ФЕДЕРАЛЬНОЕ АГЕНТСТВО
ПО ТЕХНИЧЕСКОМУ РЕГУЛИРОВАНИЮ И МЕТРОЛОГИИ
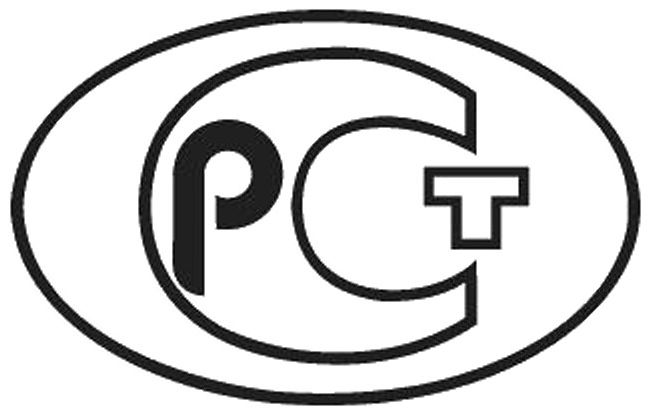
НАЦИОНАЛЬНЫЙ СТАНДАРТ РОССИЙСКОЙ ФЕДЕРАЦИИ
ГОСТ Р 70731.3— 2023
ТРУБЫ СТАЛЬНЫЕ ДЛЯ ИЗГОТОВЛЕНИЯ ОБОРУДОВАНИЯ И ТРУБОПРОВОДОВ АТОМНЫХ СТАНЦИЙ
Общие технические условия
Часть 3
Трубы стальные сварные прямошовные из нелегированной и легированной стали
Издание официальное
Москва
Российский институт стандартизации
2023
ГОСТ Р 70731.3—2023
Предисловие
1 РАЗРАБОТАН Техническим комитетом по стандартизации ТК 357 «Стальные и чугунные трубы и баллоны» и Акционерным обществом «Русский научно-исследовательский институт трубной промышленности» (АО «РусНИТИ»)
2 ВНЕСЕН Техническим комитетом по стандартизации ТК 357 «Стальные и чугунные трубы и баллоны»
3 УТВЕРЖДЕН И ВВЕДЕН В ДЕЙСТВИЕ Приказом Федерального агентства по техническому регулированию и метрологии от 20 октября 2023 г. № 1211-ст
4 ВВЕДЕН ВПЕРВЫЕ
5 ДЕЙСТВУЕТ ВЗАМЕН ПНСТ 454—2020
Правила применения настоящего стандарта установлены в статье 26 Федерального закона от 29 июня 2015 г. № 162-ФЗ «О стандартизации в Российской Федерации». Информация об изменениях к настоящему стандарту публикуется в ежегодном (по состоянию на 1 января текущего года) информационном указателе «Национальные стандарты», а официальный текст изменений и поправок — в ежемесячном информационном указателе «Национальные стандарты». В случае пересмотра (замены) или отмены настоящего стандарта соответствующее уведомление будет опубликовано в ближайшем выпуске ежемесячного информационного указателя «Национальные стандарты». Соответствующая информация, уведомление и тексты размещаются также в информационной системе общего пользования — на официальном сайте Федерального агентства по техническому регулированию и метрологии в сети Интернет (www.rst.gov.ru)
©Оформление. ФГБУ «Институт стандартизации», 2023
Настоящий стандарт не может быть полностью или частично воспроизведен, тиражирован и распространен в качестве официального издания без разрешения Федерального агентства по техническому регулированию и метрологии
II
ГОСТ Р 70731.3—2023
Содержание
1 Область применения..................................................................1
2 Нормативные ссылки..................................................................1
3 Термины и определения................................................................3
4 Обозначения.........................................................................3
5 Сортамент...........................................................................3
6 Предоставляемая информация..........................................................7
7 Технические требования...............................................................7
8 Требования безопасности и охраны окружающей среды....................................15
9 Правила приемки....................................................................15
10 Методы контроля...................................................................18
11 Гарантии изготовителя...............................................................21
Библиография........................................................................22
III
ГОСТ Р 70731.3—2023
Введение
Настоящий стандарт разработан на основе практики применения ПНСТ 454—2020 «Трубы стальные для изготовления оборудования и трубопроводов атомных станций. Общие технические условия. Часть 3. Трубы стальные сварные прямошовные из нелегированной и легированной стали», заменяет ПНСТ 454—2020 и является третьей частью комплекса стандартов на стальные трубы для оборудования и трубопроводов, применяемых на атомных станциях российского проектирования.
Настоящий стандарт разработан в соответствии с Федеральными нормами и правилами в области использования атомной энергии [1], [2], [3], [4], [5] и [6]. Положения настоящего стандарта следует учитывать при разработке новых технических условий и спецификаций на прямошовные сварные трубы, используемые на станциях российского проектирования.
IV
ГОСТ Р 70731.3—2023
НАЦИОНАЛЬНЫЙ СТАНДАРТ РОССИЙСКОЙ ФЕДЕРАЦИИ
ТРУБЫ СТАЛЬНЫЕ ДЛЯ ИЗГОТОВЛЕНИЯ ОБОРУДОВАНИЯ И ТРУБОПРОВОДОВ АТОМНЫХ СТАНЦИЙ
Общие технические условия
Часть 3
Трубы стальные сварные прямошовные из нелегированной и легированной стали
Steel pipes for manufacturing of equipment and piping of nuclear power plants. General specifications. Part 3. Longitudinally welded steel pipes of non-alloy and alloy steels
Дата введения — 2023—12—01
1 Область применения
Настоящий стандарт распространяется на электросварные прямошовные трубы из нелегированных и легированных марок стали, используемые для изготовления оборудования и трубопроводов (за исключением главного циркуляционного трубопровода):
- 2-го и 3-го классов безопасности согласно [1], отнесенных к группе В согласно [3], с расчетной температурой не более 150 °C и давлением не более 1,57 МПа;
- 3-го класса безопасности согласно [1], отнесенных к группе С согласно [3], а также 4-го класса безопасности с давлением не более 2,2 МПа и расчетной температурой:
- не более 350 °C для труб из сталей 20, 22К,
- не более 400 °C для труб из сталей 09Г2С, 16ГС,
- не более 450 °C для труб из сталей 12ХМ, 12X1 МФ,
предназначенные для атомных станций с назначенным сроком эксплуатации до 60 лет.
