылочный стандарт, на который дана недатированная ссылка, то рекомендуется использовать действующую версию этого стандарта с учетом всех внесенных в данную версию изменений. Если заменен ссылочный стандарт, на который дана датированная ссылка, то рекомендуется использовать версию этого стандарта с указанным выше годом утверждения (принятия). Если после утверждения настоящего стандарта в ссылочный стандарт, на который дана датированная ссылка, внесено изменение, затрагивающее положение, на которое дана ссылка, то это положение рекомендуется применять без учета данного изменения. Если ссылочный стандарт отменен без замены, то положение, в котором дана ссылка на него, рекомендуется применять в части, не затрагивающей эту ссылку.
3 Термины и определения
В настоящем стандарте применены термины по ГОСТ Р 52918, ГОСТ Р ИСО 3534-1, а также следующие термины с соответствующими определениями:
3.1 магнезиально-кварцевые пропанты: Пропанты, изготовленные на основе силикатов магния и кварцевого песка.
3.2 фракция пропантов: Совокупность гранул пропантов определенного размера.
3.3 основная фракция пропантов: Совокупность гранул пропантов, большая часть которых, проходя через сито, номер которого указан в числителе обозначения фракции, задерживается на сите, номер которого указан в знаменателе.
3.4 насыпная плотность пропантов: Отношение массы свободно насыпанных пропантов к занимаемому ими объему, выраженное в граммах на кубический сантиметр.
3.5 кажущаяся плотность пропантов: Отношение массы сухих пропантов к их общему объему, выраженное в граммах на кубический сантиметр.
3.6 общий объем пропантов: Объем гранул пропантов с учетом открытых и закрытых пор, выраженный в кубических сантиметрах.
3.7 абсолютная [истинная] плотность пропантов: Отношение массы пропантов к объему твердой фазы пропанта за вычетом открытых и закрытых пор, выраженное в граммах на кубический сантиметр.
3.8 открытые поры в пропанте: Поры в пропанте, насыщаемые жидкостью при проведении испытания.
3.9 истинный объем пропантов: Объем гранул пропантов без учета открытых пор и пустот между гранулами, выраженный в кубических сантиметрах.
3.10 сопротивление раздавливанию пропантов: Массовая доля гранул пропантов, разрушенных под воздействием заданной сжимающей нагрузки, выраженная в процентах.
3.11 округлость гранулы пропантов: Степень относительной сглаженности углов при вершинах и ребер гранул пропантов, выраженная в условных единицах.
3.12 сферичность гранулы пропантов: Степень приближения формы гранулы пропантов к форме сферы, выраженная в условных единицах.
3.13 мутность: Интенсивность рассеяния света на взвешенных частицах в единице объема водной суспензии пропантов, выраженная в нефелометрических единицах мутности (NTU).
3.14 относительное изменение массы пропантов при прокаливании: Относительное изменение массы пропантов с полимерным покрытием после нагрева и выдержки их при заданной температуре до достижения постоянной массы, выраженное в процентах.
3.15 прокаливание: Термическая обработка с целью окисления или разложения органических, гидратных и карбонатных компонентов огнеупорного сырья, а также предотвращения чрезмерных изменений объема или возникновения дефектов.
3.16 растворимость пропантов в кислых средах [кислоте, смеси кислот]: Относительное изменение массы пропантов после обработки растворами, содержащими кислоту (смесь кислот), выраженное в процентах.
3.17 комнатная температура: Температура окружающей среды, при которой проводят испытания, равная (22 ± 3)°C.
4 Классификация
Пропанты в зависимости от размера гранул основной фракции подразделяют на фракции, приведенные в таблице 1.
Таблица 1 — Обозначение фракций пропантов
Обозначение фракции | Характеристика | |||
10/14 | Гранулы проходят через сито номер 10 и задерживаются | на | сите | номер 14 |
12/18 | Гранулы проходят через сито номер 12 и задерживаются | на | сите | номер 18 |
16/20 | Гранулы проходят через сито номер 16 и задерживаются | на | сите | номер 20 |
16/30 | Гранулы проходят через сито номер 16 и задерживаются | на | сите | номер 30 |
20/40 | Гранулы проходят через сито номер 20 и задерживаются | на | сите | номер 40 |
30/50 | Гранулы проходят через сито номер 30 и задерживаются | на | сите | номер 50 |
40/70 | Гранулы проходят через сито номер 40 и задерживаются | на | сите | номер 70 |
Примечание — Основные требования, предъявляемые к ситам, приведены в приложении А, таблица соответствия применяемых сит требованиям ГОСТ Р 51568 — в приложении Б. |
5 Технические требования
5.1 По физико-химическим и физико-механическим показателям, гранулометрическому составу и форме пропанты должны соответствовать требованиям, приведенным в таблице 2.
Таблица 2 — Технические требования
Наименование показателя | Значение показателя для фракции | ||||||
10/14 | 12/18 | 16/20 | 16/30 | 20/40 | 30/50 | 40/70 | |
1 Массовая доля, %, не менее: МдО SiO2 | 8 50 |
Окончание таблицы 2
Наименование показателя | Значение показателя для фракции | ||||||
10/14 | 12/18 | 16/20 | 16/30 | 20/40 | 30/50 | 40/70 | |
2 Гранулометрический состав, %, не более — массовая доля гранул: оставшихся на сите номер: 6 8 12 16 20 30 прошедших через сито номер: 20 30 40 50 70 100 | 0,1 | ||||||
— | 0,1 | — | — | — | — | — | |
— | — | 0,1 | 0,1 | — | — | — | |
— | — | — | — | 0,1 | — | — | |
— | — | — | — | — | о,1 | — | |
— | — | — | — | — | — | о,1 | |
1,0 | — | — | — | — | — | — | |
— | 1,0 | — | — | — | — | — | |
— | — | 1,0 | 1,0 | — | — | — | |
— | — | — | — | 1,0 | — | — | |
— | — | — | — | — | 1,0 | — | |
— | — | — | — | — | — | 1,0 | |
3 Массовая доля гранул основной фракции, %, не менее | 90,0 | ||||||
4 Сферичность, условные единицы, не менее | 0,7 | ||||||
5 Округлость, условные единицы, не менее | 0,7 | ||||||
6 Растворимость в смеси кислот, %, не более | 10,0 | ||||||
7 Растворимость в 15 %-ной соляной кислоте, %, не более | 1,0 | ||||||
8 Мутность, NTU, не более | 250 | ||||||
9 Насыпная плотность, г/см3, не более | 1,75 | ||||||
10 Кажущаяся плотность, г/см3, не более | 3,10 | ||||||
11 Абсолютная (истинная) плотность, г/см3, не более | 3,10 | ||||||
12 Сопротивление раздавливанию, %, не более, при давлении, МПа: 34,5 51,7 68,9 | 20,0 25,0 | 15,0 20,0 25,0 | 15,0 20,0 25,0 | 10,0 15,0 20,0 | 5,0 7,0 10,0 | 2,0 5,0 10,0 | 2,0 5,0 8,0 |
13 Относительное изменение массы при прокаливании, %, не более | 4,0 |
Примечание — Сопротивление раздавливанию определяют при давлениях 34,5; 51,7 и 68,9 МПа, что соответствует давлению 5000, 7500 и 10 000 фунт/дюйм2.
5.2 Упаковка и маркировка по ГОСТ 24717 с дополнениями по 5.2.1 и 5.2.2.
5.2.1 Пропанты упаковывают в мягкие стропные специализированные контейнеры разового использования по техническому документу массой нетто не более 1000 кг с пределом допускаемой погрешности взвешивания не более ±5 кг.
Допускается упаковывать пропанты в контейнеры с вкладышами толщиной более 40 мкм по технической документации.
5.2.2 Маркировку наносят:
- сокращенную — на каждый контейнер несмываемой краской на боковые поверхности с двух сторон;
- полную — на ярлыки, которые прикрепляют к стропам каждого контейнера.
Сокращенная маркировка должна содержать:
- полное и/или сокращенное наименование и/или товарный знак предприятия-изготовителя;
- обозначения фракции и марки пропанта.
Полная маркировка должна содержать:
- полное наименование предприятия-изготовителя и/или его товарный знак;
- обозначение и наименование настоящего стандарта;
- обозначения фракции и марки пропанта;
- номер партии;
- номер контейнера;
- массу нетто контейнера;
- дату изготовления.
6 Требования безопасности и охраны окружающей среды
6.1 Пропанты являются пожаро- и взрывобезопасными, не образуют токсичных соединений в воздушной среде и сточных водах.
6.2 Пропанты не являются радиоактивными. Максимальное значение эффективной удельной активности природных радионуклидов в изделиях не превышает 370 Бк/кг по санитарным правилам [1] или по ГОСТ 30108.
6.3 При транспортировании и хранении пропанты не выделяют вредных и токсичных веществ.
6.4 Пропанты по степени воздействия на организм относятся к 3-му классу опасности по ГОСТ 12.1.007. Образующаяся при применении пропантов пыль обладает раздражающим действием на слизистую оболочку глаз и верхних дыхательных путей.
6.5 В местах возможного пыления необходимо обеспечивать принудительную приточно-вытяжную вентиляцию. Рабочий персонал должен быть обеспечен индивидуальными противопыльными или фильтрующими респираторами по ГОСТ 12.4.028 или ГОСТ 12.4.041 и индивидуальными средствами защиты глаз по ГОСТ 12.4.253. Технологические процессы, характеризующиеся применением, образованием и выделением пыли, должны быть механизированы или автоматизированы. Следует предусматривать способы подавления пыли в процессе ее образования с применением воды или других средств согласно [2] (пункт 4.1.1).
6.6 При производстве и применении пропантов контроль воздуха рабочей зоны осуществляют по ГОСТ 12.1.005: для силикатсодержащей пыли, силикатов, алюмосиликатов (высокоглиноземистая огнеупорная глина, цемент, оливин, апатит, глина, каолиновый шамот) предельно допустимая концентрация (ПДК) составляет 8 мг/м3.
6.7 При хранении и применении пропантов следует соблюдать требования ГОСТ 17.0.0.01, ГОСТ Р 58577.
6.8 При погрузочно-разгрузочных работах следует соблюдать общие требования безопасности по ГОСТ 12.3.009.
7 Правила приемки
7.1 Правила приемки пропантов по ГОСТ Р 52667 с дополнениями по 7.1.1—7.1.6.
7.1.1 Масса партии пропантов — не более 200 т.
7.1.2 Масса мгновенной пробы — не менее 0,3 кг.
7.1.3 Мгновенные пробы отбирают с использованием пробоотборника от шести произвольных контейнеров каждой предъявляемой к приемке партии пропантов.
