МЕЖГОСУДАРСТВЕННЫЙ СОВЕТ ПО СТАНДАРТИЗАЦИИ, МЕТРОЛОГИИ И СЕРТИФИКАЦИИ (МГС)
INTERSTATE COUNCIL FOR STANDARDIZATION, METROLOGY AND CERTIFICATION (ISC)
ГОСТ
34939—
2023
МЕЖГОСУДАРСТВЕННЫЙ СТАНДАРТ
ЛОКОМОТИВЫ
Требования к прочности и динамическим качествам
Издание официальное
Москва Российский институт стандартизации 2023
Предисловие
Цели, основные принципы и общие правила проведения работ по межгосударственной стандартизации установлены ГОСТ 1.0 «Межгосударственная система стандартизации. Основные положения» и ГОСТ 1.2 «Межгосударственная система стандартизации. Стандарты межгосударственные, правила и рекомендации по межгосударственной стандартизации. Правила разработки, принятия, обновления и отмены»
Сведения о стандарте
1 РАЗРАБОТАН Акционерным обществом «Научно-исследовательский и конструкторско-технологический институт подвижного состава» (АО «ВНИКТИ») и Акционерным обществом «Научно-исследовательский институт железнодорожного транспорта (АО «ВНИИЖТ»).
2 ВНЕСЕН Межгосударственным техническим комитетом по стандартизации МТК 524 «Железнодорожный транспорт»
3 ПРИНЯТ Евразийским советом по стандартизации, метрологии и сертификации (протокол от 20 января 2023 г. № 158-П)
За принятие проголосовали:
Краткое наименование страны по МП (ИСО3166) 004—97 | Код страны по МК (ИСО 3166) 004—97 | Сокращенное наименование национального органа по стандартизации |
Армения | АМ | ЗАО «Национальный орган по стандартизации и метрологии» Республики Армения |
Беларусь | BY | Госстандарт Республики Беларусь |
Казахстан | KZ | Госстандарт Республики Казахстан |
Киргизия | KG | Кыргызстандарт |
Россия | RU | Госстандарт |
Узбекистан | UZ | Узстандарт |
4 Приказом Федерального агентства по техническому регулированию и метрологии от 15 февраля 2023 г. № 92-ст межгосударственный стандарт ГОСТ 34939—2023 введен в действие в качестве национального стандарта Российской Федерации с 1 августа 2024 г. с правом досрочного применения
5 Настоящий стандарт подготовлен на основе применения ГОСТ Р 55513—2013
6 ВВЕДЕН ВПЕРВЫЕ
Информация о введении в действие (прекращении действия) настоящего стандарта и изменений к нему на территории указанных выше государств публикуется в указателях национальных стандартов, издаваемых в этих государствах, а также в сети Интернет на сайтах соответствующих национальных органов по стандартизации.
В случаях пересмотра, изменения или отмены настоящего стандарта соответствующая информация будет опубликована на официальном интернет-сайте Межгосударственного совета по стандартизации, метрологии и сертификации в каталоге «Межгосударственные стандарты»
© Оформление. ФГБУ «Институт стандартизации», 2023
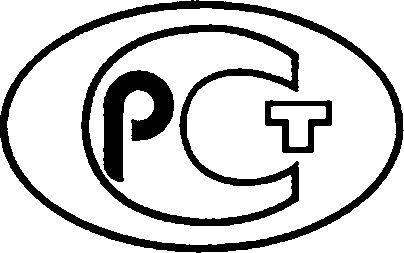
В Российской Федерации настоящий стандарт не может быть полностью или частично воспроизведен, тиражирован и распространен в качестве официального издания без разрешения Федерального агентства по техническому регулированию и метрологии
Содержание
1 Область применения
2 Нормативные ссылки
3 Термины и определения
4 Требования к динамическим качествам
5 Требования к прочности, жесткости и ресурсу
6 Расчет показателей динамики и прочности
7 Общие требования к испытаниям. Виды испытаний
8 Оценка прочности
9 Требования к прочности и динамическим качествам узлов экипажной части
10 Требования к применяемым материалам
Приложение А (обязательное) Условия нагружения путеочистителя при расчете на прочность
Приложение Б (обязательное) Экспериментальный метод определения корректирующего коэффициента для сварных конструкций из стального проката
Приложение В (рекомендуемое) Пример расчета долговечности
Приложение Г (рекомендуемое) Пример расчета ресурса буксового роликового радиального подшипника с короткими цилиндрическими роликами типа 30-32532Л1М тепловоза 2ТЭ116
Приложение Д (обязательное) Допускаемые показатели прочности резиновых деталей
Библиография
МЕЖГОСУДАРСТВЕННЫЙ СТАНДАРТ
ЛОКОМОТИВЫ
Требования к прочности и динамическим качествам
Locomotives. Requirements for bearing structure strength and dynamic properties
Дата введения — 2024—08—01 с правом досрочного применения
1 Область применения
Настоящий стандарт распространяется на локомотивы колеи 1520 мм, предназначенные для эксплуатации на железных дорогах со скоростями движения до 200 км/ч (включительно).
Настоящий стандарт устанавливает требования к прочности и жесткости узлов экипажной части локомотивов, динамическим качествам локомотивов, а также объем расчетов и виды испытаний по подтверждению показателей динамики и прочности.
2 Нормативные ссылки
В настоящем стандарте использованы нормативные ссылки на следующие межгосударственные стандарты:
ГОСТ 25.101 Расчеты и испытания на прочность. Методы схематизации случайных процессов нагружения элементов машин и конструкций и статистического представления результатов
ГОСТ 25.502 Расчеты и испытания на прочность в машиностроении. Методы механических испытаний металлов. Методы испытаний на усталость
ГОСТ 27.002 Надежность в технике. Термины и определения*
ГОСТ 380 Сталь углеродистая обыкновенного качества. Марки
ГОСТ 535 Прокат сортовой и фасонный из стали углеродистой обыкновенного качества. Общие технические условия
ГОСТ 977 Отливки стальные. Общие технические условия
ГОСТ 1050 Металлопродукция из нелегированных конструкционных качественных и специальных сталей. Общие технические условия
ГОСТ 1497 Металлы. Методы испытаний на растяжение
ГОСТ 2246 Проволока стальная сварочная. Технические условия
ГОСТ 4784 Алюминий и сплавы алюминиевые деформируемые. Марки
ГОСТ 5457 Ацетилен растворенный и газообразный технический. Технические условия
ГОСТ 5583 (ИСО 2046—73) Кислород газообразный технический и медицинский. Технические условия
ГОСТ 6331 Кислород жидкий технический и медицинский. Технические условия
ГОСТ 6713 Прокат из конструкционной стали для мостостроения. Технические условия
ГОСТ 6996 (ИСО 4136—89, ИСО 5173—81, ИСО 5177—81) Сварные соединения. Методы определения механических свойств
* В Российской Федерации действует ГОСТ Р 27.102—2021 «Надежность в технике. Надежность объекта. Термины и определения».
Издание официальное
ГОСТ 7871 Проволока сварочная из алюминия и алюминиевых сплавов. Технические условия
ГОСТ 8050 Двуокись углерода газообразная и жидкая. Технические условия
ГОСТ 8479 Поковки из конструкционной углеродистой и легированной стали. Общие технические условия
ГОСТ 9087 Флюсы сварочные плавленые. Технические условия
ГОСТ 9454 Металлы. Метод испытания на ударный изгиб при пониженных, комнатной и повышенной температурах
ГОСТ 9466 Электроды покрытые металлические для ручной дуговой сварки сталей и наплавки. Классификация и общие технические условия
ГОСТ 10157 Аргон газообразный и жидкий. Технические условия
ГОСТ 10885 Сталь листовая горячекатаная двухслойная коррозионно-стойкая. Технические условия
ГОСТ 11018 Колесные пары тягового подвижного состава железных дорог колеи 1520 мм. Общие технические условия.
ГОСТ 14637 (ИСО 4995—78) Прокат тол стол и сто вой из углеродистой стали обыкновенного качества. Технические условия
ГОСТ 16504 Система государственных испытаний продукции. Испытания и контроль качества продукции. Основные термины и определения
ГОСТ 18855 (ISO 281:2007) Подшипники качения. Динамическая грузоподъемность и номинальный ресурс
ГОСТ 19281 (ИСО 4950-2—81, ИСО 4950-3—81, ИСО 4951—79, ИСО 4995—78, ИСО 4996—78, ИСО 5952—83) Прокат из стали повышенной прочности. Общие технические условия
ГОСТ 21354 Передачи зубчатые цилиндрические эвольвентные внешнего зацепления. Расчет на прочность
ГОСТ 22703 Детали литые сцепных и автосцепных устройств железнодорожного подвижного состава. Общие технические условия
ГОСТ 23207 Сопротивление усталости. Основные термины, определения и обозначения
ГОСТ 23949 Электроды вольфрамовые сварочные неплавящиеся. Технические условия
ГОСТ 26271 Проволока порошковая для дуговой сварки углеродистых и низколегированных сталей. Общие технические условия
ГОСТ 31539 Цикл жизненный железнодорожного подвижного состава. Термины и определения
ГОСТ 34628 Пружины и комплекты пружинные рессорного подвешивания железнодорожного подвижного состава. Методы расчета на прочность при действии продольных и комбинированных нагрузок
Примечание — При пользовании настоящим стандартом целесообразно проверить действие ссылочных стандартов и классификаторов на официальном интернет-сайте Межгосударственного совета по стандартизации, метрологии и сертификации (www.easc.by) или по указателям национальных стандартов, издаваемым в государствах, указанных в предисловии, или на официальных сайтах соответствующих национальных органов по стандартизации. Если на документ дана недатированная ссылка, то следует использовать документ, действующий на текущий момент, с учетом всех внесенных в него изменений. Если заменен ссылочный документ, на который дана датированная ссылка, то следует использовать указанную версию этого документа. Если после принятия настоящего стандарта в ссылочный документ, на который дана датированная ссылка, внесено изменение, затрагивающее положение, на которое дана ссылка, то это положение применяется без учета данного изменения. Если ссылочный документ отменен без замены, то положение, в котором дана ссылка на него, применяется в части, не затрагивающей эту ссылку.
3 Термины и определения
В настоящем стандарте применены термины по ГОСТ 27.0021, ГОСТ 16504, ГОСТ 31539, а также следующие термины с соответствующими определениями:
3.1 локомотив: Железнодорожный подвижной состав, предназначенный для обеспечения передвижения по железнодорожным путям поездов или отдельных вагонов.
3.2
конструкционная скорость: Наибольшая скорость движения, заявленная в технической документации на проектирование.
[ГОСТ 34056—2017, статья 3.2.42]
3.3 несущие конструкции: Конструкции локомотива, воспринимающие эксплуатационные нагрузки.
3.4 несущий элемент: Часть конструкции или деталь, воспринимающие эксплуатационные нагрузки.
3.5 эксплуатационные нагрузки: Нагрузки, параметры которых измеряют в процессе эксплуатации или при испытании на специальных испытательных полигонах специализированными измерительными средствами и регистрируют автоматизированными приборами в аналоговом или цифровом виде.
Примечание — Эксплуатационные нагрузки характеризуются:
- характером изменения (случайное, детерминированное, одно- или многоступенчатое, статическое, квази-статическое, колебательное, ударное);
- частотой (изменения, повторения);
- видом нагружения (растяжение, сжатие, изгиб, кручение, сдвиг);
- характеристикой цикла (симметричный, асимметричный, знакопостоянный, знакопеременный);
- формой спектра (узкополосный, широкополосный);
- параметрами и условиями окружающей или рабочей среды (температура, давление, влажность, агрессивность).
3.6 экипажная часть локомотива: Конструкция, представляющая собой механическую повозку, обеспечивающую движение локомотива по рельсовой колее и предназначенную для установки силового и вспомогательного оборудования, приводов, тормозной системы.
3.7 базовая часть: Несущая составная часть конструкции, а также конструкции и детали, ответственные за безопасную эксплуатацию локомотива, которые определяют срок службы локомотива и замена которых до списания локомотива невозможна или нецелесообразна.
Примечание — Базовыми частями локомотива являются рама тележки, промежуточные рамы (балки, брусья и т. п.) второй ступени рессорного подвешивания, кузов (главная рама).
3.8 мягкое нагружение: Циклическое нагружение при постоянной амплитуде напряжений.
3.9 жесткое нагружение: Циклическое нагружение при постоянной амплитуде деформаций.
3.10 рамная сила: Поперечная горизонтальная сила взаимодействия колесной пары с рамой тележки или главной рамой (для бестележечных локомотивов) экипажной части.
3.11 максимальная статическая [осевая] нагрузка (на узел первой/второй ступени рессорного подвешивания): Статическая нагрузка, действующая от силы тяжести локомотива в полностью экипированном состоянии.
3.12 непогашенное ускорение: Часть поперечного горизонтального ускорения, действующего на локомотив на уровне оси буксы при движении в кривой, не компенсированная возвышением наружного рельса.
3.13 надрессорное строение: Совокупность всех подрессоренных конструкций экипажной части.
3.14 галопирование: Вращательное колебание надрессорного строения вокруг горизонтальной поперечной оси.
Примечание — Колебания этого рода, сопровождаемые попеременным опусканием и подниманием то переднего, то заднего концов тележки или надрессорного строения, вызываются двусторонними неровностями верхнего строения пути (например, при расположении стыков не вразбежку, а друг против друга), резкими переходами в продольном профиле (например, от уклона к площадке), а также торможениями, когда появляются опрокидывающие моменты, разгружающие одни оси и нагружающие другие.
3.15 подпрыгивание: Поступательное колебание надрессорного строения вдоль вертикальной оси.
3.16 боковая качка: Вращательное колебание надрессорного строения вокруг горизонтальной продольной оси.
3.17 виляние: Вращательное колебание надрессорного строения вокруг вертикальной оси.
3.18 относ: Перемещение надрессорного строения вдоль горизонтальной поперечной оси.
3.19 макротрещина: Трещина, видимая невооруженным глазом.
3.20 квазистатическое разрушение: Разрушение, связанное с возрастанием остаточных деформаций до уровня, соответствующего разрушению при однократном статическом нагружении.
Примечание — Нагрузки, приводящие к квазистатическому разрушению — несколько ниже нагрузок, определяющих статическую прочность.
3.21 малоцикловая усталость: Усталость материала, при которой усталостное повреждение или разрушение происходит при упруго-пластическом деформировании.
Примечание — К малоцикловой усталости условно относят область чисел циклов до разрушения от 104 до 105.
3.22 эквивалентная динамическая радиальная нагрузка: Постоянная радиальная нагрузка, которая при приложении ее к подшипнику с вращающимся внутренним и неподвижным наружным кольцом обеспечивает такой же расчетный срок службы, как и при действительных условиях нагружения и вращения.
4 Требования к динамическим качествам
4.1 Коэффициент горизонтальной динамики КдГОр должен быть не более 0,30.
4.2 Коэффициент вертикальной динамики первой ступени рессорного подвешивания Кд1 должен быть не более:
- 0,35 — для пассажирского и грузопассажирского локомотива с конструкционной скоростью 160 км/ч и менее;
- 0,30 — для пассажирского и грузопассажирского локомотива с конструкционной скоростью от 160 до 200 км/ч (включительно);
- 0,40 — для прочих локомотивов.
4.3 Коэффициент вертикальной динамики второй ступени рессорного подвешивания Кд2 должен быть, не более:
- 0,20 — для пассажирских и грузопассажирских локомотивов;
- 0,25 — для прочих локомотивов.
4.4 Коэффициент запаса устойчивости против схода колеса с рельса к должен быть не менее 1,40.
4.5 Показатели плавности хода2: в вертикальном направлении l/l/z и в горизонтальном поперечном направлении должны быть, не более:
- 3,50 для пассажирских и грузопассажирских локомотивов;
- 3,75 для прочих локомотивов.
4.6 Коэффициент конструктивного запаса пружинных комплектов Ккз ступеней рессорного подвешивания при отсутствии упругих упоров или при наличии жестких элементов, ограничивающих вертикальные перемещения подрессоренных масс, должен быть:
- первой ступени — не менее 1,6;
- второй ступени — не менее 1,4.
В случае наличия упругих упоров в схеме нагружения первой ступени рессорного подвешивания коэффициент Ккз1 должен быть:
- до включения в схему нагружения упругого упора Ккз1нач — не менее 1,4;
- после включения в схему нагружения упругого упора /<кз1уп — не менее 1,6.
4.7 Оценку динамических качеств по показателям, указанным в 4.6, выполняют проведением расчетов, приведенных в 6.2.6.
4.8 Необходимо обеспечить отсутствие взаимного касания элементов экипажной части, не предусмотренного конструкторской документацией.
4.9 При наличии в конструкции экипажной части ограничителей перемещений, предназначенных для функционирования в штатной эксплуатации, они должны иметь упругие упоры.
4.10 Конструкция экипажной части и узлов крепления оборудования локомотива должна обеспечивать отсутствие резонансных колебаний при движении локомотива и работе размещенных на кузове (главной раме) агрегатов.
При невозможности исключения резонансных колебаний следует применять конструктивные меры для снижения нагруженности несущих элементов экипажной части.
5 Требования к прочности, жесткости и ресурсу
5.1 Несущую способность элементов конструкции экипажной части оценивают при действии установленных настоящим стандартом расчетных нагрузок по допускаемым значениям:
- напряжений;
- деформаций;
- коэффициентов запаса сопротивления усталости;
- коэффициентов запаса устойчивости.
5.2 Напряжения в конструкциях при действии расчетных нагрузок в соответствии с 6.3 не должны превышать допустимых значений, приведенных в таблице 8.1.
5.3 Прочность кузова (главной рамы) при действии нормативной продольной силы, приложенной по осям сцепных устройств, следует подтвердить испытанием на соударение, а также расчетом или результатами стендовых статических испытаний с двухсторонним сжатием и растяжением. При этом условиями прочности кузова (главной рамы) являются:
- при испытании на соударение: о < о02;
- при статическом нагружении: о < 0,9 о02
где о0 2 — предел текучести применяемого при изготовлении материала;
о — напряжение, соответствующее нормативной продольной силе.
