ФЕДЕРАЛЬНОЕ АГЕНТСТВО ПО ТЕХНИЧЕСКОМУ РЕГУЛИРОВАНИЮ И МЕТРОЛОГИИ
НАЦИОНАЛЬНЫЙ СТАНДАРТ РОССИЙСКОЙ ФЕДЕРАЦИИ
ГОСТ Р
55260.3.2—
2023
Гидроэлектростанции
Часть 3-2
ГИДРОТУРБИНЫ И МЕХАНИЧЕСКАЯ ЧАСТЬ ГЕНЕРАТОРОВ
Методики оценки технического состояния
Издание официальное
Москва Российский институт стандартизации 2023
ГОСТ Р 55260.3.2—2023
Предисловие
1 РАЗРАБОТАН Обществом с ограниченной ответственностью «Центр конструкторско-технологических инноваций» (ООО «ЦКТИ») совместно с публичным акционерным обществом «Федеральная гидрогенерирующая компания — «РусГидро» (ПАО «РусГидро») при участии Ассоциации организаций и работников гидроэнергетики «Гидроэнергетика России» (Ассоциация «Гидроэнергетика России»)
2 ВНЕСЕН Техническим комитетом по стандартизации ТК 016 «Электроэнергетика»
3 УТВЕРЖДЕН И ВВЕДЕН В ДЕЙСТВИЕ Приказом Федерального агентства по техническому регулированию и метрологии от 23 ноября 2023 г. № 1465-ст
4 ВВЕДЕН ВЗАМЕН ГОСТ Р 55260.3.2—2013
Правила применения настоящего стандарта установлены в статье 26 Федерального закона от 29 июня 2015 г. № 162-ФЗ «О стандартизации в Российской Федерации». Информация об изменениях к настоящему стандарту публикуется в ежегодном (по состоянию на 1 января текущего года) информационном указателе «Национальные стандарты», а официальный текст изменений и поправок — в ежемесячном информационном указателе «Национальные стандарты». В случае пересмотра (замены) или отмены настоящего стандарта соответствующее уведомление будет опубликовано в ближайшем выпуске ежемесячного информационного указателя «Национальные стандарты». Соответствующая информация, уведомление и тексты размещаются также в информационной системе общего пользования — на официальном сайте Федерального агентства по техническому регулированию и метрологии в сети Интернет (www.rst.gov.ru)
©Оформление. ФГБУ «Институт стандартизации», 2023
Настоящий стандарт не может быть полностью или частично воспроизведен, тиражирован и распространен в качестве официального издания без разрешения Федерального агентства по техническому регулированию и метрологии
II
ГОСТ Р 55260.3.2—2023
Содержание
1 Область применения..................................................................1
2 Нормативные ссылки..................................................................2
3 Термины, определения и сокращения....................................................4
4 Общие положения....................................................................8
5 Требования к контролю и оценке технического состояния гидротурбин на ГЭС..................12
6 Оценка технического состояния гидротурбины и механической части генератора...............13
Приложение А (обязательное) Методические указания по техническому обследованию узлов
гидроагрегатов при их повреждениях.........................................82
Приложение Б (обязательное) Методики контроля геометрических форм и размеров проточной части гидротурбин.............................................................88
Приложение В (обязательное) Методики контроля состояния металла узлов и элементов гидротурбин
и механической части генератора..........................................104
Приложение Г (справочное) Основные технические данные по ГЭС, гидротурбинному и гидрогенераторному оборудованию.........................................135
Приложение Д (справочное) Методики испытания системы регулирования гидротурбин..........137
Приложение Е (обязательное) Методика контроля линии валов вертикальных гидроагрегатов.....141
Приложение Ж (справочное) Методика контроля состояния подпятников вертикальных гидроагрегатов..........................................................152
Приложение И (обязательное) Методика определения осевой жесткости агрегата...............159
Приложение К (справочное) Методики проведения натурных испытаний гидроагрегата...........161
Библиография.......................................................................170
III
ГОСТ Р 55260.3.2—2023
НАЦИОНАЛЬНЫЙ СТАНДАРТ РОССИЙСКОЙ ФЕДЕРАЦИИ
Гидроэлектростанции
Часть 3-2
ГИДРОТУРБИНЫ И МЕХАНИЧЕСКАЯ ЧАСТЬ ГЕНЕРАТОРОВ
Методики оценки технического состояния
Hydroelectric power plants. Part 3-2. Hydraulic turbines and mechanical part of hydraulic generators.
Condition evaluation procedures
Дата введения — 2024—01—01
1 Область применения
1.1 Настоящий стандарт устанавливает требования к контролю и оценке технического состояния гидротурбин и механической части генераторов на стадии эксплуатации:
- при постоянном контроле и непрерывном автоматизированном мониторинге на работающем гидроагрегате;
- периодических осмотрах и периодическом (измерительном) контроле технического состояния в периоды плановых и внеплановых ремонтов без разборки гидроагрегата и/или на работающем гидроагрегате;
- периодическом техническом диагностировании (обследовании) гидроагрегата в периоды плановых и внеплановых ремонтов с осушением и полной или частичной разборкой гидроагрегата, при реконструкции и/или модернизации.
1.2 Настоящий стандарт определяет методики, которые следует применять при оценке технического состояния гидротурбин и механической части генераторов.
1.3 Настоящий стандарт определяет нормы и объем контроля состояния гидротурбин и механической части генераторов, минимально необходимые для решения следующих задач:
- выявление и своевременное устранение возникающих в процессе эксплуатации повреждений;
- оценка фактического технического состояния, исправности и/или работоспособности контролируемого оборудования;
- определение фактических значений технических параметров для последующего определения индекса технического состояния узлов и оборудования в целом;
- принятие решения о проведении технического освидетельствования для продления срока службы или технических обследований по специальным программам в целях определения индивидуального остаточного ресурса и установления возможности, целесообразности, сроков и условий продолжения безопасной эксплуатации.
1.4 Настоящий стандарт распространяется на гидротурбинные установки с рабочими колесами поворотно-лопастного, пропеллерного, диагонального, радиально-осевого типов, а также обратимые гидроагрегаты в вертикальном исполнении. Отдельные пункты стандарта могут быть распространены на гидроагрегаты в горизонтальном исполнении.
1.5 Настоящий стандарт не устанавливает требований к типам и видам используемых при техническом контроле и мониторинге штатной контрольной аппаратуры и специальных средств измерений.
1.6 Настоящий стандарт не учитывает все возможные особенности реализации его требований на оборудовании с различным конструктивным исполнением.
Издание официальное
1
ГОСТ Р 55260.3.2—2023
2 Нормативные ссылки
В настоящем стандарте использованы нормативные ссылки на следующие стандарты:
ГОСТ 8.398 Государственная система обеспечения единства измерений. Приборы для измерения твердости металлов и сплавов. Методы и средства поверки
ГОСТ 8.417 Государственная система обеспечения единства измерений. Единицы величин
ГОСТ 8.439 Государственная система обеспечения единства измерений. Расход воды в напорных трубопроводах. Методика выполнения измерений методом площадь-скорость
ГОСТ 12.2.003 Система стандартов безопасности труда. Оборудование производственное. Общие требования безопасности
ГОСТ 25.502 Расчеты и испытания на прочность в машиностроении. Методы механических испытаний металлов. Методы испытаний на усталость
ГОСТ 25.506 Расчеты и испытания на прочность. Методы механических испытаний металлов. Определение характеристик трещиностойкости (вязкости разрушения) при статическом нагружении
ГОСТ 32 Масла турбинные. Технические условия
ГОСТ 1497 (ИСО 6892—84) Металлы. Методы испытаний на растяжение
ГОСТ 5616 Генераторы и генераторы-двигатели электрические гидротурбинные. Общие технические условия
ГОСТ 9012 (ИСО 410—82, ИСО 6506—81) Металлы. Метод измерения твердости по Бринеллю
ГОСТ 15467 Управление качеством продукции. Основные понятия. Термины и определения
ГОСТ 16504 Система государственных испытаний продукции. Испытания и контроль качества продукции. Основные термины и определения
ГОСТ 18442 Контроль неразрушающий. Капиллярные методы. Общие требования
ГОСТ 19431 Энергетика и электрификация. Термины и определения
ГОСТ 20911 Техническая диагностика. Термины и определения
ГОСТ 22761 Металлы и сплавы. Метод измерения твердости по Бринеллю переносными твердомерами статического действия
ГОСТ 23956 Турбины гидравлические. Термины и определения
ГОСТ 24346 Вибрация. Термины и определения
ГОСТ 25866 Эксплуатация техники. Термины и определения
ГОСТ 27471 Машины электрические вращающиеся. Термины и определения
ГОСТ 27807 Турбины гидравлические вертикальные. Технические требования и приемка
ГОСТ 28842 (МЭК 41—63, МЭК 607—78) Турбины гидравлические. Методы натурных приемочных испытаний
ГОСТ 33272 Безопасность машин и оборудования. Порядок установления и продления назначенных ресурса, срока службы и срока хранения. Основные положения
ГОСТ ИСО 5348 Вибрация и удар. Механическое крепление акселерометров
ГОСТ ИСО 10817-1 Вибрация. Системы измерений вибрации вращающихся валов. Часть 1. Устройство для снятия сигналов относительной и абсолютной вибрации
ГОСТ ISO 17635 Неразрушающий контроль сварных соединений. Общие правила для металлических материалов
ГОСТ ISO 17638 Неразрушающий контроль сварных соединений. Магнитопорошковый контроль
ГОСТ Р 8.000 Государственная система обеспечения единства измерений. Основные положения
ГОСТ Р 27.102 Надежность в технике. Надежность объекта. Термины и определения
ГОСТ Р 53700 (ИСО 9934-3:2002) Контроль неразрушающий. Магнитопорошковый метод. Часть 3. Оборудование
ГОСТ Р 55260.2.2 Гидроэлектростанции. Часть 2-2. Гидрогенераторы. Методики оценки технического состояния
ГОСТ Р 55260.3.1 Гидроэлектростанции. Гидротурбины. Технические требования к поставке
ГОСТ Р 55260.4.1 Гидроэлектростанции. Часть 4-1. Технологическая часть гидроэлектростанций и гидроаккумулирующих электростанций. Общие технические требования
ГОСТ Р 55562 (МЭК 60609-1:2004) Турбины гидравлические, насос-турбины и насосы гидроаккумулирующих электростанций. Оценка кавитационной эрозии. Часть 1. Оценка в реактивных турбинах, насос-турбинах и насосах гидроаккумулирующих электростанций
ГОСТ Р 55614 Контроль неразрушающий. Толщиномеры ультразвуковые. Общие технические требования
2
ГОСТ Р 55260.3.2—2023
ГОСТ Р 55621 (ЕН 45510-5-4:1998) Руководство по оснащению электростанций оборудованием. Часть 5-4. Турбины — гидравлические турбины, гидроаккумулирующие насосы и насос-турбины (обратимые гидромашины)
ГОСТ Р 55724 Контроль неразрушающий. Соединения сварные. Методы ультразвуковые
ГОСТ Р 55809 Контроль неразрушающий. Дефектоскопы ультразвуковые. Методы измерений основных параметров
ГОСТ Р 55890 Единая энергетическая система и изолированно работающие энергосистемы. Оперативно-диспетчерское управление. Регулирование частоты и перетоков активной мощности. Нормы и требования
ГОСТ Р 56512 Контроль неразрушающий. Магнитопорошковый метод. Типовые технологические процессы
ГОСТ Р 56969 Единая энергетическая система и изолированно работающие энергосистемы. Оперативно-диспетчерское управление. Обеспечение согласованной работы централизованных систем автоматического регулирования частоты и перетоков активной мощности и автоматики управления активной мощностью гидравлических электростанций. Нормы и требования
ГОСТ Р 57114 Единая энергетическая система и изолированно работающие энергосистемы. Электроэнергетические системы. Оперативно-диспетчерское управление в электроэнергетике и оперативно-технологическое управление. Термины и определения
ГОСТ Р 58599 Техническая диагностика. Диагностика стальных конструкций. Магнитный коэрци-тиметрический метод. Общие требования
ГОСТ Р 58779 Единая энергетическая система и изолированно работающие энергосистемы. Эксплуатация. Техническая эксплуатация основного технологического оборудования энергосистем, электрических станций и электрических сетей. Информационно-технический справочник основного технологического оборудования для обеспечения единых принципов построения унифицированных систем оценки, мониторинга и контроля технического состояния оборудования и сооружений, эксплуатируемых на объектах электроэнергетики
ГОСТ Р 70214 Гидротехника. Основные понятия. Термины и определения
ГОСТ Р 70810 Гидроэлектростанции. Гидроагрегаты. Эксплуатационный контроль вибрационного состояния опорных узлов
ГОСТ Р ИСО 2041 Вибрация, удар и контроль технического состояния. Термины и определения
ГОСТ Р ИСО 9712 Контроль неразрушающий. Квалификация и сертификация персонала
ГОСТ Р ИСО 9934-1 Контроль неразрушающий. Магнитопорошковый метод. Часть 1. Основные требования
ГОСТ Р ИСО 9934-2 Контроль неразрушающий. Магнитопорошковый метод. Часть 2. Дефектоскопические материалы
ГОСТ Р ИСО 13373-1 Контроль состояния и диагностика машин. Вибрационный контроль состояния машин. Часть 1. Общие методы
ГОСТ Р ИСО 13373-2 Контроль состояния и диагностика машин. Вибрационный контроль состояния машин. Часть 2. Обработка, анализ и представление результатов измерений вибрации
ГОСТ Р ИСО 13373-3 Контроль состояния и диагностика машин. Вибрационный контроль состояния машин. Часть 3. Руководство по диагностированию по параметрам вибрации
ГОСТ Р ИСО 13381-1 Контроль состояния и диагностика машин. Прогнозирование технического состояния. Часть 1. Общее руководство
ГОСТ Р ИСО 15549 Контроль неразрушающий. Контроль вихретоковый. Основные положения
ГОСТ Р ИСО 16809 Контроль неразрушающий. Контроль ультразвуковой. Измерение толщины
ГОСТ Р ИСО 17637 Контроль неразрушающий. Визуальный контроль соединений, выполненных сваркой плавлением
ГОСТ Р ИСО 17640 Неразрушающий контроль сварных соединений. Ультразвуковой контроль. Технология, уровни контроля и оценки
ГОСТ Р ИСО 20816-1 Вибрация. Измерения вибрации и оценка вибрационного состояния машин. Часть 1. Общее руководство
Примечание — При пользовании настоящим стандартом целесообразно проверить действие ссылочных стандартов в информационной системе общего пользования — на официальном сайте Федерального агентства по техническому регулированию и метрологии в сети Интернет или по ежегодному информационному указателю «Национальные стандарты», который опубликован по состоянию на 1 января текущего года, и по выпускам ежемесячного информационного указателя «Национальные стандарты» за текущий год. Если заменен ссылочный
3
ГОСТ Р 55260.3.2—2023
стандарт, на который дана недатированная ссылка, то рекомендуется использовать действующую версию этого стандарта с учетом всех внесенных в данную версию изменений. Если заменен ссылочный стандарт, на который дана датированная ссылка, то рекомендуется использовать версию этого стандарта с указанным выше годом утверждения (принятия). Если после утверждения настоящего стандарта в ссылочный стандарт, на который дана датированная ссылка, внесено изменение, затрагивающее положение, на которое дана ссылка, то это положение рекомендуется применять без учета данного изменения. Если ссылочный стандарт отменен без замены, то положение, в котором дана ссылка на него, рекомендуется применять в части, не затрагивающей эту ссылку.
3 Термины, определения и сокращения
3.1 Термины и определения
В настоящем стандарте применены термины по ГОСТ 15467, ГОСТ 16504, ГОСТ 20911, ГОСТ 23956, ГОСТ 24346, ГОСТ 25866, ГОСТ 27471, ГОСТ 28842, ГОСТ 19431, ГОСТ Р 27.102, ГОСТ Р ИСО 2041, ГОСТ Р 58779, ГОСТ Р 70214, ГОСТ Р 57114, ГОСТ Р 70810, а также следующие термины с соответствующими определениями:
3.1.1 автоматизированный мониторинг оборудования: Мониторинг оборудования с применением автоматизированных систем.
3.1.2 валопровод гидроагрегата: Система валов гидроагрегата, составленная из нескольких частей, соединенных болтовыми фланцевыми соединениями от РК гидротурбины до верха гидрогенератора.
Примечание — Перемещение валопровода ограничено направляющими и опорным подшипниками.
3.1.3 деталь оборудования: Неделимая составная часть конструктивного узла оборудования.
3.1.4 дефект: Каждое отдельное несоответствие объекта требованиям, установленным в технической документации.
3.1.5 излом линии вала гидроагрегата: Параметр валопровода гидроагрегата, характеризующий взаимное отклонение геометрических осей валов гидротурбины и гидрогенератора, и возникающий из-за неточности изготовления и сборки фланцевых соединений валов гидроагрегата.
3.1.6 измеренное значение параметра: Значение параметра, установленное в результате его измерения определенным средством контроля.
3.1.7 измерительный контроль: Контроль, осуществляемый с применением средств измерений.
3.1.8 индекс технического состояния оборудования: Интегральный показатель технического состояния.
Примечание — Определяется в соответствии с [1].
3.1.9 исправное состояние: Состояние объекта, в котором параметры объекта соответствуют требованиям, установленным в документации на этот объект.
3.1.10 испытания: Экспериментальное исследование определенных свойств гидроагрегата.
3.1.11 карта контроля: Технологический документ контроля, предназначенный для регистрации результатов измерения контролируемых параметров, с указанием подписей исполнителя операции, руководителя участка и контролирующего лица.
3.1.12 капитальный ремонт оборудования: Ремонт, выполняемый для восстановления исправности и полного или близкого к полному восстановлению ресурса оборудования с заменой или восстановлением любых его частей.
3.1.13 контроль непрерывный: Форма технического контроля, при котором поступление информации о контролируемых параметрах происходит непрерывно.
3.1.14 контроль периодический: Форма технического контроля, при котором поступление информации о контролируемых параметрах происходит через установленные интервалы времени.
3.1.15 контроль постоянный: Форма технического контроля, осуществляемого штатным персоналом гидроэлектростанции посредством инструментальных и/или визуальных наблюдений, проводимых ежедневно на работающем оборудовании.
3.1.16 контроль (технического состояния): Проверка соответствия значений параметров объекта требованиям технической документации и определение на этой основе одного из заданных видов технического состояния в данный момент времени.
3.1.17 линия вала гидроагрегата: Совокупность осей валов гидроагрегата, полученная при сборке.
4
ГОСТ Р 55260.3.2—2023
3.1.18 маяки: Базовые точки на неподвижных частях корпусов подшипников или других неподвижных частях гидроагрегата, относительно которых фиксируются линейные размеры, определяющие пространственное положение вала.
3.1.19 межремонтный период: Период времени между капитальными ремонтами агрегата, т. е. от ввода в эксплуатацию после предыдущего капитального ремонта до вывода из эксплуатации в следующий капитальный ремонт.
3.1.20 модернизация оборудования: Комплекс работ по улучшению технико-эксплуатационных характеристик изделия, находящегося в эксплуатации, путем замены отдельных составных частей.
3.1.21 мониторинг оборудования: Форма непрерывного технического контроля за состоянием оборудования, включающего сбор, обработку и хранение измерительной информации о параметрах работы оборудования в процессе его эксплуатации в режиме непрерывного контроля параметров, осуществляемого штатным персоналом гидроэлектростанции.
3.1.22 неисправное состояние: Состояние объекта, в котором хотя бы один параметр объекта не соответствует хотя бы одному из требований, установленных в документации на этот объект.
Примечание — К неисправному состоянию относятся следующие виды технического состояния: частично работоспособное, неработоспособное, предельное.
3.1.23 неработоспособное состояние: Состояние оборудования, при котором контролируемые параметры, характеризующие способность оборудования выполнять заданные функции, не соответствуют требованиям нормативной и/или конструкторской (проектной) документации и при контроле технического состояния которого выявлены критические или значительные, трудноустранимые дефекты, и восстановление работоспособности оборудования требует его немедленного вывода в ремонт.
3.1.24 несоответствие: Частичное или полное невыполнение требований.
3.1.25 номинальное значение параметра: Значение параметра, определяемое его функциональным назначением и служащее началом отсчета отклонений.
3.1.26 нормальный режим работы оборудования: Режим работы, при котором параметры состояния оборудования не отклоняются от номинальных более, чем это допустимо в соответствии с нормативными документами, техническими условиями и инструкциями.
3.1.27 нормативный документ: Документ, устанавливающий правила, общие принципы или характеристики, касающиеся различных видов деятельности или их результатов.
