ФЕДЕРАЛЬНОЕ АГЕНТСТВО
ПО ТЕХНИЧЕСКОМУ РЕГУЛИРОВАНИЮ И МЕТРОЛОГИИ
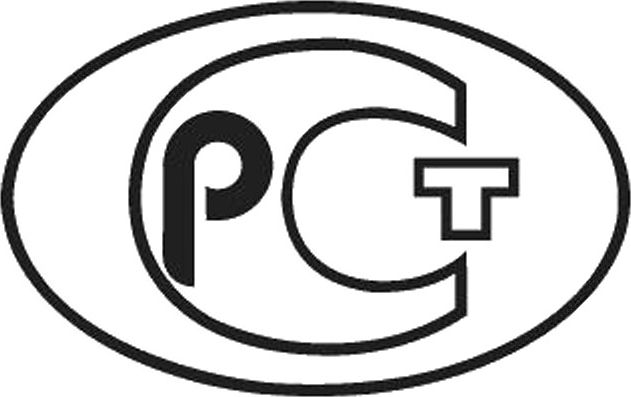
НАЦИОНАЛЬНЫЙ СТАНДАРТ РОССИЙСКОЙ ФЕДЕРАЦИИ
ГОСТ Р
71605-2024
Дороги автомобильные общего пользования
ВАНТОВЫЕ СИСТЕМЫ МОСТОВЫХ СООРУЖЕНИЙ. МАТЕРИАЛЫ И ПОЛУФАБРИКАТЫ
Общие технические условия
Издание официальное
Москва Российский институт стандартизации 2024
ГОСТ Р 71605—2024
Предисловие
1 РАЗРАБОТАН Обществом с ограниченной ответственностью «Мастерская Мостов» (ООО «Мастерская Мостов») совместно с Государственной компанией «Российские автомобильные дороги» (ГК «Автодор»), Обществом с ограниченной ответственностью «СТС» (ООО «СТС»), Открытым акционерным обществом «Северсталь-Метиз» (ОАО «Северсталь-Метиз»), Обществом с ограниченной ответственностью «Газпромнефть — Битумные материалы» (ООО «Газпромнефть — БМ»), Обществом с ограниченной ответственностью «Газпромнефть — смазочные материалы» (ООО «Газпромнефть — СМ»), Обществом с ограниченной ответственностью «СИБУР» (ООО «СИБУР»)
2 ВНЕСЕН Техническим комитетом по стандартизации ТК 418 «Дорожное хозяйство»
3 УТВЕРЖДЕН И ВВЕДЕН В ДЕЙСТВИЕ Приказом Федерального агентства по техническому регулированию и метрологии от 7 октября 2024 г. № 1393-ст
4 ВВЕДЕН ВПЕРВЫЕ
Правила применения настоящего стандарта установлены в статье 26 Федерального закона от 29 июня 2015 г. № 162-ФЗ «О стандартизации в Российской Федерации». Информация об изменениях к настоящему стандарту публикуется в ежегодном (по состоянию на 1 января текущего года) информационном указателе «Национальные стандарты», а официальный текст изменений и поправок — в ежемесячном информационном указателе «Национальные стандарты». В случае пересмотра (замены) или отмены настоящего стандарта соответствующее уведомление будет опубликовано в ближайшем выпуске ежемесячного информационного указателя «Национальные стандарты». Соответствующая информация, уведомление и тексты размещаются в информационной системе общего пользования — на официальном сайте Федерального агентства по техническому регулированию и метрологии в сети Интернет (www.rst.gov.ru)
© Оформление. ФГБУ «Институт стандартизации», 2024
Настоящий стандарт не может быть полностью или частично воспроизведен, тиражирован и распространен в качестве официального издания без разрешения Федерального агентства по техническому регулированию и метрологии
II
ГОСТ Р 71605—2024
Содержание
1 Область применения..................................................................1
2 Нормативные ссылки..................................................................1
3 Термины, определения, обозначения и сокращения........................................3
3.1 Термины и определения............................................................3
3.2 Обозначения и сокращения.........................................................5
4 Классификация материалов и полуфабрикатов вантовых систем.............................5
5 Технические требования...............................................................5
5.1 Технические требования к материалам и полуфабрикатам вант типа 1.....................5
5.2 Технические требования к материалам и полуфабрикатам вант типа 2....................10
6 Требования безопасности.............................................................17
7 Правила приемки....................................................................18
7.1 Правила приемки материалов и полуфабрикатов вант типа 1............................18
7.2 Правила приемки материалов и полуфабрикатов вант типа 2............................20
8 Методы контроля....................................................................27
9 Транспортирование и хранение........................................................28
9.1 Транспортирование и хранение материалов и полуфабрикатов вант типа 1................28
9.2 Транспортирование и хранение материалов и полуфабрикатов вант типа 2................28
10 Гарантии изготовителя..............................................................28
Библиография........................................................................29
III
ГОСТ Р 71605—2024
НАЦИОНАЛЬНЫЙ СТАНДАРТ РОССИЙСКОЙ ФЕДЕРАЦИИ
Дороги автомобильные общего пользования ВАНТОВЫЕ СИСТЕМЫ МОСТОВЫХ СООРУЖЕНИЙ. МАТЕРИАЛЫ И ПОЛУФАБРИКАТЫ
Общие технические условия
Automobile roads of general use. Cable-stayed systems of bridge structures. Materials and semi-finished products. General specifications
Дата введения — 2024—12—01
1 Область применения
Настоящий стандарт распространяется на материалы и полуфабрикаты, использующиеся при производстве вантовых систем типа 1 из закрытых канатов и вантовых систем типа 2 из параллельных прядей для автодорожных и пешеходных мостовых сооружений, расположенных на автомобильных дорогах общего пользования (далее — автомобильные дороги), в том числе при прохождении автомобильных дорог общего пользования по территории населенных пунктов.
Настоящий стандарт не распространяется на материалы и полуфабрикаты, использующиеся при производстве вантовых систем из параллельных и полупараллельных проволок, жестких стержней.
Настоящий стандарт не распространяется на технологию производства материалов и полуфабрикатов, использующихся при производстве вантовых систем.
Материалы и полуфабрикаты, использующиеся при производстве вантовых систем, предназначены для применения в мостовых сооружениях со средней температурой наружного воздуха наиболее холодной пятидневки в районе строительства до минус 40 °C включительно с обеспеченностью 0,98 по СП 35.13330 и температурой теплого времени года до плюс 60 °C, при относительной влажности от 20 % до 100 %.
При температурах ниже минус 40 °C и выше плюс 60 °C требуется научно-техническое обоснование применяемых материалов и полуфабрикатов или стандарты организации на эти материалы и полуфабрикаты, зарегистрированные в Федеральном информационном фонде стандартов в порядке, установленном законодательством Российской Федерации о стандартах.
2 Нормативные ссылки
В настоящем стандарте использованы нормативные ссылки на следующие документы:
ГОСТ 9.054—75 Единая система защиты от коррозии и старения. Консервационные масла, смазки и ингибированные пленкообразующие нефтяные составы. Методы ускоренных испытаний защитной способности
ГОСТ 9.708—83 Единая система защиты от коррозии и старения. Пластмассы. Методы испыта
ний на старение при воздействии естественных и искусственных климатических факторов
ГОСТ 166 (ИСО 3599—76) Штангенциркули. Технические условия
ГОСТ 982 Масла трансформаторные. Технические условия
ГОСТ 1497 Металлы. Методы испытаний на растяжение
ГОСТ 1510 Нефть и нефтепродукты. Маркировка, упаковка, транспортирование и хранение
ГОСТ 2517 Нефть и нефтепродукты. Методы отбора проб
ГОСТ 3241 Канаты стальные. Технические условия
ГОСТ 4255 Нефтепродукты. Метод определения температуры плавления по Жукову
Издание официальное
1
ГОСТ Р 71605—2024
ГОСТ 4333 (ISO 2592:2017) Нефтепродукты. Методы определения температур вспышки и воспламенения в открытом тигле
ГОСТ 4648 (ISO 178:2010) Пластмассы. Метод испытания на статический изгиб
ГОСТ 5346 Смазки пластичные. Методы определения пенетрации пенетрометром с конусом
ГОСТ 6507 Микрометры. Технические условия
ГОСТ 6793 Нефтепродукты. Метод определения температуры каплепадения
ГОСТ 8773—2022 Смазка Циатим-203. Технические условия
ГОСТ 10446 (ИСО 6892—84) Проволока. Метод испытания на растяжение
ГОСТ 10447 Проволока. Метод испытания на навивание
ГОСТ 11262 (ISO 527-2:2012) Пластмассы. Метод испытания на растяжение
ГОСТ 11358 Толщиномеры и стенкомеры индикаторные с ценой деления 0,01 и 0,1 мм. Техниче
ские условия
ГОСТ 11645 Пластмассы. Метод определения показателя текучести расплава термопластов
ГОСТ 12004 Сталь арматурная. Методы испытания на растяжение
ГОСТ 12020 (ISO 175:2010) Пластмассы. Методы определения стойкости к действию химических сред
ГОСТ 15139 Пластмассы. Методы определения плотности (объемной массы)
ГОСТ 15150—69 Машины, приборы и другие технические изделия. Исполнения для различных климатических районов. Категории, условия эксплуатации, хранения и транспортирования в части воз
действия климатических факторов внешней среды
ГОСТ 15173 Пластмассы. Метод определения среднего коэффициента линейного теплового расширения
ГОСТ 16338 Полиэтилен низкого давления. Технические условия
ГОСТ 18899 Канаты стальные. Канаты закрытые несущие. Технические условия
ГОСТ 23683—2021 Парафины нефтяные твердые. Технические условия
ГОСТ 25271 (ИСО 2555—89) Пластмассы, смолы жидкие, эмульсии или дисперсии. Определе
ние кажущейся вязкости по Брукфильду
ГОСТ 26311 | Полиолефины. Метод определения сажи |
ГОСТ 31939 | Материалы лакокрасочные. Определение массовой доли нелетучих веществ |
ГОСТ 32335 | Смазки пластичные. Определение коррозионного воздействия на медную пластинку |
ГОСТ 32394 | Смазки пластичные. Метод определения температуры каплепадения |
ГОСТ 33307 | Смазки пластичные. Отделение масла при повышенных температурах (метод кони- |
ческого сита)
ГОСТ EN 12385-1 Канаты проволочные стальные безопасность. Часть 1. Общие требования
ГОСТ EN 12385-10 Канаты проволочные стальные. Безопасность. Часть 10. Канаты спиральной свивки общего применения
ГОСТ EN 12593 Битум и битуминозные вяжущие. Метод определения температуры хрупкости по Фраасу
ГОСТ EN 13411-4 Концевая заделка стальных канатов. Безопасность. Часть 4. Заливка метал
лом или пластмассами
ГОСТ ISO 105-А02 Материалы текстильные. Определение устойчивости окраски. Часть А02. Серая шкала для оценки изменения окраски
ГОСТ ISO 1817 Резина. Определение стойкости к воздействию жидкостей
ГОСТ ISO 2137 Нефтепродукты. Смазки пластичные и петролатум. Определение пенетрации конусом
ГОСТ ISO 2719 Нефтепродукты и другие жидкости. Определение температуры вспышки. Метод с применением прибора Пенски—Мартенса с закрытым тиглем
ГОСТ ISO 3126—2023 Трубопроводы из пластмасс. Пластмассовые элементы трубопровода. Определение размеров
ГОСТ ISO 3675 Нефть сырая и нефтепродукты жидкие. Лабораторный метод определения плот
ности с использованием ареометра
ГОСТ ISO 10304-1 Качество воды. Определение содержания растворенных анионов методом жидкостной ионообменной хроматографии. Часть 1. Определение содержания бромидов, хлоридов, фторидов, нитратов, нитритов, фосфатов и сульфатов
ГОСТ ISO 11007 Нефтепродукты и смазочные материалы. Определение противокоррозионных свойств консистентных смазок
2
ГОСТ Р 71605—2024
ГОСТ ISO 11922-1—2019 Трубы из термопластов для транспортирования жидких и газообразных сред. Размеры и допуски. Часть 1. Метрическая серия
ГОСТ ISO 12162 Материалы термопластичные для напорных труб и соединительных деталей. Классификация, обозначение и коэффициент запаса прочности
ГОСТ ISO 18553 Трубы, фитинги и композиции из полиолефинов. Метод оценки степени распре
деления пигмента или технического углерода
ГОСТ Р 53772 Канаты стальные арматурные семипроволочные стабилизированные. Технические условия
ГОСТ Р 55971 Нефть и нефтепродукты. Паспорт. Общие требования
ГОСТ Р 56756 (ИСО 11357-6:2008) Пластмассы. Дифференциальная сканирующая калориметрия (ДСК). Часть 6. Определение времени окислительной индукции (изотермическое ВОИ) и температуры окислительной индукции (динамическая ТОЙ)
ГОСТ Р 58078 (EN 10244-2:2009) Проволока стальная и изделия из нее. Покрытия из цветных металлов на стальной проволоке. Покрытия из цинка и цинковых сплавов
ГОСТ Р 58134—2018 (EN 10264-3:2012) Проволока стальная и изделия из нее. Проволока стальная канатная. Проволока круглая и фасонная из нелегированной стали для эксплуатации в тяже
лых условиях
ГОСТ Р 58386—2019 Канаты, защищенные в оболочке для предварительно напряженных конструкций. Технические условия
ГОСТ Р 59953 Материалы лакокрасочные. Цветовой ассортимент. Нормирование цвета. Образцы цвета. Изготовление, учет и хранение
ГОСТ Р 70628.2—2023 (ИСО 4427-2:2019) Трубопроводы из пластмасс для водоснабжения, дренажа и напорной канализации. Полиэтилен (ПЭ). Часть 2. Трубы
ГОСТ Р 71216 Материалы лакокрасочные. Колориметрия. Измерение цвета. Расчет цветовых различий и индекса метамерии
ГОСТ Р ИСО 13737 Материалы нефтяные смазочные. Определение пенетрации при низкой
температуре
СП 35.13330.2011 «СНиП 2.05.03-84* Мосты и трубы»
Примечание — При пользовании настоящим стандартом целесообразно проверить действие ссылочных стандартов (сводов правил) в информационной системе общего пользования — на официальном сайте Федерального агентства по техническому регулированию и метрологии в сети Интернет или по ежегодному информационному указателю «Национальные стандарты», который опубликован по состоянию на 1 января текущего года, и по выпускам ежемесячного информационного указателя «Национальные стандарты» за текущий год. Если заменен ссылочный документ, на который дана недатированная ссылка, то рекомендуется использовать действующую версию этого документа с учетом всех внесенных в данную версию изменений. Если заменен ссылочный документ, на который дана датированная ссылка, то рекомендуется использовать версию этого документа с указанным выше годом утверждения (принятия). Если после утверждения настоящего стандарта в ссылочный документ, на который дана датированная ссылка, внесено изменение, затрагивающее положение, на которое дана ссылка, то это положение рекомендуется применять без учета данного изменения. Если ссылочный документ отменен без замены, то положение, в котором дана ссылка на него, рекомендуется применять в части, не затрагивающей эту ссылку. Сведения о действии сводов правил целесообразно проверить в Федеральном информационном фонде стандартов.
