ФЕДЕРАЛЬНОЕ АГЕНТСТВО
ПО ТЕХНИЧЕСКОМУ РЕГУЛИРОВАНИЮ И МЕТРОЛОГИИ
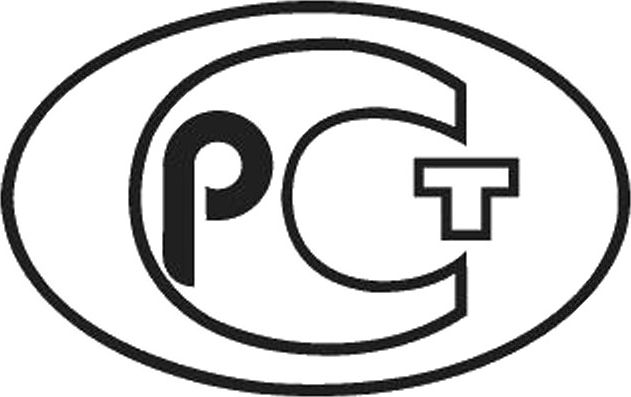
НАЦИОНАЛЬНЫЙ СТАНДАРТ РОССИЙСКОЙ ФЕДЕРАЦИИ
ГОСТ Р
53201—
2023
ТРУБЫ И ФИТИНГИ КОМПОЗИТНЫЕ ПОЛИМЕРНЫЕ С РЕЗЬБОВЫМИ СОЕДИНЕНИЯМИ ДЛЯ НАПОРНЫХ И БЕЗНАПОРНЫХ ТРУБОПРОВОДОВ
Технические условия
Издание официальное
Москва
Российский институт стандартизации
2023
ГОСТ Р 53201—2023
Предисловие
1 РАЗРАБОТАН Объединением юридических лиц «Союз производителей композитов» (Союзком-позит) совместно с Обществом с ограниченной ответственностью Научно-Производственное Предприятие «Завод стеклопластиковых труб» (ООО НПП «ЗСТ»)
2 ВНЕСЕН Техническим комитетом по стандартизации ТК497 «Композиты, конструкции и изделия из них»
3 УТВЕРЖДЕН И ВВЕДЕН В ДЕЙСТВИЕ Приказом Федерального агентства по техническому регулированию и метрологии от 16 ноября 2023 г. № 1413-ст
4 ВЗАМЕН ГОСТ Р 53201—2008
Правила применения настоящего стандарта установлены в статье 26 Федерального закона от 29 июня 2015 г. № 162-ФЗ «О стандартизации в Российской Федерации». Информация об изменениях к настоящему стандарту публикуется в ежегодном (по состоянию на 1 января текущего года) информационном указателе «Национальные стандарты», а официальный текст изменений и поправок — в ежемесячном информационном указателе «Национальные стандарты». В случае пересмотра (замены) или отмены настоящего стандарта соответствующее уведомление будет опубликовано в ближайшем выпуске ежемесячного информационного указателя «Национальные стандарты». Соответствующая информация, уведомление и тексты размещаются также в информационной системе общего пользования — на официальном сайте Федерального агентства по техническому регулированию и метрологии в сети Интернет (www.rst.gov.ru)
©Оформление. ФГБУ «Институт стандартизации», 2023
Настоящий стандарт не может быть полностью или частично воспроизведен, тиражирован и распространен в качестве официального издания без разрешения Федерального агентства по техническому регулированию и метрологии
II
ГОСТ Р 53201—2023
Содержание
1 Область применения..................................................................1
2 Нормативные ссылки..................................................................1
3 Термины и определения................................................................3
4 Основные параметры и размеры........................................................4
5 Технические требования..............................................................19
6 Требования безопасности.............................................................23
7 Требования охраны окружающей среды..................................................24
8 Правила приемки....................................................................24
9 Методы контроля....................................................................27
10 Транспортирование и хранение........................................................35
11 Указания по применению.............................................................35
12 Гарантии изготовителя...............................................................35
Приложение А (справочное) Перечень возможных дефектов поверхности труб...................36
Приложение Б (обязательное) Порядок оформления и утверждения контрольных образцов-эталонов внешнего вида...........................................39
Приложение В (справочное) Перечень возможных дефектов наружной и внутренней резьбы.......40
Приложение Г (обязательное) Требования к содержанию минимально необходимого объема информации о трубе/фитинге, соответствующей его уникальному идентификатору, хранящемуся в RFID-метке, установленной на трубе/фитинге....................41
Приложение Д (справочное) Рекомендации по монтажу трубопроводов.........................42
Приложение Е (справочное) Предельно допустимая температура некоторых агрессивных сред в трубопроводной системе...................................................47
Библиография........................................................................50
III
ГОСТ Р 53201—2023
Введение
Настоящий стандарт устанавливает требования к трубам и фитингам, изготовляемым из реактопластов, армированных волокном (полимерных композитов) и предназначенным для применения в системах различного функционального назначения, в том числе в напорных и безнапорных трубопроводных системах, транспортирующих широкий круг сред, включая химически агрессивные среды, для которых действующими документами по стандартизации Российской Федерации допускается применение труб и деталей трубопроводов из реактопластов, армированных волокном (полимерных композитов).
Ряд положений, которые содержит настоящий стандарт, см. [1], [2].
Трубы и фитинги из полимерных композитов, изготовляемые в соответствии с настоящим стандартом, пригодны для применения во всех грунтовых условиях, при подземной, наземной и надземной прокладке, а также под водой.
Сфера применения труб и фитингов из реактопластов, армированных волокном обусловлена свойствами полимерных композитов, обеспечивающими необходимую прочность, коррозионную стойкость, стойкость к внешним воздействиям, надежность, экологическую безопасность и долговечность трубопроводов в различных условиях эксплуатации.
При выборе сферы применения труб и фитингов по функциональному назначению в заданных условиях эксплуатации, следует руководствоваться требованиями настоящего стандарта.
IV
ГОСТ Р 53201—2023
НАЦИОНАЛЬНЫЙ СТАНДАРТ РОССИЙСКОЙ ФЕДЕРАЦИИ
ТРУБЫ И ФИТИНГИ КОМПОЗИТНЫЕ ПОЛИМЕРНЫЕ С РЕЗЬБОВЫМИ СОЕДИНЕНИЯМИ ДЛЯ НАПОРНЫХ И БЕЗНАПОРНЫХ ТРУБОПРОВОДОВ
Технические условия
Polymer composite pipes and fittings with threaded connections for pressure and non-pressure piping. Specifications
Дата введения — 2024—03—01
1 Область применения
Настоящий стандарт распространяется на трубы из реактопластов, армированных стекловолокном и/или базальтоволокном (стеклокомпозитов, базальтокомпозитов, вместе — полимерных композитов) номинальным диаметром от DN50 до DN200 (далее — трубы) и фитинги к ним (далее — фитинги), предназначенные для напорных и безнапорных трубопроводов, монтируемых на основе резьбовых соединений, работающих при температуре окружающей среды от минус 60 °C до плюс 60 °C и относительной влажности до 100 %.
Трубы и фитинги к ним следует применять для монтажа подземных, наземных, надземных и подводных трубопроводов, транспортирующих сырую нефть, нефтепродукты, газовый конденсат, пластовую воду, растворы солей, кислот и других химических реагентов, к воздействию которых материал труб и фитингов химически стоек, для обустройства систем нефтесбора, поддержания пластового давления, технического водоснабжения, питьевого и хозяйственно-бытового водоснабжения, включая системы горячего водоснабжения, а также для сооружения лифтовых колонн, крепления нефтяных, газовых и водозаборных скважин.
Допускается применять трубы и фитинги для монтажа систем теплоснабжения при соответствии требованиям настоящего стандарта, включая требования к допустимой максимальной температуре транспортируемой среды.
Допустимая максимальная температура транспортируемой среды — до плюс 110 °C, внутреннее рабочее давление — до 27,6 МПа.
Настоящий стандарт не распространяется на трубы и фитинги с муфтовыми клеевыми, раструбными клеевыми, резьбовыми клеевыми, муфтовыми резьбоклеевыми, раструбными резьбоклеевыми соединениями, трубы и фитинги с гибкой чекой или с буртовыми соединениями с поворотным фланцем, трубы и фитинги, предназначенные для монтажа трубопроводов, транспортирующих природный газ по ГОСТ 5542, а также для монтажа магистральных нефтепроводов и нефтепродуктопроводов.
Настоящий стандарт следует применять для целей подтверждения соответствия (обязательного, добровольного) в отношении продукции (вид — труба, фитинг; номинальный диаметр; внутреннее рабочее давление), указанной в заявке на проведение работ по подтверждению соответствия (сертификация, декларирование соответствия).
2 Нормативные ссылки
В настоящем стандарте использованы нормативные ссылки на следующие документы:
ГОСТ 9.708—83 Единая система защиты от коррозии и старения. Пластмассы. Методы испытаний на старение при воздействии естественных и искусственных климатических факторов
Издание официальное
1
ГОСТ Р 53201—2023
ГОСТ 9.719—94 Единая система защиты от коррозии и старения. Материалы полимерные. Методы испытаний на старение при воздействии влажного тепла, водяного и соляного тумана
ГОСТ 12.1.005 Система стандартов безопасности труда. Общие санитарно-гигиенические требования к воздуху рабочей зоны
ГОСТ 12.1.007 Система стандартов безопасности труда. Вредные вещества. Классификация и общие требования безопасности
ГОСТ 12.1.044 (ИСО 4589—84) Система стандартов безопасности труда. Пожаровзрывоопасность веществ и материалов. Номенклатура показателей и методы их определения
ГОСТ 12.3.030 Система стандартов безопасности труда. Переработка пластических масс. Требования безопасности
ГОСТ 12.4.011 Система стандартов безопасности труда. Средства защиты работающих. Общие требования и классификация
ГОСТ 12.4.021 Система стандартов безопасности труда. Системы вентиляционные. Общие требования
ГОСТ 17.1.3.13 Охрана природы. Гидросфера. Общие требования к охране поверхностных вод от загрязнения
ГОСТ 17.2.3.01 Охрана природы. Атмосфера. Правила контроля качества воздуха населенных пунктов
ГОСТ 166 (ИСО 3599—76) Штангенциркули. Технические условия
ГОСТ 427 Линейки измерительные металлические. Технические условия
ГОСТ 2226 Мешки из бумаги и комбинированных материалов. Общие технические условия
ГОСТ 3749 Угольники поверочные 90°. Технические условия
ГОСТ 5542 Газ природный промышленного и коммунально-бытового назначения. Технические условия
ГОСТ 4650 (ISO 62:2008) Пластмассы. Методы определения водопоглощения
ГОСТ 6507 Микрометры. Технические условия
ГОСТ 7502 Рулетки измерительные металлические. Технические условия
ГОСТ 9142 Ящики из гофрированного картона. Общие технические условия
ГОСТ 10198 Ящики деревянные для грузов массой св. 200 до 20000 кг. Общие технические условия
ГОСТ 10354 Пленка полиэтиленовая. Технические условия
ГОСТ 11358 Толщиномеры и стенкомеры индикаторные с ценой деления 0,01 и 0,1 мм. Технические условия
ГОСТ 14192 Маркировка грузов
ГОСТ 14359—69 Пластмассы. Методы механических испытаний. Общие требования
ГОСТ 15139 Пластмассы. Методы определения плотности (объемной массы)
ГОСТ 15150 Машины, приборы и другие технические изделия. Исполнения для различных климатических районов. Категории, условия эксплуатации, хранения и транспортирования в части воздействия климатических факторов внешней среды
ГОСТ 21650 Средства скрепления тарно-штучных грузов в транспортных пакетах. Общие требования
ГОСТ 32656 (ISO 527-4:1997, ISO 527-5:2009) Композиты полимерные. Методы испытаний. Испытания на растяжение
ГОСТ 32794 Композиты полимерные. Термины и определения
ГОСТ 33530 (ISO 6789:2003) Инструмент монтажный для нормированной затяжки резьбовых соединений. Ключи моментные. Общие технические условия
ГОСТ 33757 Поддоны плоские деревянные. Технические условия
ГОСТ 34646—2020 (ISO 15306:2003) Трубы из реактопластов, армированных стекловолокном. Метод определения стойкости к воздействию циклического внутреннего давления
ГОСТ 34648—2020 Трубы и детали трубопроводов из реактопластов, армированных волокном. Методы определения сопротивления труб и фитингов кратковременному воздействию внутреннего гидравлического давления
ГОСТ Р 12.4.301 Система стандартов безопасности труда. Средства индивидуальной защиты дерматологические. Общие технические условия
ГОСТ Р ИСО 3126 Трубопроводы из пластмасс. Пластмассовые элементы трубопровода. Определение размеров 2
ГОСТ Р 53201—2023
ГОСТ Р 54559—2011 Трубы и детали трубопроводов из реактопластов, армированных волокном. Термины и определения
ГОСТ Р 54924—2017 (ИСО 8513:2016) Трубы и детали трубопроводов из реактопластов, армированных стекловолокном. Методы определения механических характеристик при осевом растяжении
ГОСТ Р 54925—2012 Трубы и детали трубопроводов из реактопластов, армированных стекловолокном. Методы определения начального окружного предела прочности при растяжении
ГОСТ Р 55135 (ИСО 11357-2:1999) Пластмассы. Дифференциальная сканирующая калориметрия (ДСК). Часть 2. Определение температуры стеклования
ГОСТ Р 57687 (ИСО 14322:2012) Пластмассы. Эпоксидные смолы. Определение степени отверждения эпоксидных смол с применением дифференциальной сканирующей калориметрии
ГОСТ Р 57885 Трубы и детали трубопроводов из реактопластов, армированных стекловолокном. Определение размеров
ГОСТ Р 57942—2017 Шпунт композитный полимерный. Общие технические требования и методы испытаний
ГОСТ Р 58577 Правила установления нормативов допустимых выбросов загрязняющих веществ проектируемыми и действующими хозяйствующими субъектами и методы определения этих нормативов
ГОСТ Р 58939 Система обеспечения точности геометрических параметров в строительстве. Правила выполнения измерений. Элементы заводского изготовления
ГОСТ Р 70280 Охрана окружающей среды. Почвы. Общие требования по контролю и охране от загрязнения
СП 45.13330.2017 «СНиП 3.02.01-87 Земляные сооружения, основания и фундаменты»
Примечание — При пользовании настоящим стандартом целесообразно проверить действие ссылочных стандартов (сводов правил) в информационной системе общего пользования — на официальном сайте Федерального агентства по техническому регулированию и метрологии в сети Интернет или по ежегодному информационному указателю «Национальные стандарты», который опубликован по состоянию на 1 января текущего года, и по выпускам ежемесячного информационного указателя «Национальные стандарты» за текущий год. Если заменен ссылочный документ, на который дана недатированная ссылка, то рекомендуется использовать действующую версию этого документа с учетом всех внесенных в данную версию изменений. Если заменен ссылочный документ, на который дана датированная ссылка, то рекомендуется использовать версию этого документа с указанным выше годом утверждения (принятия). Если после утверждения настоящего стандарта в ссылочный документ, на который дана датированная ссылка, внесено изменение, затрагивающее положение, на которое дана ссылка, то это положение рекомендуется применять без учета данного изменения. Если ссылочный документ отменен без замены, то положение, в котором дана ссылка на него, рекомендуется применять в части, не затрагивающей эту ссылку.
3 Термины и определения
В настоящем стандарте применены термины по ГОСТ 32794, ГОСТ 33530, ГОСТ Р 54559, а также следующие термины с соответствующими определениями:
3.1 компаунд: Однородная смесь полимера или полимеров с другими компонентами, такими как разбавители, катализаторы, пластификаторы, красители и инертные наполнители.
Примечание — К компонентам компаунда также относят отвердители, которые вводятся в состав компаунда, как правило, непосредственно перед началом технологического процесса изготовления изделия из полимерного композита.
3.2 монтажная длина трубы: Общая длина трубы за вычетом длины соединения.
3.3 радиочастотная идентификация; технология RFID: Технология автоматической идентификации и сбора данных, которая использует электромагнитную или индуктивную связь, осуществляемую посредством радиоволн, для взаимодействия с радиочастотной меткой и однозначного считывания ридером ее уникального идентификатора путем применения различных видов модуляции сигнала и кодирования данных.
3.4 радиочастотная метка; RFID-метка: Радиоэлектронное средство, содержащее устройство хранения информации и предназначенное для однозначной идентификации объекта, на котором оно установлено.
3.5 резьбовые соединения трубопроводов: Соединения труб и фитингов, герметичность которых обеспечивается путем передачи усилия через резьбу.
3
ГОСТ Р 53201—2023
3.6 уникальный идентификатор трубы/фитинга: Уникальный идентификационный номер RFID-метки, задаваемый пользователем и однозначно сопоставляемый при считывании ридером с конкретной трубой или фитингом, на котором установлена настоящая радиочастотная метка.
Примечание — Уникальный идентификатор трубы/фитинга является пользовательским идентификатором радиочастотной метки.
3.7 устройство считывания (ридер): Устройство, предназначенное для выполнения процедур извлечения данных, хранящихся на RFID-метке, и/или записи данных на RFID-метку и, при необходимости, для управления процессами разрешения коллизий и коррекции ошибок, а также для выполнения операций канального декодирования и декодирования данных источника, что необходимо для восстановления их исходного вида.
Примечание — Устройство считывания должно иметь встроенный дисплей и/или содержать параллельный или последовательный порт для подключения к управляющему компьютеру или контроллеру.
3.8 термореактивный компаунд: Компаунд на основе термореактивной смолы.
3.9 эпоксидный компаунд: Термореактивный компаунд на основе эпоксидной смолы.
4 Основные параметры и размеры
4.1 Трубы подразделяют на следующие типы:
- насосно-компрессорные (НК);
- обсадные (О);
- линейные (Л).
4.2 Фитинги подразделяют на следующие типы:
- муфта соединительная;
- муфта переходная;
- отвод 90° (с углом поворота 90°);
- отвод 45° (с углом поворота 45°);
- отвод 22,5° (с углом поворота 22,5°);
- отвод 11,25° (с углом поворота 11,25°);
- тройник равнопроходной;
- фланец.
Примечание —Допускается изготовление фитингов других типов по конструкторской документации при их соответствии требованиям настоящего стандарта.
4.3 Трубы следует применять с равнопрочными фитингами, указанными в настоящем стандарте.
4.4 Условное обозначение труб должно включать:
- наименование продукции: «Труба»;
- условное обозначение типа трубы в соответствии с 4.1;
- сокращенное международное обозначение вида материала трубы в соответствии с приложением Б ГОСТ Р 54559—2011 (например, «GFRP» — для стеклокомпозита, «GFRP/BaFRP» — для полимерного композита, матрица которого армирована преимущественно стекловолокном и дополнительно базальтоволокном);
- внутреннее рабочее давление, МПа;
- номинальный диаметр, DN;
- указание на вид транспортируемой воды, «техническая вода», «питьевая вода» (только для труб, применяемых в системах технического водоснабжения, питьевого и хозяйственно-бытового водоснабжения соответственно);
- обозначение настоящего стандарта.
4.5 Условное обозначение фитингов должно включать:
- наименование продукции в соответствии с 4.2;
- сокращенное международное обозначение вида материала фитинга в соответствии с приложением Б ГОСТ Р 54559—2011 (например, «GFRP» — для стеклокомпозита, «GFRP/BaFRP» — для полимерного композита, матрица которого армирована преимущественно стекловолокном и дополнительно базальтоволокном);
- внутреннее рабочее давление, МПа;
4
ГОСТ Р 53201—2023
- номинальный диаметр (для переходных соединений — диаметры), DN;
- указание на вид транспортируемой воды, «техническая вода», «питьевая вода» (только для фитингов, применяемых в системах технического водоснабжения, питьевого и хозяйственно-бытового водоснабжения соответственно);
- обозначение настоящего стандарта.
Примеры условных обозначений:
Труба насосно-компрессорная, рассчитанная на внутреннее рабочее давление 10,3 МПа, номинальным диаметром DN63:
Труба НК GFRP 10,3-DN63 ГОСТ Р 53201—2023
Труба линейная, рассчитанная на внутреннее рабочее давление 12,1 МПа, номинальным диаметром DN100, применяемая для технического водоснабжения:
Труба Л GFRP 12,1-DN100 техническая вода ГОСТ Р 53201—2023
Отвод с углом поворота 90°, рассчитанный на внутреннее рабочее давление 6,9 МПа, номинальным диаметром DN63:
Отвод 90° GFRP 6,9-DN63 ГОСТ Р 53201—2023
Муфта переходная, рассчитанная на внутреннее рабочее давление 10,3 МПа, номинальными диаметрами DN100 и DN63:
Муфта переходная GFRP 10,3-DN100/63 ГОСТ Р 53201—2023
Тройник равнопроходной, рассчитанный на внутреннее рабочее давление 12,1 МПа, номинальными диаметрами DN100:
Тройник равнопроходной GFRP 12,1-DN100 ГОСТ Р 53201—2023
4.6 Конструктивное исполнение, основные размеры, расчетная масса труб по их типам, а также значения внутреннего рабочего давления должны соответствовать указанным на рисунке 1 и в таблицах 1 и 2.
Допускается по согласованию между потребителем и производителем изготовление по конструкторской документации труб номинальных диаметров, приведенных в таблицах 1 и 2, с иными значениями внутреннего рабочего давления, основными размерами и расчетной массой, при соответствии изготовляемых труб требованиям настоящего стандарта. В этом случае значения внутреннего рабочего давления, основные размеры и расчетная масса труб должны быть указаны в согласованной потребителем и производителем конструкторской документации.
4.7 Конструктивное исполнение, основные размеры, расчетная масса фитингов, а также значение внутреннего рабочего давления должны соответствовать указанным на рисунках 2—9 и в таблицах 3—10.