3.1.28 обобщенный узел: Общие параметры технического состояния, не относящиеся к функциональным узлам, включающие срок службы и энергетические характеристики (КПД, мощность) гидротурбины.
3.1.29 оборудование: Гидротурбины и механическая часть генераторов (генераторный вал, подпятник, генераторные направляющие подшипники, грузонесущая и негрузонесущая крестовины).
3.1.30 объем испытаний: Характеристика испытаний, определяемая количеством объектов и видов испытаний, а также суммарной продолжительностью испытаний.
3.1.31 осмотр оборудования: Форма технического контроля за состоянием оборудования, включающая внешний и внутренний осмотры остановленного оборудования лицами, контролирующими его безопасную эксплуатацию, или комиссией, назначаемой техническим руководителем ГЭС, с периодичностью, устанавливаемой стандартом организации каждой гидроэлектростанции.
3.1.32 определяющий параметр: Параметр изделия, используемый при контроле для определения вида технического состояния этого изделия.
3.1.33 остаточный ресурс: Суммарная наработка объекта от момента контроля его технического состояния до перехода объекта в предельное состояние.
3.1.34 отказ: Событие, заключающееся в нарушении работоспособного состояния объекта.
Примечания
1 Отказ может быть полным или частичным.
2 Полный отказ характеризуется переходом объекта в неработоспособное состояние.
3 Частичный отказ характеризуется переходом объекта в частично неработоспособное состояние.
3.1.35 параметр технического состояния: Величина, характеризирующая техническое состояние отдельного функционального узла либо оборудования в целом и подлежащая количественной оценке.
3.1.36 паспорт изделия: Эксплуатационный документ, содержащий сведения, удостоверяющие гарантии изготовителя, значения основных параметров и характеристик (свойств) изделия, а также сведения о сертификации и утилизации изделия.
5
ГОСТ Р 55260.3.2—2023
3.1.37 предельно допустимое значение параметра: Наибольшее или наименьшее значение параметра, которое может иметь работоспособное изделие.
3.1.38 периодическая вибрация: Вибрация, при которой каждое значение колеблющейся величины, характеризующее вибрацию, повторяется с точностью средства измерения через равные интервалы времени, или спектральные составляющие сигнала вибрации не меняются в течение десяти и более оборотов гидроагрегата.
Примечание — Вибрация, не соответствующая требованиям периодической вибрации, относится к непериодической вибрации.
3.1.39 работоспособное состояние: Состояние оборудования, при котором контролируемые параметры, характеризующие способность оборудования выполнять заданные функции, соответствуют требованиям нормативной и/или конструкторской (проектной) документации и при контроле технического состояния которого дефекты не выявлены или выявлены малозначительные легкоустранимые дефекты на ранней стадии развития.
3.1.40 реконструкция оборудования: Замена эксплуатируемого оборудования на аналогичное с применением новых материалов и конструктивных решений.
3.1.41 ремонт: Комплекс операций по восстановлению исправности или работоспособности изделий и восстановлению ресурсов изделий или их составных частей.
3.1.42 ремонтная документация: Совокупность нормативной, технической, технологической, организационно-распорядительной документации, а также проект производства работ и документы, фиксирующие результаты выполнения ремонта.
Примечание — Полный перечень ремонтной документации приведен в [2].
3.1.43 состояние предельное: Состояние оборудования, при контроле технического состояния которого выявлены критические дефекты и дальнейшая эксплуатация оборудования недопустима или нецелесообразна, либо восстановление его работоспособного состояния невозможно или нецелесообразно.
3.1.44 срок службы: Календарная продолжительность эксплуатации оборудования, определенная в нормативной и (или) проектной документации, по достижении которой следует провести оценку технического состояния оборудования в целях определения допустимости параметров и условий его дальнейшей эксплуатации.
3.1.45 специализированная организация: Организация, располагающая подготовленными квалифицированными кадрами, необходимым испытательным оборудованием, методической и нормативно-технической документацией и, при необходимости, полномочиями (лицензиями федеральных органов исполнительной власти, сертификатами) для выполнения одной или нескольких специализированных работ, направленных на обеспечение безопасности, надежности и экономичности технических устройств, устанавливаемых на объектах электроэнергетики.
Примечание — Специализированными работами могут быть: техническое диагностирование, работы по продлению срока службы или оценке остаточного ресурса гидроагрегата, разработка методической и нормативной документации в перечисленных областях.
3.1.46 (техническое) диагностирование: Определение технического состояния объекта.
Примечание — Задачами технического диагностирования являются: контроль технического состояния, поиск места и определение причин отказа (неисправности), прогнозирование технического состояния.
3.1.47 технический руководитель ГЭС: Лицо в штате организации собственника (эксплуатирующей организации) ГЭС, уполномоченное принимать решения и отдавать распоряжения по всем техническим вопросам касательно оборудования данного объекта электроэнергетики.
3.1.48 техническое обследование: Форма технического контроля за состоянием оборудования, включающая осмотр, измерения, испытания и углубленные исследования на остановленном оборудовании, проводимые по специальным программам, как правило, с привлечением специализированных организаций по решению технического руководителя ГЭС и/или комиссий, производящих периодический осмотр или регулярное техническое освидетельствование.
3.1.49 техническое обслуживание: Комплекс операций по поддержанию работоспособности или исправности оборудования при использовании по назначению.
3.1.50 техническая характеристика: Величина, отражающая функциональные, геометрические, деформационные, прочностные и другие свойства конструкции и/или материалов.
6
ГОСТ Р 55260.3.2—2023
3.1.51 техническое перевооружение: Комплекс работ, ведущих к полной замене оборудования на новое, более производительное с изменением или без изменения технических параметров, и проводимый без реконструкции объекта капитального строительства.
3.1.52 техническое состояние: Состояние объекта в определенный момент времени, при определенных условиях внешней среды, характеризующееся фактическими значениями параметров, установленных в документации.
3.1.53 узел: Функциональный и/или обобщенный узел.
3.1.54 уклон вала гидроагрегата: Параметр гидроагрегата, характеризующий отклонение валопровода от вертикальной оси.
3.1.55 формуляр: Документ технического контроля, содержащий результаты измерений контролируемых параметров и оценку их соответствия установленным нормам (карты измерений, протоколы, акты и др.).
3.1.56 функциональный узел: Составная часть оборудования, содержащая отдельные конструктивные элементы и детали, которая может выполнять свою функцию только совместно с другими частями единицы оборудования.
Примечание — В целях настоящего стандарта — рабочее колесо, направляющий аппарат, вал и др.
3.1.57 частично неработоспособное состояние: Состояние оборудования, при котором при контроле технического состояния выявлены значительные, но устранимые дефекты, при которых оборудование способно частично выполнять требуемые функции, и продолжение работы оборудования требует временного введения ограничений (снижения эксплуатационных нагрузок, сокращения межремонтного периода и т. п.).
3.1.58 эксплуатация: Стадия жизненного цикла изделия, на которой реализуется, поддерживается и восстанавливается его качество.
3.1.59 эксплуатационные испытания: Испытания объекта, проводимые при эксплуатации.
3.1.60 эксплуатационные документы: Конструкторские документы, предназначенные для использования при эксплуатации, обслуживании и ремонте изделия в процессе эксплуатации; текстовые и графические рабочие конструкторские документы, которые в отдельности или в совокупности дают возможность ознакомления с изделием и определяют правила его эксплуатации (использования по назначению, технического обслуживания, текущего ремонта, хранения и транспортирования), а также предназначены для отражения сведений, удостоверяющих гарантированные изготовителем значения основных параметров и характеристик (свойств) изделия, гарантий и сведений по его эксплуатации за весь период (длительность и условия работы, техническое обслуживание, ремонт и др. данные), и сведений по его утилизации.
3.1.61 эксплуатирующая организация: Организация, имеющая в собственности, хозяйственном ведении или оперативном управлении имущество гидроэлектростанции, осуществляющая в отношении этого имущества права и выполняющая обязанности, необходимые для ведения деятельности по безопасному производству электроэнергии в соответствии с действующими нормами и правилами.
3.2 Сокращения
В настоящем стандарте применены следующие сокращения:
АСУ ТП — автоматизированная система управления технологическим процессом;
ВБ — верхний бьеф;
ВИК — визуально-измерительный контроль;
ВТК — вихретоковый контроль;
ГА — гидроагрегат;
ГП — генераторный подшипник;
ГРАМ — система группового регулирования активной мощности;
ГЭС — гидравлическая электрическая станция;
ИК — измерительный контроль;
ИТС — индекс технического состояния;
КПД — коэффициент полезного действия;
7
ГОСТ Р 55260.3.2—2023
КР | — капитальный ремонт; |
КРК | — камера рабочего колеса; |
ЛБ МИЧО - | — левый берег; — механизм изменения числа оборотов; |
ммк | — метод магнитный коэрцитиметрический; |
МНУ | — маслонапорная установка; |
моо | — механизм ограничения открытия направляющего аппарата; |
мпд НА | — магнитопорошковая дефектоскопия; — направляющий аппарат; |
НБ | — нижний бьеф; |
НДС НКНА - | — напряженно-деформированное состояние; — нижнее кольцо направляющего аппарата; |
нтд ПБ | — нормативно-техническая документация; — правый берег; |
ПВК | — контроль проникающими веществами (капиллярный контроль); |
ПЛ | — поворотно-лопастная(ое) (гидротурбина, рабочее колесо); |
ПП | — подпятник; |
ПР | — пропеллерная(ое) гидротурбина (рабочее колесо); |
РК | — рабочее колесо гидротурбины; |
РО | — радиально-осевая(ое) гидротурбина (рабочее колесо); |
РЧВ САУ | — регулятор частоты вращения; — система автоматического управления; |
СК ско | — синхронный компенсатор; — среднее квадратическое отклонение сигнала; |
СНА СО | — сервомотор направляющего аппарата; — стандартный образец; |
соп СП | — стандартный образец предприятия; — сопрягающий пояс; |
сто | — стандарт организации; |
ТВ | — измерение твердости; |
тп | — турбинный подшипник; |
УЗК УЗТ | — ультразвуковой контроль; — ультразвуковая толщинометрия; |
XX ЭГР | — холостой ход; — электрогидравлический регулятор частоты вращения; |
эгп ЭМА | — электрогидравлический преобразователь; — электромагнитноакустический (способ); |
эмп | — эластичный металлопластмассовый (опорный сегмент). |
4 Общие положения
4.1 Целью оценки технического состояния гидротурбин и механической части генераторов ГЭС является:
- своевременное выявление и устранение возникающих в процессе эксплуатации повреждений (дефектов) и отклонений технических параметров от установленных значений;
8
ГОСТ Р 55260.3.2—2023
- определение вида технического состояния контролируемого оборудования;
- определение фактических значений технических параметров гидроагрегатов для последующего определения ИТС узлов и оборудования в целом;
- прогнозирование состояния оборудования и ранжирования рисков по убыванию риска отказа;
- определение возможности, целесообразности, сроков и условий продолжения эксплуатации выработавшего срок службы контролируемого оборудования, его элементов и узлов, определяющих безопасность эксплуатации ГА;
- выработка рекомендаций по продолжению эксплуатации оборудования, имеющего повреждения (дефекты), включая введение при необходимости специальных эксплуатационных мер (дополнительный контроль, режимные ограничения, внеплановый ремонт и т. п.);
- формирование и актуализация перспективных (многолетних) графиков ремонта, годовой ремонтной программы и выработка рекомендаций по объему и срокам необходимого ремонтного обслуживания;
- планирование комплекса мероприятий по техническому перевооружению и реконструкции, обоснование для модернизации гидроагрегатов в целом, их элементов и конструктивных узлов.
4.2 Определение ИТС проводится только для работоспособного оборудования. При обнаружении критических неисправностей, препятствующих дальнейшей эксплуатации (в частности, опасных трещин), решение о техническом воздействии принимается на основании углубленной оценки технического состояния, в том числе с учетом требований стандарта.
4.3 Настоящий стандарт устанавливает для применения на ГЭС следующие обязательные формы контроля технического состояния гидротурбин и механической части генераторов:
- постоянный контроль и непрерывный автоматизированный мониторинг на работающем ГА;
- периодические осмотры на остановленном ГА в периоды плановых и внеплановых ремонтов;
- периодический (измерительный) контроль на остановленном ГА в периоды плановых и внеплановых ремонтов без разборки ГА и/или на работающем ГА (при наличии технической возможности);
- периодические технические диагностирования в форме технического обследования оборудования в периоды плановых и внеплановых ремонтов с осушением и полной или частичной разборкой ГА, при реконструкции и/или модернизации ГА.
4.4 Настоящий стандарт не регламентирует требования к содержанию и объему работ при техническом освидетельствовании (как форме регулярного технического контроля). Правила проведения технического освидетельствования оборудования ГЭС определяются [3].
4.5 Объем, задачи и исполнители для каждой формы контроля технического состояния гидротурбин и механической части генераторов представлены в таблице 4.1.
9
q Таблица 4.1 — Объем, задачи и исполнители для каждой формы контроля технического состояния гидротурбин и механической части генераторов
Форма контроля | Объем контроля | Задачи контроля | Кем осуществляется контроль |
Постоянный контроль | Инструментальные и/или визуальные наблюдения, проводимые ежедневно на работающем оборудовании в режиме, определяемом инструкцией по эксплуатации или СТО ГЭС | 1. Поддержание исправного и работоспособного состояния оборудования с учетом его фактического технического состояния. 2. Оперативное выявление нарушений безопасной эксплуатации оборудования. 3. Принятие оперативных решений о необходимых мерах по устранению выявленных нарушений и/или о возможности дальнейшей работы оборудования с выявленным нарушением | Штатным персоналом ГЭС |
Автоматизированный мониторинг | Параметры работы оборудования в процессе его эксплуатации в режиме непрерывного контроля параметров с применением автоматизированных систем | - Контроль параметров работы ГА; - обнаружение и оповещение персонала ГЭС о развивающихся дефектах и неисправностях ГА (предупредительная и аварийная сигнализация); - оперативная оценка технического состояния ГА в любой момент времени путем сопоставления эксплуатационных параметров ГА с соответствующими нормативными (допустимыми) значениями; - построение трендов изменения контролируемых параметров | Штатным персоналом ГЭС с использованием средств АСУ ТП. На ГЭС без ежедневного дежурства оперативного и оперативно-ремонтного персонала должен быть налажен дистанционный контроль показателей, определяемых проектной документацией, на пункте с постоянным нахождением дежурного персонала |
Периодический осмотр | Осмотры оборудования в соответствии с графиком осмотров | - Своевременное выявление и анализ причин повреждений и дефектов, включая скрытые, которые не могут быть установлены при постоянном контроле на работающем оборудовании, и выработки решений по предупреждению их развития и устранению; - выработка рекомендаций по объему и срокам необходимого ремонтного обслуживания | Осмотр производится лицами, контролирующими безопасную эксплуатацию конкретного оборудования (элемента оборудования), или комиссией, назначаемой техническим руководителем ГЭС |
Периодический (измерительный) контроль | Инструментальные измерения, выполненные на оборудовании в периоды плановых и внеплановых технических воздействий без разборки ГА и/или на работающем ГА (при наличии технической возможности) в соответствии со стандартом организации или с ремонтной документацией | - Своевременное выявление и анализ причин повреждений и дефектов, включая скрытые, которые не могут быть установлены при постоянном контроле, и выработки решений по предупреждению их развития и устранению; - выработка рекомендаций по объему и срокам необходимого ремонтного обслуживания | Штатным персоналом ГЭС, включая персонал сервисных и ремонтных предприятий, допущенный к выполнению соответствующих видов работ |
ГОСТ Р 55260.3.2—2023
Окончание таблицы 4.1
Форма контроля | Объем контроля | Задачи контроля | Кем осуществляется контроль |
Периодическое техническое диагностирование в форме технического обследования | Обследование проводится по специальным программам1), включающим осмотр, измерения, испытания и углубленные исследования на оборудовании. Обследование проводится по решению технического руководителя ГЭС и/или комиссий, производящих периодический осмотр или регулярное техническое освидетельствование, а также в случае внезапного повреждения (отказа) оборудования в процессе эксплуатации | - Определение вида технического состояния гидротурбин и механической части генераторов (их отдельных элементов, конструктивных узлов) на основании результатов проводимых при этом испытаний и исследований; - углубленная оценка технического состояния оборудования после длительного периода эксплуатации; - определение фактических значений технических параметров ГА для последующего определения ИТС узлов и оборудования в целом; - своевременное выявление и анализ причин аварийноопасных дефектов и повреждений; - выработка рекомендаций по объему и срокам необходимого ремонтного обслуживания; - выработка технических решений по мерам, необходимым для обеспечения безопасной эксплуатации оборудования в пределах срока службы или по продлению срока службы; - выработка рекомендаций по продолжению эксплуатации оборудования, имеющего повреждения (дефекты), включая введение при необходимости специальных эксплуатационных мер (дополнительный контроль, режимные ограничения, внеплановый ремонт и т. п.) | Специализированными организациями |
1) Программы работ по техническому обследованию с указанием используемых методик разрабатываются специализированной организацией, привлекаемой к проведению обследования, и утверждаются техническим руководителем ГЭС. Программа работ по техническому обследованию разрабатывается с учетом типа, технического состояния, срока службы, условий и опыта эксплуатации обследуемого оборудования. |
ГОСТ Р 55260.3.2—2023
ГОСТ Р 55260.3.2—2023
4.6 Периодичность для каждой формы контроля устанавливается ремонтной документацией, имеющейся на каждой ГЭС, в том числе планами, графиками и программами ремонта [2].
В случаях повреждения оборудования, имевшего следствием непредвиденный вывод его из работы, должен быть произведен внеочередной контроль.
Осмотр оборудования должен проводиться не реже одного раза в год. Осмотр оборудования проводят обязательно до наступления весеннего половодья, а в отдельных случаях — летне-осеннего паводка в целях проверки готовности оборудования к работе с максимальной нагрузкой в течение многоводного периода.
4.7 В таблице 4.2 представлены виды технического состояния гидротурбин и механической части генераторов в зависимости от результатов контроля, определяющие степень работоспособности оборудования.
Таблица 4.2 — Вид технического состояния
Наименование | Описание |
«Работоспособное» (нормальное) | Контролируемые параметры, характеризующие способность оборудования выполнять заданные функции, соответствуют требованиям нормативной и/или конструкторской (проектной) документации и при контроле технического состояния дефекты не выявлены или выявлены малозначительные легкоустранимые дефекты на ранней стадии развития |
«Частично неработоспособное» (потенциально опасное) | При контроле технического состояния выявлены значительные, но устранимые дефекты, при которых оборудование способно частично выполнять требуемые функции, и продолжение работы оборудования требует временного введения ограничений (снижения эксплуатационных нагрузок, сокращения межремонтного периода и т. п.) |
«Неработоспособное» (предаварийное) | Контролируемые параметры, характеризующие способность оборудования выполнять заданные функции, не соответствуют требованиям нормативной и/или конструкторской (проектной) документации и при контроле технического состояния выявлены критические или значительные, трудноустранимые дефекты и восстановление работоспособности оборудования требует его немедленного вывода в ремонт |
«Предельное» (критическое) | При контроле технического состояния выявлены критические дефекты и дальнейшая эксплуатация оборудования недопустима или нецелесообразна либо восстановление его работоспособного состояния невозможно или нецелесообразно |
4.8 Критерии и правила выставления оценок технического состояния гидротурбин и гидрогенераторов при расчете ИТС установлены в [1], [4].
4.9 При выполнении на ГЭС работ по оценке технического состояния гидротурбин и механической части гидрогенераторов персоналу следует соблюдать требования [5].
5 Требования к контролю и оценке технического состояния гидротурбин на ГЭС
5.1 На каждой ГЭС должна быть организована постоянная и периодическая оценка технического состояния гидротурбин и механической части генераторов [6].
5.2 Постоянная оценка технического состояния гидротурбин и механической части генераторов проводится по результатам постоянного контроля и автоматизированного мониторинга с целью недопущения перехода оборудования в предельное состояние.
5.3 Периодическая оценка технического состояния гидротурбин и механической части генераторов проводится:
- при вводе в эксплуатацию;
- периодических осмотрах;
- испытаниях перед, во время и после ремонтов с осушением и частично или полной разборкой оборудования, а также в межремонтный период;
12
ГОСТ Р 55260.3.2—2023
- диагностических обследованиях, проводимых по решению технического руководителя ГЭС или в случае внезапного повреждения (отказа) оборудования в процессе эксплуатации;
- технических освидетельствованиях, требования к которым определены в [3];
- расчете ИТС в соответствии с требованиями [1];
- прогнозировании состояния оборудования и ранжировании рисков по убыванию риска отказа в соответствии с требованиями [4];
- определении возможности, целесообразности, сроков и условий продолжения эксплуатации выработавшего срок службы оборудования, его элементов и конструктивных узлов в соответствии с требованиями ГОСТ 33272.