3 Термины, определения, обозначения и сокращения
3.1 Термины и определения
В настоящем стандарте применены следующие термины с соответствующими определениями: 3.1.1
ванта: Несущий прямолинейный растянутый гибкий элемент моста. [ГОСТ Р 59629—2021, пункт 3.3]
3.1.2
ванта типа 1: Ванта, состоящая из одного главного растянутого элемента в виде закрытого каната.
[ГОСТ Р 59629—2021, пункт 3.4]
3
ГОСТ Р 71605—2024
3.1.3
ванта типа 2: Ванта, состоящая из нескольких главных растянутых элементов в виде параллельных семипроволочных прядей.
[ГОСТ Р 59629—2021, пункт 3.5]
3.1.4
вантовый мост: Мост, у которого балка жесткости поддерживается наклонными канатными элементами, закрепленными на пилоне(ах).
[ГОСТ 33178—2014, пункт 3.25]
3.1.5
вантовая прядь: Стальной семипроволочный стабилизированный арматурный канат, имеющий металлизированное покрытие, защищенный заполнителем и полуприлегающей оболочкой из высокоплотного полиэтилена, используемый в качестве главного растянутого элемента для вант типа 2.
[ГОСТ Р 59629—2021, пункт 3.6]
3.1.6
вантовая система: Совокупность элементов, связывающая другие несущие части строительной конструкции (балку жесткости с аркой или пилоном и т. п.), включающая ванту из гибких прямолинейных несущих растянутых элементов (канатов, прядей и т. п.), анкерные устройства, дополнительные устройства для повышения демпфирования, снижения усталостных, коррозионных и других опасностей.
[ГОСТ Р 59629—2021, пункт 3.7]
3.1.7 вантовая система типа 1: Вантовая система, где в качестве главного растянутого элемента применена ванта типа 1.
3.1.8 вантовая система типа 2: Вантовая система, где в качестве главного растянутого элемента применена ванта типа 2.
3.1.9
главный растянутый элемент: Гибкий несущий элемент (канат, прядь) с конструктивно неделимым на стадии монтажа поперечным сечением, применяемый для формирования ванты.
[ГОСТ Р 59629—2021, пункт 3.13]
3.1.10 защитный парафин: Водостойкий, морозостойкий состав из нефтяных масел, загущенных твердыми углеводородами, предназначенный для защиты проволок прядей от коррозии.
3.1.11 защитная смазка: Водостойкий пластичный защитный состав на основе нефтяных масел, который может содержать присадки и/или ингибиторы коррозии, предназначенный для защиты проволок каната или пряди от коррозии.
3.1.12 зетобразная проволока: Высокопрочная высокоуглеродистая стальная фасонная проволока с поперечным сечением в виде латинской буквы «Z».
3.1.13 индивидуальная защитная оболочка: Пластиковая оболочка вантовой пряди.
3.1.14 закрытый канат: Спиральный канат различного диаметра, не являющийся прядью, изготовленный из проволок круглого и зетобразного сечения, у которого наружный ряд(ы) собран(ы) из зетобразных проволок с плотной упаковкой, образующих цилиндрическую поверхность.
3.1.15 нормативное напряжение разрыва: Значение напряжения разрыва (временное сопротивление, маркировочная группа для закрытых канатов, класс прочности для прядей), указанное в документации на продукцию.
3.1.16 подвеска: Гибкий несущий элемент арочного или висячего моста, передающий усилия с балки жесткости на арку (ферму) или несущий кабель (цепь).
Примечание — В рамках настоящего стандарта к подвескам предъявляются те же требования, что и к вантам, если не оговорено иное.
3.1.17 полиэтилен низкого давления: Полимер высокой плотности, получаемый полимеризацией этилена при низком давлении.
4
ГОСТ Р 71605—2024
3.1.18 полуфабрикат: Продукт, получаемый в результате какого-либо производственного процесса и предназначенный для дальнейших действий с ним или применяемый без манипуляций с ним.
3.1.19 проволока: Высокопрочная высокоуглеродистая стальная проволока, изготовляемая методом волочения проката через ряд волок (фильер).
3.1.20 пучок: Совокупность параллельных вантовых прядей или канатов, объединенных в единый элемент.
3.1.21 фактическое напряжение разрыва: Значение напряжения разрыва каната в целом или пряди, полученное при испытаниях.
3.1.22
экстрадозный мост: Вантовый мост с низкими пилонами, в котором основная часть вертикальных воздействий передается от балки жесткости непосредственно на опоры, минуя ванты.
[ГОСТ 33178—2014, пункт 3.28]
3.2 Обозначения и сокращения
В настоящем стандарте применены следующие обозначения и сокращения:
D — номинальный диаметр каната вант типа 1;
F — площадь поперечного сечения;
d — номинальный диаметр вантовых прядей вант типа 2;
ов — предел прочности при растяжении;
о0 1 — условный предел текучести при удлинении 0,1 %;
ВС — вантовая система;
НТД — нормативно-техническая документация;
ПТР — показатель текучести расплава;
ПЭНД — полиэтилен низкого давления, высокой плотности;
ПЭ — полиэтилен;
УФ — ультрафиолет;
BST — черный стандартный термометр;
MRS — минимальная длительная прочность полиэтилена;
RAL — международная система соответствия цветов.
4 Классификация материалов и полуфабрикатов вантовых систем
Материалы и полуфабрикаты ВС подразделяют:
- на материалы и полуфабрикаты вант типа 1;
- материалы и полуфабрикаты вант типа 2.
Примечание — Настоящий стандарт не распространяется на материалы эпоксидного защитного покрытия проволок вант типов 1 и 2.
5 Технические требования
Материалы и полуфабрикаты ВС следует изготавливать в соответствии с требованиями настоящего стандарта по технологическому регламенту, утвержденному в установленном порядке.
5.1 Технические требования к материалам и полуфабрикатам вант типа 1
5.1.1 Основные характеристики канатов вант типа 1
5.1.1.1 Канаты, из которых изготавливаются ванты типа 1, должны соответствовать требованиям ГОСТ 18899, ГОСТ EN 12385-10 с учетом требований настоящего стандарта и быть изготовлены с применением компонентов, приведенных на рисунке 1.
5.1.1.2 Канаты должны быть нераскручивающимися, по направлению свивки правыми или левыми, по механическим свойствам — марки В, отвечающими требованиям ГОСТ 18899 или ГОСТ EN 12385-10.
5
ГОСТ Р 71605—2024
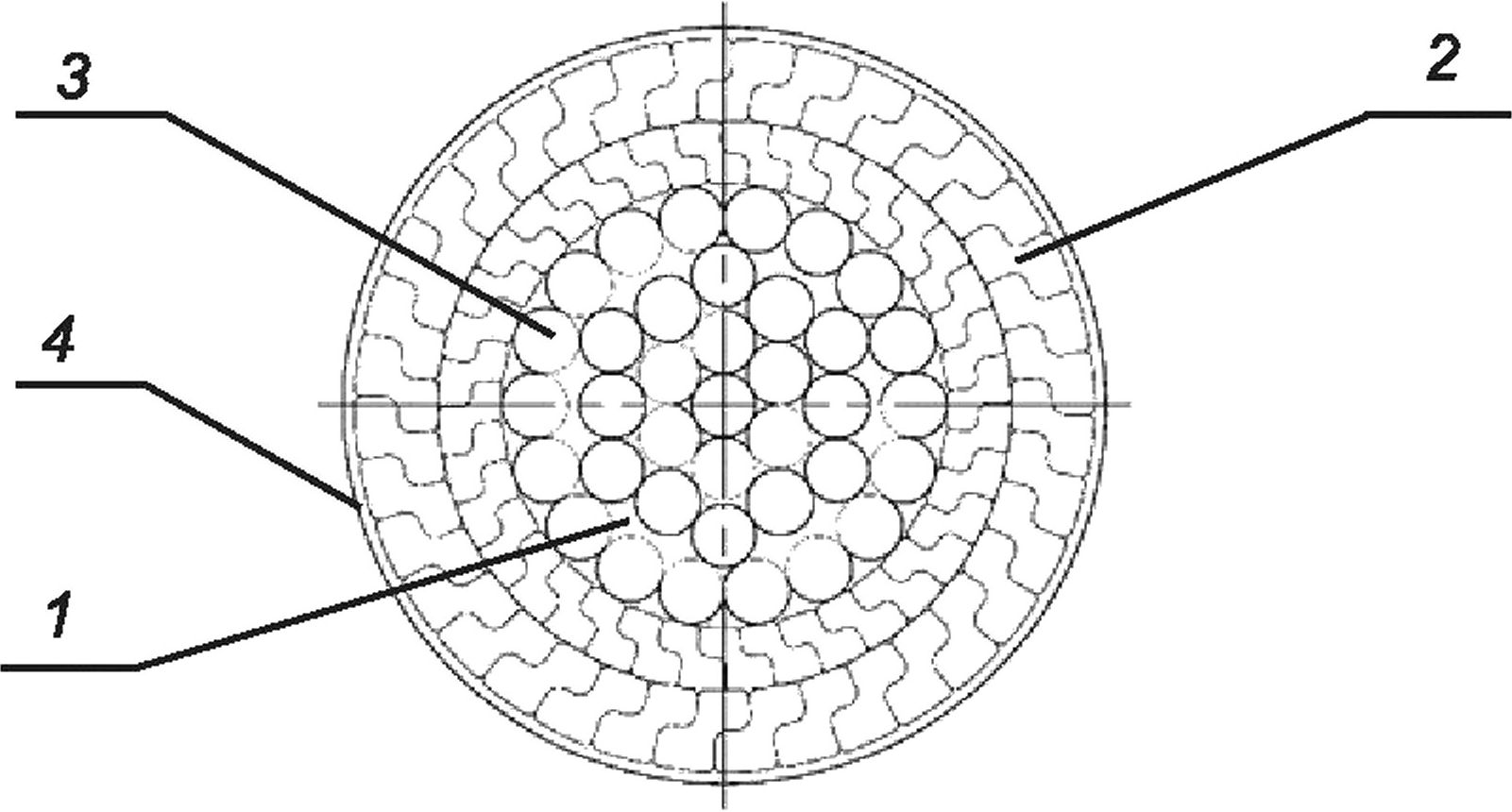
1 — защитная смазка; 2 — зетобразная проволока; 3 — круглая проволока;
4 — оболочка
Рисунок 1 — Сечение ванты типа 1 из закрытых канатов
5.1.1.3 В закрытых канатах для вант типа 1 проволоку круглого сечения применяют для изготовления внутренней части каната. В наружном(ых) слое(ях) каната должна быть использована фасонная проволока зетобразного сечения. Количество слоев круглой и зетобразной проволоки зависит от условий, заявленных заказчиком.