7.1.3.1 Мгновенные пробы объединяют в суммарную пробу, затем путем сокращения и деления получают лабораторную пробу массой не менее 2 кг (например, на ручном делителе, приведенном на рисунке 1).
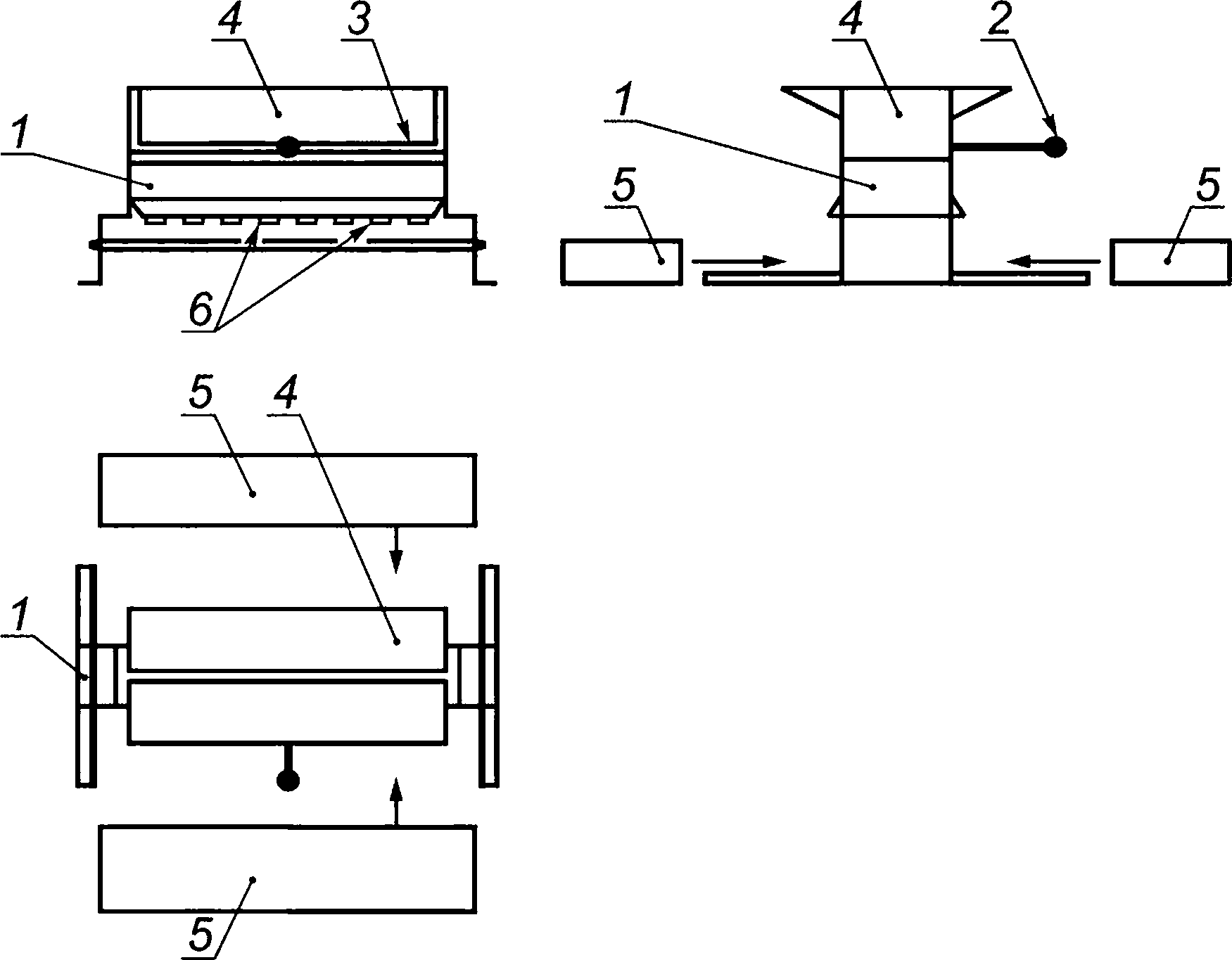
1 — основной корпус с габаритными размерами (295 ± 5) * (280 ± 5) х (165 ± 5) мм; 2 — рукоятка; 3 — задвижка; 4 — бункер;
5 — поддон; 6 — лопасти размером (12,5 ± 0,5) мм
Рисунок 1 — Ручной делитель проб
Если массы суммарной пробы недостаточно для получения необходимой массы лабораторной пробы, увеличивают количество мгновенных проб.
7.1.3.2 Перед началом приемо-сдаточных испытаний лабораторную пробу высушивают при температуре 105 °C с пределами допускаемого отклонения ±3 °C до постоянной массы в сушильном шкафу и остужают на воздухе до комнатной температуры.
7.1.4 При проверке соответствия качества пропантов требованиям настоящего стандарта проводят приемо-сдаточные испытания в соответствии с таблицей 3.
Таблица 3 — Периодичность проведения испытаний
Наименование показателя | Периодичность проведения испытаний |
Гранулометрический состав | От каждой партии |
Массовая доля гранул основной фракции | |
Насыпная плотность | |
Кажущаяся плотность | |
Сопротивление раздавливанию | |
Сферичность | |
Округлость | |
Относительное изменение массы при прокаливании | |
Массовая доля МдО и SiO2 | По требованию потребителя |
Окончание таблицы 3
Наименование показателя | Периодичность проведения испытаний |
Абсолютная (истинная) плотность | От каждой десятой партии |
Растворимость в смеси кислот | |
Растворимость в 15 %-ной соляной кислоте | По требованию потребителя |
Мутность | От каждой десятой партии |
7.1.5 Партия должна сопровождаться одним документом о качестве. Рекомендуемая форма документа о качестве — по ГОСТ Р 52667.
7.1.6 На случай разногласий в оценке качества пропантов при поставках не менее половины массы лабораторной пробы хранят в плотно закрытой упаковке в архиве. При поставках на территории Российской Федерации и на экспорт срок хранения составляет 12 мес.
8 Методы испытаний
8.1 Определение массовой доли оксида магния и оксида кремния (IV)
Массовую долю оксида магния и оксида кремния (IV) определяют по ГОСТ 2642.0, ГОСТ 2642.8 и ГОСТ 2642.3 или другими методами, обеспечивающими необходимую точность определения.
При возникновении разногласий в оценке качества пропантов применяют арбитражные методы по ГОСТ 2642.0 ГОСТ 2642.8 и ГОСТ 2642.3.
8.2 Определение гранулометрического состава
8.2.1 Сущность методаМетод основан на определении массовой доли пропантов, оставшихся на каждом сите из рекомендуемого набора сит после вибрационного воздействия на пробу для испытаний.
8.2.2 Средства измерений, аппаратура и вспомогательные устройства
Весы по ГОСТ Р 53228, класс точности высокий (II).
Просеивающая машина (вибростенд), с одновременным вращением и встряхиванием, рассчитанная с возможностью установки сит. Технические требования к вибростенду:
- частота вращения эксцентрика — от 280 до 290 мин-1;
- число встряхиваний — от 150 до 160 мин-1;
- пределы допускаемой погрешности таймера — ±5 с.
Наборы из семи сит по ГОСТ Р 51568, снабженные поддоном и крышкой (см. таблицу 4).
Квартователь лабораторный емкостью 0,5—2,0 кг.
Металлический стакан или лодочка для взвешивания.
Примечание — Использовать емкости из пластика, стекла или бумаги не допускается.
Щетка из полимерных материалов для очистки сит.
Допускается использовать другие средства измерений, испытательное и вспомогательное оборудование, обеспечивающие точность испытаний, предусмотренную настоящим стандартом.
Таблица 4 — Наборы сит для определения гранулометрического состава фракций пропантов, указанных в таблице 1.
Номер сита в наборе для рассева фракций пропантов | ||||||
10/14 | 12/18 | 16/20 | 16/30 | 20/40 | 30/50 | 40/70 |
6 | 8 | 12 | 12 | 16 | 20 | 30 |
8 | 12 | 16 | 16 | 20 | 30 | 40 |
10 | 14 | 18 | 18 | 25 | 35 | 45 |
12 | 16 | 20 | 20 | 30 | 40 | 50 |
Окончание таблицы 4
Номер сита в наборе для рассева фракций пропантов | ||||||
10/14 | 12/18 | 16/20 | 16/30 | 20/40 | 30/50 | 40/70 |
14 | 18 | 25 | 25 | 35 | 45 | 60 |
16 | 20 | 30 | 30 | 40 | 50 | 70 |
20 | 30 | 40 | 40 | 50 | 70 | 100 |
Поддон | Поддон | Поддон | Поддон | Поддон | Поддон | Поддон |
Примечание — Полужирным шрифтом выделены верхнее основное и нижнее основное сита в наборе. |
8.2.3 Проведение испытаний
Составляют набор минимум из семи сит с поддоном и крышкой в соответствии с таблицей 4 таким образом, чтобы размеры ячеек сита уменьшались сверху вниз. Таблицу 4 используют как справочную, испытания пропантов других гранулометрических составов не запрещены.
От предварительно сокращенной пробы пропанта отбирают и взвешивают пробу для испытаний массой приблизительно 100 г. Взвешивание проводят в металлической емкости с погрешностью, не превышающей ±0,1 г. Взвешивают каждое сито и поддон. Помещают пробу на верхнее сито. Устанавливают набор сит с поддоном и крышкой на просеивающую машину и встряхивают в течение 10 мин. Снимают набор сит с просеивающей машины, взвешивают каждое сито и поддон с оставшимися на них гранулами пропантов.
Допускаемое отклонение общей массы пропантов на ситах и поддоне от массы пробы для испытаний не должно превышать 0,5 %. В случае превышения необходимо повторить испытание на другой пробе пропанта.
Допускается не взвешивать лабораторные сита, а после просеивания с помощью щетки аккуратно извлечь остатки пропантов с каждого сита и поддона и взвесить.
Массовую долю гранул пропантов w, %, оставшихся на сите и поддоне, вычисляют по формуле
ГТ)? ~
(1)
где т2 — масса сита или поддона с гранулами пропантов, г;
т1 — масса сита или поддона перед испытанием, г;
тп — масса пробы для испытаний, г.
Результаты определений принимают согласно 9.3.2. Требования к погрешности измерений — по разделу 9.
8.3 Определение массовой доли гранул основной фракции
8.3.1 Средства измерений, аппаратура и вспомогательные устройстваВесы по ГОСТ Р 53228, класс точности высокий (II).
Сита номеров 6, 10, 12, 14, 16, 18, 20, 30, 40, 50, 70, 100 с поддоном и крышкой.