5.4 На каждой ГЭС на основании требований настоящего стандарта с учетом особенностей эксплуатации оборудования, графика проведения ремонтов, результатов предшествующего контроля может быть разработан стандарт ГЭС, отражающий порядок, объем, периодичность и методы технического контроля состояния гидротурбин и механической части генераторов, с указанием следующих сведений:
- объемы, сроки и методы реализации контроля;
- графики, планы и программы технического контроля;
- маршруты и периодичность обходов, осмотров и проверок;
- правила и инструкции пользования штатными средствами для контрольных измерений;
- порядок ведения технической документации по контролю технического состояния гидротурбин и механической части генераторов;
- правила безопасности при осуществлении технического контроля.
При отсутствии стандарта ГЭС необходимая информация может быть отражена в инструкции по эксплуатации.
5.5 На каждой ГЭС необходимо вести техническую документацию, в которой должны быть зарегистрированы все результаты контроля технического состояния гидротурбин и механической части генераторов.
Допускается ведение документации в электронном виде.
5.6 В организации собственника (эксплуатирующей организации) должен быть организован учет и анализ информации об отказах, повреждениях, нештатных (опасных) ситуациях в работе каждой единицы установленного на ГЭС оборудования (элемента оборудования) для разработки мероприятий по обеспечению его безопасной эксплуатации.
5.7 Вся документация, ведущаяся в эксплуатирующей организации, в которой регистрируются результаты контроля и содержится информация об отказах оборудования, повреждениях, нештатных ситуациях, должна храниться до списания оборудования (элемента оборудования).
5.8 Для обеспечения сравнимости и унификации при оформлении результатов каждой формы контроля необходимо использовать стандартные бланки и формуляры, которые определяются локальными нормативными актами с учетом рекомендаций настоящего стандарта.
5.9 Контроль за техническим состоянием оборудования требует оснащения ГЭС средствами измерения в соответствии с ГОСТ Р 55260.3.1, ГОСТ Р 55260.4.1, ГОСТ Р 55621, [7] и соблюдения правил по обеспечению единства измерений в соответствии с ГОСТ Р 8.000, ГОСТ 8.417, [8], [9].
5.10 Оснащение оборудования ГЭС средствами измерения должно быть произведено в соответствии с проектной, конструкторской и нормативной документацией и с техническими условиями на поставку оборудования. Установленные средства измерения должны обеспечивать постоянный контроль за техническим состоянием оборудования и режимом его работы.
5.11 Если ГА не оснащен стационарными средствами измерения для контроля технического состояния в объемах, предусмотренных настоящим стандартом, необходимо проводить соответствующие измерения с помощью переносных средств измерений с периодичностью, рекомендуемой заводом-изготовителем или предусмотренной инструкцией по эксплуатации.
6 Оценка технического состояния гидротурбины и механической части генератора
6.1 Общие положения
6.1.1 Оценка технического состояния оборудования должна быть проведена на основе анализа результатов всех форм технического контроля для каждого функционального и/или обобщенного узла. Требования к объемам контроля, методике проведения контроля и рекомендации по оформлению от-
13
ГОСТ Р 55260.3.2—2023
четной документации представлены в 6.2—6.13. Если иное специально не оговорено, все положения стандарта для ПЛ-гидротурбин могут быть распространены на пропеллерные и диагональные гидротурбины.
6.1.2 В процессе оценки технического состояния оборудования должны быть выявлены возникающие при эксплуатации повреждения (дефекты) и отклонения технических параметров от установленных значений.
Методические указания по техническому обследованию узлов оборудования при их повреждениях представлены в приложении А и для узлов генераторов дополнительно в ГОСТ Р 55260.2.2.
Методики контроля геометрических форм и размеров проточной части гидротурбин представлены в приложении Б.
Методики контроля состояния металла узлов и элементов гидротурбин и механической части генератора представлены в приложении В.
Перечень основных технических данных по ГЭС, гидротурбинному и гидрогенераторному оборудованию представлен в приложении Г.
В приложении Д представлены методики испытания системы регулирования гидротурбин, в приложениях Е и Ж — методики контроля линии валов и подпятников вертикальных гидроагрегатов соответственно, в приложении И — методика определения осевой жесткости агрегата, в приложении К — методики проведения натурных испытаний.
6.1.3 При определении вида технического состояния по степени работоспособности оборудования в соответствии с классификацией, приведенной в таблице 4.2, оценку технического состояния производят:
- для узла оборудования — по худшей из оценок технического состояния по всем определяющим параметрам данного узла;
- оборудования в целом — по худшей из оценок технического состояния по всем узлам.
6.1.4 Расчет ИТС узлов и оборудования в целом проводится по [1] на основании фактических значений параметров функционального узла, определенных в соответствии с требованиями и рекомендациями 6.2—6.13.
6.1.5 Определение возможности, целесообразности, сроков и условий продолжения эксплуатации контролируемого оборудования, его элементов и узлов, определяющих безопасность эксплуатации ГА, проводится с учетом углубленной оценки технического состояния на базе результатов периодического технического диагностирования оборудования и определения индивидуального остаточного ресурса.
6.1.6 На основании результатов работ по 6.1.2—6.1.5 должны быть сформулированы рекомендации по продолжению эксплуатации оборудования, в том числе имеющего повреждения (дефекты), включая (при необходимости) введение специальных эксплуатационных мер (дополнительный контроль, режимные ограничения, внеплановый ремонт и т. п.) или проведение комплекса мероприятий по техническому перевооружению, реконструкции, модернизации и замене оборудования или его отдельных узлов, а также актуализированы объемы, сроки и графики ремонта.
6.2 Рабочее колесо
6.2.1 Техническое состояние РК оценивают, исходя из степени износа основных деталей и узлов, наличия повреждений, соответствия паспортным или проектным требованиям.
6.2.2 Обтекатель РК для РО и ПЛ гидротурбин, а также днище для РК ПЛ-гидротурбин должны быть заштифтованы и плотно обтянуты, а крепежные детали застопорены. Допускаются местные зазоры не более 0,1 мм суммарной площадью не более 20 % общей площади стыкового соединения.
6.2.3 Требования к объемам контроля технического состояния рабочих колес РО- и ПЛ-типов гидротурбин и методикам его проведения для определения вида технического состояния по степени работоспособности оборудования в соответствии с классификацией, приведенной в таблице 4.2, и/или последующего определения ИТС представлены в таблицах 6.1—6.4.
14
Таблица 6.1 — Нормы контроля технического состояния РК РО-гидротурбин для последующего определения ИТС
Группа параметров функционального узла1) | Параметр функционального узла1) | Допустимые значения параметра, установленное НТД значение Н | Методика определения фактического значения параметра Ф функционального узла | Способ регистрации результатов контроля | Форма контроля | |
наименование | размерность | |||||
Зазор между подвижными и неподвижными элементами проточной части гидротурбины2) | Зазор по лабиринтному уплотнению (абсолютная величина). | мм | Проектное значение должно соответствовать нормативам кон-структорской и/или монтажной документации. При отсутствии заводских или монтажных норм — в соответствии с данными, приведенными в Б.2 | На остановленном ГА при осушенном проточном тракте в соответствии с рекомендациями Б.2 или на основании данных стационарных систем автоматизированного мониторинга, позволяющего выполнять подобные измерения | Формуляр (см. рисунок Б.2.2) с указанием схемы замеров | Периодический (измерительный) контроль, техническое обследование в периоды ремонта при осушенном проточном тракте. Автоматизированный мониторинг |
Отклонение зазора после центровки ГА | % от средней величины | |||||
Кавитационный износ элементов РК, механические повреждения | Кавитационная эрозия | кг | В соответствии с гарантиями завода-изготовителя с учетом рекомендаций ГОСТ Р 55562. В соответствии с нормами контроля по каждому виду неразрушающего контроля металла РК(см. В.2, В.З, В.4) и стандартами организации | На остановленном ГА при осушенном проточном тракте в соответствии с рекомендациями В.4 и ГОСТ Р 55562 | Акты осмотров. Формуляры и схемы замеров (см. рисунки В.4.3, В.4.4, В.4.6). Заключения по видам неразрушающего контроля. Фотографии. Технические отчеты | Периодический осмотр, периодический (измерительный) контроль в периоды ремонтов при осушенном проточном тракте. Техническое обследование в периоды КР при осушенном проточном тракте |
Повреждения кромок лопастей | ||||||
Усталостные трещины лопастей | Усталостные трещины РК и лопастей |
1) В соответствии с [1].
2) Соответствует группе параметров функционального узла «Зазор «Камера — лопасть» [1].
ГОСТ Р 55260.3.2—2023
^ Таблица 6.2 — Нормы контроля технического состояния РК РО-гидротурбин для определения вида технического состояния по степени работоспособности оборудования
Контролируемые параметры1) | Допустимые значения параметров | Методики определения фактических значений параметров | Способ регистрации результатов контроля | Форма контроля |
Давление, вакуум, пульсация давления в проточной части | Проектно-конструкторская, монтажная документация, данные завода-изготовителя, СТО ГЭС | На работающем оборудовании по данным штатных систем измерений: непрерывно при наличии датчиков дистанционного контроля, визуально не реже 1 раза в смену при обходах | Журнал дефектов, суточная ведомость, отчеты специализированного программного обеспечения | Постоянный контроль. Автоматизированный мониторинг |
Высотное положение РК | В соответствии с требованиями завода-изготовителя. Когда ротор ГА находится на ПП, вертикальные зазоры между неподвижными и вращающимися частями гидротурбины должны не менее чем на 5 мм превышать заданную заводом-изготовителем величину подъема ротора гидрогенератора на тормозах. При отсутствии заводских или монтажных норм в соответствии сданными, приведенными в Б.2 | На остановленном ГА при осушенном проточном тракте в соответствии с рекомендациями Б.2 | Акты, формуляры и схемы замеров | Периодический (измерительный) контроль. Техническое обследование |
Фактические геометрические размеры РК (равномерность лопастной решетки, толщины выходных кромок лопастей, радиусы галтельных переходов в зонах приварки лопастей к ободу и ступице, концентричность ободов и пр.) | В соответствии с конструкторской документацией. При отсутствии требований к конструкторской документации максимально допустимые отклонения по критерию однородности (отношение измеренного значения к среднему) лопастной системы рекомендуется принимать в соответствии с [10] | В соответствии с рекомендациями Б.2, включая ЗЮ-сканирование РК | Акты, формуляры и схемы замеров, отчет о проведении измерений | Периодический (измерительный) контроль или техническое обследование |
ГОСТ Р 55260.3.2—2023
Окончание таблицы 6.2
Контролируемые параметры1) | Допустимые значения параметров | Методики определения фактических значений параметров | Способ регистрации результатов контроля | Форма контроля |
Форма и плотность посадки лабиринтных уплотнений на ободе РК | Лабиринтные уплотнения, насаженные на обод РК РО-типа, целиком или отдельными частями, должны быть надежно закреплены на ободе, плотно обжимать его по окружности, а стыки сборного кольца должны быть заварены и тщательно зашлифованы. Неконцентричность между собой верхнего и нижнего уплотнительных колец и несоосность их с валом допускается в пределах 0,1 величины одностороннего зазора в лабиринтном уплотнении РК | По результатам ВИК (см. В.2.1) | Заключение ВИК | Периодический (измерительный) контроль или техническое обследование |
1) Контролируемые параметры, не вошедшие в таблицу 6.1. |
ГОСТ Р 55260.3.2—2023
00
Таблица 6.3 — Нормы контроля технического состояния РК ПЛ-гидротурбин для последующего определения ИТС
Группа параметров функционального узла1) | Параметр функционального узла1) | Допустимые значения параметра, установленное НТД значение Н | Методика определения фактического значения параметра Ф функционального узла | Способ регистрации результатов контроля | Форма контроля | |
наименование | размерность | |||||
Зазор «Камера — лопасть» | Зазор (абсолютная величина) | мм | Проектное значение должно соответствовать нормативам конструкторской и/или монтажной документации. При отсутствии заводских или монтажных норм — в соответствии с данными, приведенными в Б.З | На остановленном ГА при осушенном проточном тракте в соответствии с рекомендациями Б.З | Формуляр (см. рисунок Б.3.2) с указанием схемы замеров | Периодический (измерительный) контроль, техническое обследование в периоды ремонта при осушенном проточном тракте. Автоматизированный мониторинг |
Отклонение зазора после центровки ГА, подрезки и/или наплавки лопастей | % от средней величины | |||||
Кавитационный износ элементов РК, механические повреждения | Кавитационная эрозия | кг | В соответствии с гарантиями заво-да-изготовителя с учетом рекомендаций ГОСТ Р 55562. В соответствии с нормами контроля по каждому виду неразрушающего контроля металла РК(см. В.2, В.З, В.4) и стандартами организации | На остановленном ГА при осушенном проточном тракте в соответствии с рекомендациями В.4 и ГОСТ Р 55562 | Акты осмотров. Формуляры и схемы замеров (см. рисунки В.4.1, В.4.2, В.4.5). Заключения по видам НК. Фотографии. Технические отчеты | Периодический осмотр, периодический (измерительный) контроль в периоды ремонтов при осушенном проточном тракте. Техническое обследование (в периоды ремонта при осушенном проточном тракте) |
Повреждения кромок лопастей | ||||||
Усталостные трещины лопастей | Усталостные трещины РК и лопастей |
ГОСТ Р 55260.3.2—2023
Продолжение таблицы 6.3
Группа параметров функционального узла1) | Параметр функционального узла1) | Допустимые значения параметра, установленное НТД значение Н | Методика определения фактического значения параметра Ф функционального узла | Способ регистрации результатов контроля | Форма контроля | |
наименование | размерность | |||||
Протечки масла через уплотнения РК | Капельные протечки масла | л/сут. | В соответствии с технической документацией завода-изготовителя. В случае отсутствия заводских норм — допустимые нормы протечек запросить у изготовителя | Уплотнения испытывают в соответствии с методикой завода-изготовителя. При отсутствии заводской методики уплотнения РК ПЛ-типа должны быть испытаны пробным давлением масла в течение 24 ч при температуре РК и масла не ниже 5°С. Величину пробного давления устанавливает завод-изготовитель. Наличие протечек может быть установлено по результатам визуального осмотра (протечки или потеки масла через уплотнения лопастей, через уплотнения цапф лопастей, на втулке РК, из-под крышки втулки РК), появлению масла на поверхности воды в нижнем бьефе ГЭС, обводнению масла в системе регулирования | Отчет о проведении испытаний Акт | Периодический (измерительный) контроль в периоды ремонтов при осушенном проточном тракте. Техническое обследование. Периодический осмотр |
ГОСТ Р 55260.3.2—2023
м о
Окончание таблицы 6.3
Группа параметров функционального узла1) | Параметр функционального узла1) | Допустимые значения параметра, установленное НТД значение Н | Методика определения фактического значения параметра Ф функционального узла | Способ регистрации результатов контроля | Форма контроля | |
наименование | размерность | |||||
Перестановочные усилия | Перестановочные усилия | кгс/см2 | В соответствии с требованиями завода-изготовителя. При отсутствии заводских требований нормативное значение перестановочных усилий рассчитывается по величинам номинального давления масла в МНУ и рекомендуемым коэффициентам запаса по перестановочным усилиям в соответствии с рекомендациями Д.3.4. Рекомендуемый коэффициент запаса перестановочных усилий при расчете нормативных значений 25 %. Изменение величины перестановочных усилий допускается только в сторону уменьшения | В соответствии с рекомендациями Д-3.4 | Отчет о проведении испытаний по определению перестановочных усилий | Техническое обследование (как правило до и после КР) |
1) В соответствии с [1]. |
ГОСТ Р 55260.3.2—2023
Таблица 6.4 — Нормы контроля технического состояния РК ПЛ-гидротурбин для определения вида технического состояния по степени работоспособности оборудования
Контролируемые параметры1) | Допустимые значения параметров | Методики определения фактических значений параметров | Способ регистрации результатов контроля | Форма контроля |
Давление, вакуум, пульсация давления в проточной части | Проектно-конструкторская, монтажная документация, данные завода-изготовителя, СТО ГЭС | На работающем оборудовании по данным штатных систем измерений: непрерывно при наличии датчиков дистанционного контроля, визуально не реже 1 раза в смену при обходах | Журнал дефектов, суточная ведомость | Постоянный контроль. Автоматизированный мониторинг |
Высотное положение РК | В соответствии с требованиями завода-изготовителя. При отсутствии заводских или монтажных норм допускаемые отклонения от проектных значений в пределах допусков, приведенных в таблице Б.3.1. Вертикальные зазоры между неподвижными и вращающимися частями гидротурбины должны не менее чем на 5 мм превышать заданную заводом-изготовителем величину подъема ротора гидрогенератора на тормозах | На остановленном ГА при осушенном проточном тракте в соответствии с рекомендациями Б.З | Акты, формуляры и схемы замеров | Периодический (измерительный) контроль. Техническое обследование |
Фактические геометрические размеры лопастной системы РК (максимальное габаритное значение, равномерность лопастной решетки, углы разворота лопастей, толщина кромок и пр.) | В соответствии с конструкторской документацией. Положение лопастей по углу разворота при заданном открытии НА не должно отличаться от проектного более чем на 0,5 %. Показания величины угла разворота лопастей РК ПЛ-типа по градуировке по шкале маслоприемника должны соответствовать показаниям угла разворота их по градуировке на фланце лопасти. Расхождение в углах установки лопастей, замеренное в соответствии с требованиями раздела Б.З, не должно превышать 0,5°. Допустимые отклонения от среднего фактического значения в пределах РК не должны превышать 20 % от заданного проектного значения, указанного в конструкторской документации с учетом согласованных отклонений. При отсутствии требований к конструкторской документации максимально допустимые отклонения по критерию однородности (отношение измеренного значения к среднему) рекомендуется принимать в соответствии с рекомендациями (см. [10]) | В соответствии с рекомендациями Б.З, включая ЗО-сканирование в КРК | Акты, формуляры и схемы замеров, отчет о проведении измерений | Периодический (измерительный) контроль или техническое обследование |
ГОСТ Р 55260.3.2—2023
Окончание таблицы 6.4
Контролируемые параметры1) | Допустимые значения параметров | Методики определения фактических значений параметров | Способ регистрации результатов контроля | Форма контроля |
Состояние механизма разворота лопастей | По косвенным признакам при проверке комбинаторной зависимости, оценке равномерности углов установки лопастей, наличию люфтов и провисания лопастей | Периодический осмотр. Обследования (без разборки РК) | ||
1) Контролируемые параметры, не вошедшие в таблицу 6.3. |
ГОСТ Р 55260.3.2—2023
ГОСТ Р 55260.3.2—2023
6.2.4 Если представленные в таблицах 6.1 и 6.3 параметры РК полностью соответствуют проектным и монтажным требованиям, но при этом отмечены замечания в работе ГА (несоответствие проектной мощности, повышенные вибрации и т. п.), не связанные с неисправным состоянием других узлов ГА, следует провести контроль геометрических форм и размеров РК, включая построение профилей и решетки лопастной системы в соответствии с требованиями Б.1—Б.З.
6.2.5 Эксплуатацию РК ПЛ-типа в пропеллерном режиме следует рассматривать как эксплуатацию оборудования в неисправном состоянии (частично работоспособного). Эксплуатация РК ПЛ-типа в пропеллерном режиме допускается только по согласованию с техническим руководителем ГЭС и заводом-изготовителем.
6.3 Маслоприемник рабочего колеса поворотно-лопастной гидротурбины
6.3.1 Техническое состояние маслоприемника на работающем агрегате оценивают по внешнему виду, величине протечек масла через уплотнения штанги, величине перетоков в системе сервопривода механизма разворота лопастей РК.
6.3.2 На техническое состояние маслоприемника оказывают существенное влияние следующие факторы:
- центровка маслоприемника;
- соосность штанг маслоприемника;
- центровка ГА;
- величина отклонения от перпендикулярного положения линии вала гидрогенератора и зеркального диска ПП;
- соосность подшипников гидрогенератора;
- величины установленных в подшипниках зазоров;
- балансировка ротора.
Методика контроля линии вала должна быть выполнена в соответствии с требованиями приложения Е. Проверка центровки агрегата должна выполняться в соответствии с методикой изготовителя оборудования.
