ФЕДЕРАЛЬНОЕ АГЕНТСТВО
ПО ТЕХНИЧЕСКОМУ РЕГУЛИРОВАНИЮ И МЕТРОЛОГИИ
НАЦИОНАЛЬНЫЙ СТАНДАРТ РОССИЙСКОЙ ФЕДЕРАЦИИ
ГОСТ Р 71318.2— 2024
СИСТЕМЫ ХОЛОДИЛЬНЫЕ И ТЕПЛОВЫЕ НАСОСЫ
Оборудование, работающее под избыточным давлением
Часть 2
Трубопроводы. Общие требования
Издание официальное
Москва Российский институт стандартизации 2024
ГОСТ Р 71318.2—2024
Предисловие
1 РАЗРАБОТАН Российским союзом предприятий холодильной промышленности (Россоюзхолод-пром) и Федеральным государственным бюджетным учреждением «Российский институт стандартизации» (ФГБУ «Институт стандартизации»)
2 ВНЕСЕН Техническим комитетом по стандартизации ТК 271 «Холодильные установки»
3 УТВЕРЖДЕН И ВВЕДЕН В ДЕЙСТВИЕ Приказом Федерального агентства по техническому регулированию и метрологии от 12 сентября 2024 г. № 1230-ст
4 Настоящий стандарт разработан с учетом основных нормативных положений стандарта ДИН ЕН 14276-2:2020 «Оборудование, работающее под избыточным давлением для холодильных систем и тепловых насосов. Часть 2: Трубопроводы. Общие требования» (DIN EN 14279-2:2020 «Druckgerate fur Kalteanlagen und Warmepumpen — Teil 2: Rohrleitungen — Allgemeine Anforderungen», NEQ)
5 ВВЕДЕН ВПЕРВЫЕ
Правила применения настоящего стандарта установлены в статье 26 Федерального закона от 29 июня 2015 г. № 162-ФЗ «О стандартизации в Российской Федерации». Информация об изменениях к настоящему стандарту публикуется в ежегодном (по состоянию на 1 января текущего года) информационном указателе «Национальные стандарты», а официальный текст изменений и поправок — в ежемесячном информационном указателе «Национальные стандарты». В случае пересмотра (замены) или отмены настоящего стандарта соответствующее уведомление будет опубликовано в ближайшем выпуске ежемесячного информационного указателя «Национальные стандарты». Соответствующая информация, уведомление и тексты размещаются также в информационной системе общего пользования — на официальном сайте Федерального агентства по техническому регулированию и метрологии в сети Интернет (www.rst.gov.ru)
©Оформление. ФГБУ «Институт стандартизации», 2024
Настоящий стандарт не может быть полностью или частично воспроизведен, тиражирован и распространен в качестве официального издания без разрешения Федерального агентства по техническому регулированию и метрологии
II
ГОСТ Р 71318.2—2024
Содержание
1 Область применения..................................................................1
2 Нормативные ссылки..................................................................2
3 Термины, определения и сокращения....................................................3
4 Материалы .........................................................................4
5 Классификация трубопроводов.........................................................5
6 Проектирование
7 Производство. .
Ю CD
8 Испытания и проверки................................................................10
III
ГОСТ Р 71318.2—2024
НАЦИОНАЛЬНЫЙ СТАНДАРТ РОССИЙСКОЙ ФЕДЕРАЦИИ
СИСТЕМЫ ХОЛОДИЛЬНЫЕ И ТЕПЛОВЫЕ НАСОСЫ
Оборудование, работающее под избыточным давлением
Часть 2
Трубопроводы. Общие требования
Refrigeration systems and heat pumps. Pressure equipment.
Part 2. Piping. General requirements
Дата введения — 2025—02—01
1 Область применения
1.1 Настоящий стандарт устанавливает требования к материалам, конструкции, изготовлению, испытаниям и документации на стационарные трубопроводы, предназначенные для использования в холодильных установках, тепловых насосах и вторичных системах охлаждения и нагрева в соответствии с определениями, приведенными в ГОСТ 34891.1.
Примечание — В настоящем стандарте там, где применен термин «холодильная система», следует подразумевать, что речь идет также и о тепловых насосах.
1.2 Настоящий стандарт распространяется на трубопроводы, включая сварные или паяные соединения.
1.3 Настоящий стандарт следует применять при выборе, применении и установке предохранительных устройств, предназначенных для защиты трубопроводов на различных стадиях холодильного цикла.
1.4 Настоящий стандарт распространяется:
- на теплообменники, в которых преобладают трубопроводы, предназначенные для охлаждения или нагрева воздуха;
-трубопроводы, встроенные в изделие (например, конденсаторный блок);
- монтаж трубопроводов в местах эксплуатации.
1.5 Настоящий стандарт применим к трубопроводам с внутренним давлением до минус 1 бар, с учетом вакуумирования трубопровода перед заправкой хладагентом.
1.6 Настоящий стандарт применим для условий как механических, так и температурных нагрузок, связанных с эксплуатацией холодильных систем. Настоящий стандарт применим к трубопроводам, подверженным максимально допустимым температурам, для которых расчетные напряжения для материалов получены с применением ГОСТ Р 71318.1 или как указано в настоящем стандарте. Максимальная расчетная температура трубопровода, спроектированного в соответствии с требованиями настоящего стандарта, не может превышать 200 °C, а максимальное расчетное давление не может превышать 160 бар.
1.7 Настоящий стандарт распространяется на трубопроводы, в которых основные составляющие части, находящиеся под давлением, изготовлены из металлических пластичных материалов в соответствии с разделом 4 и ГОСТ Р 71318.1.