Лабораторный вибростенд по 8.2.2.
Металлическая емкость для взвешивания по 8.2.2.
Щетка из полимерных материалов для очистки сит.
8.3.2 Проведение испытаний
Пробу для испытаний массой приблизительно 100 г взвешивают с погрешностью, не превышающей ±0,1 г, и помещают на верхнее сито набора сит, соответствующего испытуемой фракции пропантов (см. таблицу 4) и состоящего из верхнего основного сита, нижнего основного сита, поддона и крышки. Набор сит устанавливают на ситовой лабораторный вибростенд и встряхивают в течение 10 мин. Снимают сита с вибростенда. С помощью щетки аккуратно переносят пропанты, оставшиеся на нижнем сите, в емкость, в которой взвешивали пробу для испытаний.
Допускается массовую долю основной фракции вычислять как сумму остатков на ситах номеров, находящихся между числителем и знаменателем в обозначении фракции (см. таблицу 4), полученных при определении гранулометрического состава по 8.2.3 с учетом положений раздела 4.
Массовую долю гранул основной фракции и/осн фр, %, оставшихся на нижнем сите, вычисляют по формуле
w - -^ЮО, (2)
"осн.фр /77 '
где тост — масса гранул, оставшихся на нижнем сите, г;
т — масса пробы для испытаний, г.
Полученный результат округляют до первой значащей цифры после запятой. Результаты определения принимают согласно 9.3.2. Требования к погрешности измерений — по разделу 9.
8.4 Определение сферичности и округлости
8.4.1 Сущность методаМетод основан на визуальной оценке формы гранул пропантов, увеличенных с помощью микроскопа.
8.4.2 Средства измерений аппаратура и вспомогательные материалы
Оптический микроскоп с 10—40-кратным увеличением или равнозначный.
Диаграмма Крумбьена — Шлосса (см. рисунок 2).
Весы по ГОСТ Р 53228, класс точности высокий (II).
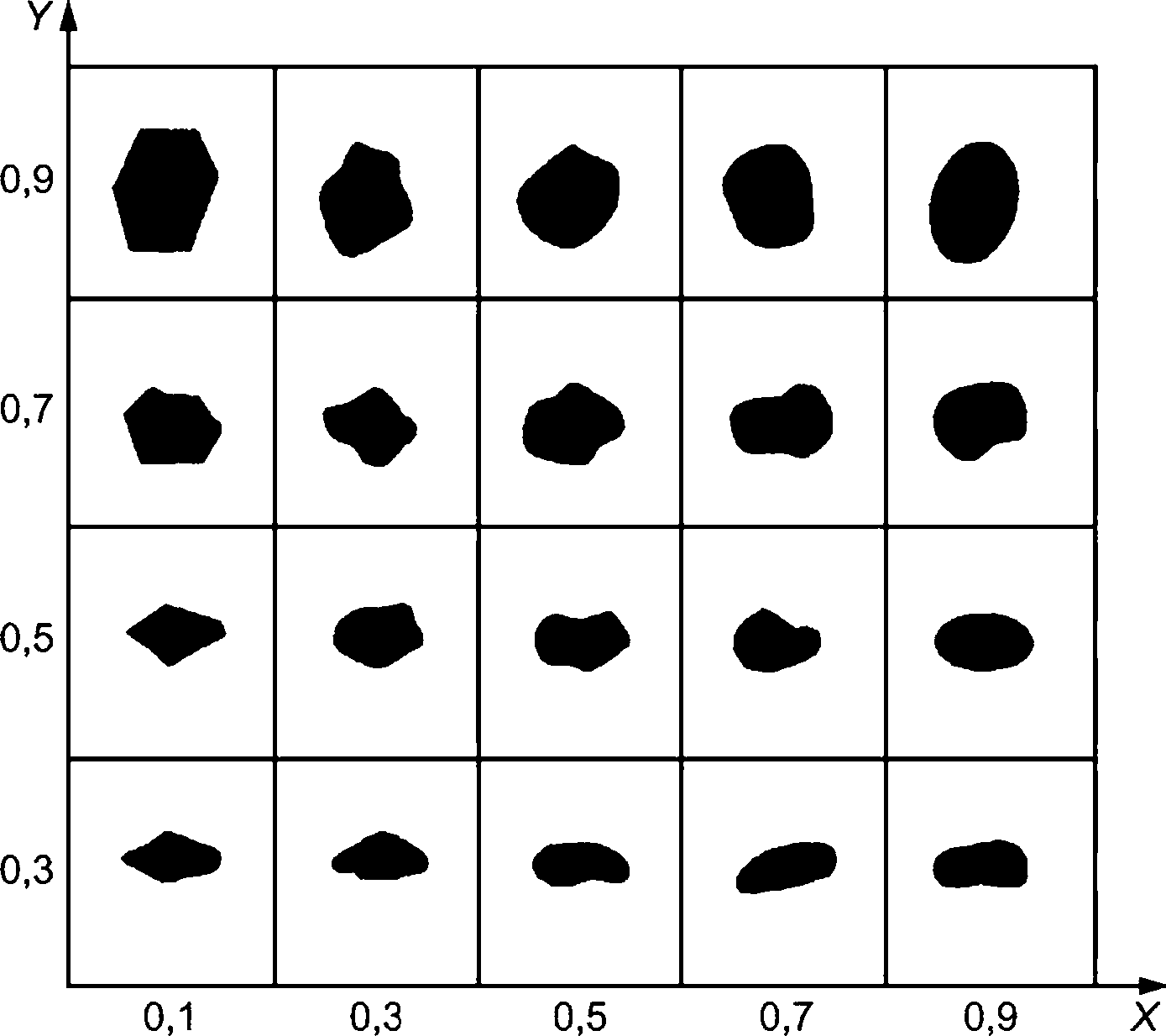
X — округлость; Y — сферичность
Рисунок 2 — Диаграмма Крумбьена — Шлосса для визуальной оценки сферичности и округлости
8.4.3 Проведение испытаний
Пробу для испытаний массой от 1 до 2 г насыпают на бумагу или другой материал слоем толщиной в одну гранулу и помещают на предметный столик микроскопа. Для светлых пропантов используют темную бумагу, для темных пропантов — белую. Для оценки формы произвольно выбирают не менее 20 гранул, находящихся в поле зрения.
При соответствующем увеличении микроскопа определяют сферичность, а затем округлость каждой из выбранных гранул путем сравнения с диаграммой Крумбьена — Шлосса (см. рисунок 2). Записывают показатели сферичности и округлости для каждой выбранной гранулы.
Вычисляют среднее арифметическое значение сферичности и округлости оцененного набора гранул с точностью до первой значащей цифры после запятой.
За результат принимают среднее арифметическое значение результатов оцененного набора гранул.
8.4.4 Допускается выполнять определение сферичности и округлости гранул пропантов, изображение которых увеличено с использованием фотографических и цифровых технологий, например цифровой фотокамеры, персонального компьютера или другого оборудования, позволяющего получать необходимую кратность увеличения. Требования к погрешности измерений — по таблице 5.
Таблица 5 — Значения показателей точности
Диапазон измерений, у. е. | Доверительные границы погрешности, ±Д (Р = 0,95) |
Сферичность и округлость от 0,3 до 0,9 включ. | 0,1 |
Порядок проведения испытаний аналогичен 8.4.3.
8.4.5 Рекомендуемое увеличение для микрофотоснимков приведено в таблице 6.
Таблица 6 — Рекомендуемое увеличение
Диапазон размеров частиц | Увеличение микрофотоснимка |
От 6/12 до 12/20 | 15-кратное |
От 16/20 до 20/40 | 30-кратное |
От 30/40 до 70/100 | 40-кратное |
8.5 Определение растворимости в кислых средах
8.5.1 Сущность методаМетод основан на гравиметрическом определении изменения массы пробы пропантов после обработки рабочими растворами кислот (смеси концентрированной соляной кислоты и фтористого кислого аммония).
8.5.2 Средства измерений, аппаратура, материалы и вспомогательные устройства
Весы по ГОСТ Р 53228, класс точности высокий (II) или специальный (I).
Водяная баня, обеспечивающая нагрев и поддержание температуры 66 °C с предельно допускаемым отклонением ±3 °C.
Сушильный шкаф, обеспечивающий нагрев и поддержание температуры 105 °C с предельно допускаемым отклонением ±3 °C.
Стакан цилиндрической формы из полипропилена диаметром 48—55 мм и высотой 80—90 мм с крышкой.
Мерный цилиндр или мерная колба вместимостью 100 см3 по ГОСТ 1770, исполнение 1.
Мерная колба вместимостью 1000 см3 по ГОСТ 1770.
Аналитический кислотостойкий фильтровальный аппарат (например, из фарфора, полиэтилена или полипропилена высокой плотности), использующий вакуум-фильтрацию с воронкой Гуча или воронкой Бюхнера.
Эксикатор по ГОСТ 25336 со стандартным осушителем (например, безводным хлоридом кальция).
Соляная кислота по ГОСТ 3118 квалификации не ниже ч. д. а.
Аммоний фтористый кислый по ГОСТ 9546 или другому нормативному документу квалификации не ниже ч. д. а.
Дистиллированная вода по ГОСТ Р 58144.
Беззольный фильтр «белая лента» по технической документации.
Таймер с пределами допускаемой погрешности ±5 с.
8.5.3 Приготовление рабочего раствора смеси кислот
Готовят рабочий раствор смеси соляной кислоты и аммония фтористого кислого HCI:NH4HF2 с массовым соотношением 4:1.
К 500 см3 дистиллированной воды, налитой в мерный цилиндр или мерную колбу вместимостью 1000 см3, добавляют 46,23 г чистого фтористого кислого аммония (NH4HF2) и растворяют при перемешивании. Массу NH4HF2 с чистотой менее 100 % рассчитывают делением 46,23 г на чистоту NH4HF2, выраженную в массовых долях. Добавляют 361 см3 соляной кислоты (с массовой концентрацией 37 %). При другой концентрации соляной кислоты указанный объем корректируют. Доводят объем раствора до 1000 см3 дистиллированной водой и тщательно перемешивают.
8.5.4 Проведение испытаний
Испытаниям подвергают пропанты, не прошедшие дополнительную механическую обработку, например просеивание на сите, испытания на сопротивление раздавливанию, измельчение.
Пробу для испытания массой 5 г, предварительно высушенную при (105 ± 3) °C до постоянной массы и охлажденную в эксикаторе, взвешивают с погрешностью, не превышающей ±0,001 г. Ее помещают в стакан цилиндрической формы, приливают 100 см3 рабочего раствора кислот, приготовленного по 8.5.3, и закрывают крышкой. Рабочий раствор и проба должны иметь комнатную температуру.