2 Нормативные ссылки
В настоящем стандарте использованы нормативные ссылки на следующие стандарты:
ГОСТ 3.1109 Единая система технологической документации. Термины и определения основных понятий
ГОСТ 9.014—78 Единая система защиты от коррозии и старения. Временная противокоррозионная защита изделий. Общие требования
ГОСТ 166—89 Штангенциркули. Технические условия
ГОСТ 427—75 Линейки измерительные металлические. Технические условия
ГОСТ 1497—84 Металлы. Методы испытаний на растяжение
ГОСТ 3282 Проволока стальная низкоуглеродистая общего назначения. Технические условия
ГОСТ 3728—78 Трубы. Метод испытания на загиб
ГОСТ 3845—2017 Трубы металлические. Метод испытания внутренним гидростатическим давлением
ГОСТ 5378—88 Угломеры с нониусом. Технические условия
ГОСТ 6507—90 Микрометры. Технические условия
ГОСТ 6996—66 Сварные соединения. Методы определения механических свойств
ГОСТ 7502—98 Рулетки измерительные металлические. Технические условия
ГОСТ 7565—81 (ИСО 377-2—89) Чугун, сталь и сплавы. Метод отбора проб для определения химического состава
ГОСТ 8026—92 Линейки поверочные. Технические условия
ГОСТ 9454—78 Металлы. Метод испытания на ударный изгиб при пониженных, комнатной и повышенных температурах
Издание официальное
1
ГОСТ Р 70731.3—2023
ГОСТ 9651 (ИСО 783—89) Металлы. Методы испытаний на растяжение при повышенных температурах
ГОСТ 10692—2015 Трубы стальные, чугунные и соединительные детали к ним. Приемка, маркировка, упаковка, транспортирование и хранение
ГОСТ 11358—89 Толщиномеры и стенкомеры индикаторные с ценой деления 0,01 и 0,1 мм. Технические условия
ГОСТ 12344 Стали легированные и высоколегированные. Методы определения углерода
ГОСТ 12345 (ИСО 671—82, ИСО 4935—89) Стали легированные и высоколегированные. Методы определения серы
ГОСТ 12346 (ИСО 439—82, ИСО 4829-1—86) Стали легированные и высоколегированные. Методы определения кремния
ГОСТ 12347 Стали легированные и высоколегированные. Методы определения фосфора
ГОСТ 12348 (ИСО 629—82) Стали легированные и высоколегированные. Методы определения марганца
ГОСТ 12350 Стали легированные и высоколегированные. Методы определения хрома
ГОСТ 12351 Стали легированные и высоколегированные. Методы определения ванадия
ГОСТ 12352 Стали легированные и высоколегированные. Методы определения никеля
ГОСТ 12354 Стали легированные и высоколегированные. Методы определения молибдена
ГОСТ 12355 Стали легированные и высоколегированные. Методы определения меди
ГОСТ 12356 Стали легированные и высоколегированные. Методы определения титана
ГОСТ 12357 Стали легированные и высоколегированные. Методы определения алюминия
ГОСТ 12359 (ИСО 4945—77) Стали углеродистые, легированные и высоколегированные. Методы определения азота
ГОСТ 16504 Система государственных испытаний продукции. Испытания и контроль качества продукции. Основные термины и определения
ГОСТ 18895 Сталь. Метод фотоэлектрического спектрального анализа
ГОСТ 19903—2015 Прокат листовой горячекатаный. Сортамент
ГОСТ 21014 Металлопродукция из стали и сплавов. Дефекты поверхности. Термины и определения
ГОСТ 22536.0 Сталь углеродистая и чугун нелегированный. Общие требования к методам анализа
ГОСТ 22536.1 Сталь углеродистая и чугун нелегированный. Методы определения общего углерода и графита
ГОСТ 22536.2 Сталь углеродистая и чугун нелегированный. Методы определения серы
ГОСТ 22536.3 Сталь углеродистая и чугун нелегированный. Методы определения фосфора
ГОСТ 22536.4 Сталь углеродистая и чугун нелегированный. Методы определения кремния
ГОСТ 22536.5 (ИСО 629—82) Сталь углеродистая и чугун нелегированный. Методы определения марганца
ГОСТ 22536.6 Сталь углеродистая и чугун нелегированный. Методы определения мышьяка
ГОСТ 22536.7 Сталь углеродистая и чугун нелегированный. Методы определения хрома
ГОСТ 22536.8 Сталь углеродистая и чугун нелегированный. Методы определения меди
ГОСТ 22536.9 Сталь углеродистая и чугун нелегированный. Методы определения никеля
ГОСТ 22727—88 Прокат листовой. Методы ультразвукового контроля
ГОСТ 26877 Металлопродукция. Методы измерений отклонений формы
ГОСТ 27809 Чугун и сталь. Методы спектрографического анализа
ГОСТ 28548 Трубы стальные. Термины и определения
ГОСТ 30432—96 Трубы металлические. Методы отбора проб, заготовок и образцов для механических и технологических испытаний
ГОСТ 31458 (ISO 10474:2013) Трубы стальные, чугунные и соединительные детали к ним. Документы о приемочном контроле
ГОСТ ISO 10893-6 Трубы стальные бесшовные и сварные. Часть 6. Радиографический контроль сварных швов для обнаружения дефектов
ГОСТ ISO 10893-7 Трубы стальные бесшовные и сварные. Часть 7. Цифровой радиографический контроль сварных швов для обнаружения дефектов
ГОСТ ISO 10893-8 Трубы стальные бесшовные и сварные. Часть 8. Ультразвуковой метод автоматизированного контроля для обнаружения расслоений
ГОСТ Р 8.932 Государственная система обеспечения единства измерений. Требования к методикам (методам) измерений в области использования атомной энергии. Основные положения
ГОСТ Р 50.05.08 Система оценки соответствия в области использования атомной энергии. Оценка соответствия в форме контроля. Унифицированные методики. Визуальный и измерительный контроль 2
ГОСТ Р 70731.3—2023
ГОСТ Р 54153 Сталь. Метод атомно-эмиссионного спектрального анализа
ГОСТ Р ИСО 10893-11 Трубы стальные бесшовные и сварные. Часть 11. Ультразвуковой метод автоматизированного контроля сварных швов для обнаружения продольных и (или) поперечных дефектов
Примечание — При пользовании настоящим стандартом целесообразно проверить действие ссылочных стандартов в информационной системе общего пользования — на официальном сайте Федерального агентства по техническому регулированию и метрологии в сети Интернет или по ежегодному информационному указателю «Национальные стандарты», который опубликован по состоянию на 1 января текущего года, и по выпускам ежемесячного информационного указателя «Национальные стандарты» за текущий год. Если заменен ссылочный стандарт, на который дана недатированная ссылка, то рекомендуется использовать действующую версию этого стандарта с учетом всех внесенных в данную версию изменений. Если заменен ссылочный стандарт, на который дана датированная ссылка, то рекомендуется использовать версию этого стандарта с указанным выше годом утверждения (принятия). Если после утверждения настоящего стандарта в ссылочный стандарт, на который дана датированная ссылка, внесено изменение, затрагивающее положение, на которое дана ссылка, то это положение рекомендуется применять без учета данного изменения. Если ссылочный стандарт отменен без замены, то положение, в котором дана ссылка на него, рекомендуется применять в части, не затрагивающей эту ссылку.
3 Термины и определения
В настоящем стандарте применены термины по ГОСТ 3.1109, ГОСТ 16504, ГОСТ 26877, ГОСТ 28548 и ГОСТ 21014 в отношении дефектов поверхности, а также следующий термин с соответствующим определением:
3.1 головная материаловедческая организация; ГМО: Организация, признанная органом управления использованием атомной энергии компетентной оказывать услуги организациям в сфере ее специализации по выбору и обоснованию применения основных и сварочных материалов, технологий выплавки и разливки металла, термической резки, обработки давлением, сварки, наплавки, термической обработки при конструировании, изготовлении, монтаже и эксплуатации оборудования и трубопроводов атомных энергетических установок.
4 Обозначения
В настоящем стандарте использованы следующие обозначения:
D — номинальный наружный диаметр трубы, мм;
KCV — ударная вязкость при испытании на образцах с V-образным надрезом, Дж/см2;
KCU — ударная вязкость при испытании на образцах с U-образным надрезом, Дж/см2;
L — длина трубы, мм;
S — номинальная толщина стенки трубы, мм;
Scp — среднеарифметическое значение толщины стенки трубы с учетом несимметричности предельных отклонений, мм;
0 — овальность концов труб;
р — плотность металла, г/см3;
aB(Rm) — временное сопротивление, Н/мм2;
о0 2^Ро 2) — предел текучести, Н/мм2;
35(Д) — относительное удлинение после разрыва, %;
y(Z) — относительное сужение после разрыва, %.
5 Сортамент
5.1 Виды труб
Трубы изготовляют прямошовными с одним или двумя продольными сварными швами.
5.2 Марки стали
Трубы изготовляют из нелегированной стали марок 20, 22К и легированной стали марок 09Г2С, 16ГС, 12ХМ и 12Х1МФ.
5.3 Размеры
5.3.1 Трубы изготовляют с размерами наружного диаметра и толщины стенки, указанными в таблице 1.
3
ГОСТ Р 70731.3—2023
5.3.2 По согласованию между изготовителем и заказчиком допускается изготовление труб других размеров в пределах, указанных в таблице 1.
5.3.3 По требованию заказчика трубы могут изготавливаться по внутреннему диаметру и толщине стенки (опция 1).
5.3.4 По длине трубы изготовляют:
а) немерной длины — от 1000 до 12 000 мм включительно;
б) мерной длины — в пределах немерной длины.
По согласованию между изготовителем и заказчиком допускается изготавливать трубы номинальной длиной более 12 000 мм.
5.3.5 Теоретическую массу одного погонного метра трубы М, кг/м, определяют по формуле (1) с использованием номинального значения наружного диаметра и среднеарифметического значения толщины стенки:
М =——-(О-5гп)-5ГП'р, (1)
1000 v ср/ ср
где тс — число Пи, принятое равным 3,14159;
р — плотность металла, г/см3, принимаемая на основании стандартных справочных данных.
Примечание — Номинальные значения толщины стенки, длины и наружного диаметра труб указаны с точностью до целого или десятых долей, при этом требования к точности изготовления труб установлены в 0. Под номинальными значениями диаметра, толщины стенки и длины в рамках настоящего стандарта следует понимать все значения указанных величин, кроме фактически измеренных на готовых изделиях.