Издание официальное
1
ГОСТ Р 71318.2—2024
2 Нормативные ссылки
В настоящем стандарте использованы нормативные ссылки на следующие стандарты:
ГОСТ 34891.1 (EN 378-1:2016) Системы холодильные и тепловые насосы. Требования безопасности и охраны окружающей среды. Часть 1. Основные требования, определения, классификация и критерии выбора
ГОСТ 34891.2 (EN 378-2:2016) Системы холодильные и тепловые насосы. Требования безопасности и охраны окружающей среды. Часть 2. Проектирование, конструкция, испытания, маркировка и документация
ГОСТ 34891.3 (EN 378-3:2016+А1:2020) Системы холодильные и тепловые насосы. Требования безопасности и охраны окружающей среды. Часть 3. Размещение оборудования и защита персонала
ГОСТ 34891.4 (EN 378-4:2016+А1:2019) Системы холодильные и тепловые насосы. Требования безопасности и охраны окружающей среды. Часть 4. Эксплуатация, техническое обслуживание, ремонт и восстановление
ГОСТ ISO 817 Хладагенты. Система обозначений
ГОСТ ISO 10893-1 Трубы стальные бесшовные и сварные. Часть 1. Автоматизированный контроль герметичности электромагнитным методом
ГОСТ ISO 10893-2 Трубы стальные бесшовные и сварные. Часть 2. Автоматизированный контроль вихретоковым методом для обнаружения дефектов
ГОСТ ISO 10893-3 Трубы стальные бесшовные и сварные. Часть 3. Автоматизированный контроль методом рассеяния магнитного потока по всей поверхности труб из ферромагнитной стали для обнаружения продольных и (или) поперечных дефектов
ГОСТ ISO 10893-4 Трубы стальные бесшовные и сварные. Часть 4. Контроль методом проникающих веществ для обнаружения поверхностных дефектов
ГОСТ ISO 10893-6 Трубы стальные бесшовные и сварные. Часть 6. Радиографический контроль сварных швов для обнаружения дефектов
ГОСТ ISO 10893-7 Трубы стальные бесшовные и сварные. Часть 7. Цифровой радиографический контроль сварных швов для обнаружения дефектов
ГОСТ ISO 10893-8 Трубы стальные бесшовные и сварные. Часть 8. Ультразвуковой метод автоматизированного контроля для обнаружения расслоений
ГОСТ ISO 10893-10 Трубы стальные бесшовные и сварные. Часть 10. Ультразвуковой метод автоматизированного контроля для обнаружения продольных и (или) поперечных дефектов по всей поверхности
ГОСТ ISO 10893-12 Трубы стальные бесшовные и сварные. Часть 12. Ультразвуковой метод автоматизированного контроля толщины стенки по всей окружности
ГОСТ ISO 11666 Неразрушающий контроль сварных соединений. Ультразвуковой контроль. Уровни приемки
ГОСТ ISO 17636-1 Неразрушающий контроль сварных соединений. Радиографический контроль. Часть 1. Способы рентгене- и гаммаграфического контроля с применением пленки
ГОСТ ISO 17636-2 Неразрушающий контроль сварных соединений. Радиографический контроль. Часть 2. Способы рентгене- и гаммаграфического контроля с применением цифровых детекторов
ГОСТ ISO 23277—2023 Неразрушающий контроль сварных соединений. Контроль проникающими веществами. Уровни приемки
ГОСТ Р 71318.1—2024 Холодильные системы и тепловые насосы. Оборудование, работающее под избыточным давлением. Часть 1. Сосуды. Общие требования
ГОСТ Р ИСО 2553 Сварка и родственные процессы. Условные обозначения на чертежах. Сварные соединения
ГОСТ Р ИСО 3452-1 Контроль неразрушающий. Проникающий контроль. Часть 1. Основные требования
ГОСТ Р ИСО 4063 Сварка и родственные процессы. Перечень и условные обозначения процессов
ГОСТ Р ИСО 5817 Сварка. Сварные соединения из стали, никеля, титана и их сплавов, полученные сваркой плавлением (исключая лучевые способы сварки). Уровни качества
ГОСТ Р ИСО 10042 Сварка. Сварные соединения из алюминия и его сплавов, полученные дуговой сваркой. Уровни качества
2
ГОСТ Р 71318.2—2024
ГОСТ Р ИСО 10893-11 Трубы стальные бесшовные и сварные. Часть 11. Ультразвуковой метод автоматизированного контроля сварных швов для обнаружения продольных и (или) поперечных дефектов
ГОСТ Р ИСО 16826 Неразрушающий контроль. Ультразвуковой контроль. Выявление дефектов, перпендикулярных к поверхности
ГОСТ Р ИСО 17637 Контроль неразрушающий. Визуальный контроль соединений, выполненных сваркой плавлением
ГОСТ Р ИСО 17640 Неразрушающий контроль сварных соединений. Ультразвуковой контроль. Технология, уровни контроля и оценки
Примечание — При пользовании настоящим стандартом целесообразно проверить действие ссылочных стандартов в информационной системе общего пользования — на официальном сайте Федерального агентства по техническому регулированию и метрологии в сети Интернет или по ежегодному информационному указателю «Национальные стандарты», который опубликован по состоянию на 1 января текущего года, и по выпускам ежемесячного информационного указателя «Национальные стандарты» за текущий год. Если заменен ссылочный стандарт, на который дана недатированная ссылка, то рекомендуется использовать действующую версию этого стандарта с учетом всех внесенных в данную версию изменений. Если заменен ссылочный стандарт, на который дана датированная ссылка, то рекомендуется использовать версию этого стандарта с указанным выше годом утверждения (принятия). Если после утверждения настоящего стандарта в ссылочный стандарт, на который дана датированная ссылка, внесено изменение, затрагивающее положение, на которое дана ссылка, то это положение рекомендуется применять без учета данного изменения. Если ссылочный стандарт отменен без замены, то положение, в котором дана ссылка на него, рекомендуется применять в части, не затрагивающей эту ссылку.
3 Термины, определения и сокращения
3.1 Термины и определения
В настоящем стандарте применены термины по ГОСТ 34891.1, ГОСТ Р 71318.1, а также следующий термин с соответствующим определением:
3.1.1 змеевик (coil): Теплообменник, состоящий из одной трубы или нескольких трубок, используемый для охлаждения или нагрева воздуха.
Примечания
1 Может быть изготовлен из одной или нескольких изогнутых труб.
2 См. рисунок 1.