Устанавливают стакан на водяную баню при 66 °C и выдерживают, не перемешивая, в течение 30 мин. Уровень жидкости в водяной бане должен быть не ниже уровня жидкости в стакане.
Фильтр «белая лента» высушивают в сушильном шкафу при (105 ± 3) °C до постоянной массы, охлаждают в эксикаторе и определяют массу высушенного фильтра. Переносят содержимое стакана в фильтровальный аппарат, убедившись, что все частицы из стакана перенесены на фильтр. Фильтруют через предварительно взвешенный фильтр, установленный в предварительно взвешенную фильтровальную воронку. Вакуум-фильтрование выполняют в течение 1 мин.
Промывают пробу в фильтровальном аппарате тремя порциями по 20 см3 дистиллированной воды.
Фильтр с оставшейся на нем пробой высушивают при температуре (105 ± 3) °C до постоянной массы и взвешивают. Перед взвешиванием фильтр «белая лента» с пробой охлаждают в эксикаторе.
Растворимость в смеси кислот S, %, вычисляют по формуле
л ms + mF-mFS
S = --а100.
(3)
где ms — масса пробы до обработки рабочим раствором, г;
mF — масса высушенного фильтра, г;
mFS — масса фильтра с пробой после обработки рабочим раствором, отмывания и высушивания, г.
Полученный результат округляют до первой значащей цифры после запятой. Результаты определения принимают согласно 9.3.2. Требования к погрешности измерений — по разделу 9.
8.6 Определение растворимости в 15 %-ной соляной кислоте
8.6.1 Сущность методаМетод основан на гравиметрическом определении изменения массы пробы пропантов после обработки раствором соляной кислоты с массовой долей 15 %.
8.6.2 Средства измерений, аппаратура, материалы и вспомогательные устройства
Весы по ГОСТ Р 53228, класс точности высокий (II) или специальный (I).
Водяная баня, обеспечивающая нагрев и поддержание температуры 66 °C с предельно допускаемым отклонением ±3 °C.
Сушильный шкаф, обеспечивающий нагрев и поддержание температуры 105 °C с предельно допускаемым отклонением ±3 °C.
Кислота соляная по ГОСТ 3118, квалификация не ниже ч. д. а.
Дистиллированная вода по ГОСТ Р 58144.
Мерный цилиндр или мерная колба вместимостью 100 см3 по ГОСТ 1770, исполнение 1.
Мерная колба вместимостью 1000 см3.
Стакан цилиндрический формы из полипропилена диаметром 48—55 мм и высотой 80—90 мм с крышкой.
Аналитический кислотостойкий фильтровальный аппарат, например из фарфора, полиэтилена или полипропилена высокой плотности с режимом вакуумфильтрации с воронкой Гуча или воронкой Бюхнера.
Беззольный фильтр «белая лента» по технической документации.
Таймер с пределами допускаемой погрешности ±5 с.
Эксикатор по ГОСТ 25336 со стандартным осушителем (безводным хлоридом кальция).
8.6.3 Проведение испытаний
Испытаниям подвергают пропанты, не прошедшие дополнительную механическую обработку, например просеивание на сите, испытания на сопротивление раздавливанию, измельчение.
Предварительно готовят рабочий раствор соляной кислоты с массовой долей 15 %. К 500 см3 дистиллированной воды, налитой в мерную колбу вместимостью 1000 см3, добавляют 366 см3 соляной кислоты (с массовой концентрацией 37 %). При применении раствора соляной кислоты другой концентрации его объем корректируют. Смесь перемешивают, доводят до 1000 см3 дистиллированной водой и тщательно перемешивают.
Пробу для испытаний массой приблизительно 5 г, предварительно высушенную при (105 ± 3) °C до постоянной массы и охлажденную в эксикаторе, взвешивают с погрешностью, не превышающей ±0,001 г. Ее помещают в стакан цилиндрической формы, приливают 100 см3 рабочего раствора соляной кислоты и закрывают прозрачной крышкой. Рабочий раствор и проба должны иметь комнатную температуру.
Устанавливают стакан на водяную баню при 66 °C и выдерживают, не перемешивая, в течение 30 мин. Уровень жидкости в водяной бане должен быть не ниже уровня жидкости в стакане. Фильтр «белая лента» высушивают в сушильном шкафу при (105 ± 3) °C до постоянной массы, охлаждают в эксикаторе и определяют массу фильтра.
Переносят содержимое стакана в фильтровальный аппарат, убедившись, что все частицы из стакана перенесены на фильтр. Фильтруют через предварительно взвешенный фильтр, установленный в предварительно взвешенную фильтровальную воронку. Вакуум-фильтрование выполняют в течение 1 мин.
Промывают пробу в фильтровальном аппарате тремя порциями по 20 см3 дистиллированной воды. Фильтр с оставшейся на нем пробой высушивают при (105 ± 3) °C до постоянной массы и взвешивают.
Перед взвешиванием фильтр с пробой охлаждают в эксикаторе.
Растворимость в соляной кислоте SHCp %, вычисляют по формуле где ms — масса пробы до обработки рабочим раствором, г;
$hci =
ms + mF-mFS
100,
(4)
mF — масса высушенного фильтра, г;
mFS — масса фильтра с пробой после обработки рабочим раствором, отмывания и высушивания, г.
Полученный результат округляют до первой значащей цифры после запятой. Результаты определения принимают согласно 9.3.2. Требования к погрешности измерений — по разделу 9.
8.7 Определение мутности
8.7.1 Сущность методаМетод основан на измерении интенсивности рассеяния света в водной суспензии, полученной в результате перемешивания пробы пропантов с дистиллированной водой, нефелометрическим методом в единицах NTU.
8.7.2 Средства измерений, аппаратура и вспомогательные устройства
Весы по ГОСТ Р 53228, класс точности высокий (II) или специальный (I).
Мутномер или турбидиметр с пределом допускаемой относительной погрешности в диапазоне 0,1—1000 NTU ±6 %.
Встряхиватель для колб, обеспечивающий вращение виброэксцентрика с частотой (385 ± 15) мин “1 и диаметром вращения (амплитудой) 4,5 мм.
Мерные колбы по ГОСТ 1770 вместимостью 200, 500, 1000 см3.
Пипетки градуированные по ГОСТ 29169 вместимостью 1,5, 10, 20, 25 см3.
Коническая колба из полипропилена вместимостью 500 и 250 см3 с винтовой полипропиленовой крышкой (Колба Эрленмейера).
Стеклянный мерный цилиндр по ГОСТ 1770 вместимостью 100 см3.
Сернокислый гидразин по ГОСТ 5841, квалификации не ниже ч. д. а.
Технический уротропин (гексаметилентетрамин) по ГОСТ 1381, квалификации не ниже ч. д. а.
Дистиллированная вода по ГОСТ Р 58144.
Таймер с пределами допускаемой погрешности ±5 с.
8.7.3 Приготовление стандартных растворов формазина для градуировки мутнометра
8.7.3.1 Приготовление исходного раствора формазина с мутностью 4000 NTU
5,000 г сернокислого гидразина помещают в коническую колбу емкостью 500 см3 и растворяют в 400 см3 дистиллированной воды. 50,000 г гексаметилентетрамина помещают в коническую колбу емкостью 500 см3 и растворяют в 400 см3 дистиллированной воды. Переносят оба приготовленных раствора в мерную колбу вместимостью 1000 см3 и доводят до 1000 см3 дистиллированной водой.
Полученный раствор тщательно перемешивают и дают отстояться в течение 24 ч при комнатной температуре.
Срок хранения исходного раствора формазина с мутностью 4000 NTU — не более одного года.
8.7.3.2 Приготовление растворов для градуировки мутномера
Для градуировки прибора используют растворы формазина. Порядок приготовления раствора заключается в отборе в чистую мерную колбу стандартного раствора формазина с мутностью 4000 NTU, доведения колбы до метки дистиллированной водой и тщательным перемешиванием содержимого колбы в соответствии с таблицей 7.
Допускается осуществлять градуировку по формазиновым точкам, приготовленным согласно инструкции по эксплуатации прибора. Растворы готовят в день выполнения измерений.
Таблица 7
Значение мутности в растворе, NTU | Объем стандартного раствора формазина, см3 | Объем мерной колбы, см3 |
500 | 25,00 | 200 |
200 | 10,00 | 200 |
100 | 5,00 | 200 |
20 | 1,00 | 200 |
8.7.4 Проведение испытаний
Выбирают кюветы для выполнения измерений и их положение в держателе кюветного отделения в соответствии с инструкцией по эксплуатации прибора. Градуировку мутномера проводят в соответствии с инструкцией по эксплуатации прибора.
Для испытаний берут 20 см3 сухой пробы. Допускается отбирать пробу для испытаний на весах, предварительно рассчитав ее массу умножением рекомендованного объема 20 см3 на значение насыпной плотности испытуемых пропантов по 8.8, с погрешностью взвешивания, не превышающей ±0,1 г.
Пробу для испытаний помещают в коническую колбу с широким горлом и закручивающейся крышкой вместимостью 250 см3, добавляют 100 см3 дистиллированной воды. Колбу закрывают крышкой и выдерживают в течение 30 мин.
Устанавливают на встряхивателе скорость вращения на значение (385 ± 15) мин-1, встряхивают колбу в течение 30 с. Снимают колбу и выдерживают в течение 5 мин.
С помощью пипетки из центра объема суспензии над пропантом отбирают суспензию в количестве, необходимом для заполнения измерительной кюветы мутномера. При этом частицы пропанта не должны извлекаться, так как это приведет к искажению результатов.
Помещают отобранное количество водной суспензии в кювету мутномера для измерений мутности. Результаты измерений записывают в единицах NTU.
Требования к погрешности измерений — по разделу 9.
8.8 Определение насыпной плотности
8.8.1 Сущность методаМетод основан на взвешивании пропантов в калиброванном цилиндре после определения его вместимости с использованием специального устройства.
8.8.2 Средства измерений, аппаратура и вспомогательные устройства
Весы по ГОСТ Р 53228, класс точности высокий (II).
Калиброванный металлический мерный цилиндр из немагнитного металла или сплава.
Стеклянная (выравнивающая) пластина, полностью перекрывающая отверстие цилиндра.
Металлическая пластина для снятия излишков пропанта в цилиндре.
Дистиллированная вода по ГОСТ Р 58144.
Стакан вместимостью 150 см3 по ГОСТ 25336.