При изготовлении по согласованию между потребителем и производителем труб по конструкторской документации согласно 4.6 допускается изготовление фитингов для соединения данных труб со значениями внутреннего рабочего давления, основными размерами и расчетной массой, отличными от приведенных в таблицах 3—10, при соответствии изготовляемых фитингов требованиям настоящего стандарта. В этом случае значения внутреннего рабочего давления, основные размеры и расчетная масса фитингов должны быть указаны в согласованной потребителем и производителем конструкторской документации.
5
ГОСТ Р 53201—2023
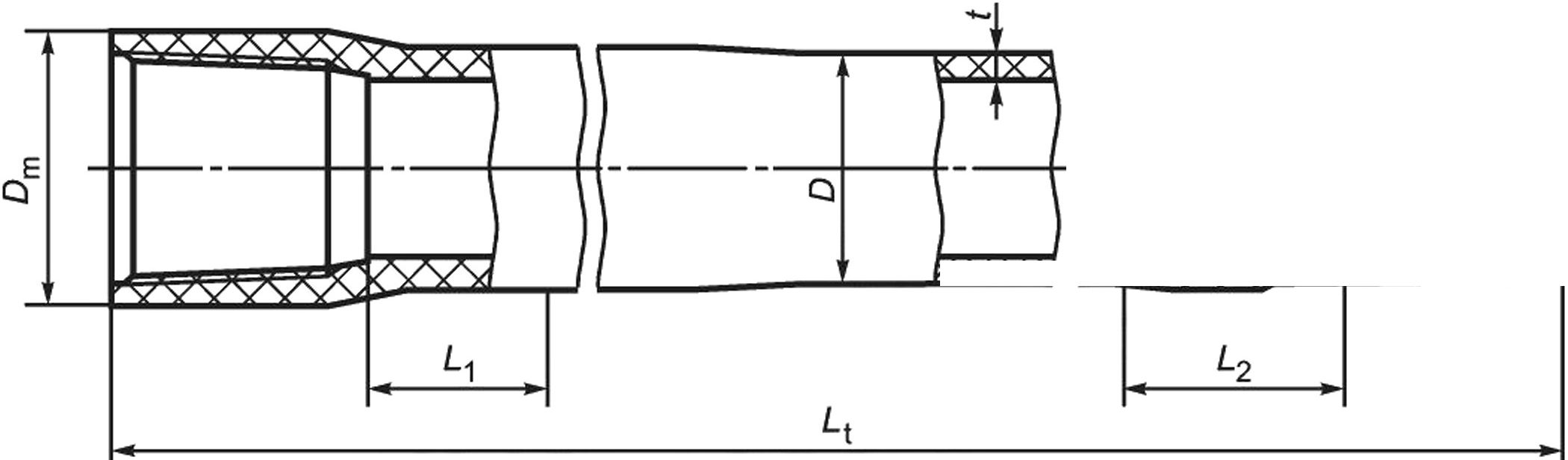
1ШХХЖ
Lt — длина трубы; D — наружный диаметр трубы; Dm — диаметр раструба; d — номинальный диаметр;
t — толщина стенки трубы; Ly и /_2 — длина зон, на которых разрешено работать ременными (ремешковыми) ключами и другим инструментом
Рисунок 1 — Основные размеры труб
4.8 Длина зон труб L^, L2 (рисунок 1), на которых разрешено работать ременными (ремешковыми) ключами и другим инструментом — до 400 мм от конца сбега резьбы.
Таблица 1 — Основные размеры, внутреннее рабочее давление и масса насосно-компрессорных и обсадных труб
Номинальный диаметр трубы, DN | Внутреннее рабочее давление, МПа | Размер резьбы труб, дюймы | Минимальная толщина стенки / мм | Расчетная масса 1 м трубы, кг | Минимальный наружный диаметр D, мм |
50 | До 10,3 | 2 3/8 | 4,2 | 1,7 | 58,4 |
12,1 | 2 3/8 | 4,5 | 1,9 | 59,0 | |
13,8 | 2 3/8 | 4,6 | 2,3 | 59,2 | |
17,2 | 2 3/8 | 6,5 | 2,4 | 63,0 | |
20,7 | 2 3/8 | 6,7 | 3,3 | 63,4 | |
24,1 | 2 3/8 | 7,3 | 3,5 | 64,6 | |
27,6 | 2 3/8 | 8,3 | 3,7 | 66,6 | |
63 | До 10,3 | 2 7/8 | 4,2 | 2,3 | 71,4 |
12,1 | 2 7/8 | 4,5 | 2,4 | 72,0 | |
13,8 | 2 7/8 | 4,6 | 2,5 | 72,2 | |
17,2 | 2 7/8 | 6,5 | 2,8 | 76,0 | |
20,7 | 2 7/8 | 7,4 | 3,4 | 77,8 | |
24,1 | 2 7/8 | 8,6 | 3,6 | 80,2 | |
27,6 | 2 7/8 | 9,1 | 4,2 | 81,2 | |
76 | До 10,3 | 3 1/2 | 4,9 | 2,9 | 85,8 |
12,1 | 3 1/2 | 5,3 | 3,1 | 86,6 | |
13,8 | 3 1/2 | 6,3 | 3,6 | 88,6 | |
15,5 | 3 1/2 | 7,7 | 4,1 | 91,4 | |
17,2 | 3 1/2 | 8,0 | 4,5 | 92,0 | |
20,7 | 3 1/2 | 9,4 | 5,0 | 94,8 | |
24,1 | 3 1/2 | 10,8 | 7,0 | 97,6 | |
27,6 | 3 1/2 | 12,4 | 9,2 | 100,8 |
6
Окончание таблицы 1
ГОСТ Р 53201—2023
Номинальный диаметр трубы, DN | Внутреннее рабочее давление, МПа | Размер резьбы труб, дюймы | Минимальная толщина стенки t, мм | Расчетная масса 1 м трубы, кг | Минимальный наружный диаметр D, мм |
100 | До 10,3 | 4 1/2 | 6,7 | 4,7 | 113,4 |
12,1 | 4 1/2 | 7,1 | 5,0 | 114,2 | |
13,8 | 4 1/2 | 8,7 | 6,1 | 117,4 | |
17,2 | 4 1/2 | 10,0 | 6,9 | 120,0 | |
20,7 | 4 1/2 | 11,8 | 9,5 | 123,6 | |
150 | До 6,9 | 7 | 7,1 | 9,3 | 164,2 |
8,6 | 7 | 7,9 | 9,9 | 165,8 | |
10,3 | 7 | 9,0 | 10,3 | 168,0 | |
13,8 | 7 | 12,1 | 13,2 | 174,2 | |
200 | До 6,9 | 8 5/8 | 5,9 | 8,8 | 211,8 |
8,6 | 8 5/8 | 10,0 | 13,0 | 220,0 | |
10,3 | 8 5/8 | 10,5 | 14,2 | 221,0 | |
12,1 | 8 5/8 | 14,7 | 17,4 | 229,4 |
Примечание —Диаметр раструба Dm (см. рисунок 1) настоящим стандартом не регламентируется и должен быть установлен в конструкторской документации.
Таблица 2 — Основные размеры, внутреннее рабочее давление и масса линейных труб
Номинальный диаметр трубы, DN | Внутреннее рабочее давление, МПа | Размер резьбы труб, дюйм | Минимальная толщина стенки Г, мм | Расчетная масса 1 м трубы, кг | Минимальный наружный диаметр D, мм | Минимальный диаметр раструба Dm, мм |
50 | До 10,3 | 2 3/8 | 3,8 | 1,2 | 57,6 | 73,1 |
12,1 | 2 3/8 | 4,1 | 1,4 | 58,2 | 74,1 | |
13,8 | 2 3/8 | 4,3 | 1,5 | 58,6 | 75,1 | |
15,5 | 2 3/8 | 4,9 | 1,8 | 59,8 | 76,1 | |
17,2 | 2 3/8 | 5,2 | 1,9 | 60,4 | 77,2 | |
20,7 | 2 3/8 | 5,4 | 2,1 | 60,8 | 79,1 | |
24,1 | 2 3/8 | 6,7 | 2,2 | 63,4 | 81,3 | |
27,6 | 2 3/8 | 8,1 | 2,3 | 66,2 | 83,7 | |
63 | До 10,3 | 2 7/8 | 3,8 | 1,7 | 70,6 | 87,3 |
12,1 | 2 7/8 | 4,1 | 2,0 | 71,2 | 88,3 | |
13,8 | 2 7/8 | 4,3 | 2,5 | 71,6 | 89,3 | |
15,5 | 2 7/8 | 4,9 | 2,6 | 72,8 | 90,9 | |
17,2 | 2 7/8 | 5,9 | 2,7 | 74,8 | 91,9 | |
20,7 | 2 7/8 | 7,0 | 3,0 | 77,0 | 94,4 | |
24,1 | 2 7/8 | 8,2 | 3,2 | 79,4 | 97,4 | |
27,6 | 2 7/8 | 8,6 | 3,4 | 80,2 | 100,0 |
7
ГОСТ Р 53201—2023
Окончание таблицы 2
Номинальный диаметр трубы, DN | Внутреннее рабочее давление, МПа | Размер резьбы труб, дюйм | Минимальная толщина стенки /, мм | Расчетная масса 1 м трубы, кг | Минимальный наружный диаметр D, мм | Минимальный диаметр раструба Dm, мм |
76 | До 10,3 | 3 1/2 | 4,4 | 2,6 | 84,8 | 109,3 |
12,1 | 3 1/2 | 4,5 | 2,7 | 85,0 | 111,0 | |
13,8 | 3 1/2 | 5,9 | 3,2 | 87,8 | 111,7 | |
15,5 | 3 1/2 | 7,1 | 3,6 | 90,2 | 114,4 | |
17,2 | 3 1/2 | 7,3 | 4,3 | 90,6 | 118,9 | |
20,7 | 3 1/2 | 7,5 | 4,9 | 91,0 | 123,0 | |
24,1 | 3 1/2 | 9,9 | 7,0 | 95,8 | 125,4 | |
27,6 | 3 1/2 | 11,1 | 8,9 | 98,2 | 128,3 | |
100 | 5,5 | 4 1/2 | 3,9 | 2,3 | 107,8 | 127,9 |
6,9 | 4 1/2 | 4,1 | 2,8 | 108,2 | 129,4 | |
8,6 | 4 1/2 | 4,3 | 3,3 | 108,6 | 131,4 | |
10,3 | 4 1/2 | 4,4 | 3,6 | 108,8 | 133,5 | |
12,1 | 4 1/2 | 4,6 | 3,8 | 109,2 | 135,5 | |
13,8 | 4 1/2 | 5,0 | 4,9 | 110,0 | 137,0 | |
15,5 | 4 1/2 | 6,7 | 5,3 | 113,4 | 139,1 | |
17,2 | 4 1/2 | 7,0 | 5,5 | 114,0 | 141,1 | |
20,7 | 4 1/2 | 7,4 | 5,8 | 114,8 | 145,7 | |
24,1 | 4 1/2 | 9,0 | 7,0 | 118,0 | 149,7 | |
150 | 5,5 | 7 | 4,6 | 5,1 | 159,2 | 189,3 |
6,9 | 7 | 4,8 | 5,9 | 159,6 | 190,9 | |
8,6 | 7 | 5,0 | 6,2 | 160,0 | 193,9 | |
10,3 | 7 | 5,2 | 6,5 | 160,4 | 196,5 | |
12,1 | 7 | 7,2 | 8,6 | 164,4 | 199,6 | |
13,8 | 7 | 9,0 | 11,7 | 168,0 | 202,6 | |
200 | 5,5 | 8 5/8 | 5,1 | 8,1 | 210,2 | 233,2 |
6,9 | 8 5/8 | 5,6 | 8,5 | 211,2 | 235,2 | |
8,6 | 8 5/8 | 8,9 | 12,1 | 217,8 | 238,8 | |
10,3 | 8 5/8 | 9,2 | 13,8 | 218,4 | 242,8 | |
12,1 | 8 5/8 | 12,7 | 19,3 | 225,4 | 246,9 |
8
ГОСТ Р 53201—2023
4.9 Трубы следует изготовлять в прямых отрезках.
Номинальное значение длины труб составляет 9140 мм.
Допускается изготовлять трубы длиной, отличной от номинальной, но не более 12000 мм.
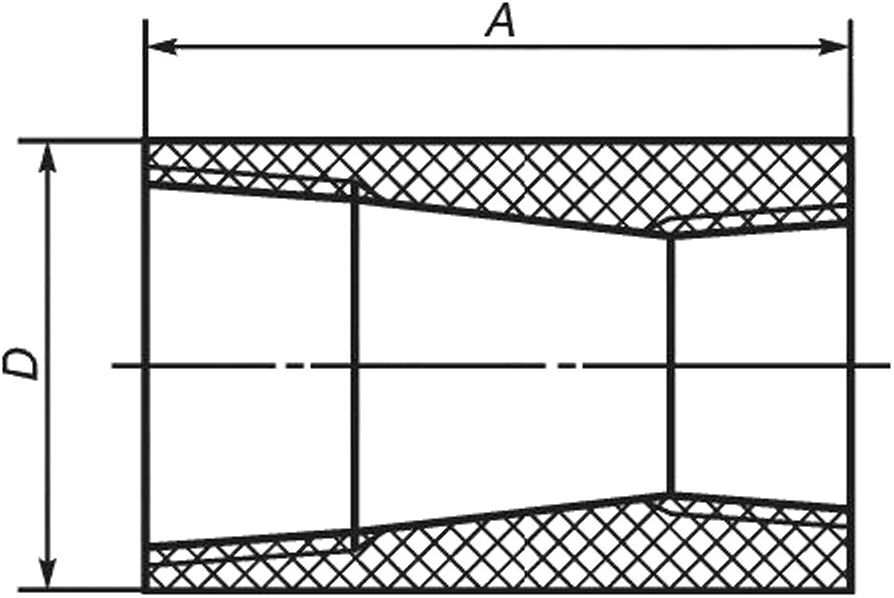
А — длина муфты; D — наружный диаметр
Рисунок 2 — Переходная муфта
Таблица 3 — Основные размеры, внутреннее рабочее давление и масса переходных муфт
Номинальные диаметры, DN | Размер резьбы, дюймы | Внутреннее рабочее давление, МПа, не более | А, мм | D, мм | Масса, кг |
63/50 | 2% / 2% | 27,6 | 234,0 | 114,0 | 2,8 |
76/63 | ЗУ2 / 2% | 24,1 | 257,0 | 149,0 | 6,3 |
100/76 | 4У2 / ЗУ2 | 24,1 | 332,0 | 190,0 | 7,9 |
150/100 | 7 / 41/2 | 17.2 | 354,0 | 220,0 | 8,1 |
200/150 | 8% / 7 | 10,3 | 382,0 | 280,0 | 14,3 |
А
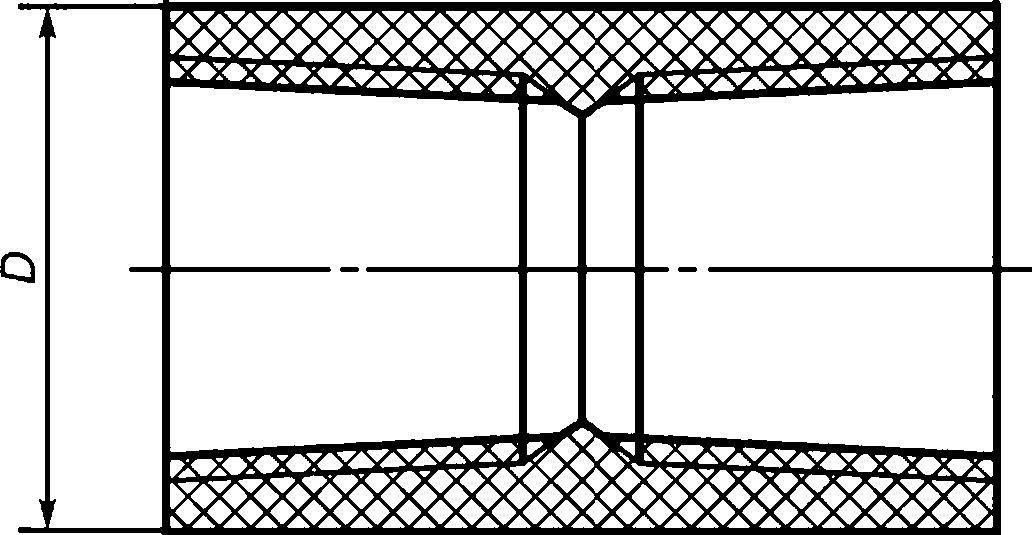
А — длина муфты; D — наружный диаметр
Рисунок 3 — Соединительная муфта
9
ГОСТ Р 53201—2023