4
Таблица 1 — Размеры сварных труб из нелегированной и легированной стали
Наружный диаметр, мм | Толщина стенки, мм | |||||||||||||||||||||||||||
Исполнение 1 | Исполнение 2 | 6,0 | 6,3 | 7,0 | 7,1 | 8,0 | 8,8 | 9,0 | 10,0 | 11,0 | 12,0 | 12,5 | 13,0 | 14,0 | 14,2 | 15,0 | 16,0 | 17,0 | 17,5 | 18,0 | 19,0 | 20,0 | 21,0 | 22,0 | 22,2 | 23,0 | 24,0 | 25,0 |
133,0 | ||||||||||||||||||||||||||||
139,7 | ||||||||||||||||||||||||||||
152,4 | ||||||||||||||||||||||||||||
159,0 | ||||||||||||||||||||||||||||
168,3 | ||||||||||||||||||||||||||||
177,8 | ||||||||||||||||||||||||||||
193,7 | ||||||||||||||||||||||||||||
219,1 | ||||||||||||||||||||||||||||
244,5 | ||||||||||||||||||||||||||||
273,0 | ||||||||||||||||||||||||||||
323,9 | ||||||||||||||||||||||||||||
355,6 | ||||||||||||||||||||||||||||
406,4 | ||||||||||||||||||||||||||||
426,0 | ||||||||||||||||||||||||||||
457,0 | ||||||||||||||||||||||||||||
508,0 | ||||||||||||||||||||||||||||
530,0 | ||||||||||||||||||||||||||||
559,0 | ||||||||||||||||||||||||||||
610,0 | ||||||||||||||||||||||||||||
630,0 | ||||||||||||||||||||||||||||
660,0 | ||||||||||||||||||||||||||||
711,0 | ||||||||||||||||||||||||||||
720,0 |
ГОСТ Р 70731.3—2023
° Окончание таблицы 1
Наружный диаметр, мм | Толщина стенки, мм | |||||||||||||||||||||||||||
Исполнение 1 | Исполнение 2 | 6,0 | 6,3 | 7,0 | 7,1 | 8,0 | 8,8 | 9,0 | 10,0 | 11,0 | 12,0 | 12,5 | 13,0 | 14,0 | 14,2 | 15,0 | 16,0 | 17,0 | 17,5 | 18,0 | 19,0 | 20,0 | 21,0 | 22,0 | 22,2 | 23,0 | 24,0 | 25,0 |
762,0 | ||||||||||||||||||||||||||||
813,0 | ||||||||||||||||||||||||||||
820,0 | ||||||||||||||||||||||||||||
864,0 | ||||||||||||||||||||||||||||
914,0 | ||||||||||||||||||||||||||||
920,0 | ||||||||||||||||||||||||||||
1016,0 | ||||||||||||||||||||||||||||
1020,0 | ||||||||||||||||||||||||||||
1118,0 | ||||||||||||||||||||||||||||
1219,0 | ||||||||||||||||||||||||||||
1220,0 | ||||||||||||||||||||||||||||
1420,0 | ||||||||||||||||||||||||||||
1422,0 | ||||||||||||||||||||||||||||
1620,0 | ||||||||||||||||||||||||||||
1626,0 |
ГОСТ Р 70731.3—2023
ГОСТ Р 70731.3—2023
6 Предоставляемая информация
6.1 Обязательная информация
При оформлении заказа на трубы заказчик должен указать следующие обязательные сведения:
- количество (например, общая масса или общая длина труб либо общее количество в штуках);
- марка стали — см. 5.2;
- номинальный размер (наружный диаметр, толщина стенки) — см. 5.3.1;
- вид длины (мерная, с указанием меры, немерная) — см. 5.3.4;
- категория труб (1 или 2) — см. 9.1.2 и 9.1.3.
6.2 Дополнительная информация
В настоящем стандарте предусмотрен ряд дополнительных требований (опций), которые описаны ниже. Если заказчик при заказе не указывает дополнительных требований, трубы изготовляют с учетом обязательной информации и обязательных испытаний в соответствии с 6.1, 9.1.2 и 9.1.3.
Дополнительные требования (опции):
- поставка труб по внутреннему диаметру и толщине стенки (опция 1) — см. 5.3.3;
- определение химического состава металла готовых труб (опция 2) — см. 7.4.2;
- определение механических свойств основного металла при повышенной (расчетной) температуре (опция 3) — см. 7.4.6;
- испытания на ударный изгиб основного металла труб при отрицательных температурах (опция 4) — см. 7.4.7;
- определение механических свойств сварного соединения труб при повышенной (расчетной) температуре (опция 5) — см. 7.5.2;
- испытания на ударный изгиб сварного соединения труб при отрицательных температурах (опция 6) — см. 7.5.3;
- ультразвуковой контроль (УЗК) торцов труб на наличие расслоений (опция 7) — см. 7.8.1;
- радиографический контроль сварного соединения (опция 8) — см. 7.9.1;
- контроль наружного диаметра по длине трубы (опция 9) — см. 7.10.2;
- поставка труб со снятыми фасками (опция 10) — см. 7.10.10;
- поставка труб с концами, закрытыми предохранительными пробками, заглушками или колпачками (опция 11) — см. 7.11.6;
- консервация труб (опция 12) — см. 7.11.7;
- условия сдачи труб — поштучно (опция 13) — см. 9.1.1.
6.3 Примеры условных обозначений труб
Трубы сварные одношовные с номинальным наружным диаметром 219,1 мм, номинальной толщиной стенки 8,8 мм, мерной длиной 8000 мм, из стали марки 22К, категория труб 2:
Труба — С1 — 219,1 *8,8 * 8000—22К—2— ГОСТР 70731.3—2023
Трубы сварные двухшовные с номинальным наружным диаметром 1420,0 мм, номинальной толщиной стенки 24,0 мм, немерной длины, из стали марки 16ГС, категория труб 1, с определением механических свойств при повышенной температуре основного металла и сварного соединения (опции 3, 5), с закрытыми предохранительными пробками концами (опция 11) и консервационным покрытием труб (опция 12):
Труба—С2—1420,0 *24,0— 16ГС— 1 — 0.3,5,11,12 — ГОСТР 70731.3—2023
Трубы сварные одношовные с номинальным внутренним диаметром 600,0 мм, номинальной толщиной стенки 15,0 мм (опция 1), мерной длины 12 000 мм, из стали марки 12X1 МФ, категория труб 2, с определением химического состава готовых труб (опция 2), с испытанием на ударный изгиб основного металла и сварного соединения труб при отрицательных температурах (опции 4, 6), контроль наружного диаметра по длине трубы (опция 9), с поштучной приемкой (опция 13):
Труба — С1 — вн 600*15*12 000— 12Х1МФ—2—0.1,2,4,6,9,13 —ГОСТР 70731.3—2023
7 Технические требования
7.1 Способ производства
7.1.1 Трубы изготовляют из горячекатаного листового проката методом холодной формовки с последующей автоматической аргонодуговой сваркой или автоматической сваркой под флюсом.
7
ГОСТ Р 70731.3—2023
7.1.2 До начала исполнения заказа изготовитель предъявляет заказчику результаты контрольной проверки технологии производства труб.
Примечание — Контрольную проверку соответствия технологии производства труб требованиям настоящего стандарта в части обеспечения требуемого уровня качества продукции организует и проводит изготовитель с привлечением ГМО не реже одного раза в три года.
7.2 Требования к листовому прокату
7.2.1 Требования к форме, размерам и допускам горячекатаного листового проката устанавливает изготовитель трубы.
7.2.2 Химический состав стали (по плавочному анализу металла ковшевой пробы) должен соответствовать характеристикам, приведенным в таблице 2.
7.2.3 Листы поставляют в термически обработанном состоянии. Допускается нормализация листов из стали 20, 22К, 16ГС и 09Г2С с деформационного нагрева.
7.2.4 Механические свойства листов при комнатной температуре в состоянии поставки должны соответствовать характеристикам, приведенным в таблице 3.
7.2.5 Предел текучести листового проката при повышенной температуре должен соответствовать характеристикам, приведенным в таблице 4.
7.2.6 Ударная вязкость листов при отрицательных температурах должна соответствовать характеристикам, приведенным в таблице 5.
7.2.7 Листы должны выдерживать испытания на изгиб в холодном состоянии на угол 180°, определяемый визуально без использования средств измерения.
7.2.7.1 Номинальное значение толщины оправки должно быть приблизительно в два раза больше номинального значения толщины листа.
7.2.7.2 Образец считается выдержавшим испытание, если в месте изгиба отсутствуют трещины и расслоения, видимые невооруженным глазом.
7.2.8 На поверхности листов допускается тонкий слой неотстающей окалины, не препятствующий выявлению поверхностных недопустимых несплошностей: трещин, плен, раскатанных пузырей и вкатанной окалины.