Устройство для определения насыпной плотности (см. рисунок 3), состоящее:
- из штатива для воронки, имеющего квадратное металлическое основание размерами (305,0 ± 1,0) * (305,0 ± 1,0) мм и треногу высотой (305,0 ± 1,0) мм;
- калиброванного металлического мерного цилиндра из немагнитного металла или сплава вместимостью приблизительно 100 см3 с внутренним диаметром (38,9 ± 0,1) мм;
- воронки из нержавеющей стали с гладкими внутренними швами и отсекающим клапаном на выходе.
Основные размеры воронки:
- верхний внутренний диаметр — (114,3 ± 0,4) мм;
- нижний внутренний диаметр — (12,7 ± 0,4) мм;
- высота конической части — (76,2 ± 0,4) мм;
- высота цилиндрической части — (12,7 ± 0,4) мм.
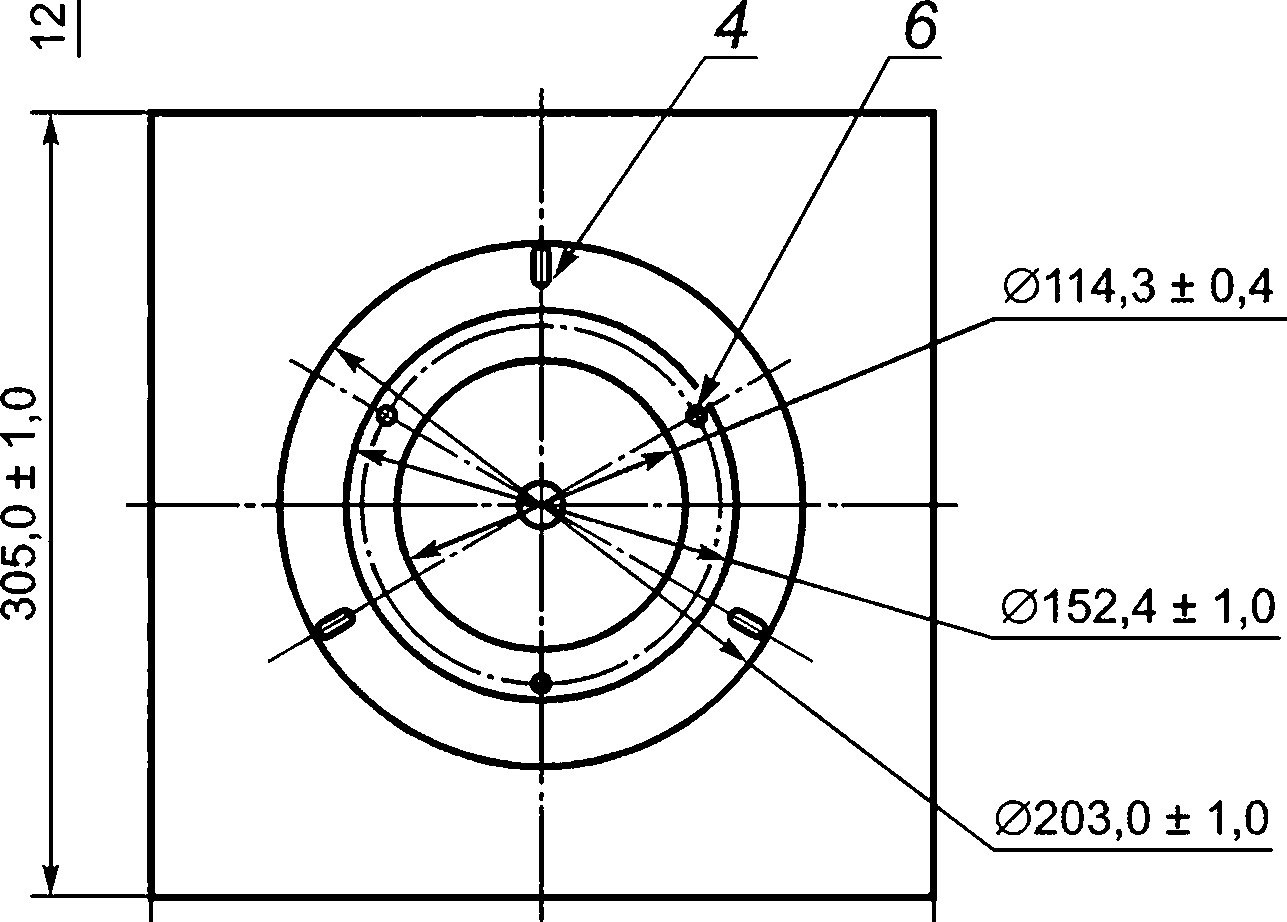
305,0 ± 1,0
1 — воронка; 2 — пружина, 3 — стопорный резиновый шарик; 4 — опора; 5 — калиброванный цилиндр; б — отверстия для винтов Рисунок 3 — Устройство для измерений насыпной плотности
Верхняя часть опоры состоит из горизонтального кольца диаметром (203,0 ± 1,0) мм, представляющего собой опору для сменной воронки, которую юстируют и крепят с помощью винтов.
Для гарантированного расположения цилиндра по центру выпускного отверстия воронки на основании устройства проставляют метки.
Клапан состоит из резинового стопорного шарика диаметром 34,9 мм, прикрепленного к воронке двумя винтовыми пружинами с усилием, обеспечивающим его плотное прилегание.
Допускается применение устройства для измерений насыпной плотности с другими размерами, не влияющими на точность измерений.
8.8.3 Определение вместимости цилиндра
Испытания проводят в условиях повторяемости на двух пробах.
Взвешивают пустой сухой цилиндр со стеклянной пластиной с погрешностью, не превышающей ±0,02 г. Наполняют цилиндр дистиллированной водой и проводят пластиной по верхней кромке ци-
14
линдра, удаляя воду точно по плоскости кромки. При плотно прижатой пластине удаляют, например, с помощью фильтровальной бумаги избыток воды и определяют общую массу цилиндра с водой и пластиной с погрешностью, не превышающей ±0,02 г.
Вместимость цилиндра У, см3, вычисляют по формуле
Рв
(5)
где тц в — общая масса цилиндра с водой и стеклянной пластиной, г;
тцс — масса пустого сухого цилиндра со стеклянной пластиной, г;
рв — плотность воды, соответствующая ее температуре во время определения вместимости цилиндра, г/см3.
Результатом определения вместимости цилиндра является среднее арифметическое значение результатов двух параллельных измерений.
Допускается принимать за результат определения вместимости цилиндра значение вместимости цилиндра, приведенное в сертификате о калибровке.
8.8.4 Проведение испытаний
Испытания проводят при температуре испытуемого материала в интервале от 19 °C до 28 °C. Взвешивают сухой пустой калиброванный цилиндр с погрешностью, не превышающей ±0,1 г. В воронку, выходное отверстие которой закрыто резиновым стопорным шариком, насыпают 150 см3 пробы для испытаний. Под центром выходного отверстия воронки помещают калиброванный цилиндр. Перемещая резиновый шарик влево или вправо, выпускают весь объем пропантов в цилиндр. Излишек пропантов в калиброванном цилиндре аккуратно снимают металлической пластиной по кромке цилиндра без встряхивания и трамбования.
Взвешивают калиброванный цилиндр с пробой с погрешностью, не превышающей ±0,1 г.
Насыпную плотность рн, г/см3, вычисляют по формуле где /лцп — масса калиброванного цилиндра с пробой для испытаний, г;
тц — масса сухого пустого калиброванного цилиндра, г;
\/ — вместимость цилиндра, см3.
Полученный результат округляют до второй значащей цифры после запятой. Результаты измерений принимают по 9.3.2. Требования к погрешности измерений — по разделу 9.
8.9 Определение кажущейся плотности
8.9.1 Сущность методаМетод основан на пикнометрическом определении плотности пропантов путем установления объема пробы пропантов для испытаний с учетом имеющихся в них открытых пор.
8.9.2 Средства измерений, аппаратура, материалы и вспомогательные устройства
Весы по ГОСТ Р 53228, класс точности высокий (II).
Ртутный термометр с диапазоном измерений от 0 °C до 50 °C и ценой деления шкалы не более 0,1 °C.
Жидкостной пикнометр вместимостью 25 или 50 мл по ГОСТ 22524.
Сушильный шкаф, обеспечивающий нагрев и поддержание температуры 105 °C с предельно допускаемыми отклонениями ±3 °C.
Вакуумная установка, состоящая из вакуумного насоса, вакуумного эксикатора, манометра и многоходового клапана и позволяющая создавать и поддерживать остаточное давление (8 ± 2) кПа [(60 ± 15) мм рт. ст.].
Емкость для взвешивания.
Пипетка градуированная по ГОСТ 29169 вместимостью 50 см3.
Воронка с ножкой для установки внутри пикнометра.
Эксикатор по ГОСТ 25336 со стандартным осушителем (например, безводным хлоридом кальция).
Дистиллированная вода по ГОСТ Р 58144.
Уайт-спирит по ГОСТ 3134.
Авиационный керосин ТС-1 по ГОСТ 10227.
Емкость для вакуумированной дистиллированной воды.
8.9.3 Приготовление вакуумированной дистиллированной воды
В эксикатор вакуумной установки помещают емкость с дистиллированной водой, создают в нем остаточное давление (8 ± 2) кПа [(60 ± 15) мм рт. ст.] и выдерживают емкость при данном давлении в течение 45 мин. Затем давление доводят до атмосферного, извлекают емкость и плотно закрывают крышкой.
8.9.4 Проведение испытаний
8.9.4.1 Определение кажущейся плотности пропантов с использованием вакуумированной воды
Испытания проводят при температуре испытуемого материала и воды в интервале от 19 °C до 28 °C.
Осторожно заполняют пикнометр до метки вакуумированной дистиллированной водой. Проверяют, чтобы в жидкости отсутствовали пузырьки воздуха. Удаляют излишки жидкости с внешней поверхности пикнометра.
Взвешивают пикнометр, заполненный вакуумированной дистиллированной водой, с погрешностью, не превышающей ±0,01 г.
Определяют массу емкости для взвешивания, добавляют приблизительно 10 г пробы для испытаний, предварительно высушенной при (105 ± 3) °C до постоянной массы и охлажденной в эксикаторе. Взвешивают емкость с пробой с погрешностью, не превышающей ±0,01 г. Рассчитывают массу пропантов. Выливают примерно половину объема воды из пикнометра и помещают взвешенную пробу из емкости для взвешивания в пикнометр. Для перенесения пропантов из емкости в пикнометр используют воронку.
Осторожно добавляют пипеткой вакуумированную дистиллированную воду комнатной температуры в пикнометр до метки и удаляют ее остатки с поверхности пикнометра. Взвешивают пикнометр с пропантами и вакуумированной дистиллированной водой с погрешностью, не превышающей ±0,01 г.