Таблица 4 — Основные размеры, внутреннее рабочее давление и масса соединительных муфт
Номинальный диаметр, DN | Размер резьбы, дюймы | Внутреннее рабочее давление, МПа | А, мм | D, мм | Масса, кг |
50 | 2% | До 10,3 | 200,0 | 83,0 | 1,0 |
12,1-17,2 | 91,4 | 1,6 | |||
19,0-27,6 | 102,0 | 2,4 | |||
63 | 2% | До 10,3 | 216,0 | 100,0 | 1,5 |
12,1-17,2 | 114,0 | 2,6 | |||
20,7-27,6 | 123,0 | 3,8 | |||
76 | 31/2 | До 8,6 | 228,5 | 120,0 | 2,4 |
10,3-15,5 | 135,0 | 3,1 | |||
17,2-27,6 | 149,0 | 6,7 | |||
100 | 41/2 | До 6,9 | 248,0 | 150,0 | 3,6 |
8,6-13,8 | 165,0 | 5,2 | |||
15,5-24,1 | 190,0 | 8,8 | |||
150 | 7 | До 8,6 | 279,5 | 206,0 | 5,4 |
10,3 | 220,0 | 8,4 | |||
12,1-13,8 | 260,0 | 16,1 | |||
200 | 8% | До 6,9 | 305,0 | 251,0 | 9,3 |
8,6 | 272,0 | 13,7 | |||
10,3-12,1 | 300,0 | 17,2 |
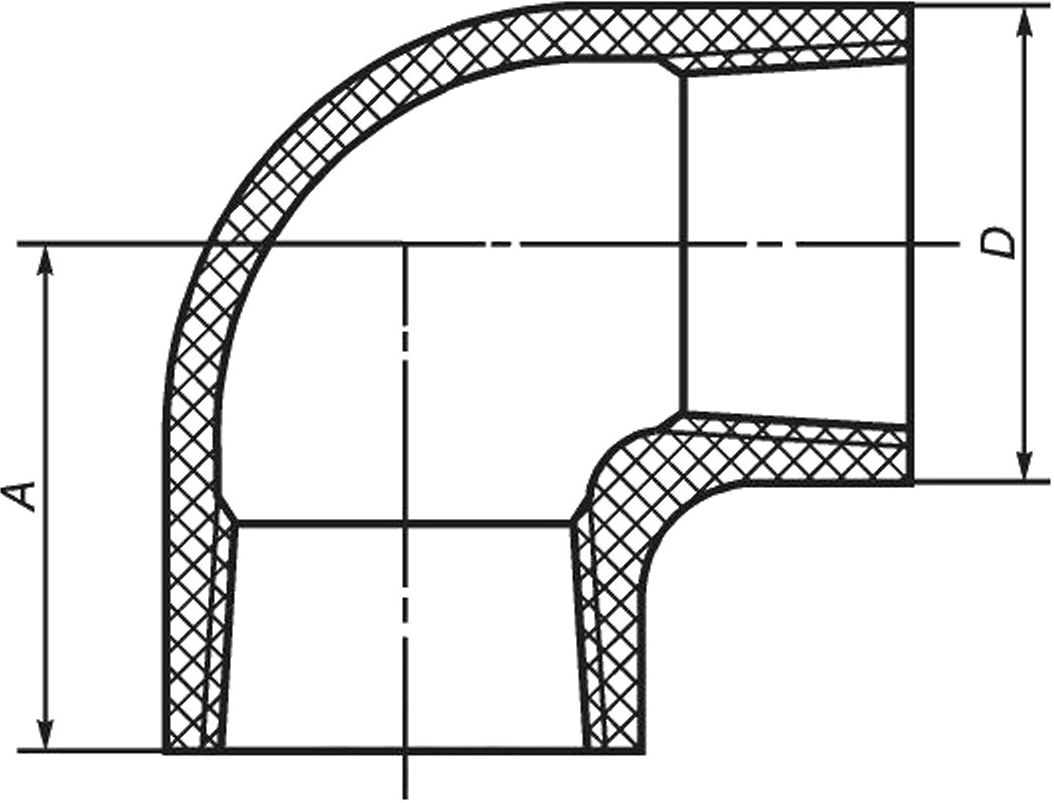
А — длина оси присоединительной части отвода; D — наружный диаметр
Рисунок 4 — Отвод с углом поворота 90°
10
ГОСТ Р 53201—2023
Таблица 5 — Основные размеры, внутреннее рабочее давление и масса отводов с углом поворота 90°
Номинальный диаметр, DN | Размер резьбы, дюймы | Внутреннее рабочее давление, МПа | А, мм | D, мм | Масса, кг |
50 | 2% | До 10,3 | 150,8 | 83,0 | 1,9 |
12,1-17,2 | 91,4 | 2,6 | |||
19,0-27,6 | 102,0 | 3,4 | |||
63 | 2% | До 10,3 | 174,4 | 100,0 | 2,3 |
12,1-17,2 | 114,0 | 4,1 | |||
20,7-27,6 | 123,0 | 6,4 | |||
76 | 31/2 | До 8,6 | 190,5 | 120,0 | 3,9 |
10,3-15,5 | 135,0 | 6,2 | |||
17,2-27,6 | 149,0 | 9,0 | |||
100 | 47г | До 10,3 | 225,4 | 150,0 | 6,4 |
12,1-13,8 | 165,0 | 9,3 | |||
15,5-24,1 | 190,0 | 12,6 | |||
150 | 7 | До 8,6 | 292,1 | 206,0 | 12,1 |
10,3 | 220,0 | 18,0 | |||
12,1-13,8 | 260,0 | 24,3 | |||
200 | 8% | До 6,9 | 345,9 | 251,0 | 15,9 |
8,6 | 272,0 | 21,3 | |||
10,3-12,1 | 300,0 | 28,0 |
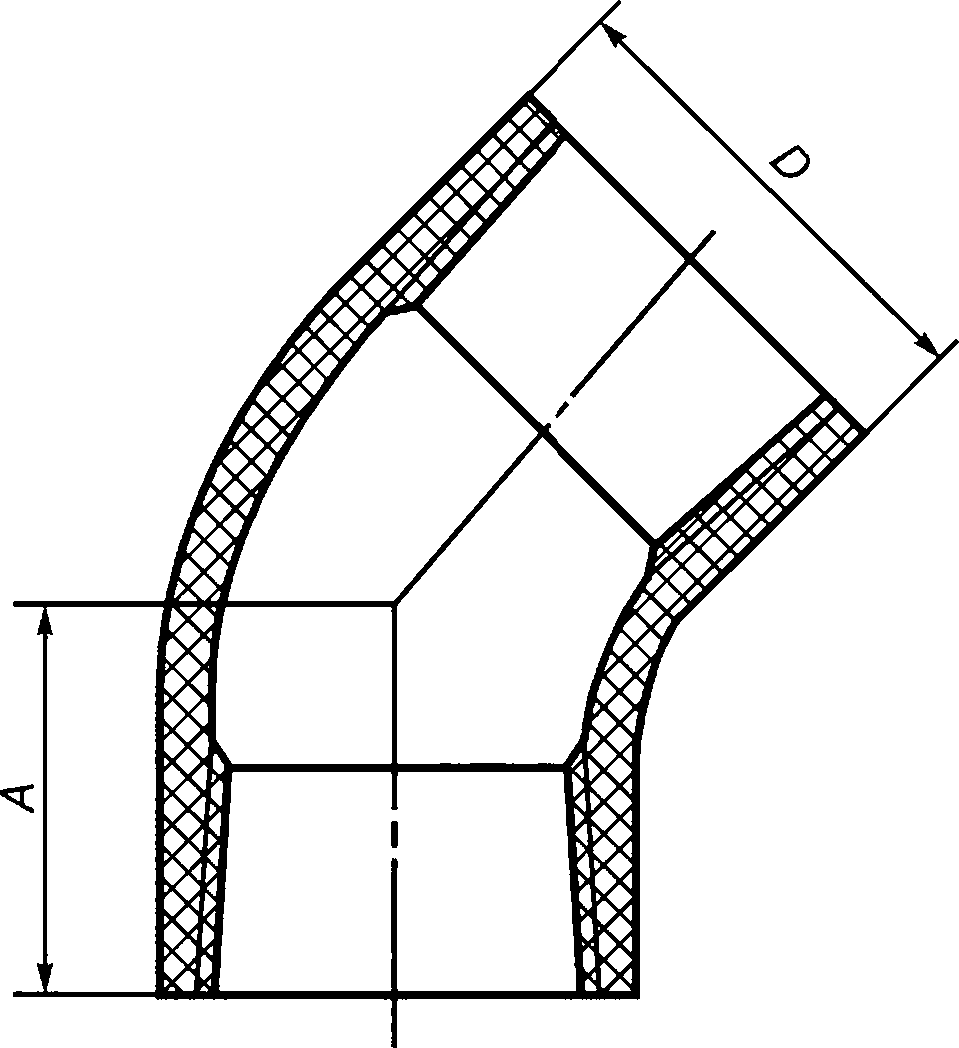
А — длина оси присоединительной части отвода; D — наружный диаметр
Рисунок 5 — Отвод с углом поворота 45°
11
ГОСТ Р 53201—2023
Таблица 6 — Основные размеры, внутреннее рабочее давление и масса отводов с углом поворота 45°
Номинальный диаметр, DN | Размер резьбы, дюймы | Внутреннее рабочее давление, МПа | А, мм | D, мм | Масса, кг |
50 | 2% | До 10,3 | 138,1 | 83,0 | 1,7 |
12,1-17,2 | 91,4 | 2,3 | |||
19,0-27,6 | 102,0 | 3,0 | |||
63 | 2% | До 10,3 | 152,5 | 100,0 | 2,2 |
12,1-17,2 | 114,0 | 3,6 | |||
20,7-27,6 | 123,0 | 6,4 | |||
76 | 31/2 | До 8,6 | 152,5 | 120,0 | 3,2 |
10,3-15,5 | 135,0 | 5,7 | |||
17,2-27,6 | 149,0 | 6,7 | |||
100 | 472 | До 8,6 | 168,3 | 150,0 | 4,8 |
10,3-13,8 | 165,0 | 7,2 | |||
15,5-24,1 | 190,0 | 12,6 | |||
150 | 7 | До 8,6 | 196,9 | 206,0 | 12,1 |
10.3 | 220,0 | 18,0 | |||
12,1-13,8 | 260,0 | 22,0 | |||
200 | 8% | До 6,9 | 209,6 | 251,0 | 16,0 |
8,6 | 272,0 | 21,3 | |||
10,3-12,1 | 300,0 | 28,0 |
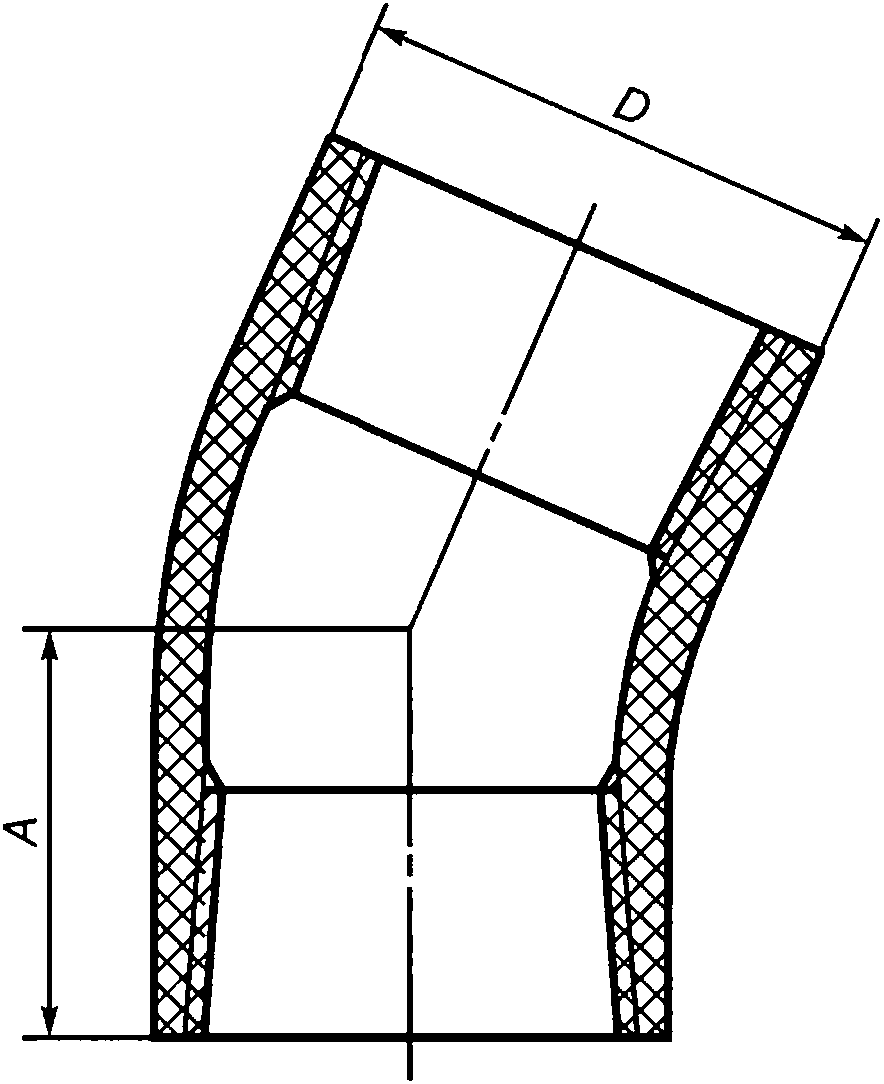
А — длина оси присоединительной части отвода; D — наружный диаметр
Рисунок 6 — Отвод с углом поворота 22,5°
12
ГОСТ Р 53201—2023
Таблица 7 — Основные размеры, внутреннее рабочее давление и масса отвода с углом поворота 22,5°
Номинальный диаметр, DN | Размер резьбы, дюймы | Внутреннее рабочее давление, МПа | А, мм | D, мм | Масса, кг |
50 | 2% | До 10,3 | 155,0 | 83,0 | 1,7 |
12,1-17,2 | 91,4 | 2,3 | |||
19,0-27,6 | 102,0 | 3,0 | |||
63 | 2% | До 10,3 | 163,0 | 100,0 | 2,2 |
12,1-17,2 | 114,0 | 3,6 | |||
20,7-27,6 | 123,0 | 5,9 | |||
76 | 3% | До 8,6 | 167,4 | 120,0 | 3,2 |
10,3-15,5 | 135,0 | 5,6 | |||
17,2-27,6 | 149,0 | 7,7 | |||
100 | 4% | До 8,6 | 179,0 | 150,0 | 5,5 |
10,3 | 165,0 | 7,0 | |||
12,1-13,8 | 190,0 | 13,0 | |||
150 | 7 | До 8,6 | 200,0 | 206,0 | 8,6 |
10,3 | 220,0 | 12,6 | |||
12,1-13,8 | 260,0 | 22,6 | |||
200 | 8% | До 6,9 | 212,5 | 251,0 | 13,0 |
8,6 | 272,0 | 17,7 | |||
10,3-12,1 | 300,0 | 28,0 |
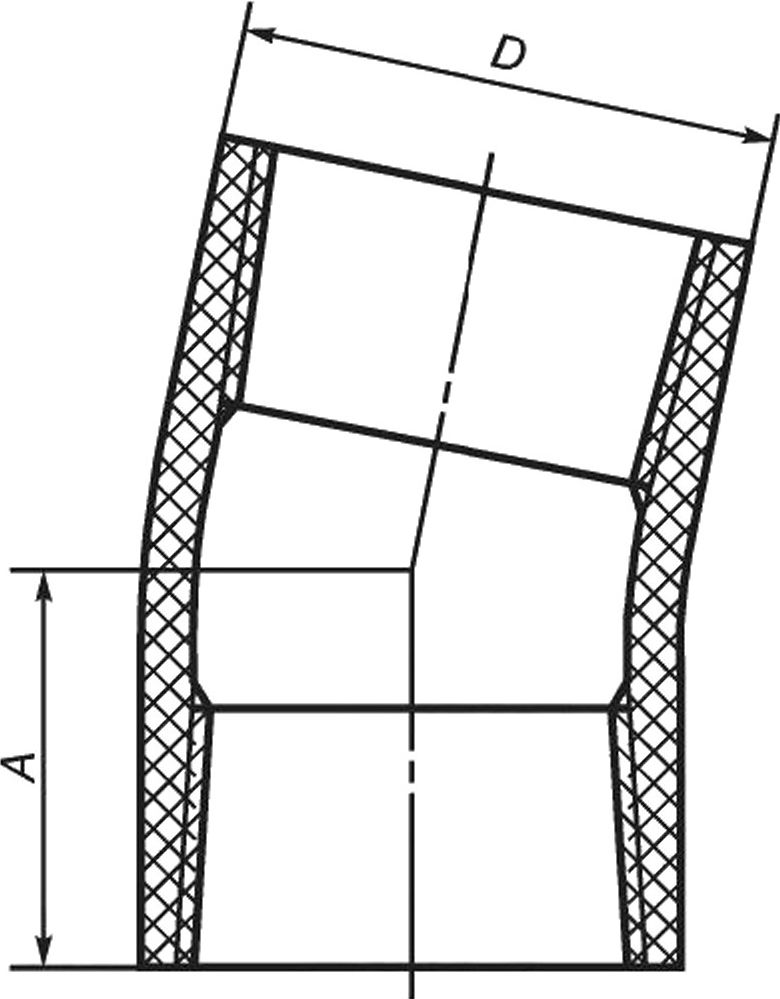
А — длина оси присоединительной части отвода; D — наружный диаметр
Рисунок 7 — Отвод с углом поворота 11,25°
13
ГОСТ Р 53201—2023
Таблица 8 — Основные размеры, внутреннее рабочее давление и масса отвода с углом поворота 11,25°
Номинальный диаметр, DN | Размер резьбы, дюймы | Внутреннее рабочее давление, МПа | А, мм | D, мм | Масса, кг |
63 | 27/8 | До 10,3 | 163 | 100,0 | 2,2 |
12,1-17,2 | 114,0 | 3,6 | |||
20,7-27,6 | 130,0 | 5,9 | |||
100 | 4!4 | До 8,6 | 179,0 | 150,0 | 4,7 |
10,3-13,8 | 165,0 | 7,0 | |||
15,5-24,1 | 190,0 | 9,5 | |||
150 | 7 | До 8,6 | 204,7 | 206,0 | 8,6 |
10,3 | 220,0 | 12,6 | |||
12,1-13,8 | 260,0 | 24,5 | |||
200 | 8% | До 6,9 | 217,4 | 251,0 | 13,0 |
8.6 | 272,0 | 15,4 | |||
10,3-12,1 | 300,0 | 24,0 |
Примечание — Отводы с углом поворота 11,25° DN50 и DN76 изготавливают по согласованию между потребителем и производителем по конструкторской документации. Основные размеры, внутреннее рабочее давление и масса данных отводов настоящим стандартом не регламентируются и должны быть установлены в конструкторской документации.
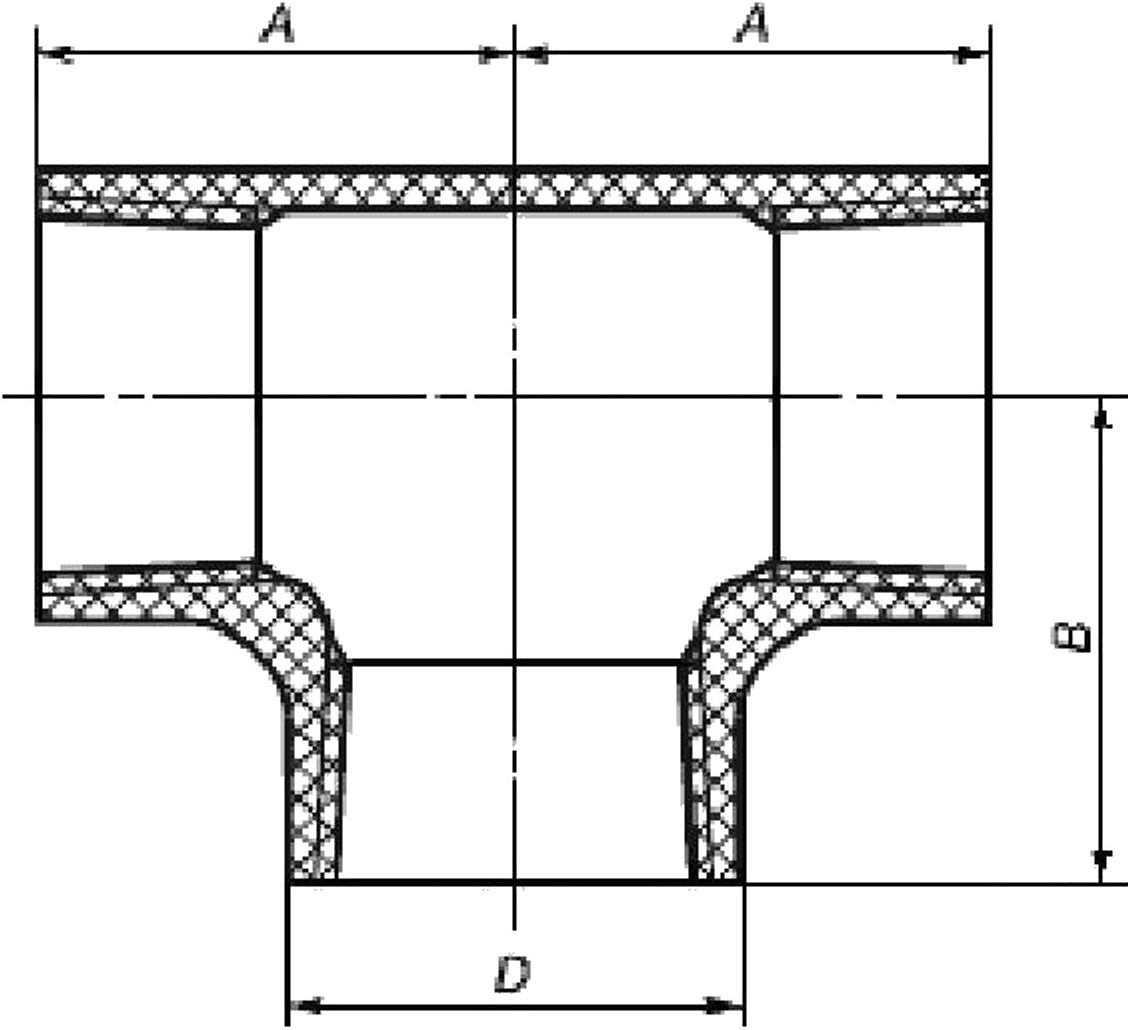
А, В — длины осей присоединительной части тройника; D — наружный диаметр
Рисунок 8 — Равнопроходной тройник
14
ГОСТ Р 53201—2023
Таблица 9 — Основные размеры, внутреннее рабочее давление и масса равнопроходного тройника
Номинальный диаметр, DN | Размер резьбы, дюймы | Внутреннее рабочее давление, МПа | 4, мм | В, мм | D, мм | Масса, кг |
50 | 2% | До 10,3 | 150,8 | 150,8 | 85,0 | 2,7 |
12,1-17,2 | 93,0 | 3,5 | ||||
19,0-27,6 | 102,0 | 4,4 | ||||
63 | 2% | До 10,3 | 171,5 | 171,5 | 102,0 | 4,4 |
12,1-17,2 | 114,0 | 5,5 | ||||
20,7-27,6 | 123,0 | 6,9 | ||||
76 | 31/2 | До 8,6 | 167,4 | 167,4 | 122,0 | 6,6 |
10,3-15,5 | 135,0 | 9,5 | ||||
17,2-27,6 | 149,0 | 12,6 | ||||
100 | 4% | До 8,6 | 225,4 | 225,4 | 152,0 | 9,7 |
10,3 | 165,0 | 12,9 | ||||
12,1-24,1 | 190 | 17,4 | ||||
150 | 7 | До 8,6 | 292,1 | 292,1 | 208,0 | 17,3 |
10,3 | 220,0 | 23,0 | ||||
12,1-13,8 | 260,0 | 44,0 | ||||
200 | 8% | До 6,9 | 346,4 | 346,4 | 254,0 | 23,0 |
8,6 | 272,0 | 30.9 | ||||
10,3-12,1 | 300,0 | 41,7 |
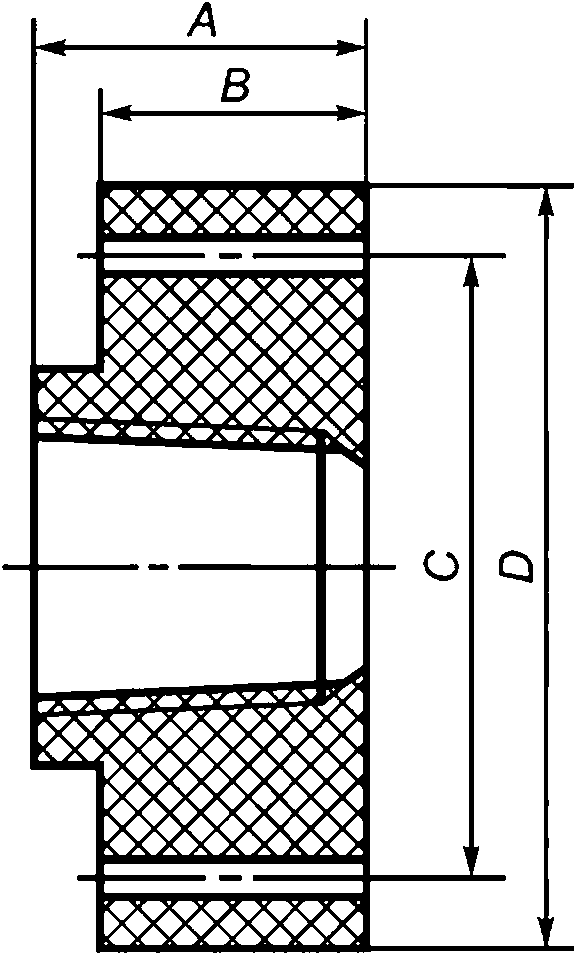
А — общая длина фланца; В — длина фланца по наружному диаметру; С — диаметр расположения осей отверстий; D — наружный диаметр
Рисунок 9 — Фланец
15
ГОСТ Р 53201—2023
Таблица 10 — Основные размеры и внутреннее рабочее давление фланцев
Номинальный диаметр, DN | Размер резьбы, дюймы | Внутреннее рабочее давление, МПа | В, мм |
50 | 2% | 10,3 | 86,0 |
63 | 2% | 10,3 | 98,0 |
76 | ЗУг | 10,3 | 98,0 |
100 | 4% | 10,3 | 105,0 |
150 | 7 | 10,3 | 116,0 |
200 | 8% | 6,9 | 122,0 |
Примечание — Размеры А, С и D определяют в конструкторской документации. |
4.10 Основные размеры резьбового соединения труб и фитингов, форма и размеры профиля резьбы приведены на рисунках 10 и 11 ив таблицах 11 и 12.