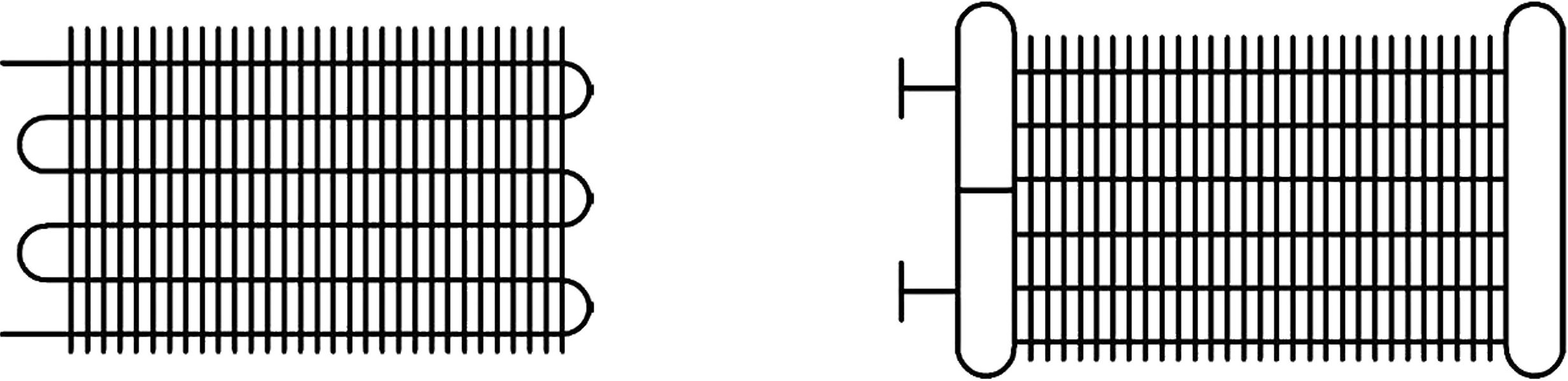
а) Змеевик с коленами и прямыми трубками б) Змеевик с коленом и коллекторами
Рисунок 1 — Змеевики
3.2 Сокращения
В настоящем стандарте применены следующие сокращения:
DBA — проектирование путем анализа данных;
DBF —проектирование путем расчета по формулам;
3
ГОСТ Р 71318.2—2024
De — внешний диаметр трубы, мм;
DN —номинальный диаметр;
е —толщина стенок трубопровода, мм;
f —номинальное расчетное напряжение при расчетной температуре, МПа;
Рс — расчетное давление (в формулах Рс можно заменить на Р);
Pd —проектное давление, МПа;
PS — максимально допустимое давление, МПа;
РТ —проникающее испытание;
R — радиус кривизны трубы;
RT —рентгенографическое испытание;
tc —расчетная температура, °C;
td —проектная температура, °C;
^тах —максимально допустимая температура, °C;
TSmin — минимально допустимая температура, °C;
UT —ультразвуковое испытание;
VT —визуальный контроль;
z — коэффициент соединения сварных швов.
4 Материалы
4.1 Общие положения
Если к материалам не предъявляется специальных требований настоящего стандарта, они должны соответствовать требованиям ГОСТ Р 71318.1.
Разрешается использовать неметаллические материалы (например, прокладки, покрытия, изоляционные материалы, смотровые стекла) при условии, что они совместимы с другими используемыми материалами, хладагентами, маслами и смазками.
4.2 Требования к материалам, применяемым в частях оборудования, находящихся под давлением
Материалы, указанные в настоящем стандарте, предназначены для использования в трубопроводах холодильного оборудования. При необходимости использования материала, не указанного в настоящем стандарте, следует учитывать общие и индивидуальные требования к холодильным установкам.
4.3 Материалы
4.3.1 Общие положения
4.3.1.1 Если трубопроводы изготовлены из материалов, указанных ниже, то они удовлетворяют требованиям, предъявляемым к оборудованию, находящемуся под давлением.
4.3.1.2 Если механические свойства материала могут измениться в процессе изготовления трубопровода, то его следует выбирать из групп материалов, установленных в ГОСТ Р 71318.1—2024 (приложение А):
- группы стали: 1.1, 1.2, 8.1;
- группы алюминия и алюминиевых сплавов: 21,22;
- группы меди: 31, 32, 33, 34, 35.
4.4 Требования по предотвращению хрупкого разрушения
Применяют требования ГОСТ Р 71318.1.
Хрупкое разрушение следует определять только тогда, когда толщина материала позволяет изготовить образец для испытаний с минимальным размером сечения (5 * 10) мм.
4.5 Документация на материалы
Применяют требования ГОСТ Р 71318.1—2024 (пункт 4.5).
4
ГОСТ Р 71318.2—2024
4.6 Материалы для частей оборудования, не находящихся под давлением
Применяют требования ГОСТ Р 71318.1—2024 (пункт 4.6).
5 Классификация трубопроводов
Напорные трубопроводы классифицируют на две категории в соответствии с таблицей 1 и со следующими положениями:
а) произведение максимально допустимого давления PS (в барах) на DN;
б) классификация рабочих сред по ГОСТ Р 71318.1—2024 (пункт 5.2);
в) агрегатного состояния рабочей среды:
1) газы, сжиженные газы, газы, растворенные под давлением, и те жидкости, давление паров которых при максимально допустимой температуре превышает 0,5 бар;
2) жидкости, имеющие давление паров при максимально допустимой температуре не более 0,5 бар.
В настоящем стандарте части оборудования, содержащие хладагент, рассматриваются как газовый контур.
Таблица 1 — Классификация трубопроводов по категориям
Категория | Среда по ГОСТ Р 71318.1—2024 (пункт 5.2) | Критерий |
X | Группа 1 | PS < 0,5 бар, если нет ограничений по DN или 0,5 бар < PS < 10 бар, DN < 100 или 10 бар < PS < 40 бар: PS * DN < 1000 или PS > 40 бар, DN < 25 |
Группа 2 | PS < 0,5 бар, если нет ограничений по DN или 0,5 бар < PS < 35 бар, PS * DN < 3500 или PS>35 бар, DN< 100 | |
Y | Группа 1 | Кроме критериев для категории X группы 1 |
Группа 2 | Кроме критериев для категории X группы 2 |
6 Проектирование
6.1 Общие положения
Требования раздела 6 распространяются на напорные трубопроводы, изготовленные из материалов, указанных в разделе 4. Части оборудования, находящиеся под давлением, должны выдерживать проектное давление Pd при проектной температуре td.
Для трубопроводов в местах эксплуатации следует применять требования ГОСТ 34891.2.
6.2 Коррозия и защита от коррозии
Применяют требования ГОСТ Р 71318.1—2024 (пункты 6.2 и 6.3).