6.3.3 При оценке текущего состояния маслоприемника необходимо учитывать величину и характер относительных вибраций вала у верхнего ГП, радиальную составляющую абсолютных вибрации верхней крестовины генератора и корпуса маслоприемника, которые должны отвечать допустимым нормам в соответствии с требованиями К.5. Превышение этих норм ведет к прогрессивному ухудшению состояния маслоприемника.
Оценку технического состояния маслоприемника необходимо проводить совместно с оценкой технического состояния системы регулирования в соответствии с приложением Д и местными инструкциями.
6.3.4 При контроле технического состояния особое внимание должно быть обращено на состояние узлов и деталей маслоприемника, поломки которых имели место в период эксплуатации. При этом объем и методы контроля определяются исходя из необходимости и получения полной информации о причинах имевшихся нарушений.
6.3.5 Требования к объемам контроля технического состояния узлов и механизмов маслоприемника ПЛ-гидротурбины для определения вида технического состояния представлены в таблице 6.5.
6.3.6 При нормальном состоянии системы регулирования сервомотора механизма разворота лопастей РК и маслоприемника насос работает в режиме 1:(12...2О). Об ухудшении состояния названных узлов свидетельствует режим работы 1:(4...6). Резкое изменение параметров может свидетельствовать о некорректно выполненных ремонтных работах, дефектах оборудования, изменении режима эксплуатации оборудования. При любом стечении обстоятельств требуется проведение анализа показаний и сопоставление их с результатами воздействий.
6.3.7 При оценке состояния узла маслоприемника необходимо исключать влияние на его работу других элементов системы регулирования гидротурбины путем временного ограничения их перемещений или перекрытия задвижек на маслопроводах СНА.
6.3.8 При осмотрах и освидетельствованиях маслоприемника необходимо по результатам измерений оценить протечки и перетоки масла в маслоприемнике и сервомоторе РК, механическое состояние узлов механизма обратной связи (заделка троса, крепление кронштейнов, состояние подшипников, троса или штанги, люфты, зазоры и др.), провести проверку манометров и датчика уровня масла.
23
^ Таблица 6.5 — Нормы контроля технического состояния узлов и механизмов маслоприемника
Контролируемые параметры | Допустимые значения параметров | Методики определения фактических значений параметров | Способ регистрации результатов контроля | Форма контроля |
Внешний вид: наличие потеков масла на корпусе, фланцевых соединениях и опорных конструкциях маслоприемника, наличие и вид натиров, раковин, следов перегрева и других повреждений | В соответствии с конструкторской документацией и требованиями завода-изготовителя | ВИК в соответствии с В.2.1 | Формуляры, протоколы осмотра с указанием повреждений, их местоположения, характера и размеров | Периодический осмотр. Периодический (измерительный) контроль. Техническое обследование |
Состояние уплотняющих элементов | Визуальный осмотр | Акт осмотра, журнал дефектов, срочная инфор-мация для ремонтного и оперативного персонала | ||
Состояние штанги в зоне ее перемещения (при технической возможности) | Визуальный осмотр | |||
Механическое состояние втулок, качество и плотность их запрессовки в корпус, состояние стопорных устройств, степень износа (если не оговорено особо) | Визуальный осмотр | |||
Состояние крепежа и контрящих устройств корпуса маслоприемника и фланцевых соединений | В соответствии с требованиями завода-изготовителя. При отсутствии заводских требований нормы контроля качества в соответствии с требованиями ГОСТ 18442, ГОСТ 22761, ГОСТРИСО 16809, [11] | ВИК, при необходимости УЗК, ТВ | ||
Состояние пар трения «штанга — втулка» | В соответствии с требованиями завода-изготовителя. При отсутствии заводских требований величина протечек и температура не должны превышать установившихся значений, одностороннее смещение штанги не допускается | ВИК |
ГОСТ Р 55260.3.2—2023
Продолжение таблицы 6.5
Контролируемые параметры | Допустимые значения параметров | Методики определения фактических значений параметров | Способ регистрации результатов контроля | Форма контроля |
Соосность штанг маслопри-емника, зазоры между втулками и штангой, соосность корпуса маслоприемника с основанием (ванной) | Зазоры «штанга — втулка» в зоне перемещения штанги должны быть равномерными по окружности втулок и соответствовать проектному значению, монтажным формулярам или требованиям завода-изготовителя. При отсутствии данных следует руководствоваться таблицей 6.6 | ИК в соответствии с требованиями В.2.1 и принятыми на ГЭС картами контроля. ЗО-сканирование узлов маслоприемника | ||
Положение нижнего опорного фланца маслоприемника | Нижний опорный фланец маслоприемника при его установке не должен отклоняться от горизонтали более чем на 0,05 мм на 1 м его диаметра | |||
Положение верхнего опорного фланца основания маслоприемника (ванны) | Негоризонтальность верхнего опорного фланца основания маслоприемника (ванны) не должна превышать значений, приведенных в таблице 6.6 | |||
Зазоры между гребенками в основании маслоприемника и в маслоотражателе | Неравномерность зазоров между гребенками в основании маслоприемника и в маслоотражателе не должна превышать значений, приведенных в таблице 6.6 | ВИК в соответствии с В.2.1 | ||
Сопротивление изоляции корпуса маслоприемника и обратной связи комбинатора | Сопротивление изоляции корпуса маслоприемника и обратной связи комбинатора от корпуса магнитной системы должно быть не менее 1 МОм | — | ||
Соответствие показаний указателей угла разворота лопастей на маслоприемнике, колонке регулятора и фланце лопастей РК | В соответствии с конструкторской документацией | Визуально |
ГОСТ Р 55260.3.2—2023
м
CD
Окончание таблицы 6.5
Контролируемые параметры | Допустимые значения параметров | Методики определения фактических значений параметров | Способ регистрации результатов контроля | Форма контроля |
Уровень масла в ванне мас-лоприемника (величина протечек масла через фланцевые соединения и уплотнения штанг) | Не превышает установившийся уровень. Не допускается повышение уровня до гребенки лабиринтного уплотнения | Визуально по величине протечек, а при наличии датчика уровня в ванне маслоприем-ника — дистанционно | Стационарная контролирующая аппаратура, журнал дефектов, срочная информация для ремонтного и оперативного персонала | Постоянный контроль на работающем оборудовании (1 раз в сутки). Автоматизированный мониторинг (при наличии дистанционного контроля). Периодический(измерительный) контроль |
Вибрация маслованны, верхней крестовины | Параметры не должны превышать значений, установленных заводской документацией и требованиями К.5 | По результатам вибрационных испытаний и штатным системам виброконтроля | Отчет о проведении испытаний. Запись в журнал дефектов, информация для ремонтного и оперативного персонала | Постоянный контроль (по штатным системам — при обходах оборудования 1 раз в смену). Автоматизированный мониторинг (при наличии дистанционного контроля). Техническое обследование (испытания — до и после ремонта, и в межремонтный период) |
ГОСТ Р 55260.3.2—2023
ГОСТ Р 55260.3.2—2023
Таблица 6.6 — Допуски для оценки технического состояния маслоприемника
Диаметр РК, м | 3 | 5 | 7 | 9 и более |
Негоризонтальность верхнего опорного фланца основания маслопри-емника (ванны), мм | 0,10 | 0,10 | 0,15 | 0,20 |
Неконцентричность зазоров в лабиринтном уплотнении маслоотражателя, мм | 0,05 | 0,10 | 0,15 | 0,15 |
Несоосность корпуса маслоприемника с основанием (ванной), мм | 0,05 | 0,05 | 0,10 | 0,10 |
6.4 Направляющий аппарат с сервомоторами
6.4.1 Техническое состояние НА оценивают исходя из состояния кинематики НА, определяющего объем ремонтных восстановительных работ для восстановления проектных параметров. Настоящий стандарт устанавливает требования к оценке технического состояния цилиндрического НА, кинематического механизма и элементов СНА вертикального ГА.
6.4.2 Все кольцевые детали НА, такие как верхнее кольцо НА, крышка турбины и обтекатель крышки турбины, должны быть надежно соединены между собой, а верхнее кольцо еще и с поясом статора: заштифтованы, крепежные детали обтянуты проектным моментом и застопорены. Допускаются местные зазоры не более 0,2 мм на 1/3 глубины стыка.
6.4.3 Требования к оценке технического состояния НА с сервомоторами гидротурбин для определения вида технического состояния по степени работоспособности оборудования в соответствии с классификацией, приведенной в таблице 4.2, и последующего определения ИТС содержатся в таблицах 6.7—6.8.
6.4.4 При контроле технического состояния особое внимание должно быть обращено на состояние узлов и деталей НА и СНА, поломки которых имели место в период эксплуатации. При этом объем и методы контроля определяются исходя из необходимости получения полной информации о причинах имевшихся нарушений. Рекомендации по испытанию СНА содержатся в Д.З.
27
^ Таблица 6.7 — Нормы контроля технического состояния НА для последующего определения ИТС
Группа параметров функционального узла1) | Параметр функционального узла1) | Допустимые значения параметра, установленное НТД значение Н | Методика определения фактического значения параметра Ф функционального узла | Способ регистрации результатов контроля | Форма контроля | |
наименование | размерность | |||||
Коррозионный, абразивный и кавитационный износ лопаток НА | Глубина коррозионного и абразивного износа лопаток НА | мм | Уровень коррозионного и абразивного износа частей НА не должен быть более высоким, чем на прилегающих к нему элементах проточной части, выполненных из аналогичного материала, при этом глубина должна быть не более 5 мм | Визуальный осмотр, ВИК на остановленном ГА при осушенном проточном тракте в соответствии с рекомендациями В.1, В.2.1 | Акт осмотра. Заключение ВИК. Формуляр повреждений. Фотографии с привязкой поврежденных участков к осям ГА, бьефам и берегам или к другим фиксированным элементам для воз-можности сравнения с предыдущими замерами | Техническое обследование (в периоды ремонта при осушенном проточном тракте) |
Скорость коррозионного и абразивного износа лопаток НА | мм/год | 0,1 мм/год (при обнаружении скорости износа более 0,1 мм/год следует проводить специальные восстановительные мероприятия) | Расчетом на базе результатов ВИК | |||
Кавитационный износ лопаток НА | Не допускается | Визуальный осмотр, ВИК на остановленном ГА при осушенном проточном тракте в соответствии с В.1, В.2.1 и ГОСТ Р 55562 | ||||
Коррозионный, абразивный и кавитационный износ верхнего и нижнего колец НА | Глубина коррозионного и абразивного износа верхнего и нижнего колец НА | мм | Не более 5 мм | Визуальный осмотр, ВИК на остановленном ГА при осушенном проточном тракте в соответствии с В.1, В.2.1 | Акт осмотра. Заключение ВИК. Формуляр повреждений. Фотографии с при-вязкой повреж денных участков к осям ГА, бьефам и берегам или к другим фиксированным элементам для возможности сравнения с предыдущими замерами | Техническое обследование (в периоды ремонта при осушенном проточном тракте) |
Скорость коррозионного и абразивного износа верхнего и нижнего колец НА | мм/год | 0,1 мм/год | Расчетом на базе результатов ВИК | |||
Кавитационный износ верхнего и нижнего колец НА | Не допускается | Визуальный осмотр, ВИК на остановленном ГА при осушенном проточном тракте в соответствии с В.1, В.2.1 и ГОСТ Р 55562 |
ГОСТ Р 55260.3.2—2023
Продолжение таблицы 6.7
Группа параметров функционального узла1) | Параметр функционального узла1) | Допустимые значения параметра, установленное НТД значение Н | Методика определения фактического значения параметра Ф функционального узла | Способ регистрации результатов контроля | Форма контроля | |
наименование | размерность | |||||
Состояние подшипников лопаток, втулок цапф лопаток2) | Зазоры в подшипниках и втулках цапф лопаток | мм | Зазоры в пределах допусков, предусмотренных в чертежах | Визуальный осмотр, ИК, ВИК на остановленном ГА при осушенном проточном тракте в соответствии с рекомендациями разделов В.1, В.2.1 | Заключение ВИК. Формуляр зазоров | Техническое обследование (в периоды ремонта при осушенном проточном тракте) |
Износ и дефекты цапф лопаток и втулок | Трещины, отслоение и выкрашивание не допускаются | ВИК, ПВК или МПД или ВТК на остановленном ГА при осушенном проточном тракте в соответствии с В.2 | Заключение ВИК, ПВК или МПД или ВТК. Формуляр повреждений | |||
Количество втулок цапф лопаток, требующих замены в КР или межремонтный период | % от общего числа | По количеству забракованных по результатам контроля | Акт, журнал дефектов | |||
Состояние узлов и деталей кинематики НА3) | Зазоры в узлах и деталях кинематики НА | мм | Зазоры в пределах допусков, предусмотренных в чертежах | Измерительный контроль | Формуляр зазоров | Техническое обследование (в периоды ремон-та при осушенном проточном тракте) |
Суммарный люфт в узлах и деталях кинематики НА | % от полного хода сервомотора | Не более 0,5 % от полного хода сервомотора | Измерительный контроль | Формуляр | ||
Повреждения срезных пальцев или талрепов в межремонтный период | Не допускаются повторяющиеся дефекты (поломки) | Визуальный осмотр, ВИК в соответствии с В.2.1 | Акт осмотра. Заключение ВИК. Журнал дефектов с отметкой о повторяющемся повреждении (если применимо) | |||
Увеличение перестановочных усилий | Усилия в пределах допусков завода-изготовителя | В соответствии с Д.3.4 | Отчет по испытаниям по определению перестановочных усилий | |||
Трещины в деталях кинематики | шт. | Не допускается | ВИК, ПВК, МПД, ВТК, УЗК на остановленном ГА при осушенном проточном тракте в соответствии с В.2 | Заключения и протоколы по неразрушающему контролю, журнал дефектов |
ГОСТ Р 55260.3.2—2023
“ Продолжение таблицы 6.7
Группа параметров функционального узла1) | Параметр функционального узла1) | Допустимые значения параметра, установленное НТД значение Н | Методика определения фактического значения параметра Ф функционального узла | Способ регистрации результатов контроля | Форма контроля | |
наименование | размерность | |||||
Состояние уплотнений лопаток по перу и торцам4) | Протечки через НА | — | Допускаются протечки, приводящие к остановке ГА на выбеге без торможения | Визуально | Акт | Техническое обследование (в периоды ремонта при осушен-ном проточном тракте) |
Зазоры по высоте лопаток без резинового уплотнения | мм | Размеры допускаемых зазоров в НА, не имеющих уплотнений, нормируются в зависимости от высоты пера лопатки или диаметра РК гидротурбины (см. таблицу 6.9) | Измерительный контроль: зазоры измеряют в трех точках по высоте лопаток щупом при закрытом положении НА; при высоте лопаток менее 500 мм измерения производят в двух точках по их высоте | Формуляр зазоров | ||
Зазоры по высоте лопаток с резиновым уплотнением | мм | Зазоры по металлу в зоне контакта между соседними лопатками должны быть равномерными по высоте пера и составлять 0,5— 1,0 мм. Должно обеспечиваться плотное и равномерное сжатие резины по всей длине лопатки без зазоров при сервомоторе, находящемся на стопоре | Измерительный контроль: зазоры измеряют в трех точках по высоте лопатки щупом при сервомоторе, находящемся на стопоре. Резина уплотнения при измерениях должна быть сжата равномерно без зазоров по всей высоте пера | |||
Суммарная длина местных зазоров между смежными лопатками без резиновых уплотнений | % длины тела лопатки | Суммарная длина всех местных зазоров между двумя смежными лопатками, превышающих норму, не должна превышать 20 % от длины пера лопатки | Расчетным способом | |||
Количество торцевых уплотнений, требующих ремонта (замены) | % от общего числа | По количеству забракованных по результатам контроля | Акт, журнал дефектов |
ГОСТ Р 55260.3.2—2023
Окончание таблицы 6.7
Группа параметров функционального узла1) | Параметр функционального узла1) | Допустимые значения параметра, установленное НТД значение Н | Методика определения фактического значения параметра Ф функционального узла | Способ регистрации результатов контроля | Форма контроля | |
наименование | размерность | |||||
Состояние регулирующего кольца НА5) | Износ трущихся деталей и направляющих регулирующего кольца | % | Нормы завода-изготовителя в пределах конструктивных зазоров. При отсутствии данных — 0,001 от диаметра кольца,но не более 5 мм | Визуальный осмотр. Измерительный контроль | Акт осмотра. Формуляр повреждений | Техническое обследование (в периоды ремонта при осушенном проточном тракте) |
Перекосы в установке сервомоторов и их штоков | — | Не допускаются | ||||
Трещины на креплении опор сервомоторов | — | Не допускаются | ВИК, при необходимости ПВК или МПД или ВТК | |||
Повышенные перемещения и люфты в узлах трения | — | Не допускаются | Визуальный осмотр. Измерительный контроль |
1) В соответствии с [1].
2) Соответствует группе параметров функционального узла «Подшипники лопаток, втулки цапф лопаток» [1].
3) Соответствует группе параметров функционального узла «Узлы и детали кинематики» [1].
4) Соответствует группе параметров функционального узла «Уплотнение лопаток по перу и торцам» [1].
5) Соответствует группе параметров функционального узла «Регулирующее кольцо НА» [1].