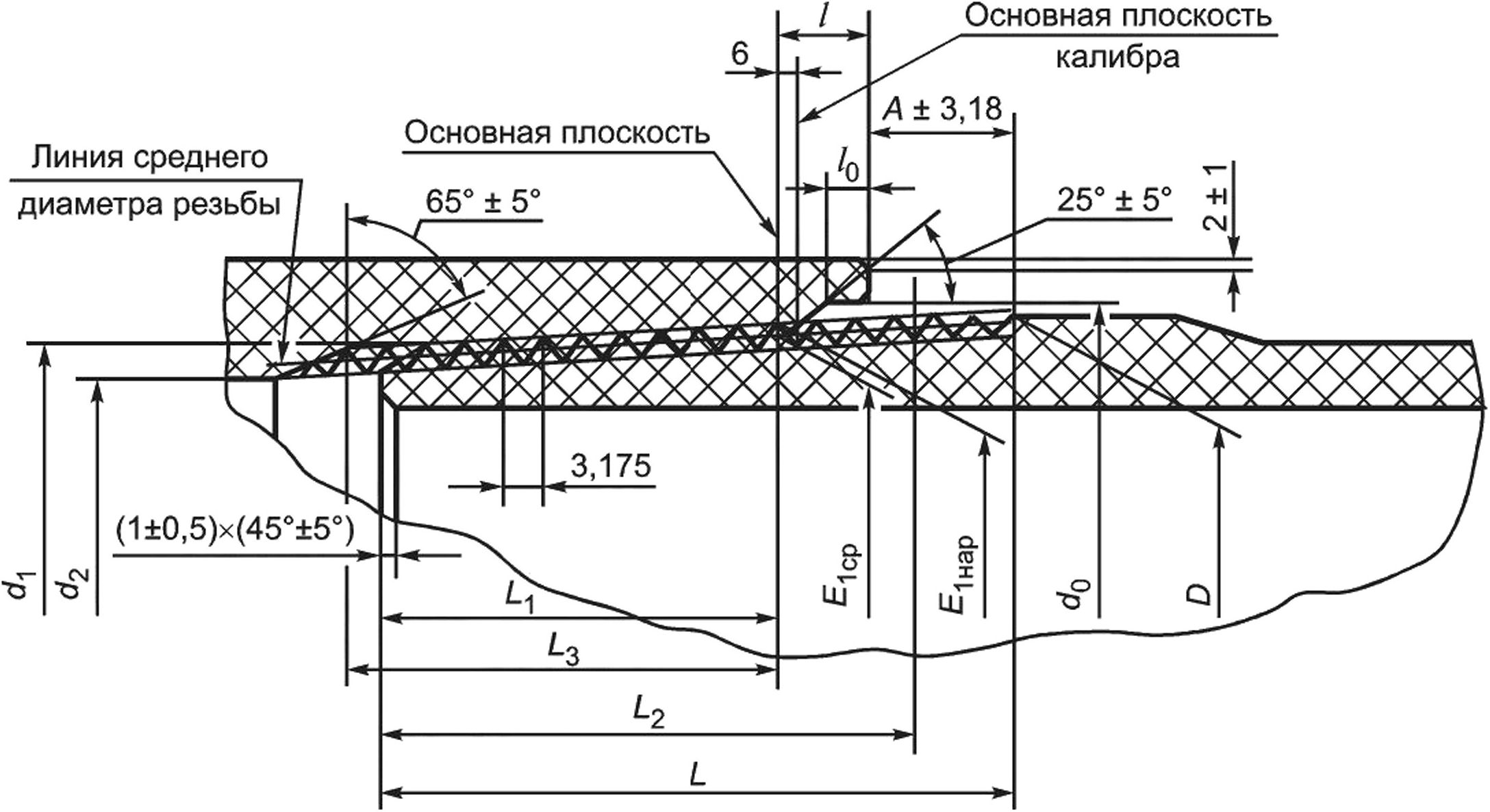
^1 ср и ^1 нар — средний и наружный диаметры резьбы в основной плоскости; ф — расчетный диаметр пересечения наружного конуса резьбы с торцом ниппеля; d2 — малый диаметр фаски; D — диаметр в конце сбега резьбы; ф — диаметр цилиндрического буртика раструба; L — общая длина резьбы (до конца сбега); L1 — длина от торца ниппеля до основной плоскости резьбы; L2 — длина рабочей части резьбы; L3 — расстояние от основной плоскости резьбы до начала сбега резьбы; /— размер от торца раструба до основной плоскости резьбы; /0 — глубина буртика раструба от торца до фаски; А — натяг при сворачивании труб специальными ключами
Рисунок 10 — Резьбовое соединение труб и фитингов
Таблица 11 — Значения параметров резьбы
В миллиметрах
Размер резьбы, дюймы | ^1 ср | ^1 нар | di | d2 | D | ^0 | L1 | L2 | L | / | ^0 |
2% | 63,7 | 65,4 | 62,5 | 67,0 | 69,0 | 67,5 | 45,2 | 67,6 | 91,0 | 13,6 | 9,5 |
2% | 76,4 | 78,1 | 74,8 | 79,0 | 81,0 | 80,2 | 53,1 | 77,5 | 99,0 | 13,6 | 9,5 |
31/2 | 93,1 | 94,8 | 91,9 | 96,0 | 98,0 | 97,0 | 59,5 | 83,5 | 105,0 | 13,6 | 9,5 |
16
ГОСТ Р 53201—2023
Окончание таблицы 11 В миллиметрах
Размер резьбы, дюймы | ^1 ср | ^1 нар | ^1 | ^2 | D | ^0 | *-1 | L2 | L | / | |
41/2 | 118,5 | 120,2 | 115,9 | 121,0 | 123,0 | 122,3 | 69,0 | 91,5 | 115,0 | 13,6 | 9,5 |
7 | 175,4 | 177,1 | 172,5 | 178,0 | 180,0 | 180,2 | 74,2 | 99,8 | 127,0 | 17,9 | 12,7 |
8% | 216,5 | 218,3 | 212,9 | 219,0 | 221.5 | 221,5 | 85,2 | 112,4 | 140,0 | 18,0 | 12,7 |
Примечание — Размер L3 и параметр А устанавливают в конструкторской документации. |
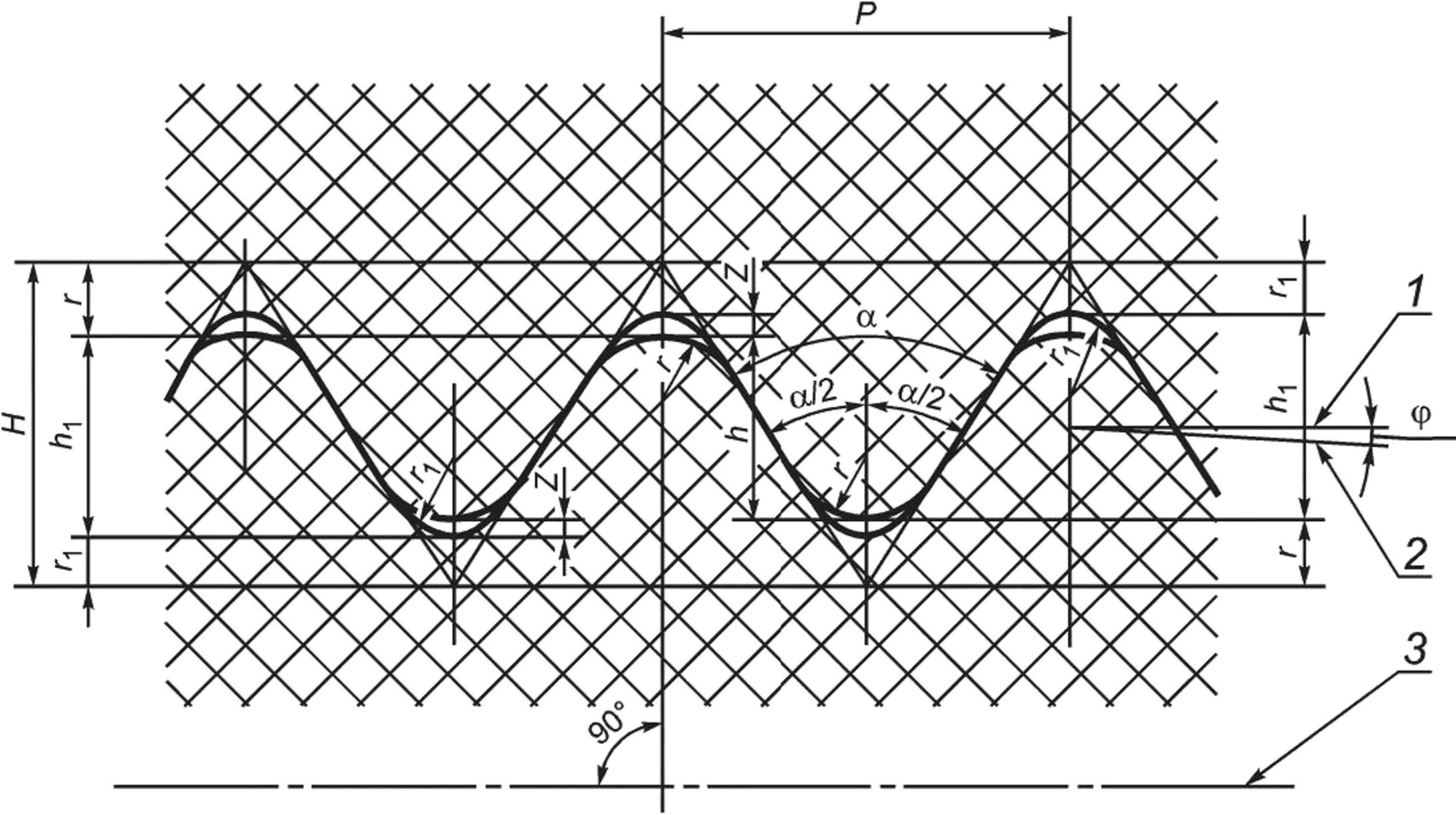
1 — линия, параллельная оси резьбы; 2 — линия среднего диаметра резьбы; 3 — ось резьбы; Р — шаг резьбы (измеряют параллельно оси резьбы); Н — высота исходного профиля; h1 — высота профиля; h — рабочая высота профиля; а — угол профиля; Z — зазор; <р — угол наклона; г, г^ — радиус закругления
Рисунок 11 — Форма и размеры профиля резьбы
Таблица 12 — Основные размеры профиля резьбы
Наименование показателя | Значение |
Шаг резьбы Р, мм | 3,175 |
Высота исходного профиля Н, мм | 2,750 |
Высота профиля hv мм | 1 Я1+0’05 1’°1-0,10 |
Рабочая высота профиля h, мм | 1,734 |
Угол профиля а | 60° ±1° |
Зазор Z, мм | 0,076 |
Угол наклона <р | 1°47'24" |
Радиус закругления г, мм | О,5О8+0045 |
Радиус закругления Гр мм | °’432-0,045 |
Конусность 2 tg ср | 1:16 |
17
ГОСТ Р 53201—2023
4.11 Допускаемые предельные отклонения от номинальных размеров труб и фитингов должны соответствовать значениям, приведенным в таблице 13.
Таблица 13 — Предельные отклонения размеров труб и фитингов от номинальных
Наименование показателя | Предельное отклонение |
Длина трубы, % | +5 -5 |
Толщина стенки трубы (фитинга), % | +23,0 -0 |
Конусность резьбы трубы и раструба на длине 1 м на диаметр, мм | +5,208 -2,600 |
Отклонение трубы от прямолинейности (кривизна) на 1 погонный метр, мм | ±2,0 |
Угол между осями углообразующих отводов | ±1° |
Общая длина резьбы, мм | ±3,175 |
Угол профиля резьбы | ±1,0° |
Наружный диаметр фитингов, % | ±10 |
Шаг резьбы на длине 25,4 мм (1 дюйм), мм | ±0,076 |
Шаг резьбы на всей длине резьбы с полным профилем, мм | ±0,152 |
Глубина буртика муфтовой части резьбы, мм | ±3,18 |
Примечания 1 Предельные отклонения конусности (отклонения от разности двух диаметров) приняты на длине один метр и относятся к среднему диаметру резьбы трубы и раструба, а также к наружному диаметру резьбы раструба. 2 Предельные отклонения шага резьбы на длине, не превышающей 25,4 мм, допускаются для расстояния между любыми двумя нитками с профилем. Для расстояния между нитками более 25,4 мм допускается увеличение предельных отклонений, пропорционально увеличению расстояния, но не свыше указанных в настоящей таблице для всей резьбы с полным профилем. 3 Предельные отклонения труб по наружному диаметру настоящим стандартом не регламентируются, их устанавливают в конструкторской документации. |
4.12 Предельные отклонения массы труб и фитингов не должны превышать +14 %.
4.13 Образующая наружных поверхностей фитингов должна лежать в одной плоскости. Отклонение образующей наружных поверхностей фитингов от горизонтальной плоскости не должно превышать 3,0 мм.
4.14 Не допускается разностенность в плоскости торца раструбного конца трубы более 2,0 мм.
4.15 Концы труб должны быть перпендикулярны к продольной оси и иметь фаски, соответствующие указанным в конструкторской документации.
4.16 Предельные отклонения от перпендикулярности торцевой поверхности к продольной оси трубы не должны превышать 3,0 мм.
4.17 Овальность труб относительно их наружного диаметра не должна превышать 5 %.
4.18 Место перехода раструбного конца трубы к ее гладкой части с толщиной стенки (см. рисунок 1) не должно иметь резких уступов.
4.19 Толщина стенки в переходной части раструбного конца не должна быть менее минимально допустимой толщины стенки гладкой части трубы.
18
ГОСТ Р 53201—2023
5 Технические требования
5.1 Трубы и фитинги следует изготовлять методом намотки ровингов из стекловолокна, пропитанных эпоксидным компаундом.
Допускается применение армирующих наполнителей из базальтоволокна при соответствии изготовленных труб и фитингов требованиям настоящего стандарта.
Трубы и фитинги должны соответствовать требованиям настоящего стандарта и быть изготовлены по конструкторской и технологической документации, утвержденной в установленном порядке.
В случае устройства тепловой изоляции наружной поверхности трубопроводов, монтируемых из труб и фитингов, теплоизоляционная конструкция должна соответствовать требованиям пожарной и промышленной безопасности.
5.2 Характеристики
5.2.1 Основные характеристики полимерного композита труб и фитингов должны соответствовать требованиям, приведенным в таблице 14.
Таблица 14 — Основные характеристики полимерного композита труб и фитингов
Наименование показателя | Значение показателя |
Физико-механические характеристики | |
Предел прочности при растяжении, МПа, не менее: в осевом (продольном) направлении в окружном (поперечном) направлении | 160 250 |
Модуль упругости при растяжении, МПа, не менее: в осевом (продольном) направлении в окружном (поперечном) направлении | 10000 20000 |
Физико-химические характеристики | |
Плотность, кг/м3 | 1800—2100 |
Водопоглощение, %, не более | 0,15 |
5.2.2 Степень отверждения материала матрицы (эпоксидного компаунда) полимерного композита труб и фитингов должна быть не менее 95 %.
5.2.3 Температура стеклования материала матрицы (эпоксидного компаунда) полимерного композита труб и фитингов должна превышать на 30 °C максимальную температуру транспортируемой среды и быть не менее 75 °C.
5.2.4 Цвет полимерного композита материала изделий (труб; фитингов), входящих в одну партию, должен быть одинаков. Изменение цвета наружной поверхности в процессе эксплуатации не допускается.
5.2.5 Миграция красителей из полимерного композита в процессе эксплуатации не допускается.
5.2.6 Полимерный композит должен допускать нанесение на поверхность труб и фитингов лакокрасочных материалов, определенных конструкторской документацией.
5.2.7 Полимерный композит труб и фитингов для наземных и надземных трубопроводов должен сохранять свои характеристики и быть стойким к внешним воздействиям влаги, повышенной температуры, климатических факторов, пониженной температуры. Показатели стойкости полимерного композита труб и фитингов к внешним воздействиям приведены в таблице 15.
Стойкость полимерного композита труб и фитингов к внешним воздействиям подтверждается коэффициентами сохранения свойств материала после воздействия влаги, повышенной температуры, климатических факторов, пониженной температуры соответственно. Численные значения коэффициентов сохранения свойств полимерного композита должны соответствовать требованиям, указанным в таблице 15.
19
ГОСТ Р 53201—2023
Таблица 15 — Показатели стойкости полимерного композита труб и фитингов к внешним воздействиям
Наименование показателя | Значение коэффициента сохранения свойств, не более | Метод испытания |
Влагостойкость, Кв | 1,2 | По 9.10 |
Термостойкость, Кт | 1,2 | По 9.11 |
Стойкость к климатическому старению, Ккс | 1,2 | По 9.12 |
Морозостойкость, Км | 1,1 | По 9.13 |
Влагостойкость, термостойкость, стойкость к климатическому старению, морозостойкость определяют по изменению пределов прочности при растяжении в осевом и окружном направлении после воздействия влаги, повышенной температуры, климатических факторов и пониженной температуры соответственно.
5.2.8 Линейные трубы, фитинги и их соединения в процессе эксплуатации должны сохранять прочность и герметичность при воздействии постоянного внутреннего гидравлического давления.
5.2.9 Сопротивление стенки линейной трубы (фитинга) кратковременному воздействию внутреннего гидравлического давления должно соответствовать установленному в конструкторской документации и обеспечивать работоспособность труб (фитингов) в составе трубопровода, исходя из режимов и условий эксплуатации в течение всего срока службы.
5.2.10 Линейные трубы, фитинги и их соединения должны выдерживать без разрушения и потери герметичности воздействие кратковременного внутреннего гидростатического давления, составляющего не менее 230 % номинального значения.
5.2.11 Линейные трубы, фитинги и их соединения должны выдерживать без разрушения и потери герметичности воздействие постоянного внутреннего гидростатического давления, составляющего не менее 150 % номинального значения в течение не менее 120 с.
5.2.12 Линейные трубы, фитинги и их соединения должны выдерживать без разрушения и потери герметичности воздействие постоянного внутреннего гидростатического давления, составляющего не менее 125 % номинального значения в течение не менее 12 ч.
5.2.13 Насосно-компрессорные и обсадные трубы и их соединения в процессе эксплуатации должны сохранять герметичность при одновременном воздействии постоянного внутреннего гидростатического давления и постоянной внешней осевой нагрузки.
Сопротивление стенки трубы воздействию постоянного внутреннего гидростатического давления и постоянной внешней осевой нагрузки должно соответствовать установленному в конструкторской документации и обеспечивать работоспособность трубы в составе трубопровода, исходя из режимов и условий эксплуатации.
Предельно допустимые значения давления, нагрузок и сопротивления материала стенки трубы определяют расчетным путем в соответствии с требованиями настоящего стандарта, режимами и условиями эксплуатации и указывают в конструкторской документации.
5.2.14 Насосно-компрессорные и обсадные трубы и их соединения должны выдерживать без разрушения и потери герметичности:
- воздействие кратковременного внутреннего гидростатического давления, составляющего не менее 230 % номинального значения;
- воздействие постоянного внутреннего гидростатического давления, составляющего не менее 150 % номинального значения в течение не менее 120 с;
- одновременное воздействие постоянного внутреннего гидростатического давления и постоянной внешней осевой нагрузки в течение не менее 120 с.
5.2.15 Допускается по согласованию между потребителем и производителем определять дополнительные к требованиям настоящего стандарта характеристики полимерного композита труб и/или фитингов, труб, фитингов, обусловленные особенностями условий их эксплуатации.
5.3 Требования к внешнему виду
5.3.1 Трубы и фитинги должны иметь гладкие однородные наружные и внутренние поверхности без вздутий, расслоений, раковин, углублений, инородных включений и иных дефектов, приводящих к
20
ГОСТ Р 53201—2023
их отбраковке, и соответствующие в части отсутствия данных дефектов контрольному образцу-эталону, утвержденному в установленном порядке.
5.3.2 Перечень возможных дефектов поверхности труб, критерии их допустимости и рекомендуемые корректирующие действия приведены в приложении А. Порядок оформления и утверждения контрольного образца-эталона внешнего вида приведен в приложении Б.
5.3.3 Допускается незначительная волнистость на наружной поверхности труб и фитингов, не выходящая за пределы допуска на толщину стенки.
5.3.4 На внутренней поверхности труб и фитингов не должны быть видны выступающие волокна.
На внутренней поверхности труб и фитингов не допускаются раковины, являющиеся следствием поверхностных воздушных включений.
5.3.5 Царапины, потертости на поверхности труб и фитингов допускаются, если их глубина не превышает толщины поверхностного слоя смолы (армирующие волокна не выступают на поверхность).
Если глубина царапины превышает толщину поверхностного слоя смолы и визуально зафиксировано повреждение армирующих волокон, трубу или фитинг отбраковывают до принятия решения изготовителем о возможности их использования и маркируют соответствующим образом.
5.3.6 Требования к цвету наружной поверхности труб и фитингов и качеству покрытий при их эксплуатации должны соответствовать установленным в конструкторской документации.
5.4 Требования к резьбовым соединениям
5.4.1 Резьба должна быть полного профиля, без сорванных и недооформленных ниток.
Резьба должна обеспечивать свинчиваемость труб и фитингов.
5.4.2 Резьба должна быть гладкой, без разрывов, сколов, выкрашиваний и других дефектов, нарушающих непрерывность витков, а также прочность и герметичность резьбового соединения.