6.3 Нагрузка
Эксплуатационная нагрузка на трубопровод, которая установлена в настоящем стандарте, состоит:
- из внутреннего/внешнего давления;
- температуры окружающей среды и рабочей температуры;
- статического давления и массы содержимого трубопровода в условиях эксплуатации и испытаний;
- силы, передающейся от опор и креплений.
Требования ГОСТ 34891.2 следует применять к трубным опорам и креплениям.
Изготовителю следует указать максимально допустимое давление PS для отдельных частей или трубопровода в целом.
Pd и Рс должны быть не менее PS.
5
ГОСТ Р 71318.2—2024
6.4 Проектная температура td и минимальная температура материала
Максимальная проектная температура частей оборудования, содержащих хладагент под давлением, должна быть не ниже максимально допустимой температуры TSmax.
TSmax не должна быть ниже температуры насыщения (температуры точки росы), соответствующей PS рабочей среды, и максимальной рабочей температуры.
Локальные высокие температуры (например, перегретый хладагент) следует учитывать в соответствующих местах напорного трубопровода.
Минимальная расчетная температура не должна превышать минимально допустимую темпера-ТУРУ ^тщ-
Поскольку TSmin — это минимальная температура, которая может возникнуть во время работы или в условиях простоя оборудования, то данную температуру следует учитывать при выборе материалов, чтобы избежать хрупкого разрушения. TS^ не должна превышать 20 °C.
Локальные низкие температуры, связанные с быстрой заправкой хладагентов или их смесей (расширение летучей жидкости в вакуум), следует учитывать в соответствующих местах трубопровода.
Для данных мест испытание на удар следует проводить при низких температурах в соответствии с 4.4.
6.5 Расчетная температура tc
6.5.1 Общие положения
Расчетную температуру tc следует использовать для определения соответствующего проектного напряжения для выбранного материала.
6.5.2 Трубопровод без нагревателя
tc, если она не определена на основе подробных расчетов, испытаний и измерений, следует определять следующим образом:
1) трубопровод теплоизолирован: tc равно 7Smax;
2)трубопровод не теплоизолирован:
- при температуре рабочей среды менее 40 °C tc равна TSmax;
- при температуре рабочей среды выше или равной 40 °C tc равна VSmax, за исключением болтовых соединений, где tc равно 80 % TSmax.
6.5.3 Трубопровод с нагревателем
Если трубопровод оборудован нагревателем, расчетную температуру следует определять испытанием или принимать равной температуре, определенной в 6.5.2 плюс 50 К.
Изготовителю при выборе нагревателя следует с помощью количественных показателей оценить риск перегрева рабочей среды или материалов и принять соответствующие меры для ограничения такого риска, например путем установки предохранительных устройств и/или включения соответствующих предупредительных знаков, и/или включения соответствующих инструкций в документацию.
6.6 Коэффициент соединения сварных швов
Для расчета требуемой толщины сварных соединений важных компонентов (например, цилиндров, конусов и сферических компонентов) формулы содержат коэффициент соединения сварных швов z.
Примерами сварных соединений для z являются:
- продольные или винтовые швы цилиндрической обечайки;
- продольные швы конической обечайки;
- любой основной сварной шов в днище или сферическом сосуде;
- основные сварные швы в днище, изготовленном из двух и более деталей.
К сварным соединениям для z не относятся следующие сварные соединения:
- окружной сварной шов между цилиндрической или конической обечайкой и фланцем или заглушкой, кроме полусферической;
- сварные швы крепления патрубков к обечайкам;
- сварные швы, подвергающиеся исключительно сжимающим напряжениям.
Примечание — Кольцевые соединения могут стать основными из-за внешних нагрузок.
Для нормальной рабочей нагрузки значение z приведено в таблице 2.
Группа испытаний компонентов в местах важных сварных соединений определяет минимальное количество испытаний для сварных швов, включая сварные швы патрубков.
6
Таблица 2 — Группы испытаний
Коэффициент соединения сварных швов | Группы испы-тани1> | Разрешенный материал. Группа стали | Максимальная толщина по категории материала, мм | Сварочный процесс | Диапазон рабочих температур, °C | Группы рабочей среды | Объем визуального контроля,% | Объем неразрушающего контроля, кроме визуального контроля, основных сварных соединений,% | |
Группа стали 1.1/8.1 | Группа стали 1.2 | ||||||||
1 | 1b | 1.1/1.2/8.1 | Не ограничен2) | Не ограничен2) | Не ограничен2) | Не ограничен2) | 1/2 | 100 | 100 |
1 | 2Ь | 1.1/1.2/8.1 | <50 | <30 | Только полностью механическая сварка3) | Не ограничен2) | 1/2 | 100 | 100—104)’5) |
0,85 | ЗЬ | 1.1/1.2/8.1 | <50 | <30 | Не ограничен2) | Не ограничен2) | 1/2 | 100 | 10 |
0,7 | 4 | 1.1/1.2/8.1 | <16 | <12 | Не ограничен2) | 50—200 | 1/2 | 100 | 0 |
1) Определение групп испытаний. Все группы испытаний требуют визуального осмотра. 2) «Не ограничен» означает отсутствие дополнительных ограничений при испытаниях. Ограничения, указанные в таблице, являются ограничениями, налагаемыми испытаниями. Другие ограничения (такие как конструкция, ограничения по материалам), также должны быть приняты во внимание. 3) Полностью механизированный и/или автоматический процесс сварки, при котором, по крайней мере, головка сварочного агрегата, а также подача сварочных расходных материалов механизированы. 4) Первая цифра применяется изначально, вторая цифра применяется после испытания. Процент относится к проценту сварных швов каждого отдельного сосуда. 5) Объем неразрушающего контроля, отличный от визуального контроля, может быть заменен разрушающим контролем для группы 2Ь. |
ГОСТ Р 71318.2—2024
ГОСТ Р 71318.2—2024
Для материалов, отличных от стали группы 1.1, 1.2 или 8.1, следует использовать применимые требования.Объем неразрушающего контроля и применимые методы контроля стальных сварных соединений, кроме визуального, установлены в ГОСТ Р 71318.1—2024 (пункт 8.7).
При отсутствии важных сварных соединений применяют группу испытаний 4 со значением z, равным 1,0 для целей расчета.
6.7 Расчетное напряжение
Величина расчетного напряжения должна учитывать условия проектирования и испытаний. Требования ГОСТ Р 71318.1—2024 (пункт 6.12) следует применять, когда материалы не подвержены ползучести. Если материалы подвержены ползучести, используют применимые требования.