5.4 Коэффициенты запаса сопротивления усталости п конструкций экипажной части (за исключением колесных пар, валов тягового привода, зубчатых колес и пружин рессорного подвешивания) должны быть не менее:
- 2,0 — для конструкций из стали;
- 2,2 — для конструкций из алюминиевых сплавов.
Выполнение данного требования на стадии проектирования проверяют по результатам расчетов, а при наличии опытного образца подтверждают результатами испытаний (см. 8.3).
5.5 Сопротивление усталости рам тележек и промежуточных рам (балок, брусьев и т. п.) второй ступени рессорного подвешивания следует подтвердить отсутствием усталостных трещин после 10 млн циклов нагружения на вибрационном стенде при нагружении согласно требованиям 8.3.7.
5.6 Коэффициент запаса устойчивости для элементов кузова (главной рамы) пу должен быть не менее 1,10 при расчетных режимах I и IV по 6.3.
5.7 Жесткость конструкции элементов экипажной части и узлов крепления оборудования должна обеспечивать выполнение требований 4.10.
Максимальная расчетная величина прогиба нижнего пояса кузова (главной рамы), отнесенная к его полной длине, не должна превышать:
- от вертикальной нагрузки брутто: для несущего кузова — 0,4 мм/м, для несущей (главной) рамы — 0,6 мм/м;
- при одновременном действии вертикальной нагрузки брутто и расчетной продольной силы: для несущего кузова — 1,5 мм/м, для несущей рамы — 2,2 мм/м.
5.8 Расчетные показатели прочности пружин рессорного подвешивания должны соответствовать требованиям ГОСТ 34628.
5.9 Расчетный ресурс подшипниковых узлов, соответствующий 90 % надежности, L10a должен быть не менее:
- 3 • 106 км для подшипников буксовых узлов;
- 2 • 106 км для якорных подшипников тягового электродвигателя (далее — ТЭД) при посадке шестерни на хвостовике вала якоря;
- 3 • 106 км для якорных подшипников ТЭД при разделении ведущей шестерни и вала якоря;
- 2 • 106 км для подшипников шестерни тягового редуктора;
- 5 • 106 км для опорных подшипников тяговых редукторов, подшипников зубчатого колеса (при передаче с полым валом) и моторно-осевых подшипников качения.
Ресурс подшипников иных узлов — в соответствии с нормативными документами на конкретные типы подшипников.
5.10 Предел выносливости, коэффициент запаса сопротивления усталости и статической прочности оси и колеса в составе колесной пары должны соответствовать требованиям ГОСТ 11018.
6 Расчет показателей динамики и прочности
6.1 Общие требования
6.1.1 После выбора материалов при проектировании несущих конструкций экипажной части для заданных параметров нагружения расчетным путем выполняют:
- выбор размеров и конструктивных форм несущих элементов для заданных параметров нагружения;
- выбор характеристик рессорного подвешивания;
- оценку динамических качеств локомотива;
- анализ напряженно-деформированного состояния в наиболее нагруженных зонах для различных расчетных нагрузок;
- оценку прочности и сопротивления усталости;
- оценку ожидаемого ресурса.
6.1.2 Для оценки динамических качеств локомотива и выбора упруго-диссипативных характеристик рессорного подвешивания при проектировании используют программные комплексы, позволяющие путем компьютерного моделирования определить значения динамических показателей, указанных в разделе 4 — при движении в прямых и кривых участках пути с учетом возвышения наружного рельса и неровностей пути, а также с одновременным расчетом ускорений, скоростей и перемещений заданных элементов конструкции.
Проверку правильности выбора расчетной математической модели выполняют путем сравнения результатов компьютерного моделирования с результатами динамико-прочностных испытаний локомотива, имеющего аналогичную экипажную часть.
Расхождение результатов (по напряжениям и спектру частот) не должно превышать 20%.
6.1.3 Расчетам на прочность подлежат: кузов (главная рама), рамы тележек, промежуточные рамы (балки, брусья и т. п.) второй ступени рессорного подвешивания, элементы связи кузова (главной рамы) с тележками (шкворень, тяги и др.), пружины рессорного подвешивания, корпуса букс, узлы крепления оборудования. Их следует рассчитать на действие нагрузок, приведенных в 6.3.
6.2 Расчет показателей динамики
6.2.1 Коэффициент горизонтальной динамикиКоэффициент горизонтальной динамики Кдгор определяют как отношение значения динамической составляющей рамной силы У^ин, действующей от колесной пары на раму тележки или главную раму (для бестележечных локомотивов), полученного по приведенному в данном пункте алгоритму, к максимальной вертикальной статической осевой нагрузке Рслос на колесную пару.
Значение динамической составляющей рамной силы УДИН в кривых участках пути определяют путем исключения (фильтрации) квазистатической составляющей динамического процесса рамных сил У При этом частота, отделяющая квазистатическую составляющую от динамической, должна быть не выше 80 % от низшей собственной частоты колебаний локомотива на рессорном подвешивании в горизонтально-поперечном направлении.
Значение УДИН вычисляют как среднее арифметическое из трех максимальных амплитуд У^ин, за исключением полученных при движении по стрелочным переводам.
Максимальные амплитуды динамических составляющих рамных сил УДИН определяют как половинное значение размахов, получаемых при обработке динамических процессов методами «дождя» или полных циклов по ГОСТ 25.101.
При проектировании при определении значения Рстос принимают расчетные нагрузки, при испытаниях— фактические нагрузки, полученные при поколесном взвешивании.
При проектировании расчет и оценку коэффициента горизонтальной динамики Кдгор осуществляют для всех колесных пар.
6.2.2 Коэффициент вертикальной динамики первой ступени рессорного подвешивания
Коэффициент вертикальной динамики первой ступени рессорного подвешивания Кд1 определяют как отношение значения динамической составляющей вертикальной силы в первой ступени рессорного подвешивания Р^н к статической нагрузке в первой ступени рессорного подвешивания Рст1 .
Значение динамической составляющей вертикальной силы определяют в порядке, аналогичном изложенному в 6.2.1, для определения динамической составляющей рамной силы.
Показатель Кд1 определяют для узлов первой ступени рессорного подвешивания. При этом используют значения статических нагрузок (сил), приходящихся на каждый конкретный узел первой ступени рессорного подвешивания.
Статическую нагрузку в первой ступени рессорного подвешивания определяют по данным, приведенным в конструкторской документации, или экспериментальным путем.
6.2.3 Коэффициент вертикальной динамики второй ступени рессорного подвешивания
Коэффициент вертикальной динамики второй ступени рессорного подвешивания Кд2 определяют как отношение значения динамической составляющей вертикальной силы во второй ступени рессорно-го подвешивания Р?2 к статической нагрузке во второй ступени рессорного подвешивания Рст2.
Значение динамической составляющей вертикальной силы определяют в порядке, аналогичном изложенному в 6.2.1, для определения динамической составляющей рамной силы.
Показатель Кд2 определяют для узлов второй ступени рессорного подвешивания. При этом используют значения статических нагрузок (сил), приходящихся на каждый конкретный узел второй ступени рессорного подвешивания.
Статическую нагрузку во второй ступени рессорного подвешивания определяют по данным, приведенным в конструкторской документации, или экспериментальным путем.
6.2.4 Коэффициент запаса устойчивости против схода колеса с рельса
Коэффициент запаса устойчивости против схода колеса с рельса X вычисляют по формулам:
Yp/ + C2|iHH(l + 0,5|iHsin2[3) + C1pHcos2 р ctgp + |iH’
С1 = 2Q (b - а2) - Р£-|_|-|к (/+ a-|) + Рzi-hhk а2 + г + ^нп Ф ~ а2^’ (6-2)
С2 - 2Q (b — а^) — PZ1.HHK (/ + а2) + Р/т-цк ai — г + ^нп № ~ ai)’ ($•$)
где С1 и С2 — промежуточные величины, введенные для упрощения записи основной формулы;
рн — коэффициент трения между гребнем набегающего колеса и рельсом;
цНН — коэффициент трения между поверхностью катания ненабегающего колеса и рельсом;
Р — угол наклона образующей гребня колеса к горизонтальной плоскости, градусы (рисунок 6.1);
Ур — рамная сила, действующая на колесную пару, кН;
Q — сила тяжести подрессоренной части локомотива, приходящаяся на шейку оси колесной пары, кН;
дНп — сила тяжести неподрессоренных частей, приходящаяся на колесную пару, кН, вычисляют по формуле 9.9 (см. 9.3.1.4);
PZ1_HK и ^zi-hhk — вертикальные динамические силы в первой ступени рессорного подвешивания (с учетом квазистатических составляющих) соответственно на набегающем и ненабегающем колесах колесной пары, кН (при обезгрузке PZ1_HK > 0 и ^zi-hhk > b — половина расстояния между точками приложения вертикальных нагрузок к шейкам оси колесной пары, м;
а1 — поперечное расстояние между точкой приложения вертикальной нагрузки на шейку оси на набегающем колесе и точкой контакта на его гребне, м;
а2 — поперечное расстояние между точкой приложения вертикальной нагрузки на шейку оси на ненабегающем колесе и точкой контакта на его гребне, м;
г — радиус колеса по кругу катания, м;
/ — расстояние между точками контакта с рельсами набегающего и ненабегающего колес, м.
Набегающее на рельс колесо колесной пары при расчетах коэффициентов запаса устойчивости определяют по направлению действия рамной силы на колесную пару в соответствии с рисунком 6.1.
Расстояние / вычисляют по формуле
/= 2Ь-(а1 + а2). (6.4)
При обработке данных принимают цн = цнн = 0,25.
Набегающее на рельс колесо определяют по направлению действия рамной силы, т. е. рамная сила направлена от ненабегающего колеса к набегающему.
При вычислении показателя X используют мгновенные значения динамических процессов Ур , PZ1_HK и PZ1.HHK в один момент времени.
При проектировании данный показатель рассчитывают для всех колесных пар локомотива. При проведении динамико-прочностных испытаний этот показатель рассчитывают для крайних колесных пар локомотива.
Оценку соответствия локомотива требованию 4.4 выполняют по наименьшему из всех вычисленных значений данного показателя.
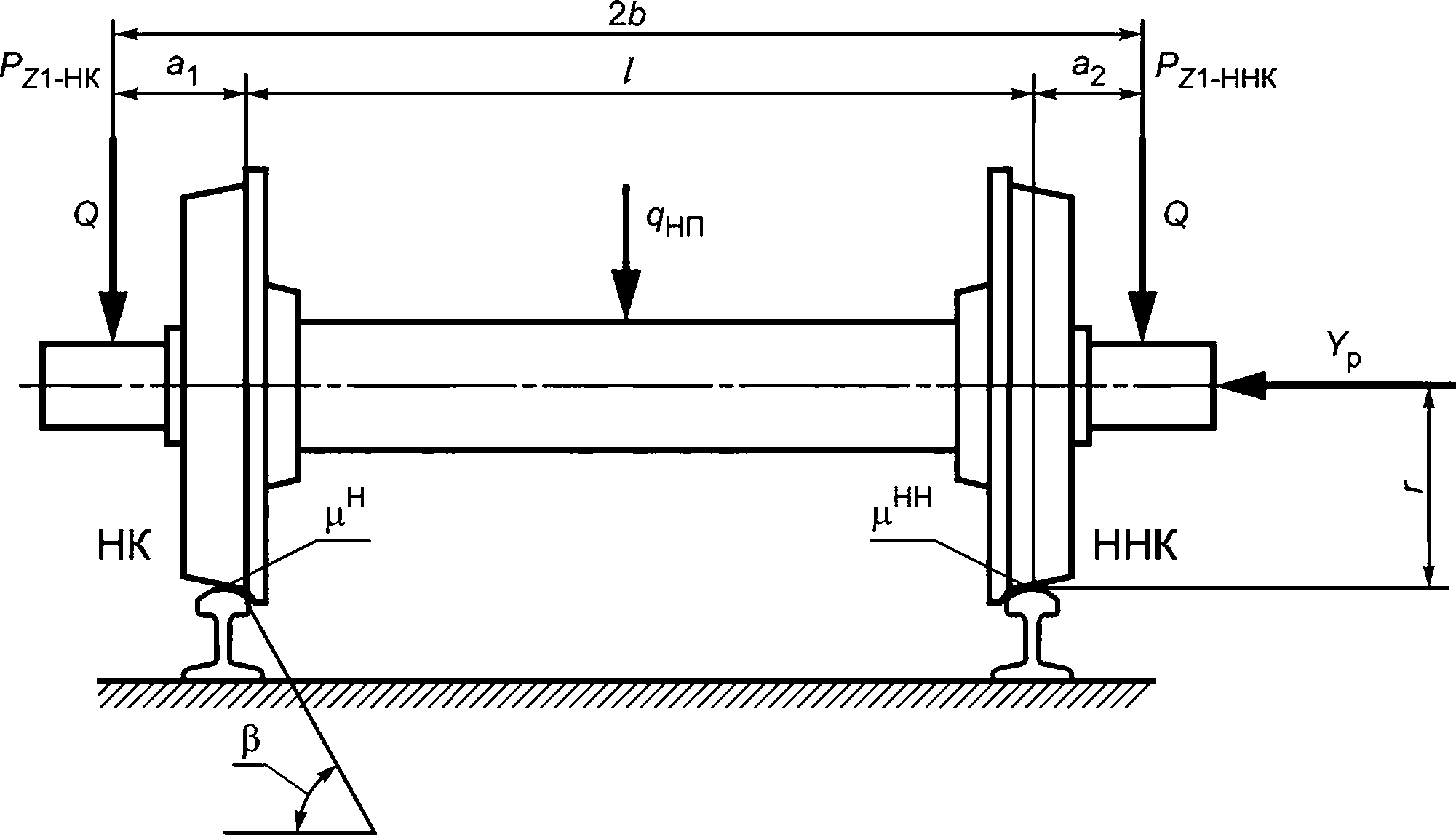
НК — набегающее колесо; ННК — ненабегающее колесо
Рисунок 6.1— Схема сил, действующих на колесную пару
6.2.5 Показатели плавности хода
Для оценки показателей плавности хода Wz и И/у используют временные зависимости ускорений контрольной точки кабины машиниста, получаемые либо при проведении моделирования динамики движения экипажной части, либо путем их непосредственной регистрации при проведении испытаний. Контрольная точка ускорений для определения показателей l/l/z и И/у располагается на полу кабины машиниста позади опорной стойки кресла машиниста, смотря по направлению движения, на минимально возможном расстоянии от оси стойки кресла машиниста.
Для расчета показателей плавности хода используют динамические составляющие виброускорений, полученные при движении локомотива по прямым участкам пути и по кривым участкам с радиусом не менее 600 м (не менее 1000 м для скоростного движения). Суммарная длительность измерений в каждом диапазоне скоростей должна быть не менее 200 с.
Для обеспечения требований к плавности хода и предотвращения резонансных явлений первая собственная частота изгибных колебаний кузова локомотива в вертикальной плоскости должна быть не ниже 8 Гц и превышать собственные частоты колебаний подпрыгивания и галопирования тележек не менее чем на 40%.
Показатели плавности хода (Wz)k, (WY)k для каждого к-го диапазона скоростей движения для вибрации, действующей соответственно в вертикальном и в горизонтальном поперечном направлениях, вычисляют по формулам:
(Wz)k=4,346 (az)°'3,
(Wy)fc = 4,676 (ay)°'3,
где (az)k, (aY)k — вертикальное и горизонтальное поперечное средние квадратические корректированные виброускорения в к-м диапазоне скорости движения, м/с2.
Виброускорения (az)^ и > м/с2> вычисляют по формулам:
(^к = J2j q2„(f)(Sz)k
(®Y)k = J2J qZ(f)(SY)k(f)df,
где fH — значение нижней граничной частоты диапазона измерения плавности хода,
Гн = 0,5 Гц;
fB — значение верхней граничной частоты диапазона измерения плавности хода, принимают равной частоте вращения колеса при конструкционной скорости движения, но не менее 20 Гц;
qH(f) — значения нормированной амплитудно-частотной характеристики корректирующего фильтра;
(Sz)k(f), (Sy)^(0 — функции спектральной плотности вертикального и горизонтального поперечного виброускорений в к-м диапазоне скорости движения, м2/(с4Тц).
Значения qH(f) вычисляют по формуле
(l + 4,04f2)((l-0,0364/:2)2
+ 0,045f2
(6.9)
где f — частота колебаний, Гц.
Допускается разбивать время измерения Тк виброускорений при движении сданной скоростью на отрезки продолжительностью Ту, каждому из которых соответствуют свои средние квадратические значения корректированных виброускорений (az)^n (aY)y, определенных на неперекрывающихся участках пути. В этом случае средние квадратические значения корректированных виброускорений для к-го диапазона скорости движения (az)k и (ау)к, м/с2, вычисляют по формулам:
(6.10)
(6.11)
где Ту — продолжительность /-го отрезка времени к-го диапазона скорости движения, с;
Тк — суммарное время движения со скоростями, входящими в к-й диапазон скоростей движения, с.
При проведении динамико-прочностных испытаний показатели плавности хода контролируют для скоростей движения от половины конструкционной скорости до конструкционной скорости с шагом от 10 до 20 км/ч.
6.2.6 Коэффициенты конструктивного запаса пружинных комплектов рессорного подвешивания
6.2.6.1 Коэффициент конструктивного запаса пружинных комплектов Ккз для первой и второй ступеней рессорного подвешивания в случае одновременного начала сжатия пружин, составляющих пружинный комплект, и при отсутствии в конструкции рессорного подвешивания ограничения сжатия вычисляют по формуле
Хкз=^-. (6.12)
^СТ
где Ртах — максимальная сила, соответствующая допускаемому конструкцией пружинного комплекта сжатию, при которой существует запас пружин на 3 мм до замыкания витков любой из них, кН; Рсг — максимальная статическая нагрузка на пружинный комплект для первой и второй ступени рессорного подвешивания, кН.