5.4.3 Возможные технологические дефекты наружной и внутренней резьбы, критерии их допустимости и рекомендуемые корректирующие действия приведены в приложении В.
5.4.4 Резьба раструбов и ниппелей должна быть защищена от повреждений специальными предохранительными колпачками и пробками.
Колпачок должен иметь такую длину, чтобы при навинчивании его на ниппель видимыми оставались не более трех витков резьбы.
Длина пробки должна закрывать не менее двух третей длины резьбы раструба.
5.5 Требования к сырью и материалам
5.5.1 Сырье и материалы, применяемые для изготовления труб и фитингов, должны соответствовать требованиям документов по стандартизации или технической документации, иметь сопроводительную документацию, включая протоколы испытаний, и должны быть подвергнуты входному контролю.
5.5.2 В случае отсутствия сопроводительной документации, включая протоколы испытаний или при несоответствии технологическим требованиям по результатам входного контроля, сырье и материалы применению не подлежат.
5.6 Маркировка
5.6.1 Каждая труба и каждый фитинг должны иметь маркировку, содержащую минимально необходимый объем информации для однозначной идентификации и верификации изделия в течение всего его жизненного цикла.
5.6.2 Маркировку следует наносить способом, не ухудшающим качество трубы или фитинга. Способ нанесения маркировки должен обеспечивать ее сохранность в процессе транспортирования, хранения и эксплуатации.
Допускается по согласованию между потребителем и производителем осуществлять маркировку с помощью RFID-метки, хранящей уникальный идентификатор трубы/фитинга.
Примечание — Способ нанесения маркировки следует устанавливать в конструкторской документации.
5.6.3 Маркировку следует наносить на наружную поверхность каждой трубы или фитинга:
- для труб — на расстоянии 600—800 мм от торца трубы;
- для фитингов — в соответствии с конструкторской документацией.
21
ГОСТ Р 53201—2023
RFID-метка (при маркировке с помощью RFID-метки) должна находиться на наружной поверхности каждой трубы или фитинга под полимерным композитом, соединенным с материалом трубы или фитинга клеевым способом.
5.6.4 Маркировка должна включать:
- наименование или товарный знак предприятия-изготовителя;
- условное обозначение трубы в соответствии с 4.4 или фитинга в соответствии с 4.5;
- номер партии;
- дату изготовления (месяц, год).
5.6.5 Маркировка должна сохраняться в течение всего срока службы трубы или фитинга при хранении, транспортировании, погрузочно-разгрузочных работах и эксплуатации.
5.6.6 При маркировке с помощью RFID-метки:
- уникальный идентификатор трубы/фитинга должен быть однократно записан на предприятии-изготовителе трубы/фитинга после приемки отделом технического контроля предприятия и многократно считываться ридером, хранящим минимально необходимый объем информации об изделии;
- маркировка, нанесенная с помощью RFID-метки, должна оставаться легко считываемой ридером в течение всего срока службы трубы или фитинга;
- диапазон рабочих частот меток — от 865 до 868 МГц;
- рабочая температура от минус 60 °C до плюс 60 °C.
Примечание — Требования к содержанию минимально необходимого объема информации приведены в приложении Г.
5.6.7 Дополнительно к маркировке по 5.6.1—5.6.6 каждая партия труб/фитингов должна сопровождаться паспортом качества, содержащим следующую информацию:
- наименование или товарный знак предприятия-изготовителя;
- адрес предприятия-изготовителя;
- наименование и условное обозначение продукции;
- условное обозначение трубы/фитинга в соответствии с 4.4/4.5;
- номер партии;
- количество изделий в партии (для труб — в метрах, для фитингов — в штуках);
- дату изготовления (месяц, год);
- реквизиты документов о подтверждении соответствия изделий требованиям настоящего стандарта (сертификаты соответствия, протоколы испытаний);
- информацию о пригодности изделий для использования в хозяйственно-питьевом водоснабжении с указанием реквизитов документа о подтверждении соответствия (пригодности) — только для труб, применяемых в системах технического водоснабжения и/или питьевого и хозяйственно-бытового водоснабжения;
- условия и сроки хранения;
- отметку технического контроля (штамп ОТК) о соответствии изделий требованиям настоящего стандарта.
К паспорту качества должны быть приложены, заверенные руководителем и круглой печатью предприятия-изготовителя, копии документов о подтверждении соответствия изделий требованиям настоящего стандарта (сертификаты соответствия, протоколы испытаний) и документов о пригодности изделий для использования в системах технического водоснабжения и/или питьевого и хозяйственнобытового водоснабжения с учетом требований по 6.11 или о запрете использования изделий из данной партии в системах водоснабжения.
Допускается указывать в паспорте качества дополнительные сведения.
5.6.8 Транспортную маркировку наносят в соответствии с требованиями ГОСТ 14192.
5.7 Упаковка
5.7.1 Трубы укладывают на деревянные поддоны по ГОСТ 33757.
При укладке между трубами следует прокладывать мягкие ложементы для их защиты от механических повреждений в процессе транспортирования.
5.7.2 При упаковывании труб используют средства скрепления грузов по ГОСТ 21650 или другие средства, по качеству не ниже указанных.
5.7.3 Фитинги упаковывают в деревянные ящики по ГОСТ 10198, ящики из гофрированного картона по ГОСТ 9142, мешки из полиэтиленовой пленки по ГОСТ 10354 или бумажные мешки по ГОСТ 2226. 22
ГОСТ Р 53201—2023
5.7.4 Допускается по согласованию с потребителем использование другого вида упаковки, обеспечивающей сохранность труб и фитингов при транспортировании и хранении, а также безопасность при погрузочно-разгрузочных работах.
5.7.5 Каждая партия труб/фитингов должна сопровождаться руководством по монтажу и эксплуатации. Порядок передачи потребителю сопроводительных документов, включая руководство по монтажу и эксплуатации, определяют по согласованию между потребителем и производителем.
6 Требования безопасности
6.1 По степени воздействия вредных веществ на организм человека полимерные композиты при их производстве и механической обработке относятся к 3-му классу опасности по ГОСТ 12.1.007.
6.2 При механической обработке полимерного композита в воздушную среду выделяется пыль полимерного композита, которая раздражающе действует на слизистые оболочки дыхательных путей и кожные покровы работающих, вызывая зуд кожи.
6.3 При производстве и переработке полимерных композитов на основе эпоксидных компаундов возможны выделения в воздушную среду паров толуола, стеклянной пыли, пыли полимерного композита.
6.4 Предельно допустимые концентрации (ПДК) в воздухе рабочей зоны и классы опасности указанных веществ согласно ГОСТ 12.1.005 и гигиеническим нормативам [3] приведены в таблице 16.
Таблица 16 — Предельно-допустимые концентрации веществ в воздухе рабочей зоны
Наименование веществ | ПДК, мг/м3 | Класс опасности | ||
по ГОСТ 12.1.005 | по [3] | по ГОСТ 12.1.005 | по [3] | |
Толуол | 50 | 150/50 | III | 3 |
Стеклянная пыль | 2 | 6/2 | III | 3 |
Пыль полимерного композита | 5 | 5 | III | 3 |
Примечание — При наличии двух значений: в числителе указано значение максимально разовой предельно допустимой концентрации (ПДК м.р.), в знаменателе — среднесменной предельно допустимой концентрации (ПДК с.с). |
6.5 При попадании на кожу рук эпоксидный компаунд вызывает раздражения и дерматиты.
Толуол обладает токсическим действием на нервную систему и печень, раздражает дыхательные пути.
Стеклянная пыль и пыль полимерного композита раздражающе действует на слизистые дыхательных путей и кожу.
6.6 Для защиты органов дыхания от пыли необходимо использовать респиратор марки ШБ-1 «Лепесток» и общие средства защиты по ГОСТ 12.4.011. Для защиты кожи рук необходимо применять защитные средства для рук по ГОСТ Р 12.4.301.
6.7 Требования безопасности при производстве труб и фитингов должны соответствовать ГОСТ 12.3.030.
6.8 Производственные помещения, в которых проводят механическую обработку полимерного композита, должны быть оборудованы приточно-вытяжной вентиляцией, отвечающей требованиям ГОСТ 12.4.021 и обеспечивающей состояние воздушной среды в соответствии с ГОСТ 12.1.005 и гигиеническими нормативами [3].
Пыль должна улавливаться пылеулавливающими установками.
6.9 Полимерные композиты труб и фитингов, изготавливаемых в соответствии с настоящим стандартом, относятся к трудногорючим материалам по ГОСТ 12.1.044.
6.10 Производственные помещения должны быть оборудованы всеми необходимыми средствами пожаротушения.
Средства пожаротушения: углекислотные и порошковые огнетушители, вода, пар, асбестовое полотно, песок — должны применяться в соответствии с правилами по безопасному ведению работ. При значительных очагах пожара применяют объемное тушение.
23
ГОСТ Р 53201—2023
6.11 Трубы и фитинги систем технического водоснабжения, питьевого и хозяйственно-бытового водоснабжения должны обеспечивать качество и безопасность транспортируемой воды в соответствии с требованиями [3].
7 Требования охраны окружающей среды
7.1 Стеклянная пыль и пыль дисперсных наполнителей должна улавливаться и возвращаться в производство.
7.2 Отходы производства — обрезки стекловолокна, базальтоволокна и/или полимерного композитного материала, должны подвергаться утилизации или переработке.
7.3 Отходы, не подлежащие переработке, уничтожают в соответствии с санитарными правилами, предусматривающим порядок накопления, транспортирования, обезвреживания и захоронения промышленных отходов.
7.4 Правила контроля качества воздуха — по ГОСТ 17.2.3.01 и ГОСТ Р 58577.
Выделяющиеся в атмосферу пыль полимерного композита и другие вредные вещества не должны превышать установленные нормы ПДК.
7.5 При аварийном загрязнении требования к контролю и охране почвы — по ГОСТ Р 70280, воды — по ГОСТ 17.1.3.13.
8 Правила приемки
8.1 Трубы и фитинги принимают партиями.
Партией считают количество труб и фитингов одного внутреннего диаметра и толщины стенки, изготовленных из идентичных исходных компонентов и по одному технологическому процессу, сдаваемых одновременно и сопровождаемых одним документом о качестве.
8.2 Размер партии труб должен быть не более 1525 м.
Размер партии фитингов определяют согласно условиям заказа по каждому их типу.
8.3 Паспорт качества оформляют по 5.6.7. Уникальный идентификатор (при маркировке с помощью RFID-метки) записывают на RFID-метку, устанавливаемую на каждую трубу/фитинг.
8.4 Для проверки соответствия труб и фитингов требованиям настоящего стандарта проводят квалификационные, приемо-сдаточные, периодические и типовые испытания.
8.5 Для проведения квалификационных испытаний изготавливают образцы в соответствии с разработанной конструкторской документацией в количестве не менее 5 шт.
Для проведения приемо-сдаточных, периодических и типовых испытаний от партии методом случайного отбора выбирают 5 % изделий, но не менее 5 шт., за исключением испытаний для определения показателей по пунктам 4—6, пункту 14 и пункту 16 таблицы 17.
Для проведения испытаний по пунктам 14 и 16 таблицы 17 методом случайного отбора от партии выбирают не менее 2 шт. изделий (труб; фитингов).
Испытания по пунктам 4—6 таблицы 17 проводят на одном произвольно взятом изделии (трубе; фитинге).
Примечания
1 Допускается формировать выборки у изготовителя равномерно в течение всего процесса производства.
2 Материал для испытаний по пунктам 4—6 таблицы 17 отбирают из технологического припуска трубы (фитинга).
8.6 Приемке продукции, выпуск которой начат предприятием-изготовителем впервые (при постановке на производство), должны предшествовать квалификационные испытания.
8.7 Приемо-сдаточные испытания проводят с целью контроля соответствия характеристик продукции требованиям настоящего стандарта. Приемо-сдаточным испытаниям подвергают каждую партию труб и фитингов.
8.8 Периодические испытания проводят с целью: периодического подтверждения качества продукции и стабильности технологического процесса в установленный период, подтверждения возможности продолжения изготовления продукции по действующей конструкторской и технологической документации и продолжения приемки продукции.
Периодические испытания проводят не реже одного раза в 12 мес на выборке, отобранной по 8.5 от партии, прошедшей приемо-сдаточные испытания.
24
ГОСТ Р 53201—2023
8.9 Типовые испытания проводят с целью оценки эффективности и целесообразности предлагаемых изменений в конструкцию или технологию изготовления, которые могут повлиять на технические характеристики продукции, связанные с безопасностью для жизни, здоровья или имущества граждан, либо могут повлиять на эксплуатацию продукции, в том числе на важнейшие потребительские свойства продукции или на соблюдение условий охраны окружающей среды, при замене исходных материалов, при переносе производства на другое предприятие — на выборке, отобранной по 8.5 от партии, прошедшей приемо-сдаточные испытания.
8.10 Состав и виды испытаний, проводимых для проверки соответствия труб и фитингов требованиям настоящего стандарта, приведены в таблице 17.
Таблица 17 — Состав и виды испытаний
Наименование показателя | Номер пункта настоящего стандарта | Вид испытаний | ||
технических требований | методов контроля | Приемосдаточные | Периодические | |
1 Внешний вид труб, фитингов резьбовых соединений, цвет | 5.2.4; 5.3; 5.4 | 9.2 | + | + |
2 Размеры труб, фитингов, их предельные отклонения; овальность; параметры резьбы | 4.6—4.7; 4,9—4.11; 4.17 | 9.3 | + | + |
3 Масса труб, фитингов | 4.6—4.7,4.12 | 9.4 | + | + |
4 Плотность полимерного композита | 5.2.1 | 9.5 | + | + |
5 Водопоглощение полимерного композита | 5.2.1 | 9.6 | + | + |
6 Степень отверждения материала матрицы полимерного композита | 5.2.2 | 9.7 | + | + |
7 Температура стеклования материала матрицы полимерного композита | 5.2.3 | 9.8 | — | + |
8 Предел прочности и модуль упругости при растяжении полимерного композита в осевом (продольном) направлении | 5.2.1 | 9.9 | — | + |
9 Предел прочности и модуль упругости при растяжении полимерного композита в окружном (поперечном) направлении | 5.2.1 | 9.9 | — | + |
10 Влагостойкость | 5.2.7 | 9.10 | — | — |
11 Термостойкость | 5.2.7 | 9.11 | — | — |
12 Стойкость к климатическому старению | 5.2.7 | 9.12 | — | — |
13 Морозостойкость | 5.2.7 | 9.13 | — | — |
14 Прочность и герметичность труб, фитингов и их соединений при воздействии кратковременного внутреннего гидростатического давления, составляющего не менее 230 % номинального значения | 5.2.10, 5.2.14 | 9.14 | — | + |
15 Прочность и герметичность труб, фитингов и их соединений при воздействии постоянного внутреннего гидростатического давления, составляющего не менее 150 % номинального значения | 5.2.11, 5.2.14 | 9.15 | + | + |
25
ГОСТ Р 53201—2023
Окончание таблицы 17
Наименование показателя | Номер пункта настоящего стандарта | Вид испытаний | ||
технических требований | методов контроля | Приемосдаточные | Периодические | |
16 Прочность и герметичность труб, фитингов и их соединений при воздействии постоянного внутреннего гидростатического давления, составляющего не менее 125 % номинального значения | 5.2.12 | 9.16 | — | + |
17 Прочность и герметичность труб и их соединений при одновременном воздействии постоянного внутреннего гидростатического давления и постоянной внешней осевой нагрузки | 5.2.14 | 9.17 | + | + |
18 Маркировка | 5.6.1—5.6.6 | 9.18 | + | + |
5.6.7 | 9.18 | + | + | |
19 Упаковка | 5.7 | 9.19 | + | + |
8.11 Квалификационные и типовые испытания проводят по всем показателям таблицы 17 на образцах, изготовленных с учетом требований 8.5 (квалификационные испытания) или отобранных по 8.5 (типовые испытания).
8.12 Приемо-сдаточные и периодические испытания проводят по показателям, приведенным в таблице 17 для данных видов испытаний на образцах, отобранных по 8.5, с учетом требований 8.13.
8.13 Внешний вид труб, фитингов, резьбовых соединений, цвет и маркировку проверяют методом сплошного контроля.
8.14 При получении неудовлетворительных результатов приемо-сдаточных испытаний хотя бы по одному показателю по нему проводят повторные испытания на удвоенной выборке. При получении неудовлетворительных результатов повторных приемо-сдаточных испытаний партию труб или фитингов бракуют. При получении удовлетворительных результатов повторных приемо-сдаточных испытаний бракуют только трубы или фитинги, не прошедшие испытания.
Результаты приемо-сдаточных испытаний оформляют протоколом. Протокол приемо-сдаточных испытаний должен быть включен в комплект сопроводительной документации партии продукции.
8.15 При получении неудовлетворительных результатов периодических испытаний по какому-либо из показателей, проводят анализ причин получения неудовлетворительных результатов и принимают решение о проведении повторных испытаний по данным показателям на удвоенной выборке.
При получении неудовлетворительных результатов повторных периодических испытаний производство труб или фитингов приостанавливают вплоть до устранения причин получения неудовлетворительных результатов. При получении удовлетворительных результатов повторных приемо-сдаточных испытаний бракуют только трубы или фитинги, не прошедшие испытания.
Результаты периодических испытаний оформляют протоколом и предъявляют потребителю по его требованию.
8.16 При получении неудовлетворительных результатов типовых испытаний (при изменении конструкции, технологического процесса, при замене исходных материалов, при переносе производства на другое предприятие) хотя бы по одному из показателей, проводят анализ причин получения неудовлетворительных результатов и принимают решение о проведении повторных испытаний или прекращении проведения данных работ.
Предусмотренные по результатам испытаний изменения (измененный технологический процесс, иные исходные материалы и т. д.) в ранее разработанную и утвержденную документацию не вносят. В отношении продукции, изготовленной в соответствии с предусмотренными изменениями, принимают решение о ее утилизации или возможности ее применения по определенным видам функционального назначения, приведенным в области применения настоящего стандарта с ограничениями или без ограничений.
26
ГОСТ Р 53201—2023
Результаты типовых испытаний оформляют протоколом.
8.17 Результаты квалификационных испытаний оформляют протоколом и хранят в установленном на предприятии порядке вплоть до снятия продукции с производства.
9 Методы контроля
9.1 Испытания следует проводить не ранее чем через 24 ч после окончания полимеризации (отверждения) полимерного композита труб (фитингов).
9.2 Внешний вид труб, фитингов, резьбы проверяют визуально без применения увеличительных приборов путем сравнения с контрольным образцом-эталоном, в части отсутствия дефектов, приводящих к их отбраковке и сопоставления с типами дефектов и критериями приемки, приведенными в приложении А и приложении В.
При необходимости может быть использовано местное освещение.
9.3 Определение размеров труб (фитингов) и их предельных отклонений
9.3.1 Размеры труб и фитингов определяют при температуре (23 ± 5) °C на каждом отобранном образце. Перед испытанием образцы выдерживают при указанной температуре не менее двух часов.
9.3.2 Средства измерений:
- штангенциркуль по ГОСТ 166 с погрешностью измерения 0,1 мм;
- линейка металлическая по ГОСТ 427 с ценой деления 1,0 мм и пределом измерения 1000 мм;
- микрометры типов МТ и МК по ГОСТ 6507;
- угольники поверочные 90° по ГОСТ 3749;
- стенкомеры по ГОСТ 11358 с ценой деления 0,1 мм;
- рулетка по ГОСТ 7502 с ценой деления 1,0 мм и пределом измерения 20 м;
- иные средства измерений по ГОСТ Р 57885.
9.3.3 Определение размеров труб (фитингов) и их предельных отклонений проводят по ГОСТ Р 57885 или по 9.3.4—9.3.12.
9.3.4 Определение наружного диаметра труб и фитингов проводят по ГОСТ Р ИСО 3126. Измерение наружного диаметра труб проводят на расстоянии не менее 100 мм от торцов. Измерение наружного диаметра фитингов проводят на расстоянии не менее 10 мм от торцов. Допускается определять наружный диаметр труб как среднее арифметическое значение результатов четырех равномерно распределенных измерений.
9.3.5 Измерение номинального диаметра труб и фитингов проводят по ГОСТ Р 58939 штангенциркулем в двух взаимно перпендикулярных направлениях в сечении, удаленном от торца не менее чем на 10 мм.
9.3.6 Толщину стенки труб определяют по ГОСТ Р ИСО 3126 микрометром типа МТ или стенко-мером на каждом отобранном образце с обоих торцов на расстоянии не менее 10 мм от их кромки, не менее чем в шести точках, равномерно расположенных по окружности трубы.
Допускается по согласованию между потребителем и производителем и/или аккредитованной испытательной лабораторией применение альтернативных методов контроля толщины стенки труб.
9.3.7 Измерение длины труб, а также ширины фланца (размеры А и В) фитингов проводят по наружной поверхности металлической линейкой или рулеткой.
Установленные размеры осевых составляющих присоединительной части фитингов обеспечиваются технологической оснасткой при изготовлении.
9.3.8 Угол поворота фитингов проверяют при помощи оптического квадранта или шаблона.
9.3.9 Определение размеров профиля, натяга и конусности резьбы
9.3.9.1 Контроль размеров профиля резьбы раструбов и ниппелей труб и профиля резьбы фитингов следует проводить резьбовыми калибрами-пробками и резьбовыми калибрами-кольцами.
Конусность наружной резьбы по наружному диаметру и внутренней резьбы по внутреннему диаметру проверяют гладкими коническими калибрами-кольцами и калибрами-пробками.
9.3.9.2 При измерении конусности по наружному диаметру наружной резьбы гладкий калибр-кольцо надевают на резьбу, и если при этом имеет место качание в поперечном направлении, то величину имеющегося зазора измеряют с использованием набора пластинчатых щупов шириной 3 мм (для труб диаметром до 130 мм) или 4 мм (для труб больших диаметров).