Значения предела текучести и предела прочности при растяжении материала должны соответствовать значениям для окончательного изготовленного состояния и указанным в соответствующих проектных спецификациях.
Данные значения можно использовать для целей проектирования, при условии, что термическая обработка не приводит к более низким значениям.
Для металлических материалов значение при 20 °C следует применять для температур до 50 °C включительно. Если сварной или паяный металл после изготовления дает более низкие значения прочности, то следует использовать эти значения.
При оценке исключительных условий эксплуатации (например, вакуум -1 бар) расчетное напряжение следует принимать за условие испытаний, а температуру материала принимать такой же, как и для исключительных условий.
6.8 Дверки и люки для доступа и осмотра, устройства для подачи и дренажа, устройства для заправки и извлечения хладагента
6.8.1 Дверки и люки для доступа и осмотра
Дополнительные требования для смотровых окон и дверей доступа отсутствуют, за исключением непосредственно монтируемых на трубопроводе. В случае коррозионно-активных рабочих сред изготовителю следует указать в документации по эксплуатации рекомендуемую периодичность и методы проверок.
6.8.2 Подача и дренаж
Конструкция сосуда должна обеспечивать достаточную подачу испытательной среды во время гидравлического испытания и ее слив после проведения испытания.
6.8.3 Обеспечение заправки и извлечения хладагента
Для предотвращения опасности выброса хладагента применяют требования ГОСТ 34891.2, ГОСТ 34891.3 и ГОСТ 34891.4 во время заправки холодильной системы или извлечения хладагента из нее.
Если часть трубопровода применяют для сбора и хранения хладагента, документация должна содержать значение максимального уровня хладагента и применение предохранительных устройств.
6.9 Методы проектирования
6.9.1 Общие положения
6.9.1.1 Общие положения
Основным методом проектирования является метод проектирования путем расчета по формулам DBF. Кроме того, для дополнения или замены DBF можно использовать два других метода:
а) проектирование путем анализа данных DBA;
б) экспериментальные методы.
Правила применения экспериментальных методов приведены в ГОСТ Р 71318.1—2024 (приложение Е). Для трубопроводов категории X дополнительные методы приведены в 6.9.1.2 и 6.9.1.3.
6.9.1.2 Типовое испытание на разрыв
Трубопровод должен выдерживать давление не менее 3 PS без разрыва.
Температура при проведении испытаний должна составлять не менее 20 °C. В случае если расчетная температура для медных или алюминиевых трубопроводов превышает 125 °C, температура испытания должна составлять не менее 200 °C. Для материалов, отличных от стали, меди или алюминия, влияние температуры на поведение материала следует оценить и результаты оценки включить в процедуру испытаний.
8
ГОСТ Р 71318.2—2024
6.9.1.3 Типовое испытание на усталость
Процедура испытаний и критерии приемки следующие:
а) три образца испытывают при двукратном PS;
б) три дополнительных образца подвергают следующим этапам испытаний:
этап 1: испытание на PS без остаточных деформаций и утечек;
этап 2: 250 000 циклов от 0,2 PS или ниже до 0,7 PS или выше;
этап 3: испытание в соответствии с ГОСТ Р 71318.1—2024, формула (И.1).
Во время проведения испытаний ни один из шести образцов не должен разорваться, лопнуть или дать течь. Температура испытаний должна соответствовать требованиям 6.9.1.2.
6.9.2 Расчет по формулам DBF
6.9.2.1 Прямой трубопровод
Минимальную требуемую толщину стенок без припуска на коррозию для прямой трубы определяют по формуле
6.9.2.2 Изгиб трубопровода
Для изогнутой трубы, для материала, отличного от меди группы 31, минимальную требуемую толщину стенок перед изгибом без припуска на коррозию определяют по формуле
Для меди группы 31 формулу (1) применяют, если расчет производится для отожженного материала и при отсутствии термической обработки в зоне изгиба. В противном случае применяют формулу (2).
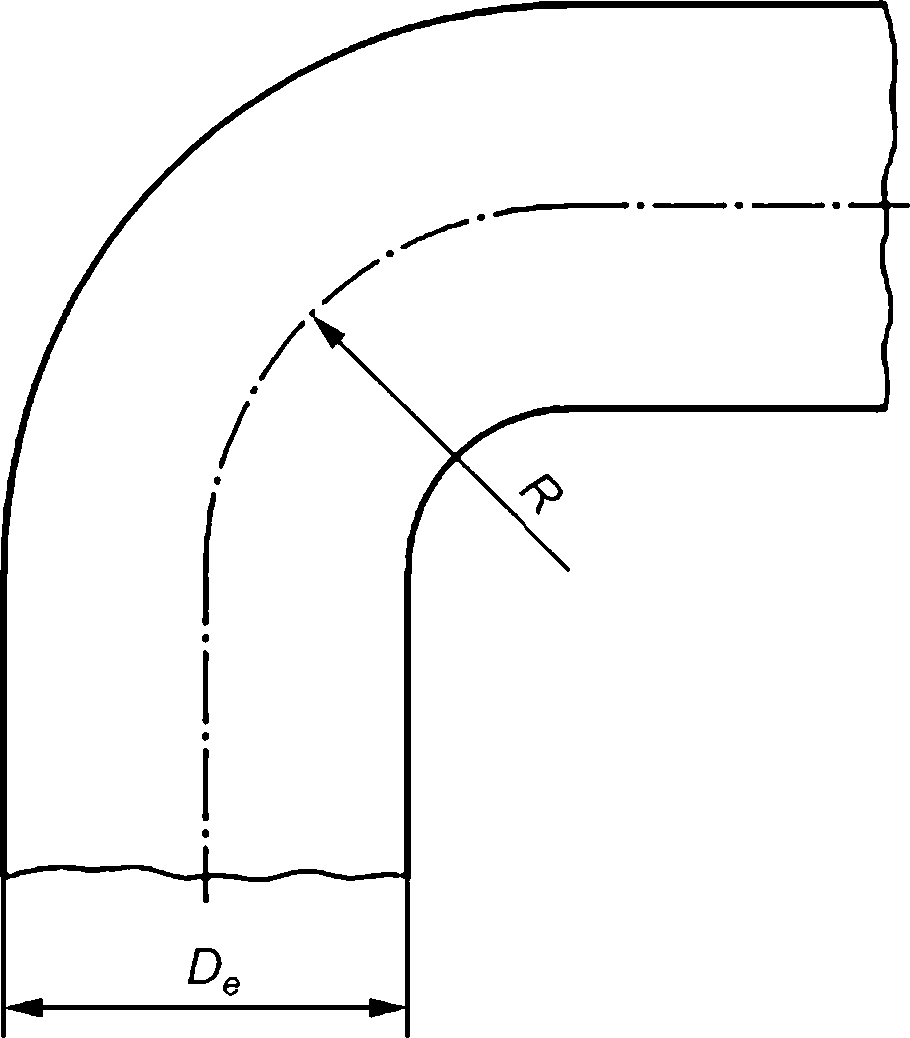
De — внешний диаметр трубы; R — радиус кривизны трубы
Рисунок 2 — Изгиб трубопровода
6.9.3 Проектирование соединений
Применяют требования ГОСТ Р 71318.1—2024 (пункт 6.14.3).