5.1.1.4 Поверхность каната должна быть без следов смазки.
5.1.1.5 Механические и геометрические свойства стальных канатов вант типа 1 должны соответствовать указанным в таблице 1.
Таблица 1 — Свойства стальных канатов вант типа 1
Наименование | Значение (характеристика) показателя | Метод испытаний |
Предел прочности на растяжение круглой проволоки (внутренние слои ванты), Н/мм2, не менее | 1570 | По ГОСТ 10446 |
Предел прочности на растяжение зетобразной проволоки (наружные слои ванты), Н/мм2, не более | 1570 | По ГОСТ 10446 |
Шаг свивки каната, не более | 150 | По ГОСТ 18899 |
Различие шага свивки канатов одного типоразмера, % | ±2 | По ГОСТ 18899 |
Предельные отклонения по диаметру каната D от номинального, %, не более | D^ | По ГОСТ 18899, TOCTEN 12385-1 |
Усталостная прочность1) | Количество циклов: не менее 2 ■ 106. Максимальное напряжение: 45 % фактического разрывного напряжения с размахом, равным 200 МПа и частотой не более 10 Гц | По [1] |
Остаточная прочность на растяжение после испытания на усталость, не менее | 95 % нормативного напряжения разрыва или 92 % фактического напряжения разрыва, в зависимости от того, что больше | По [2] |
Минимальное удлинение образца при растяжении, %, не менее | 1,5 | По ГОСТ 12004 |
1) Опорные поверхности концевых заделок каната повернуты от плоскости, перпендикулярной к оси каната, на 0,6 °(10 мрад) и параллельны, образуя S-образный профиль испытуемого каната. |
6
ГОСТ Р 71605—2024
5.1.2 Требования к материалам канатов вант типа 1
Происхождение проволок должно полностью прослеживаться. Паспорт на проволоку должен содержать следующую информацию:
- обозначение стандарта;
- наименование изготовителя;
- значение нормативного напряжения разрыва (временного сопротивления);
- состояние поверхности;
- номер плавки;
- номер заказа;
- идентификационный номер;
- массу или длину единицы продукции*.
5.1.3 Основные характеристики антикоррозионного покрытия отдельных проволок
5.1.3.1 Проволока круглого и зетобразного сечений, используемая для производства канатов, должна иметь покрытие из цинка или цинкового сплава Zn95AI5 по ГОСТ Р 58078 с учетом требований настоящего стандарта.
5.1.3.2 Физико-механические свойства антикоррозионного металлического покрытия отдельных проволок должны соответствовать указанным в таблице 2.
Таблица 2 — Свойства металлического покрытия отдельных проволок (до свивки в канат) стального каната вант типа 1
Наименование | Значение (характеристика) показателя | Метод испытаний |
Поверхностная плотность покрытия цинком или цинковым сплавом Zn95AI5, г/м2 | 200—350 | По ГОСТ Р 58078 |
Равномерность покрытия | Должно выдержать не менее двух погружений длительностью 1 мин | По ГОСТ Р 58078 |
Прочность сцепления покрытия с основным металлом | Цинковое покрытие при навивке проволоки на оправку должно быть прочным, не должно отслаиваться и растрескиваться | По ГОСТ 104471> |
Внешний вид поверхности покрытия | Гладкое, без наплывов | Визуальный |
1> С учетом требований 8.3. |
Примечания
1 Рекомендуется применение для зетобразных проволок цинкового покрытия из расчета 300 г/м2.
2 Рекомендуется использовать цинковый сплав Zn95AI5 по ГОСТ Р 58078 для покрытия круглой и зетобраз-ной проволоки в качестве основного компонента.
5.1.4 Основные характеристики антикоррозионной защиты внутренней части каната вант типа 1
5.1.4.1 На все слои каната, за исключением двух последних, должна быть наложена водостойкая пластичная алюминий- или цинк-наполненная защитная смазка или ингибитор коррозии, препятствующие проникновению и распространению влаги в канате. Антикоррозионная защита должна заполнять все полости между проволоками смазанных слоев.
5.1.4.2 Физико-химические свойства цинксодержащего ингибитора коррозии должны соответствовать указанным в таблице 3.
Таблица 3 — Свойства ингибитора коррозии
Наименование | Значение показателя | Метод испытаний |
Кажущаяся вязкость по Брукфильду, сП | 10 000 | По ГОСТ 25271 |
Плотность, г/см3, не менее | 1,27 | Указывается производителем |
Сухая масса, %, не менее | 75 |
По требованию заказчика.
7
ГОСТ Р 71605—2024
Окончание таблицы 3
Наименование | Значение показателя | Метод испытаний |
Содержание ингибитора атмосферной коррозии в сухой массе, %, не менее | 47 | Указывается производителем |
Количество цинка в пересчете на сухую массу, %, не менее | 40 | |
Количество смолы в пересчете на сухую массу, %, не менее | 13 | |
Устойчивость к солевому туману, ч, не менее | 500 | По [3] |
Устойчивость к воздействию влаги, ч, не менее | 500 | Указывается производителем |
5.1.4.3 Физико-химические свойства пластичной алюминий-наполненной защитной смазки должны соответствовать указанным в таблице 4.
Таблица 4 — Свойства пластичной защитной смазки
Наименование | Значение (характеристика) показателя | Метод испытаний |
Инфракрасный спектр дисперсной среды | Соответствует контрольному | По [4] |
Рентгенофлуоресцентный спектр без растворителя | Соответствует контрольному | По [5] |
Массовая доля растворителя, %, не более | 35 | По ГОСТ 31939 |
Температура вспышки с применением прибора Пенски — Мартенса в закрытом тигле с растворителем, °C | 23—60 | По ГОСТ ISO 2719 |
Температура хрупкости по Фраасу без растворителя для слоя смазки поверхностной плотностью 75 г/м2, °C, не более | -40 | ПоГОСТ EN 12593 |
Коррозионная защита1) при повышенной относительной влажности и воздействии диоксида серы с периодической конденсацией влаги, после восьми циклов при 40 °C, для слоя смазки поверхностной плотностью 75 г/м2 | Без коррозии | По [6], условие KFW 2,0S |
Коррозионная защита1) в нейтральном соляном тумане 168 ч при (35± 1)°С | Выдерживает | По ГОСТ 9.054 (метод 3) |
Плотность при 15 °C, г/см3, не менее | 1,0 | По ГОСТ ISO 3675 |
Температура каплепадения без растворителя, °C, не менее | 120 | По ГОСТ 32394 |
Отделение масла при 23 °C без растворителя, через 168 ч, без груза, %, не более | 0,5 | По [7] |
1) Образец для испытаний состоит из листовой конструкционной стали 17ГС, 17Г1С или 09Г2С с шероховатостью поверхности, сопоставимой с шероховатостью проволок каната. |
5.1.5 Основные характеристики антикоррозионной защиты наружной части каната вант типа 1
5.1.5.1 Канат вант типа 1 должен иметь наружное антикоррозионное покрытие. В качестве такого покрытия могут выступать внешняя защитная оболочка из полиэтилена низкого давления (полиэтилена высокой плотности), наносимая на канат методом горячей экструзии, или система окрашивания на основе цинка.
5.1.5.2 Выбор системы коррозионной защиты определяется в проекте исходя из агрессивности окружающей среды и ремонтопригодности сооружения (рекомендуется систему окрашивания на основе цинка рассматривать к применению, как альтернативу внешней оболочке, для пешеходных мостов с пролетами не более 90 м и автодорожных мостов с пролетами не более 150 м).
8
ГОСТ Р 71605—2024
5.1.5.3 Физико-механические свойства внешней защитной оболочки должны соответствовать указанным в таблице 5.
Таблица 5 — Свойства внешней защитной оболочки
Наименование | Значение (характеристика) показателя | Метод испытаний | |
ПТР при нагрузке 5 кг при 190 °C, г/10 мин, не более | 1,4 | По ГОСТ 11645 | |
Плотность, г/см3, не менее | 0,94 | По ГОСТ 15139 | |
Содержание сажи1), % | (2,3 ±0,3) | По ГОСТ 26311 | |
Класс распределения сажи1), не более | 3 | ПоГОСТ ISO 18553 | |
Тип распределения сажи1), не хуже | С2 | По ГОСТ ISO 18553 | |
Время окислительной индукции (термостабильность) при 210 °C, мин, не менее | 30 | По ГОСТ Р 56756 | |
Прочность при разрыве (скорость нагружения 50 мм/мин) при 23 °C, МПа, не менее | сырье | 22 | По ГОСТ 112622) |
оболочка | 18 | ||
Относительное удлинение при разрыве (скорость на-гружения 50 мм/мин) при 23 °C, %, не менее | сырье | 600 | По ГОСТ 112622) |
оболочка | 350 | ||
Относительное удлинение при разрыве (скорость на-гружения 50 мм/мин) при минус (20 ± 2) °C, %, не менее | сырье | 150 | По ГОСТ 112622) |
оболочка | 100 | ||
Сопротивление растрескиванию3) под воздействием окружающей среды (при 50 °C появление трещин у 50 % образцов), ч, не менее | 1000 | По [8] | |
Стойкость к УФ-излучению | Указывается производителем ВС | По ГОСТ 9.708—83 (раздел 2, метод 2) | |
Определение снижения механических свойств оболочки после испытаний на стойкость к УФ-излучению: - прочность при разрыве4) при 23 °C; - относительное удлинение5) при разрыве при 23 °C; - относительное удлинение при разрыве при минус (20 ± 2) °C | Указывается производителем ВС | По ГОСТ 112622) |
1) Только для оболочек черного цвета.
2) С учетом требований 8.9.
3) При испытании на растрескивание под воздействием окружающей среды число образцов — не менее 10. Толщина образцов (1,90 ± 0,07) мм. Глубина надреза (0,35 ± 0,05) мм.
4) После 1500 ч испытаний прочность при разрыве не менее 16 МПа.
5) После 1500 ч испытаний относительное удлинение при разрыве не менее 300 %.
5.1.5.4 Стабильность механических свойств и цвета под воздействием УФ должна быть обеспечена в течение срока, указанного в проекте, и быть подтверждена соответствующими испытаниями на ускоренное старение.
Результаты испытаний на стойкость к УФ-излучению и снижению механических свойств оболочки после испытаний на стойкость к УФ-излучению или их отсутствие до 1 января 2029 г. не являются браковочным признаком, их заносят в документ о качестве.
Примечание — При испытаниях по ГОСТ 9.708—83 (раздел 2, метод 2) 1000 ч испытаний соответствуют одному году реального воздействия в условиях средней полосы Российской Федерации.
5.1.5.5 Минимальная толщина внешней защитной оболочки должна быть равна 1/15 наружного диаметра каната, но не менее 3 мм.
9
ГОСТ Р 71605—2024
Поверхность оболочки не должна иметь дефектов или механических повреждений, которые могут локально уменьшить толщину оболочки более чем на 20 %. Оболочка должна плотно прилегать к поверхности каната и быть водонепроницаемой.
5.1.5.6 Оболочки необходимо испытывать на коэффициент аэродинамического сопротивления и на исключение потери аэроупругой устойчивости при совместном действии ветра и дождя.
5.1.5.7 Минимальные требования системы защиты на основе окраски должны включать в себя:
-два грунтовочных слоя на основе полиуретана толщиной не менее 50 мкм каждый с высокодисперсным цинком;
- два финишных слоя на основе полиуретана толщиной не менее 125 мкм каждый с железосодержащей слюдой.
5.1.6 Требования к сырью внешней защитной оболочки
5.1.6.1 Внешнюю защитную оболочку выполняют из ПЭНД высшего сорта по ГОСТ 16338 или аналогичного с минимальной длительной прочностью MRS 10 МПа (композиция ПЭ 100) по ГОСТ ISO 12162.
5.1.6.2 Использование переработанного ПЭНД для изготовления внешних защитных оболочек не допускается.
5.1.7 Основные характеристики материалов для заделок канатов в концевые анкерные устройства вант типа 1
Материалы для заделок канатов в концевые анкерные устройства вант типа 1 должны соответствовать требованиям ГОСТEN 13411-4.
5.1.8 Маркировка полуфабрикатов вант типа 1
5.1.8.1 Для маркировки следует использовать специальные маркировочные краски (эмали), обладающие высокой механической прочностью и адгезией к маркируемым поверхностям, стойкостью во всех климатических условиях и грибостойкостью.
5.1.8.2 Для стальных канатов в составе вант типа 1 к каждому барабану (катушке) должны быть прикреплены два ярлыка из синтетического материала, устойчивые к атмосферным воздействиям. Один закрепляют на конце каната до упаковки, а другой — на внешней стороне барабана (катушки). На ярлыках указывают:
- товарный знак или наименование предприятия-изготовителя;
- наименование объекта, на который осуществляется поставка вант;
- номер ванты по системе нумерации предприятия-изготовителя;
- соответствие ванты НТД проекта;
- номинальный диаметр вант в миллиметрах;
- тип ванты;
- разрывное усилие вант в килоньютонах;
- дату изготовления ванты;
- изображение знака соответствия при обязательной и/или добровольной сертификации.