Зазор в этом случае характеризует отклонение разности диаметров от номинального значения на длине контакта резьбы с калибром.
27
ГОСТ Р 53201—2023
Если гладкий калибр не имеет качания, то щупом проверяют зазоры между калибром и резьбой. Максимальный суммарный зазор, измеренный в двух противоположных по образующей калибра точках, характеризует отклонение разности диаметров на длине калибра.
9.3.9.3 При измерении конусности по внутреннему диаметру внутренней резьбы гладкий калибр-пробку плотно вставляют в резьбу, и если при этом имеет место качание в поперечном направлении, то калибр отжимают к одной стороне резьбы, а образовавшийся зазор измеряют с использованием набора щупов.
Зазор характеризует отклонение разности диаметров от номинального значения на длине контакта калибра с контролируемой поверхностью.
Если гладкий калибр-пробка не имеет качания, то щупом проверяют зазоры между калибром и контролируемой поверхностью по всей окружности.
Максимальный суммарный зазор, измеренный в двух противоположных по образующей калибра точках, характеризует отклонение разности диаметров на длине калибра.
9.3.9.4 Допуск на величину конусности на длине резьбы один метр на диаметр составляет минус 2,600 и плюс 5,208 мм.
При измерении конусности калибрами проводят перерасчет указанной величины допуска на длину используемых при проверке гладких калибров.
9.3.9.5 Натяг резьбы проверяют резьбовыми калибрами-пробками и резьбовыми калибрами-кольцами. Резьбовые калибры должны навинчиваться на резьбу до отказа усилием одного человека с применением рычага длиной, равной двум диаметрам калибра (для диаметров резьбы до 180 мм) или полутора диаметрам (для изделий с резьбой больших размеров).
В зависимости от размера резьбы труб натяги по резьбовому калибру-пробке должны соответствовать:
- размер резьбы 2 дюйма — 6,5 мм;
- размер резьбы 2,5 дюйма — 6,5 мм;
- размер резьбы 4 дюйма — 6,5 мм;
- размер резьбы 6 дюймов — 9,5 мм;
- размер резьбы 8 дюймов — 11 мм.
В зависимости от условного размера резьбы труб натяги по резьбовому калибру-кольцу должны соответствовать:
- размер резьбы 2 дюйма — 11,65 мм;
- размер резьбы 2,5 дюйма — 12,71 мм;
- размер резьбы 4 дюйма — 18,89 мм;
- размер резьбы 6—7 дюймов — 18,89 мм;
- размер резьбы 8 дюймов — 24,89 мм.
Допуск на величину указанных натягов: ±3,18 мм.
9.3.10 Овальность труб определяют как разность между максимальным и минимальным значениями наружного диаметра в одном сечении.
9.3.11 Отклонение трубы от прямолинейности определяют измерением расстояния от трубы до базовой поверхности в процессе поворота трубы вокруг своей оси на 360° на двух опорах, расстояние между которыми должно быть равно 2/3 длины трубы в соответствии со схемой, приведенной на рисунке 12.
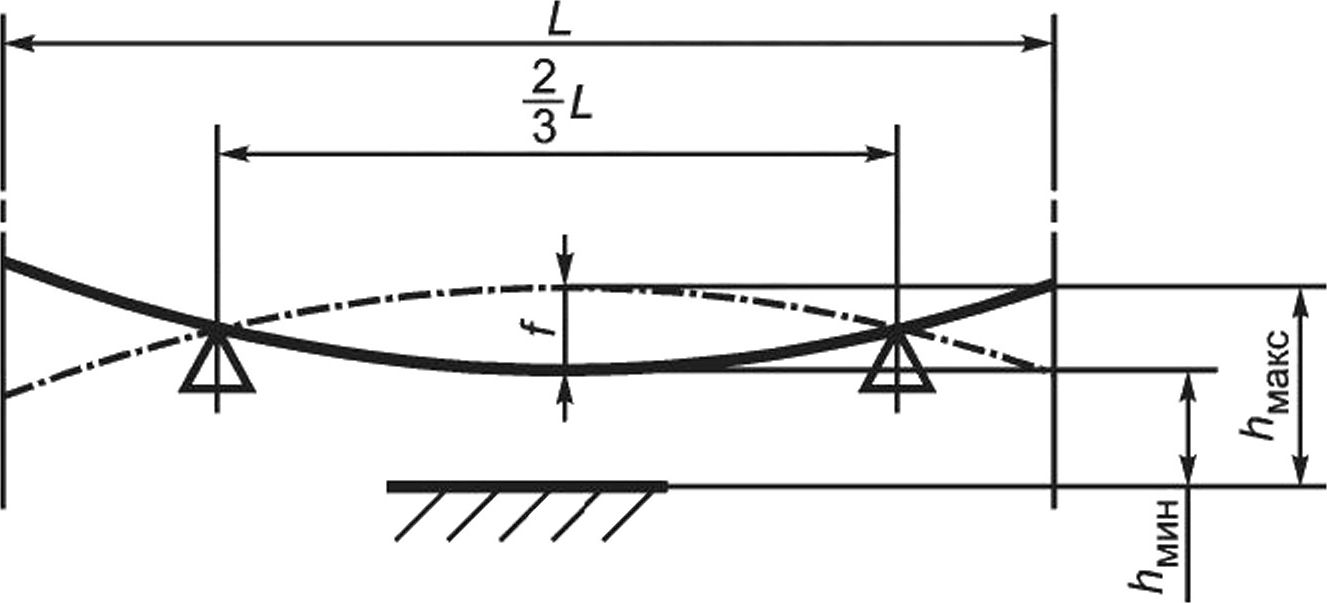
Размер 2/3 L должен быть выдержан с погрешностью не более 1,5 %
Рисунок 12
28
ГОСТ Р 53201—2023
Измеряют максимальное Лмакс и минимальное Лмин значения расстояния от трубы до базовой поверхности в середине между опорами, результат измерения округляют до 1 мм.
За отклонение от прямолинейности Г принимают
^“ (^макс — ^мин)^- (1)
9.3.12 Отклонение от перпендикулярности плоскости торцов труб к их осям определяют измерением линейкой размера наибольшего зазора между торцом ствола трубы и стороной приложенного к ней угольника по ГОСТ 3749 или шаблона.
Сторона угольника или шаблона, прикладываемая к стволу трубы, должна быть равна длине ствола до раструба и соприкасаться с трубой не менее чем в двух точках, а длина другой стороны угольника или шаблона должна быть не менее наружного диаметра ствола трубы.
9.4 Определение массы труб и фитингов осуществляют взвешиванием на весах с погрешностью измерения не более ±10 г.
9.5 Плотность полимерного композита определяют по ГОСТ 15139.
9.6 Водопоглощение полимерного композита определяют по ГОСТ 4650.
9.7 Степень отверждения материала матрицы (эпоксидного компаунда) полимерного композита определяют по ГОСТ Р 57687.
9.8 Температуру стеклования материала матрицы (эпоксидного компаунда) полимерного композита определяют по ГОСТ Р 55135.
9.9 Определение предела прочности и модуля упругости при растяжении
9.9.1 Предел прочности при растяжении полимерного композита труб и фитингов в осевом (продольном) направлении определяют по ГОСТ Р 54924.
9.9.2 Модуль упругости при растяжении полимерного композита труб и фитингов в осевом (продольном) направлении определяют по ГОСТ 32656, при этом подготовку образцов осуществляют по ГОСТ Р 54924—2017 (пункт 6.1.2.4). При использовании криволинейных образцов испытательная машина должна быть оснащена изогнутыми захватами.
9.9.3 Предел прочности при растяжении полимерного композита труб и фитингов в окружном (поперечном) направлении определяют по ГОСТ Р 54925.
9.9.4 Модуль упругости при растяжении полимерного композита труб и фитингов в окружном (поперечном) направлении определяют по ГОСТ Р 54925—2012 (метод В, Г или Д) с учетом следующих изменений и дополнений:
- используют образцы без надрезов;
- обработку результатов испытания проводят по ГОСТ 32656.
9.10 Определение влагостойкости полимерного композита труб и фитингов
9.10.1 Влагостойкость определяют по ГОСТ 9.719—94 (раздел 4).
9.10.2 Сущность метода заключается в том, что образцы полимерного композита труб и фитингов по ГОСТ Р 54924 и по ГОСТ Р 54925 подвергают воздействию водяного тумана в течение не менее 168 ч и определяют изменение пределов прочности при растяжении в осевом и окружном направлении.
9.10.3 Коэффициенты сохранения свойств (влагостойкость) Кв вычисляют по формуле
°РВ
где ор — среднее арифметическое значение предела прочности при растяжении в осевом (окружном) направлении полимерного композита труб (фитингов) до испытаний (в исходном состоянии), МПа;
йрв — среднее арифметическое значение предела прочности при растяжении в осевом (окружном) направлении полимерного композита труб (фитингов) после испытаний, МПа.
9.10.4 Средние арифметические значения пределов прочности при растяжении в осевом (окружном) направлении образцов полимерного композита труб (фитингов) до (в исходном состоянии) бр и после йрв испытаний вычисляют в соответствии с ГОСТ 14359—69 (пункт 4.3).
29
ГОСТ Р 53201—2023
9.11 Определение термостойкости полимерного композита труб и фитингов
9.11.1 Сущность метода заключается в том, что образцы полимерного композита труб и фитингов подвергают нагреву до заданной температуры и определяют стойкость к указанному воздействию по изменению пределов прочности при растяжении в осевом и окружном направлении.
9.11.2 Оборудование для определения пределов прочности при растяжении в осевом направлении — по ГОСТ Р 54924, для определения пределов прочности при растяжении в окружном направлении — по ГОСТ Р 54925, а также термокамера для испытательных машин.
9.11.3 Для испытания применяют образцы:
- для определения пределов прочности при растяжении в осевом направлении — по ГОСТ Р 54924;
- для определения пределов прочности при растяжении в окружном направлении — по ГОСТ Р 54925.
9.11.4 На контрольных образцах определяют исходный предел прочности:
- при растяжении в осевом направлении — по ГОСТ Р 54924;
- при растяжении в окружном направлении — по ГОСТ Р 54925.
9.11.5 Основные образцы нагревают в термокамере до температуры 60 °C. Время выдержки образцов при заданной температуре должно быть не менее 20 мин на 1 мм его толщины.
9.11.6 Проводят испытания основных образцов и обработку результатов:
- для предела прочности при растяжении в осевом направлении — по ГОСТ Р 54924;
- для предела прочности при растяжении в окружном направлении — по ГОСТ Р 54925.
9.11.7 Коэффициенты сохранения свойств (термостойкость) Кт вычисляют по формуле
(3) ПРТ
где ор — среднее арифметическое значение предела прочности при растяжении в осевом (окружном) направлении полимерного композита труб (фитингов) до испытаний (в исходном состоянии), МПа;
GpT — среднее арифметическое значение предела прочности при растяжении в осевом (окружном) направлении полимерного композита труб (фитингов) после испытаний, МПа.
9.11.8 Средние арифметические значения пределов прочности при растяжении в осевом (окружном) направлении образцов полимерного композита труб (фитингов) до (в исходном состоянии) йр и после аРТ испытаний вычисляют в соответствии с ГОСТ 14359—69 (пункт 4.3).
9.12 Определение стойкости к климатическому старению полимерного композита труб и фитингов
9.12.1 Стойкость к климатическому старению определяют по ГОСТ 9.708—83 (метод 2).
Сущность метода заключается в том, что образцы полимерного композита труб и фитингов по ГОСТ Р 54924 и по ГОСТ Р 54925 подвергают воздействию искусственно созданных факторов в аппарате искусственной погоды в течение заданной продолжительности испытаний и определяют изменение пределов прочности при растяжении в осевом и окружном направлении.
Искусственные факторы и время воздействия устанавливают в соответствии с ГОСТ Р 57942— 2017 (таблица 6). Количество образцов после одного периода испытаний должно быть не менее 5.
9.12.2 Коэффициент сохранения свойств (стойкость к климатическому старению) Ккс вычисляют по формуле
«КС = <4)
СРКС
где ор — среднее арифметическое значение предела прочности при растяжении в осевом (окружном) направлении полимерного композита труб (фитингов) до испытаний (в исходном состоянии), МПа;
йркс — среднее арифметическое значение предела прочности при растяжении в осевом (окружном) направлении полимерного композита труб (фитингов) после испытаний, МПа.
30
ГОСТ Р 53201—2023
9.12.3 Средние арифметические значения пределов прочности при растяжении в осевом (окружном) направлении образцов полимерного композита труб (фитингов) до (в исходном состоянии) ор и после йркс испытаний вычисляют в соответствии с ГОСТ 14359—69 (пункт 4.3).
9.13 Определение морозостойкости полимерного композита труб и фитингов
9.13.1 Морозостойкость полимерного композита труб и фитингов определяется по ГОСТ Р 57942— 2017 (пункт 6.4) с изменениями по 9.13.2—9.13.9.
9.13.2 Сущность метода заключается в том, что образцы полимерного композита труб и фитингов подвергают многократному замораживанию и оттаиванию и определяют стойкость к указанному воздействию по изменению пределов прочности при растяжении в осевом и окружном направлении.
9.13.3 Для испытания применяют образцы:
- для определения пределов прочности при растяжении в осевом направлении основных и контрольных образцов — по ГОСТ Р 54924;
- для определения пределов прочности при растяжении в окружном направлении основных и контрольных образцов — по ГОСТ Р 54925.
9.13.4 Контрольные образцы извлекают из раствора, обтирают влажной тканью, взвешивают и испытывают:
- для определения пределов прочности при растяжении в осевом направлении — по ГОСТ Р 54924;
- для определения пределов прочности при растяжении в окружном направлении — по ГОСТ Р 54925.
9.13.5 Число циклов замораживания и оттаивания, после которых определяют пределы прочности при растяжении в осевом и окружном направлении, принимают равным 100.
9.13.6 Основные образцы после проведения заданного числа циклов замораживания и оттаивания осматривают. Материал, отделяющийся от образца, снимают жесткой капроновой щеткой. Образцы обтирают влажной тканью, взвешивают и испытывают для определения пределов прочности при растяжении в осевом и окружном направлении.
9.13.7 Основные образцы испытывают:
- для определения пределов прочности при растяжении в осевом направлении — по ГОСТ Р 54924;
- для определения пределов прочности при растяжении в окружном направлении — по ГОСТ Р 54925.
9.13.8 Коэффициенты сохранения свойств (морозостойкость) Км вычисляют по формуле
К, <5)
°РМ
где ор — среднее арифметическое значение предела прочности при растяжении в осевом (окружном) направлении контрольных образцов полимерного композита труб (фитингов) до испытаний (в исходном состоянии), МПа;
йрм — среднее арифметическое значение предела прочности при растяжении в осевом (окружном) направлении основных образцов полимерного композита труб (фитингов) после испытаний, МПа.
9.13.9 Средние арифметические значения пределов прочности при растяжении в осевом (окружном) направлении контрольных йр и основных орм образцов полимерного композита труб (фитингов) вычисляют в соответствии с ГОСТ 14359—69 (пункт 4.3).
9.14 Прочность и герметичность труб, фитингов и их соединений при воздействии кратковременного внутреннего гидростатического давления, составляющего не менее 230 % номинального значения
9.14.1 Прочность и герметичность труб и фитингов при воздействии кратковременного внутреннего гидростатического давления, составляющего не менее 230 % номинального значения, определяют на трубах и фитингах по ГОСТ 34648—2020 (пункт 6.2, метод Б) с изменениями по 9.14.1.1—9.14.1.4.
31
ГОСТ Р 53201—2023
9.14.1.1 При проведении испытания применяют торцевые заглушки по ГОСТ 34646—2020 (пункт 4.2, рисунок 1), передающие осевые напряжения на образец.
9.14.1.2 Допускается, по согласованию между потребителем и производителем, определять прочность и герметичность труб, фитингов и их соединений на сборных узлах. Соединения образцов в трубопроводы (сборные узлы) осуществляют следующим образом:
- от каждой отобранной трубы отрезают два образца такой длины, чтобы свободная длина сборного узла составляла (1500 ± 50) мм;
- образцы труб соединяют фитингом;
- на концах собранного узла монтируют торцевые заглушки.
9.14.1.3 Скорость повышения давления следует устанавливать таким образом, чтобы в интервале от 60 до 70 с было достигнуто или превышено заданное минимальное внутреннее гидростатическое давление (230 % номинального значения) без разрушения трубы, фитинга или сборного узла.
9.14.1.4 Под разрушением трубы, фитинга или сборного узла понимают:
- резкое (мгновенное) падение внутреннего давления в трубе, фитинге или сборном узле;
- прерывистое и неравномерное повышение внутреннего давления в трубе, фитинге или сборном узле;
- любое визуально-заметное прохождение рабочей среды через стенку трубы, фитинга или любого элемента сборного узла;
- течь в торцевой заглушке.
9.14.2 Квалификационные испытания проводят на пяти образцах труб или пяти образцах фитингов одного номинального диаметра и давления или пяти сборных узлах одного номинального диаметра и давления, собранных из образцов, отобранных по 8.5.
9.14.3 Периодические и типовые испытания проводят на двух образцах труб или двух образцах фитингов одного номинального диаметра и давления или двух сборных узлах одного номинального диаметра и давления, собранных из образцов, отобранных по 8.5.
9.15 Прочность и герметичность труб, фитингов и их соединений при воздействии постоянного внутреннего гидростатического давления, составляющего не менее 150 % номинального значения
9.15.1 Прочность и герметичность труб и фитингов при воздействии постоянного внутреннего гидростатического давления, составляющего не менее 150% номинального значения, определяют на трубах и фитингах по ГОСТ 34648—2020 (пункт 6.2, метод Б) с изменениями по 9.14.1.1—9.14.1.2, 9.14.1.4 и изменением 9.15.1.1.
9.15.1.1 Скорость повышения давления следует устанавливать таким образом, чтобы в течение до 70 с было достигнуто заданное постоянное внутреннее гидростатическое давление (150 % номинального значения) без разрушения трубы, фитинга или сборного узла. После чего труба, фитинг или сборный узел выдерживают под достигнутым давлением в течение не менее 120 с.
9.15.2 Испытания проводят на пяти образцах труб или пяти образцах фитингов одного номинального диаметра и давления или пяти сборных узлах одного номинального диаметра и давления, собранных из образцов, отобранных по 8.5.
Примечание — Четыре трубы выдерживают под давлением не менее 120 с и одну трубу — не менее 600 с.
9.15.3 Оборудование и условия проведения испытаний — по ГОСТ 34648, точность поддержания испытательной установкой заданного внутреннего гидростатического давления в течение цикла нагружения — по ГОСТ 34646.
9.16 Прочность и герметичность труб, фитингов и их соединений при воздействии постоянного внутреннего гидравлического давления, составляющего не менее 125 % номинального значения
9.16.1 Прочность и герметичность труб и фитингов при воздействии постоянного внутреннего гидростатического давления, составляющего не менее 125% номинального значения, определяют на трубах и фитингах по ГОСТ 34648—2020 (пункт 6.2, метод Б) с изменениями по 9.14.1.1—9.14.1.2, 9.14.1.4 и изменением 9.16.1.1 :
9.16.1.1 Скорость повышения давления следует устанавливать таким образом, чтобы в течение до 70 с было достигнуто заданное постоянное внутреннее гидростатическое давление (125 % номи-32
ГОСТ Р 53201—2023
нального значения) без разрушения трубы, фитинга или сборного узла. После чего трубу, фитинг или сборный узел выдерживают под достигнутым давлением в течение не менее 12 ч.
9.16.2 Квалификационные испытания проводят на пяти образцах труб или пяти образцах фитингов одного номинального диаметра и давления или пяти сборных узлах одного номинального диаметра и давления, собранных из образцов, отобранных по 8.5.
9.16.3 Периодические и типовые испытания проводят на двух образцах труб или двух образцах фитингов одного номинального диаметра и давления или двух сборных узлах одного номинального диаметра и давления, собранных из образцов, отобранных по 8.5.
9.16.4 Оборудование и условия проведения испытаний по — ГОСТ 34648, точность поддержания испытательной установкой заданного внутреннего гидростатического давления в течение цикла нагружения — по ГОСТ 34646.
9.17 Прочность и герметичность труб и их соединений при одновременном воздействии постоянного внутреннего гидростатического давления и постоянной внешней осевой нагрузки
9.17.1 Испытанию по определению прочности и герметичности при одновременном воздействии постоянного внутреннего гидростатического давления и постоянной внешней осевой нагрузки подвергают только насосно-компрессорные и обсадные трубы.
9.17.2 Испытанию подвергают насосно-компрессорные и обсадные трубы, прошедшие испытания постоянным внутренним гидростатическим давлением согласно 9.15 без разрушения.
В установленной для проведения испытаний трубе создают постоянное испытательное внутреннее гидростатическое давление равное внутреннему рабочему давлению и прикладывают постоянную внешнюю осевую нагрузку в соответствии с таблицей 18. Трубу выдерживают под заданным постоянным испытательным внутренним гидростатическим давлением и постоянной внешней осевой нагрузкой в течение не менее 120 с.