ГОСТ Р 55260.3.2—2023
“ Таблица 6.8 — Нормы контроля технического состояния НА для определения вида технического состояния по степени работоспособности оборудования
Контролируемые параметры1) | Допустимые значения параметров | Методики определения фактических значений параметров | Способ регистрации результатов контроля | Форма контроля |
Состояние лопаток НА в зоне перехода пера к цапфам (наличие трещин) | Трещины не допускаются | ВИК, ПВК, МПД, ВТК, УЗК на остановленном ГА при осушенном проточном тракте по В.2. При повторяющемся выявлении трещин на лопатках, при необходимости, следует проводить контроль металла путем вырезки образцов для металлографического анализа и определения свойств металла по В.З | Заключения и протоколы по видам неразрушающего контроля. Формуляр повреждений | Техническое обследование (в периоды ремонта при осушенном проточном тракте) |
Состояние резиновых уплотнений по перу и торцам лопаток, пазов и контактных поясков лопаток НА | Не допускается отсутствие уплотнителя | Визуальный осмотр. В случае обнаружения повреждений или отсутствия уплотнителя необходимо оценить состояние пазов под закладку нового шнура, а также входных кромок на торцах лопаток | Акт осмотра. Формуляр повреждений | Техническое обследование (в периоды ремонта при осушенном проточном тракте) |
Состояние регулирующего кольца (наличие трещин, степень износа направляющих регулирующего кольца при открытии и закрытии НА в диаметральном и вертикальном направлениях, наличие перекосов установки сервомоторов и их штоков, наличие трещин в местах крепления опор сервомоторов) | Не допускаются: трещины, повышенные перемещения регулирующего кольца и люфт (в этом случае производится разборка узлов трения с последующей оценкой их состояния) | Визуальный осмотр. При необходимости ВИК, ПВК, МПД, ВТК, УЗК на остановленном ГА при осушенном проточном тракте по В.2 | Заключения и протоколы по видам неразрушающего контроля. Формуляр повреждений | Периодические осмотры. Техническое обследование (в периоды ремонта при осушенном проточном тракте) |
Износ трущихся поверхностей кинематики (наличие натиров и иных повреждений) | Допускаются незначительные натиры, не приводящие к зазорам и люфтам, превышающим нормативные значения | Визуальный осмотр. Измерительный контроль | Акт осмотра. Формуляр повреждений | Техническое обследование (в периоды ремонта при осушенном проточном тракте) |
ГОСТ Р 55260.3.2—2023
Продолжение таблицы 6.8
Контролируемые параметры1) | Допустимые значения параметров | Методики определения фактических значений параметров | Способ регистрации результатов контроля | Форма контроля |
Состояние уплотнений цапф лопаток | Не допускается разрушение или значительное повреждение уплотнений. Уплотнительные манжеты в подшипниках направляющих лопаток должны обеспечивать достаточную герметичность. Протечки воды через манжеты допускаются только небольшими прерывистыми струйками, полностью проходящими через сливные трубки | Визуальный осмотр | Акт осмотра. Формуляр повреждений | Постоянный контроль (протечки). Техническое обследование (в периоды ремонта при осушенном проточном тракте) |
Состояние сервомоторов (износ поршней, цилиндров, штоков, уплотнений поршней) | Не допускаются трещины. Допускаются перетоки через поршень, величина которых обеспечивает цикл насосов МНУ не более 1:10 | Визуальный осмотр. При необходимости ВИК, ПВК или МПД или ТВК | Акт осмотра. Формуляр повреждений | Постоянный контроль (протечки). Периодический (измерительный) контроль. Техническое обследование (в периоды ремонта при осушенном проточном тракте) |
Натяг сервомотора НА | Величина натяга сервомотора НА должна соответствовать документации завода-изготовителя. При этом минимальное давление в МНУ, обеспечивающее проектный натяг, не должно превышать заданного заводом. При отсутствии документации натяг проверяют при минимальном давлении в МНУ, обеспечивающем перемещение регулирующих органов. Давление натяга должно превышать давление, требуемое на разворот лопаток на 0,08—0,12 Рном. | Измерительный контроль | Формуляр | Периодический (измерительный) контроль. Техническое обследование (в периоды ремонта при осушенном проточном тракте) |
ГОСТ Р 55260.3.2—2023
^ Продолжение таблицы 6.8
Контролируемые параметры1) | Допустимые значения параметров | Методики определения фактических значений параметров | Способ регистрации результатов контроля | Форма контроля |
Натяг сервомотора НА | Величина натяга должна составлять 1 % —1,5 % от полного хода сервомотора. После снятия давления установленная величина натяга должна обеспечивать плотное закрытие НА без зазоров и перекосов. При этом резиновый шнур между лопатками должен быть сжат до величины зазора между металлическими поверхностями лопаток 0,5—0,1 мм. При зазоре между вилкой стопора и упором поршня 0,5—0,8 мм натяг при снятом давлении в сервомоторах должен сохраняться (обеспечивать плотность закрытия НА), несмотря на возврат поршня сервомотора со стопором на величину зазора и поршня без стопора на большую величину | |||
Состояние фланцевых соединений | Протечки не допускаются. Все фланцевые и стыковые соединения частей НА, находящиеся под воздействием водотока, должны быть уплотнены и не должны допускать протечек; в этих соединениях резкие уступы не допускаются | Визуальный осмотр | Запись в журнале осмотра | Постоянный контроль (протечки) |
Время выбега ГА после подачи команды на останов и закрытие НА | Увеличение времени выбега ГА после подачи команды на останов и закрытие НА свидетельствует об ухудшении состояния НА | По штатным средствам контроля | Запись в журнале осмотра. Журнал дефектов | Постоянный контроль |
Возобновление вращения ротора ГА после полной остановки и отключения тормозов | Не допускается | |||
Наличие значительных протечек воды через уплотнения цапф лопаток НА | Допускаемые значения принимаются в соответствии с технической документацией на ГА или рекомендациями завода-изготовителя |
ГОСТ Р 55260.3.2—2023
Продолжение таблицы 6.8
Контролируемые параметры1) | Допустимые значения параметров | Методики определения фактических значений параметров | Способ регистрации результатов контроля | Форма контроля |
Повторяющиеся повреждения предохранительных устройств на рычагах лопаток (разрывных болтов, срезных штифтов, пальцев и др.) | Не допускаются | На основании анализа журнала дефектов и формуляров повреждений | ||
Наличие шума текущей воды в проточной части гидротурбины при закрытом НА | Не допускается | |||
Увеличение потерь сжатого воздуха (увеличение частоты подкачки) при работе ГА в режиме СК | Допускаемые значения принимаются в соответствии с технической документацией на ГА или рекомендациями завода-изготовителя | По штатным средствам контроля | ||
Увеличение протечек и перетоков в сервомоторах НА (изменение цикла «включение-выключение» насосов МНУ) | Допускаемые значения принимаются в соответствии с технической документацией на ГА или рекомендациями завода-изготовителя | По штатным средствам контроля | ||
Увеличение частоты включения ле-кажного агрегата | Допускаемые значения принимаются в соответствии с технической документацией на ГА или рекомендациями завода-изготовителя | По штатным средствам контроля | ||
Наличие стуков и заеданий при перемещении регулирующего кольца, необычное смещение элементов кинематики (например, при разрушении срезного пальца) | Не допускается | — | ||
Повышенные перестановочные усилия сервомоторов НА | Допускаемые значения принимаются в соответствии с технической документацией на ГА или рекомендациями завода- из гото вител я | При наличии технической возможности по данным автоматизированного мониторинга в соответствии с Д.3.4 | Автоматизированный мониторинг (при наличии дистанционного контроля). Техническое обследование (в периоды ремонта при осушенном проточном тракте) |
ГОСТ Р 55260.3.2—2023
Окончание таблицы 6.8
Контролируемые параметры1) | Допустимые значения параметров | Методики определения фактических значений параметров | Способ регистрации результатов контроля | Форма контроля |
Размер полного открытия НА | Величина полного открытия смонтированного НА должна соответствовать проектной. Общее отклонение допускается только в сторону увеличения. Отклонение размеров полного открытия между разными лопатками не должно превышать 3 % | Измерительный контроль: измеряют нутромером по минимальному расстоянию в свету (просвет) между полностью развернутыми соседними лопатками | Формуляр замеров | Техническое обследование (в периоды ремонта при осушенном проточном тракте) |
Суммарные люфты и мертвый ход в обратной связи (в жестких обратных связях в случае необходимости люфты должны определяться поэлементно для выявления изношенных шарниров) | В соответствии с конструкторской документацией | Измерительный контроль | Формуляр замеров | Техническое обследование (в периоды ремонта при осушенном проточном тракте) |
1) Контролируемые параметры, не вошедшие в таблицу 6.7. |
ГОСТ Р 55260.3.2—2023
ГОСТ Р 55260.3.2—2023
Таблица 6.9 — Размеры допускаемых зазоров в НА в зависимости от высоты пера лопатки или диаметра РК
Параметр | Значение, мм | |||
Высота лопатки | 500 | 1000 | 1500 | 2000 и более |
Диаметр РК | 2000 | 3000 | 4000 | 5000 и более |
Зазор | 0,05 | 0,10 | 0,15 | 0,20 |
6.5 Крышка турбины
6.5.1 Оценку технического состояния крышки гидротурбины следует производить с учетом ее функций в качестве элемента, отделяющего проточный тракт гидротурбины от помещений ГЭС, а также места размещения конструктивных узлов, агрегатов и деталей ряда элементов и технических систем ГА (опорных конструкций ПП гидрогенератора и направляющего подшипника гидротурбины, клапана срыва вакуума, системы откачки воды, сервомоторов и кинематики НА, стопорных и предохранительных устройств НА, аппаратуры и трубопроводов системы перевода ГА в режим СК, лекажного агрегата и др.).
6.5.2 Крышка гидротурбины является сборником протечек воды из проточной части через неплотности уплотнений ряда узлов и деталей. Также в крышку турбины может попадать масло в случае нарушений в работе уплотнений из всех расположенных выше маслосодержащих элементов ГА (масло-ванн, маслопроводов, арматуры).
По объему и содержанию протечек, откачиваемых с крышки гидротурбины, можно косвенно оценить качество работы водяных и масляных уплотнений, состояние стыков и фланцевых соединений.
6.5.3 Требования к оценке технического состояния крышки гидротурбины для определения вида технического состояния по степени работоспособности оборудования в соответствии с классификацией, приведенной в таблице 4.2, и последующего определения ИТС содержатся в таблицах 6.10—6.11.
6.5.4 При контроле технического состояния особое внимание должно быть обращено на состояние узлов и деталей крышки гидротурбины, поломки которых имели место в период эксплуатации. При этом объем и методы контроля определяются, исходя из необходимости и получения полной информации о причинах имевшихся нарушений.
6.5.5 Выявление неудовлетворительной работы (состояния) конструкций и систем, связанной с их размещением на крышке гидротурбины, может потребовать технического обследования (испытаний) крышки по специальным программам, в том числе связанным с оценкой ее прочности и жесткости.
6.5.6 Смещение оси крышки гидротурбины относительно оси вала допускается в зависимости от диаметра РК в пределах, приведенных в таблице 6.12.
6.5.7 В конструкциях гидротурбин с подшипниками лопаток НА, расположенными в крышке турбины, центровка крышки турбины производится по соосности лопаток со своими подшипниками, с проверкой вращения лопаток.
37
w Таблица 6.10 — Нормы контроля технического состояния крышки гидротурбины для последующего определения ИТС
Группа параметров функционального узла1) | Параметр функционального узла1) | Допустимые значения параметра, установленное НТД значение Н | Методика определения фактического значения параметра Ф функционального узла | Способ регистрации результатов контроля | Форма контроля | |
наименование | размерность | |||||
Вибрационное состояние | Вертикальная вибрация | мкм | Параметры не должны превышать значений, установленных заводской документацией, ГОСТ Р 70810 и требованиями К.5 | Переносная виброизме-рительная аппаратура, при наличии — штатные датчики. В соответствии с К.5 и ГОСТ Р 70810 | Отчет о проведении испытаний. Запись в журнал дефектов, информация для ремонтного и оперативного персонала | Постоянный контроль (по штатным системам — при обходах оборудования один раз в смену). Автоматизированный мониторинг (при наличии дистанционного контроля). Техническое обследование (испытания — до и после ремонта, и в межремонтный период) |
Тенденция отклонения вертикальной вибрации крышки турбины по сравнению с исходным значением Фо в сопоставимых условиях (в соответствии с НТД, требования которой применяются при оценке) | мкм | Расчетом на базе результатов виброконтроля | Запись в журнал осмотра, информация для ремонтного и оперативного персонала | Периодический (измерительный) контроль Техническое обследование |
ГОСТ Р 55260.3.2—2023
Окончание таблицы 6.10
Группа параметров функционального узла1) | Параметр функционального узла1) | Допустимые значения параметра, установленное НТД значение Н | Методика определения фактического значения параметра Ф функционального узла | Способ регистрации результатов контроля | Форма контроля | |
наименование | размерность | |||||
Наличие и объем протечек | Цикл работы (отношение времени работы ко времени останова) насосов осушения крышки турбины (дренажных насосов)2) | Допускается непрерывная работа основного насоса | По штатным системам контроля | Запись в журнале осмотра | Постоянный контроль(при обходах оборудования один раз в смену) | |
Протечки масла3) | — | Протечки масла не допускаются | Визуальный осмотр | Формуляры, акты, схема замеров | ||
Состояние крепежных деталей | Трещины в крепежных деталях | — | Не допускаются | ВИК, ПВК, МПД, ВТК, УЗК на остановленном ГА при осушенном проточном тракте в соответствии с В.2 и [11] | Заключения и протоколы по неразрушающему контролю. Журнал дефектов. Формуляр повреждений. Фотографии | Периодический осмотр (на остановленном ГА со стороны шахты гидротурбины). Техническое обследование (в периоды ремонта при осушенном проточном тракте) |
Повреждение резьбы крепежных деталей | — | Не допускаются на резьбовой поверхности надрывы, волосовины, рванины, сколы, смятия, вытяжка и другие дефекты ниток резьбы | ||||
Выкрашивание ниток резьбы | — | Не допускается | ||||
Крепежные детали (необходимость замены) | Не допускается использование крепежных элементов с трещинами, указанными выше дефектами резьбы, с отклонениями по марке и/или твердости материала (включая соответствие твердости в паре «шпилька (болт)-гайка»), с искажением геометрической формы и/или отклонениями от размеров, указанных в конструкторской документации | На основе анализа результатов контроля и истории эксплуатации |
1) В соответствии с [1].
2) Соответствует параметру «Цикл работы (отношение времени работы ко времени останова) насосов осушения шахты турбины (дренажных насосов)» [1].
3) Соответствует параметру «Протечки масла через крышку» [1].
ГОСТ Р 55260.3.2—2023
£ Таблица 6.11 — Нормы контроля технического состояния крышки гидротурбины для определения вида технического состояния по степени работоспособности оборудования
Контролируемые параметры1) | Допустимые значения параметров | Методики определения фактических значений параметров | Способ регистрации результатов контроля | Форма контроля |
Давление под крышкой | Параметры не должны превышать значений, установленных заводской документацией | По штатным системам измерений | Запись в журнал дефектов, информация для ремонтного и оперативного персонала | Постоянный контроль |
Уровень воды в крышке (наличие и объем протечек через уплотнения цапф лопаток НА, уплотнение вала в крышке ТП и крышке гидротурбины, фланцевые соединения крышки, люки, клапаны, сливные и дренажные устройства) | Параметры не должны превышать значений, установленных заводской документацией. Допустимый уровень — объем протечек не превышает производительности насосов осушения | Визуальный и автоматизированный дистанционный контроль уровня воды в крышке | Запись в журнале осмотра | Постоянный контроль (при обходах оборудования один раз в смену). Автоматизированный мониторинг (при наличии дистанционного контроля) |
Состояние крышки турбины по кавитационным разрушениям, гидроабразивному и коррозионному износу, внутренним сколам, трещинам и иным механическим повреждениям, включая зоны за НА в месте стыка крышки и верхнего кольца НА и состояние металла вокруг отверстий в крышке | Трещины не допускаются. Оценка кавитационных повреждений в соответствии с ГОСТ Р 55562. Допустимость механических повреждений оценивается на основании оценки усталостной прочности и трещи-ностойкости конструкции с учетом наличия повреждений | Визуальный осмотр, ВИК на остановленном ГА при осушенном проточном тракте в соответствии с В.1, В.2.1 и ГОСТ Р 55562. При необходимости — ПВК, ВТК, МПД | Акт осмотра. Заключение, протоколы по неразрушающему контролю. Формуляр повреждений. Фотографии | Периодический осмотр (на остановленном ГА при осушенном проточном тракте). Техническое обследование (в периоды ремонтов при осушенном проточном тракте) |
Наличие масла на поверхностях деталей и оборудования и в крышке | Протечки масла не допускаются | Визуальный осмотр | Запись в журнале осмотра. Акт осмотра | Постоянный контроль (при обходах оборудования 1 раз в смену) |
Эффективность работы эжектора | — | — | Запись в журнале осмотра | Постоянный контроль (при обходах оборудования 1 раз в смену) |
Наличие посторонних звуков в проточной части | — | — | Запись в журнале осмотра | Постоянный контроль (при обходах оборудования 1 раз в смену) |
ГОСТ Р 55260.3.2—2023
Окончание таблицы 6.11
Контролируемые параметры1) | Допустимые значения параметров | Методики определения фактических значений параметров | Способ регистрации результатов контроля | Форма контроля |
Состояние элементов крепежа | Нормы контроля качества в соответствии с требованиями ГОСТ 18442, ГОСТ 22761, ГОСТ Р ИСО 16809, [11] | ВИК, ПВК, МПД, ВТК, УЗК на остановленном ГА при осушенном проточном тракте в соответствии с В.2 и [11] | Заключения и протоколы по неразрушающему контролю. Журнал дефектов. Формуляр повреждений. Фотографии | Периодический осмотр (на остановленном ГА при осушенном проточном тракте). Техническое обследование (в периоды ремонта при осушенном проточном тракте) |
Момент затяжки крепежных изделий | В соответствии с конструкторской документацией или рекомендациями завода-изготовителя. При отсутствии информации допускается устанавливать момент затяжки ответственных крепежных изделий на основании рекомендаций специализированных организаций | Одним из трех способов: 1) затяжкой гаек динамометрическим ключом; 2) завертыванием гаек на расчетный угол; 3) измерением упругого удлинения болта при затяжке | Протокол (формуляр) | Периодический осмотр (на остановленном ГА при осушенном проточном тракте). Техническое обследование (в периоды ремонта при осушенном проточном тракте) |
Показания контрольно-измерительных приборов в шахте турбины | В соответствии с конструкторской и эксплуатационной документацией | По штатным системам измерений | Запись в журнале осмотра | Постоянный контроль |
1) Контролируемые параметры, не вошедшие в таблицу 6.10. |
ГОСТ Р 55260.3.2—2023
ГОСТ Р 55260.3.2—2023
Таблица 6.12 — Смещение оси крышки гидротурбины
Диаметр РК, м | Величина смещения, мм |
<3,0 | 0,75 |
> 3,0 и < 5,0 | 1,50 |
> 5,0 и < 7,5 | 2,0 |
> 7,5 и < 9,5 | 2,5 |
> 9,5 и < 10,5 | 3,0 |
6.6 Проточная часть гидротурбины
6.6.1 Техническое состояние проточной части гидротурбины оценивают по степени ее износа, появлению внутренних дефектов и повреждений, определяющих объем ремонтных восстановительных работ для восстановления проектных параметров.
Проточная часть гидротурбины вертикального ГА состоит из КРК ПЛ гидротурбины, фундаментного кольца (для РО гидротурбины), облицовки спиральной камеры, облицовки отсасывающей трубы, статора гидротурбины и закладных элементов проточной части турбины (водозаборов, приямков, сбросных трубопроводов).
6.6.2 Требования к обработанным поверхностям закладных частей гидротурбин, подверженных воздействию потока воды, приведены в Б.8.1.
6.6.3 Смонтированные конструкции проточной части гидротурбин должны быть тщательно уплотнены в местах соединения отдельных элементов и не должны допускать протечек. Плотным считается соединение, в которое щуп толщиной 0,05 мм не проходит. Допускаются местные неплотности, в которые щуп 0,05 мм проходит на глубину не более 20 % ширины стыка данного соединения.
6.6.4 При контроле технического состояния особое внимание должно быть обращено на состояние узлов и деталей проточной части, поломки которых имели место в период эксплуатации. При этом объем и методы контроля определяются, исходя из необходимости и получения полной информации о причинах имевшихся нарушений.
6.6.5 Требования к оценке технического состояния проточной части гидротурбины для определения вида технического состояния по степени работоспособности оборудования в соответствии с классификацией, приведенной в таблице 4.2, и последующего определения ИТС содержатся в таблицах 6.13—6.14.