При наличии в конструкции ступеней рессорного подвешивания жестких элементов ограничения сжатия коэффициент ККЗ вычисляют по формуле
р и г тах огр Ккз - Ъ ^ст
(6.13)
где Г’тахогр — сила, под действием которой наступает ограничение деформации сжатия пружинного комплекта в ступени рессорного комплекта, кН; при этом выполняется условие: Р < Р ' max огр ' max’
6.2.6.2 В случае наличия упругого упора в схеме нагружения первой ступени рессорного подвешивания в качестве упругого ограничителя вертикальных перемещений букс колесных пар относительно рамы тележки или главной рамы (для бестележечных локомотивов) вычисляют начальный коэффициент запаса пружинного комплекта Ккз1нач до включения упругого упора совместно с пружинным комплектом по формуле
Р
Ккз1нач=-^> (6-14)
140 I Г1С1п ’ \ /
'ст
где Рнач — сила, соответствующая нагрузке на пружинный комплект в момент включения упругого упора в схеме нагружения.
При работе упругого упора совместно с пружинным комплектом в схеме нагружения первой ступени рессорного подвешивания коэффициент Ккз1уп вычисляют по формуле
Рнач+(Суп+СПк)5уп
кз 1 уп ------------Б----------------> (6 • 1 о)
*ст1
где Спк — жесткость пружинного комплекта под действием силы Рнач;
Суп — жесткость упругих упоров, определяемая по формуле
р г' _ уп Суп ~ ’ (6.16)
°уп
где Syn— деформация упругого упора совместно с пружинным комплектом.
Расчет максимальных сил Ртах выполняют по лимитирующей пружине комплекта в соответствующей ступени рессорного подвешивания с учетом конструктивных особенностей установки пружин при неодновременном включении в работу пружин и других упругих элементов, работающих параллельно с пружинным комплектом.
При расчете Ртах используют значения геометрических размеров пружин по их рабочим чертежам. Расчеты Ккз1 и Ккз2 должны содержать соответствующие конструктивные схемы ступеней рессорного подвешивания в исходном состоянии без нагрузки, позволяющие проследить порядок включения в работу всех учитываемых жесткостей упругих элементов при нагружении пружинных комплектов.
6.3 Расчетные режимы для оценки прочности
6.3.1 Для оценки прочности по допускаемым напряжениям по отношению к пределу текучести материала используют расчетные режимы I—IV.
Для оценки сопротивления усталости используют расчетный режим III.
Режим I включает:
- режим la для учета максимальных продольных квазистатических сил;
- режим I6 для учета максимальных продольных сил удара в сцепное устройство (соударения).
Режим II включает:
- режим На для учета сил, действующих при движении в кривых участках пути с максимальным разрешенным непогашенным ускорением;
- режим 116 для учета сил, действующих при трогании;
- режим 11в для учета сил, действующих при экстренном торможении.
Примечание — Максимальное разрешенное непогашенное ускорение задают в технических требованиях на локомотив применительно к особенностям полигона эксплуатации и конструктивному исполнению экипажной части (например, принудительному наклону кузова (главной рамы).
Режим III учитывает силы, действующие при движении с различными скоростями, вплоть до конструкционной, по прямому участку пути.
Режим IV предназначен для учета сил, обусловленных технологией ремонта и производством аварийно-восстановительных работ и возникающих:
- при подъеме кузова (главной рамы) на двух диагонально расположенных домкратах;
- при подъеме локомотива за узел автосцепного устройства;
- при выкатке колесной пары.
6.3.2 При расчетах на прочность экипажной части локомотива учитывают:
- собственную силу тяжести (вес) экипажной части и силу тяжести (вес) размещенного на нем оборудования;
- инерционные, упругие и диссипативные силы, вызванные колебаниями локомотива при его движении;
- силы, возникающие при работе тяговых двигателей и других механизмов, установленных на локомотиве;
- силы, связанные с тягой локомотива и торможением поезда;
- силы, возникающие при движении локомотива в кривых участках пути;
- силы соударения;
- силы, возникающие при ремонтно-восстановительных работах.
Перечисленные статические и динамические силы принимают действующими статически и подразделяют по схемам их приложения на вертикальные, продольные, горизонтальные поперечные и кососимметричные.
6.3.3 К расчетным вертикальным силам относят:
- собственную силу тяжести экипажной части локомотива;
- силы тяжести размещенного на нем оборудования;
- вертикальные динамические силы, возникающие при движении локомотива;
- дополнительные вертикальные силы, возникающие на опорах кузова (главной рамы) на тележки или на колесные пары (для бестележечных локомотивов) при действии продольных и горизонтальных поперечных нагрузок в рассматриваемом режиме.
6.3.3.1 Под силой тяжести экипажной части локомотива понимают суммарную силу собственной тяжести элементов и оборудования полностью экипированного локомотива.
Действие этой силы рассматривают:
- при опирании кузова (главной рамы) на тележки или на колесные пары (для бестележечных локомотивов);
- при подъеме кузова (главной рамы) двумя домкратами, установленными по диагонали локомотива на поддомкратные опоры;
- при аварийном подъеме локомотива с тележкой или с колесной парой (для бестележечных локомотивов) за лобовый брус или узел автосцепного устройства.
При аварийном подъеме за узел автосцепного устройства учитывают сумму силы тяжести полностью оборудованного и экипированного кузова (главной рамы) и силы тяжести поднимаемой тележки или колесной пары (для бестележечных локомотивов), имеющей связь с кузовом (главной рамой).
При выкатке колесной пары из-под тележки или из-под главной рамы (для бестележечных локомотивов) должны быть рассмотрены два случая:
- выкатка средней колесной пары трехосной тележки или трехосного локомотива (для бестележечных локомотивов);
- выкатка крайней колесной пары трехосной или двухосной тележки, либо трехосного/двухосного локомотива (для бестележечных локомотивов).
6.3.3.2 Динамическую вертикальную силу от колебаний тележки или главной рамы (для бестележечных локомотивов) на первой ступени рессорного подвешивания определяют умножением силы тяжести ее подрессоренной массы и силы тяжести полностью оборудованного и экипированного кузова (главной рамы), приходящейся на тележку или на колесную пару (для бестележечных локомотивов), на максимальное значение показателя К^.
Динамическую вертикальную силу для кузова (главной рамы) и промежуточных рам (балок, брусьев и т. п.) второй ступени рессорного подвешивания вычисляют умножением силы тяжести полностью оборудованного и экипированного кузова (главной рамы) (для промежуточных рам, балок, брусьев — с учетом их силы тяжести) на максимальное значение показателя Кд2.
В качестве максимальных значений показателей Кд1 и Кд2 принимают увеличенные на 20 % значения этих показателей, полученные в результате математического моделирования движения локомотива, но не выше максимально допустимых значений этих показателей по 4.2 и 4.3.
Допускается принимать значения показателей Кд1 и /<д2 по экспериментальным данным, полученным для конструкций с аналогичной экипажной частью.
6.3.3.3 Дополнительную вертикальную силу, прикладываемую к опорам кузова (главной рамы) в результате действия продольной силы инерции полностью оборудованного и экипированного кузова (главной рамы), АР, кН, вычисляют по формуле
^ = ^ик^> (6-17)
где Рик — сила инерции кузова (главной рамы), кН;
hK — расстояние от центра тяжести кузова (главной рамы) до плоскости опор на тележку, м;
2L — база кузова (главной рамы), м.
Примечание — Дополнительные вертикальные силы нагружают одну тележку или колесную пару (для бестележечных локомотивов) и разгружают другую.
6.3.3.4 Дополнительные силы на опоры кузова (главной рамы), опоры тягового двигателя, опоры тягового редуктора, узлы передачи силы тяги при трогании с места рассчитывают исходя из условий равновесия экипажной части при реализации максимальной силы тяги, определяемой по 6.3.4.2.
6.3.3.5 Дополнительную вертикальную силу, действующую на опоры кузова (главной рамы) при торможении, вызванную моментом пары сил, одна из которых — продольная сила инерции локомотива, другая — суммарная касательная сила торможения на ободе колес, необходимо рассчитывать исходя из условий равновесия экипажной части.
6.3.4 Продольные силы представляют собой силы взаимодействия между локомотивом и вагонами при их движении в поезде и выполнении маневров, силы тяги и торможения и возникающие при тяге и торможении продольные силы инерции. Продольные силы прикладывают к сцепным устройствам, элементам связи колесных пар с тележками или главной рамой (для бестележечных локомотивов) и тележек с кузовом (главной рамой).
6.3.4.1 Значения продольных сил FN, прикладываемых к сцепным устройствам локомотивов массой секции более 100 т, устанавливают в соответствии с таблицей 6.1. При этом выбирают либо минимальные, либо, в случае предъявления специальных требований заказчика, максимальные значения продольных сил.
Таблица 6.1 — Значения расчетных продольных сил для локомотивов массой секции более 100 т
Тип локомотива | Для расчетного режима, кН | |||
la* | 1б*‘ | |||
Минимальные | Максимальные | Минимальные | Максимальные | |
Пассажирский | ±2000 | ±2500 | -2000 | -2500 |
Все, кроме пассажирского | ±2500 | ±3000 | -2500 | -3000 |
|
Для локомотивов массой секции до 50 т (включительно) величину продольной силы принимают равной удвоенной силе тяжести локомотива, свыше 50 т и до 100 т (включительно) — как для пассажирских локомотивов массой секции более 100 т.
6.3.4.2 Продольные силы тяги и торможения определяют, рассматривая равновесие экипажной части в целом и отдельных ее узлов.
Максимальную силу тяги, приходящуюся на одну колесную пару в режиме трогания с места, определяют из условия полной реализации сцепления колес с рельсами. Коэффициент сцепления принимают равным 0,35. Допускается принимать иное значение в соответствии с техническим заданием на локомотив, но не менее 0,3.
6.3.4.3 Силы, действующие на раму тележки или главную раму (для бестележечных локомотивов) со стороны тормозной системы, определяют силой нажатия на тормозные колодки (при колодочном тормозе) или диск (при дисковом тормозе) и их коэффициентом трения.
Значения, направления и точки приложения этих сил определяют исходя из конструкции тормозной системы.
6.3.4.4 Продольные силы инерции, действующие на отдельные узлы и элементы локомотива, считают приложенными к центрам их масс.
Продольные силы инерции, действующие на кузов (главную раму) при соударениях локомотива с единицами подвижного состава, вычисляют через продольное ускорение ах полностью оборудованного и экипированного кузова (главной рамы). При этом принимают, что тележка или колесные пары (для бестележечных локомотивов) имеет/имеют продольное ускорение 3g. Ускорение кузова (главной рамы) ах, м/с2, вычисляют с учетом силы, приложенной к упорам автосцепных устройств, и сил инерции присоединенных масс тележек или колесных пар (для бестележечных локомотивов) по формуле
(6.18)
где Fn — продольная сила, приложенная к упорам сцепных устройств (по п. 6.3.4.1), кН;
/тел — число тележек или колесных пар (для бестележечных локомотивов) под секцией локомотива; тт — масса тележки или колесной пары (для бестележечных локомотивов), т;
тс — общая масса секции локомотива, т.
Величина ускорения ах не должна превышать значения 3g. Для выполнения этого условия допускается соответствующее снижение величины силы FN.
При расчете продольной силы инерции тележки или колесных пар (для бестележечных локомотивов) при торможении следует учитывать инерцию вращающихся частей. Для этого массу тележки или колесной пары (для бестележечных локомотивов) увеличивают на добавочную величину Ател, т, вычисляемую по формуле
_ лкп • Лп + ПТЭД • Аэд ’ 'ред л Q.
^тел 2 ’ (6.19)
(б,5• DKp min)
где лкп — количество колесных пар в тележке;
JKr) — момент инерции колесной пары относительно поперечной оси, т-м2;
лТЭд — количество ТЭД в тележке (для локомотивов с электрической передачей);
7ТЭд — момент инерции ТЭД относительно поперечной оси (для локомотивов с электрической передачей), т м2;
/ред — передаточное отношение редуктора;
Окр min — минимально допустимый в эксплуатации диаметр колеса по кругу катания, м.
Примечание — Для локомотивов с гидравлической передачей мощности лТЭд-Лтэд /ред = 0.
6.3.4.5 Продольную динамическую силу при движении локомотива с конструкционной скоростью в прямом участке пути рассчитывают исходя из ускорения приведенной массы тележки (колесной пары для бестележечных локомотивов) вдоль оси пути. Допускается при отсутствии достоверных данных это ускорение принимать равным 0,4g.
6.3.5 Горизонтальные поперечные силы определяются динамической составляющей рамной силы и силами, соответствующими непогашенному ускорению 0,7 м/с2, действующими по направлению оси колесной пары и поперечных осей, проходящих через центры масс тележки (центры масс колесных пар с буксовыми узлами — для бестележечных локомотивов) и кузова (главной рамы).
6.3.5.1 Центробежную силу определяют отдельно для массы кузова (главной рамы) и масс тележек (масс колесных пар с буксовыми узлами — для бестележечных локомотивов) при максимальном допускаемом непогашенном горизонтальном поперечном ускорении, равном 0,7 м/с2.
Допускается применение иного значения допускаемого непогашенного горизонтального поперечного ускорения, установленного в конструкторской документации.
6.3.5.2 Рамные силы, действующие от колесной пары на раму тележки или главную раму (для бестележечных локомотивов), определяют умножением максимальной вертикальной статической осевой нагрузки Рсуос на максимальное значение показателя Кдгор.
В качестве максимального значения показателя Кдгор принимают увеличенное на 20 % значение этого показателя, полученное в результате математического моделирования движения локомотива, но не выше максимально допустимого значения этого показателя по 4.1.
Допускается принимать значения рамных сил по экспериментальным данным, полученным для конструкций с аналогичной экипажной частью.
6.3.6 Вертикальные кососимметричные силы, представляющие собой систему взаимно уравновешенных сил, приложенных со стороны рессорного подвешивания к раме тележки, учитывают только при расчетах тележек, имеющих конструкцию, способную воспринимать эти силы (с замкнутым контуром, Н-образную и т. п.). Они состоят из четырех равных по абсолютной величине вертикальных сил, из которых две, расположенные по диагонали, действуют вверх, а две другие — вниз. Они могут возникать в двух- или трехосных тележках и действуют со стороны букс на раму тележки. В случае трехосных тележек принимают, что нагрузка на пружинный комплект средней колесной пары остается неизменной.
Значения кососимметричных сил принимают равными 10 % от вертикальной нагрузки на буксовый узел.
6.3.7 Для локомотивов с электрической передачей вертикальные инерционные силы со стороны масс ТЭД, возникающие при колебаниях рамы тележки с учетом дисбаланса вращающихся частей двигателя, принимают исходя из ускорений:
- при опорно-осевом подвешивании ТЭД в месте крепления на раме тележки — не менее 2g;
- при опорно-рамном подвешивании ТЭД на раме тележки — не менее 1g по центру массы ТЭД.
Также вертикальные инерционные силы со стороны масс ТЭД, возникающие при колебаниях рамы тележки с учетом дисбаланса вращающихся частей двигателя, могут быть определены экспериментальным путем или по результатам специального расчета тележки с учетом упругости рамы.
Для локомотивов с гидравлической передачей инерционные силы от вращающихся масс не учитываются.
6.3.8 При проведении расчетов следует учитывать силы, возникающие при работе механизмов, установленных на локомотиве. Для расчетного режима III напряжения от действия этих сил суммируют с напряжениями от действия динамических нагрузок.
6.3.9 При расчетах конструкций, подвергаемых деформациям при сборке (монтаже), учитывают возникающие при этом усилия (например, усилия от запрессовки, горячей посадки и т. п.).
6.3.10 Сочетания сил, действующих на экипажную часть в соответствии с расчетными режимами, представлены в таблицах 6.2 и 6.3.
Таблица 6.2 — Сочетания сил при расчетных режимах нагружения кузова (главной рамы)
Расчетные силы | Сочетание сил для расчетного режима | ||||
la | I6 | На | III | IV | |
Силы тяжести | по 6.3.3.1, схема опирания 1 | по 6.3.3.1, схемы опирания 2, 3 | |||
Вертикальные динамические силы при движении | — | — | по 6.3.3.2 | по 6.3.3.2 | — |
Продольные силы на упорах сцепных устройств | по 6.3.4.1 | по 6.3.4.1 | — | — | — |
Продольные силы инерции | — | по 6.3.4.4 | — | — | — |
Центробежная сила | — | — | по 6.3.5.1 | — | — |
Таблица 6.3 — Сочетания сил при расчетных режимах нагружения тележки
Расчетные силы | Сочетания сил для расчетного режима | |||||
I6 | Па | Пб | Ив | III | IV | |
Силы тяжести | по 6.3.3.1, схема опирания 1 | |||||
Вертикальные динамические силы при движении | — | по 6.3.3.2 | — | — | по 6.3.3.2 | — |
Дополнительные вертикальные силы на опорах кузова (главной рамы) от действия продольной силы инерции кузова (главной рамы) | по 6.3.3.3 | — | — | — | — | — |
Дополнительные вертикальные силы на опорах кузова (главной рамы) при трогании с места | — | — | по 6.3.3.4 | — | — | — |
Дополнительные силы на опорах ТЭД и тягового редуктора при трогании с места (для локомотивов с электрической передачей) | — | — | 6.3.3.4 | — | — | — |
Вертикальные инерционные силы со стороны масс ТЭД (для локомотивов с электрической передачей) | — | по 6.3.7 | — | — | по 6.3.7 | — |
Дополнительные вертикальные силы на опорах кузова (главной рамы) при торможении | — | — | — | по 6.3.3.5 | — | — |
Силы тяги | — | — | по 6.3.4.2 | — | — | — |
Силы, действующие со стороны тормозной системы | — | — | — | по 6.3.4.3 | — | — |
Продольные силы инерции | по 6.3.4.4 | — | — | по 6.3.4.4 | по 6.3.4.5 | — |
Окончание таблицы 6.3
Расчетные силы | Сочетания сил для расчетного режима | |||||
I6 | На | Нб | Ив | Ill | IV | |
Центробежная сила | — | по 6.3.5.1 | — | — | — | — |
Рамные силы | — | по 6.3.5.2 | — | — | по 6.3.5.2 | — |
Кососимметричные силы со стороны букс | — | по 6.3.6 | — | — | — | — |
6.3.11 Дополнительно к расчетным режимам I—IV узлы связи кузова (главной рамы) с тележкой или колесной парой (для бестележечных локомотивов), передающие силу тяги, рассчитывают при действии инерционных сил, вызванных продольными ускорениями тележки или колесной пары (для бестележечных локомотивов) ± 3g. При этом напряжения в элементах узлов связи кузова (главной рамы) с тележкой или колесной парой (для бестележечных локомотивов) не должны превышать значения О,9о02.