Таблица 18 — Требования к нагружению насосно-компрессорных и обсадных труб
Номинальный диаметр, DN | Внутреннее рабочее давление, МПа | Испытательное давление, МПа | Осевая нагрузка, кг |
50 | До 10,3 | 10,3 | 5100 |
12,1 | 12,1 | 5700 | |
13,8 | 13,8 | 6900 | |
17,2 | 17,2 | 7200 | |
20,7 | 20,7 | 9900 | |
24,1 | 24,1 | 10500 | |
27,6 | 27,6 | 11100 | |
63 | До 10,3 | 10,3 | 6900 |
12,1 | 12,1 | 7200 | |
13.8 | 13,8 | 7500 | |
17,2 | 17,2 | 8400 | |
20,7 | 20,7 | 10200 | |
24,1 | 24,1 | 10800 | |
27,6 | 27,6 | 12600 |
33
ГОСТ Р 53201—2023
Окончание таблицы 18
Номинальный диаметр, DN | Внутреннее рабочее давление, МПа | Испытательное давление, МПа | Осевая нагрузка, кг |
76 | До 10,3 | 10,3 | 8700 |
12,1 | 12,1 | 9300 | |
13,8 | 13,8 | 10800 | |
15,5 | 15,5 | 12300 | |
17,2 | 17.2 | 13500 | |
20,7 | 20,7 | 15000 | |
24,1 | 24,1 | 21000 | |
27,6 | 27,6 | 27400 | |
100 | До 10,3 | 10,3 | 14100 |
12,1 | 12,1 | 15000 | |
13,8 | 13.8 | 18300 | |
17,2 | 17.2 | 20700 | |
20,7 | 20,7 | 28500 | |
150 | До 6,9 | 6,9 | 27900 |
8,6 | 8.6 | 29700 | |
10,3 | 10,3 | 30000 (30900) | |
13,8 | 13,8 | 30000 (39600) | |
200 | До 6,9 | 6.9 | 26400 |
8,6 | 8,6 | 30000 (39000) | |
10,3 | 10,3 | 30000 (42600) | |
12,1 | 12,1 | 30000 (52200) |
Примечания
1 Осевая нагрузка рассчитана на глубину погружения до 3000 м.
2 Постоянную внешнюю осевую нагрузку, приведенную в скобках, допускается прикладывать только по согласованию между производителем и потребителем и при наличии документально подтвержденной возможности применения данной нагрузки на испытательном стенде без возможности его разрушения. При этом должны быть приняты исчерпывающие меры для обеспечения безопасности персонала и оборудования при проведении испытаний.
9.18 Цвет труб, фитингов проверяют визуально.
9.19 Маркировку определяют по 5.6. Наличие и содержание паспорта качества — визуально.
9.20 Упаковку определяют визуально. Наличие и содержание руководства по монтажу и эксплуатации — визуально.
9.21 Дополнительные характеристики полимерного композита труб и/или фитингов, труб, фитингов по 5.2.15 определяют в соответствии с документами по стандартизации, согласованными между потребителем и производителем.
34
ГОСТ Р 53201—2023
10 Транспортирование и хранение
10.1 Трубы и фитинги транспортируют любым видом транспорта в соответствии с правилами перевозки грузов, действующими для данного вида транспорта.
Транспортирование следует проводить с максимальным использованием вместимости транспортного средства.
10.2 При погрузке, выгрузке и транспортировании труб и фитингов должны быть приняты меры предосторожности, обеспечивающие их сохранность от механических повреждений.
10.3 Транспортирование и хранение труб и фитингов следует осуществлять в заводской упаковке по 5.7.1.
Допускается транспортирование и хранение труб без упаковки (навалом). В этом случае под нижний ряд и между рядами труб следует подкладывать деревянные прокладки толщиной не менее 40 мм. Расстояние между прокладками по длине труб должно быть 1,5—2,0 м.
10.4 Все опорные поверхности транспортного средства, контактирующие с изделиями, должны быть ровными и гладкими, без выступающих частей, острых предметов и кромок, способных нанести повреждение наружной поверхности труб и фитингов.
10.5 Трубы и фитинги хранят в условиях 5 (ОЖ 4) по ГОСТ 15150 рассортированными по типоразмерам в горизонтальном положении.
Высота штабелей труб при хранении не должна превышать 2 м.
Не допускается хранение труб и фитингов навалом.
11 Указания по применению
11.1 На все виды труб и фитингов должны быть разработаны и утверждены предприятием-изготовителем руководства по монтажу и эксплуатации.
11.2 Трубы и фитинги следует применять строго по функциональному назначению в условиях, установленных настоящим стандартом.
11.3 Эксплуатацию труб и фитингов следует осуществлять в соответствии с руководством по монтажу и эксплуатации, включаемым предприятием-изготовителем в комплект поставки.
11.4 Монтаж трубопроводов из труб и фитингов, их гидравлические испытания, а также ремонтные работы следует проводить в соответствии с требованиями проектной документации, действующих строительных норм и правил, а также положениями руководства по монтажу и эксплуатации.
Температура окружающей среды при производстве строительно-монтажных работ допускается от минус 50 °C до плюс 50 °C.
Примечание — Замерзание жидкости внутри трубопровода не допускается.
11.5 Общие указания по осуществлению монтажных работ приведены в приложении Д.
11.6 Трубопроводы питьевого и хозяйственно-бытового водоснабжения перед сдачей в эксплуатацию следует промывать водой в течение не менее 2 ч.
11.7 Предельно допустимая температура некоторых агрессивных сред при эксплуатации трубопроводов приведена в приложении Е.
11.8 При соблюдении требований и правил эксплуатации труб и фитингов из полимерного композита их средний срок службы составляет не менее 20 лет.
12 Гарантии изготовителя
12.1 Изготовитель гарантирует соответствие труб и фитингов требованиям настоящего стандарта при соблюдении условий транспортирования и хранения.
12.2 Гарантийный срок хранения — 1 год со дня изготовления.
35
ГОСТ Р 53201—2023
Приложение А (справочное)
Перечень возможных дефектов поверхности труб
А.1 Типы дефектов, критерии приемки и рекомендуемые корректирующие действия приведены в таблице А.1.
Таблица А.1 — Типы дефектов и критерии приемки
Тип дефекта | Описание | Критерии | Корректирующие действия при контроле |
Вздутия | Вздутия, образующиеся на поверхности или внутри слоя, обогащенного смолой | Не допускаются | Отбраковка |
Изменение цвета | Термическое разложение, подтверждаемое деформацией или изменением цвета поверхности полимерного композита | Деформация и/или обгорание на глубину, превышающую толщину поверхностного слоя смолы | Отбраковка |
Разрушение покрытия и ослабление волокон | Небольшое повреждение наружной поверхности под действием ультрафиолетового излучения или кислотного дождя, вызываемое хранением в течение длительного времени | Глубина не ограничивается поверхностным слоем, площадь поверхности не ограничивается, волокна не ослабляются | Отбраковка (текущий ремонт) |
Скол | Небольшой кусок материала, оторванный от края или поверхности (если армирующие волокна разрываются, повреждение определяется как трещина) | Неповрежденные волокна обнажены на некоторой площади или волокна не обнажены, но на площади, превышающей 100 мм2, обнаруживается недостаток смолы | Отбраковка (текущий ремонт) |
Волокна не обнажаются и площадь, на которой смолы недостаточно, составляет менее 100 мм2 | Принятие | ||
Трещина | Реальное разделение полимерного композита, видимое на противоположных поверхностях, проходящее через стенку. Непре-рывная трещина может идентифицироваться светлым участком | Максимальная глубина равна толщине слоя смолы или менее толщины этого слоя | Отбраковка (текущий ремонт) |
Максимальная глубина более толщины слоя смолы | Отбраковка | ||
Волосяные трещины | Тонкие трещины на поверхности полимерного композита или под ней | Максимальная длина трещин — менее 25 мм | Принятие |
Максимальная длина трещин — более 25 мм | Отбраковка (текущий ремонт) | ||
Разрезанный ровинг | Разорванный или разрезанный ровинг как результат зачистки, истирания или технологического процесса | Максимум три участка разрезанных ровингов на трубу площадью каждого участка менее 25*25 мм. Максимальная глубина такова, что толщина стенки не уменьшается до значения, менее ее минимального значения | Принятие |
36
Продолжение таблицы А. 1
ГОСТ Р 53201—2023
Тип дефекта | Описание | Критерии | Корректирующие действия при контроле |
Деформация | Долговременное изменение размеров | Утечка не допускается | Отбраковка |
Расслаивание (внутреннее) | Видимая сплошная область в полимерном композите как результат недостаточного сцепления между смолой и волокнами. Разделение слоев полимерного композита | Не допускается | Отбраковка |
Оголение волокон | Место на поверхности, в котором армирующий наполнитель должен быть полностью покрыт смолой | Не допускается | Отбраковка |
Разрыв | Разрушение полимерного композита с полным проникновением. Большинство волокон разорвано. Место разрушения выглядит как более светлая окрашенная область | Не допускается | Отбраковка |
Механические повреждения | Светлая область с разорванными волокнами или без разорванных волокон | Наличие круговых или эллипсоидальных «ярких сплошных» областей (диаметром более 10 мм) не допускается. Отсутствие утечки при расчетном давлении или при нормальном рабочем давлении | Отбраковка |
Кольцевые области диаметром менее 10 мм. Отсутствие утечки при расчетном или нормальном рабочем давлении | Отбраковка (текущий ремонт) | ||
Утечка при расчетном или нормальном рабочем давлении | Отбраковка | ||
Несоответствующее отверждение смолы или клеевого слоя | Температура и влажность не отвечают техническим требованиям. Неправильная процедура отверждения/склеивания | Не допускается | Отбраковка |
Инородные включения | Посторонние вещества, вкрапленные в полимерный композит | Не допускаются | Отбраковка |
Неправильное наслоение | Соединение в замок, наслоенное с пропуском слоев | Не допускается | Отбраковка |
Недостаток волокон | Слишком высокое значение соотношения содержания смолы и волокна | Не допускается | Отбраковка |
37
ГОСТ Р 53201—2023
Окончание таблицы А. 1
Тип дефекта | Описание | Критерии | Корректирующие действия при контроле |
Ямка (микроотверстие) | Небольшой кратер на внутренней поверхности полимерного композита, ширина (максимальный диаметр) которого равна или менее глубины | Диаметр более 0,8 мм и/или глубина, превышающая толщину футеровки, или составляющая 10 % толщины стенки, и/или поврежденные волокна | Отбраковка |
Диаметр менее 0,8 мм и/или глубина менее толщины футеровки, или составляющая 10 % толщины стенки, и неповрежденные волокна | Принятие | ||
Царапины | Неглубокие царапины, возникающие в результате неправильного перемещения, хранения и/или транспортирования. Если волокна армирующего наполнителя разрываются, то такое повреждение считается трещиной | Неповрежденные волокна остаются незащищенными на всей площади или таких волокон нет, но на площади, равной или превышающей 100 мм2, недостает смолы | Отбраковка (текущий ремонт) |
Незащищенных волокон нет и площадь, на которой недостает смолы, составляет менее 100 мм2 | Отбраковка (текущий ремонт) | ||
Разрывы, разрезы, дробление, кромки или другие дефекты | Нарушается непрерывность резьбы | Не допускается в пределах минимальной длины в вершине наружной резьбы, отсчитываемой от конца трубы | Отбраковка |
38
ГОСТ Р 53201—2023
Приложение Б (обязательное)
Порядок оформления и утверждения контрольных образцов-эталонов внешнего вида
Б.1 Контрольные образцы-эталоны представляют собой один или несколько отрезков труб (не более пяти) одного номинального диаметра и толщины стенки длиной не менее 500 мм, с маркировкой и раструбом на одном из них, пронумерованных и отобранных от серийной партии труб, изготовленной в соответствии с требованиями настоящего стандарта.
Б.2 Контрольные образцы-эталоны внешнего вида, как правило, оформляют на один типовой образец от каждого типа труб по диаметрам: 50—100 мм и 100—200 мм.
Б.З К каждому контрольному образцу — эталону, имеющему маркировку по 5.6, прикрепляют опломбированный ярлык, в котором указывают:
- условное обозначение трубы;
- наименование предприятия-изготовителя;
- гриф утверждения контрольного образца-эталона руководителем предприятия-изготовителя, заверенный круглой печатью с указанием даты утверждения.
Б.4 Контрольные образцы-эталоны хранят на предприятии-изготовителе.
39
ГОСТ Р 53201—2023
Приложение В (справочное)
Перечень возможных дефектов наружной и внутренней резьбы
Типы дефектов, критерии приемки и рекомендуемые корректирующие действия приведены в таблице В.1.
Таблица В.1 — Типы дефектов и критерии приемки
Тип дефекта | Описание | Критерии | Корректирующие действия при изготовлении |
Пузырьки, раковины | Воздушные включения, раковины в виде пузырьков или раковин | Максимальный размер — не более 3 мм. Линейное размещение не должно затрагивать по образующей более трех последовательных ниток. Число пузырьков или раковин, диаметр которых от 2 до 3 мм, не должно превышать 15 на резьбу | Принятие |
Инородные включения | Включение инородных частиц на витках резьбы | Размер включений не более 3 мм, количество — не более трех на резьбу | Принятие |
Цветные пятна | Белые зоны на поверхности витков резьбы | Общая площадь поверхности таких зон — не более 2 см2 на резьбу | Принятие |
Сколы, вырывы материала, пустоты, впадины | Вырывание материала, пустоты, впадины, сколы на витках резьбы | Глубина — не более 1 мм, длина не превышает 4 мм. Число витков с вырванным материалом — не более пяти при условии, что все они не находятся в зоне, площадь которой менее 2 см2 | Принятие |
Царапины и борозды | Круговые царапины и бороздки на витках резьбы | Максимальная глубина не должна превышать 0,5 мм. Царапина не должна захватывать более пяти витков | Принятие |
Примечание — Вышеуказанные дефекты не учитывают для двух первых и двух последних витков резьбы. |
40
ГОСТ Р 53201—2023
Приложение Г (обязательное)
Требования к содержанию минимально необходимого объема информации о трубе/фитинге, соответствующей его уникальному идентификатору, хранящемуся в RFID-метке, установленной на трубе/фитинге
На предприятии — изготовителе трубы/фитинга в ридер должна быть внесена следующая информация:
- наименование и условное обозначение трубы/фитинга;
- наименование страны изготовителя трубы/фитинга;
- наименование и товарный знак и/или товарная марка предприятия-изготовителя трубы/фитинга;
- юридический и фактический адрес изготовителя трубы/фитинга, адрес производственной площадки, на которой произведены труба/фитинг;
- виды и типы исходных материалов, из которых изготовлены труба/фитинг;
- даты изготовления, сроки годности и результаты заводского входного контроля исходных материалов, из которых изготовлены труба/фитинг;
- метод изготовления трубы/фитинга;
- фактические значения основных физико-механических показателей, физико-химических показателей трубы/фитинга, в том числе полимерных композитов трубы/фитинга, показателей стойкости труб и фитингов к внешним воздействиям;
- комплектность поставки;
- дата изготовления трубы/фитинга, номер смены, номер партии, ФИО контролера;
- обозначение документов по стандартизации, по которым трубу/фитинг изготавливают и идентифицируют;
- документы (сертификаты и протоколы испытаний) о подтверждении соответствия трубы/фитинга требованиям настоящего стандарта;
- документы, подтверждающие пригодность для использования трубы/фитинга в хозяйственно-питьевом водоснабжении (только для труб, применяемых в системах технического водоснабжения, питьевого водоснабжения);
- рекомендации по эксплуатации и ремонту трубы/фитинга.
41
ГОСТ Р 53201—2023
Приложение Д (справочное)
Рекомендации по монтажу трубопроводов
Д.1 Рекомендации по монтажу насосно-компрессорных и обсадных труб
Д.1.1 Перед спуском в скважину трубы необходимо скомплектовать по размерам в соответствии с конструкцией скважины.
Для соединения между собой труб разного диаметра следует использовать соответствующие фитинги.
Д.1.2 При подъеме труб и монтаже трубопровода необходимо предохранять соединяемые части от ударов и механических повреждений.
Д.1.3 При проведении монтажа полимерных композитных трубопроводов используют стандартное оборудование, предназначенное для работы с металлическими насосно-компрессорными и обсадными трубами, за исключением автоматических ключей для свинчивания труб.
Свинчивание труб следует проводить вручную с использованием предельных моментных (динамометрических) ключей, используемых при нормированной затяжке резьбовых соединений, оснащенных динамометрическими устройствами (см. поз. 4—6 — рисунок Д.1). Рекомендуется использовать предельные шарнирные динамометрические ключи, приведенные на рисунке Д.1 или аналогичные предельные шарнирные динамометрические ключи.
Примечание — При применении предельных моментных (динамометрических) ключей, на них заранее устанавливают заданное значение крутящего момента силы, после достижения которого подается звуковой сигнал (сигнальный щелчок).
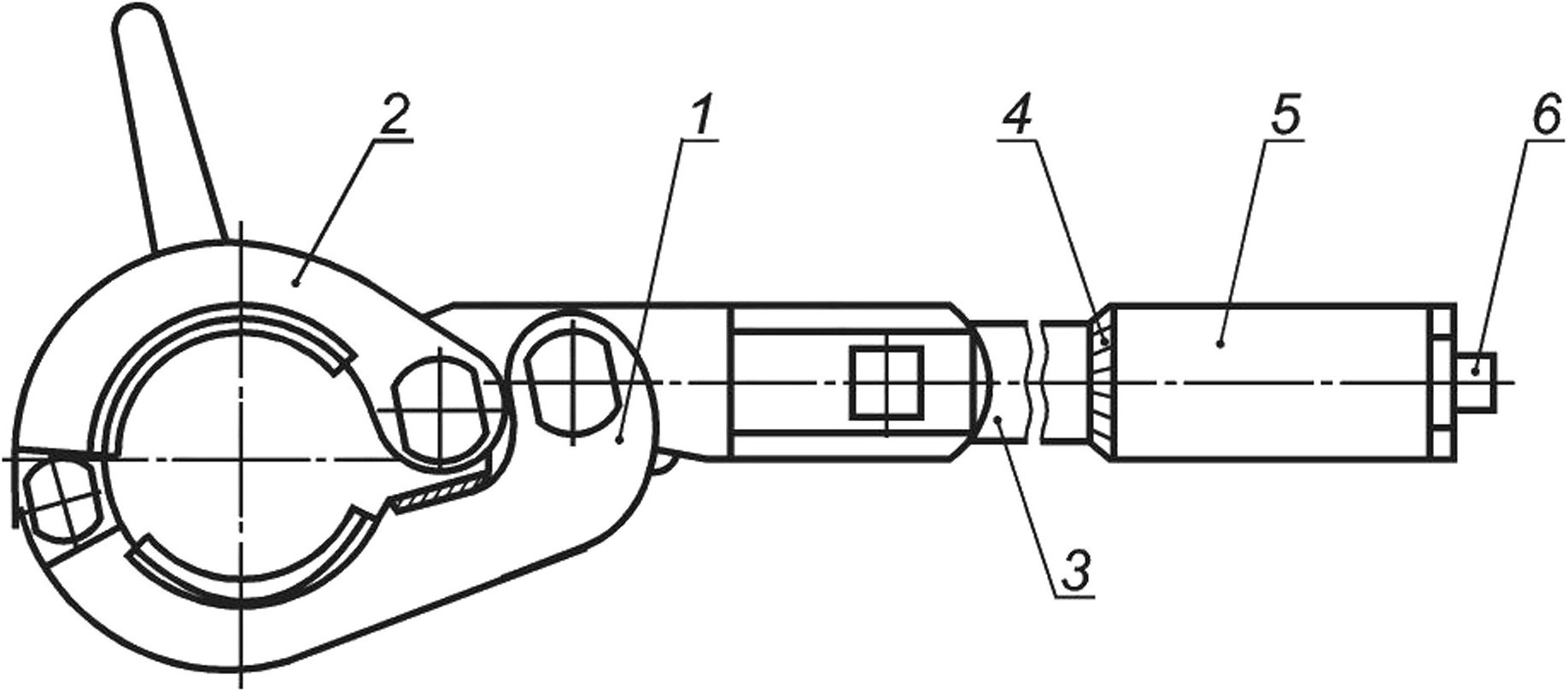
1 — челюсть; 2 — захват; 3 — рукоятка ключа; 4 — шкала динамометрического устройства;
5 — рукоятка динамометрического устройства: б — стопорный винт динамометрического устройства
Рисунок Д.1 — Рекомендуемый предельный шарнирный динамометрический ключ
Отвинчивание труб следует проводить вручную с использованием демонтажных шарнирных ключей, аналогичных приведенным на рисунке Д.1, но не оснащенных динамометрическими устройствами (укороченных шарнирных ключей). Для облегчения отвинчивания труб допускается удлинение рукоятки демонтажного шарнирного ключа стальной трубой подходящего сечения.
Использование стандартных трубных ключей для свинчивания и отвинчивания труб не допускается.
При свинчивании и отвинчивании ключи следует устанавливать на расстоянии до 400 мм от торца раструба или ниппеля.
Не допускается накладывать ключи на резьбу ниппеля.
Д.1.4 Спуск труб в скважину
Д.1.4.1 Непосредственно перед спуском насосно-компрессорных или обсадных труб скважину следует тщательно промыть и проработать в интервалах расположения уступов и местных сужений ствола.
При наличии каверн и зон поглощений надо принять меры к их изоляции.
Д. 1.4.2 Чтобы обеспечить спуск колонны обсадных труб и создать противодавление на забой, обсадные трубы необходимо периодически заполнять промывочным раствором.
Частоту заполнения обсадных труб раствором определяют с учетом массы труб в скважине, удельного веса промывочного раствора, пластового давления и других факторов. В большинстве случаев достаточно доливать промывочный раствор после спуска каждых 6—10 труб.
42
ГОСТ Р 53201—2023
Д.1.4.3 Непосредственно перед подъемом с мостков необходимо еще раз проверить наличие маркировки и клейма приемки труб, а также отсутствие недопустимых повреждений во избежание попадания в колонну дефектных труб. Подъем насосно-компрессорных или обсадных труб с мостков необходимо осуществлять только при наличии защитного колпачка наружной резьбы. Предохранительную пробку внутренней резьбы допускается удалить до подъема труб.