Кажущуюся плотность ркаж, г/см3, вычисляют по формуле
_ ^2рв.в
Ркаж“ + т2-т3’
где рв в — плотность вакуумированной дистиллированной воды при комнатной температуре по ГОСТ 2211, г/см3;
т1 — масса пикнометра с вакуумированной дистиллированной водой, г;
т2 — расчетная масса пропантов, г;
т3 — масса пикнометра с вакуумированной дистиллированной водой и пробой для испытаний, г.
Полученный результат округляют до второй значащей цифры после запятой. Результаты измерений принимают по 9.3.2. Требования к погрешности измерений — по разделу 9.
8.9.4.2 Определение кажущейся плотности пропантов с использованием органических жидкостей Испытания проводят при температуре испытуемого материала и органической жидкости в интервале от 19 °C до 28 °C.
Для определения кажущейся плотности пропантов используют органические жидкости, характеризующиеся вязкостью менее 5 МПа с при температуре проведения испытаний и температурой начала кипения не ниже 150 °C (например, уайт-спирит, керосин авиационный ТС-1).
Для определения плотности органической жидкости в условиях проведения испытаний взвешивают пустой сухой пикнометр. Заполняют пикнометр жидкостью до наливной линии, удаляют излишки жидкости с внешней поверхности, взвешивают пикнометр с жидкостью. Плотность органической жидкости роргж, г/см3, рассчитывают по формуле
_ /п5-/п4
Рорг.ж V ’ (8)
'п
где т5 — масса пикнометра и органической жидкости при комнатной температуре испытания, г;
т4 — масса сухого пикнометра, г;
\/п — объем пикнометра, см3.
Определение проводят в соответствии с 8.9.4.1, заменяя вакуумированную дистиллированную воду на используемую органическую жидкость. Рассчитывают кажущуюся плотность пропанта Ркаж, г/см3, по формуле
__ffizPoprjc
(9)
Рмж= т5 + тг- т6’
где mQ — масса пикнометра с пробой пропанта, заполненного органической жидкостью при комнатной
температуре, г.
Полученный результат округляют до второй значащей цифры после запятой. Результаты измерений принимают по 9.3.2. Требования к погрешности измерений — по разделу 9.
8.10 Определение абсолютной (истинной) плотности
8.10.1 Сущность методаМетод основан на определении плотности пропантов путем установления объема пробы пропантов с учетом имеющихся в них открытых и закрытых пор с помощью гелиевого пикнометра. Измерение давления газа при заполнении им камеры пикнометра с пробой для испытаний и затем при перекачивании его во вторую пустую камеру пикнометра позволяет рассчитать объем твердой фазы пробы.
8.10.2 Средства измерений, аппаратура, материалы и вспомогательные устройства
Газовый пикнометр, позволяющий выполнять измерения с относительной погрешностью, не превышающей ±0,3 %.
Весы по ГОСТ Р 53228, класс точности высокий (II).
Сушильный шкаф, обеспечивающий нагрев и поддержание температуры 105 °C с предельно допускаемыми отклонениями ±3 °C.
Газообразный сжатый очищенный гелий по технической документации.
Эксикатор по ГОСТ 25336 со стандартным осушителем (например, безводным хлоридом кальция).
8.10.3 Проведение испытаний
Выполняют градуировку газового пикнометра в соответствии с инструкцией по эксплуатации. Пропанты в количестве, равном 2/3 объема ячейки для пробы пикнометра, высушивают при (105 ± 3) °C до постоянной массы и охлаждают в эксикаторе до комнатной температуры. Определяют массу пробы для испытаний с погрешностью, не превышающей ±0,01 г.
Устанавливают ячейку с пропантами в камеру для пробы пикнометра. Продувают камеру газом при давлении не более 13,8 кПа в течение времени, установленного стандартной программой измерений пикнометра.
Проводят определение абсолютной (истинной) плотности пробы пропантов, выполняя 10 продувок пробы газом и пять промежуточных измерений плотности.
За результат принимают среднее значение пяти промежуточных измерений. Результат округляют до третьей значащей цифры после запятой. Требования к погрешности измерений — по разделу 9.
8.11 Определение сопротивления раздавливанию
8 .11.1 Сущность методаМетод основан на определении массовой доли гранул, разрушенных заданной сжимающей нагрузкой.
8 .11.2 Средства измерений, аппаратура и вспомогательные устройства
Гидравлическая или механическая машина для испытаний на сжатие, обеспечивающая постепенное и плавное увеличение усилия и оборудованная системой измерений приложенного усилия с предельно допускаемыми отклонениями не более ±2 %.
Ячейка для раздавливания гранул (см. рисунок 4) или аналогичная.
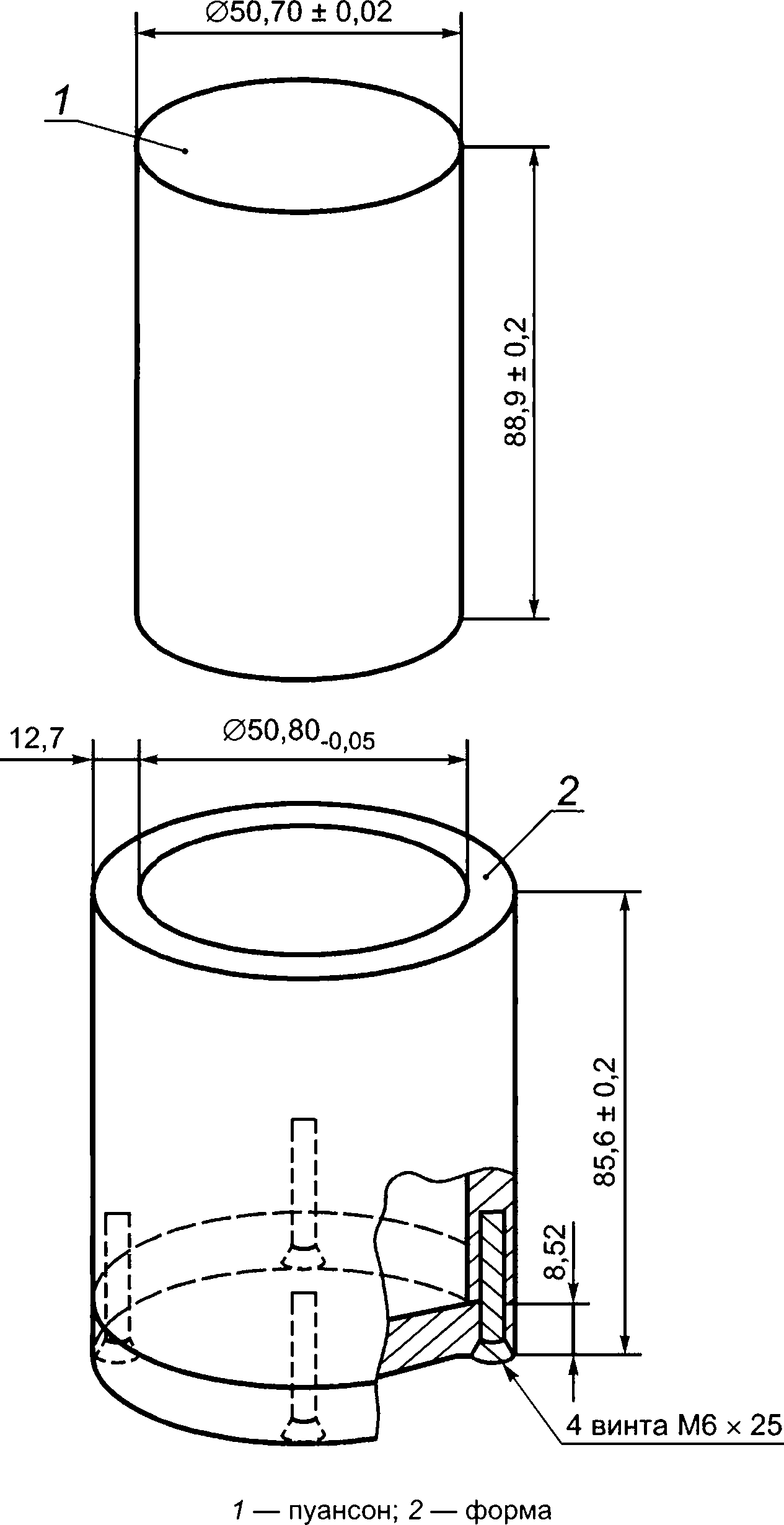
Рисунок 4 — Ячейка для раздавливания гранул
Примечания
1 Ячейку рекомендуется изготовлять из стали марки 4340 с твердостью по Роквеллу не менее 43,0 по шкале С или стали аналогичной марки, обеспечивающей при закалке требуемую твердость.
2 Форму периодически проверяют на износ по внутреннему диаметру — не реже одного раза в шесть месяцев.
3 При превышении значения внутреннего диаметра формы более 3,25 % осуществляют ее замену.
4 Допускается применение ячеек других размеров, не приводящее к изменению аттестованных характеристик метода испытаний.
Лабораторные сита, поддон и крышка. Номера сит определяют в соответствии с фракцией испытуемых пропантов.
Весы по ГОСТ Р 53228, класс точности высокий (II).
Просеивающая машина (вибростенд), с одновременным вращением и встряхиванием, допускающая установку сит. Технические требования — по 8.2.2.
Таймер с пределами допускаемой погрешности ±5 с.
Металлическая емкость для взвешивания по 8.2.2.
8 .11.3 Подготовка пробы
Пробу для испытаний массой от 100 до 120 г просеивают на просеивающей машине в течение 10 мин через набор сит, номера которых соответствуют фракциям испытуемых пропантов. Пропанты, оставшиеся на верхнем сите и прошедшие через нижнее сито, удаляют, а остальные используют для испытаний.
8 .11.4 Проведение испытаний
Массу пробы для испытаний т, г, вычисляют по формуле
т = 1,22рн-^ (10)
где 1,22 — постоянная ячейки для раздавливания, учитывающая объем пропантов, приходящийся на 1 см2 площади дна ячейки, см;
рн — насыпная плотность [см. формулу (6)], г/см3;
dBH — внутренний диаметр ячейки для раздавливания, см.
Взвешивают рассчитанное количество просеянных пропантов с погрешностью, не превышающей ±0,1 г, и засыпают через воронку в ячейку для раздавливания, перемещая струю пропантов так, чтобы их поверхность в ячейке была ровной. Записывают массу в граммах, с двумя значащими цифрами после запятой. Поверхность пропантов выравнивают поворотом пуансона на 180° без приложения усилия.
Затем без встряхивания помещают ячейку в машину для испытаний на сжатие.