6.3.12 Дополнительно к расчетным режимам I—IV элементы крепления съемного оборудования, расположенного на кузове (главной раме), рассчитывают для каждого из следующих случаев нагружения:
- действие вертикальной нагрузки, вызванной вертикальными ускорениями (1 ± с) д, где с = 2 в конце секции локомотива и линейно убывает до значения 0,5 в середине секции локомотива;
- совместное действие силы тяжести оборудования и инерционных сил, вызванных продольными ускорениями ± 3g;
- совместное действие силы тяжести оборудования и инерционных сил, вызванных горизонтальными поперечными ускорениями ± д.
Узлы крепления к кузову емкости для природного газа или другого альтернативного топлива рассчитывают исходя из продольного ускорения 6g.
Для каждого из этих случаев напряжения в элементах крепления оборудования не должны превышать О,9сто 2.
6.3.13 Прочность узлов крепления демпферов рессорного подвешивания оценивают для расчетного режима III по условию о < О,6о02 и по допускаемым коэффициентам запаса сопротивления усталости по 8.3.
Динамические силы, действующие со стороны демпферов, определяют по результатам математического моделирования движения экипажной части.
6.3.14 Оборудование, жестко закрепленное на обрессоренной раме тележки, за исключением тягового двигателя, расчитывают с учетом сил инерции исходя из ускорений в вертикальном направлении, равных 2g в средней части (между колесными парами) и 3g на консолях рам тележек. Ускорение всех частей рам тележек в поперечном направлении принимают равным 1,5g, а в продольном направлении — 3g. Элементы оборудования (противобоксовочные датчики, скоростемер, заземлитель и др.), жестко закрепленные на неподрессоренных частях тележки или колесной пары (для бестележечных локомотивов), рассчитываются с учетом сил инерции исходя из ускорения массы деталей в вертикальном направлении 5g.
7 Общие требования к испытаниям. Виды испытаний
Испытаниям по определению показателей динамических качеств подвергают локомотив в целом.
Испытаниям по определению показателей прочности подвергают как локомотив в целом, так и секции локомотива, а также отдельные узлы его экипажной части.
Виды испытаний для оценки показателей динамических качеств и прочности конструкций приведены в таблице 7.1.
Таблица 7.1
Наименование показателя | Условное обозначение показателя | Виды испытаний | |
Стендовые | Динамикопрочностные | ||
Коэффициент горизонтальной динамики | Кдгор | — | + |
Коэффициент вертикальной динамики первой ступени рессорного подвешивания | КД1 | — | + |
Окончание таблицы 7.1
Наименование показателя | Условное обозначение показателя | Виды испытаний | |
Стендовые | Динамикопрочностные | ||
Коэффициент вертикальной динамики второй ступени рессорного подвешивания | КД2 | — | + |
Коэффициент запаса устойчивости против схода колеса с рельса | X | — | + |
Показатели плавности хода в вертикальном и горизонтальном поперечном направлениях | — | + | |
Отсутствие взаимного касания элементов экипажной части, не предусмотренного конструкторской документацией | — | — | + |
Коэффициенты запаса сопротивления усталости конструкций экипажной части, за исключением колесных пар, валов тягового привода, зубчатых колес и пружин рессорного подвешивания | п | — | + |
Сопротивление усталости рам тележек и промежуточных рам (балок, брусьев и т. п.) второй ступени рессорного подвешивания | — | +* | — |
Прочность кузова (главной рамы) при действии нормативной силы соударения, приложенной по оси сцепного устройства | — | — | + |
* Проводят вибрационные испытания в соответствии с 8.3.7. |
8 Оценка прочности
8.1 Общие положения
8.1.1 Оценку прочности проводят:
- при проектировании;
- при испытаниях опытного образца;
- при введении конструктивных или технологических изменений, влияющих на прочность;
- при изменении нагруженности.
Значения показателей прочности должны удовлетворять требованиям раздела 5.
8.1.2 Оценку прочности проводят по следующим предельным состояниям:
- появление остаточных деформаций при статическом нагружении, возникающих в результате превышения предела текучести материала о0 2;
- возникновение макротрещин при циклическом (много- и малоцикловом) нагружении;
- потеря устойчивости (несохранение первоначальной формы конструкции или ее элемента вследствие их недостаточной жесткости);
- недопустимое изменение геометрии и размеров деталей вследствие накопления пластических деформаций.
8.2 Методы расчета и оценки прочности
8.2.1 Методы оценки прочности определяют в зависимости от условий работы рассматриваемого элемента и достижения его предельного состояния.
8.2.2 Кузова (главные рамы), рамы тележек, промежуточные рамы (балки, брусья и т. п.) второй ступени рессорного подвешивания, пружины рессорного подвешивания, узлы связей и узлы передачи сил тяги и торможения оценивают как по допускаемым напряжениям, так и по сопротивлению усталости.
8.2.3 Оценку прочности по допускаемым напряжениям (выполнение требования 5.2) проводят для случаев наиболее невыгодного возможного сочетания одновременно действующих нормативных нагрузок в соответствии с расчетными режимами по 6.3.
Полученные в результате расчета суммарные напряжения не должны превышать допускаемых значений, установленных в таблице 8.1 для соответствующих расчетных режимов.
8.2.4 Оценку сопротивления усталости конструкций экипажной части (за исключением колесных пар, валов тягового привода, зубчатых колес и пружин рессорного подвешивания) выполняют путем расчета коэффициентов запаса сопротивления усталости по 8.3.
Таблица 8.1 — Допускаемые напряжения для элементов кузова (главной рамы) и тележки
Расчетный режим | Допускаемое напряжение для элементов | ||
кузова (главной рамы) | тележки | ||
Режим I | la | О,9о02 | |
I6 | 0,9 о0 2 | О,9о0 2 | |
Режим II | О,6о0 2 | ||
Режим III | 0,6 о0 2 | ||
Режим IV | 0,9 о0 2 | ||
* При проведении испытаний используют значение о0 2. Примечание — о02 — условный предел текучести материала, который принимают по справочным данным или определяют по ГОСТ 1497. |
При проектировании оценку сопротивления усталости допускается выполнять по другим апробированным методикам.
Для рам тележек и промежуточных рам (балок, брусьев и т. п.) второй ступени рессорного подвешивания дополнительно выполняют оценку сопротивления усталости по критерию отсутствия усталостных трещин после 10 млн циклов нагружения на вибрационном стенде в соответствии с 8.3.7.
8.2.5 Узлы передачи силы от сцепных устройств, шкворни и другие элементы связи кузова (главной рамы) с тележками или с колесными парами (для бестележечных локомотивов), а также концевые части рамы кузова, в которых могут возникать упруго-пластические деформации под воздействием эксплуатационных нагрузок при числе циклов нагружения до 105, рекомендуется рассчитывать на малоцикловую усталость по 8.4.
Оценку прочности при этом следует проводить как по критериям малоциклового нагружения, так и по критерию разрушения (образование макротрещин) вследствие накопления усталостных повреждений.
Для оценки несущей способности при малоцикловом нагружении рассчитывают коэффициенты запаса прочности и долговечности, которые не должны быть ниже заданных в 8.4.2.3.
8.2.6 Для сжатых элементов кузова (главной рамы), обшивки необходимо проверить возможность потери как общей, так и местной устойчивости для режимов I и IV. Коэффициенты запаса устойчивости должны быть не ниже заданных в 5.6.
Выполнение данного требования подтверждают расчетом.
8.2.7 Прочность конструкции путеочистителя должна быть обеспечена по условию о < 0,85 ов при нагружении в соответствии с приложением А.
8.3 Оценка запаса сопротивления усталости
8.3.1 Оценку прочности по коэффициенту запаса сопротивления усталости несущих элементов, за исключением оси и колеса в составе колесной пары, проводят в зависимости от имеющейся информации о характеристиках сопротивления усталости объекта и его нагруженности:
- при отсутствии представительной гистограммы распределения амплитудных значений напряжений, характеризующих нагруженность объекта при эксплуатации — по 8.3.2;
- при известном фактическом значении предела выносливости натурной детали — по 8.3.3;
- при наличии представительной гистограммы динамических напряжений — по 8.3.5.
У словия получения представительной гистограммы динамических напряжений приведены в 8.3.5.1.
8.3.2 При отсутствии представительной гистограммы распределения амплитудных значений напряжений, характеризующих нагруженность объекта при эксплуатации, коэффициент запаса сопротивления усталости п вычисляют по формуле
0 ’ ' ' '
Ka Oa + Vc -щ-
где о_1р — предел выносливости стандартного образца при растяжении-сжатии с симметричным циклом нагружения, МПа;
оа — амплитуда напряжений (максимальных в зоне концентрации) цикла, МПа;
— коэффициент, характеризующий влияние асимметрии цикла; принимают = 0,3 при от > 0, = 0 при от < 0;
вт — среднее напряжение цикла, МПа;
ао — теоретический коэффициент концентрации напряжений;
KQ — коэффициент, характеризующий понижение предела выносливости конструкции по отношению к пределу выносливости стандартного образца (коэффициент концентрации).
Предел выносливости о_1р принимают по справочным данным или определяют экспериментально по ГОСТ 25.502 на круглых образцах диаметром 7,5 мм или 10 мм.
Для несущих элементов с высотой сечения до 100 мм включительно, работающих на изгиб, а также для зон элементов несущей конструкции, имеющих местную деформацию изгиба листа, коэффициенты запаса сопротивления усталости рассчитывают по формуле
(8.2)
где о_1 — предел выносливости при изгибе с симметричным циклом нагружения, полученный по результатам испытаний стандартных образцов или принятый по справочным данным.
Допускается использовать следующие эмпирические зависимости:
о_1р=0,7о_1 ;
о_1 = (0,45 - 0,5) ов — для прокатной стали;
0-1 = 0,4 ов — для литых сталей и алюминиевых сплавов.
8.3.2.1 Значение коэффициента оса принимают равным:
- 1,4 — для зон концентрации на границах сварных швов (кроме стыковых), в выточках и переходах с радиусами не более 150 мм;
- 1,1 — на границах сварных стыковых швов;
- 1,0 — для других зон.
8.3.2.2 За среднее напряжение цикла <зт как при проведении испытаний, так и при расчете принимают напряжения, возникающие от постоянно действующих вертикальных статических нагрузок ост, т. е. <зт = ост .
8.3.2.3 При испытаниях амплитуду напряжений цикла оа определяют на основании экспериментальных данных, полученных при проведении динамико-прочностных испытаний. Значение оа определяют в порядке, аналогичном изложенному в 6.2.1 для динамической составляющей рамной силы.
При проектировании расчетную амплитуду напряжений цикла оа определяют методом решения задачи вынужденных колебаний динамической модели экипажной части.
8.3.2.4 Значения коэффициента концентрации К вычисляют по формуле
Кд К9
Кс =—!—^К3, v-K
(8.3)
где Кд — коэффициент, учитывающий влияние неоднородности материала детали; для проката, поковки и штамповки принимают = 1,1, для литых деталей принимают Кд = 1,25;
К2 — коэффициент, учитывающий влияние внутренних напряжений в детали, принимаемый, в зависимости от ее наибольшего поперечного размера, равным:
- 1,0 — при размере до 250 мм;
- от 1,0 до 1,2 — при размере от 250 до 1000 мм, пропорционально размеру;
Кт — коэффициент, учитывающий состояние поверхности детали и в зависимости от способа обработки принимаемый равным:
- 1,0 — для полированной поверхности;
- 0,9 — для поверхности после чистовой станочной обработки;
- 0,8 — для поверхностей после черновой станочной обработки, поверхностей с окалиной и поверхностей стальных литых деталей после пескоструйной обработки;
у — коэффициент, учитывающий влияние размерного фактора и выбираемый в зависимости от наибольшего размера поперечного сечения детали h;
К3 — корректирующий коэффициент, используемый для зон сварных соединений, зон выточек и переходов с радиусами менее 10 мм сварных несущих конструкций экипажной части, за исключением сварных несущих конструкций надрамного строения кузова (боковые стенки кузова, крыша кузова, кабина машиниста, торцевая стенка, перегородки и др.).
Значение коэффициента у выбирают равным:
- 0,8 — при высоте сечения h до 100 мм включ.;
- 0,75 — при высоте сечения h св. 100 до 250 мм включ;
- 0,7 — при высоте сечения h св. 250 мм.
Значение корректирующего коэффициента К3 принимают равным:
- 1,4 — для сплавов на основе алюминия;
- 1,0 — для углеродистых прокатных сталей марок Ст15, Ст20 по ГОСТ 1050, СтЗсп по ГОСТ 380;
- 1,2 — для низколегированных прокатных сталей марок 09Г2, 09Г2Д, 09Г2С, 09Г2СД по ГОСТ 19281;
- 1,2 — для коррозионно-стойких прокатных сталей.
Для других марок прокатных сталей коэффициент К3 определяют экспериментально. Для этого проводят стендовые циклические испытания на усталость типового сварного образца по методу, указанному в приложении Б.
Для этого проводят стендовые вибрационные испытания типового сварного образца по методу, указанному в приложении Б.
8.3.3 Если определено фактическое значение предела выносливости натурной детали по результатам стендовых испытаний на усталость, коэффициент запаса сопротивления усталости п вычисляют по формуле
°а+-^т
где о_1а — предел выносливости детали, определенный экспериментальным путем, при симметричном цикле нагружения на базе 107 циклов, МПа.
При известном пределе выносливости детали при асимметричном цикле нагружения коэффициент п может быть вычислен по формуле
<5Г
п =(8.5) ° а
где ог— предел выносливости детали при асимметричном цикле нагружения, МПа.
8.3.4 Коэффициенты запаса сопротивления усталости, вычисленные по формулам (8.1), (8.2), (8.4), (8.5), не должны быть меньше значений, приведенных в 5.4.
8.3.5 При наличии представительной гистограммы динамических напряжений расчет на усталость выполняют вероятностными методами, исходя из предпосылки, что амплитуда переменных напряжений является случайной величиной.
8.3.5.1 Представительную гистограмму динамических напряжений получают путем статистической обработки схематизированных случайных процессов, записанных в ходе динамико-прочностных испытаний локомотива с выполнением следующих условий:
- испытания проведены в послеремонтном (или в начале ввода в эксплуатацию) и в предремонт-ном (включая предельный износ по кругу катания колес) состояниях экипажной части локомотива;
- для каждого из состояний экипажной части локомотива испытания проведены при состояниях пути, характерных для сезонов зима и лето;
- для каждого из состояний экипажной части локомотива (послеремонтное и предремонтное) и состояний пути (зима и лето) испытания проведены на различных участках с суммарной протяженностью не менее 2000 км при движении по прямым участкам пути, кривым и стрелочным переводам (включая съезды на боковой путь) (п. 8.3.5.3);
- при испытаниях реализованы эксплуатационные режимы движения (тяга, выбег, служебное торможение) с различными скоростями вплоть до конструкционной или максимальной эксплуатационной;
- регистрация напряжений осуществлялась непрерывно при движении локомотива.
Примечания
1 Послеремонтное состояние экипажной части локомотива — состояние при пробеге локомотива не более 10 % от межремонтного (между капитальными ремонтами) пробега с момента изготовления или последнего капитального ремонта локомотива.
2 Предремонтное состояние экипажной части локомотива — состояние при пробеге локомотива не менее 50 % от межремонтного (между капитальными ремонтами) пробега с момента изготовления или последнего капитального ремонта локомотива.
Достижение требуемой суммарной протяженности участка (не менее 2000 км) путем многократного движения локомотива по одному и тому же пути недопустимо. Допускается снижение суммарной протяженности участка в случае, если в технических условиях на локомотив установлен ограниченный участок его эксплуатации (обращения), протяженность которого с учетом движения по различным путям не достигает 2000 км.
8.3.5.2 Коэффициент запаса сопротивления усталости п вычисляют по формуле
п = —У~, (8.6)
°аэ
где о_1а — предел выносливости детали, определенный экспериментальным путем, при симметричном цикле нагружения на базе 107 циклов, МПа
оаэ — эквивалентная амплитуда динамических напряжений, МПа.
Примечание — Под эквивалентной амплитудой динамических напряжений следует понимать амплитуду напряжений условного симметричного цикла, эквивалентную по повреждающему действию реальному режиму эксплуатационных напряжений за расчетный срок службы детали.
8.3.5.3 При аппроксимации кривой усталости наклонной и горизонтальной прямыми линиями эквивалентную амплитуду динамических напряжений оаэ, МПа, вычисляют по формуле, полученной на основании гипотезы линейного суммирования повреждений
(8.7)
где т — показатель степени в уравнении кривой усталости в амплитудах напряжений (нагрузок); Л/^ — суммарное число циклов действия динамических напряжений, определяют по результатам обработки схематизированных случайных процессов;
Л/о — базовое число циклов (для стальных конструкций Л/о = 107);
pv. — доля времени, приходящаяся на эксплуатацию в ДУ—м интервале скоростей (значения pv. принимают по таблице 8.2);
К Kv. — принятое соответственно число разрядов амплитуд напряжений в /-м интервале скоростей и число разрядов скоростей движения;
КуЧ;— средняя доля протяженности прямых (/ = 1), кривых участков пути (/ = 2) и стрелок (/ = 3) в общей длине железнодорожных линий, по которым предполагают эксплуатацию испытуемого локомотива;
оа/ — амплитуда напряжений /-го уровня, МПа;
р — частота (вероятность) появления амплитуд напряжений с уровнем оа/в АУ-м интервале скоростей движения локомотива.