42
Таблица 6.13 — Нормы контроля технического состояния проточной части гидротурбин для последующего определения ИТС
Группа параметров функционального узла1) | Параметр функционального узла1) | Допустимые значения параметра, установленное НТД значение Н | Методика определения фактического значения параметра Ф функционального узла | Способ регистрации результатов контроля | Форма контроля | |
наименование | размерность | |||||
Механические повреждения | Повреждения и трещины проточной части | Не допускаются усталостные трещины и механические повреждения, параметры которых находятся за пределами НТД. В соответствии с нормами контроля по каждому виду неразрушающего контроля металла РК (см. В.2, В.З, В.4) | ВИК, ПВК или МПД или ВТК на остановленном ГА при осушенном проточном тракте в соответствии с В.2. Визуальный осмотр состояния бетона для бетонных спиральных камер, отсасывающей трубы | Заключения и протоколы по неразрушающему контролю. Формуляр повреждений | Периодический осмотр (на остановленном ГА при осушенном проточном тракте). Техническое обследование (в периоды ремонта при осушенном проточном тракте) | |
Искажение формы КРК от формы, определенной организацией-изготовителем | мм | Проектное значение должно соответствовать нормативам конструкторской и/или монтажной документации. При отсутствии соответствующих документов зазор «камера —лопасть» не должен превышать 0,001 от диаметра РК. Допустимые значения в пределах 20 % от заданного проектного зазора «камера — лопасть» | ИК на остановленном ГА при осушенном проточном тракте в соответствии с Б.З—Б.4 | Формуляр (рисунок Б.З.2) с указанием схемы замеров | Техническое обследование (в периоды ремонта при осушенном проточном тракте) |
ГОСТ Р 55260.3.2—2023
Окончание таблицы 6.13
Группа параметров функционального узла1) | Параметр функционального узла1) | Допустимые значения параметра, установленное НТД значение Н | Методика определения фактического значения параметра Ф функционального узла | Способ регистрации результатов контроля | Форма контроля | |
наименование | размерность | |||||
Состояние КРК | Кавитационная эрозия | кг | В соответствии с гарантиями завода-изготовителя с учетом рекомендаций ГОСТ Р 55562 | На остановленном ГА при осушенном проточном тракте в соответствии с В.5 и ГОСТ Р 55562 | Акты осмотров. Формуляры и схемы замеров (см. рисунки В.4.9, В.4.10, В.4.11). Фотографии. Технические отчеты | Периодический осмотр (на остановленном ГА при осушенном проточном тракте). Техническое обследование (в периоды ремонта при осу-шенном проточном тракте) |
Дефекты прилегания облицовки КРК и СП к штрабному бетону | % от общей площади | В соответствии с требованиями завода-изготовителя, а при их отсутствии допускается 0,5 % от общей площади | Простукивание (метод свободных колебаний) в соответствии с В.5 | Акты осмотров. Формуляры и схемы замеров. Технические отчеты | ||
Повреждения креплений отъемного сегмента | Не допускается | ВИК, при необходимости УЗК, ТВ | Акты осмотров. Заключения по неразрушающему контролю. Формуляры и схемы замеров | |||
Состояние штраб-ного бетона | Площадь участков разрушенного бетона | % от общей площади | В соответствии с требованиями завода-изготовителя и монтажной документацией | Определяют качество прилегания облицовки КРК к штрабному бетону, ребрам жесткости и другим частям КРК, а также плотность прилегания облицовки спиральной камеры к бетону методом простукивания (метод свободных колебаний) в соответствии с В.5 | Формуляры и схемы замеров с указанием площади и координат относительно характерных точек КРК, описания заобли-цовочных пустот | |
Глубина участков разрушенного бетона | м | |||||
1) В соответствии с [1]. |
ГОСТ Р 55260.3.2—2023
Таблица 6.14 — Нормы контроля технического состояния проточной части гидротурбины для определения вида технического состояния по степени работоспособности оборудования
Контролируемые параметры1) | Допустимые значения параметров | Методики определения фактических значений параметров | Способ регистрации результатов контроля | Форма контроля |
Давление, вакуум, пульсация давления в проточной части | Проектно-конструкторская, монтажная документация, данные завода-изготовителя, СТО ГЭС | На работающем оборудовании по данным штатных систем измерений: непрерывно при наличии датчиков дистанционного контроля, визуально не реже 1 раза в смену при обходах | Журнал дефектов, суточная ведомость | Постоянный контроль. Автоматизированный мониторинг |
Наличие механических, коррозионных, кавитационных и гидроабразивных повреждений металлических поверхностей (облицовки КРК и спиральной камеры, отъемного сегмента, СП, колонн статора) | Допустимую норму уноса металла определяют по конструкторской документации (гарантиям) завода-изпэтови-теля, а при ее отсутствии — на основании ГОСТ Р 55562. Не допускается эксплуатация КРК, спиральных камер, колонн статора с трещинами, сквозными отверстиями и значительными механическими повреждениями конструктивных частей | Визуальный осмотр, ВИК на остановленном ГА при осушенном проточном тракте в соответствии с В.1, В.2.1 и ГОСТ Р 55562. Порядок осмотра металлических облицовок спиральной камеры и отсасывающей трубы соответствует порядку, рекомендованному для осмотра КРК | Акт осмотра. Заключение ВИК. Формуляр повреждений. Фотографии с указанием характера, площади и глубины повреждений с привязкой к характерным точкам КРК, краткое описание для сравнения с результатами предыдущих осмотров | Периодический осмотр (на остановленном ГА при осушенном проточном тракте). Техническое обследование (в периоды ремонта при осушенном проточном тракте) |
Повреждения (дефекты) конструктивных и ремонтных сварных швов и зон наплавок | В соответствии с требованиями конструкторской документации и норм оценки качества для каждого вида неразрушающего контроля | Неразрушающий контроль в соответствии с В.2, В.5 | Заключения и протоколы неразрушающего контроля. Формуляры повреждений. Фотографии | |
Геометрия КРК | В соответствии с требованиями конструкторской документации. При отсутствии требований к конструкторской документации максимально допустимые отклонения по критерию однородности (отношение измеренного значения к среднему) рекомендуется принимать в соответствии с [10] | ИК в соответствии с документацией завода-изготовителя или с требованиями раздела Б.4: габаритные размеры и форма сферической части КРК (отклонение формы от окружности) | Акты, формуляры и схемы замеров, отчет о проведении измерений |
ГОСТ Р 55260.3.2—2023
Окончание таблицы 6.14
Контролируемые параметры1) | Допустимые значения параметров | Методики определения фактических значений параметров | Способ регистрации результатов контроля | Форма контроля |
Толщина облицовки КРК, спиральной камеры | В соответствии с требованиями конструкторской документации. При наличии уноса металла толщину облицовки восстанавливают до проектного значения | ИК (УЗТ в соответствии с В.2.5): измеряют толщину облицовки в характерных точках | Протокол измерения толщины. Формуляр состояния КРК и спиральной камеры. Схемы замеров с привязкой к характерным точкам КРК и спиральной камеры | |
Состояние (повреждения, дефекты) пробок заглушек, штуцеров, ниппелей, отводящих и подводящих трубопроводов, водозаборов, сливных приямков, люков, лаза в камеру отъемного сегмента, сопряжения облицовки с закладными частями турбины | Не допускаются трещины, а также иные повреждения и дефекты, превышающие нормы оценки качества для каждого вида неразрушающего контроля | Визуальный осмотр. При необходимости — неразрушающий контроль в соответствии с В.2 | Акт осмотра. Формуляр повреждений. Заключения и протоколы неразрушающего контроля | |
Состояние отъемного сегмента: - общее состояние конструктивных частей сегмента и сопрягающихся с ним конструктивных частей КРК; - состояние крепежа, талрепов, домкратов, закладных и крепежных элементов в нише бетонного массива; - качество и состояние соединения облицовок отъемного сегмента | Не допускаются трещины. Нормы контроля качества крепежа — в соответствии с требованиями ГОСТ 18442, ГОСТ 22761, ГОСТ Р ИСО 16809, [11] | Визуальный осмотр. При необходимости — неразрушающий контроль в соответствии с В.2 | Акт осмотра. Формуляр повреждений. Заключения и протоколы неразрушающего контроля | |
1) Контролируемые параметры, не вошедшие в таблицу 6.1. |
ГОСТ Р 55260.3.2—2023
ГОСТ Р 55260.3.2—2023
6.7 Подшипник направляющий турбинный
6.7.1 Техническое состояние ТП гидротурбины следует оценивать совместно с валом ГА.
6.7.2 К стыковым соединениям корпуса, вкладыша и ванн направляющего подшипника предъявляются требования, относящиеся к плотным соединениям деталей гидротурбин (см. 6.6.3):
- смонтированные конструкции должны быть тщательно уплотнены в местах соединения отдельных элементов и не должны допускать протечек;
- все фланцевые соединения, находящиеся под воздействием водотока, должны быть уплотнены и не должны допускать протечек (в этих соединениях резкие уступы не допускаются);
- крепежные детали обтянуты проектным моментом и застопорены.
6.7.3 Требования к оценке технического состояния ТП с водяной и масляной смазкой для определения вида технического состояния по степени работоспособности оборудования в соответствии с классификацией, приведенной в таблице 4.2, и последующего определения ИТС содержатся в таблицах 6.15—6.17.
6.7.4 При контроле технического состояния особое внимание должно быть обращено на состояние деталей ТП, поломки которых имели место в период эксплуатации. При этом объем и методы контроля определяются исходя из необходимости и получения полной информации о причинах имевшихся нарушений.
47
£ Таблица 6.15 — Нормы контроля технического состояния ТП и вала для последующего определения ИТС
Группа параметров функционального узла1) | Параметр функционального узла1) | Допустимые значения параметра, установленное НТД значение Н | Методика определения фактического значения параметра Ф функционального узла | Способ регистрации результатов контроля | Форма контроля | |
наименование | размерность | |||||
Водяная смазка и охлаждение подшипника | Отклонение давления в напорной ванне подшипника от нижней (далее — Ни) или верхней (далее — Нв) границы диапазона значений, установленных НТД | кгс/см2 | Соответствие давления требованиям завода-изготовителя | Штатные средства контроля | Запись в суточной ведомости | Постоянный контроль |
Отклонение расхода воды на смазку и охлаждение от Ни или Нв границы диапазона значений, установленных НТД | л/с | Соответствие расхода воды требованиям завода-изготовителя. Необходимо отмечать увеличение расхода воды на смазку и охлаждение подшипника при обходах | Штатные средства контроля, например, дифманометр или иные средства контроля. Визуально — указатель наличия струи | Запись в журнале дефектов. Акт осмотра | Постоянный контроль | |
Состояние вала в зоне подшипника | Относительное виброперемещение2) вала в зоне подшип ника | мм | Параметры не должны превышать значений,установленных заводской документацией, ГОСТ Р 70810 и требованиями К.5 | В соответствии с рекомендациями К.5 и ГОСТ Р 70810 | Отчет о проведении испытаний. Запись в суточную ведомость, журнал дефектов, информация для ремонтного и оперативного персонала | Постоянный контроль (по штатным системам — при обходах оборудования 1—2 раза в смену). Автоматизированный мониторинг(при наличии дистанционного контроля). При возникновении повышенного биения вала частоту контроля по решению технического руководителя ГЭС увеличивают. Техническое обследование (виброиспытания — до и после ремонта, и в межремонтный период) |
ГОСТ Р 55260.3.2—2023
Продолжение таблицы 6.15
Группа параметров функционального узла1) | Параметр функционального узла1) | Допустимые значения параметра, установленное НТД значение Н | Методика определения фактического значения параметра Ф функционального узла | Способ регистрации результатов контроля | Форма контроля | |
наименование | размерность | |||||
Выработка облицовки3) вала | мм | В соответствии с конструкторской документацией и данными завода-изготовителя | Визуальный осмотр. Измерительный контроль в соответствии с В.1, В.2.1 | Акт осмотра. Формуляр замеров. Заключение ВИК | Периодический (инструментальный) контроль (в периоды ремонтов при разборке подшипника) | |
Состояние подшипника | Вибрация корпуса подшипника | мкм | Параметры не должны превышать значений, установленных заводской документацией, ГОСТ Р 70810 и требованиями К.5 | В соответствии с рекомендациями К.5 и ГОСТ Р 70810 | Отчет о проведении испытаний. Запись в журнал дефектов, информация для ремонтного и оперативного персонала | Постоянный контроль (по штатным системам — при обходах оборудования 1—2 раза в смену). Автоматизированный мониторинг(при наличии дистанционного контроля). При возникновении повышенного биения вала частоту контроля по решению технического руководителя ГЭС увеличивают. Техническое обследование (виброиспытания — до и после ремонта, и в межремонтный период) |
Тенденция изменения вибрации корпуса подшипника по сравнению с исходным значением Фо в сопоставимых условиях (в соответствии с применяемой НТД) | мкм | Расчетом на базе результатов виброконтроля | Запись в журнал осмотра, информация для ремонтного и оперативного персонала | Автоматизированный мониторинг(при наличии дистанционного контроля). Периодический (инструментальный) контроль. Техническое обследование |
ГОСТ Р 55260.3.2—2023
g Окончание таблицы 6.15
Группа параметров функционального узла1) | Параметр функционального узла1) | Допустимые значения параметра, установленное НТД значение Н | Методика определения фактического значения параметра Ф функционального узла | Способ регистрации результатов контроля | Форма контроля | |
наименование | размерность | |||||
Степень износа вкладышей ТП | % | В соответствии с конструкторской документацией и данными завода-изготовителя | Визуальный осмотр. Измерительный контроль в соответствии с В.1, В.2.1 | Акт осмотра. Формуляр замеров. Заключение ВИК | Периодический (инструментальный) контроль (в периоды ремонтов при разборке подшипника) |
ГОСТ Р 55260.3.2—2023
1) В соответствии с [1].
2) Соответствует параметру «Бой вала в зоне подшипника» [1].
3) Соответствует параметру «Выработка рубашки вала» [1].
Таблица 6.16 — Нормы контроля технического состояния вала и подшипника с обрезиненным вкладышем на водяной смазке для определения вида технического состояния по степени работоспособности оборудования
Контролируемые параметры1) | Допустимые значения параметров | Методики определения фактических значений параметров | Способ регистрации результатов контроля | Форма контроля |
Относительное виброперемещение вала у ТП | Относительное виброперемещение вала не должно превышать значений, установленных заводской документацией, ГОСТ Р 70810 и требованиями К.5 | Индикатор, при наличии — штатные датчики биения вала | Запись в суточной ведомости. Запись в журнале дефектов. Акт осмотра | Постоянный контроль (по штатным системам — при обходах оборудования 1—2 раза в смену). Автоматизированный мониторинг (при наличии дистанционного контроля). При возникновении повышенного биения вала частоту контроля по решению технического руководителя ГЭС увеличивают. Техническое обследование (виброиспытания — до и после ремонта, и в межремонтный период) |
Тенденция изменения амплитуды относительной вибрации вала в зоне подшипника | При выявлении устойчивой тенденции к увеличению амплитуды относительного виброперемещения вала в зоне подшипника при работе ГА на номинальных нагрузках и напорах, провести дополнительные обследования с целью выявления причины нарастания вибрации | Расчетом на базе результатов виброконтроля | Запись в журнал осмотра, информация для ремонтного и оперативного персонала | Автоматизированный мониторинг (при наличии дистанционного контроля). Периодический (инструментальный) контроль. Техническое обследование |
Продолжение таблицы 6.16
Контролируемые параметры1) | Допустимые значения параметров | Методики определения фактических значений параметров | Способ регистрации результатов контроля | Форма контроля |
Уплотнение вала (в зависимости от конструкции): - состояние уплотняющего элемента (воротника, плоской кольцевой манжеты, сальниковой набивки и др.); - состояние вала в зоне контакта с уплотнением по размерам выработки и состоянию поверхности; - состояние торцевого уплотнения (однорядного или двухрядного) по степени и равномерности износа в зоне контакта и по состоянию уплотняющих элементов; - при наличии принудительной подачи воды к уплотнению оценивают состояние системы подвода (засорение, повреждения коррозией, зарастание дрейсеной, износ арматуры и др.) | В соответствии с конструкторской документацией и данными завода-изготовителя | Визуальный осмотр | Запись в журнал осмотра | Периодический (инструментальный) контроль. Техническое обследование |
Давление воды в подводящем трубопроводе | Соответствие давления требованиям завода-изготовителя | Штатные средства контроля (электро-контактный манометр) | Запись в суточной ведомости | Постоянный контроль |
ГОСТ Р 55260.3.2—2023
Ц Продолжение таблицы 6.16
Контролируемые параметры1) | Допустимые значения параметров | Методики определения фактических значений параметров | Способ регистрации результатов контроля | Форма контроля |
Расход воды на смазку и охлаждение подшипника | Соответствие расхода воды требованиям завода-изготовителя. Необходимо отмечать увеличение расхода воды на смазку и охлаждение подшипника при обходах | Штатные средства контроля, например, дифманометр или иные средства контроля (см. Ж.5.4). Визуально — указатель наличия струи | Запись в журнале дефектов. Акт осмотра | Постоянный контроль |
Состояние крепления корпуса подшипника | Крепление корпуса подшипника не должно быть ослаблено и вызывать его податливость | Визуальный осмотр | Запись в журнале дефектов. Акт осмотра | Периодический (инструментальный) контроль (на работающем оборудовании). Техническое обследование |
Неравномерность зазора между расточкой верхнего фланца крышки ванны подшипника и валом | До 0,75 мм включительно | ИК (в кольцевом подшипнике — в четырех направлениях, в сегментном подшипнике — по каждому сегменту) | Формуляр замеров | Периодический (инструментальный) контроль. Техническое обследование |
Отклонение зазора между вкладышем подшипника и валом | До 20 % включительно | |||
Вертикальный зазор в уплотнении торцового (лепесткового) типа | Устанавливается с учетом изменения высотного положения вала ГА при нагрузке | ИК | Формуляр замеров | Периодический (инструментальный) контроль. Техническое обследование |
Наличие трещин на сухарях, по сварным швам, на корпусе | Трещины не допускаются | Визуальный осмотр, ВИК на остановленном ГА ПВК или ТВК или МПД по результатам ВИК. В соответствии с В.2 | Акт осмотра. Заключения и протоколы неразрушающего контроля ВИК. Формуляр повреждений. Фотографии | Периодический (инструментальный) контроль. Техническое обследование |
Состояние опорных элементов (болтов, клиньев) | В соответствии с конструкторской документацией и данными завода-изготовителя | Визуальный осмотр, ВИК на остановленном ГА | Акт осмотра. Заключение ВИК. Формуляр повреждений. Фотографии | Периодический (инструментальный) контроль. Техническое обследование |
ГОСТ Р 55260.3.2—2023
Окончание таблицы 6.16
Контролируемые параметры1' | Допустимые значения параметров | Методики определения фактических значений параметров | Способ регистрации результатов контроля | Форма контроля |
Состояние крепежных болтов | Нормы контроля качества в соответствии с требованиями ГОСТ 18442, ГОСТ 22761, ГОСТ Р ИСО 16809, [11] | Визуальный осмотр, ВИК в соответствии с В.2.1 и СТО ГЭС (при наличии) на остановленном ГА | Акт осмотра. Заключение ВИК. Формуляр повреждений. Фотографии | Периодический (инструментальный) контроль. Техническое обследование |
1 > Контролируемые параметры, не вошедшие в таблицу 6.15. |
Таблица 6.17 — Нормы контроля технического состояния вала и подшипника с масляной смазкой для определения вида технического состояния по степени работоспособности оборудования
Контролируемые параметры1) | Допустимые значения параметров | Методики определения фактических значений параметров | Способ регистрации результатов контроля | Форма контроля |
Относительное виброперемещение вала у подшипника, уровень вибрации корпусов маслованн | Относительное виброперемещение вала и уровень вибрации корпусов маслованн не должны превышать значений, установленных заводской документацией, ГОСТ Р 70810 и требованиями К.5 | Индикатор, при наличии штатные датчики биения вала | Запись в суточной ведомости. Запись в журнале дефектов. Акт осмотра | Постоянный контроль (по штатным системам — при обходах оборудования 1—2 раза в смену). Автоматизированный мони-торинг (при наличии дистанционного контроля). При возникновении повышенного биения вала частоту контроля по решению технического руководителя ГЭС увеличивают. Техническое обследование (виброиспытания — до и после ремонта, и в межремонтный период) |
Тенденция изменения амплитуды относительной вибрации вала в зоне подшипника | При выявлении устойчивой тенденции к увеличению амплитуды относительного виброперемещения вала в зоне подшипника при работе ГА на номинальных нагрузках и напорах провести дополнительные обследования с целью выявления причины нарастания вибрации | Расчетом на базе результатов виброконтроля | Запись в журнал осмотра, информация для ремонтного и оперативного персонала |
ГОСТ Р 55260.3.2—2023
g Продолжение таблицы 6.17
Контролируемые параметры1) | Допустимые значения параметров | Методики определения фактических значений параметров | Способ регистрации результатов контроля | Форма контроля |
Температура вкладышей, сегментов, масла (включая изменение температуры в сходных режимах в процессе эксплуатации) | В соответствии с эксплуатационной документацией (температура, установленная местной инструкцией по эксплуатации). Повышение температуры вкладышей (сегментов) подшипника указывает на недостаточный зазор, ухудшение охлаждения либо ухудшение состояния рабочих поверхностей вкладышей (сегментов) подшипника и вала. Постепенное повышение температуры сегментов ТП на 2 °C — 3 °C по сравнению с установившейся величиной, рост температуры масла и сегментов на одинаковую величину; вероятная причина — уменьшение расхода охлаждающей воды в маслоохладителе ТП либо понижение уровня масла в маслованне. Резкое повышение температуры сегментов ТП до температуры 65 °C на сигнал и до 70 °C на отключение агрегата; вероятные причины — подплавление сегментов подшипника вследствие понижения уровня масла; повышение уровня масла и вытеснение его водой из маслоохладителей; неправильно выставленные зазоры по сегментам подшипника (возможно при выходе ГА из ремонта или монтажа); уменьшение или прекращение поступления охлаждающей воды в маслоохладители ТП; заклинивание одного или нескольких сегментов подшипника; попадание твердых частиц между трущимися поверхностями сегментов подшипника и втулкой вала; неисправность датчиков температурного контроля | Штатные средства контроля (термосопротивления, термосигнализатор) | Запись в суточной ведомости | Постоянный контроль. Автоматизированный мониторинг (при наличии дистанционного контроля) |
ГОСТ Р 55260.3.2—2023
Продолжение таблицы 6.17
Контролируемые параметры1) | Допустимые значения параметров | Методики определения фактических значений параметров | Способ регистрации результатов контроля | Форма контроля |
Состояние уплотнений и маслованн подшипника | Протечки масла через выгородки маслованн, фланцевые соединения и уплотнения недопустимы. Уплотнительные элементы (резина, войлок, кожа) не должны иметь задиров, должны обеспечивать плотный контакт с валом. При этом уплотнение должно работать, не вызывая местный перегрев зоны контакта на валу ГА | Визуальный осмотр | Запись в журнале дефектов. Акт осмотра | Периодический (инструментальный) контроль. Техническое обследование |
Уровень масла в маслованне подшипника | Уровень масла не должен выходить за максимальное и минимальное значение, установленное местной инструкцией по эксплуатации. Повышение уровня масла в маслованне подшипника может свидетельствовать о попадании воды из маслоохладителей в маслованну или перелив масла при заливке или доливке в маслованну. Понижение уровня масла в маслованне подшипника может свидетельствовать об утечке масла через неплотно закрытый сливной пробковый кран маслован-ны, через неплотности соединения выгородки и корпуса маслованны | Реле давления, визуально по масломерному стеклу | Запись в журнале дефектов. Акт осмотра | Постоянный контроль |
Состояние крепления корпуса подшипника | Крепление корпуса подшипника не должно быть ослаблено и вызывать его податливость | Визуальный осмотр | Запись в журнале дефектов. Акт осмотра | Периодический (инструментальный) контроль (на работающем оборудовании) |
Неравномерность зазора между расточкой верхнего фланца крышки ванны подшипника и валом | До 0,75 мм включительно | ИК (в кольцевом подшипнике — в четырех направлениях, в сегментном подшипнике — по каждому сегменту) | Формуляр замеров | Периодический (инструментальный) контроль. Техническое обследование |
Отклонение зазора между вкладышем подшипника и валом | До 20 % включительно |
ГОСТ Р 55260.3.2—2023
g Окончание таблицы 6.17
Контролируемые параметры1) | Допустимые значения параметров | Методики определения фактических значений параметров | Способ регистрации результатов контроля | Форма контроля |
Вертикальный зазор в уплотнении торцового типа | Устанавливается с учетом изменения высотного положения вала ГА при нагрузке | ИК | Формуляр замеров | Периодический (инструментальный) контроль. Техническое обследование |
Наличие трещин на сухарях, по сварным швам, на корпусе | Трещины не допускаются | Визуальный осмотр, ВИК на остановленном ГА ПВК или ВТК или МПД по результатам ВИК. В соответствии с В.2 | Акт осмотра. Заключения и протоколы неразрушающего контроля ВИК. Формуляр повреждений. Фотографии | Периодический (инструментальный) контроль. Техническое обследование |
Состояние опорных элементов (болтов, клиньев) | В соответствии с конструкторской документацией и данными завода-изготовителя | Визуальный осмотр, ВИК на остановленном ГА | Акт осмотра. Заключение ВИК. Формуляр повреждений. Фотографии | Периодический (инструментальный) контроль. Техническое обследование |
Состояние крепежных болтов | Нормы контроля качества в соответствии с требованиями ГОСТ 18442, ГОСТ 22761, ГОСТ РИСО 16809, [11] | Визуальный осмотр, ВИК в соответствии с В.2.1 и СТО ГЭС (при наличии) на остановленном ГА | Акт осмотра. Заключение ВИК. Формуляр повреждений. Фотографии | Периодический контроль. Техническое обследование |
Состояние масла | Соответствие масла требованиям технической документации на ГА | По результатам химического анализа проб масла маслованн подшипников. Отбор масла для контроля производится в соответствии с эксплуатационной документацией и указаниями завода — изготовителя оборудования, а также перед выводом ГА в ремонт и в случаях проявления нарушений в работе подшипника | Протокол результатов химического анализа. Формуляр повреждений | Лабораторные исследования |
1) Контролируемые параметры, не вошедшие в таблицу 6.15. |
ГОСТ Р 55260.3.2—2023
ГОСТ Р 55260.3.2—2023
6.8 Система автоматического управления
6.8.1 Техническое состояние САУ оценивают с учетом ее функций по обеспечению автоматической работы ГА во всех эксплуатационных режимах (нахождение в резерве, пуск, XX, работа под нагрузкой, насосный режим (для обратимых гидротурбин), режим СК, останов) и при переходах между режимами с соблюдением требований ГОСТ 5616, гарантий регулирования и установленных заводом — изготовителем гидротурбины ограничений на работу в эонах эксплуатационной характеристики.