5.1.9 Упаковка полуфабрикатов вант типа 1
5.1.9.1 Стальные канаты в составе вант типа 1 наматывают на барабан (катушку).
5.1.9.2 Для удержания проволок наружного слоя в свивке минимальный внутренний диаметр барабана (катушки) должен быть не менее чем 45 диаметров канатов.
5.1.9.3 Допускается по условиям транспортирования наматывать канат на барабаны (катушки) с минимальным внутренним диаметром, равным 35 диаметрам каната, при условии обязательной перемотки после транспортирования (с обязательным сохранением положения маркировочной линией каната) на барабаны (катушки) стандартного размера. Хранение на барабанах (катушках) с минимальным внутренним диаметром, равным 35 диаметрам каната, не допускается.
5.2 Технические требования к материалам и полуфабрикатам вант типа 2
5.2.1 Основные характеристики стального каната вантовой пряди
5.2.1.1 Конструкция вантовой пряди показана на рисунке 2.
Конструкция каната должна соответствовать канату типа К7 по ГОСТ Р 53772.
5.2.1.2 Канат для вантовой пряди следует изготавливать из стальной проволоки круглого сечения, покрытой цинком или цинковым сплавом Zn95AI5 по ГОСТ Р 58078. Покрытия на основе эпоксидных компонентов не допускаются. Физико-механические и геометрические свойства стального каната вантовых прядей с защитным покрытием должны соответствовать ГОСТ Р 53772 с учетом свойств, указанных в таблице 6.
10
ГОСТ Р 71605—2024
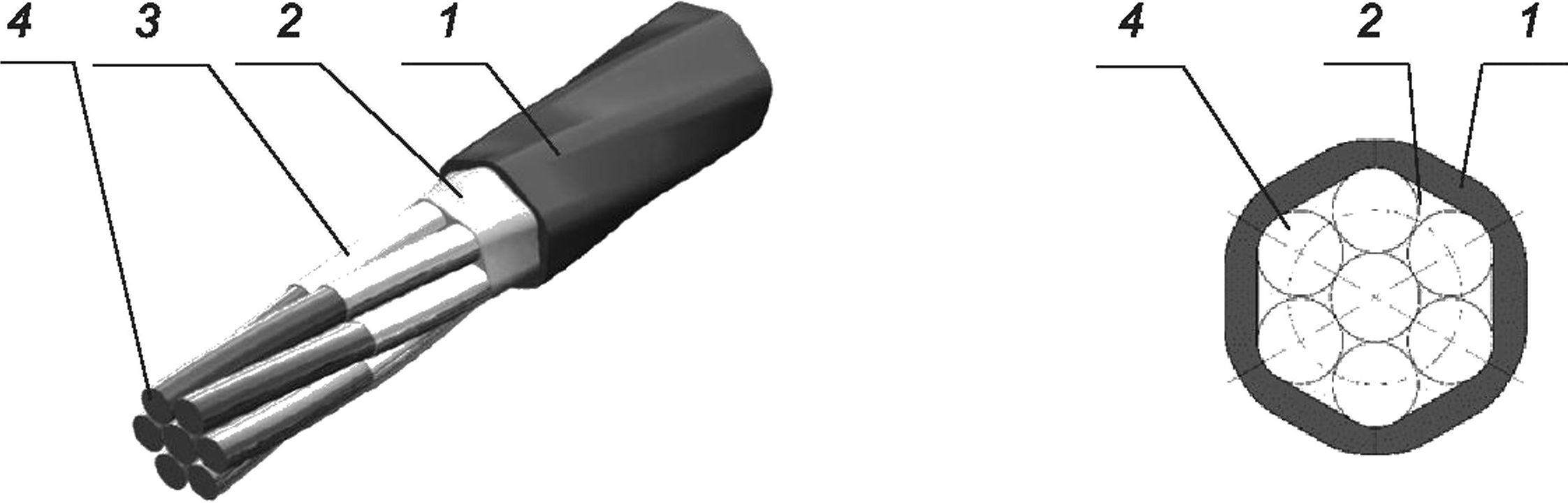
1 — индивидуальная оболочка; 2 — защитная смазка или парафин; 3 — защитное покрытие проволок цинком или цинковым сплавом Zn95AI5; 4 — стальной канат типа К7
Рисунок 2 — Вантовая прядь
Таблица 6 — Свойства стального каната вантовых прядей
Наименование | Значение (характеристика) показателей для канатов номинальным диаметром d | Метод испытаний | ||
15,2 мм | 15,7 мм | |||
Диаметр стального каната, мм | 15 2+0,4 -0,2 | 15 7+0,4 | По ГОСТ Р 53772 | |
Масса 1 пог. м стального каната, г | (1086 ±2) % | (1172 ±2) % | По ГОСТ Р 53772 | |
Площадь поперечного сечения стальной части каната, мм2 | (139 ±2) % | (150 ±2) % | По ГОСТ Р 53772 | |
Шаг свивки каната, мм | (14—18) с/ | По ГОСТ Р 53772 | ||
Предел прочности при растяжении ов (класс проч-ности), Н/мм2, не менее | 1770 | По ГОСТ 12004 | ||
1860 | ||||
Условный предел текучести при растяжении о01, Н/мм2, не менее | 1550 | По ГОСТ 12004 | ||
1650 | ||||
Минимальное разрывное усилие, кН | при ав = 1770 Н/мм2 | 246,0 | 265,5 | По ГОСТ 12004 |
при ов = 1860 Н/мм2 | 258,5 | 279,0 | ||
Максимальное разрывное усилие, кН | при ов = 1770 Н/мм2 | 283,0 | 306,0 | По ГОСТ 12004 |
при ав = 1860 Н/мм2 | 298,0 | 321,0 | ||
Полное относительное удлинение при максимальной нагрузке, %, не менее | 3,5 | По ГОСТ 12004 | ||
Сужение при разрыве, видимое невооруженным глазом, коэффициент сужения, %, не менее | 25 | По ГОСТ 1497, [9] | ||
Модуль упругости, ГПа | (195 ± 10) | По ГОСТ 12004 | ||
Потери напряжения от релаксации при начальном напряжении 70 % от фактического разрывного напряжения после 10001^ ч выдержки под нагрузкой при температуре 20 °C , %, не более | 2,52> | По [9] | ||
Усталостная прочность | Количество циклов: не менее 2 ■ 106. Максимальное напряжение: 45 % фактического разрывного напряжения с размахом, равным 300 МПа и частотой не более 30 Гц | По [9] |
11
ГОСТ Р 71605—2024
Окончание таблицы 6
Наименование | Значение (характеристика) показателей для канатов номинальным диаметром d | Метод испытаний |
15,2 мм 15,7 мм | ||
Остаточная прочность на растяжение после испытания на усталость, не менее | 95 % фактического напряжения разрыва | По ГОСТ 12004 |
Снижение прочности при растяжении с изгибом, %, не более | 20 | По ГОСТ Р 53772 |
1) Допускается проведение испытаний в течение 120 ч с экстраполированием до 1000 ч после первоначального однократного испытания в течение 1000 ч при постановке на производство. 2) Значение применимо для испытаний образцов, взятых сразу после изготовления. |
Вышеприведенные требования также должны быть выполнены после нанесения защитной смазки или защитного парафина и индивидуальной защитной оболочки.
5.2.1.3 Оценка применимости канатов для использования в ВС осуществляется производителем ВС на основе испытаний.
5.2.2 Основные характеристики антикоррозионного покрытия отдельных проволок вантовых прядей вант типа 2
Проволока круглого сечения, используемая для производства вантовых прядей, должна иметь покрытие из цинка или цинкового сплава Zn95AI5 по ГОСТ Р 58078 с учетом требований настоящего стандарта. Физико-механические свойства антикоррозионного металлического покрытия отдельных проволок вантовых прядей должны соответствовать указанным в таблицах 2 и 7.
Таблица 7 — Свойства металлического покрытия отдельных проволок (до свивки в прядь) вантовых прядей вант типа 2
Наименование | Значение показателя | Метод испытаний |
Поверхностная плотность покрытия цинком или цинковым сплавом Zn95AI5, г/м2 | 190—350 | По ГОСТ Р 58078 |
5.2.3 Основные характеристики защитной смазки и защитного парафина вантовых прядей
5.2.3.1 Физико-химические свойства защитной смазки вантовых прядей должны соответствовать указанным в таблице 8.
Таблица 8 — Свойства защитной смазки
Наименование | Значение (характеристика) показателя | Метод испытаний | |
Температура каплепадения, °C, не ниже | 150 | По ГОСТ 6793 | |
Температура вспышки в открытом тигле, °C, не ниже | 250 | По ГОСТ 4333 | |
Пенетрация конуса для смазки, перемешанной при 60 двойных тактах при температуре 25 °C, хЮ-1 мм | 220—300 | По ГОСТ ISO 2137, ГОСТ 5346 | |
Отделение масла при 40 °C, %, не более | через 72 ч | 2,5 | По ГОСТ 33307 |
через 168 ч | 4,5 | ||
Отделение масла через 50 ч при 100 °C, %, не более | 4,0 | ||
Определение устойчивости к окислению при 100 °C, МПа, не более | через 100 ч | 0,06 | По [10] |
через 1000 ч | 0,2 | ||
Противокоррозионные свойства в растворе NaCI (0,5 моль/дм3) | 0(без коррозии) | По ГОСТ ISO 11007 |
12
ГОСТ Р 71605—2024
Окончание таблицы 8
Наименование | Значение (характеристика) показателя | Метод испытаний | |
Коррозионная защита1) в водном тумане в течение 168 ч при (35 ± 1) °C | Выдерживает | По ГОСТ 9.054 (метод 1) | |
Коррозионная защита1) в нейтральном соляном тумане 168 ч при (35± 1)°С | Выдерживает | По ГОСТ 9.054 (метод 3) | |
Содержание агрессивных элементов (анионов), %, не более | - Cl", - S2", - NO3" | 0,005 | Применительно2) к ГОСТ ISO 10304-1 |
- SO42- | 0,010 | ||
1) Образец для испытаний состоит из листовой конструкционной стали 17ГС, 17Г1С или 09Г2С с шероховатостью поверхности, сопоставимой с шероховатостью проволок пряди. Пластина покрыта слоем смазки максимальной толщиной 125 мкм. Нанесение смазки и контроль толщины рекомендуется выполнять по ГОСТ 9.054—75 (приложение 2). 2) Предварительно необходимо подготовить водную фазу (вытяжку) защитной смазки. При (23 ± 2) °C содержание агрессивных элементов (анионов) в защитной смазке 0,005 % соответствует массовой концентрации 50 мг/дм3, 0,010 % соответствует массовой концентрации 100 мг/дм3. |
Результаты испытаний по коррозионной защите в водном тумане или их отсутствие до 1 января 2027 г. не являются браковочным признаком, их заносят в документ о качестве.
Результаты испытаний по коррозионной защите в нейтральном соляном тумане или их отсутствие до 1 января 2027 г. не являются браковочным признаком, их заносят в документ о качестве.
Результаты испытаний по содержанию агрессивных элементов или их отсутствие до 1 января 2029 г. не являются браковочным признаком, их заносят в документ о качестве.
5.2.3.2 Физико-химические свойства защитного парафина вантовых прядей должны соответствовать указанным в таблице 9.
Таблица 9 — Свойства защитного парафина вантовых прядей
Наименование | Значение (характеристика) показателя | Метод испытаний | |
Температура плавления, °C, не ниже | 65 | По ГОСТ 4255 | |
Температура каплепадения, °C, не ниже | 60 | По ГОСТ 6793 | |
Температура вспышки в открытом тигле, °C, не менее | 250 | По ГОСТ 4333 | |
Пенетрация конуса при температуре 25°С, хЮ-1мм, не более | 125 | По ГОСТ ISO 2137 | |
Хладостойкость при минус 40 °C | Выдерживает | По ГОСТ ISO 2137 и ГОСТР ИСО 137371) | |
Отделение масла через 168 ч при 40 °C, %, не более | 1,0 | По ГОСТ 33307 | |
Определение устойчивости к окислению через 100 ч при 100 °C, МПа, не более | 0,03 | По [10] | |
Коррозия медной пластинки 100 ч при 100 °C, класс | 1а | По ГОСТ 32335 | |
Коррозионная защита2) в водном тумане в течение 168 ч при (35 ± 1) °C | Выдерживает | По ГОСТ 9.054 (метод 1) | |
Коррозионная защита2) в нейтральном соляном тумане в течение 168 ч при (35±1)°С | Выдерживает | По ГОСТ 9.054 (метод 3) | |
Содержание агрессивных элементов (анио-нов), %, не более | - СГ - S2", - NO3" | 0,005 | Применительно3) к ГОСТ ISO 10304-1 |
- so42- | 0,010 |
13
ГОСТ Р 71605—2024
Окончание таблицы 9
1) Время кондиционирования образца может быть увеличено до 6 ч и более для достижения необходимой температуры. С дополнением по 8.13.