Таблица 8.2 — Рекомендуемые значения долей времени pv.
Интервал скорости движения, м/с | Средняя ско-рость интервала, м/с | Значение долей времени pv. | ||||||
Пассажирские локомотивы | Грузовые локомотивы | |||||||
Конструкционная скорость, м/с (км/ч) | ||||||||
55,5 (200) | 44,4 (160) | 38,9 (140) | 38,9 (140) | 33,3 (120) | 27,8 (100) | 25 (90) | ||
0—12,5 | 6,25 | 0,01 | 0,02 | 0,03 | 0,02 | 0,03 | 0,05 | 0,08 |
12,5—15,0 | 13,75 | 0,02 | 0,05 | 0,06 | 0,06 | 0,07 | 0,12 | 0,17 |
15,0—17,5 | 16,25 | 0,03 | 0,07 | 0,08 | 0,07 | 0,09 | 0,15 | 0,22 |
17,5—20,0 | 18,75 | 0,04 | 0,09 | 0,10 | 0,10 | 0,12 | 0,20 | 0,30 |
Окончание таблицы 8.2
Интервал скорости движения, м/с | Средняя ско-рость интервала, м/с | Значение долей времени pv. | ||||||
Пассажирские локомотивы | Грузовые локомотивы | |||||||
Конструкционная скорость, м/с (км/ч) | ||||||||
55,5 (200) | 44,4 (160) | 38,9 (140) | 38,9 (140) | 33,3 (120) | 27,8 (100) | 25 (90) | ||
20,0—22,5 | 21,25 | 0,06 | 0,11 | 0,12 | 0,13 | 0,16 | 0,25 | 0,18 |
22,5—25,0 | 23,75 | 0,07 | 0,13 | 0,13 | 0,14 | 0,19 | 0,15 | 0,05 |
25,0—27,5 | 26,25 | 0,09 | 0,15 | 0,13 | 0,13 | 0,16 | 0,06 | — |
27,5—30,0 | 28,75 | 0,12 | 0,13 | 0,12 | 0,11 | 0,10 | 0,02 | — |
30,0—32,5 | 31,25 | 0,13 | 0,09 | 0,10 | 0,10 | 0,06 | — | — |
32,5—35,0 | 33,75 | 0,12 | 0,06 | 0,06 | 0,07 | 0,02 | — | — |
35,0—37,5 | 36,25 | 0,10 | 0,04 | 0,05 | 0,05 | — | — | — |
37,5—40,0 | 38,75 | 0,07 | 0,03 | 0,02 | 0,02 | — | — | — |
40,0—42,5 | 41,25 | 0,05 | 0,02 | — | — | — | — | — |
42,5—45,0 | 43,75 | 0,03 | 0,01 | — | — | — | — | — |
45,0—47,5 | 46,25 | 0,02 | — | — | — | — | — | — |
47,5—50,0 | 48,75 | 0,02 | — | — | — | — | — | — |
50,0—52,5 | 51,25 | 0,01 | — | — | — | — | — | — |
52,5—55,0 | 53,75 | 0,01 | — | — | — | — | — | — |
Для сети железных дорог общего пользования принимают:
Куч1 = 0,87 — для прямых участков пути;
Куч2 = 0,11 — для кривых участков пути;
Куч3 = 0,02 — для стрелочных переводов.
Значения показателя степени кривой усталости т для локомотивных конструкций рекомендуется принимать:
8 — для гладких, чисто обточенных и шлифованных валов и осей с галтелями без поверхностного упрочнения;
18 — то же, с упрочненной накаткой поверхностью;
4 — для сварных конструкций из проката без упрочняющей обработки швов;
6 — то же, с механической или аргонно-дуговой обработкой швов;
4 — с нормализацией;
5 — с закалкой и отпуском.
8. 3.6 В качестве минимально допустимого значения коэффициента запаса сопротивления усталости, рассчитанного по 8.3.5, рекомендуется принимать 2,2.
8. 3.7 Для оценки сопротивления усталости рам тележек и промежуточных рам (балок, брусьев и т. п.) второй ступени рессорного подвешивания проводят стендовые вибрационные испытания на базе 10 млн циклов нагружения. Испытаниям подвергают один образец.
К объекту испытаний прикладывают статические и динамические (циклические) нагрузки. Значения статических нагрузок принимают равными силам тяжести устанавливаемого на объект испытаний оборудования, включая полностью оборудованный и экипированный кузов (главную раму).
Динамические показатели вертикальных и горизонтальных испытательных нагрузок выбирают из условия движения локомотива в прямых участках пути. Значения основных динамических (циклических) нагрузок — динамических составляющих вертикальных сил от веса надрессорного строения (Р^ии —для рамы тележки; рД”н —дЛя промежуточной рамы [балки, бруса]) и динамических составляющих рамных сил (У^ин) принимают по результатам динамико-прочностных испытаний конкретного 21
типа локомотива, конструкции которого подлежат стендовым вибрационным испытаниям. При отсутствии результатов динамико-прочностных испытаний конкретного типа локомотива за значения циклических нагрузок принимают увеличенные на 20 % значения У^ин, Р^\Н, ?Z2H (см- —6.2.3), полу
ченные по результатам математического моделирования движения соответствующего локомотива, но не более значений, вычисленных умножением максимально допустимых значений показателей в соответствии с 4.1—4.3 на соответствующие статические нагрузки. Максимальные величины боковых сил, возникающие при движении в кривых, должны приниматься как действующие статически (квазистатически) и оцениваться по допускаемым значениям напряжений.
Объекты испытаний, нагружаемые в эксплуатации вертикальными силами от веса надрессорного строения и рамными силами, при испытании нагружают этими силами одновременно.
Испытания рам тележек и промежуточных рам (балок, брусьев и т. п.) второй ступени рессорного подвешивания выполняют в следующих случаях:
- при разработке новой конструкции;
- при модернизации конструкции;
- при смене изготовителя;
- при замене материала для изготовления конструкции;
- при изменении технологии изготовления, влияющей на прочность конструкции;
- при увеличении нагрузок более чем на 10,0 % по сравнению с ранее реализованными при проведении стендовых вибрационных испытаний.
Если в конструкции локомотива применяют рамы тележек, промежуточные рамы (балки, брусья и т. п.), изготовленные разными предприятиями, испытаниям подлежат конструкции всех изготовителей.
8.4 Рекомендации по расчету на прочность при малоцикловом нагружении
8.4.1 Расчет на малоцикловую усталость8.4.1.1 Расчет при малоцикловом нагружении выполняют для тех зон конструкций, где могут возникать локальные упругопластические деформации, циклическое изменение которых приводит к разрушению квазистатического либо усталостного типа.
8.4.1.2 Расчет на прочность при малоцикловом нагружении элементов конструкций для заданных условий эксплуатации (число циклов, асимметрия цикла и т. д.) проводят по деформационно-кинетическим критериям малоцикловой прочности, основанным на суммировании усталостных и квазистатиче-ских разрушений (повреждений).
8.4.1.3 При расчете малоцикловой долговечности и оценке накопления повреждений используют:
- значения местных упругопластических деформаций в максимально напряженных зонах конструкции;
- кривую малоцикловой усталости конструкционного материала Nf =
где Nf— число циклов до образования трещин, gW — пластическая деформация в к-м полуцикле нагружения;
- диаграмму статического и циклического деформирования.
Местные деформации в элементах конструкций определяют расчетным путем или по результатам измерений деформаций на моделях и на натурных конструкциях при эксплуатационных нагрузках.
При расчете местных деформаций используют диаграммы циклического деформирования, получаемые по данным испытаний лабораторных образцов, или расчетные диаграммы деформирования, построенные по диаграммам статического деформирования.
Параметры диаграмм циклического деформирования некоторых сталей в стабильном состоянии приведены в таблице 8.3.
Таблица 8.3 — Параметры диаграмм циклического деформирования
Сталь СтЗсп ГОСТ 380 | Сталь 09Г2 ГОСТ 19281 | Сталь 10ХСНД ГОСТ 19281 | Сплав 1561 | ||||
Размах деформаций Де, % | Размах напряжений До, МПа | Размах деформаций Де, % | Размах напряжений До, МПа | Размах деформаций Де, % | Размах напряжений До, МПа | Размах деформаций Де, % | Размах напряжений До, МПа |
0,2 | 332 | 0,05 | 105 | 0,05 | 105 | 0,2 | 140 |
0,3 | 458 | 0,10 | 210 | 0,10 | 210 | 0,3 | 211 |
0,4 | 515 | 0,15 | 303 | 0,15 | 315 | 0,4 | 275 |
Окончание таблицы 8.3
Сталь СтЗсп ГОСТ 380 | Сталь 09Г2 ГОСТ 19281 | Сталь 10ХСНД ГОСТ 19281 | Сплав 1561 | ||||
Размах деформаций Ле, % | Размах напряжений До, МПа | Размах деформаций Де, % | Размах напряжений До, МПа | Размах деформаций Де, % | Размах напряжений Да, МПа | Размах деформаций Де, % | Размах напряжений Да, МПа |
0,5 | 553 | 0,20 | 363 | 0,20 | 415 | 0,5 | 319 |
0,6 | 583 | 0,25 | 435 | 0,25 | 485 | 0,6 | 350 |
0,7 | 610 | 0,30 | 482 | 0,30 | 535 | 0,7 | 372 |
0,8 | 635 | 0,35 | 520 | 0,35 | 585 | 0,8 | 389 |
0,9 | 658 | 0,40 | 548 | 0,40 | 631 | 0,9 | 401 |
1,0 | 682 | 0,45 | 569 | 0,45 | 669 | 1,0 | 410 |
1,1 | 701 | 0,50 | 585 | 0,50 | 703 | 1,1 | 418 |
1,2 | 718 | 0,55 | 594 | 0,55 | 730 | 1,2 | 425 |
1,3 | 733 | 0,60 | 610 | 0,60 | 756 | 1,3 | 430 |
1,4 | 747 | 0,65 | 620 | 0,65 | 779 | 1,4 | 437 |
1,5 | 761 | 0,70 | 629 | 0,70 | 800 | 1,5 | 442 |
1,6 | 775 | 0,75 | 635 | 0,75 | 816 | 1,6 | 447 |
1,7 | 787 | 0,80 | 644 | 0,80 | 833 | 1,7 | 451 |
1,8 | 800 | 0,85 | 650 | 0,85 | 849 | 1,8 | 455 |
1,9 | 811 | 0,90 | 657 | 0,90 | 863 | 1,9 | 460 |
2,0 | 821 | 1,00 | 671 | 1,00 | 877 | 2,0 | 464 |
2,1 | 832 | 1,10 | 684 | 1,10 | 890 | 2,1 | 467 |
2,2 | 842 | 1,20 | 693 | 1,20 | 903 | 2,2 | 471 |
2,3 | 852 | 1,30 | 704 | 1,30 | 916 | 2,3 | 474 |
2,4 | 862 | 1,40 | 715 | 1,40 | 929 | 2,4 | 477 |
2,5 | 871 | 1,50 | 724 | 1,50 | 940 | 2,5 | 480 |
2,6 | 880 | 1,60 | 733 | — | — | — | — |
Испытания для построения диаграмм деформирования проводят в соответствии с ГОСТ 25.502 и ГОСТ 1497.
Кривую малоцикловой усталости, выражающую зависимость долговечности от циклической упругопластической деформации, строят по результатам испытаний серии образцов. Объем серии — по ГОСТ 25.502.
При жестком нагружении кривую описывают уравнением Мэнсона — Коффина
Де^ =CfN~m,
Л (Л) ,
где ДЕр — размах пластической деформации в k-м цикле нагружения;
С^и m — константы кривой усталости.
При мягком нагружении уравнение кривой усталости представляют в виде
а^ЛЛ1 =авЛ/£,
где ц = 0,2 1д(с>в/о_1) —показатель степени наклона левой ветви кривой малоцикловой усталости, определяемый через характеристики материала ов (предел прочности) и о_1 (предел выносливости);
N, Л/в — число циклов до разрушения на уровне предела выносливости и предела прочности материала соответственно.
Для учета влияния упругой и пластической составляющих деформации при жестком нагружении во всей малоцикловой области используют кривую усталости в виде
= Cf- N~m +^-L, (8.10)
где eW — пластическая деформация в к-м цикле нагружения;
Е — модуль упругости материала, МПа.
Первое слагаемое в уравнении (8.10) характеризует пластическую, второе — упругую составляющую циклической деформации.
При смешанном нагружении (во всем мало- и многоцикловом диапазоне) следует использовать универсальное уравнение кривой усталости
e = C,N-m + ^
' Е
1-
-0.5(NMIN,), (8.11)
где Рт — нагрузка, соответствующая пределу текучести материала рассматриваемого элемента конструкции;
Рпр — предельная нагрузка для этого же элемента в упругопластической области;
Л/м — число циклов квазистатического нагружения в малоцикловой области;
Л/1 — число циклов в единичном (годовом) блоке нагружения.
Примечание — В уравнении (8.11) коэффициент [1 - (Рт / Рпр)2] учитывает снижение предела выносливости материала под действием неупругих деформаций, а коэффициент NM/N^ учитывает долю малоцикловых нагрузок в действующем эксплуатационном блоке.
Коэффициенты С^и т уравнений кривых малоцикловой усталости (8.8), (8.10) и (8.11) определяют по результатам испытаний образцов при малоцикловом нагружении с симметричным циклом деформаций.
При отсутствии результатов испытаний коэффициент т принимают равным 0,5—0,6, а коэффициент Cf вычисляют по формуле
1
Cf=0,5ln----, (8.12)
1-V
где v — коэффициент сужения, характеризующий сужение поперечного сечения образца и выраженный в относительных единицах.
Для сталей с пределом прочности не более 1200 МПа значение коэффициента сужения Т вычисляют по формуле
[Ъпри^0,3
т [0,15 + 0,5^ при >0,3 v ’
где ук — коэффициент сужения, определяемый по результатам испытания на разрыв стандартных образцов и соответствующий разрыву образца.
8.4.1.4 При отсутствии экспериментальных данных о значениях местных напряжений и деформаций в зонах концентрации (при возникновении упругопластических деформаций) в расчет вводят коэффициенты концентрации упругопластических деформаций Ке , которые определяют по формуле
Ке = Ю2пр/Ка, (8.14)
где (оса)пр — приведенный теоретический коэффициент концентрации напряжений, т. е. определенный по соответствующим коэффициентам концентрации для каждой из составляющих главных напряжений;
KQ — коэффициент концентрации напряжений в упругопластической области (при упругих деформациях Кс = ао).
Примечание — Формула (8.14) используется при (аа)пр - 3,5, а при (ао)пр > 3,5 ее применение дает результаты, идущие в запас прочности.
Коэффициент Кс при известных максимальной местной деформации цикла (emax)np или амплитуды местной деформации (еа)пр вычисляют соответственно по формулам:
- _ а0,2 _ °0,2
£’(етах)пр (°тах)пр
к _ q0,2 _ °0,2
°~Е (еа) ~ (оа) ’
\ а/Пр \ а/Пр
(8.15)
(8.16)
где о0 2 — условный предел текучести материала.
Если в зонах концентрации расположены сварные швы, то в формулах (8.15), (8.16) значение о0 2 принимают наименьшим из значений для металла шва и для основного металла.
Значение Ке, уточненное с учетом упрочнения материала в упругопластической области, вычисляют по формуле где епр • Е = (б‘)пр — приведенное напряжение без учета концентрации напряжений, МПа;
Ке - К (ао)пр’
епр ' Е а0,2
пр’
(8-17)
о0 2 — условный предел текучести, МПа;
К* — коэффициент, зависящий от («а)пр и показателя упрочнения при статическом нагружении (нулевой цикл).
Коэффициент К* выбирают по таблице 8.4.
Таблица 8.4 — Значения коэффициента К*
(ао)пр | Значение коэффициента К* при показателе упрочнения п№ | ||||||
0,30 | 0,25 | 0,18 | 0,13 | 0,07 | 0,04 | 0 | |
1,5 | 0,26 | 0,32 | 0,38 | 0,44 | 0,48 | 0,53 | 0,64 |
2,0 | 0,32 | 0,38 | 0,45 | 0,50 | 0,55 | 0,60 | 0,70 |
3,0 | 0,31 | 0,37 | 0,43 | 0,50 | 0,56 | 0,65 | 0,70 |
5,0 | 0,29 | 0,35 | 0,42 | 0,51 | 0,57 | 0,68 | 0,75 |
Примечание — Для промежуточных значений (ао)пр и гг№\ не указанных в таблице, значение К* определяют путем линейной интерполяции (экстраполяции) табличных данных.
Показатель упрочнения выбирают по таблице 8.5 в зависимости от коэффициента сужения у и отношения о02/ов.
Таблица 8.5 — Значения показателя упрочнения т<°)
°0,2 ! °в | Значения показателя упрочнения т® при коэффициенте сужения у | ||
0,1 | 0,2 | 0,3 —0,6 | |
0,30 | 0,29 | 0,27 | 0,35 |
0,50 | 0,21 | 0,17 | 0,19 |
0,70 | 0,11 | 0,11 | 0,13 |
0,90 | 0,05 | 0,06 | 0,07 |
0,95 | 0,02 | 0,03 | 0,04 |
1,00 | 0 | 0 | 0 |
8.4.1.5 Если эксплуатационные местные деформации (напряжения) в конструкции определены (экспериментально или расчетным путем), то независимо от циклических свойств металла разрушающие амплитуды напряжений (деформаций) для конструкции при заданном числе циклов до разрушения (или число циклов до разрушения при заданной разрушающей амплитуде деформаций) вычисляют по уравнениям деформационного критерия разрушения:
0,5Е_______ 1 _______0,5SK_______
(8.18)
(8.19)
'JW)'"’ + + nJ(4[W])m- +1±4
L J [
0,5E ,1
=------------:: 1n-------+---------------------------
(4nN[<»+^
1-r
где [о*] — амплитуда местных условных упругих приведенных напряжений по гипотезе наибольших касательных напряжений, МПа;
Е — модуль упругости, МПа;
у — коэффициент относительного сужения поперечного сечения;
SK — сопротивление разрыву в шейке при растяжении стандартного образца по ГОСТ 25.502, определяемое как разрушающее напряжение в шейке поданным испытаний, МПа;
п — коэффициент безопасности по напряжениям;
nN — коэффициент безопасности по числу циклов (по долговечности);
тр, те — характеристики кривой малоцикловой и многоцикловой усталости соответственно;
г— коэффициент асимметрии цикла местных упругих напряжений;
г* — коэффициент асимметрии цикла местных условных упругих напряжений (деформаций).