8
Таблица 2 — Химический состав и предельные отклонения в листах и трубах
Марка стали | Углерод | Массовая доля элемент Кремний Марганец Хром Никель Молибден | ов. % Медь Сера Фосфор Ванадий -------------------------- Не более | Зару- Мышьяк Азот бежные’) ___________________ стали-ана- логи |
20 | 0,17—0,24 | Не более 0,17—0,37 0,35—0,65 --------------------- — 0,25 0,30 | — 0,30 0,040 0,035 | |
Допускаемые отклонения в металле листов | и в основном металле труб | Г I | ||
±0,01 | ±0,02 ±0,03 | +0,005 | — — | |
22 К | 0,19—0,26 | Не более 0,17—0,40 0,70—1,0 --------------------- — 0,30 0,30 | — 0,30 0,035 0,040 | 0,08 0,012 |
+0,03 -0,02 | Допускаемые отклонения в металле листов +0,03 +0,05 -0,02 -0,03 | и в основном металле труб — — +0,005 +0,005 | — — | |
16ГС | 0,12—0,18 | Не более 0,4—0,7 0,9—1,2 --------------------- — 0,30 0,30 Допускаемые отклонения в металле листов | — 0,30 0,035 0,040 и в основном металле труб | 0,08 0,012 |
±0,02 | ±0,05 ±0,10 ±0,05 | +0,005 +0,005 | — — | |
09Г2С | Не более 0,12 | Не более 0,5—0,8 1,3—1,7 --------------------- — 0,30 0,30 | — 0,30 0,040 0,035 | 0,08 0,012 |
±0,02 | Допускаемые отклонения в металле листов ±0,05 ±0,10 ±0,05 | и в основном металле труб — — +0,005 +0,005 | — — | |
12ХМ | Не более 0,16 | 0,17—0,37 0,4—0,7 0,8—1,10 ^qzq^ 0,40—0,55 | — — — 0,025 | — — |
±0,01 | Допускаемые отклонения в металле листов ±0,02 ±0,02 ±0,05 — ±0,02 | и в основном металле труб — — +0,005 +0,005 | 13СгМо4-5 | |
12X1 МФ | 0,08—0,15 | 0,17—0,37 0,4—0,7 0,9—1,2 ^^3^ 0,25—0,35 | 0,15—0,30 0,20 0,025 0,025 | — — |
Допускаемые отклонения в металле листов | и в основном металле труб | — | ||
±0,01 | ±0,02 ±0,02 ±0,05 — ±0,02 | ±0,02 — +0,005 +0,005 | — — |
1) Применение материалов осуществляется в соответствии с Федеральными нормами и правилами в области использования атомной энергии.
Примечание — Прочерк означает, что легирование данным химическим элементом не предусмотрено.
ГОСТ Р 70731.3—2023
ГОСТ Р 70731.3—2023
Таблица 3 — Механические свойства листов, основного металла и сварных соединений при комнатной температуре
Марка стали | Номинальная толщина, мм | Режим термической обработки | о8, Н/мм2 | СТ0,2’ H/mmz | 35. % | кси, Дж/см2 | KCU после механического старения, Дж/см2 |
Не менее | |||||||
20 | До 25 | Нормализация | 400—550 | 230 | 28 | 25 | 29 |
22К | До 25 | 430—590 | 265 | 20 | 69* | ||
16ГС | До Ю | Не менее 490 | 325 | 21 | 59 | ||
Св. 10 до 20 | Не менее 480 | 315 | |||||
Св. 20 до 25 | Не менее 470 | 295 | |||||
09Г2С | До Ю | Не менее 490 | 345 | 21 | 59 | ||
Св. 10 до 20 | Не менее 470 | 325 | |||||
Св. 20 до 25 | Не менее 460 | 305 | |||||
12ХМ | До 25 | Нормализация с отпуском | 430—550 | 245 | 22 | 59 | |
12X1 МФ | 440—590 | 295 | 21 | 79 |
Значение ударной вязкости на образцах типа KCV.
Таблица 4 — Предел текучести листового проката, основного металла и сварных соединений при расчетной температуре
Температура испытания, °C | Марка стали | |||||
20 | 22К | 16ГС | 09Г2С | 12ХМ | 12X1 МФ | |
о'0 2- Н/мм2, не менее | ||||||
100 | 206 | 196 | 235 | 235 | 235 | 255 |
150 | 206 | 186 | 226 | 226 | 235 | 255 |
200 | 196 | 186 | 216 | 216 | 226 | 255 |
250 | 196 | 186 | 216 | 216 | 226 | 245 |
300 | 177 | 186 | 196 | 196 | 216 | 235 |
350 | 157 | 177 | 177 | 176 | 206 | 226 |
Таблица 5 — Ударная вязкость листов, основного металла и сварных соединений при отрицательных температурах
Марка стали | Номинальная толщина листа, мм | KCU при температуре | |||
—10 °C | —20 °C | —40 °C | —70 °C | ||
не менее, Дж/см2 | |||||
20 | До 25 | — | 29 | — | — |
22К | От 20 до 25 | — | — | — | — |
16ГС | До Ю | — | — | 39 | 29 |
Св. 10 до 20 | — | — | 29 | 24 | |
Св. 20 до 25 | — | — |
10
Окончание таблицы 5
ГОСТ Р 70731.3—2023
Марка стали | Номинальная толщина листа, мм | KCU при температуре | |||
—10 °C | —20 °C | —40 °C | —70 °C | ||
не менее, Дж/см2 | |||||
09Г2С | До 10 | — | — | 34 | 29 |
Св.10 до 20 | — | — | |||
Св. 20 до 25 | 49* | — |
* Значение ударной вязкости на образцах с V-образным надрезом.
Примечание — Прочерк означает, что легирование данным химическим элементом не предусмотрено.
7.2.9 На поверхности листов допускаются без зачистки отдельные забоины, риски, царапины, если их глубина не выводит толщину листа за допустимые пределы.
7.2.10 Ремонт листового проката с применением сварки не допускается.
7.2.11 Каждый лист должен быть проконтролирован методом ультразвуковой дефектоскопии (УЗК). Норма сплошности по всей площади проката — класс 1 (приложение 4 ГОСТ 22727—88), настройка чувствительности контроля — D53 (приложение 4 ГОСТ 22727—88). Норма сплошности листов по продольным и поперечным прикромочным зонам (шириной не менее 50 мм) — в соответствии с нормами, установленными для III категории сварных соединений по [4].
7.3 Требования к сварке
7.3.1 Сварочные материалы, подготовка кромок листов под сварку и выполнение сварных соединений должны отвечать требованиям [4].
7.3.2 Проверка качества сварочных материалов должна выполняться в соответствии с требованиями [5].
7.3.3 Химический состав наплавленного металла и механические свойства металла шва должны соответствовать нормам, установленным [5]. Сварочные материалы должны соответствовать требованиям [4].
7.4 Требования к основному металлу труб
7.4.1 Химический состав металла труб принимается по сертификатным данным на листовой прокат и должен соответствовать характеристикам, приведенным в таблице 2.
7.4.2 По требованию заказчика (опция 2) выполняется контроль химического состава металла труб, результаты которого должны отвечать требованиям таблицы 3, установленным для марки стали, с учетом допускаемых отклонений.
7.4.3 Трубы из легированных марок стали должны пройти качественную оценку наличия легирующих химических элементов.
7.4.4 Термической обработке подлежат трубы в соответствии с таблицей 6.
Таблица 6 — Трубы, подлежащие отпуску
Трубы из стали | Номинальная толщина, мм | Температура отпуска, °C |
12ХМ | Св. 10 | 710±20 |
12X1 МФ | Св. 6 | 730±20 |
7.4.5 Механические свойства основного металла труб при испытании на растяжение и ударный изгиб при комнатной температуре должны соответствовать характеристикам, приведенным в таблице 3.
7.4.6 По требованию заказчика (опция 3) предел текучести основного металла труб, предназначенных для изготовления трубопроводов, при расчетной температуре должен соответствовать характеристикам, приведенным в таблице 4.
7.4.7 По требованию заказчика (опция 4) ударная вязкость основного металла труб при отрицательных температурах должна соответствовать характеристикам, приведенным в таблице 5.
11
ГОСТ Р 70731.3—2023
7.4.8 Основной металл труб должен выдерживать испытание на загиб (изгиб) на образце в виде полосы. При загибе (изгибе) образца до заданного угла 90° (определяемого визуально без использования средств измерения) на его поверхности не должно быть трещин и расслоений, видимых при визуальном контроле.
7.5 Требования к сварным соединениям
7.5.1 Требования к качеству сварного соединения при визуальном и измерительном контроле установлены в соответствии с нормами, принятыми для III категории сварных соединений по [5].
7.5.2 Механические свойства сварного соединения при испытании на растяжение и ударный изгиб при комнатной температуре должны отвечать требованиям таблицы 4, а при дополнительном требовании при повышенной температуре — требованиям таблицы 5 (опция 5).
7.5.3 По требованию заказчика (опция 6) должно быть обеспечено соответствие ударной вязкости сварного соединения при отрицательных температурах характеристикам, приведенным в таблице 5.
7.5.4 При испытании на статический изгиб сварного соединения труб номинальной толщиной не более 20 мм номинальный угол изгиба должен быть не менее 160°, номинальной толщиной более 20 мм — не менее 120°.