2) Образец для испытаний состоит из листовой конструкционной стали 17ГС, 17Г1С или 09Г2С с шероховатостью поверхности, сопоставимой с шероховатостью проволок пряди. Пластина покрыта слоем парафина максимальной толщиной 125 мкм. Нанесение парафина и контроль толщины рекомендуется выполнять по ГОСТ 9.054—75 (пункт 3 приложения 2).
3> Предварительно необходимо подготовить водную фазу (вытяжку) защитного парафина. При (23 ± 2) °C содержание агрессивных элементов (анионов) в защитном парафине 0,005 % соответствует массовой концентрации 50 мг/дм3, 0,010 % соответствует массовой концентрации 100 мг/дм3.
Результаты испытаний по коррозионной защите в водном тумане или их отсутствие до 1 января 2027 г. не являются браковочным признаком, их заносят в документ о качестве.
Результаты испытаний по коррозионной защите в нейтральном соляном тумане или их отсутствие до 1 января 2027 г. не являются браковочным признаком, их заносят в документ о качестве.
Результаты испытаний по содержанию агрессивных элементов или их отсутствие до 1 января 2029 г. не являются браковочным признаком, их заносят в документ о качестве.
5.2.4 Основные характеристики индивидуальной оболочки вантовой пряди
5.2.4.1 Индивидуальную оболочку выполняют из ПЭНД высшего сорта по ГОСТ 16338 или по другим нормативным документам, без использования переработанного материала, заполненного сажей или светостабилизирующими добавками. Индивидуальную оболочку изготовляют путем экструзии ПЭНД непосредственно на стальной канат с уже нанесенным защитным заполнителем.
5.2.4.2 Индивидуальная защитная оболочка вантовой пряди должна соответствовать требованиями таблицы 5, за исключением требований к относительному удлинению оболочки при разрыве при 23 °C, сопротивлению растрескиванию под воздействием окружающей среды и стойкости к УФ-излучению.
5.2.4.3 Механические свойства (относительное удлинение) индивидуальной защитной оболочки при разрыве при 23 °C должны соответствовать указанным в таблице 10.
Таблица 10 — Свойства индивидуальной защитной оболочки вантовых прядей вант типа 2
Наименование | Значение показателя | Метод испытаний |
Относительное удлинение оболочки при разрыве (скорость нагружения 50 мм/мин) при 23 °C, %, не менее | 250 | По ГОСТ 112621> |
1) С учетом требований 8.9. |
5.2.5 Основные характеристики готовой вантовой пряди
5.2.5.1 Поверхность оболочки готовой вантовой пряди не должна иметь дефектов или механических повреждений, которые могут локально уменьшить толщину оболочки более чем на 20 %. Оболочка должна быть водонепроницаемой.
5.2.5.2 Физико-механические и геометрические свойства готовой вантовой пряди должны соответствовать указанным в таблице 11.
Таблица 11 — Свойства готовой вантовой пряди
Наименование | Значение (характеристика) показателя | Метод испытаний | |
Масса защитной смазки или парафина на 1 м пряди, г, не менее | 5 | По ГОСТ Р 58386 | |
Диаметр готовой пряди, мм | стальная часть номинальным диаметром 15,2 мм | 18,2—19,4 | По ГОСТ Р 58386 |
стальная часть номинальным диаметром 15,7 мм | 18,7—19,9 | ||
Толщина оболочки, мм, не менее | 1,5 | По 8.6 | |
Масса оболочки на единицу длины, г/м, не менее | 80 | По ГОСТ Р 58386 |
14
ГОСТ Р 71605—2024
Окончание таблицы 11
Наименование | Значение (характеристика) показателя | Метод испытаний |
Прямолинейность1), мм, не более | 25 | По ГОСТ Р 58386 |
Водонепроницаемость2). Увеличение суммарной массы образца и продукта в приемном стакане, г, не более | 0,5 | По ГОСТ Р 58386 |
Начальное сопротивление скольжению между оболочкой и канатом3), Н, не менее | 667 | По ГОСТ Р 58386 |
Устойчивость4) оболочки к ударным нагрузкам | Без отверстий | По ГОСТ Р 58386 |
Устойчивость оболочки к растрескиванию | Отсутствие растрескивания | По ГОСТ Р 58386 |
Устойчивость оболочки к воздействию агрессивной среды (трансформаторное масло, при 23 °C, в течение 168 ч) | Без трещин | По ГОСТ 120205) |
Снижение механических свойств оболочки после испытаний на воздействие агрессивной среды, %, не более: - предел прочности при 23 °C; - относительное удлинение при разрыве при 23 °C; - относительное удлинение при разрыве при минус (20 ± 2) °C | 25 | ГОСТ 11262 |
Изменение объема образца оболочки после испытаний на воздействие агрессивной среды, %, не более | 5 | ГОСТ ISO 1817 |
1) На образце длиной не менее 1,3 м и длине основания сегмента 1 м. 2) Длина образца 1 м, высота водного столба 1 м при выдержке 24 ч. 3) Длина образца с оболочкой 0,3 м. Образец также должен иметь участок каната без оболочки и оболочки без каната для захвата в испытательной машине. 4) Масса молота (1000 ± 1) г, высота падения (30 ± 1) см. 5) С учетом требований 8.12. |
5.2.5.3 Примеры условных обозначений готовых вантовых прядей:
- вантовая прядь номинальным диаметром 15,2 мм класса прочности 1770 Н/мм2
В—К7—15,2—1770 ГОСТ Р 71605—2024
- вантовая прядь номинальным диаметром 15,7 мм класса прочности 1860 Н/мм2
В—К7—15,7—1860 ГОСТ Р 71605—2024
5.2.6 Основные характеристики основной вантовой оболочки
5.2.6.1 Вантовые пряди на свободной длине помещают в основную вантовую оболочку, которая выполняет защитные функции (см. рисунок 3). Основная вантовая оболочка не обязательно должна быть герметичной.
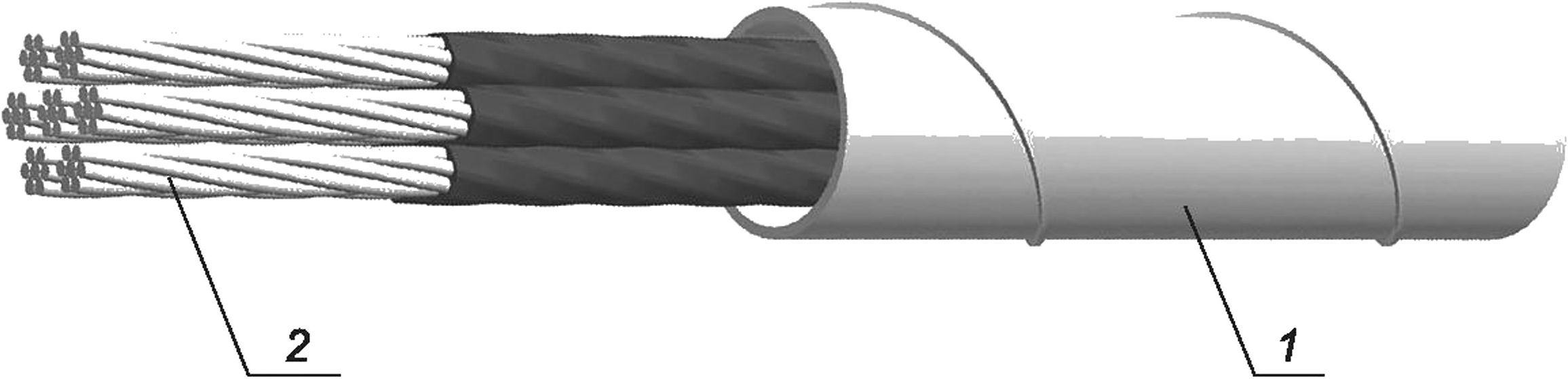
1 — основная вантовая оболочка; 2 — пучок вантовых прядей Рисунок 3 — Общая компоновка ванты типа 2
15
ГОСТ Р 71605—2024
5.2.6.2 Свойства материала основной вантовой оболочки должны удовлетворять следующим требованиям:
- материал, из которого изготовлена основная вантовая оболочка, не должен быть агрессивен к вантовым прядям;
- материал должен быть устойчив к старению и УФ-воздействию;
- материал должен выдерживать возможные механические воздействия, в том числе продольные изгибы, возникающие от сжатия основной вантовой оболочки под собственным весом, включая расчетные нагрузки от обледенения и т. п., при опирании на антивандальную трубу.
5.2.6.3 Основные вантовые оболочки должны быть выполнены из материала ПЭНД высшего сорта по ГОСТ 16338 или аналогичного с минимальной длительной прочностью MRS 8 МПа (композиция ПЭ 80), MRS 10 МПа (композиция ПЭ 100) по ГОСТ ISO 12162.
Использование переработанного ПЭНД для изготовления оболочек не допускается.
Основную вантовую оболочку выполняют методом соэкструзии с черным внутренним слоем и цветным внешним слоем, имеющим высокую сопротивляемость ультрафиолету.
5.2.6.4 Рекомендуемый цвет внешней части основной вантовой оболочки — белый (RAL 9003, 9010, 9016 по ГОСТ Р 59953) ввиду его способности отражать инфракрасное излучение. Допускается использование иных цветов.
5.2.6.5 Вантовая оболочка должна иметь внешние спиралевидные буртики (или иной рельеф) для обеспечения аэроупругой устойчивости при одновременном воздействии дождя и ветра, подтвержденной результатами испытаний. При необходимости или по требованию заказчика должны быть приняты меры по эффективному противодействию обледенению вант.
5.2.6.6 Внутренний диаметр основной вантовой оболочки должен быть достаточным для протягивания вантовых прядей.
5.2.6.7 Овальность основной вантовой оболочки должна соответствовать требованиям ГОСТ ISO 11922-1—2019 (подраздел 4.2, квалитет М).
5.2.6.8 Толщина стенки основной вантовой оболочки должна быть достаточной для стыковой сварки, не менее 5 мм или 1/33 наружного диаметра оболочки (принимают большее значение).
5.2.6.9 Стабильность механических свойств и цвета под воздействием УФ должна быть обеспечена в течение срока, указанного в проекте, и быть подтверждена соответствующими испытаниями на ускоренное старение.
Результаты испытаний или их отсутствие до 1 января 2029 г. не являются браковочным признаком, их заносят в документ о качестве.
Примечание — При испытаниях по ГОСТ 9.708—83 (раздел 2, метод 2) 1000 ч испытаний соответствуют одному году реального воздействия в условиях средней полосы Российской Федерации.
5.2.6.10 Физико-механические свойства основной вантовой оболочки должны соответствовать указанным в таблицах 5 и 12.
Таблица 12 — Свойства основной вантовой оболочки
Наименование | Значение (характеристика) показателя | Метод испытаний | |
Коэффициент теплового расширения | Указывается производителем оболочки | По ГОСТ 15173 | |
Модуль упругости при изгибе при 23 °C, МПа, не менее | сырье | 750 | По ГОСТ 4648 |
оболочка | 600 | ||
Сопротивление растрескиванию под воздействием окружающей среды1) (при 100 °C появление трещин у 20 % образцов), ч, не менее | 600 | По [8]1) |
1) При испытании на растрескивание под воздействием окружающей среды число образцов — не менее 10. Толщина образцов — (1,90 ± 0,07) мм. Глубина надреза — (0,35 ± 0,05) мм.
5.2.7 Маркировка полуфабрикатов вант типа 2
5.2.7.1 Требования к маркировочным краскам (эмалям) приведены в 5.6.1.
16
ГОСТ Р 71605—2024
5.2.7.2 Для полуфабрикатов — вантовых прядей вант типа 2 к каждому барабану (катушке) или мотку вантовых прядей на внешней стороне барабана (катушки) или мотка должен быть прикреплен ярлык, устойчивый к атмосферным воздействиям. На ярлыке указывают:
- товарный знак или наименование предприятия-изготовителя;
- условное обозначение вантовой пряди;
- номер партии;
- длину вантовой пряди на данном барабане (катушке) или мотке;
- порядковый номер барабана (катушки) или мотка;
- массу нетто вантовой пряди;
- массу брутто вантовой пряди;
- номер заказа;
- дату изготовления пряди;
- изображение знака соответствия при обязательной и/или добровольной сертификации.
5.2.7.3 Для полуфабрикатов — основных вантовых оболочек вант типа 2 маркировку наносят на концах отрезков оболочки на поверхность методом цветной печати или другим способом, не ухудшающим качество оболочки. Маркировка должна включать:
- наименование предприятия-изготовителя и/или товарный знак,
- номер партии;
- значение внешнего диаметра оболочки в миллиметрах;
- наименование объекта строительства (при необходимости);
- номер ванты (при необходимости);
- другие сведения, которые изготовитель считает необходимым указать.