Усилие F, Н, необходимое для обеспечения заданного давления, вычисляют по формуле где р — давление, МПа.
Равномерно в течение 1 мин увеличивают нагрузку до достижения рассчитанного усилия и поддерживают его в течение 2 мин.
Примечание — Допускается увеличивать нагрузку с постоянным ее возрастанием на 13,8 МПа в минуту до достижения рассчитанного усилия, которое поддерживают в течение 2 мин.
Снижают усилие до нуля, снимают ячейку для раздавливания гранул с машины для испытаний и переносят ее содержимое на набор сит. После рассева на лабораторном вибростенде в течение 10 мин взвешивают разрушенные гранулы из поддона с погрешностью, не превышающей ±0,1 г. Записывают массу в граммах, с двумя значащими цифрами после запятой.
Массовую долю разрушенных гранул (сопротивление раздавливанию) f, %, вычисляют по формуле
Г=^. (12)
где тр — масса разрушенных гранул, г.
Результат округляют до второй значащей цифры после запятой. Результаты измерений принимают согласно 9.3.2. Требования к погрешности измерений — по разделу 9.
8.12 Определение относительного изменения массы при прокаливании
8.12.1 Сущность методаМетод основан на определении количества сгораемого материала в пробе пропантов с полимерным покрытием при прокаливании в муфельной печи.
8.12.2 Средства измерений, аппаратура и вспомогательные устройства
Весы по ГОСТ Р 53228, класс точности высокий (II).
Сушильный шкаф, обеспечивающий нагрев и поддержание температуры 105 °C с предельно допускаемым отклонением ±3 °C.
Обычная или микроволновая муфельная печь, обеспечивающая нагрев и поддержание температуры 950 °C с предельно допускаемым отклонением ±20 °C.
Керамический или кварцевый тигель с крышкой для прокаливания.
Тигельные щипцы.
Прочные и изолирующие хлопчатобумажные перчатки и экран для защиты лица.
Эксикатор по ГОСТ 25336 со стандартным осушителем (например, безводным хлоридом кальция).
Ручной делитель пробы (см. рисунок 1).
8.12.3 Проведение испытаний
Тигель с крышкой предварительно прокаливают до постоянной массы в печи, нагретой до температуры 950 °C, и охлаждают в печи, а затем в эксикаторе — до комнатной температуры и взвешивают в граммах с точностью до четырех значащих цифр после запятой.
Для получения представительной пробы массой до 10 г используют ручной делитель пробы, а также последовательное квартование.
Затем отбирают в тигель пробу для испытаний массой от 6 до 8 г, предварительно высушенную в сушильном шкафу при температуре (105 ± 3) °C до постоянной массы и охлажденную в эксикаторе.
Пробу для испытаний не сушат, если ее отбирают непосредственно после обжига или испытывают пропанты с полимерным покрытием.
Взвешивают тигель с крышкой и пробой в граммах с точностью до четырех значащих цифр после запятой.
Помещают закрытый тигель с пробой в муфельную печь, нагревают ее до температуры 950 °C. Прокаливают пробу при этой температуре до постоянной массы. Рекомендуемое время прокаливания:
- не менее 2 ч — в муфельной печи;
- 15 мин — в микроволновой печи.
Повторно взвешивают тигель с крышкой и пробой в граммах с точностью до четырех значащих цифр после запятой.
Относительное изменение массы при прокаливании Ат, %, вычисляют по формуле
ту-тя
&п’ = -Ц^1'00' (13)
где т2 — масса тигля с крышкой и пробой, г;
т3 — масса тигля с крышкой и пробой после прокаливания, г;
т1 — масса тигля с крышкой после прокаливания в печи, г.
Результат округляют до второй значащей цифры после запятой. Результаты измерений принимают согласно 9.3.2. Требования к погрешности измерений — по разделу 9.
9 Требования к погрешности измерений
9.1 Значения показателей точности, повторяемости и воспроизводимости результатов измерений при выполнении испытаний приведены в таблице 8. Определения и методы измерений точности, повторяемости и воспроизводимости по ГОСТ Р ИСО 5725-1.
Таблица 8 — Значения показателей точности, повторяемости и воспроизводимости результатов измерений при выполнении испытаний
Диапазон измерений показателя | Предел допускаемой погрешности, Д(ботн) (Р = 0,95) | Показатель воспроизводимости С КО* gr | Показатель вну-трилабораторной прецизионности, С КО* о | Показатель повторяемости ОКО’ ог |
1 Гранулометрический состав, %: | ||||
от 0,05 до 2,00 включ. | 0,4Х | 0,20Х | 0,17Х | 0,14Х |
св. 2 » 5 » | 0,9 | 0,48 | 0,40 | 0,33 |
» 5 »10 » | 1,1 | 0,58 | 0,48 | 0,40 |
» 10 » 20 » | 1,5 | 0,79 | 0,66 | 0,55 |
»20 »50 » | 2,7 | 1,4 | 1,2 | 1,0 |
»50 » 95 » | 4,0 | 2,2 | 1,8 | 1,5 |
2 Массовая доля гранул основной | ||||
фракции, %: | ||||
от 80,0 до 99,9 включ. | 1,5 | 0,75 | 0,71 | 0,68 |
Окончание таблицы 8
Диапазон измерений показателя | Предел допускаемой погрешности, Д(80ТН) (Р = 0,95) | Показатель воспроизводимости CKO* cR | Показатель вну-трилабораторной прецизионности, СКО* о | Показатель повторяемости СКО* |
3 Растворимость в смеси кислот, %: | ||||
от 1 до 2 включ. | 0,3 | 0,17 | 0,14 | 0,12 |
св. 2 » 5 » | 0,5 | 0,24 | 0,20 | 0,17 |
» 5 » 10 » | 0,7 | 0,34 | 0,29 | 0,24 |
» 10» 20 » | 1,0 | 0,53 | 0,44 | 0,37 |
4 Растворимость в 15 %-ной соляной кислоте, %: | ||||
от 0,1 до 0,5 включ. | 0,3 | 0,17 | 0,14 | 0,12 |
св. 0,5 » 1,0 » | 0,4 | 0,20 | 0,17 | 0,14 |
5 Мутность, NTU: | ||||
от 20 до 50 включ. | 6 | 3,0 | 2,5 | 1,5 |
св. 50 » 100 » | 9 | 4,8 | 4,0 | 2,4 |
» 100» 200 » | 15 | 7,6 | 6,3 | 3,8 |
» 200 » 500 » | 25 | 13 | 11 | 6,5 |
6 Насыпная плотность, г/см3: | ||||
от 1,00 до 1,75 включ. | 0,01 | 0,0070 | 0,0040 | 0,0036 |
7 Кажущаяся плотность, г/см3: | ||||
от 1 до 2 включ. | 0,07 | 0,035 | 0,029 | 0,024 |
св. 2 » 5 » | 0,11 | 0,056 | 0,047 | 0,039 |
» 5 » 6 » | 0,12 | 0,062 | 0,052 | 0,043 |
8 Абсолютная (истинная) плотность, г/см3: | ||||
от 1 до 2 включ. | 0,007 | 0,0034 | 0,0028 | 0,0024 |
св. 2 » 5 » | 0,010 | 0,0052 | 0,0043 | 0,0036 |
» 5 » 6 » | 0,011 | 0,0056 | 0,0047 | 0,0039 |
9 Сопротивление раздавливанию (массовая доля разрушенных гранул), %: | ||||
от 1 до 50 включ. | 0,20Х | 0,1 ОХ | 0,08Х | 0,06Х |
10 Относительное изменение массы при прокаливании, %: | ||||
от 1 до 2 включ. | 0,11 | 0,056 | 0,047 | 0,039 |
св. 2 » 5 » | 0,17 | 0,087 | 0,073 | 0,061 |
* СКО — среднее квадратическое отклонение. |
9.2 Значения пределов повторяемости, воспроизводимости и нормативы контроля результатов при выполнении измерений приведены в таблице 9.
Таблица 9 — Значения пределов повторяемости, воспроизводимости и нормативы контроля результатов при выполнении измерений
Диапазон измерений показателя | Предел повторяемости г (Р = 0,95) | Критический диапазон Cf?0,95 (4) | Норматив контроля внутрилабо-раторной прецизионности Кл(Р = 0,95) | Предел воспроизводимости R (Р = 0,95) | Норматив контроля процедуры выполнения измерений Кт (Р = 0,90) |
1 Гранулометрический состав, %: от 0,05 до 2,00 включ. | 0,4Х | 0,5Х | 0,5Х | 0,6Х | — |
св. 2 » 5 » | 0,9 | 1,2 | 1,1 | 1,3 | — |
» 5 » 10 » | 1,1 | 1,5 | 1,3 | 1,6 | — |
»10» 20 » | 1,5 | 2,0 | 1,8 | 2,2 | — |
» 20 « 50 » | 2,8 | 3,6 | 3,3 | 3,9 | — |
» 50 » 95 » | 4 | 5 | 5 | 6 | — |
2 Массовая доля гранул основной фракции, %: от 80,0 до 99,9 включ. | 1,9 | 2,5 | 2,0 | 2,1 | 1,2 |
3 Мутность, NTU: от 20 до 50 включ. | 4 | 5 | 7 | 8 | — |
св. 50 » 100 » | 7 | 9 | 11 | 13 | — |
» 100» 200 » | 11 | 14 | 17 | 21 | — |
» 200 » 500 » | 18 | 24 | 30 | 36 | — |
4 Растворимость в смеси кислот, %: от 1 до 2 включ. | 0,3 | 0,4 | 0,4 | 0,5 | 0,2 |
св. 2 » 5 » | 0,5 | 0,6 | 0,6 | 0,7 | 0,3 |
» 5 » 10 » | 0,7 | 0,9 | 0,8 | 0,9 | 0,5 |
» 10 » 20 » | 1,0 | 1,3 | 1,2 | 1,5 | 0,7 |
5 Растворимость в 15 % соляной кислоте, %: от 0,1 до 0,5 включ. | 0,3 | 0,4 | 0,4 | 0,5 | 0,2 |
св. 0,5 » 1,0 » | 0,4 | 0,5 | 0,5 | 0,6 | 0,3 |
6 Насыпная плотность, г/см3: от 1,00 до 1,75 включ. | 0,01 | 0,01 | 0,01 | 0,02 | 0,01 |
7 Кажущаяся плотность, г/см3: от 1 до 2 включ. | 0,07 | 0,09 | 0,08 | 0,10 | 0,05 |
св. 2 » 5 » | 0,11 | 0,14 | 0,13 | 0,16 | 0,08 |
» 5 » 6 » | 0,12 | 0,16 | 0,14 | 0,17 | 0,09 |
8 Абсолютная (истинная) плотность, г/см3: от 1 до 2 включ. | 0,007 | 0,009 | 0,008 | 0,009 | 0,005 |
св. 2 » 5 » | 0,010 | 0,013 | 0,012 | 0,014 | 0,007 |
» 5» 6 » | 0,011 | 0,014 | 0,013 | 0,016 | 0,008 |
9 Сопротивление раздавливанию (массовая доля разрушенных гранул), %: от 1 до 50 включ. | 0,17Х | 0,22Х | 0,22Х | 0,28Х | 0,1 ЗХ |
Окончание таблицы 9
Диапазон измерений показателя | Предел повторяемости г (Р= 0,95) | Критический диапазон ^0,95 (4) | Норматив контроля внутрилабо-раторной прецизионности Рл(Р = 0,95) | Предел воспроизводимости R (Р = 0,95) | Норматив контроля процедуры выполнения измерений /<т (Р = 0,90) |
10 Относительное изменение массы при прокаливании, %: от 1 до 2 включ. св. 2 » 5 » | 0,11 0,17 | 0,14 0,22 | 0,13 0,20 | 0,16 0,24 | 0,08 0,12 |
9.3 Проверка приемлемости и обработка результатов измерений
9.3.1 Проверку приемлемости результатов измерений выполняют для определения гранулометрического состава, массовой доли гранул основной фракции, растворимости в смеси кислот, растворимости в 15 %-ной соляной кислоте, мутности, насыпной, кажущейся и абсолютной (истинной) плотности, сопротивления раздавливанию и относительного изменения массы при прокаливании.