Результаты испытаний считаются удовлетворительными, если при достижении заданного угла изгиба на растянутой стороне и на кромках образца не возникло трещин длиной более 20 % от номинальной ширины образца при его номинальной ширине не более 25 мм и не более 5 мм при номинальной ширине образца более 25 мм.
Примечание — В рамках настоящего стандарта под длиной трещины понимается кратчайшее расстояние между двумя крайними точками трещины.
7.5.5 Допускается ремонт дефектных мест сварных швов сваркой при условии их суммарной протяженности не более 10 % от длины трубы.
7.5.5.1 Исправление выявленных дефектов производится в соответствии с производственно-технологической документацией (технологической инструкцией), разработанной в соответствии с [4].
7.5.5.2 Не допускается проведение ремонта дефектных мест между дефектом внутреннего и наружного швов, находящихся на расстоянии менее 100 мм.
7.5.5.3 Ремонт сваркой в одном и том же месте сварного шва допускается проводить не более двух раз.
7.5.5.4 Все отремонтированные сваркой участки сварного шва должны быть подвергнуты тем же методам контроля, которыми был выявлен дефект.
7.6 Состояние поверхности труб
7.6.1 Поверхность основного металла труб должна отвечать требованиям, предъявляемым к исходному листовому прокату (см. 7.2.8, 7.2.9, 7.2.10).
7.6.2 На внутренней и наружной поверхностях труб допускаются риски и следы от технологического инструмента глубиной не более 0,2 мм, а также следы зачистки, не выводящие толщину стенки трубы за допустимые пределы.
7.6.3 На торцах труб расслоения не допускаются; торцы труб должны быть свободны от заусенцев.
7.6.4 Допускается удаление дефектов механическим способом абразивным инструментом. Все исправленные места должны плавно сопрягаться с поверхностью трубы.
7.7 Контроль герметичности
Трубы должны выдерживать испытательное давление, рассчитанное по пункту 6.2 ГОСТ 3845—2017, при расчете значение R принимается равным О,9о0 2 (значения о0 2 для каждой марки стали приведены в таблице 3).
7.8 Ультразвуковой контроль
7.8.1 По требованию заказчика качественный контроль концов труб ультразвуковым методом на расслоение выполняют на номинальной длине не менее 200 мм в соответствии с 10.7.2 (опция 7).
7.8.2 Сварное соединение должно подвергаться УЗК по всей длине трубы в соответствии с 10.7.3.
12
ГОСТ Р 70731.3—2023
7.9 Радиографический контроль
7.9.1 По требованию заказчика качественному радиографическому контролю подвергается весь сварной шов в соответствии с 10.8.1 (опция 8).
7.9.2 Обязательному качественному радиографическому контролю подлежат:
-дефектные участки продольных швов, выявленные при УЗК;
- участки сварных швов после ремонта сваркой.
Результаты контроля радиографическим методом являются окончательными.
7.9.3 Контроль радиографическим методом выполняют после испытаний труб внутренним гидростатическим давлением.
7.9.4 При контроле радиографическим методом сварное соединение должно отвечать требованиям, установленным [5] для III категории сварных соединений.
7.9.5 По согласованию между изготовителем и заказчиком радиографический контроль по 10.8.1 может быть заменен на цифровой радиографический контроль по 10.8.2.
7.10 Предельные отклонения размеров, длины и формы
7.10.1 Отклонения наружного диаметра труб по концам не должны быть более предельных отклонений, установленных в таблице 7.
Таблица 7 — Предельные отклонения наружного диаметра
Номинальный наружный диаметр трубы, мм | Предельное отклонение наружного диаметра, мм | |
по концам трубы (на длине не менее 100 мм от торца) | корпуса трубы | |
До 457 включ. | ±2,0 | ±2,5 |
Св. 457 до 630 включ. | ±2,5 | ±3,0 |
Св. 630 | ±3,0 | ±4,0 |
Примечание — Контроль наружного диаметра по длине корпуса трубы выполняется в качестве дополнительного требования (опция 8). |
7.10.2 По требованию заказчика контроль наружного диаметра на соответствие требованиям таблицы 8 выполняется на всей длине трубы (опция 9).
7.10.3 По согласованию между изготовителем и заказчиком трубы могут изготавливать с предельными отклонениями по наружному периметру трубы, рассчитанному по 7.10.3.2.
7.10.3.1 Отклонения наружного периметра труб по концам не должны быть более:
- ±3,0 мм для диаметра не более 426 мм;
- ±4,0 мм для диаметра более 426 мм, но не более 1220 мм;
- ±5,0 мм для диаметра более 1220 мм.
7.10.3.2 Номинальный наружный периметр трубы QH> мм, рассчитывается по формуле (2) и округляется до одного знака после запятой
QH = nD. (2)
7.10.4 Предельные отклонения толщины стенки должны соответствовать таблице 3, подраздел 2.3, ГОСТ 19903—2015 для толщин не более 13 мм, таблице 4, подраздел 2.3, ГОСТ 19903—2015 для толщин более 13 мм для листов обычной точности прокатки с учетом их ширины.
7.10.5 Предельные отклонения длины труб мерной длины:
- до 6000 мм включительно — +5/0 мм;
- св. 6000 мм — +10/0 мм;
- св. 12 000 мм — по согласованию с заказчиком.
7.10.6 Отклонение от прямолинейности по всей длине трубы L не должно превышать 0,15 % от L.
7.10.7 Отклонение от прямолинейности любого участка трубы длиной 1000 мм должно быть не более 3 мм.
7.10.8 Овальность концов труб не должна превышать 1 %.
7.10.9 Торцы труб должны быть перпендикулярны образующей трубы.
13
ГОСТ Р 70731.3—2023
7.10.9.1 Косина реза не должна превышать:
- для труб номинальным диаметром менее 1020 мм — 1,6 мм;
- для труб номинальным диаметром не менее 1020 мм — 2,0 мм.
7.10.9.2 Изготовитель гарантирует соответствие косины реза указанным требованиям без проведения контроля.
7.10.10 Трубы номинальным диаметром не более 720 мм по требованию заказчика поставляют со снятыми фасками (опция 10) (см. рисунок 1). При номинальной толщине стенки трубы не более 20 мм угол О+5
скоса кромки а должен быть равным ЗО°о с поверхностью С, равной (1,6 ± 0,8) мм, при толщине стенки трубы более 20 мм угол скоса устанавливается по согласованию между изготовителем и заказчиком.
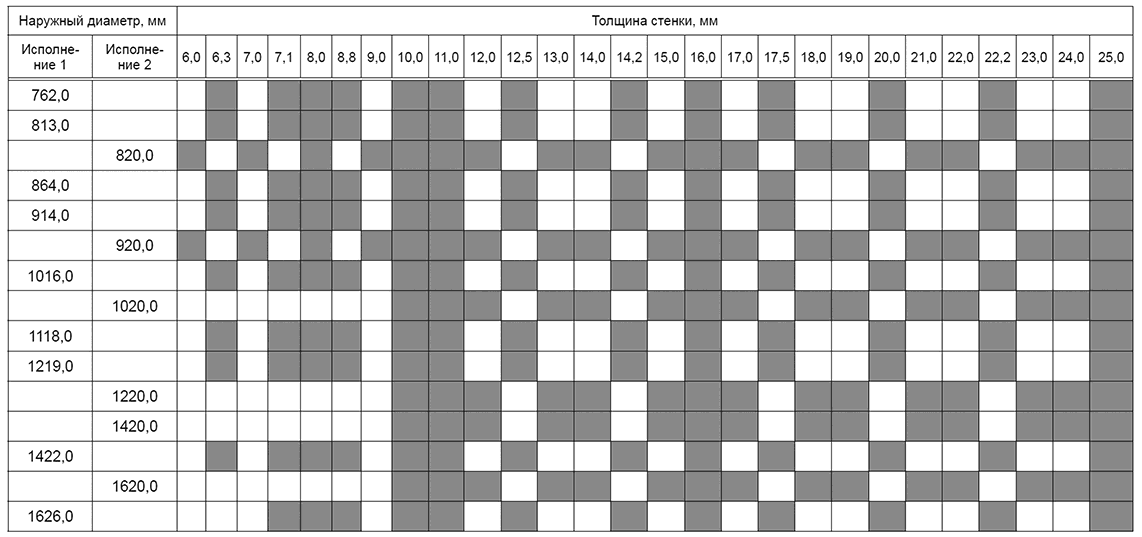
Рисунок 1 — Способ исполнения фаски
Допускается увеличение притупления фаски на концах труб в районе сварного шва (не более 40 мм по обе стороны шва) на величину усиления шва.
7.11 Маркировка, упаковка, транспортирование и хранение
7.11.1 Общие требования к маркировке, упаковке, транспортированию и хранению труб должны соответствовать разделам 5, 6, 7 и 8 ГОСТ 10692—2015 соответственно, условиям заказа (опции 11, 12) и требованиям настоящего раздела.