7 Производство
7.1 Прослеживаемость материалов
Для категории трубопровода Y (см. таблицу 1) применяют требования ГОСТ Р 71318.1—2024 (пункт 7.1).
9
ГОСТ Р 71318.2—2024
7.2 Производственные допуски
Изготовителю следует указать производственные допуски в спецификациях к оборудованию.
7.3 Неразъемные соединения
Применяют требования ГОСТ Р 71318.1—2024 (пункт 7.3).
7.4 Формование деталей, работающих под давлением
Применяют требования ГОСТ Р 71318.1—2024 (пункт 7.4).
7.5 Внутренняя чистота
Применяют требования ГОСТ Р 71318.1—2024 (пункт 7.5).
7.6 Ремонт/модернизация
Ремонт и изменения документируют.
Процедуры выполнения неразъемных соединений и персонал аттестуют в соответствии с требованиями настоящего стандарта.
7.7 Заключительные работы
Трубопроводы защищают от загрязнения, в том числе при коррозии и попадании посторонних частиц при транспортировании и хранении.
8 Испытания и проверки
8.1 Проведение проверок и испытаний
Трубопровод следует проверить, испытать и осмотреть на соответствующих стадиях проектирования и производства.
Тип, количество, глубину и частоту проверок, испытаний и осмотров каждого сосуда следует основывать:
- на группе рабочей среды, произведении давления на объем и агрегатном состоянии рабочей среды;
- категории испытаний, учитывающей коэффициент соединения сварных швов, процессы сварки, группы и толщину материалов;
- обеспечении того, чтобы конструкция, материалы, методы изготовления и испытаний соответствовали требованиям настоящего стандарта.
Другие факторы, такие как процедуры формования и подготовки кромок, также должны влиять на уровень контроля и испытаний.
Все действия по проверке, испытаниям и осмотру следует документировать.
8.2 Проектная документация, рассмотрение и утверждение
8.2.1 Общие положения
Изготовление сосуда не следует начинать до тех пор, пока проектная документация не будет разработана и утверждена изготовителем.
8.2.2 Проектная документация
Результаты проверки должны подтвердить, что конструкторская документация соответствует настоящему стандарту.
Изготовитель может использовать одну и ту же конструкторскую документацию для нескольких трубопроводов при соблюдении следующих условий:
а) трубы изготавливаются одним и тем же изготовителем с использованием одних и тех же процессов (например, формовка, соединение, термообработка);
б) трубопроводы выполняют ту же функцию в холодильной системе (например, трубопроводы низкого давления, трубопроводы высокого давления, маслопроводы);
в) трубопроводы применяют к одним и тем же группам сред;
г) трубопровод имеет одинаковые условия эксплуатации (диапазон давления/температуры);
10
ГОСТ Р 71318.2—2024
д) материал трубопровода соответствует спецификации, указанной в технической документации;
е) трубопровод имеет одинаковые расчетные условия, т. е. допуск на коррозию, защиту от коррозии, совместимость материалов со средами;
ж) трубопроводы имеют одинаковый коэффициент соединения для сварных швов;
и) трубопровод имеет аналогичные нагрузки без давления и местные нагрузки.
В документации следует отразить как минимум следующее:
а) общее описание трубопровода;
б) перечень трубопроводов, на которые распространяется конструкторская документация;
в) рабочие и расчетные условия: давление, температуру, статическую, циклическую и динамическую нагрузку, где применимо, допуск на коррозию, среду или группу сред, испытательное давление и испытательную среду;
г) перечень используемых стандартов на продукцию, других документов или принятых решений, а также идентификацию компонентов, которые разработаны не в соответствии со стандартами;
д) проектный(е) чертеж(и), который(ые) представляет(ют) собой документ (или комплект документов), содержащий всю информацию о том, что трубопровод полностью соответствует требованиям настоящего стандарта. Проектный чертеж при необходимости может быть дополнен более подробными чертежами или схемами узлов или компонентов. Чертежи могут быть дополнены письменным описанием для облегчения понимания;
е) информацию о маркировке;
ж) список выбранных материалов с указанием сертификатов на материал и специальными характеристиками, если применимо;
и) проектные расчеты и/или протокол испытаний в случае частичного или полного применения экспериментального метода;
к) информацию о неразъемных соединениях:
1) описание неразъемного соединения: форма, подготовка, предполагаемый процесс соединения деталей или обозначения в соответствии с ГОСТ Р ИСО 2553 и ГОСТ Р ИСО 4063;
2) присадочные и вспомогательные материалы в случае сварки и/или пайки;
3) ссылку на аттестованную процедуру соединения деталей и/или ссылку на стандарты или другие документы;
4) коэффициент соединения сварных швов, где применимо;
5) процедуры термической обработки после сварки, если применимо;
6) процедуры формовки, если они влияют на конструкцию и/или характеристики материала;
7) процедуры термообработки, необходимые для восстановления характеристик материала;
8) процедуры неразрушающего контроля;
9) перечень испытаний и проверок, проводимых на этапах изготовления, необходимых для обеспечения соответствия трубопровода конструкторской документации и, если применимо, ссылки на применяемые методики и (или) стандарты;
10) информацию об аттестации работников для проведения работ для неразъемного соединения и для неразрушающего контроля (например уровень квалификации, ссылка на стандарт или процедуры изготовителя).