В качестве расчетных характеристик используются минимальные значения [о*] и [Л/], полученные из решения нелинейной системы уравнений (8.18), (8.19).
Примечания
1 Уравнения (8.18), (8.19) справедливы как для малоцикловой области, так и для многоцикловой (10° < N< 1010) и позволяют учесть асимметрию цикла деформаций (напряжений), нестационарность нагружения, уменьшение пластичности при технологических и монтажных операциях или деформационном старении, наличие сварных швов и др.
2 Коэффициент безопасности по напряжениям для заданного режима нагружения определяют соотношением п<7 = фМэ-
где о* — разрушающая амплитуда местных напряжений;
с*э — амплитуда местных напряжений в наиболее нагруженной при эксплуатации зоне рассчитываемого на прочность элемента конструкции.
3 Коэффициент безопасности по долговечности определяют соотношением
nN=N/N3,
где N — разрушающее число циклов для эксплуатационных уровней напряжений (о*э);
N3 — эксплуатационное количество циклов нагружения за расчетный срок службы, определяемое по результатам обработки схематизированных случайных процессов, зарегистрированных при динамико-прочностных испытаниях опытного образца локомотива или локомотива, имеющего аналогичную экипажную часть.
8 .4.2 Оценка прочности при малоцикловом нагружении
8.4.2.1 По уравнениям (8.8) — (8.10) определяют число циклов нагружения до разрушения для элементов, подвергающихся в эксплуатации нагружению в малоцикловом диапазоне.
8.4.2.2 Элементы конструкций, подвергающиеся в эксплуатации смешанному нагружению от сил тяги, торможения, инерции тележек при соударениях (узлы передачи силы от сцепных устройств, шкворневые узлы, элементы связи кузова (главной рамы) с тележками), рассчитывают на долговечность по уравнению кривой усталости (8.11) или уравнениям (8.18) и (8.19).
При расчете по уравнениям (8.18) и (8.19) для заданных коэффициентов безопасности строят соответствующие кривые, после чего сопоставляют действующие в эксплуатации амплитуды и числа циклов с допустимыми.
8.4.2.3 Значения коэффициентов лст и nN принимают с учетом типа конструкций, условий их эксплуатации и ответственности, опыта проектирования и изготовления, точности расчетов и задания исходной информации, рассеяния характеристик нагруженности и механических свойств.
Для элементов конструкций с высокой концентрацией напряжений принимают:
ла = от 1,5 до 2,0, nN = от 3,0 до 10,0.
Если испытанию при эксплуатационных нагрузках подвергают натурные конструкции или полномасштабные модели, то значения коэффициентов запаса должны удовлетворять условиям
па г 1,25, nw22,1.
8.5 Расчет долговечности (ресурса) несущих элементов металлоконструкций локомотивов
8.5.1 Расчеты несущих конструкций локомотивов на циклическую долговечность выполняют:
- для установления назначенных сроков службы на основе определения ресурса при проектировании и модернизации;
- для оценки возможности дальнейшей эксплуатации (продление или установление нового назначенного срока службы на основании расчета остаточного ресурса);
- при изменении нагруженности (интенсивности эксплуатации);
- для выполнения условий безопасности в соответствии с требованиями [1] по установлению назначенного срока службы и ресурса (раздел 11).
8.5.2 Расчет долговечности (ресурса) проводят на основе гипотезы линейного суммирования повреждений.
Необходимыми исходными данными для расчета долговечности являются:
- результаты исследования напряженно-деформированного состояния детали, полученные расчетным либо экспериментальным путем;
- блок эксплуатационных нагрузок (например, в течение 1 года работы, 1 км пробега), полученный по результатам математического моделирования либо по результатам динамико-прочностных испытаний опытного образца локомотива и представленный в виде ступенчатой функции распределения ам-
СТд/ О
плитуд динамических напряжений, заданной парой чисел (-----, f,), где -----— амплитуда напряга max Gamax
жений /-го уровня, отнесенная к максимальному напряжению блока; tj—доля напряжений /-го уровня в общем блоке;
- параметры кривой усталости (предел выносливости о_1а, точка перелома NG и показатели степени наклона прямых, аппроксимирующих кривую усталости /л1 и т2). Предлагается при проектных расчетах т1 принимать равными: 4 — для литых деталей и 5 — для сварных; т2 = 2 - 1.
8.5.3 Если кривая усталости аппроксимирована наклонной и горизонтальной прямыми линиями, т. е. т2 = то напряжения менее 0,5о_1(Э в расчете не учитывают и используют уравнение
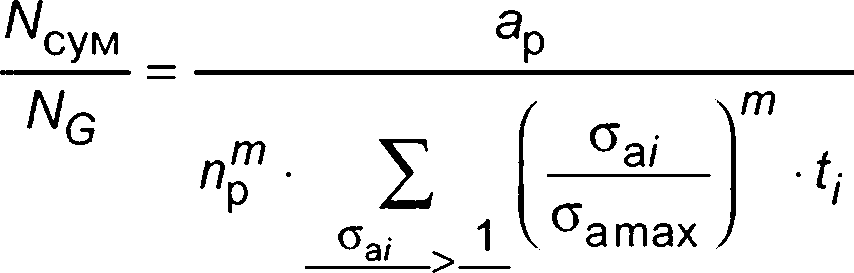
^атах
где Л/сум — суммарное количество циклов за срок службы детали;
Ng — число циклов, соответствующее точке перелома кривой усталости;
ар — параметр, корректирующий линейную гипотезу накопления повреждений при нерегулярном нагружении, для локомотивных конструкций рекомендуется принимать равным 0,6—0,8 (может уточняться по экспериментальным и эксплуатационным данным);
лр — коэффициент перегрузки.
Примечания
1 Согласно корректированной линейной гипотезе накопления повреждений условие разрушения имеет вид
ni
— = а0.
Ni р
2 Коэффициент перегрузки определяется соотношением
где Oanfax — максимальное напряжение в предельном блоке нагружения, который подобен действующему и вызывает разрушение при числе циклов Л/сум.
Уравнение (8.20) позволяет определить медианное (соответствующее вероятности разрушения 50 %) число циклов.
8 .5.4 Для расчета долговечности, соответствующей вероятности разрушения р, используют формулу
(8.21)
где Up — квантиль нормального распределения, соответствующий вероятности разрушения р, %; п — относительный коэффициент запаса, определяется из соотношения
„пред
° a max
°amax
(8.22)
- ЛР п = — п
где п = атах — действительный коэффициент нагруженности детали; а-1Э
Ое, О£ — коэффициенты вариации нормально распределенных величин предела выносливости о_15 и максимального напряжения <татах в действующем блоке нагружения.
Коэффициенты вариации при расчете принимают равными 0,10—0,20.
8 .5.5 Для кривой усталости, аппроксимируемой двумя наклонными прямыми линиями с показателями наклона т1 и т2, используют уравнение, аналогичное уравнению (8.20)
^сум nG
аР
^атах
(8.23)
В этом случае при расчете учитывают все напряжения из блока нагружения.
Задавшись вероятностью разрушения детали Р, по формулам 8.20, 8.21 или 8.23 определяют долговечность Л/сум, соответствующую этой вероятности, и срок службы L, который определяют по формуле
_ ^сум
(8-24)
ГОД
где год — количество циклов напряжений за 1 год.
Примечание — год определяется по частоте изменения напряжений и скорости движения.
Пример расчета долговечности приведен в приложении В.
Для расчетов долговечности (ресурса) ответственных конструкций и деталей могут быть использованы и другие методики по нормативной документации, принятой национальным законодательством3.
9 Требования к прочности и динамическим качествам узлов экипажной части
9.1 Корпус тягового опорно-осевого редуктора
9.1.1 Корпус тягового редуктора должен быть рассчитан на воздействие:
- перекоса подвески редуктора;
- тягового (тормозного) момента, низкочастотных крутильных колебаний и фрикционных автоколебаний при боксовании локомотива;
- колебаний неподрессоренных масс;
- динамических сил со стороны деталей зубчатой передачи.
9.1.2 Для снижения влияния динамических сил со стороны деталей зубчатой передачи и неподрессоренных масс на корпус и другие детали редуктора необходимо выполнение следующих условий:
- корпус редуктора не должен иметь локальных зон (кронштейн крепления подвески, горловина масломерного щупа и другие выступающие детали), частота свободных колебаний которых при скоростях движения локомотива от 50 км/ч до конструкционной скорости равна:
а) частоте пересопряжения зубьев зубчатой передачи;
б) двойной частоте пересопряжения зубьев зубчатой передачи;
- установка стаканов подшипников и лабиринтных крышек в корпусе редуктора должна быть беззазорной (для моноблочных корпусов допускается применение скользящей посадки);
- резьбовое крепление стаканов подшипников и лабиринтных крышек должно быть раздельным.
9.2 Расчет на прочность элементов тягового привода
9.2.1 При расчете на прочность зубчатой передачи тягового привода проводят расчеты по ГОСТ 21354:
- активных поверхностей зубьев на контактное сопротивление усталости (контактную выносливость);
- зубьев на сопротивление усталости при изгибе.
Примечание — Фраза в скобках приведена в редакции ГОСТ 21354, однако термин «выносливость» является недопустимым по ГОСТ 23207.
9.2.2 Элементы тягового привода, передающие крутящий момент, должны быть рассчитаны на нагруженность:
- при совместном действии:
а) крутящего момента при трогании;
б) в часовом режиме с учетом динамического момента;
в) динамического крутящего момента;
г) сил, возникающих при радиальной расцентровке и осевом смещении валов;
- от фрикционных автоколебаний при боксовании локомотива.
9.2.3 Низкочастотные (от 1,5 до 20 Гц) динамические нагрузки на элементы тягового привода при проектировании определяют как результат математического моделирования движения локомотива.
9.2.4 При расчете на прочность деталей тягового привода (кроме зубчатой передачи) должны быть учтены два основных вида динамических нагрузок:
- общие для всего тягового привода низкочастотные (от 1,5 до 8,0 Гц) динамические моменты, обусловленные кинематическим возмущением при колебаниях экипажной части;
- высокочастотный динамический крутящий момент, рассчитываемый по 9.2.5.
9.2.5 Высокочастотный динамический крутящий момент определяется высшими гармониками собственных колебаний зубчатой пары.
Высокочастотный динамический крутящий момент на валу шестерни для прямозубой передачи М3, Н м, рекомендуется вычислять по приближенной эмпирической формуле
М3 = 0,0032-^Св • Мд, (9.1)
где Св — крутильная жесткость части вала, определяемая параметрами прессовых соединений, ступенчатых изменений диаметров валов, проточек и галтелей, между фланцем муфты и шестерней, Н-м/рад;
Мд — динамический момент, обусловленный кинематическим возмущением при колебаниях экипажной части.
9.2.6 Элементы тягового привода должны быть рассчитаны на сопротивление усталости в соответствии с 8.3.
9.3 Определение расчетного ресурса подшипников буксовых узлов
9.3.1 Буксовые узлы необходимо рассчитывать на ресурс примененных в них подшипников исходя из условий эксплуатации и ожидаемого уровня и характера приложения нагрузок.
Расчетный ресурс подшипника, соответствующий 90 % надежности, L10a, км пробега, вычисляют по формулам:
а) для роликовых подшипников
(г А10/3 о I I
LWa = а23лС)кр.ср 10 l'^_| ’ (9-2)
б) для радиальных и радиально-упорных шариковых подшипников
з ( сг }3
^-Юа _ а23л^кр.ср ’ 10 "р- ’ (9-3)
в) для упорных шариковых подшипников
3 ( Са ?
^-10а _ ^З^^кр.ср ’10 "р” ’ (9-4)
где а23 — коэффициент, корректирующий ресурс в зависимости от специальных свойств подшипника и от условий его эксплуатации;
ОКрср — диаметр среднеизношенного колеса по кругу катания, м;
Сг, Са — соответственно радиальная и осевая базовые динамические расчетные грузоподъемности подшипника, кН;
Рг, Ра — соответственно радиальная и осевая эквивалентные динамические нагрузки, кН.
Примечание — Диаметр среднеизношенного колеса по кругу катания — среднее значение диаметра колеса между номинальным и минимальным допустимым в эксплуатации значениями.
9.3.1.1 При расчете ресурса буксовых подшипников, эксплуатирующихся при обычных условиях (при отсутствии повреждений и перекосов, правильном способе смазывания, наличии защиты от проникновения инородных частиц, нагрузках, не превышающих предельные, эксплуатации в допустимом диапазоне температур) с применением типовой пластичной смазки в необходимом количестве, принимают следующие значения коэффициента а23:
- 0,55 — для подшипников радиальных роликовых с короткими цилиндрическими роликами;
- 0,35 — для подшипников радиальных роликовых сферических;
- 0,65 — для подшипников радиально-упорных роликовых конических;
- 0,75 — для подшипников радиальных или упорных шариковых.
Для подшипников, изготовленных из высококачественных сталей с особенно низким содержанием вредных примесей, газов, неметаллических включений, при надежном обеспечении гидродинамической пленки масла между контактирующими поверхностями колец и роликов и отсутствии повышенных перекосов в узле, значение коэффициента а23 может быть увеличено до двух раз.
9.3.1.2 В качестве базовой динамической радиальной расчетной грузоподъемности Сг используют данные изготовителя подшипников.
Для подшипников новых конструкций значение Сг также может быть определено по ГОСТ 18855.
9.3.1.3 Эквивалентную динамическую радиальную нагрузку Рр кН, вычисляют по формулам:
а) для радиально-упорных роликовых, а также радиальных и радиально-упорных шариковых подшипников
= (X • Fr • Квр + У • Fa) • Кб-Кт; (9.5)
б) для роликовых подшипников с короткими цилиндрическими роликами
Pr=Fr'KBp Кб-Кт, (9.6)
где X, Y — коэффициенты радиальной и осевой нагрузок;
Fr, Fa — радиальная и осевая нагрузки, постоянные по значению и направлению, кН;
КВр — коэффициент вращения (при вращении внутреннего кольца Квр = 1, наружного — Квр =1,2);
Кб — коэффициент безопасности, учитывающий динамические условия работы подшипника (для буксовых подшипников локомотивов принимают Кб = 1,4);
Кт — температурный коэффициент подшипника (Хт = 1,00 при рабочей температуре до 100 °C).
Примечание — Коэффициенты X, Y зависят от соотношения радиальной и осевой нагрузок, а также параметра осевого нагружения е.
Значения коэффициентов X, Y определяют по ГОСТ 18855. Допускается использовать данные изготовителя подшипников.
Эквивалентную динамическую осевую нагрузку для упорных шариковых подшипников Ра, кН, вычисляют по формуле
Ра = Ра’Кб Кг. (9.7)
9.3.1.4 Радиальную нагрузку на один буксовый подшипник Fr, кН, вычисляют по формуле
F _ ро - <7н п гг ~
(9.8)
Пг
где — максимальная осевая статическая нагрузка (на рельсы);
пг— количество роликовых подшипников на оси, воспринимающих радиальную нагрузку (в двух буксах);
< 7нп — сила тяжести (вес) неподрессоренных частей, приходящаяся на колесную пару, кН;
Силу <7НГ| вычисляют по формуле
Знп = $КП + Qp + Уд’ (9-9)
где дкп — сила тяжести (вес) колесной пары;
< 7Р — сила тяжести (вес) неподрессоренной части редуктора;
< 7д — сила тяжести (вес) деталей, не передающих нагрузку на подшипники (лабиринтные кольца, торцовые гайки или шайбы, дистанционные кольца, шариковые подшипники при их наличии).
Примечание — Под силой тяжести (весом) неподрессоренной части редуктора подразумевают сумму массы зубчатого венца, его ступицы и 2/3 общей массы нижней и верхней частей корпуса с учетом массы шестерни и половины массы муфты.
9.3.1.5 При отсутствии экспериментальных или расчетных данных допускается средние осевые нагрузки, действующие на буксовый подшипник при движении локомотива в прямых и кривых участках пути Fanp и FaKp, кН, вычислять по эмпирическим формулам:
Fanp = KO,O3Fo, (9.10)
^акр^'0-06^- (9.11)
где К— коэффициент распределения осевой нагрузки между буксами колесной пары.
Значения коэффициента К принимают равными:
- 0,5 — при равномерном распределении осевой (рамной) силы между правым и левым буксовыми узлами колесной пары;
-1,0 — при восприятии осевой (рамной) силы одним буксовым узлом колесной пары.
При наличии данных об осевых нагрузках, полученных расчетным путем, или по результатам испытаний конкретных типов локомотивов осевую нагрузку в прямых и кривых участках пути вычисляют по формуле
\0,3
-3,33 Qn Пп П ЮО пт)
р у 3,33 Qi n1 [ -J-3,33 n2
(9.12)
(9.13)
a ( 1 100'nm 2 100’nm
где Tv T2,..., Tn — нагрузки на подшипник при каждом режиме работы, кН;
qv q2,..., qn — продолжительность работы при каждом режиме, % от общего цикла;
rij, п2.....пп — частота вращения при каждом режиме работы, мин-1;
пт — средняя частота вращения при работе, мин-1.
Частоту пт вычисляют по формуле
Ф $2 Уп
Пт =--'-Пл + —±-п2 + ... + ——пп.
т 100 1 100 z 100 п
9.3.1.6 Эквивалентную динамическую радиальную нагрузку в случаях применения в буксовых узлах локомотива радиально-упорных подшипников (например, конических двухрядных кассетного типа или роликовых радиальных сферических двухрядных) вычисляют по (9.5).