7.11.2 На наружной поверхности каждой трубы на расстоянии 300—400 мм от одного из торцов и 100—150 мм от сварного шва должна быть нанесена маркировка, содержащая:
- товарный знак или условное обозначение изготовителя;
- знак технического контроля (ТК);
- номер трубы;
- размер трубы (наружный или внутренний номинальный диаметр и номинальная толщина стенки);
- марку стали.
7.11.3 Способ маркировки выбирает изготовитель.
7.11.3.1 Изготовитель должен обеспечить качество выполнения и сохранность маркировки при транспортировании и хранении труб в течение 6 мес при условии соблюдения требований к транспортированию и хранению.
7.11.3.2 По согласованию между изготовителем и заказчиком может быть выполнена дополнительная маркировка труб.
7.11.4 Допускается наличие маркировки на внутренней поверхности труб.
7.11.5 Трубы упаковываются поштучно. Каждую трубу обкладывают досками и обвязывают проволокой любого типа и технических характеристик в рамках требований ГОСТ 3282 не менее чем в трех местах по длине трубы.
7.11.6 По требованию заказчика (опция 11) концы труб должны быть плотно закрыты специальными предохранительными пробками, заглушками или колпачками.
7.11.7 По требованию заказчика (опция 12) для защиты от воздействия окружающей среды на поверхность труб должно быть нанесено временное консервационное покрытие, обеспечивающее защиту поверхности труб при транспортировании и хранении сроком до 6 мес.
7.11.8 Способы нанесения и удаления консервационного покрытия должны соответствовать приложению 3 ГОСТ 9.014—78.
14
ГОСТ Р 70731.3—2023
8 Требования безопасности и охраны окружающей среды
Стальные трубы пожаробезопасны, взрывобезопасны, нетоксичны и не требуют специальных мер при транспортировании, хранении и переработке.
Осуществление специальных мер по охране окружающей среды не требуется.
9 Правила приемки
9.1 Общие положения
9.1.1 Контроль и сдачу труб в соответствии с заказом производят партией или по требованию заказчика поштучно (опция 13).
Партия формируется из труб одного номинального диаметра и толщины стенки, одной плавки и одного процесса изготовления. Количество труб в партии не должно превышать 100 шт.
9.1.2 Для проверки соответствия труб, сдаваемых партией, требованиям настоящего стандарта изготовитель проводит приемочные испытания, вид и объем которых в зависимости от категории труб 1 или категории труб 2 приведен в таблице 8.
9.1.3 Для проверки соответствия труб, сдаваемых поштучно, требованиям настоящего стандарта изготовитель проводит все виды обязательных и дополнительных (в соответствии с заказом) испытаний, приведенные в таблице 8 для категории труб 2.
9.1.4 При получении неудовлетворительных результатов хотя бы по одному из видов контроля по нему проводят повторный контроль на удвоенном количестве труб, отобранных от той же партии.
9.1.4.1 Удовлетворительные результаты повторного контроля распространяются на всю партию, исключая трубы, не выдержавшие испытаний.
9.1.4.2 При получении неудовлетворительных результатов повторного контроля хотя бы одного образца все трубы партии, за исключением труб, не выдержавших испытания, подвергают данному контролю.
9.1.5 При получении неудовлетворительных результатов хотя бы по одному из видов контроля при поштучной приемке, труба, для которой получены неудовлетворительные результаты, бракуется или подвергается переработке с последующей повторной приемкой.
9.1.6 Оценка соответствия труб в форме контроля при их изготовлении должна выполняться в соответствии с [2].
Таблица 8 — Виды контроля, норма отбора труб и образцов
Требования к выполнению испытаний | Виды испытания | Номер пункта | Норма отбора1) труб от партии при категории | Норма отбора образцов от каждой отобранной трубы | ||
технических требований | требований к методике | 1 | 2 | |||
Обязательные испытания | Контроль химического состава по результатам плавочного анализа: - основной металл - наплавленный металл | 7.3.3 7.4.1 | 10.3 | Одна проба от плавки | — | |
Контроль на наличие легирующих элементов в металле труб | 7.4.3 | 10.3.5 | 100 % | — | ||
Испытание на растяжение при комнатной температуре: - основной металл - сварное соединение - металл шва | 7.3.3 7.4.5 7.5.2 | 10.4.1, 10.4.3 | Две | 5 %, но не менее трех труб | Один | |
Испытание на ударный изгиб при комнатной температуре: - основной металл - сварное соединение | 7.4.5 7.5.2 | 10.4.2, 10.4.3 | Две | 5 %, но не менее трех труб | Три |
15
ГОСТ Р 70731.3—2023
Окончание таблицы 8
Требования к выполнению испытаний | Виды испытания | Номер пункта | Норма отбора1) труб от партии при категории | Норма отбора образцов от каждой отобранной трубы | ||
технических требований | требований к методике | 1 | 2 | |||
Обязательные испытания | Испытание основного металла на загиб (изгиб) | 7.4.8 | 10.5 | Одна | 10 %, но не менее одной трубы | Один |
Испытание сварного соединения на статический изгиб | 7.5.4 | 10.5 | Одна | 10 %, но не менее одной трубы | Один | |
Контроль: - диаметра, наружного периметра (в соответствии с заказом) - толщины стенки - длины - овальности - отклонения от прямолинейности по всей длине трубы - отделки концов | 7.10.1, 7.10.3— 7.10.9 | 10.2.1— 10.2.4 10.2 | 100 % | |||
Измерительный контроль сварного соединения | 7.5.1 | 10.2.1— 10.2.2 | ||||
Контроль состояния поверхности | 7.5.1, 7.6 | 10.1 | ||||
УЗК основного металла | 7.2.11 | 10.7.1 | ||||
УЗК сварного соединения | 7.8.2 | 10.7.3 | ||||
Контроль герметичности | 7.7 | 10.6 | ||||
Дополнительные испытания (опции) | Определение химического состава готовых труб (опция 2) | 7.4.2 | 10.3 | — | Две | Один |
Определение механических2) свойств при испытании на растяжение при повышенной температуре с определением о0 2, (Rp0 2): - основной металл (опция 3) - сварное соединение (опция 5) | 7.4.6 7.5.2 | 10.4.1, 10.4.3 | Две | 5 %, но не менее трех труб | Два | |
Испытания на ударный изгиб сварного соединения труб при отрицательных температурах: - основной металл (опция 4) - сварное соединение (опция 6) | 7.4.7 7.5.3 | 10.4.2, 10.4.3 | Две | 5 %, но не менее трех труб | Три | |
УЗК концов труб для выявления расслоений(опция 7) | 7.8.1 | 10.7.2 | — | 100 % | — | |
Радиографический контроль сварного соединения (опция 8) | 7.9.1 | 10.8 | 100 % | — | ||
Измерительный контроль труб: - наружного диаметра по длине корпуса трубы (опция 9) | 7.10.2 | 10.2.2, 10.2.3 | — | 100 % | — | |
Снятие фаски (опция 10) | 7.10.10 | 10.2.2 | — | 100 % | — |
1>100 % означает, что конкретному испытанию подвергается каждая труба партии, 5 % (10 %) означает, что для проведения испытаний отбирается 5 % (10 %) от общего количества труб, при расчете значение округляется до целого.
2) Заказывается для трубопроводов с расчетной температурой свыше 100 °C.
16
ГОСТ Р 70731.3—2023
9.2 Отбор проб
9.2.1 Пробы для определения химического состава металла готовых труб отбирают согласно требованиям раздела 3 ГОСТ 7565—81 от образцов для механических испытаний или от трубы в том же месте, где отбираются пробы для механических испытаний.
9.2.2 Пробы для контроля механических свойств отбирают от конца трубы.
9.2.3 Вырезку образцов для механических испытаний производят в соответствии с разделом 4 ГОСТ 30432—96, для испытаний технологических свойств — в соответствии с разделом 5 ГОСТ 30432—96:
- из основного металла — перпендикулярно оси трубы;
- из сварного соединения — перпендикулярно сварному шву.
9.2.4 Если размер труб не позволяет изготовить из основного металла трубы тангенциальные образцы, испытание проводят на продольных образцах.
9.2.5 При изготовлении образцов для механических испытаний сварных соединений допускается правка образцов с использованием статической нагрузки при условии, что данная правка не затрагивает рабочую часть образца.
9.2.6 Испытания на растяжение основного металла выполняют:
- при комнатной температуре — на плоских пропорциональных образцах по ГОСТ 1497—84 (приложение 3) или цилиндрических образцах по ГОСТ 1497—84 (приложение 2);
- при повышенной температуре — на плоских пропорциональных или цилиндрических образцах по ГОСТ 9651.