9.3.2 Проверка приемлемости и обработка результатов измерений, полученных в условиях повторяемости
Выполняют два параллельных измерения в условиях повторяемости. Абсолютное расхождение полученных результатов измерений | Х1 - Х2| сравнивают с пределом повторяемости г, равным 2,77ог при доверительной вероятности Р = 0,95 (см. таблицу 9). Если абсолютное расхождение результатов двух параллельных измерений, не превышающих значения повторяемости | Х1 - Х21 г, то результаты измерений признают приемлемыми и в качестве окончательного результата принимают их среднее арифметическое значение по формуле
- х,+х2
Х= ~~2 (14)
Если абсолютное расхождение | Х1 - Х21 превышает значения г, то проводят еще два параллельных измерения.
Если абсолютное расхождение между результатами четырех измерений |Xmax - Xmin| не более критического диапазона С/?095(4), равного 3,63ог, т. е. | Xmax - Xmin| < С/?095^, то в качестве окончательного результата принимают среднее арифметическое четырех измерении. Если условие I \пах “ ^min I - 95(4) не выполнено, в качестве окончательного результата принимают медиану
результатов четырех измерений X, которую вычисляют по формуле
у_Х2+Х3
X——2—• (15)
где Х2 — второй по значению наименьший результат измерений;
Х3 — третий по значению наименьший результат измерений.
В этом случае выясняют и устраняют причину повышенного разброса результатов измерений.
В протоколе испытаний указывают результат измерений, его погрешность Д в абсолютных единицах в виде X ± Д с доверительной вероятностью Р = 0,95. Допускается вместо погрешности результатов измерений приводить ссылку на настоящий стандарт.
9.3.3 Проверка приемлемости и обработка результатов измерений, полученных в условиях воспроизводимости _ _
Результаты измерений, полученные в двух лабораториях, Х^ и Х2 признают приемлемыми, если значение их абсолютного расхождения не превышает значения предела воспроизводимости R, приведенного в таблице 9, т. е.
(16)
При выполнении этого условия в качестве окончательного результата может быть принято общее среднее значение результатов измерений.
При нарушении условия устанавливают причины, вызвавшие превышение допускаемого расхождения результатов измерений.
9.3.4 Контроль качества результатов измерений при выполнении испытаний
Оперативный контроль точности выполняют для определения гранулометрического состава; массовой доли гранул основной фракции, растворимости в смеси кислот, растворимости в 15 %-ной соляной кислоте, мутности, насыпной, кажущейся и абсолютной (истинной) плотности, сопротивления раздавливанию и относительного изменения массы при прокаливании.
Контроль внутрилабораторной прецизионности результатов измерений выполняют для показателей качества пропантов, приведенных в 9.3.1.
9.3.4.1 Оперативный контроль точности выполнения измерений
Для контроля процедуры выполнения измерений (контроля точности результатов измерений) проводят измерения образца для контроля. Если значение отклонения результата измерений образца для контроля X от аттестованного (расчетного) значения С не превышает значения норматива контроля Kv приведенного в таблице 11, т. е. | X- С| < /<т, то результаты контрольной процедуры признают удовлетворительными.
При невыполнении данного условия испытания прекращают до выявления и устранения причин, приводящих к неудовлетворительным результатам.
9.3.4.2 Контроль внутрилабораторной прецизионности результатов измерений
В целях контроля внутрилабораторной прецизионности выполняют повторные измерения проб, ранее уже проходивших процедуру выполнения измерений для определения значения контролируемого показателя качества, изменяя влияющие факторы (разное время, разные средства измерений и испытательное оборудование, разные операторы и т. д.).
Значение абсолютного расхождения между двумя результатами измерений, полученными в условиях внутрилабораторной прецизионности, Х1 и Х2, не должно превышать значения норматива контроля внутрилабораторной прецизионности /?л по таблице 9.
При нарушении данного условия устанавливают и устраняют причины, вызвавшие недопускаемое расхождение результатов измерений.
При соблюдении условий 9.3.4 погрешность результата измерений не должна превышать значения А, приведенного в таблице 8.
10 Транспортирование и хранение
10.1 Транспортирование и хранение по ГОСТ 24717 с дополнениями по 10.1.1 и 10.1.2.
10.1.1 Пропанты, упакованные по 5.2, транспортируют железнодорожным транспортом в открытом подвижном составе или автомобильным транспортом.
10.1.2 Пропанты хранят в крытых складских помещениях в условиях, исключающих повреждение упаковки, дополнительное увлажнение пропантов и упаковки.
При использовании упаковочной тары (мягкие контейнеры) с вкладышами толщиной более 40 мкм пропанты хранят на открытых площадках в условиях, исключающих попадание атмосферных осадков.
Приложение А (справочное)
Основные требования, предъявляемые к ситам для испытаний
А.1 Основные требования, предъявляемые к ситам для испытаний (см. [3]), приведены в таблице А.1.
Таблица А.1 — Основные требования, предъявляемые к ситам для испытаний
В миллиметрах
Номер сита | Номинальный размер ячейки в свету х, у | Предельно допускаемое отклонение среднего размера ячейки в свету от номинального | Номинальный диаметр проволоки dy |
6 | 3,350 | ±0,110 | 1,250 |
8 | 2,360 | ±0,080 | 1,000 |
10 | 2,000 | ±0,070 | 0,900 |
12 | 1,700 | ±0,060 | 0,800 |
14 | 1,400 | ±0,050 | 0,710 |
16 | 1,180 | ±0,045 | 0,630 |
18 | 1,000 | ±0,040 | 0,560 |
20 | 0,850 | ±0,035 | 0,500 |
25 | 0,710 | ±0,030 | 0,450 |
30 | 0,600 | ±0,025 | 0,400 |
35 | 0,500 | ±0,020 | 0,315 |
40 | 0,425 | ±0,019 | 0,280 |
45 | 0,355 | ±0,016 | 0,224 |
50 | 0,300 | ±0,014 | 0,200 |
60 | 0,250 | ±0,012 | 0,160 |
70 | 0,212 | ±0,010 | 0,140 |
100 | 0,150 | ±0,008 | 0,100 |
А.2 Сита изготовляют из проволочных тканых полотен с квадратными ячейками и с плоским плетением.
Для изготовления полотен используют проволоку из нержавеющей стали, латуни, бронзы или других аналогичных материалов без покрытия.
Плетение полотна должно быть жестким, без видимых дефектов.
А.З Средний размер ячейки в свету измеряют, как показано на рисунке А.1, в горизонтальном направлении «х» и вертикальном «у» относительно центра ячейки.
Каждое из измеренных значений должно соответствовать номинальному размеру ячейки в свету с учетом предельно допускаемого отклонения по таблице А.1.
А.4 Средний диаметр проволоки измеряют, как показано на рисунке А.1.
Предельно допускаемое отклонение от номинального диаметра каждого из измеренных значений — не более ±15 % (см. таблицу А.1).

Рисунок А.1 — Схема измерений размеров ячейки и проволоки
А.5 Допускается использовать лабораторные сита из металлической проволочной сетки по ГОСТ Р 51568.
Приложение Б (справочное)
Соответствие номеров сит настоящего стандарта обозначениям сит по ГОСТ Р 51568
Соответствие номеров сит настоящего стандарта обозначениям сит по ГОСТ Р 51568 приведено в таблице Б.1.
Таблица Б.1
Номера сит по настоящему стандарту | Обозначение сита по ГОСТ Р 51568 |
8 | 2,36 мм |
10 | 2 мм |
12 | 1,7 мм |
14 | 1,4 мм |
16 | 1,18 мм |
18 | 1 мм |
20 | 850 мкм |
25 | 710 мкм |
30 | 600 мкм |
35 | 500 мкм |
40 | 425 мкм |
45 | 355 мкм |
50 | 300 мкм |
60 | 250 мкм |
70 | 212 мкм |
100 | 150 мкм |
Примечание — Номинальные размеры ячеек сит по ГОСТ Р 51568 указаны для R 40/3. |
Библиография
[1] | СП 2.6.1.2523-09 | Нормы радиационной безопасности (НРБ-99/2009) |
[2] | СП 2.2.3670-20 | Санитарно-эпидемиологические требования к условиям труда |
[3] | АСТМ Е11-22 | Стандартная спецификация для испытаний проволочной ткани и сит |
УДК 666.762:006.354
ОКС 81.080
Ключевые слова: пропанты магнезиально-кварцевые, гранулированный порошок, фракции, сито, гранулометрический состав, техническое требование, метод испытаний
Редактор Н.В. Таланова Технический редактор И.Е. Черепкова Корректор М.И. Першина Компьютерная верстка М.В. Малеевой
Сдано в набор 14.07.2023. Подписано в печать 24.07.2023. Формат 60х841/8. Гарнитура Ариал. Усл. печ. л. 3,72. Уч.-изд. л. 3,34.
Подготовлено на основе электронной версии, предоставленной разработчиком стандарта
Создано в единичном исполнении в ФГБУ «Институт стандартизации» , 117418 Москва, Нахимовский пр-т, д. 31, к. 2.