Динамические эквивалентные нагрузки для прямых Рг кН, и кривых Рг кН, участков пути вычисляют по формулам:
^гпр^^Л^апрИбА- (9-14)
(9.15)
Pr^X-Fr+Y- WK6'\-
Динамическую эквивалентную радиальную нагрузку Рг, кН, с учетом процентного соотношения доли прямых и кривых участков пути на железных дорогах Российской Федерации (~80 % — прямые участки пути, ~20 % — кривые участки пути) вычисляют по формуле
Pr = (o.SPrnp3 + O.2Pr1K°p'3)0,3. (9.16)
Динамические эквивалентные нагрузки в случаях применения в буксовых узлах локомотивов радиально-упорных и упорных шариковых подшипников, освобожденных от восприятия радиальных сил, вычисляют по формулам (9.5), (9.7). Осевую нагрузку на эти типы подшипников вычисляют по формуле
Ра = (о.ар^р3 + 0,2Яа1п0'3)0,3 . (9.17)
9.3.2 Расчетный ресурс буксовых подшипников локомотива должен соответствовать 5.9.
9.3.3 Пример расчета ресурса буксовых подшипников тепловоза 2ТЭ116 приведен в приложении Г.
9.4 Рекомендации по проектированию рессорного подвешивания
9.4.1 Для обеспечения устойчивости пружин круглого сечения, работающих на сжатие, отношение высоты нагруженной пружины Н к ее наружному диаметру должно быть:
- не более 1,75 при шарнирном закреплении опорных витков (опирание на шарнирные опоры);
- не более 3,5 при жестком закреплении опорных витков (опирание на жесткое основание).
9.4.2 Расчет цилиндрических стальных пружин проводят по ГОСТ 34628.
9.4.3 Эффективность демпфирования оценивают по коэффициентам относительного демпфирования низкочастотных форм колебаний экипажной части Код, которые должны быть:
- 0,2—0,3 для гашения форм, характеризующих колебания галопирования и подпрыгивания кузова (главной рамы), а также вертикальных колебаний тележек;
- 0,3—0,4 для гашения форм, характеризующих горизонтальные колебания кузова (главной рамы) — виляние, относ;
- 0,1—0,2 для гашения формы колебаний, характеризующей боковую качку кузова (главной рамы).
9.4.4 При использовании в экипажной части гидравлических демпферов с линейной зависимостью силы от скорости характеристики гидродемпферов определяют в следующем порядке.
Коэффициент относительного демпфирования /-й формы колебаний экипажной части вычисляют по формуле
где С и М — соответственно матрицы демпфирования и инерции динамической модели экипажной части, в которой кузов (главная рама) и подрессоренные массы тележек представляют собой твердые тела, соединенные между собой упругими и диссипативными связями;
Vj — вектор-столбец, характеризующий /-ю форму колебаний;
со, — собственная частота /-й формы колебаний.
Примечание — Индекс т означает операцию транспонирования.
Частоты со,-и вектор-столбцы ^находят из решения задачи о собственных значениях:
(К-со 2-М) • \Л = 0, /= 1,2, ...лсв, (9.19)
где Кж — матрица жесткости динамической модели;
псв — число степеней свободы.
Задача нахождения сох и Vj сводится к вычислению собственных значений и собственных векторов матрицы М-1 • К.
Варьируя коэффициенты сопротивления в матрице демпфирования, находят решения, при которых коэффициенты относительного демпфирования различных форм колебаний экипажной части соответствуют 9.4.3.
9.4.5 Выбранные характеристики гидродемпферов при необходимости корректируют по результатам динамико-прочностных испытаний локомотива и «сброса локомотива с клиньев».
При динамико-прочностных испытаниях эффективность демпфирования определяют по критериям, приведенным в разделе 4.
При «сбросе локомотива с клиньев» коэффициенты относительного демпфирования различных форм колебаний определяют по формулам:
. 1 I АГ
(9.20)
(9.21)
d: =
2.тс
или
1
d; =
' 2л(г-1) Ar
гдеА^ A2, ...,Ar — последовательно измеренные амплитуды затухающего колебательного процесса, расположенные по одну сторону оси от оси абсцисс.
10 Требования к применяемым материалам
10.1 Требования к материалам для изготовления сварных конструкций
10.1.1 Для изготовления сварных элементов конструкций базовых частей применяют прокат из углеродистых или низколегированных сталей следующих марок: 09Г2, 09Г2С, 09Г2СД, 10Г2Б, 10Г2СБ, 10Г2БД, 10ХСНД, 12Г2Б, 14Г2АФ по ГОСТ 19281.
Применение кипящей и полуспокойной стали в этих элементах не допускается.
Для изготовления кузовов (главных рам) помимо указанных сталей применяют сплавы на основе алюминия марок АМг5, АМгб и марки 1915 по ГОСТ 4784.
10.1.2 Для прочих несущих элементов химический состав сталей и механические свойства изготовляемого из них стального проката должны быть выбраны по ГОСТ 535, ГОСТ 1050, ГОСТ 14637, ГОСТ 19281.
10.1.3 Применение сталей других марок для изготовления сварных несущих элементов допускается после проведения комплекса испытаний с целью определения следующих показателей:
- ударная вязкость KCV и KCU при комнатной и пониженной температурах по ГОСТ 9454;
- свариваемость.
Свариваемость оценивают по результатам испытаний:
- по определению механических свойств сварных соединений по ГОСТ 6996;
- на сопротивляемость образованию горячих трещин по нормативным документам государства, принявшего стандарт4;
- на сопротивляемость образованию холодных трещин по нормативным документам государства, принявшего стандарт5.
Ударная вязкость и свариваемость должны быть не хуже, чем у проката:
- класса прочности 295 из низколегированной стали 09Г2Д по ГОСТ 19281 для элементов конструкций базовых частей;
- СтЗсп5 (категории 5 из стали СтЗсп по ГОСТ 380) по ГОСТ 14637 для других несущих элементов.
10.1.4 Для изготовления сварных конструкций из двухслойных сталей должны применяться стали марок: 12Х18Н10Т+ВСтЗсп, 06ХН28МДТ+ВСтЗсп, 08Х17Н13М2Т+20Х, 10Х17Н13М2Т+20К, 12Х18Н10Т+09Г2С по ГОСТ 10885.
10.1.5 Допускается применение сварных соединений из коррозионно-стойких (нержавеющих) сталей с углеродистыми сталями марок СтЗсп по ГОСТ 380, 15 и 20 по ГОСТ 1050, низколегированными сталями марок 16Д по ГОСТ 6713, 09Г2, 09Г2Д, 10Г2БД, 09Г2С, 09Г2СД, 10ХНДП, 15ХСНД по ГОСТ 19281 и другими низколегированными сталями.
10.1.6 Литые приварные несущие детали локомотивов следует изготавливать из низколегированных сталей марок 20ГЛ, 20ГФЛ, 20Г1ФЛ и углеродистых 15Л, 20Л, 25Л по ГОСТ 977.
Отливки следует применять только после термической обработки.
Содержание марганца в отливках должно быть не более 1,4 %, углерода — не более 0,23 %.
Для стали марки 20Г1ФЛ максимальное содержание углерода допускается не более 0,25 %, содержание марганца — не более 1,5 %. Ударная вязкость KCU при температуре минус 60 °C должна быть не менее 25 Дж/см2.
10.1.7 Приварные литые детали автосцепного устройства должны удовлетворять требованиям ГОСТ 22703.
10.1.8 Приварные детали из поковки из конструкционной углеродистой и легированной стали должны соответствовать требованиям ГОСТ 8479.
10.2 Требования к сварочным материалам
10.2.1 Электроды для ручной дуговой сварки и прихватки должны соответствовать требованиям:
- сталей — ГОСТ 9466;
- сплавов на основе алюминия — ГОСТ 23949.
10.2.2 Стальная сварочная проволока, применяемая для дуговой сварки и прихватки, должна соответствовать требованиям ГОСТ 2246, сварочная порошковая проволока — ГОСТ 26271.
Сварочная (присадочная) проволока из алюминия и алюминиевых сплавов должна соответствовать требованиям ГОСТ 7871.
10.2.3 Флюсы, применяемые для сварки конструкций, должны соответствовать ГОСТ 9087.
10.2.4 Для дуговой сварки в защитном газе следует применять следующие виды газов:
- двуокись углерода по ГОСТ 8050;
- аргон по ГОСТ 10157;
- газовые смеси (СО2 + О2, Аг + СО2, Аг + О2 Аг + СО2 + О2) по техническим условиям.
10.2.5 Газы, применяемые при резке сталей, должны соответствовать:
- кислород газообразный — ГОСТ 5583;
- кислород жидкий — ГОСТ 6331;
- ацетилен — ГОСТ 5457.
10.3 Требования к материалам для амортизирующих элементов
Для изготовления амортизирующих элементов, прокладок (виброизолирующих и уплотнительных) следует применять резины, обладающие регламентированными свойствами в соответствии с таблицами Д.1 и Д.2 (приложение Д).
По таблицам Д.1 и Д.2 проводят оценку работоспособности резиновых деталей по допускаемым напряжениям.
Приложение А (обязательное)
Условия нагружения путеочистителя при расчете на прочность
Конструкция путеочистителя и узлы его крепления подлежат расчету на прочность при поочередном действии центральной и боковой продольной (см. рисунок А.1) статических нагрузок, значения которых указаны в таблице А.1. Схемы приложения нагрузок приведены на рисунке А.1.
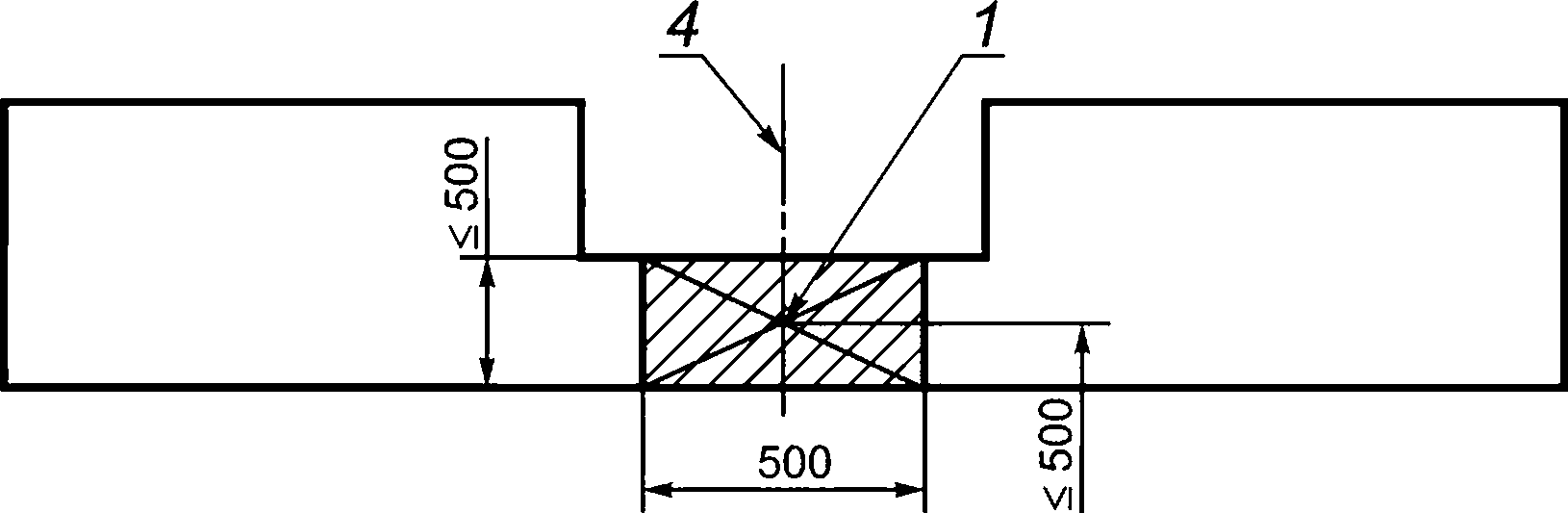
а — Центральная продольная нагрузка
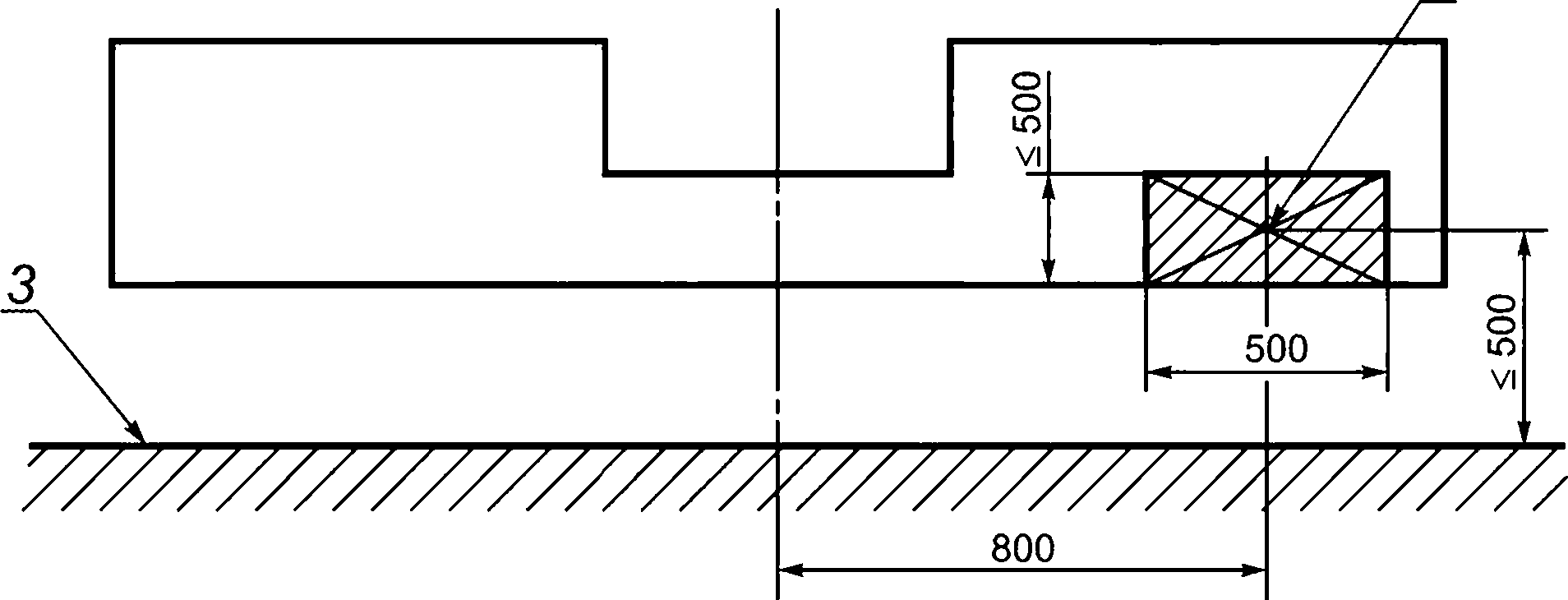
б — Боковая продольная нагрузка (по линии, расположенной над рельсом)
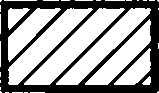
нагружаемая зона < 0,25 м2
1 — центральная продольная нагрузка; 2 — боковая продольная нагрузка (одинаковая для обеих сторон от продольной оси);
3 — уровень головки рельса; 4 — зазор под сцепку (при наличии)
Рисунок А.1 — Схема нагружения путеочистителя (вид на путеочиститель спереди)
Таблица А.1 — Значения нагрузок, прикладываемых к путеочистителю
В килоньютонах
Наименование нагрузки | Значение нагрузки при конструкционной скорости, км/ч | ||||
> 160 | 140 | 120 | 100 | <80 | |
Центральная продольная | 300 | 240 | 180 | 120 | 60 |
Боковая продольная | 250 | 200 | 150 | 100 | 50 |
Примечание — Для конструкционных скоростей, значения которых отличаются от указанных, значения нагрузки определяют путем линейной интерполяции. |
Приложение Б (обязательное)
Экспериментальный метод определения корректирующего коэффициента для сварных конструкций из стального проката
Б.1 Для определения корректирующего коэффициента К3, используемого при вычислениях коэффициентов запаса сопротивления усталости сварных конструкций из стального проката, изготавливают серию типовых сварных образцов, проводят стендовые вибрационные испытания и, основываясь на их результатах, вычисляют корректирующий коэффициент К3 по формуле
0-1 аК(СтЗсп5) 3 -----.
(Б.1)
°-1(СтЗсп5)
где о_1 — среднее значение предела выносливости стандартного образца из применяемой стали при изгибе с симметричным циклом нагружения;
oR — предел выносливости типового сварного образца из применяемой стали, определяемый в результате стендовых вибрационных испытаний при изгибе с асимметричным циклом нагружения с коэффициентом асимметрии R = 0,25;
°Я(СтЗсп5) — предел выносливости типового сварного образца, изготовленного из проката категории 5 по ГОСТ 14637 из стали СтЗсп по ГОСТ 380 при изгибе с асимметричным циклом нагружения с коэффициентом асимметрии R = 0,25;
°-1(СтЗсп5) — предел выносливости стандартного образца, изготовленного из проката категории 5 по ГОСТ 14637 из стали СтЗсп по ГОСТ 380 при изгибе с симметричным циклом нагружения.
Принимают а_1(Ст3сп5) = 195 МПа, с^Ст3сп5| = 90 МПа.
Б.2 Типовой сварной образец (рисунок Б.1) представляет собой полую сварную балку прямоугольного сечения с накладкой прямоугольной формы.
При изготовлении и подготовке образцов к испытаниям необходимо учитывать следующее:
- образцы изготавливают на предприятии, изделия которого подлежат контролю по коэффициентам запаса сопротивления усталости;
- накладку приваривают после изготовления и полного остывания балки;
Рисунок Б.1 — Типовой сварной образец
- не допускается после приварки накладки к горизонтальному листу балки выполнять сглаживающую механическую обработку по границе сплавления шва в месте перехода его на горизонтальный лист балки;
- не допускаются наклеп, аргонодуговая обработка и другие способы упрочняющей или сглаживающей обработки, а также термическая обработка.