6.8.2 Оценку технического состояния САУ необходимо проводить совместно с оценкой технического состояния сервомоторов НА и сервомоторов РК для ПЛ-гидротурбин.
6.8.3 Требования к техническому контролю САУ гидротурбин для определения вида технического состояния по степени работоспособности оборудования в соответствии с классификацией, приведенной в таблице 4.2, и последующего определения ИТС содержатся в таблицах 6.18—6.19.
6.8.4 Гарантии регулирования должны проверяться периодически в соответствии с рекомендациями завода-изготовителя и руководством по эксплуатации гидротурбины.
6.8.5 Рекомендации по испытаниям исполнительных органов системы регулирования гидротурбин представлены в Д.З.
57
g Таблица 6.18 — Нормы контроля технического состояния САУ для последующего определения ИТС
Группа параметров функционального узла1) | Параметр функционального узла1) | Допустимые значения параметра, установленное НТД значение Н | Методика определения фактического значения параметра Ф функционального узла | Способ регистрации результатов контроля | Форма контроля | |
наименование | размерность | |||||
Комбинаторная зависимость (для ПЛ-турбин) | Угол отклонения от оптимального значения, установленного НТД | град | Комбинаторная зависимость должна соответствовать оптимальной. Метки на фланце лопасти, маслоприемнике и регуляторе должны совпадать | В соответствии с рекомендациями Д.3.3 и К.4 | Отчет о проведении испытаний по определению комбинаторной зависимости | Техническое обследование. Допускается (при наличии технической возможности) определение фактической комбинаторной зависимости по данным автоматизированного мониторинга |
Разница в развороте лопастей при одном и том же открытии НА после отработки сигналов на «прибавить» и «убавить» | град | Положение лопастей по углу разворота при заданном открытии НА не должно отличаться от проектного более чем на 0,5 %. Показания величины угла разворота лопастей РК ПЛ-типа по градуировке по шкале маслоприемника должны соответствовать показаниям угла разворота их по градуировке на фланце лопасти. Расхождение в углах установки лопастей, замеренное в соответствии с Б.З, не должно превышать 1,0 % от угла их полного разворота. Допустимые отклонения от среднего фактического значения в пределах РК не должны превышать 20 % от заданного проектного значения,указанного в конструкторской документации с учетом согласованных отклонений. При отсутствии требований к конструкторской документации максимально допустимые отклонения по критерию однородности (отношение измеренного значения к среднему) рекомендуется принимать в соответствии с (см. [10]) | В соответствии с Б.З, включая ЗО-сканирование в КРК | Акты, формуляры и схемы замеров, отчет о проведении измерений | Техническое обследование |
ГОСТ Р 55260.3.2—2023
Окончание таблицы 6.18
Группа параметров функционального узла1) | Параметр функционального узла1) | Допустимые значения параметра, установленное НТД значение Н | Методика определения фактического значения параметра Ф функционального узла | Способ регистрации результатов контроля | Форма контроля | |
наименование | размерность | |||||
Давление в полостях сервомоторов при отсутствии регулирования (для ПЛ-турбин) | Разность давлений в полостях сервомоторов | кгс/см2 | В соответствии с проектно-конструкторской документацией и опытом эксплуатации | В соответствии с Д.3.3 или по данным автоматизированного мониторинга | Отчет о проведении испытаний системы регулирования, определении перестановочных усилий | Техническое обследование (испытания — до и после ремонта). Автоматизированный мониторинг (при наличии дистанционного контроля) |
Состояние регулятора скорости в целом | Отказы регулятора скорости в процессе эксплуатации в межремонтный период | По данным штатных средств контроля. Из анализа эксплуатационной документации | Журнал дефектов. Суточная ведомость | Постоянный контроль | ||
Дефекты в межремонтный период | — | — | ||||
Цикл работы насосов МНУ | Цикл работы (отношение времени работы ко времени останова) насосов МНУ в режиме работы ГА без отработки сигналов регулирования | При нормальном состоянии системы регулирования сервомотора механизма разворота лопастей РК и маслоприемника насос работает в режиме 1:(12...2О). Об ухудшении состояния названных узлов свидетельствует режим работы 1 :(4...6). Для СНА допускаются протечки, величина которых обеспечивает цикл насосов МНУ не хуже 1:10 | По данным штатных средств контроля. Из анализа эксплуатационной документации | Журнал дефектов. Суточная ведомость | Постоянный контроль | |
1) В соответствии с [1]. |
ГОСТ Р 55260.3.2—2023
g Таблица 6.19 — Нормы контроля технического состояния САУ для определения вида технического состояния по степени работоспособности оборудования
Контролируемые параметры1) | Допустимые значения параметров | Методики определения фактических значений параметров | Способ регистрации результатов контроля | Форма контроля |
Перетоки масла в сервоприводе разворота лопастей | В соответствии с проектноконструкторской документацией. Предельное значение перетоков соответствует переливу масла через гребенку лабиринтного уплотнения маслоприемника | Увеличение перетоков масла в сервоприводе разворота лопастей определяют по повышенному уровню масла в ванне маслоприемника при работе ГА под нагрузкой. Объем перетоков оценивают по результатам испытаний системы регулирования (см. приложение Д) | Отчет о проведении испытаний системы регулирования | Постоянный контроль. Периодический осмотр |
Потери масла из системы регулирования | Предельное снижение уровня контролируется уставкой датчика уровня | Определяют по снижению уровня масла в баке МНУ | Постоянный контроль. Периодический осмотр | |
Обводнение масла в системе регулирования | В соответствии с технической документацией на ГА | Визуально по появлению масла на поверхности воды в нижнем бьефе ГЭС вследствие ухудшения работы уплотняющих конструкций втулки РК | Постоянный контроль. Периодический осмотр | |
Величина люфтов механизма обратной связи | Не более 0,5 % от полного хода сервомотора | ИК | Акт осмотра. Формуляр замеров | Техническое обследование |
Суммарные люфты и мертвый ход в обратной связи (в жестких обратных связях в случае необходимости люфты должны определяться поэлементно для выявления изношенных шарниров) | В соответствии с конструкторской документацией |
ГОСТ Р 55260.3.2—2023
1) Контролируемые параметры, не вошедшие в таблицу 6.18.
ГОСТ Р 55260.3.2—2023
6.9 Вал (валопровод)
6.9.1 В общем случае валопровод может состоять из вала турбины, вала генератора, промежуточного вала, вала-надставки, остова ротора генератора, сопряженных с помощью фланцевых соединений.
6.9.2 Техническое состояние валопровода, включая шейки валов в зоне установки подшипников, следует оценивать совместно с направляющими подшипниками (турбинный, генераторные) и опорным подшипником гидрогенератора (подпятником).
6.9.3 Контроль технического состояния валопровода осуществляют на работающем и остановленном ГА. Методика контроля линии вала агрегата и нормы оценки представлены в приложении Е.
6.9.4 Требования к оценке технического состояния вала с направляющими подшипниками с водяной и масляной смазкой для определения вида технического состояния по степени работоспособности оборудования в соответствии с классификацией, приведенной в таблице 4.2, и последующего определения ИТС содержатся в таблицах 6.15—6.17.
6.9.5 Дополнительно, на остановленном ГА при проведении осмотра проверяют плотность фланцевых соединений по внешним признакам (наличие течи масла через фланцевое соединение для агрегатов с ПЛ турбинами, раскрытие фланцевого соединения визуально) и состояние облицовки вала в соответствии с требованиями таблицы 6.20.
61
g Таблица 6.20 — Нормы контроля технического состояния валопровода для определения вида технического состояния по степени работоспособности оборудования
Контролируемые параметры1) | Допустимые значения параметров | Методики определения фактических значений параметров | Способ регистрации результатов контроля | Форма контроля |
Состояние металла вала (наличие трещин в зоне фланцев, галтельных переходов, отверстий под болты) | Трещины не допускаются | ВИК, ПВК, МПД, ВТК, УЗК на остановленном ГА при осушенном проточном тракте в соответствии с В.2 | Заключения и протоколы по неразрушающему контролю. Журнал дефектов. Формуляр повреждений. Фотографии | Периодический (инструментальный) контроль (на остановленном оборудовании при разборке подшипника). Техническое обследование |
Плотность фланцевых соединений | Односторонний зазор до 0,03 мм на длине не более 200 мм | Визуальный осмотр, ВИК в соответствии с В.2.1 и СТО ГЭС (при наличии) на оста-новленном ГА | Акт осмотра. Заключение ВИК. Формуляр повреждений | |
Износ шейки, наличие трещин, отставания облицовки, вырывов | Износ шейки — в соответствии с допусками в конструкторской документации. Трещины и вырывы не допускаются | |||
Посадка и плотность соединения по стыкам в сборном остове (звезде) ротора | В соответствии с заводской документацией. Плотным считается соединение, в которое щуп 0,1 мм не проходит. Допускаются местные неплотности, в которые может проходить щуп 0,1 мм, не более 10 % ширины сопрягаемого стыка, а длина отдельного неплотного участка допускается не более 100 мм. Общая длина всех неуплотненных местных участков не должна превышать в сумме 15 % длины соединяемого стыка | Визуальный осмотр. Измерительный контроль (на плотность). По косвенным признакам (нестабильность вибрационного состояния) | Акт осмотра. Формуляр повреждений | Периодический (инструментальный) контроль. Техническое обследование |
Затяг и состояние крепежа | Нормы контроля качества в соответствии с требованиями ГОСТ 18442, ГОСТ 22761, ГОСТР ИСО 16809, [11] | Визуальный осмотр, ВИК в соответствии с В.2.1 и СТО ГЭС (при наличии) на остановленном ГА | Акт осмотра. Заключение ВИК. Формуляр повреждений. Фотографии | Периодический (инструментальный) контроль. Техническое обследование |
1) Контролируемые параметры, не вошедшие в таблицы 6.15—6.17. |
ГОСТ Р 55260.3.2—2023
ГОСТ Р 55260.3.2—2023
6.9.6 На работающем ГА следует обращать внимание на следующие признаки ухудшения состояния линии вала:
- повышенное значение относительного виброперемещения вала ГА у направляющих подшипников и фланцевых соединений валов, что может быть следствием излома во фланцевых соединениях, износа шейки вала в подшипнике;
- повышенная горизонтальная вибрация направляющих подшипников ГА;
- повышенная вертикальная вибрация опоры пяты;
- постепенное повышение относительного виброперемещения вала (увеличение зазоров в направляющих подшипниках) в течение межремонтного периода при одинаковых режимах работы ГА;
- односторонний перегрев сегментов направляющих подшипников из-за расцентровки вала.
6.10 Подшипник опорный генераторный (подпятник)
6.10.1 Техническое состояние ПП следует оценивать совместно с линией вала, ГП, грузонесущей и негрузонесущей крестовинами.
Данный раздел предъявляет требования к техническому состоянию ПП зонтичного и подвесного исполнения с сегментами, облицованными баббитом, и с эластичными металлопластмассовыми сегментами (ЭМП-сегментами).
Данный раздел предъявляет требования к техническому состоянию ПП как механической части ГА. Для оценки технического состояния ПП в полном объеме необходимо учитывать требования к оценке электрической части генератора в соответствии с ГОСТ Р 55260.2.2.
6.10.2 Стыковые и фланцевые соединения масляной ванны и крышки ПП должны быть плотными: протечки масла не допускаются.
6.10.3 Требования к оценке технического состояния ПП для определения вида технического состояния по степени работоспособности оборудования в соответствии с классификацией, приведенной в таблице 4.2, и последующего определения ИТС содержатся в таблицах 6.21—6.22.
6.10.4 При контроле технического состояния особое внимание должно быть обращено на состояние деталей ПП, поломки которых имели место в период эксплуатации. При этом объем и методы контроля определяются исходя из необходимости и получения полной информации о причинах имевшихся нарушений.
6.10.5 Для каждого гидрогенератора на основании регулярных наблюдений при гарантированно нормальной работе ПП должны быть установлены и указаны максимально допустимые установившиеся значения температуры сегментов и масла в маслованне для наибольших температур наружного воздуха (для данного времени года).
6.10.6 Методики проведения испытаний для определения в целях получения характеристик подпятников и углубленной оценки их технического состояния с выяснением причин ненадежной работы подпятников приведены в приложении Ж.