Маркировка не должна приводить к ухудшению каких-либо характеристик оболочки и должна быть нестираемой.
При нанесении маркировки методом печати цвет маркировки должен отличаться от цвета внешнего (при наличии) слоя оболочки. Размер шрифта и качество нанесения маркировки должны обеспечивать ее разборчивость без применения увеличительных приборов.
5.2.8 Упаковка полуфабрикатов вант типа 2
5.2.8.1 Вантовые пряди для вант типа 2 наматывают рядной намоткой в моток или на барабан (катушку). Масса нетто прядей — не более 3,5 т. Концы прядей должны быть легко находимы.
5.2.8.2 Внутренний диаметр мотка или барабана (катушки) должен быть не менее шестидесятикратного номинального диаметра каната без оболочки и парафина.
5.2.8.3 Барабаны (катушки) упаковывают сотовым полимерным листом или рулонным упаковочным материалом, который фиксируется полипропиленовой лентой в двух местах. По требованию потребителя деревянный барабан обшивают досками.
5.2.8.4 Мотки обвязывают лентой не менее чем в восьми местах, равномерно расположенных по окружности мотка.
5.2.8.5 По согласованию с заказчиком возможны иные способы упаковки вантовых прядей.
5.2.8.6 Основные вантовые оболочки при диаметре менее 70 мм могут поставляться в бухтах, при этом диаметр бухты должен быть не менее 25 диаметров оболочки. Большие типоразмеры поставляют прямолинейными отрезками от 11,8 до 13,3 м с допуском от минус 0,5 % до 1 % номинальной длины. Отрезки основной вантовой оболочки поставляют в деревянной обрешетке. Бухты и отрезки оболочки индивидуально упаковывают в полиэтилен. По согласованию с потребителем допускаются иные длины отрезков и упаковка.
6 Требования безопасности
6.1 К полиэтилену, из которого изготовляют оболочки канатов вант типа 1, индивидуальные защитные оболочки вантовых прядей и основные вантовые оболочки вант типа 2, предъявляют требования безопасности по ГОСТ Р 70628.2 — 2023 (раздел 15).
6.2 К защитной смазке предъявляют требования безопасности по ГОСТ 8773—2022 (раздел 4).
6.3 К защитному парафину предъявляют требования безопасности по ГОСТ 23683—2021 (раздел 5).
17
ГОСТ Р 71605—2024
7 Правила приемки
7.1 Правила приемки материалов и полуфабрикатов вант типа 1
7.1.1 Приемка стальных канатов
7.1.1.1 Полуфабрикаты вант типа 1 — стальные канаты — принимают партиями, состоящими из канатов, предназначенных для одного объекта строительства.
7.1.1.2 Изготовленные полуфабрикаты вант типа 1 — стальные канаты — принимает служба технического контроля предприятия-изготовителя. Служба технического контроля проверяет соответствие стальных канатов технической документации, по которой изготовлены канаты.
7.1.1.3 Для оценки соответствия стальных канатов требованиям технической документации проводят входной и операционный контроль, а также проводят испытания, подтверждающие характеристики канатов. Испытания проводят для каждого нового объекта применения стальных канатов в вантах типа 1 и каждого диаметра каната в проекте.
7.1.1.4 При входном контроле проверяют соответствие исходного сырья и материалов, применяемых в стальных канатах, требованиям технической документации на сырье и материалы стальных канатов.
7.1.1.5 Операционный контроль проводят при выполнении технологических операций, влияющих на качество изготавливаемых канатов. Порядок и процедуру проведения операционного контроля устанавливает предприятие-изготовитель.
7.1.1.6 Канаты принимают по ГОСТ 18899, ГОСТ EN 12385-1 и ГОСТ EN 12385-10 с учетом требований настоящего стандарта. Периодичность и виды испытаний приведены в ГОСТ 18899 или ГОСТ EN 12385-1.
7.1.1.7 Для достижения стабилизированного модуля упругости канат должен быть предварительно вытянут.
7.1.1.8 Предварительную вытяжку каната выполняют циклическими нагружениями не менее пяти циклов с размахом от 10 % до 50 % нормативного разрывного усилия, пока кривые нагрузка/удлинение для двух последовательных циклов нагружения не совпадут. Диаграмма зависимости удлинения от нагрузки должна регистрироваться соответствующей аппаратурой.
7.1.1.9 После предварительной вытяжки канатов осуществляют расчет модуля упругости. Модуль упругости может быть определен с учетом [11].
7.1.1.10 После предварительной вытяжки по поверхности каждого каната вдоль продольной оси наносят полосу краской. В процессе монтажа ванты (подвески) эта полоса должна быть параллельна оси ванты (подвески). Осевая маркировка не только исключает перекручивание каната, но и идентифицирует проектное положение анкеров, а также исключает их повреждение в процессе монтажа.
7.1.1.11 Разметку каната подлине проводят после предварительной вытяжки. Разметку осуществляют с учетом расчетного модуля упругости размечаемого каната на прямолинейной поверхности в выпрямленном положении.
7.1.1.12 В заказе на поставку вант указывают расчетную длину при температуре, указанной в проекте, и усилиях при эксплуатации мостового сооружения. Задают длину между базами посадочных мест концевых анкерных устройств — осей симметрии пальцев вилок анкеров, торцов цилиндров анкеров или регулировочных гаек.
7.1.1.13 Допускаемое максимальное отклонение подлине ванты, подвергнутой вытяжке, AL, мм, вычисляют по формуле
AL =
л/Г + 5,
(1)
где L — длина ванты по заказу, м.
7.1.1.14 Фактическое разрывное усилие каната в целом определяют на основании результатов испытаний в соответствии с ГОСТ 3241 или ГОСТ EN 12385-10. Испытание считают действительным, если разрывное усилие каната равно или более нормативного разрывного усилия по документации производителя.
7.1.1.15 На усталостную прочность проводят не менее одного испытания для каждого диаметра канатов в проекте при первоначальных (квалификационных) испытаниях. Также испытания проводят при постановке на производство и при изменении технологического процесса. Длина образца каната между зажимами или анкерами — не менее 5 м. После завершения циклов переменного нагружения 18
ГОСТ Р 71605—2024
проводят оценку состояния образца. Испытание на усталость считается успешно пройденным, если выполнены следующие условия:
- оборвалось не более двух проволок, если их общее количество в канате менее 100, или не более 2 % общего количества проволок с округлением до ближайшего большего целого числа, если их общее количество в канате не менее 100;
- после испытания на усталость успешно пройдено испытание на остаточную прочность и минимальное удлинение образца при растяжении (см. таблицу 1).
7.1.2 Приемка защитных заполнителей вант типа 1
7.1.2.1 Приемку цинксодержащего ингибитора коррозии для защиты вант типа 1 проводят по документации производителя.
7.1.2.2 Приемку пластичной алюминий-наполненной защитной смазки для защиты вант типа 1 проводят по документации производителя.
7.1.3 Приемка внешней защитной оболочки вант типа 1
7.1.3.1 Приемку внешней защитной оболочки ванты осуществляют партиями*.
7.1.3.2 Изготовленные внешние защитные оболочки вант типа 1 принимает служба технического контроля предприятия-изготовителя. Служба технического контроля проверяет соответствие внешних защитных оболочек настоящему стандарту.
7.1.3.3 Для оценки соответствия внешних защитных оболочек требованиям настоящего стандарта проводят входной и операционный контроль, а также проводят испытания, подтверждающие характеристики оболочек.
7.1.3.4 При входном контроле проверяют соответствие исходного сырья, применяемого во внешних защитных оболочках, требованиям настоящего стандарта, установленным в таблице 5.
7.1.3.5 Операционный контроль проводят при выполнении технологических операций, влияющих на качество изготавливаемых внешних защитных оболочек. Порядок и процедуру проведения операционного контроля устанавливает предприятие-изготовитель.
7.1.3.6 Для проверки соответствия качества требованиям настоящего стандарта каждая партия внешних защитных оболочек должна проходить приемо-сдаточные испытания по программе, приведенной в таблице 13.
7.1.3.7 Квалификационные испытания внешней защитной оболочки вант типа 1 выполняют при постановке на производство, а также при изменении технологического процесса или исходного сырья и/или материалов. Объем квалификационных испытаний принимают по таблице 13 с учетом приемосдаточных испытаний в количестве трех образцов на каждое испытание.
Таблица 13 — Программа испытаний внешней защитной оболочки вант типа 1 в соответствии с таблицей 5
Наименование | Объем испытаний |
Приемо-сдаточные испытания | |
ПТР | Одно испытание на партию1) сырья, одно испытание на каждый размер оболочки каната в проекте, но не менее одного испытания на партию сырья (на оболочке) |
Плотность | Одно испытание на партию сырья |
Содержание сажи2) | |
Класс распределения сажи2) | |
Тип распределение сажи2) | |
Предел прочности на растяжение | Три испытания на партию сырья, три испытания на каждый размер оболочки в проекте |
Относительное удлинение при разрыве при 23 °C | |
Относительное удлинение при минус 20 °C | |
Время окислительной индукции | Одно испытание на каждый размер оболочки в проекте, но не менее одного испытания на партию сырья (на оболочке) |
Партия соответствует мощности одной произведенной единицы массой не более 30 т.
19
ГОСТ Р 71605—2024
Окончание таблицы 13
Наименование | Объем испытаний |
Квалификационные испытания3) | |
Сопротивление к растрескиванию под воздействием окружающей среды | Десять испытаний образцов из оболочки из одного исходного материала и способа изготовления оболочки |
Стойкость к УФ-излучению | Одно испытание образцов оболочки на каждый цвет, исходный материал и способ изготовления оболочки |
Квалификационные испытания3) | |
Определение снижения механических свойств оболочки после испытаний на стойкость к УФ-излучению: - прочность при разрыве при 23 °C; - относительное удлинение при разрыве при 23 °C; - относительное удлинение при разрыве при минус 20 °C | По пять испытаний образцов из оболочки на каждый цвет, из одного исходного материала и способа изготовления оболочки до и после УФ-излучения |
1) Для партии сырья ПЭНД отбор проб проводят в разных точках партии. 2) Только для оболочек черного цвета. 3) Квалификационные испытания включают в себя и проведение приемо-сдаточных по 7.1.3.7. |
7.1.3.8 При проведении приемо-сдаточных испытаний при получении отрицательного результата одного испытания допускается выполнить два последующих успешных испытания для признания результата испытаний положительным.
7.1.3.9 Документ о качестве на партию материала внешней защитной оболочки оформляют по ГОСТ 16338. Дополнительно он должен содержать даты, номера протоколов, результаты приемо-сдаточных и квалификационных испытаний.
7.1.4 Дополнительные требования к приемке
По согласованию между производителем канатов и заказчиком допускается применение дополнительных требований к приемке материалов и полуфабрикатов для вант типа 1.
7.2 Правила приемки материалов и полуфабрикатов вант типа 2
7.2.1 Приемка вантовых прядей
7.2.1.1 Вантовые пряди принимают партиями* в соответствии с ГОСТ Р 53772 и ГОСТ Р 58386 с учетом требований настоящего стандарта.
7.2.1.2 Изготовленные полуфабрикаты вант типа 2 — вантовые пряди — принимает служба технического контроля предприятия-изготовителя. Служба технического контроля проверяет соответствие вантовых прядей технической документации, по которой изготовлены пряди.
7.2.1.3 Для оценки соответствия вантовых прядей требованиям технической документации проводят входной и операционный контроль, а также проводят испытания, подтверждающие характеристики прядей.
7.2.1.4 При входном контроле проверяют соответствие исходного сырья и материалов, применяемых в вантовых прядях, требованиям технической документации на сырье и материалы вантовых прядей с учетом требований настоящего стандарта.
7.2.1.5 Операционный контроль проводят при выполнении технологических операций, влияющих на качество изготавливаемых вантовых прядей. Порядок и процедуру проведения операционного контроля устанавливает предприятие-изготовитель.
7.2.1.6 С целью контроля соответствия готовой продукции требованиям настоящего стандарта каждая партия вантовой пряди должна проходить приемо-сдаточные испытания по программе, приведенной в таблице 14.
7.2.1.7 С целью контроля стабильности качества продукции и возможности продолжения ее выпуска изготовителем необходимо проводить периодические испытания вантовых прядей по программе, также приведенной в таблице 14.
* Партия — количество, соответствующее одному номеру плавки, массой не более 200 т.
20
ГОСТ Р 71605—2024
7.2.1.8 Первоначальные (квалификационные) испытания вантовых прядей выполняют при постановке на производство, а также при изменении технологического процесса исходного сырья и/или материалов. Объем квалификационных испытаний принимают по перечню приемо-сдаточных и периодических испытаний по таблице 14 в количестве трех образцов на каждое испытание.