Б.З На испытания представляют не менее 10 типовых сварных образцов, изготовленных с учетом требований Б.2.
Б.4 Испытания проводят на стенде, оборудованном счетчиком циклов, по схеме поперечного изгиба балки, лежащей на двух опорах, как показано на рисунке Б.2.
р Граница сварного шва | ||||
|' I I | || I I | I I | I I I | |
Ll | Lv |
I Г
Lj= Lv
Рисунок Б.2 — Схема нагружения типового сварного образца (точка приложения пульсирующей нагрузки Р может быть изменена в зависимости от конструкции стенда)
Б.5 Испытания проводят на базе 107 циклов нагружения.
Коэффициент асимметрии цикла нагружения R устанавливают равным 0,25.
Б.6 При подготовке испытаний для каждого образца задают (с учетом результатов испытаний предыдущих образцов) номинальное максимальное напряжение цикла нагружения отах в сечениях балки I—I и Г—Г в соответствии с рисунком Б.2 и вычисляют номинальное минимальное напряжение цикла omin, МПа, по формуле
$min _ R $тах’
Ориентировочные значения сил Ртах и Pmin , кН, вычисляют по формулам:
р _ $гпах ' Wj-I /г- q\
'max ,
Н
р _ $min ~ ^-1
'min , >
Н
где И/|_| — номинальный момент сопротивления поперечного сечения балки, см3 (И/,_| = 405 см3);
Z-I — номинальное расстояние от точки приложения силы Р до границы лобового шва приварки накладки, мм (см. рисунок Б.1, L| = 378 мм).
Окончательные значения сил Ртах и Pmin , фактически создающие заданные уровни напряженного состояния °тах и °min в сечениях балки I — I и Г— Г, определяют с помощью тензометрирования. Тензорезисторы 1—4 устанавливают по схеме, приведенной на рисунке Б.З, в сечениях балки II — II и II' — II'.
Примечание — Тензорезисторы устанавливают на расстоянии 60 мм от границы лобового сварного шва приварки накладки (сечения балки I — I и Г — I') для исключения влияния на их показания концентратора напряжений на границе лобового шва.
Номинальные напряжения о™ах и Он1"1 в сечении балки II — II (II'— 1Г) вычисляют по формулам:
max _ I /г—
$11 — $max’YJ"» (Е>-5)
_min _. HI /г— /2* \
$11 ~ $min -7_’ (Б.6)
Ч
где отах и Gmjn — номинальные максимальное и минимальное напряжения в сечении I — I (Г — Г), задаваемые для испытаний конкретного образца;
L| и Z_|| — номинальные расстояния отточки приложения силы Рдо сечений I — I и II — II соответственно (L| = 378 мм; £ц = 318 мм).
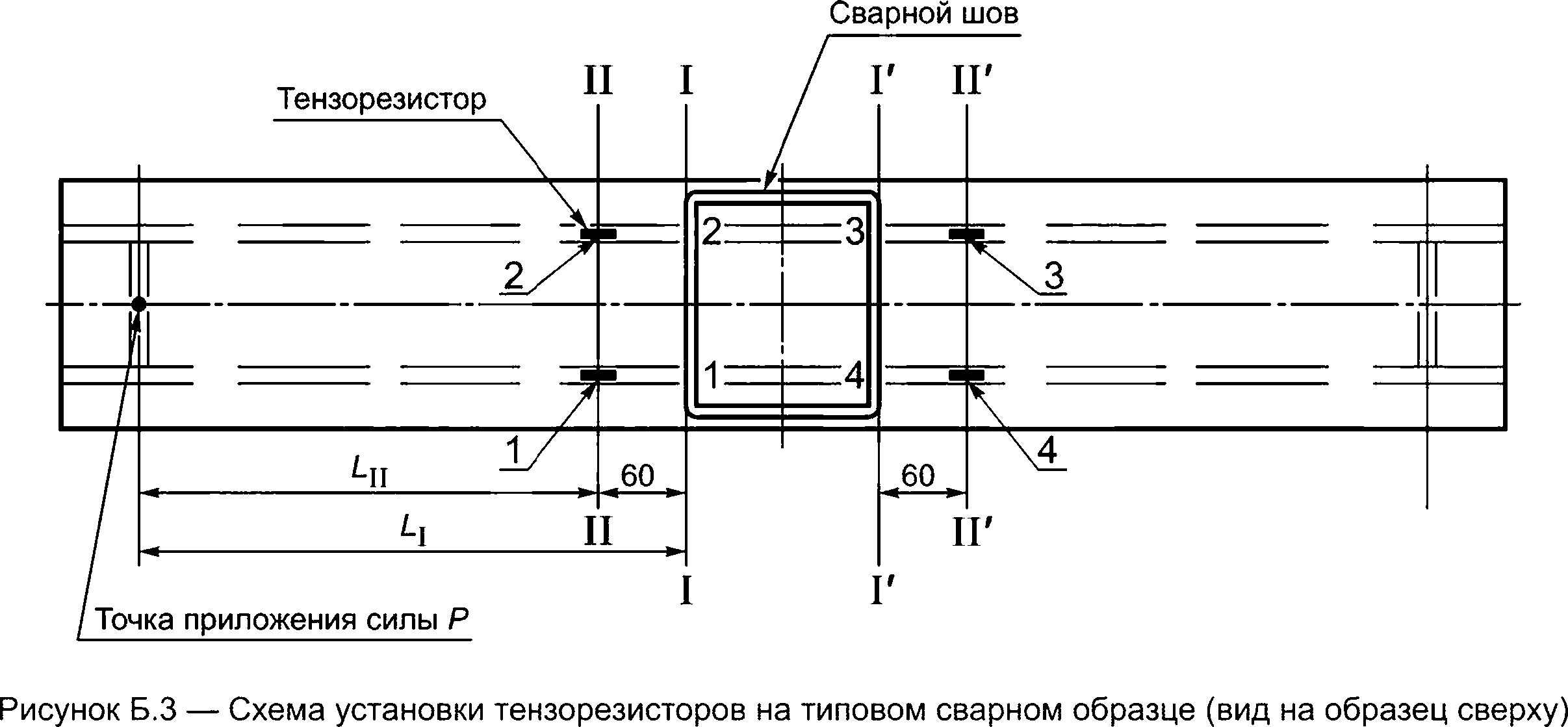
Б.7 Циклическое (вибрационное) нагружение каждого образца осуществляют установленными на стенде силами Ртах и Pmjn, создающими заданный уровень напряженного состояния отах для конкретного образца, подтвержденный показаниями тензорезисторов.
Б.8 Перед началом испытаний каждого образца счетчик циклов обнуляют.
Циклическое нагружение каждого образца осуществляют до достижения базы испытаний, указанной в Б.5, или до момента возникновения усталостной трещины длиной от 5 до 10 мм на границе (см. рисунок Б.2) лобового (поперечного) шва приварки накладки.
Б.9 При возникновении усталостной трещины в ином, чем указано в Б.8, месте испытания данного образца прекращают и результат испытаний данного образца из рассмотрения с целью определения значения oR исключают.
Б. 10 Наличие усталостных трещин определяют методом «керосиновой пробы», который заключается в том, что на поверхность образца в зоне предполагаемого возникновения усталостной трещины при испытаниях наносят кисточкой смесь керосина с маслом в объемном соотношении 3:1. Наличие усталостной трещины характеризуется образованием воздушных пузырьков, наблюдаемых визуально при циклическом нагружении типового сварного образца.
Допускается применение других методов, обеспечивающих обнаружение усталостной трещины длиной от 5 до 10 мм.
Б. 11 Результаты испытаний каждого образца заносят в журнал испытаний.
Б. 12 Пределом выносливости типового сварного образца oR считают значение отах, при котором не менее двух образцов не имеют усталостных трещин в зонах, указанных в Б.8, после достижения базы испытаний, указанной в Б.5. При этом из рассмотрения исключают образцы в соответствии с Б.9.
Приложение В (рекомендуемое)
Пример расчета долговечности
Расчет долговечности (ресурса) выполнен для рамы тележки (челюстного типа) тепловоза М62.
Результирующий блок амплитуд эксплуатационных напряжений для этой рамы представлен в таблице В.1.
Таблица В.1 — Блок нагружения рамы тележки тепловоза М62 (Vmax = 80 км/ч)
оа/, МПа | °а// / сатах | ti | / / \т1 I к /$атах/ | / ✓ \m? \ai/ I к /$атах ) | | ®ai/ | . f. к /Оатах/ | / ✓ \ПЪ (®ai/ | . f. к /оатах7 |
2 | 0,0833 | 0,4132 | 0,000004 | 0 | 0,0000017 | 0 |
4 | 0,1667 | 0,2509 | 0,000129 | 0,0000036 | 0,000032 | 0,0000009 |
6 | 0,2500 | 0,1496 | 0,000193 | 0,0000610 | 0,000029 | 0,0000091 |
8 | 0,3333 | 0,0859 | 0,004098 | 0,0004569 | 0,000353 | 0,0000392 |
10 | 0,4167 | 0,0469 | 0,012564 | 0,0021815 | 0,000589 | 0,0001023 |
12 | 0,5000 | 0,0250 | 0,031250 | 0,0078125 | 0,000780 | 0,0001953 |
14 | 0,5833 | 0,0134 | 0,067524 | 0,0229740 | 0,000905 | 0,0003079 |
16 | 0,6667 | 0,0073 | 0,131720 | 0,0587328 | 0,000962 | 0,0004287 |
18 | 0,7500 | 0,0041 | 0,237305 | 0,1334839 | 0,000973 | 0,0005473 |
20 | 0,8333 | 0,0023 | 0,401797 | 0,2790035 | 0,000924 | 0,0006417 |
22 | 0,9167 | 0,0013 | 0,647346 | 0,5439896 | 0,000842 | 0,0007072 |
24 | 1,0000 | 0,0001 | 1,000000 | 1,0000000 | 0,000100 | 0,0001000 |
Е | — | 1,0000 | — | — | — | — |
Расчет выполнен с использованием уравнения (8.24), т. е. для случая, когда кривая усталости аппроксимирована двумя наклонными прямыми линиями. Параметры кривой усталости приведены в таблице В.2.
Таблица В.2 — Параметры кривой усталости рамы тележки тепловоза М62
Наименование параметра | Обозначение | Значение |
Предел выносливости детали, МПа | а-1Э | 30 |
Коэффициент вариации предела выносливости | $е | 0,12 |
Коэффициент вариации максимального напряжения | 0,1 | |
Показатель степени наклона левой и правой ветвей кривой усталости | Л71 т2 | 5 7 |
Ордината точки перелома кривой усталости | ng | 6-106 |
Коэффициент вариации максимального напряжения принят = 0,1, вероятность разрушения детали р = 0,0001, количество циклов напряжений за 1 год
Л/1год= 2,88 - 106.
Заданной вероятности разрушения р = 0,0001 соответствует значение квантиля Up = - 3,719.
Путем решения уравнения (8.22) вычисляют относительный коэффициент запаса
п = 1,944.
С учетом формулы (8.23) вычисляют значение предельного коэффициента нагруженности
о 24
ло =п п = л- атах =1,944 —= 1,555
Р о_1Э 30
1
и, соответственно, — = 0,643.
Вычисляют значения сумм, стоящих в знаменателе правой части уравнения (8.24):
£ °а/ ,t, =0,0001 + 0,000842 + 0,000924 + 0,000973 + 0,000962 = 0,003801;
оа, 1 ксатах /
$атах
X | | . t. = о, 0003079 + 0,0001953 + 0,0001023 + 0,0000392 + 0,0000091 + 0,0000009 + 0 = 0,0006547.
°а/ 1 К^атах/
°атах
Определяют значение относительной долговечности по уравнению (8.24)
—НХМ =----------------!----------------« 20,43
Ng 1,5555 • 0,003801 +1,5557 • 0,0006547
и срок службы рамы, лет:
Л/сум _ 20,43 /VG 20.43 6 Ю6 126
ГОД ^1 ГОД 2,88 • 1О6
Приложение Г (рекомендуемое)
Пример расчета ресурса буксового роликового радиального подшипника с короткими цилиндрическими роликами типа 30-32532Л1М тепловоза 2ТЭ116
Г.1 Для расчета ресурса подшипника использованы следующие исходные данные:
- подшипник роликовый радиальный с короткими цилиндрическими роликами типа 32532: габаритные размеры 160x290x80 мм; базовая динамическая радиальная расчетная грузоподъемность Сг= 809 кН;
- нагрузка от колесной пары на рельсы Ро = 226 кН;
- сила тяжести неподрессоренных частей, приходящихся на колесную пару, днп = 36 кН;
- диаметр среднеизношенного колеса по кругу катания Окрср = 1,00 м;
- коэффициент безопасности Кб = 1,4;
- рабочая температура подшипника < 100 °C (Кт = 1,0);
- объединенный коэффициент а23 = 0,55;
- количество подшипников на оси колесной пары пг = 4.
Г.2 Радиальную нагрузку на буксовый подшипник Fr кН, вычисляют по формуле (9.8)
Fг=^Ннп=475 ,Г1)
пг
Г.З Динамическую эквивалентную радиальную нагрузку на подшипник Рг, кН, вычисляют по формуле (9.6)
Pr = Fr Kq Кт = 47,5 • 1,4 • 1,0 = 66,5. (Г.2)
Г.4 Расчетный ресурс буксового подшипника L10a, км пробега, вычисляют по формуле (9.2)
а(с V0/3 ^ГвоэУ073 r
^10а = а23яРк103^ I = 0,55-3,14 1,00 103^j ~ 7,1 10е. (Г.З)
Полученное значение расчетного ресурса буксового подшипника L10a > 3 • 106 км, что соответствует 9.4.2.
Приложение Д (обязательное)
Допускаемые показатели прочности резиновых деталей
Таблица Д.1 — Допускаемые напряжения сжатия резиновых деталей
Фактор формы* | Напряжение сжатия, не более, при твердости по Шору (шкала А), МПа | ||||
30 | 40 | 50 | 60 | 70 | |
При статических нагрузках | |||||
0,25 | 0,5 | 0,6 | 0,8 | 1,0 | 1,2 |
0,50 | 0,7 | 0,8 | 1,0 | 1,2 | 1,5 |
0,75 | 0,9 | 1,0 | 1,2 | 1,5 | 1,8 |
1,00 | 1,1 | 1,2 | 1,5 | 1,8 | 2,2 |
1,25 | 1,3 | 1,5 | 1,8 | 2,2 | 2,5 |
1,50 | 1,5 | 1,8 | 2,0 | 2,5 | 2,8 |
При статических нагрузках со случайными и эпизодическими динамическими нагрузками | |||||
0,25 | 0,4 | 0,5 | 0,6 | 0,8 | 1,0 |
0,50 | 0,5 | 0,6 | 0,8 | 1,0 | 1,2 |
0,75 | 0,7 | 0,8 | 1,0 | 1,2 | 1,5 |
1,00 | 0,9 | 1,0 | 1,2 | 1,5 | 1,8 |
1,25 | 1,1 | 1,2 | 1,4 | 1,8 | 2,2 |
1,50 | 1,3 | 1,5 | 1,6 | 2,0 | 2,5 |
При стационарных динамических нагрузках | |||||
0,25 | 0,3 | 0,4 | 0,45 | 0,6 | 0,75 |
0,50 | 0,4 | 0,45 | 0,6 | 0,75 | 0,9 |
0,75 | 0,55 | 0,6 | 0,75 | 0,9 | 1,1 |
1,00 | 0,7 | 0,75 | 0,9 | 1,1 | 1,3 |
1,25 | 0,8 | 0,9 | 1,0 | 1,3 | 1,6 |
1,50 | 1,0 | 1,1 | 1,2 | 1,5 | 2,0 |
* Фактором формы является отношение площади нагружения к площади свободной (боковой) поверхности детали. Примечание — Для промежуточных значений твердости, не указанных в таблице, значение напряжения определяют путем линейной интерполяции табличных данных. |
Таблица Д.2 — Допускаемые напряжения сдвига резиновых деталей
Нагрузки | Напряжение сдвига, не более, при твердости по Шору (шкала А), МПа | |||
40 | 50 | 60 | 70 | |
Статические | 0,20 | 0,30 | 0,40 | 0,50 |
Статические со случайными и эпизодическими кратковременными динамическими | 0,15 | 0,20 | 0,25 | 0,30 |
Стационарные динамические | 0,10 | 0,15 | 0,18 | 0,22 |
Примечание — Для промежуточных значений твердости, не указанных в таблице, значение напряжения определяют путем линейной интерполяции табличных данных.
[1] Технический регламент Таможенного союза ТРТС 001/2011
Библиография
«О безопасности железнодорожного подвижного состава»
УДК 629.4.014.22:006.354
МКС 45.060.10
Ключевые слова: локомотивы, требования к прочности, динамические качества
Редактор Е.Ю. Митрофанова Технический редактор В.Н. Прусакова Корректор Л. С. Лысенко Компьютерная верстка Е.О. Астатина
Сдано в набор 17.02.2023. Подписано в печать 22.02.2023. Формат 60x84%. Гарнитура Ариал. Усл. печ. л. 5,58. Уч.-изд. л. 4,48.
Подготовлено на основе электронной версии, предоставленной разработчиком стандарта
Создано в единичном исполнении в ФГБУ «Институт стандартизации» , 117418 Москва, Нахимовский пр-т, д. 31, к. 2.
1
В Российской Федерации действует ГОСТ Р 27.102—2021 «Надежность в технике. Надежность объекта. Термины и определения».
2
Необходимость определения показателей плавности хода устанавливают в соответствии с национальным законодательством стран, принявших данный стандарт.
3
В Российской Федерации требования к методам определения ресурса приведены в ГОСТ Р 57445—2017 «Железнодорожные технические средства. Общие требования к методам определения ресурса».
4
В Российской Федерации — ГОСТ 26389 «Соединения сварные. Методы испытаний на сопротивляемость образованию горячих трещин при сварке плавлением».
5
" В Российской Федерации — ГОСТ 26388 «Соединения сварные. Методы испытаний на сопротивляемость образованию холодных трещин при сварке плавлением».