После подъема трубы следует снять защитный колпачок с наружной резьбы и проверить ее состояние внешним осмотром. Резьбы очищают от грязи и инородных предметов щеткой (не допускается использование металлических щеток).
Если трубы используют повторно, то их резьбы следует промыть растворителем, в качестве которого может быть использован бензин, ацетон, уайт-спирит или керосин. Излишки растворителя удаляют сжатым воздухом или ветошью. Необходимо при этом следить за тем, чтобы промытая резьба имела чистые витки без каких-либо инородных включений, в том числе ниток ветоши.
На всю поверхность резьбы должен быть нанесен равномерный слой смазки, рекомендованной предприятием — изготовителем труб.
Смазку наносят непрерывным слоем неметаллической щеткой или шпателем.
Примечание — Не следует допускать попадания песка или других механических примесей в смазку.
Для равномерного нанесения температура смазки должна быть не ниже 18 °C.
Д.1.4.4 При свинчивании (посадке) трубы с муфтой трубу медленно вращают, чтобы убедиться в том, что обеспечено правильное, без перекоса, зацепление резьбы.
Д.1.4.5 Свинчивание резьбовых соединений насосно-компрессорных или обсадных труб проводят вручную усилием одного человека.
Д.1.4.6 После предварительного свинчивания проводят докрепление резьбового соединения. Докрепление резьбового соединения необходимо проводить осторожно, исключая повреждение наружных поверхностей труб и витков резьбы.
Соединение считают затянутым правильно, если торец раструба совпадает с концом сбега резьбы ниппеля или не совпадает с ним не более чем на один виток.
Д.1.4.7 Рекомендуемые моменты свинчивания для насосно-компрессорных и обсадных труб различных диаметров приведены в таблице Д.1.
Таблица Д.1 — Рекомендуемые моменты свинчивания резьбовых соединений насосно-компрессорных и обсадных труб
Номинальный диаметр трубы, DN | Момент свинчивания | |
Нм | КГМ | |
50 | 206 | 21 |
63 | 255 | 26 |
76 | 343 | 35 |
100 | 461 | 47 |
150 | 892 | 91 |
200 | 1147 | 117 |
Д.1.4.8 Если при указанных значениях моментов свинчивания не обеспечивается качественное соединение, соединение необходимо разобрать, проверить состояние витков резьбы и наличие на них инородных включений.
Д.1.4.9 После свинчивания труб проводят спуск колонны в скважину. Колонну следует спускать плавно, без рывков.
Д.1.4.10 Спуск колонны труб на забой следует выполнять плавно, на минимальной скорости, исключающей ударные нагрузки.
Обсадную колонну из труб не допускается ставить на забой, так как это может привести к продольному изгибу, особенно в наиболее расширенном участке скважины.
Колонна труб после ее установки и цементирования должна быть натянута.
Параметры натяжения колонны определяют расчетным путем.
Д.1.5 Цементировать обсадную колонну необходимо с таким расчетом, чтобы исключить наличие внутри нее цементного моста, так как при его последующем разбуривании может быть нарушена целостность колонны и снижена прочность контакта ее наружной поверхности с цементным камнем.
43
ГОСТ Р 53201—2023
Д.1.6 После первичного цементирования, а также после установки цементных мостов для изоляции опробованных объектов каждая обсадная колонна должна подвергаться испытанию для проверки качества цементирования, определения ее прочности и герметичности.
Колонну считают выдержавшей испытание на герметичность способом опрессовки в том случае, если после замены раствора водой отсутствует перелив жидкости и выделение газа из колонны, а также если отсутствует снижение давления в течение 30 мин.
При невыполнении данных требований следует принять меры к повышению герметичности колонны (до-крепление, прокачка полимерных растворов и др.), после чего герметичность должна быть проверена повторно.
Д.1.7 Подъем труб
Д. 1.7.1 Подъем колонны труб следует проводить плавно, без ударов, рывков и перехода с одной скорости на другую. Перед началом подъема следует убедиться в отсутствии прихвата колонны путем осторожного ее натягивания. Растягивающие усилия не должны превышать допустимые нагрузки для резьбовых соединений.
Поднятые из скважины и установленные на вышке трубы должны быть надежно закреплены. На резьбовые соединения поднятых из скважины труб следует установить предохранительные пробки и колпачки.
Д.1.7.2 При каждом подъеме насосно-компрессорных труб рекомендуется распределять возможный износ резьбовых соединений труб путем перестановки их с верхней части колонны в ее нижнюю часть. При применении многосекционных лифтовых колонн перестановку труб следует проводить внутри каждой секции.
Д.1.8 Перед вторичным использованием или отправкой труб на склад необходимо провести контроль состояния труб и их соединений внешним осмотром.
Д.1.9 Поврежденные трубы складывают отдельно для принятия решения по использованию каждой дефектной трубы.
Д.2 Рекомендации по монтажу линейного трубопровода
Д.2.1 Монтаж подземного трубопровода
Д.2.1.1 Сборку подземного трубопровода проводят над или внутри траншеи. В обоих случаях возможно применение деревянных прокладок или подставок с роликами для центрирования соединяемых труб.
Д.2.1.2 Перед сборкой трубопровода все трубы следует разложить вдоль траншеи в непрерывную нитку на расстоянии 1,0—1,5 м от ее кромки на свободной от насыпи стороне. Раскладку труб вдоль траншеи следует проводить таким образом, чтобы ниппельные концы труб были расположены в направлении потока транспортируемой рабочей среды.
Д.2.1.3 Перед свинчиванием резьбовых соединений труб с них необходимо снять защитные колпачки и проверить состояние резьбы внешним осмотром.
Д.2.1.4 Резьбы очищают от грязи и инородных предметов щеткой (не допускается использование металлических щеток).
Если трубы используют повторно, то их резьбы следует промыть растворителем, в качестве которого может быть использован бензин, ацетон, уайт-спирит или керосин. Излишки растворителя удаляют сжатым воздухом или ветошью. Необходимо при этом следить за тем, чтобы промытая резьба имела чистые витки без каких-либо инородных включений, в том числе ниток ветоши.
Д.2.1.5 На резьбовые части следует нанести резьбовую смазку, рекомендованную предприятием — изготовителем труб.
Д.2.1.6 Свинчивание труб следует проводить вручную с использованием предельных моментных (динамометрических) ключей, используемых при нормированной затяжке резьбовых соединений, оснащенных съемными динамометрическими устройствами (см. поз. 5—8 — рисунок Д.2). Рекомендуется использовать предельные ременные (ремешковые) динамометрические ключи, приведенные на рисунке Д.2 или аналогичные предельные ременные (ремешковые) динамометрические ключи.
Примечание — При применении предельных моментных (динамометрических) ключей, на них заранее устанавливают заданное значение крутящего момента силы, после достижения которого подается звуковой сигнал (сигнальный щелчок).
44
ГОСТ Р 53201—2023
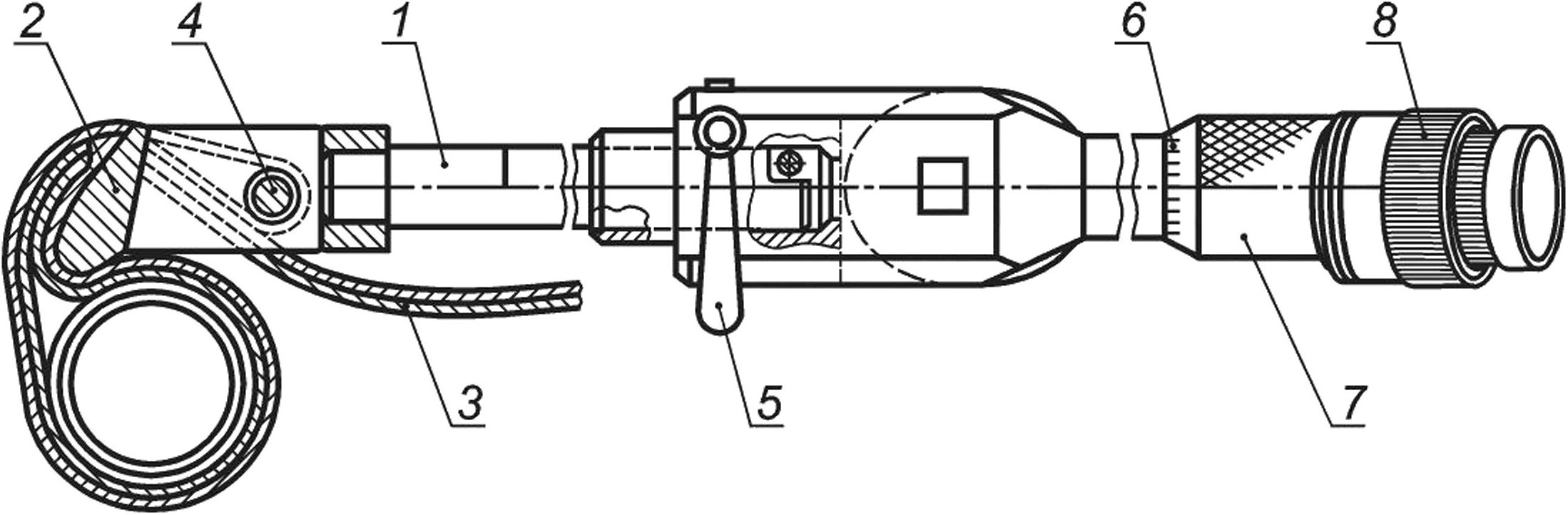
1 — рукоятка ключа; 2 — механизм натяжения; 3 — ремень; 4 — ось закрепления ремня; 5 — ручка тангенциального зажима;
6 — шкала динамометрического устройства; 7 — рукоятка динамометрического устройства;
8 — блокирующее кольцо динамометрического устройства
Рисунок Д.2 — Рекомендуемый предельный ременный (ремешковый) динамометрический ключ
Отвинчивание труб следует проводить вручную с использованием предельных моментных (динамометрических) ключей, используемых при свинчивании труб, но со снятым динамометрическим устройством. Для облегчения отвинчивания труб допускается удлинение рукоятки ременного (ремешкового) ключа без динамометрического устройства стальной трубой подходящего сечения.
Рекомендуемые моменты свинчивания для линейных труб различных диаметров приведены в таблице Д.2.
Таблица Д.2 — Рекомендуемые моменты свинчивания резьбовых соединений линейных труб
Номинальный диаметр трубы, DN | Момент свинчивания | |
Нм | КГМ | |
50 | 235 | 24 |
63 | 284 | 29 |
76 | 373 | 38 |
100 | 500 | 51 |
150 | 951 | 98 |
200 | 1530 | 156 |
Примечание — При монтаже линейных труб номинальными диаметрами DN50, DN63, DN76, DN100 с внутренним рабочим давлением 10,3 МПа и выше, а также линейных труб номинальными диаметрами DN150, DN200 с внутренним рабочим давлением 6,9 МПа и выше, допускается превышать момент свинчивания резьбовых соединений до 30 % от указанных рекомендуемых значений. |
Д.2.1.7 При необходимости может быть осуществлено укорачивание длины резьбы в соответствии с указаниями, приведенными в таблице Д.З.
Таблица Д.З — Укорачивание длины резьбы линейных труб
Номинальный диаметр трубы, DN | Количество отрезаемых витков резьбы, шт. |
50 | 5 |
63 | 5 |
76 | 5 |
100 | 6 |
150 | 7 |
200 | 9 |
45
ГОСТ Р 53201—2023
Д.2.1.8 Спуск свинченных труб в траншею следует проводить вручную, автомобильными кранами или трубоукладчиками. При этом для защиты поверхностей труб от повреждений необходимо использовать специальные полотенца, брезентовые ремни, обрезиненные тросы или веревки.
Спускать трубы нужно плавно, избегая ударов о стенки и дно траншеи.
Д.2.1.9 Прокладку трубопроводов в грунтах с наличием щебня или других каменистых включений в скальных и мерзлых грунтах следует предусматриваться с подсыпкой дна траншеи песком или мягким грунтом высотой слоя не менее 10 см (от верха выступающих неровностей дна траншеи) и присыпкой трубы на высоту не менее 20 см.
Уклон стенок траншеи должен быть равным 1:0,5. В качестве подстилающего слоя вместо подсыпки могут применяться штучные податливые изделия: мешки из геосинтетических (геотекстильных) материалов, заполненные песком, резиновой крошкой, полимерной ватой и другими аналогичными материалами.
Примечание —Уклон стенок траншеи в однородных немерзлых грунтах определяют по СП 45.13330.2017 (приложение В), в насыпных, песчаных и пылевато-глинистых грунтах выше уровня грунтовых вод (с учетом капиллярного поднятия) или грунтах, осушенных с помощью искусственного водопонижения по [4] — с учетом требований [5].
Д.2.1.10 После укладки трубопровода в траншею следует осуществить его частичную засыпку грунтом, в количестве достаточном для фиксации положения трубопровода в траншее. При этом места расположения соединений (400 мм до соединения и 400 мм после соединения) не засыпают для обеспечения возможности их контроля при испытании на прочность и герметичность.
Затем проводят очистку полости трубопровода, испытание на прочность и герметичность и (при положительном результате испытаний) осуществляют окончательную засыпку.
Для предохранения трубопровода от повреждений при его засыпке слежавшимся грунтом трубопровод вначале следует присыпать песком или мягким грунтом на высоту, превышающую диаметр трубопровода на 150—200 мм.
Следует избегать засыпки трубопровода промерзшим грунтом.
Также не рекомендуется засыпать траншею, заполненную водой. Предварительно следует откачать воду, проверить расположение труб, убедиться, что под трубопроводом нет пустот. Все пустоты должны быть заполнены и засыпаны сухим, мягким грунтом, после чего следует провести уплотнение грунтом пазух траншеи.
Трамбовать грунт непосредственно над трубопроводом запрещается.
Д.З Монтаж надземного трубопровода
Д.3.1 Монтаж надземного полимерного композитного трубопровода осуществляют на опорах.
Д.З.2 Опоры должны иметь достаточную ширину, обеспечивающую поддержку трубопровода без нанесения ему повреждений, и иметь покрытия из эластомерного материала.
Д.3.3 Усилие зажима трубы в опоре, если оно прилагается, не должно приводить к смятию трубы.
Д.3.4 Рекомендуется устанавливать опоры для секций труб, а не для фитингов или соединений.
Д.З.5 Опоры следует располагать по отношению друг к другу так, чтобы исключить провисание (чрезмерное смещение с течением времени) и/или чрезмерные вибрации в течение расчетного срока службы трубопроводов. Кроме того, расстояние от опоры до резьбового соединения не должно превышать 1,2 м. Расстояние между опорами для монтажа надземного линейного трубопровода приведено в таблице Д.4.
Таблица Д.4 — Расстояние между опорами для монтажа надземного линейного трубопровода
Номинальный диаметр трубы, DN | Длина пролета, м |
50 | 2,6 |
63 | 2,8 |
76 | 2,9 |
100 | 3,1 |
150 | 3,5 |
200 | 3,7 |
Д.З.6 Свинчивание и отвинчивание труб следует проводить аналогично Д.2.1.6.
Д.З.7 При сборке отдельных элементов надземных полимерных композитных трубопроводов (трубных плетей, узлов) на земле, их подъем на опоры и эстакады рекомендуется проводить вручную или с помощью автомобильных кранов. Трубы необходимо поднимать плавно, избегая ударов о металлические и бетонные элементы опор или эстакад.
При этом для предохранения поверхностей труб от повреждений необходимо пользоваться специальными полотенцами, брезентовыми ремнями, обрезиненными тросами или веревками.
46
ГОСТ Р 53201—2023
Приложение Е (справочное)
Предельно допустимая температура некоторых агрессивных сред в трубопроводной системе
Максимальная рабочая температура некоторых агрессивных сред, допустимая при эксплуатации полимерного композитного трубопровода, приведена в таблице Е.1.
Таблица Е.1 — Максимальная рабочая температура некоторых агрессивных сред
Наименование среды | Температура, °C |
Анилин | 38 |
Азотная кислота, до 10 % | 38 |
Аммиак мокрый | 38 |
Ацетон | 49 |
Фосфорная кислота, до 54 % | 80 |
Фосфорная кислота, до 75 % | 80 |
Соляная кислота, до 35 % | 80 |
Плавиковая кислота, до 2 % | 40 |
Борная кислота, насыщенная | 93 |
Кремнефтористоводородная кислота, до 5 % | 30 |
Уксусная кислота, до 50% | 50 |
Растворы солей: аммония, бария, алюминия, кальция, калия, меди, железа, магния, свинца, натрия, никеля, серебра любой концентрации | 80 |
Сырая нефть | 110 |
Дизельное топливо | 93 |
Этилцеллозольв | 38 |
Соляная кислота (26,5 г/л) | 50 |
Соляная кислота (45 г/л) | 50 |
Серная кислота (204,8 г/л) | 50 |
Серная кислота (40 г/л) | 50 |
Бромистоводородная кислота (225 г/л) | 50 |
Окисленный йодосодержащий рассол | 50 |
Окисленный бромосодержащий рассол | 50 |
Бромистое железо | 20 |
Хлористый барий, 18 % | 80 |
Хлористый натрий, 30 % | 80 |
Жидкие комплексные удобрения (ЖКУ) | 40 |
Двуокись серы | 66 |
Серная кислота (до 15 % + 0,1 %) | 50 |
Фосфорная кислота (до 32 % Р2О5 + 1,5 %) | 70 |
47
ГОСТ Р 53201—2023
Продолжение таблицы Е. 1
Наименование среды | Температура, °C |
Угольная кислота | 93 |
Уксусная кислота, 5% | 49 |
Рапа, окисленная хлором | 80 |
Углекислый аммоний | 66 |
Хлористый аммоний | 66 |
Хлористый натрий | 110 |
Хлористый алюминий | 110 |
Хлорид кальция | 110 |
Фреон | 66 |
Жидкая фаза в производстве азотосодержащих красителей: NaOH —до 5 %, NaNO3 и NaNO2 — до 4,5 % | 40 |
Гексахлорциклопентадиен технический | 25 |
Гексахлорбутадиен | 25 |
Глицерин | 110 |
Раствор аммиачной селитры, 50 % | 50 |
Раствор аммиачной селитры, 63 % | 80 |
Водный раствор, содержащий 15 % гидроксиламинсульфата, 2 % серной кислоты, 2 % сульфата аммония | 60 |
Сточные воды, содержащие 1 % сернистой кислоты | 30 |
Толуол | 66 |
Дихлорэтилен | 38 |
Раствор сульфата аммония, содержащий серную кислоту | 50 |
Раствор сульфата аммония, 40 % | 50 |
Раствор сульфата аммония, 15 %, содержащий 1 % серной кислоты | 60 |
Сточные воды, содержащие 2 % серной кислоты и 2 % азотной кислоты | 40 |
Водный раствор, содержащий 10 % азотной кислоты и 10 % азотнокислого магния | 30 |
Раствор, содержащий 18 % гидроксиламинсульфата, 12 % серной кислоты и 35 % сульфата аммония | 80 |
Декарбонизованная вода (pH 5), подкисленная серной кислотой | 30 |
Водный раствор, содержащий 20 % азотнокислого аммония, 12 % углекислого аммония, 2 % аммиачной селитры и 1 % аммиака | 20 |
Бензин кислый | 110 |
Бензин рафинированный | 66 |
Бензол | 66 |
Бутадиен | 38 |
Гептан | 66 |
Гексан | 38 |
48
Окончание таблицы Е. 1
ГОСТ Р 53201—2023
Наименование среды | Температура, °C |
Дибутилфталат | 66 |
Вода соленая | 110 |
Вода дистиллированная или минерализованная | 110 |
Спирт метиловый | 66 |
Спирт изобутиловый | 66 |
Воздух | 93 |
Керосин | 110 |
Лигроин | 93 |
Тетраборат натрия (Бораке) | 110 |
49
ГОСТ Р 53201—2023
Библиография
[1] ИСО 14692-2:2017 Нефтяная и газовая промышленность. Трубопроводы из пластмасс, армированных стекловолокном. Часть 2. Квалификация и производство
[Petroleum and natural gas industries — Glass-reinforced plastics (GRP) piping — Part 2: Qualification and manufacture]
[2] АПИ Технические условия 15 XP (четвертое издание, февраль 2016). Трубопровод высокого давления из стекловолокна (API Specification 15HR (fourth edition, February 2016). High-pressure Fiberglass Line Pipe)
[3] СанПиН 1.2.3685—21 Гигиенические нормативы и требования к обеспечению безопасности и (или) безвред
ности для человека факторов среды обитания
[4] СНиП 12-04-2002 Безопасность труда в строительстве. Часть 2. Строительное производство
[5] Приказ Минтруда России от 11 декабря 2020 г. № 883н «Об утверждении Правил по охране труда при строительстве, реконструкции и ремонте»
УДК 622.692.4:006.354
ОКС 23.040.20
23.040.45
83.120
Ключевые слова: трубы композитные полимерные, фитинги композитные полимерные, соединения резьбовые, технические требования, основные размеры, маркировка, RFID-метки, уникальный идентификатор трубы/фитинга, упаковка, требования безопасности, методы испытаний, транспортирование, хранение, гарантия
Редактор Н.А. Аргунова
Технический редактор И.Е. Черепкова
Корректор Р.А. Ментова
Компьютерная верстка Е.А. Кондрашовой
Сдано в набор 22.11.2023. Подписано в печать 30.11.2023. Формат 60x84%. Гарнитура Ариал.
Усл. печ. л. 6,05. Уч.-изд. л. 5,14.
Подготовлено на основе электронной версии, предоставленной разработчиком стандарта
Создано в единичном исполнении в ФГБУ «Институт стандартизации» , 117418 Москва, Нахимовский пр-т, д. 31, к. 2.