9.2.7 Образцы для испытания на ударный изгиб изготовляют в соответствии с разделом 1 ГОСТ 9454—78 типов 1, 11 для труб номинальной толщиной стенки не менее 12,0 мм, типа 2, 3, 12, 13 — для труб номинальной толщиной стенки от 7,0 до 12,0 мм.
9.2.8 Испытания на загиб (изгиб) основного металла выполняют на образцах в виде полос, отобранных от трубы согласно требованиям раздела 1 ГОСТ 3728—78.
9.2.9 Испытания на растяжение и ударный изгиб сварного соединения выполняют на образцах, отобранных в соответствии с требованиями разделов 2, 4 и 5 ГОСТ 6996—66.
9.3 Отчетная документация по приемочному контролю
9.3.1 На принятую партию труб или на трубы при поштучной сдаче оформляют документ о приемочном контроле: тип 3.1 или 3.2 по ГОСТ 31458.
9.3.2 Документация о приемочном контроле может быть представлена в печатном или электронном виде в системе электронного обмена данными (EDI), соответствующем любому соглашению об электронном обмене данными между заказчиком и изготовителем.
9.3.3 Документ о приемочном контроле (сертификат качества) должен содержать следующие сведения:
- наименование и адрес изготовителя;
- наименование и адрес заказчика;
- номер заказа;
- обозначение стандарта на листовой прокат;
- номинальные диаметр, толщину стенки, длину;
- номер партии или трубы;
- химический состав стали по результатам плавочного анализа (и металла изделия в соответствии с заказом);
- номер плавки;
- результаты контроля на наличие легирующих элементов в металле труб из легированных сталей;
- результаты испытаний на растяжение основного металла и сварного соединения при комнатной и повышенной (в соответствии с заказом) температуре с указанием типа, размера, расположения и ориентации образцов для испытаний;
- результаты испытаний на ударный изгиб основного металла и сварного соединения при комнатной (пониженной в соответствии с заказом) температуре с указанием типа, размера, расположения и ориентации образцов для испытаний;
- результаты проведения испытаний труб внутренним гидростатическим давлением;
- результаты неразрушающего контроля основного металла из документа о приемочном контроле на лист и выполненного изготовителем труб контроля сварного соединения с указанием применяемого метода, вида и размера применяемого искусственного дефекта;
- результаты испытания основного металла и сварного соединения на изгиб;
- результаты визуального и измерительного контроля;
17
ГОСТ Р 70731.3—2023
- результаты любых дополнительных испытаний, указанных в заказе;
- дату оформления документа.
9.3.4 По согласованию между изготовителем и заказчиком в документ о приемочном контроле могут быть внесены дополнительные сведения.
10 Методы контроля
10.1 Визуальный контроль состояния поверхности
Визуальный контроль проводят без применения увеличительных приборов и средств измерения в соответствии с [5], ГОСТ Р 50.05.08. Процедура контроля включает:
- визуальный контроль состояния поверхности основного металла, сварных соединений и торцов труб;
- контроль наличия маркировки.
10.2 Измерительный контроль
10.2.1 В рамках осуществления измерительного контроля все измерения следует выполнять с применением:
- средств измерений утвержденного типа, имеющих действующие свидетельства о поверке, — толщиномера, стенкомера, микрометра, штангенциркуля, рулетки измерительной металлической, линейки измерительной металлической, линейки поверочной, ультразвукового толщиномера, угломера с нониусом (см. 10.2.2);
- средств допускового контроля, имеющих сертификаты калибровки.
10.2.2 Измерительный контроль выполняют следующими средствами измерений:
- измерение длины трубы проводят вдоль ее образующей, а измерение наружного периметра поперечного сечения трубы для расчета наружного диаметра по формуле (3) проводят по концам трубы при помощи измерительной металлической рулетки класса точности 2 или 3 по ГОСТ 7502 методом прямых измерений в соответствии с руководством по эксплуатации рулетки. Допускаемое отклонение действительной длины интервала шкалы рулетки от нанесенного на шкале при температуре окружающей среды 20 °C и натяжении измерительной ленты рабочим усилием должно быть не более указанного в ГОСТ 7502—98 (таблица 1);
- контроль толщины стенки труб проводят по концам трубы толщиномерами, стенкомерами по ГОСТ 11358 или микрометрами по ГОСТ 6507. Измерения толщины стенки труб проводят методом прямых измерений в соответствии с руководством по эксплуатации толщиномера, стенкомера или микрометра не менее чем в четырех центральных сечениях, при этом решение о соответствии или несоответствии значения толщины стенки труб требованиям 7.10.4 принимается на основе результата измерения, имеющего наибольшее по модулю отклонение от номинального значения. Пределы допускаемой погрешности стенкомера или толщиномера должны соответствовать ГОСТ 11358—89 (подраздел 2.2); предел допускаемой погрешности микрометра должен соответствовать ГОСТ 6507—90 (подпункт 2.1.1.3);
- измерение толщины стенки в местах зачистки дефектов производят методом прямых измерений в соответствии с руководством по эксплуатации при помощи ультразвукового толщиномера, метрологические характеристики которого позволяют обеспечить соблюдение требований 7.10.4;
- угол скоса фаски измеряют методом прямых измерений в соответствии с руководством по эксплуатации при помощи угломера с нониусом любого из типов, указанных в подразделе 1.1 ГОСТ 5378—88; предел допускаемой погрешности угломера данного типа как при незатянутом, так и при затянутом стопоре при температуре окружающего воздуха (20 ± 5) °C и относительной влажности не более 80 % не должен превышать значений, указанных в таблице 2 ГОСТ 5378—88 для угломера данного типа;
- ширину торцевого кольца (притупления) (величина С на рисунке 1) на фаске измеряют штангенциркулем по ГОСТ 166. Измерения проводят методом прямых измерений в соответствии с руководством по эксплуатации штангенциркуля не менее чем в четырех центральных сечениях при измерении ширины торцевого кольца, при этом решение о соответствии или несоответствии значений ширины торцевого кольца требованиям 7.10.10 принимается на основе результата измерения, имеющего наибольшее по модулю отклонение от номинального значения. Пределы допускаемой погрешности штангенциркуля должны соответствовать требованиям таблицы 3, раздела 2 ГОСТ 166—89;
- измерение диаметра для расчета овальности на торцах труб выполняют штангенциркулем по ГОСТ 166—89. Измерения проводят методом прямых измерений в соответствии с руководством по экс-
18
ГОСТ Р 70731.3—2023
плуатации штангенциркуля в двух взаимно перпендикулярных плоскостях в определяемом визуально месте, где наружный или внутренний диаметр принимает наибольшее значение, за исключением участков в зоне шва на расстоянии 100 мм от его оси. Пределы допускаемой погрешности штангенциркуля должны соответствовать требованиям таблицы 3, раздела 2 ГОСТ 166—89;
- смещение кромок сварного соединения, высоту усиления и глубину вогнутости (седловины) сварных швов измеряют при помощи средств измерений или средств допускового контроля, произведенных по документации изготовителя и соответствующих требованиям пункта 10.2.1. В случае измерения методом косвенных измерений используются аттестованные методики измерения;
- контроль отклонения труб от прямолинейности проводят;
а) по всей длине трубы — с помощью струны или проволоки, натянутой между концами трубы, и измерительной металлической линейки по ГОСТ 427 [отклонения от номинальных значений длины шкалы и расстояний между любым штрихом и началом или концом шкалы не должны превышать значений, указанных в ГОСТ 427—75 (таблица 2)]. Отклонение от прямолинейности в данной точке поверхности трубы — это расстояние, измеренное методом прямых измерений в соответствии с руководством по эксплуатации при помощи линейки перпендикулярно к образующей трубы, от данной точки трубы до точки на струне или проволоке. Отклонение от прямолинейности измеряют не менее чем в одной точке на каждые 1000 мм длины трубы. Решение о соответствии или несоответствии значения отклонения от прямолинейности требованию 0 принимается на основе наибольшего из результатов измерений,
б) на участке длиной 1000 мм — с помощью линейки поверочной по ГОСТ 8026 [прямолинейность рабочих поверхностей линейки при температуре окружающей среды (20 ± 5) °C, при изменении температуры, не превышающем 0,5 °С/ч, в диапазоне угла наклона линеек ±20° от среднего положения, должна соответствовать требованиям ГОСТ 8026—92 (таблица 2)] и набора щупов (допускаемые отклонения толщины щупов должны обеспечивать выполнение требований 7.10.7). За значение отклонения от прямолинейности принимается значение толщины такого щупа (совокупности щупов), который можно без видимого зазора поместить между поверхностями трубы и линейки. Отклонение от прямолинейности измеряют не менее чем в трех точках, расположенных вдоль образующей трубы. Решение о соответствии или несоответствии значения отклонения от прямолинейности требованиям 7.10.7 принимается на основе наибольшего из результатов измерений.