Таблица 14 — Программа испытаний вантовых прядей
Наименование | Объем испытаний |
Приемо-сдаточные испытания | |
Стальные части вантовых прядей в соответствии с таблицей 6 | |
Диаметр пряди | Одно испытание от каждого мотка1) |
Площадь сечения пряди | |
Масса стальной части пряди | |
Шаг свивки | |
Предел прочности при растяжении ов | |
Приемо-сдаточные испытания | |
Стальные части вантовых прядей в соответствии с таблицей 6 | |
Минимальное разрывное усилие | Одно испытание от каждого мотка1) |
Полное относительное удлинение при максимальной нагрузке | |
Сужение при разрыве | |
Модуль упругости | |
Потери напряжения от релаксации | Одно испытание на партию, но не менее одного испытания на плавку и не менее одного испытания на каждые 100 т |
Металлическое покрытие проволок пряди в соответствии с таблицами 2 и 7 | |
Поверхностная плотность покрытия | Одно испытание на партию, но не менее одного испы-тания на каждые 20 т стальной части |
Равномерность покрытия | |
Прочность сцепления покрытия с основным металлом | |
Внешний вид поверхности покрытия | |
Готовые вантовые пряди в соответствии с таблицей 11 | |
Масса защитной смазки или парафина на 1 м пряди | Одно испытание от каждого мотка1) |
Диаметр готовой пряди | |
Толщина оболочки | |
Масса оболочки | |
Прямолинейность | |
Водонепроницаемость | Три испытания от партии, но не менее, чем три образца от каждых 100 т, при этом должно выполняться условие, что все образцы отобраны из разных мотков |
Начальное сопротивление скольжению между оболочкой и канатом | |
Устойчивость оболочки к ударным нагрузкам |
21
ГОСТ Р 71605—2024
Окончание таблицы 14
Наименование | Объем испытаний |
Периодические испытания | |
Стальные части вантовых прядей в соответствии с таблицей 6 | |
Усталостная прочность | Два испытания2^ на каждые 100 т, но не реже двух испытаний каждые два года |
Остаточная прочность на растяжение после испытания на усталость | |
Снижение прочности при растяжении с изгибом | Не менее двух испытаний2) на каждые 100 т, не реже одного испытания каждые два года |
Готовые вантовые пряди в соответствии с таблицей 11 | |
Устойчивость оболочки к растрескиванию | Один раз в год на двух образцах, отобранных от производственной партии2) (не более 20 т) |
Устойчивость оболочки к воздействию агрессивной среды | |
Снижение механических свойств оболочки после испытаний на воздействие агрессивной среды: - предел прочности при 23 °C; - относительное удлинение при разрыве при 23 °C; - относительное удлинение при разрыве при минус 20 °C | Два испытания2) от производственной партии один раз В год |
Изменение объема образца оболочки после испытаний на воздействие агрессивной среды | |
1> Единица поставки массой не более 5 т. 2) Один образец должен быть отобран в начале партии, второй — в конце. |
7.2.1.9 При получении отрицательного результата одного испытания (кроме испытаний массы защитной смазки, массы и толщины оболочки, испытания на начальное сопротивление скольжению, испытания на ударные нагрузки и водонепроницаемость) допускается выполнить два последующих успешных испытания для признания результата испытаний положительным.
7.2.1.10 При получении неудовлетворительных результатов при испытаниях массы защитной смазки, массы и толщины оболочки, испытаниях на начальное сопротивление скольжению, испытаниях на ударные нагрузки и водонепроницаемость, результаты испытаний распространяют на весь моток вантовых прядей. Повторные испытания не допускаются.
7.2.1.11 Документ о качестве на каждый барабан (катушку) или моток из партии вантовых прядей должен содержать:
- товарный знак или наименование предприятия-изготовителя;
- условное обозначение вантовой пряди;
- номер партии;
- длину вантовой пряди на данном барабане (катушке) или мотке;
- порядковый номер барабана (катушки) или мотка;
- массу нетто вантовой пряди;
- дату изготовления пряди;
-даты, номера протоколов и результаты приемо-сдаточных, периодических и квалификационных испытаний;
- отметку службы технического контроля.
7.2.2 Приемка защитной смазки
7.2.2.1 Приемку защитной смазки осуществляют партиями*.
7.2.2.2 Изготовленную партию защитной смазки принимает служба технического контроля предприятия-изготовителя. Служба технического контроля проверяет соответствие защитной смазки технической документации, по которой изготовлена смазка.
* Партия — однородное по физико-химическим показателям количество продукта, изготовленного по одному технологическому регламенту, одной рецептуре за один производственный цикл.
22
ГОСТ Р 71605—2024
7.2.2.3 Для оценки соответствия защитной смазки требованиям технической документации проводят входной и операционный контроль, а также проводят испытания, подтверждающие характеристики смазки.
7.2.2.4 При входном контроле проверяют соответствие исходного сырья и материалов, применяемых при изготовлении защитной смазки, технической документации на сырье и материалы.
7.2.2.5 Операционный контроль проводят при выполнении технологических операций, влияющих на качество изготавливаемой защитной смазки. Порядок и процедуру проведения операционного контроля устанавливает предприятие-изготовитель.
7.2.2.6 С целью контроля соответствия готовой продукции требованиям настоящего стандарта каждая партия защитной смазки должна проходить приемо-сдаточные испытания по программе, приведенной в таблице 15.
7.2.2.7 Отбор проб осуществляют в соответствии с ГОСТ 2517.
7.2.2.8 Квалификационные испытания защитной смазки выполняют при постановке на производство, а также при изменении технологического процесса или исходного сырья и/или материалов. Для квалификационных испытаний отбирают три пробы по ГОСТ 2517.
7.2.2.9 Квалификационные испытания проводят согласно таблице 15.
Таблица 15 — Программа испытаний защитной смазки в соответствии с таблицей 8
Наименование | Объем испытаний |
Приемо-сдаточные испытания | |
Температура каплепадения, °C | Одно испытание на партию |
Температура вспышки в открытом тигле, °C | |
Пенетрация конуса при 25 °C | |
Отделение масла при 40 °C | |
Отделение масла при 100 °C | |
Противокоррозионные свойства в растворе NaCI | |
Содержание агрессивных элементов (анионов) | |
Квалификационные испытания1) | |
Определение устойчивости к окислению при 100 °C | Для каждой пробы по 7.2.2.8 |
Коррозионная защита в водном тумане | |
Коррозионная защита в соляном тумане | |
1) Квалификационные испытания включают в себя и проведение приемо-сдаточных для каждой пробы по 7.2.2.8. |
7.2.2.10 При неудовлетворительных результатах приемо-сдаточных испытаний защитной смазки хотя бы по одному показателю проводят испытания пробы, отобранной повторно из той же партии.
Повторные испытания проводят по показателям с неудовлетворительными результатами испытаний или по более широкому перечню показателей по решению предприятия-изготовителя.
При неудовлетворительных результатах повторных испытаний данная партия защитной смазки бракуется и приемке не подлежит.
Результаты повторных испытаний распространяются на всю партию.
7.2.2.11 Результаты квалификационных испытаний оформляют протоколами на каждый образец, информацию о протоколах квалификационных испытаний заносят в документ о качестве.
7.2.2.12 Каждая принятая службами контроля качества предприятия-изготовителя партия защитной смазки должна сопровождаться документом о качестве в соответствии с ГОСТ Р 55971.
7.2.3 Приемка защитного парафина
7.2.3.1 Приемку защитного парафина осуществляют партиями*.
* Партия — однородное по физико-химическим показателям количество продукта, изготовленного по одному технологическому регламенту, одной рецептуре за один производственный цикл.
23
ГОСТ Р 71605—2024
7.2.3.2 Изготовленную партию защитного парафина принимает служба технического контроля предприятия-изготовителя. Служба технического контроля проверяет соответствие защитного парафина технической документации, по которой изготовлен парафин.
7.2.3.3 Для оценки соответствия защитного парафина требованиям технической документации проводят входной и операционный контроль, а также проводят испытания, подтверждающие характеристики парафина.
7.2.3.4 При входном контроле проверяют соответствие исходного сырья и материалов, применяемых при изготовлении защитного парафина, технической документации на сырье и материалы.
7.2.3.5 Операционный контроль проводят при выполнении технологических операций, влияющих на качество изготавливаемого защитного парафина. Порядок и процедуру проведения операционного контроля устанавливает предприятие-изготовитель.
7.2.3.6 С целью контроля соответствия готовой продукции требованиям настоящего стандарта каждая партия парафина должна проходить приемо-сдаточные испытания по программе, приведенной в таблице 16.
7.2.3.7 Отбор проб осуществляют в соответствии с ГОСТ 2517.
7.2.3.8 Квалификационные испытания защитного парафина выполняют при постановке на производство, а также при изменении технологического процесса или исходного сырья и/или материалов. Для квалификационных испытаний отбирается три пробы по ГОСТ 2517.
7.2.3.9 Квалификационные испытания проводят согласно таблице 16.
Таблица 16 — Программа испытаний защитного парафина в соответствии с таблицей 9
Наименование | Объем испытаний |
Приемо-сдаточные испытания | |
Температура плавления, °C | Одно испытание на партию |
Температура каплепадения, °C | |
Температура вспышки в открытом тигле, °C | |
Пенетрация конуса при 25 °C | |
Хладостойкость при минус 40 °C | |
Отделение масла при 40 °C | |
Содержание агрессивных элементов (анионов) | |
Квалификационные испытания1) | |
Определение устойчивости к окислению при 100 °C | Для каждой пробы по 7.2.3.8 |
Коррозия медной пластинки при 100 °C | |
Коррозионная защита в водном тумане | |
Коррозионная защита в соляном тумане | |
1) Квалификационные испытания включают в себя и проведение приемо-сдаточных для каждой пробы по 7.2.3.8. |
7.2.3.10 При неудовлетворительных результатах приемо-сдаточных испытаний защитного парафина хотя бы по одному показателю проводят испытания пробы, отобранной повторно из той же партии.
Повторные испытания проводят по показателям с неудовлетворительными результатами испытаний или по более широкому перечню показателей по решению предприятия-изготовителя.
При неудовлетворительных результатах повторных испытаний данная партия защитного парафина бракуется и приемке не подлежит.
Результаты повторных испытаний распространяются на всю партию.
7.2.3.11 Результаты квалификационных испытаний оформляют протоколами на каждый образец, информацию о протоколах квалификационных испытаний заносят в документ о качестве.
7.2.3.12 Каждая принятая службами контроля качества предприятия-изготовителя партия защитного парафина должна сопровождаться документом о качестве в соответствии с ГОСТ Р 55971.
24
ГОСТ Р 71605—2024
7.2.4 Приемка индивидуальной защитной оболочки вантовой пряди
7.2.4.1 Приемку материала индивидуальной оболочки пряди осуществляют партиями*.
7.2.4.2 Материал индивидуальной оболочки пряди принимает служба технического контроля предприятия-изготовителя. Служба технического контроля проверяет соответствие материала индивидуальной оболочки пряди настоящему стандарту.
7.2.4.3 Для оценки соответствия материала индивидуальной оболочки пряди требованиям настоящего стандарта проводят входной и операционный контроль, а также проводят испытания, подтверждающие характеристики материала.
7.2.4.4 При входном контроле проверяют соответствие исходного сырья, применяемого в индивидуальных оболочках прядей, требованиям настоящего стандарта, установленным в таблице 5.
7.2.4.5 Операционный контроль проводят при выполнении технологических операций, влияющих на качество изготавливаемых индивидуальных оболочек прядей. Порядок и процедуру проведения операционного контроля устанавливает предприятие-изготовитель.
7.2.4.6 С целью контроля соответствия готовой продукции требованиям настоящего стандарта каждая партия материала должна проходить приемо-сдаточные испытания по программе, приведенной в таблице 17.
7.2.4.7 Квалификационные испытания материала индивидуальной защитной оболочки выполняют при постановке на производство, а также при изменении технологического процесса или исходного сырья и/или материалов. Объем квалификационных испытаний принимают по таблице 17 по перечню приемо-сдаточных испытаний в объеме по три образца на каждое испытание.
Таблица 17 — Программа испытаний индивидуальной вантовой оболочки вантовой пряди в соответствии с таблицами 5 и 10
Наименование | Объем испытаний |
Приемо-сдаточные испытания | |
ПТР | Одно испытание на партию1) сырья |
Приемо-сдаточные испытания | |
Плотность | Одно испытание на партию1) сырья |
Содержание сажи2) | |
Класс распределения сажи2) | |
Тип распределение сажи2) | |
Время окислительной индукции (термостабильность) при 210 °C | |
Прочность при разрыве при 23 °C | Одно испытание на партию сырья, три испытания на 10 т материала оболочки |
Относительное удлинение при разрыве при 23 °C | |
Относительное удлинение при разрыве при минус 20 °C | |
1) Для партии сырья ПОНД отбор проб проводят в разных точках партии. 2) Только для оболочек черного цвета. |
7.2.4.8 При получении отрицательного результата одного испытания допускается выполнить два последующих успешных испытания для признания результата испытаний положительным.