8.2.3 Экспертиза проекта и утверждение проекта
Применяют требования ГОСТ Р 71318.1—2024 (пункт 8.2.3).
8.2.4 Изменение проектной документации
Применяют требования ГОСТ Р 71318.1—2024 (пункт 8.2.4).
8.3 Испытание типового образца
Применяют требования ГОСТ Р 71318.1—2024 (пункт 8.3).
8.4 Калибровка
Применяют требования ГОСТ Р 71318.1—2024 (пункт 8.4).
8.5 Материал
Применяют требования ГОСТ Р 71318.1—2024 (пункт 8.5).
11
ГОСТ Р 71318.2—2024
8.6 Производство
Применяют требования ГОСТ Р 71318.1—2024 (пункт 8.6).
8.7 Неразрушающий и разрушающий контроль
Применяют требования ГОСТ Р 71318.1—2024 (пункт 8.7 и 8.8).
8.8 Элементы субподряда
Изготовителю следует установить требования к выполнению субподрядных работ и следить за правильностью их выполнения.
8.9 Заключительный осмотр
8.9.1 Общие положения
Готовый трубопровод, спроектированный и изготовленный в соответствии с настоящим стандартом, подлежит окончательной проверке на соответствие конструкторской документации и настоящему стандарту.
Окончательную проверку следует проводить после завершения всех производственных операций до нанесения любого покрытия, независимо от его типа.
Если проверка внутренних элементов из-за их размещения невозможна после завершения монтажа трубопровода, то изготовителю следует проводить заключительный осмотр таких элементов перед их установкой.
Окончательная проверка состоит:
- из визуального осмотра трубопровода;
- проверки документации;
- испытания давлением.
8.9.2 Визуальный осмотр
Объем визуального осмотра включает:
- соответствие конструкции чертежам, в том числе размерам, с учетом допусков, указанных в конструкторской документации и настоящем стандарте;
- состояние в готовом трубопроводе сварных швов, паяных соединений, соединений патрубков, креплений и опор с точки зрения внешнего вида неразъемных соединений, общей геометрии на соответствие конструкторской документации и настоящего стандарта;
- сверку маркировки материала с соответствующими документами и зарегистрированными записями на материал, если прослеживаемость материала осуществляется посредством маркировки;
- сверку маркировки неразъемных соединений сданными о проведении неразрушающего контроля и с документацией, если это применимо.
Любое несоответствие должно быть задокументировано, а затем исправлено, после чего перед продолжением работ трубопровод следует осмотреть повторно.
8.9.3 Проверка документации
В данную проверку следует включать, как минимум, следующее:
- проверку документов (документов: подтверждающих квалификацию сварщиков, паяльщиков и операторов; специалистов по проведению неразрушающего контроля; аттестации процедур выполнения неразъемных соединений, протоколы испытаний, протоколы неразрушающего контроля, данные о термообработке после сварки, сертификаты на материалы, протоколы визуального и инструментального контроля);
- для трубопроводов категории Y (см. таблицу 1) проверку прослеживаемости примененных материалов по документально оформленным записям.
Любое несоответствие документируют и исправляют, а документацию повторно проверяют перед продолжением работ.
8.9.4 Испытание давлением
8.9.4.1 Испытание давлением для трубопроводов категории X проводят как определено в таблице 1. Имеются три альтернативных метода испытания трубопровода давлением:
- испытание давлением в соответствии с 8.9.4.2, или
- типовое испытание на разрыв в соответствии с 6.9.1.2, или
- типовое испытание на усталость по 6.9.1.3.
12
ГОСТ Р 71318.2—2024
8.9.4.2 Испытание давлением для трубопроводов категории Y проводят в соответствии с таблицей 1. Механическую прочность и герметичность трубопроводов, изготовленных в соответствии с настоящим стандартом, определяют путем проведения испытаний, установленных в ГОСТ Р 71318.1—2024 (приложение И), со следующими условиями и вариантами:
- вариант 1: трубопровод испытывают при давлении, установленном в ГОСТ Р 71318.1—2024 (приложение И), никаких дополнительных мер не требуется.
- вариант 2: в качестве альтернативы испытание может быть проведено при пневматическом испытательном давлении, в 1,1 раза превышающем максимально допустимое давление на трубопроводе или отдельном узле. Перед испытанием следует провести 100 % визуальный контроль всех соединений. Для сварных соединений неразрушающий контроль следует выполнить в соответствии таблицей 3, а методы неразрушающего контроля и критерии приемки должны соответствовать установленным в таблице 4.
Примечание — В некоторых случаях использование воды вредно для трубопровода (окисление, отсутствие возможности правильной сушки после испытания) и при испытании трубопровода на сборке (в бессальниковых или герметичных компрессорах с маслом в качестве смазки имеются ограничения по влажности).