Допускается проводить измерительный контроль труб другими средствами измерений, удовлетворяющими требованиям 7.2.1, метрологические характеристики которых позволяют обеспечить соблюдение требований 7.10. Если измерительный контроль труб проводят методом косвенных измерений, то соответствующая методика измерений должна быть аттестована и соответствовать требованиям ГОСТ Р 8.932.
10.2.3 Наружный диаметр труб D, мм, рассчитывается по формуле
D=Q/ic-2'Aq-0,2, (3)
где Q — периметр трубы, мм;
Ар — номинальная толщина ленты рулетки, мм.
10.2.4 Овальность концов труб 0 рассчитывается по формуле
e = 2'(Dmax-Dmin)-100/(Dmax + Dmin), (4)
где Dmax и Dmin — наибольший и наименьший наружные диаметры соответственно, измеренные в одном сечении.
10.3 Определение химического состава
10.3.1 В рамках процедуры определения химического состава все измерения следует выполнять с применением средств измерений утвержденного типа, имеющих действующие свидетельства о поверке, а применяемые методики (методы) измерений должны соответствовать требованиям ГОСТ Р 8.932.
10.3.2 Химический состав стали принимают по документу о качестве листового проката и переносят в отчетную документацию по приемочному контролю труб.
10.3.3 Определение химического состава металла труб осуществляют методами химического анализа по ГОСТ 12344, ГОСТ 12345, ГОСТ 12346, ГОСТ 12347, ГОСТ 12348, ГОСТ 12350, ГОСТ 12351, ГОСТ 12352, ГОСТ 12354, ГОСТ 12355, ГОСТ 12356, ГОСТ 12357, ГОСТ 12359, ГОСТ 22536.0, ГОСТ 22536.1, ГОСТ 22536.2, ГОСТ 22536.3, ГОСТ 22536.4, ГОСТ 22536.5, ГОСТ 22536.6, ГОСТ 22536.7, ГОСТ 22536.8, ГОСТ 22536.9, ГОСТ 27809.
10.3.4 Допускается проводить определение химического состава металлов фотоэлектрическим методом спектрального анализа по ГОСТ 18895 и ГОСТ Р 54153.
19
ГОСТ Р 70731.3—2023
10.3.5 Качественную оценку наличия легирующих химических элементов в трубах из легированной стали проводят методом стилоскопирования по документации изготовителя или методами спектрального анализа.
10.4 Испытания на растяжение и ударный изгиб
10.4.1 Испытания основного металла на растяжение выполняют по методике контроля, разработанной в соответствии с требованиями ГОСТ 1497 и ГОСТ Р 8.932, при повышенной температуре — по ГОСТ 9651.
10.4.2 Испытания на ударный изгиб основного металла при комнатной и отрицательных температурах выполняют по методике контроля, разработанной в соответствии с требованиями ГОСТ 9454 и ГОСТ Р 8.932.
Ударная вязкость определяется как среднее арифметическое значение результатов испытаний трех образцов; на одном образце допускается снижение ударной вязкости на 9,8 Дж/см2.
10.4.3 Испытания на растяжение и ударный изгиб сварного соединения выполняют в соответствии с ГОСТ 6996.
10.5 Испытания на загиб, статический изгиб
10.5.1 Проведение испытаний на загиб, статический изгиб следует выполнять при помощи испытательного оборудования, имеющего действующий аттестат в соответствии с требованиями [7]; если техническое устройство для воспроизведения условий испытаний одновременно является и средством измерения (СИ), причем точностные характеристики воспроизведения условий испытаний полностью определяются метрологическими характеристиками этого СИ, то такое устройство должно иметь действующее свидетельство о поверке или сертификат калибровки. Все измерения в рамках проведения испытаний на загиб, статический изгиб следует выполнять с применением СИ утвержденного типа, имеющих действующие свидетельства о поверке, а применяемые косвенные методики (методы) измерения должны быть аттестованы и соответствовать ГОСТ Р 8.932.
10.5.2 Качественное испытание на загиб, статический изгиб проводят до номинального угла 90° в соответствии с разделом 2 ГОСТ 3728—78 на образцах в виде продольных полос, а для сварного соединения — в виде поперечных полос со сварным швом в центре образца. Толщина образца должна быть равна полной толщине стенки трубы. Номинальное значение толщины оправки должно быть приблизительно в два раза больше номинального значения толщины стенки.
10.6 Метод проведения контроля герметичности
10.6.1 Гидростатические испытания труб проводят в соответствии с разделом 7 ГОСТ 3845—2017 с выдержкой труб под испытательным давлением не менее 10 с (время выдержки измеряют методом прямых измерений в соответствии с руководством по эксплуатации при помощи секундомера, имеющего действующее свидетельство о поверке или сертификат калибровки, требования к погрешности измерения секундомера в настоящем стандарте не устанавливаются).
10.6.2 Труба считается годной, если в процессе испытания не происходило падение давления и не обнаружены течи и разрывы металла, а при осмотре не выявлены видимые остаточные деформации.
10.7 Методы проведения ультразвукового контроля
10.7.1 Результаты УЗК основного металла труб на наличие продольных и/или поперечных дефектов принимаются по документам на исходный полуфабрикат (листовой прокат).
10.7.2 УЗК труб для выявления расслоений проводят по методике контроля, разработанной в соответствии с требованиями ГОСТ ISO 10893-8, уровень приемки U2. Данный метод контроля является качественным, поэтому требования к измерениям не устанавливаются.
10.7.3 УЗК сварного соединения проводят по методике контроля, разработанной в соответствии с требованиями ГОСТ Р ИСО 10893-11, уровень приемки U2. Данный метод контроля является качественным, поэтому требования к измерениям не устанавливаются.
10.8 Методы проведения радиографического контроля
10.8.1 Радиографический контроль сварного соединения выполняют по методике контроля, разработанной в соответствии с требованиями ГОСТ ISO 10893-6, класс качества В. Данный метод контроля является качественным, поэтому требования к измерениям не устанавливаются.
20
ГОСТ Р 70731.3—2023
10.8.2 Цифровой радиографический контроль сварного соединения выполняют по методике контроля, разработанной в соответствии с требованиями ГОСТ ISO 10893-7, класс качества В. Данный метод контроля является качественным, поэтому требования к измерениям не устанавливаются.
11 Гарантии изготовителя
Изготовитель должен гарантировать соответствие труб требованиям настоящего стандарта при условии соблюдения потребителем правил транспортирования и хранения, установленных в разделах 7, 8 ГОСТ 10692—2015 соответственно.
21
ГОСТ Р 70731.3—2023
Библиография
[1] Федеральные нормы и правила в области использования атомной энергии НП-001-15
Общие положения обеспечения безопасности атомных станций
[2]
Федеральные нормы и правила в области использования атомной энергии НП-071-18
[3]
[4]
[5]
Федеральные нормы и правила в области использования атомной энергии НП-089-15 Федеральные нормы и правила в области использования атомной энергии НП-104-18 Федеральные нормы и правила в области использования атомной энергии НП-105-18
Правила оценки соответствия продукции, для которой устанавливаются требования, связанные с обеспечением безопасности в области использования атомной энергии, а также процессов ее проектирования (включая изыскания), производства, строительства, монтажа, наладки, эксплуатации, хранения, перевозки, реализации, утилизации и захоронения
Правила устройства и безопасной эксплуатации оборудования и трубопроводов атомных энергетических установок
Сварка и наплавка оборудования и трубопроводов атомных энергетических установок
Правила контроля металла оборудования и трубопроводов атомных энергетических установок при изготовлении и монтаже
[6] Постановление Правительства Российской Федерации от 27 мая 2019 г. № 669 «О внесении изменений в некоторые акты Правительства Российской Федерации»
[7] СТО 95 12056—2019
Стандарт Госкорпорации «Росатом». Аттестация испытательного оборудования. Требования в области использования атомной энергии
22
УДК 621.774.2:006.354
ГОСТ Р 70731.3—2023
ОКС 23.040.10
27.120.99
Ключевые слова: стальные сварные прямошовные трубы, трубы для атомных энергетических установок, размер, способ производства, химический состав, механические свойства при комнатной температуре, технологические свойства, макроструктура, качество поверхности, отделка концов труб, маркировка, упаковка, приемка, испытания, контроль, транспортирование, хранение
23
Редактор Н.А. Шугарова
Технический редактор В.Н. Прусакова
Корректор М.И. Першина
Компьютерная верстка Е.О. Асташина
Сдано в набор 24.10.2023. Подписано в печать 14.11.2023. Формат 60x847s. Гарнитура Ариал.
Усл. печ. л. 3,26. Уч.-изд. л. 2,90.
Подготовлено на основе электронной версии, предоставленной разработчиком стандарта
Создано в единичном исполнении в ФГБУ «Институт стандартизации» , 117418 Москва, Нахимовский пр-т, д. 31, к. 2.