7.2.4.9 Документ о качестве на партию материала индивидуальной вантовой оболочки оформляют по ГОСТ 16338. Дополнительно он должен содержать даты, номера протоколов, результаты приемосдаточных и квалификационных испытаний.
7.2.5 Приемка основной вантовой оболочки вант типа 2
7.2.5.1 Приемку основной оболочки ванты осуществляют партиями*.
7.2.5.2 Основные вантовые оболочки принимает служба технического контроля предприятия-изготовителя. Служба технического контроля проверяет соответствие основной вантовой оболочки настоящему стандарту.
Партия соответствует мощности одной произведенной единицы массой не более 30 т.
25
ГОСТ Р 71605—2024
7.2.5.3 Для оценки соответствия основной вантовой оболочки требованиям настоящего стандарта проводят входной и операционный контроль, а также проводят испытания, подтверждающие характеристики оболочек.
7.2.5.4 При входном контроле проверяют соответствие исходного сырья, применяемого в основных вантовых оболочках, требованиям, установленным в таблицах 5 и 12.
7.2.5.5 Операционный контроль проводят при выполнении технологических операций, влияющих на качество изготавливаемых основных вантовых оболочек. Порядок и процедуру проведения операционного контроля устанавливает предприятие-изготовитель.
7.2.5.6 С целью контроля соответствия готовой продукции требованиям настоящего стандарта каждая партия основных вантовых оболочек должна проходить приемо-сдаточные испытания по программе, приведенной в таблице 18.
7.2.5.7 Квалификационные испытания основной вантовой оболочки выполняют при постановке на производство, а также при изменении технологического процесса или исходного сырья и/или материалов. Объем квалификационных испытаний принимают по таблице 18 с учетом приемо-сдаточных испытаний в количестве трех образцов на каждое испытание.
Таблица 18 — Программа испытаний внешней вантовой оболочки вант типа 2 в соответствии с таблицами 5 и 12, а также 5.2.6
Наименование | Объем испытаний |
Приемо-сдаточные испытания | |
Внешний диаметр | Три образца каждого размера в проекте |
Толщина | |
Овальность | |
ПТР | Одно испытание на партию1) сырья, одно испытание на каждый размер оболочки каната в проекте, но не менее одного испытания на партию сырья (на оболочке) |
Плотность | Одно испытание на партию сырья |
Содержание сажи2) | |
Класс распределения сажи2) | |
Тип распределение сажи2) | |
Предел прочности на растяжение | Три испытания на партию сырья, три испытания на каждый размер оболочки в партии |
Относительное удлинение при разрыве при 23 °C | |
Относительное удлинение при минус 20 °C | |
Модуль упругости при изгибе | |
Время окислительной индукции | Одно испытание на каждый размер оболочки в проекте, но не менее одного испытания на партию сырья (на оболочке) |
Квалификационные испытания3) | |
Коэффициент теплового расширения | Три испытания на образцах из одного исходного материала и способа изготовления оболочки |
Сопротивление к растрескиванию под воздействием окружающей среды | 10 испытаний образцов из оболочки среднего размера из одного исходного материала и способа изготовления оболочки |
Стойкость к УФ-излучению | Одно испытание образца оболочки среднего размера на каждый цвет, исходный материал и способ изготовления оболочки |
26
ГОСТ Р 71605—2024
Окончание таблицы 18
Наименование | Объем испытаний |
Определение снижения механических свойств оболочки после испытаний на стойкость к УФ-излучению: - прочность при разрыве при 23 °C; - относительное удлинение при разрыве при 23 °C; - относительное удлинение при разрыве при минус 20 °C | По пять испытаний образцов из оболочки среднего размера на каждый цвет, из одного исходного материала и способа изготовления оболочки до и после УФ-излучения |
1) Для партии сырья ПЭНД отбор проб проводят в разных точках партии. 2) Только для оболочек черного цвета. 3) Квалификационные испытания включают в себя и проведение приемо-сдаточных по 7.2.5.7. |
7.2.5.8 При проведении приемо-сдаточных испытаний в случае получения отрицательного результата одного испытания допускается выполнить два последующих успешных испытания для признания результата испытаний положительным.
7.2.5.9 Документ о качестве на партию основных вантовых оболочек, кроме данных, указанных в документе о качестве по ГОСТ 16338, также должен содержать даты, номера протоколов, результаты приемо-сдаточных и квалификационных испытаний.
7.2.6 Дополнительные требования к приемке
По согласованию между производителем канатов и заказчиком допускается применение дополнительных требований к приемке материалов и полуфабрикатов для вант типа 2.
8 Методы контроля
8.1 Характеристики, приведенные в таблицах, определяют в соответствии с нормативными документами с учетом требований настоящего стандарта и нижеследующих дополнений.
8.2 Оценку стабильности уровня механических свойств вантовых прядей проводят в соответствии с ГОСТ Р 58386—2019 (пункт 6.7).
8.3 При контроле прочности сцепления покрытия с основным металлом проволок при навивке проволоки на оправку число витков должно быть не менее шести, навивка на стержень диаметром не более 5^ [где с/1—диаметр в миллиметрах круглой проволоки каната или эквивалентный диаметр круга (а) зетобразной проволоки по ГОСТ Р 58134—2018 (пункт 5.2.2)].
8.4 Кажущуюся вязкость по Брукфильду определяют, используя вискозиметр типа А при 20 об/мин.
8.5 Толщину оболочек каната (для вант типа 1) и основной вантовой оболочки (для вант типа 2) измеряют в соответствии с ГОСТ Р 58386—2019 (раздел 7).
8.6 Толщину оболочки вантовой пряди (для вант типа 2) измеряют на образце, длиной не менее 0,5 м в восьми различных точках: в четырех точках на одном конце образца и в четырех точках на другом конце образца в местах с визуально наименьшей толщиной оболочки микрометром по ГОСТ 6507 или штангенциркулем по ГОСТ 166 с ценой деления 0,01 мм, или стенкомером по ГОСТ 11358, или другим измерительным инструментом, обеспечивающим требуемую точность измерения. Толщину оболочки принимают равной среднему значению восьми измерений. Значения измерений округляют до первого десятичного знака.
8.7 Овальность основной вантовой оболочки определяют по ГОСТ ISO 3126—2023 (подраздел 5.4).
8.8 Качество поверхности оболочки вантовых канатов и прядей проверяют в соответствии с ГОСТ Р 58386—2019 (раздел 7).
8.9 При подготовке образцов оболочек из ПЭНД вант типа 2 к механическим испытаниям следует удалять спиральные ребра внутри оболочки, образовавшиеся при нанесении ПЭНД на прядь, для получения одинаковой толщины образца. Определение механических свойств оболочки вант типа 2 проводят на образцах типа 1 по ГОСТ 11262.
8.10 Сопротивление оболочек УФ-излучению определяют при следующих условиях испытаний:
- контроль температуры с помощью стандартного черного термометра (BST);
- экспонирование с использованием фильтров дневного света;
- период воздействия: 102 мин — сухое, 18 мин — распыление воды;
27
ГОСТ Р 71605—2024
- освещенность в диапазоне от 280 до 400 нм (68 ± 2) Вт/м2;
- температура черного цвета (65 ± 3) °C;
- температура камеры (38 ± 3) °C;
- относительная влажность (50 ± 10) %.
Примечание — Для материалов, чувствительных к влажности, рекомендуется использовать (65 ±10) % относительной влажности.
8.11 Изменение цвета после воздействия УФ-излучения определяют визуальным способом по ГОСТ ISO 105-А02 или инструментальным способом по ГОСТ Р 71216.
8.12 Устойчивость оболочек к воздействию агрессивной среды проводят в трансформаторном масле по ГОСТ 982.
8.13 При проведении испытания по ГОСТ Р ИСО 13737 при температуре минус (40,0 ± 0,5) °C для оценки хладостойкости фиксируют наличие либо отсутствие растрескивания образца при погружении в него конуса. Образец считают выдержавшим испытание при отсутствии растрескивания. За результат испытания принимают результат оценки хладостойкости одного образца.
9 Транспортирование и хранение
9.1 Транспортирование и хранение материалов и полуфабрикатов вант типа 1
9.1.1 Материалы и полуфабрикаты вант типа 1 транспортируют и хранят по ГОСТ 1510, ГОСТ 15150—69 (таблица 13, условия 5 или 8) всеми видами транспорта в соответствии с правилами перевозки грузов, действующими на транспорте данного вида.
9.1.2 При транспортировании и хранении каната, намотанного на барабан (катушку), ось последнего должна быть параллельна платформе, на которую установлен барабан (катушка).
9.2 Транспортирование и хранение материалов и полуфабрикатов вант типа 2
9.2.1 Материалы и полуфабрикаты вант типа 2 транспортируют и хранят по ГОСТ 1510, ГОСТ 15150—69 (таблица 13, условия 5) и по ГОСТ Р 58386—2019 (раздел 8).
9.2.2 Хранение основных вантовых оболочек необходимо осуществлять в хорошо дренируемой зоне, с твердым покрытием и приспособленной для хранения ПЭНД оболочек, защищенной от дождя, ветра и УФ-излучения. Высота штабеля при хранении оболочек не должна превышать 12 рядов.
9.2.3 Вантовые пряди поставляют намотанными на деревянные барабаны (катушки) или в мотках на деревянных поддонах, в процессе транспортирования катушки (барабаны) должны быть жестко закреплены. Хранение вантовых прядей, намотанных на барабаны (катушки), допускается в вертикальном положении. При этом поверхность для хранения должна быть твердой, позволяющей использовать манипуляторы. Хранить и перевозить барабаны (катушки) плашмя (на боку) не допускается.
Хранение вантовых прядей, намотанных в мотки, допускается в два яруса, с прокладкой из деревянного настила между ярусами.
10 Гарантии изготовителя
10.1 Изготовитель гарантирует соответствие материалов и полуфабрикатов требованиям настоящего стандарта при соблюдении условий транспортирования, хранения, монтажа и эксплуатации.
10.2 Гарантийный срок хранения канатов вант типа 1 и вантовых прядей вант типа 2—12 мес с момента изготовления.
10.3 Гарантийный срок эксплуатации определяют по согласованию с заказчиком, но не менее 10 лет с момента изготовления.
10.4 Срок службы покрытия канатов на основе окраски вант типа 1 определяют по согласованию с заказчиком, но не менее 15 лет.
10.5 Срок службы канатов вант типа 1 и вантовых прядей вант типа 2 определяют по согласованию с заказчиком, но не менее 100 лет.
28
ГОСТ Р 71605—2024
Библиография | |
[1] ЕН 1993-1-11:2006 | Еврокод 3. Проектирование стальных конструкций. Часть 1-11. Проектирование конструкций с напрягаемыми элементами |
[2] ЕН 1993-1-9:2005 [3] АСТМ В117—19 [4] ДИН 51451:2020 | Еврокод 3. Проектирование стальных конструкций. Часть 1-9. Усталость Стандартный метод испытаний в соленом тумане (FOG) Продукты нефтяные и аналогичные им. Испытания. Общие принципы спектрометрического анализа в области инфракрасного излучения |
[5] ДИН 51001:2003 | Испытание оксидных сырьевых и исходных материалов. Основные принципы анализа методом рентгеновской флуоресценции |
[6] ДИН 50018:2013 [7] ДИН 51817:2014 [8] АСТМ D1693—21 | Испытания в насыщенной атмосфере в присутствии диоксида серы Смазки пластичные. Определение выделения масла при статических условиях Стандартный метод испытаний этиленовых пластиков на растрескивание под воздействием окружающей среды |
[9] ИСО 15630-3:2019 | Сталь для армирования и преднапряжения бетона. Методы испытаний. Часть 3. Сталь для преднапряжения бетона |
[10] АСТМ D942—23 | Стандартный метод испытания для определения стойкости к окислению пластичных смазок с помощью метода кислородного сосуда под давлением |
[11] ИСО 12076:2002 | Стальные канаты. Определение фактического модуля упругости |
29
ГОСТ Р 71605—2024
УДК 624.21.01/.09:625.7/.8:006.3/.8:006.354
ОКС 93.040
Ключевые слова: ванты, материалы, полуфабрикаты, требования
30
Редактор Н.В. Таланова Технический редактор В.Н. Прусакова Корректор О.В. Лазарева Компьютерная верстка Л.А. Круговой
Сдано в набор 08.10.2024. Подписано в печать 29.10.2024. Формат 60x84%. Гарнитура Ариал. Усл. печ. л. 4,19. Уч.-изд. л. 3,32.
Подготовлено на основе электронной версии, предоставленной разработчиком стандарта
Создано в единичном исполнении в ФГБУ «Институт стандартизации» , 117418 Москва, Нахимовский пр-т, д. 31, к. 2.