Таблица 3 — Объем неразрушающего контроля сварных соединений при испытании пневматическим давлением по варианту 2
Тип сварного шва | Степень неразрушающего контроля |
Кольцевые сварные швыЧ Приварные швы отводов и патрубков DN > 100 | 10 %2) РТили UT |
Приварные швы отводов и патрубков DN <100 | 10 % РТ |
Приварка патрубков и патрубков DN < 100 и сварка враструб | 100 % РТили UT |
1) Для сварных швов, если UT или RT не позволяют провести четкую оценку, необходимо провести РТ. 2) Для DN< 600, 10 % сварных швов подлежат контролю 100 %, при DN > 600 10 % общей длины сварных швов. |
Таблица 4 — Технологии неразрушающего контроля, методы, критерии приемки сварных соединений
Метод неразрушающего контроля | Условия проведения | Критерии приемки |
Визуальный осмотр VT | ГОСТ Р ИСО 17637 | Для стали: ГОСТ Р ИСО 5817, уровень качества В Для алюминия: ГОСТ Р ИСО 10042, уровень качества В1) |
Рентгенография RT | ГОСТ ISO 17636-1 или ГОСТ ISO 17636-2 ГОСТ ISO 17636-2, класс В2) | Для стали: устанавливает изготовитель Для алюминия: устанавливает изготовитель |
Ультразвуковой контроль UT | Ручной UT, ГОСТ Р ИСО 17640 Автоматический UT, ГОСТ ISO 10893-1, ГОСТ ISO 10893-2, ГОСТ ISO 10893-3, ГОСТ ISO 10893-4, ГОСТ ISO 10893-6, ГОСТ ISO 10893-7, ГОСТ ISO 10893-8, ГОСТ ISO 10893-10, ГОСТ ISO 10893-124> Для толщины t, мм 4 < f < 40 класс А f > 40 < 100 класс В f > 100 класс С | ГОСТ ISO 11666, уровень приемки 23) |
13
ГОСТ Р 71318.2—2024
Окончание таблицы 4
Метод неразрушающего контроля | Условия проведения | Критерии приемки |
Проникающие испытания РТ | ГОСТ Р ИСО 3452-1 и параметры испытаний ГОСТ ISO 23277—2023, таблица А.1 | ГОСТ ISO 23277, уровень приемки 2 |
1) Для дефектов № 1.6 (поверхностные поры), 1.11 (чрезмерная выпуклость) и 1.14 (чрезмерное проникновение) в соответствии с ГОСТ Р ИСО 10042 достаточно уровня С. 2) Максимальная площадь для однократного облучения должна соответствовать требованиям класса А ГОСТ ISO 17636-1 или ГОСТ ISO 17636-2. 3) Плоские дефекты не допускаются. Для е > 60 мм UT проверку дефектов перпендикулярно поверхности проводят в соответствии с ГОСТ Р ИСО 16826. 4) Серию ГОСТ ISO 10893 применяют к неразрушающему контролю стальных труб. До тех пор, пока не будет выпущен стандарт неразрушающего контроля для автоматического ультразвукового контроля материалов из алюминия и алюминиевых сплавов, ГОСТ Р ИСО 10893-11 и ГОСТ ISO 10893-8 следует использовать в качестве стандарта для приемки. |
8.9.5 Испытания на герметичность
Применяют требования ГОСТ Р 71318.1—2024 (пункт 8.10.5).
8.10 Маркировка
Для трубопровода категории Y маркировку следует наносить на сборку (например, автономная система, конденсаторный блок) в соответствии с ГОСТ 34891.2 или на отдельный трубопровод в соответствии с тем, как установлено ниже.
Трубопровод следует поставлять с маркировкой, которая должна быть доступной, читаемой и закреплена несъемным способом.
Способ нанесения маркировки не должен повреждать трубопровод. Маркировка может быть выполнена:
- прямой маркировкой на трубопроводе, или
- отдельной заводской табличкой или ярлыком, закрепленными несъемным способом к оборудованию. Содержание маркировки должно включать как минимум следующее:
- идентификацию изготовителя трубопровода: наименование, логотип или товарный знак и почтовый адрес;
- идентификацию трубопровода: тип и/или серийный номер;
- год выпуска.
Следующие три позиции могут быть указаны либо на заводской табличке трубопровода, либо на заводской табличке всей сборки. Следует избегать дублирования информации:
- максимально допустимое давление PS в барах и минимальное давление при нормальной эксплуатации трубопровода ниже 0 бар;
- максимально допустимая температура TSmax;
- минимально допустимая температура TSmin.
На заводской табличке трубопровода, на заводской табличке сборки или документации следует указать следующую информацию:
- обозначение хладагента по ГОСТ ISO 817 или, как минимум, группу рабочей среды 1 или 2;
- обозначение среды (если не хладагент) или, как минимум, группу рабочей среды 1 или 2;
- DN или внутренний диаметр.
8.11 Документация
8.11.1 Общие положения
После завершения проверки и всех отделочных работ каждый трубопровод категории У следует поставлять со следующей документацией.
8.11.2 Инструкции по эксплуатации
Изготовителю необходимо предоставить, где это применимо, следующую информацию:
- критерии выбора трубопровода при его использовании;
- минимальный и максимальный расход;
14
ГОСТ Р 71318.2—2024
- тип и качество среды (как минимум, группа среды 1 или 2);
-данные для монтажа, включая максимальные внешние нагрузки;
- вес, размеры;
- данные о правильном применении;
- защита от коррозии;
- теплоизоляция;
- устройства безопасности;
- обслуживание;
- периодическая проверка;
- допуск на коррозию;
- периодическая чистка.
8.11.3 Техническая документация для пользователя
Трубопровод следует поставлять с руководством по эксплуатации, позволяющим обеспечить должный периодический осмотр и ремонт и включающим в себя:
- чертеж трубопровода;
- перечень материалов, используемых для отдельных частей под давлением;
- информацию о неразъемных соединениях;
- значение примененного испытательного давления с указанием даты проведения испытания;
- данные об испытании на утечку, если проводилось;
-документы, подтверждающие соответствие.
8.11.4 Записи
Изготовителю следует хранить следующие записи и данные в течение как минимум 10 лет после изготовления трубопровода:
- проектную документацию, если применимо, включая данные проверки проекта;
- если применимо, данные о типовых испытаниях;
- записи об изменениях конструкторской документации;
- аттестации процессов проведения процедур неразъемных соединений;
- данные по неразъемным соединениям и неразрушающему контролю;
-документы, выданные проверяющими органами, если применимо;
- данные или ссылки на документы, позволяющие оценить соответствие трубопровода настоящему стандарту.
Дополнительно для каждого изготовленного трубопровода и там, где это применимо:
- список использованных материалов;
- сертификаты на материалы;
- график проверок;
- отчеты о проверках;
- результаты неразрушающего контроля;
- записи о термообработке;
- любые отчеты о несоответствиях;
- протоколы заключительных испытаний;
-документы, подтверждающие соответствие;
- руководство по эксплуатации.
15
ГОСТ Р 71318.2—2024
УДК 66.065.54:006.354
ОКС 23.020.30
27.080
27.200
Ключевые слова: холодильная система, тепловой насос, давление, трубопровод, испытания
Редактор Е.Ю. Митрофанова Технический редактор В.Н. Прусакова Корректор С.И. Фирсова Компьютерная верстка М.В. Малеевой
Сдано в набор 16.09.2024. Подписано в печать 30.09.2024. Формат 60x847s. Гарнитура Ариал. Усл. печ. л. 2,32. Уч.-изд. л. 1,80.
Подготовлено на основе электронной версии, предоставленной разработчиком стандарта
Создано в единичном исполнении в ФГБУ «Институт стандартизации» , 117418 Москва, Нахимовский пр-т, д. 31, к. 2.