63
g Таблица 6.21 — Нормы контроля технического состояния ПП для последующего определения ИТС
Группа параметров функционального узла1) | Параметр функционального узла1) | Допустимые значения параметра, установленное НТД значение Н | Методика определения фактического значения параметра Ф функционального узла | Способ регистрации результатов контроля | Форма контроля | |
наименование | размерность | |||||
Состояние зеркального диска | Макронеровность в радиальном направлении | мм | Для дисков диаметром менее 2 м — не более 0,03 мм. Для дисков диаметром более 2 м — не более 0,04 мм | С помощью часовых индикаторов или датчиков, перемещаемых в радиальном направлении, и лекальной линейки. Измерения проводятся на двенадцати радиусах | Акт осмотра. Формуляр замеров | Техническое обследование (при вскрытой маслованне при каждом капитальном и аварийном ремонте) |
Тенденция изменения макронеровности в радиальном направлении по сравнению с предыдущим замером Фпред | мм | Расчетом на базе результатов измерений | Запись в журнал осмотра, информация для ремонтного и оперативного персонала | Периодический (инструментальный) контроль. Техническое обследование | ||
Макронеровность в направлении вращения | мм | 0,08 мм — для однорядных, 0,12 мм — для двухрядных и ПП на гидравлической опоре | Часовые индикаторы или датчики с автоматической регистрацией. Измерения производятся при прокрутке ротора | Акт осмотра. Формуляр замеров | Техническое обследование (при вскрытой маслованне при каждом капитальном и аварийном ремонте) | |
Тенденция изменения макронеровности в направлении вращения по сравнению с предыдущим замером Ф пред | мм | Расчетом на базе результатов измерений | Запись в журнал осмотра, информация для ремонтного и оперативного персонала | Периодический (инструментальный) контроль. Техническое обследование | ||
Тенденция изменения макронеровности в направлении вращения по сравнению с предыдущим замером Ф пред | мкм | Расчетом на базе результатов измерений | Запись в журнал осмотра, информация для ремонтного и оперативного персонала | Периодический (инструментальный) контроль. Техническое обследование |
ГОСТ Р 55260.3.2—2023
Продолжение таблицы 6.21
Группа параметров функционального узла1) | Параметр функционального узла1) | Допустимые значения параметра, установленное НТД значение Н | Методика определения фактического значения параметра Ф функционального узла | Способ регистрации результатов контроля | Форма контроля | |
наименование | размерность | |||||
Состояние зеркального диска | Вертикальная вибрация грузонесу-щей крестовины | мкм | Параметры не должны превышать значений, установленных заводской документацией, ГОСТ Р 70810 и требованиями К.5 | Переносная виброизме-рительная аппаратура, при наличии, штатные датчики. В соответствии с К.5 и ГОСТ Р 70810 | Отчет о проведении испытаний. Запись в журнал дефектов, информация для ремонтного и оперативного персонала | Постоянный контроль (по штатным системам — при обходах оборудования 1 раз в смену). Автоматизированный мониторинг(при наличии дистанционного контроля). Техническое обследование (испытания — до и после ремонта, и в межремонтный период) |
Радиальная вибрация опоры ПП (при негрузонесу-щей крестовине) | мкм | Параметры не должны превышать значений, установленных заводской документацией, ГОСТ Р 70810 и требованиями К.5 | Переносная виброизме-рительная аппаратура, при наличии штатные датчики. В соответствии с К.5 и ГОСТ Р 70810 | Отчет о проведении испытаний. Запись в журнал дефектов, информация для ремонтного и оперативного персонала | Постоянный контроль (по штатным системам — при обходах оборудования 1 раз в смену). Автоматизированный мониторинг(при наличии дистанционного контроля). Техническое обследование (испытания — до и после ремонта, и в межремонтный период) |
ГОСТ Р 55260.3.2—2023
g Продолжение таблицы 6.21
Группа параметров функционального узла1) | Параметр функционального узла1) | Допустимые значения параметра, установленное НТД значение Н | Методика определения фактического значения параметра Ф функционального узла | Способ регистрации результатов контроля | Форма контроля | |
наименование | размерность | |||||
Состояние зеркального диска | Тенденция от клонения вертикальной вибрации грузонесущей крестовины по сравнению с предыдущим замером Ф пред | Расчетом на базе результатов виброконтроля | Запись в журнал осмотра, информация для ремонтного и оперативного персонала | Периодический (измерительный) контроль. Техническое обследование | ||
Тенденция отклонения радиальной вибрации опоры ПП по сравнению с предыдущим замером Фпред (ПРИ негрузонесущей крестовине) | мкм | Расчетом на базе результатов виброконтроля | Запись в журнал осмотра, информация для ремонтного и оперативного персонала | Периодический (измерительный) контроль. Техническое обследование | ||
Шероховатость зеркала | мкм | Ra < 0,32 мкм | Визуальный осмотр. Измерения с помощью профилометра | Акт осмотра. Формуляр замеров | Техническое обследование (при вскрытой маслованне при каждом капитальном и аварийном ремонте) | |
Тенденция отклонения шероховатости зеркала по сравнению с предыдущим замером Ф пред | мкм | Расчетом на базе результатов измерений | Запись в журнал осмотра, информация для ремонтного и оперативного персонала | Периодический (измерительный) контроль. Техническое обследование |
ГОСТ Р 55260.3.2—2023
Продолжение таблицы 6.21
Группа параметров функционального узла1) | Параметр функционального узла1) | Допустимые значения параметра, установленное НТД значение Н | Методика определения фактического значения параметра Ф функционального узла | Способ регистрации результатов контроля | Форма контроля | |
наименование | размерность | |||||
Состояние сегментов | Температурный режим | °C | Устанавливается документацией ГЭС в соответствии с 6.10.5. Значения предупредительных и аварийных уставок автоматической системы контроля определяются опытным путем. Повышение температуры одного или нескольких сегментов ПП на 3 °C — 4 °C выше обычных установившихся значений для данного времени года при сохранении температуры масла на прежнем уровне, является признаком ухудшения состояния поверхностей трения этих сегментов и требует усиления контроля за ними. Понижение температуры одного или нескольких сегментов однорядного ПП на жесткой винтовой опоре до значений, близких к температуре масла в маслованне (при исправном термоконтроле), свидетельствует о выходе этих сегментов из работы, что может произойти в результате разрушения тарельчатых опор, и требует осмотра этих сегментов и замены опор | Визуально по стандартным термодатчикам (см. Ж.5.3) | Запись в суточной ведомости | Непрерывный контроль (по штатным системам не реже 1 раза в смену, при отсутствии автоматизированного мониторинга). Автоматизированный мониторинг (при наличии дистанционного контроля). При повышении температуры одного или нескольких сегментов сверх наибольшего установившегося в процессе эксплуатации значения (в самое жаркое время года): - при автоматической системе контроля при превышении температуры на 5 °C должен подаваться предупредительный сигнал, а при превышении на 10 °C — аварийный сигнал (импульс на останов ГА); - при отсутствии автоматической системы контроля при превышении температуры на 5 °C увеличить частоту контроля до 1 раза в час, а при превышении на 10 °C — остановить ГА |
ГОСТ Р 55260.3.2—2023
g Продолжение таблицы 6.21
Группа параметров функционального узла1) | Параметр функционального узла1) | Допустимые значения параметра, установленное НТД значение Н | Методика определения фактического значения параметра Ф функционального узла | Способ регистрации результатов контроля | Форма контроля | |
наименование | размерность | |||||
Состояние сегментов | Распределение нагрузки между сегментами | кг | Общая нагрузка на подпятник должна быть распределена между сегментами равномерно. Отклонение нагрузки, приходящейся на каждый сегмент, не должно превышать: 10 % разброса нагрузки для подпятников на жесткой опоре; 0,2 мм разницы проседания — для гидравлических подпятников | Рычажно-индикаторный способ для ПП на жесткой опоре. Индикаторный способ для ПП на гидравлической опоре | Акт осмотра. Формуляр замеров | Техническое обследование (при вскрытой маслованне при каждом капитальном и аварийном ремонте) |
ГОСТ Р 55260.3.2—2023
Продолжение таблицы 6.21
Группа параметров функционального узла1) | Параметр функционального узла1) | Допустимые значения параметра, установленное НТД значение Н | Методика определения фактического значения параметра Ф функционального узла | Способ регистрации результатов контроля | Форма контроля | |
наименование | размерность | |||||
Состояние сегментов | Различие значений параметров регулировки эксцентриситетов | % | Тангенциальный эксцентриситет сегментов с баббитовым покрытием должен устанавливаться в диапазоне 6 % — 10 %, а ЭМП сегментов в диапазоне 4 % — 6 %. В ПП обратимых ГА тангенциальный эксцентриситет сегментов должен устанавливаться равным нулю. Радиальный эксцентриситет сегментов должен устанавливаться в диапазоне ±1,5 %. Для каждого ПП в зависимости от его параметров (окружная скорость, конфигурация сегментов и др.) точное значение оптимальной величины радиального эксцентриситета должно быть определено специальными испытаниями. Разброс эксцентриситетов (тангенциального и радиального) отдельных сегментов ПП не должен превышать 1,5 % | Измерения с помощью контрольных линеек и приспособлений и вычисление по формулам | Акт осмотра. Формуляр замеров | Техническое обследование (при вскрытой маслованне при каждом капитальном и аварийном ремонте) |
ГОСТ Р 55260.3.2—2023
^ Продолжение таблицы 6.21
Группа параметров функционального узла1) | Параметр функционального узла1) | Допустимые значения параметра, установленное НТД значение Н | Методика определения фактического значения параметра Ф функционального узла | Способ регистрации результатов контроля | Форма контроля | |
наименование | размерность | |||||
Опорные болты, тарельчатые опоры. Упругие камеры (гофры) ПП на гидравлической опоре | Дефекты опорных деталей | Вмятины в местах контакта с опорными болтами не должны превышать 0,25 мм. Разрушение (наличие трещин) тарельчатых опор не допускается | Визуальный осмотр. Измерительный контроль с помощью индикатора: величина смятия опорных вкладышей, величина вмятин на тарельчатых опорах в местах контакта с опорными болтами, наличие трещин на верхней стороне тарельчатых опор | Акт осмотра. Формуляр замеров | Периодический (измерительный) контроль. Техническое обследование | |
Дефекты сферических головок болтов | — | Величина смятия сферических головок опорных болтов или опорных вкладышей не должна превышать 0,05 мм | Специальный шаблон и Щуп | Акт осмотра. Формуляр замеров | Периодический(измерительный) контроль. Техническое обследование |
ГОСТ Р 55260.3.2—2023
Окончание таблицы 6.21
Группа параметров функционального узла1) | Параметр функционального узла1) | Допустимые значения параметра, установленное НТД значение Н | Методика определения фактического значения параметра Ф функционального узла | Способ регистрации результатов контроля | Форма контроля | |
наименование | размерность | |||||
Опорные болты, тарельчатые опоры. Упругие камеры (гофры) ПП на гидравлической опоре | Дефекты упругих камер (гофр) ПП на гидравлической опоре | Проседание упругих камер ниже нормального уровня (при работе агрегата под нагрузкой): на 1 мм — (формирование предупредительного сигнала), на 2 мм — импульс на останов. Наличие трещин не допускается. При обнаружении трещины на упругой камере ПП на гидравлической опоре следует перевести подпятник в нежесткое опирание. При отклонении измеряемых значений при контроле герметичности упругих камер от первоначальных более чем на 0,5 мм должны быть приняты меры по восстановлению первоначального состояния | Специальные датчики или контакты, проверка по «маякам». Способы контроля за герметичностью упругих ПП на гидравлической опоре: - измерение расстояния от корпуса ПП до зеркальной поверхности диска в четырех местах (через 90° по окружности диска); - определение среднего значения проседания всех упругих камер. Измерения должны производиться при одной и той же температуре ПП | Постоянный контроль (по штатным системам). Автоматизированный мониторинг (при наличии дистанционного контроля) | ||
1) В соответствии с [1]. |
ГОСТ Р 55260.3.2—2023
^ Таблица 6.22 — Нормы контроля технического состояния ПП для определения вида технического состояния по степени работоспособности оборудования
Контролируемые параметры1) | Допустимые значения параметров | Методики определения фактических значений параметров | Способ регистрации результатов контроля | Форма контроля |
Концентричность образующей окружности сегментов относительно диска пяты | Допустимая неконцентрич-ность в пределах, указанных в таблице 6.23 значений | Расчетом на базе результатов измерений | Акт осмотра. Формуляр измерений | Периодический (измерительный) контроль. Техническое обследование |
Неперпендикулярность плоскости пяты к оси вала ГА | Полное торцевое биение зеркального диска не должно превышать 0,08 мм для однорядных подпятников и 0,12 мм для двухрядных | По результатам проверки общей линии валов методом поворота ротора агрегата на 360° в соответствии с приложениями Е, Ж | Формуляры измерений | Периодический (измерительный) контроль. Техническое обследование |
Износ рабочей поверхности ЭМП-сегментов | При износе фторопласта до выхода на поверхность бронзовой основы ЭМП-сегменты должны быть заменены. Допускается временная работа при незначительных местных выходах бронзовой проволоки на рабочую поверхность | Контроль износа (см. Ж.2.5) фторопластовой поверхности по истиранию контрольных кольцевых рисок. При полном износе контрольных кольцевых рисок — путем измерения толщины ЭМП-сегментов | Акт осмотра. Формуляр измерений (толщины сегментов) | Периодический (измерительный) контроль. Техническое обследование |
Величины зазоров между сегментами и ограничивающими упорами в тангенциальном и радиальном направлениях. В двухрядных ПП дополнительно: - зазоры между балансирами и стенками балансирных коробок; - длины плеч балансиров | В соответствии с конструкторской документацией | Визуальный осмотр. Измерительный контроль | Акт осмотра. Формуляры измерений | Периодический (измерительный) контроль. Техническое обследование |
ГОСТ Р 55260.3.2—2023
Продолжение таблицы 6.22
Контролируемые параметры1) | Допустимые значения параметров | Методики определения фактических значений параметров | Способ регистрации результатов контроля | Форма контроля |
Температура масла в ванне ПП | Устанавливается документацией ГЭС в соответствии с 6.10.5. Повышение температуры масла в маслованне ПП сверх установившегося значения для данного времени года с последующим повышением температуры сегментов является признаком ухудшения работы системы охлаждения и требует проверки системы охлаждения и при необходимости проведения чистки фильтров, трубок маслоохладителей | Стандартный термодатчик | Запись в суточной ведомости | Непрерывный контроль (по штатным системам не реже 1 раза в смену, при отсутствии автоматизированного мониторинга). Автоматизированный мониторинг (при наличии дистанционного контроля) |
Уровень масла в ванне ПП | В соответствии с конструкторской документацией и инструкцией по эксплуатации. При повышении уровня масла сверх допустимого значения требуются срочный анализ наличия воды в маслованне и проверка отсутствия повреждения трубок маслоохладителей. При понижении уровня масла ниже допустимого значения необходимо проверить плотность конструкций и арматуры маслованны в целях предупреждения утечки масла и обеспечить долив масла до нормального уровня | Стандартный датчик уровня | Запись в журнале при выходе за нормативные значения | Автоматизированный мониторинг (при наличии дистанционного контроля, постоянно с автоматической выдачей сигнала при выходе за установленные пределы. Периодический (измерительный) контроль (по масломерному стеклу по утвержденному на ГЭС графику) |
ГОСТ Р 55260.3.2—2023
Окончание таблицы 6.22
Контролируемые параметры1) | Допустимые значения параметров | Методики определения фактических значений параметров | Способ регистрации результатов контроля | Форма контроля |
Состояние системы охлаждения масла | В соответствии с технической документацией на ГА | Наличие потока охлаждающей воды через маслоохладители, контроль отсутствия повреждения трубок маслоохладителей (см. Ж.2.2) | Запись в журнале дефектов (при наличии отклонений от нормальной работы) | Постоянный контроль (по штатным системам не реже 1 раза в смену) |
Выход масла или масляных паров из маслованны | В соответствии с технической документацией на ГА | Контроль отсутствия повышенного выхода масла или масляных паров из маслованны | Запись в журнале дефектов (при наличии отклонений от нормальной работы) | Постоянный контроль (по штатным системам не реже 1 раза в смену) |
Состояние крепежных элементов | Нормы контроля качества в соответствии с требованиями ГОСТ 18442, ГОСТ 22761, ГОСТ Р ИСО 16809, [11] | Визуальный осмотр, ВИК в соответствии с В.2.1 и СТО ГЭС (при наличии) на остановленном ГА | Акт осмотра. Заключение ВИК. Формуляр повреждений. Фотографии | Периодический (измерительный) контроль. Техническое обследование |
1) Контролируемые параметры, не вошедшие в таблицу 6.1. |
ГОСТ Р 55260.3.2—2023
Таблица 6.23 — Допуск неконцентричности ПП относительно диска пяты
Диаметр диска пяты, м | Допустимая неконцентричность, мм |
< 1 | 1,0 |
>1 и <2 | 1,5 |
>2 и < 3 | 2,0 |
>3 и < 4 | 2,5 |
ГОСТ Р 55260.3.2—2023
6.11 Подшипник направляющий генераторный (верхний/нижний)
6.11.1 Техническое состояние ГП следует оценивать совместно с подпятником, крестовинами и валом ГА.
6.11.2 К стыковым соединениям корпуса, вкладыша и ванн ГП предъявляются требования, относящиеся к плотным соединениям деталей гидротурбин: смонтированные конструкции должны быть тщательно уплотнены в местах соединения отдельных элементов и не допускать протечек.
6.11.3 Требования к оценке технического состояния ГП с масляной смазкой для последующего определения ИТС содержатся в таблице 6.24.
Требования к оценке технического состояния ГП с масляной смазкой для определения вида технического состояния аналогичны требованиям к оценке технического состояния ТП с масляной смазкой и содержатся в таблице 6.17.
6.11.4 При контроле технического состояния особое внимание должно быть обращено на состояние деталей ГП, поломки которых имели место в период эксплуатации. При этом объем и методы контроля определяются исходя из необходимости и получения полной информации о причинах имевшихся нарушений.
75
^ Таблица 6.24 — Нормы контроля технического состояния ГП и вала для последующего определения ИТС
Группа параметров функционального узла1) | Параметр функционального узла1) | Допустимые значения параметра, установленное НТД значение Н | Методика определения фактического значения параметра Ф функционального узла | Способ регистрации результатов контроля | Форма контроля | |
наименование | размерность | |||||
Состояние ГП | Температура сегментов | °C | В соответствии с эксплуатационной документацией (температура, установленная местной инструкцией по эксплуатации) | Штатные средства контроля (термосопротивления, термосигнализатор) | Запись в суточной ведомости | Постоянный контроль. Автоматизированный мониторинг (при наличии дистанционного контроля) |
Тенденция изменения значений температуры сегментов по сравнению с исходным значением Фо (в соответствии с применяемой НТД) | °C | Расчетом на базе результатов термоконтроля | Запись в журнал осмотра, информация для ремонтного и оперативного персонала | Автоматизированный мониторинг (при наличии дистанционного контроля). Периодический (измерительный) контроль. Техническое обследование | ||
Тенденция изменения температуры сегментов по сравнению с предыдущим замером Фпред | °C | Расчетом на базе результатов термоконтроля | Запись в журнал осмотра, информация для ремонтного и оперативного персонала | Автоматизированный мониторинг (при наличии дистанционного контроля). Периодический (измерительный) контроль. Техническое обследование | ||
Температура масла | °C | В соответствии с эксплуатационной документацией (температура, установленная местной инструкцией по эксплуатации) | Штатные средства контроля (термосопротивления, термосигнализатор) | Запись в суточной ведомости | Постоянный контроль. Автоматизированный мониторинг (при наличии дистанционного контроля) |
ГОСТ Р 55260.3.2—2023
Продолжение таблицы 6.24
Группа параметров функционального узла1) | Параметр функционального узла1) | Допустимые значения параметра, установленное НТД значение Н | Методика определения фактического значения параметра Ф функционального узла | Способ регистрации результатов контроля | Форма контроля | |
наименование | размерность | |||||
Состояние ГП | Тенденция отклонения значений температуры масла по сравнению с исходным значением Фо (в соответствии с применяемой НТД) | °C | Расчетом на базе результатов термоконтроля | Запись в журнал осмотра, информация для ремонтного и оперативного персонала | Автоматизированный мониторинг (при наличии дистанционного контроля). Периодический (измерительный) контроль. Техническое обследование | |
Вибрация корпуса подшипника | мкм | Параметры не должны превышать значений, установленных заводской документацией, ГОСТ Р 70810 и требованиями К.5 | В соответствии с К.5 и ГОСТ Р 70810 | Отчет о проведении испытаний. Запись в журнал дефектов, информация для ремонтного и оперативного персонала | Постоянный контроль (по штатным системам — при обходах оборудования 1 раз в смену). Автоматизированный мониоринг (при наличии дистанционного контроля). Техническое обследование (испытания — до и после ремонта, и в межремонтный период) | |
Тенденция изменения вибрации корпуса подшипника по сравнению с исходным значением Фо в сопоставимых условиях (в соответствии с применяемой НТД) | мкм | Расчетом на базе результатов виброконтроля | Запись в журнал осмотра, информация для ремонтного и оперативного персонала | Автоматизированный мониторинг (при наличии дистанционного контроля). Периодический (измерительный) контроль. Техническое обследование |
ГОСТ Р 55260.3.2—2023
^ Продолжение таблицы 6.24
Группа параметров функционального узла1) | Параметр функционального узла1) | Допустимые значения параметра, установленное НТД значение Н | Методика определения фактического значения параметра Ф функционального узла | Способ регистрации результатов контроля | Форма контроля | |
наименование | размерность | |||||
Состояние ГП | Относительное виброперемещение2) вала в зоне подшипника | мм | Параметры не должны превышать значений, установленных заводской документацией, ГОСТ Р 70810 и требованиями К.5 | В соответствии с К.5 и ГОСТ Р 70810 | Отчет о проведении испытаний. Запись в суточную ведомость, журнал дефектов, информация для ремонтного и оперативного персонала | Постоянный контроль (по штатным системам — при обходах оборудования 1—2 раза в смену). Автоматизированный мониторинг (при наличии дистанционного контроля). При возникновении повышенного биения вала частоту контроля по решению технического руководителя ГЭС увеличивают. Техническое обследование (виброиспытания — до и после ремонта, и в межремонтный период) |
Тенденция увеличения боя вала по сравнению с предыдущим замером Ф пред | мм | При выявлении устойчивой тенденции к увеличению амплитуды относительного виброперемещения вала в зоне подшипника при работе ГА на номинальных нагрузках и напорах провести дополнительные обследования с целью выявления причины нарастания вибрации | Расчетом на базе результатов виброконтроля | Запись в журнал осмотра, информация для ремонтного и оперативного персонала | Автоматизированный мониторинг (при наличии дистанционного контроля). Периодический (измерительный) контроль. Техническое обследование | |
Выработка облицовки3) вала | мм | В соответствии с конструкторской документацией и данными завода-изготовителя | Визуальный осмотр. Измерительный контроль в соответствии с В.1, В.2.1 | Акт осмотра. Формуляр замеров. Заключение ВИК | Периодический (измерительный) контроль (в периоды ремонтов при разборке подшипника) |
ГОСТ Р 55260.3.2—2023
Окончание таблицы 6.24
Группа параметров функционального узла1) | Параметр функционального узла1) | Допустимые значения параметра, установленное НТД значение Н | Методика определения фактического значения параметра Ф функционального узла | Способ регистрации результатов контроля | Форма контроля | |
наименование | размерность | |||||
Состояние ГП | Дефекты уплотнения вала (протечки масла через выгородки маслованн, фланцевые соединения и уплотнения) | В соответствии с конструкторской документацией и данными завода-изготовителя | Визуальный осмотр | Запись в журнал осмотра | Периодический (измерительный) контроль. Техническое обследование |
1> В соответствии с [1].
2) Соответствует параметру «бой вала в зоне подшипника» [1].
3) Соответствует параметру «Выработка рубашки вала» [1].
ГОСТ Р 55260.3.2—2023
ГОСТ Р 55260.3.2—2023
6.12 Крестовина гидроагрегата грузонесущая/негрузонесущая
6.12.1 Техническое состояние крестовин ГА следует оценивать совместно с направляющими подшипниками, подпятником и маслоприемником РК.
6.12.2 Крестовины генераторов, независимо от их назначения и места установки (на фундаменте, на статоре), должны быть надежно закреплены на своем основании и зафиксированы штифтами либо фиксирующими планками, которые должны быть надежно приварены к основанию, где они установлены. Смонтированная крестовина может иметь отклонения от установочных данных в пределах следующих положений высотной отметки относительно фланца вала гидротурбины:
- опорная (грузонесущая) крестовина ±2,0 мм;
- поддерживающая крестовина ±3,0 мм;
- соосность с валом ГА ±1,5 мм;
- негоризонтальность 0,1 мм на 1 м диаметра установочной плоскости.
6.12.3 Элементы сборных конструкций крестовин в местах их соединений должны быть плотно закреплены. Надлежащее качество креплений в наиболее ответственных соединениях (лапы) обеспечивается предельной расчетной равномерной затяжкой болтов и плотностью стыкуемых плоскостей. Плотным считается соединение, в которое щуп 0,1 мм не проходит. Допускаются местные неплотности, в которые может проходить щуп 0,5 мм на глубину не более 15 % ширины сопрягаемого соединения. Длина отдельного неплотного участка в соединении не должна превышать 200 мм, а суммарная длина всех неплотных участков на одной стороне соединения не должна превышать 20 % ее длины. Достаточная плотность в соединениях элементов крестовины в случае необходимости может быть достигнута применением подогнанных по месту металлических прокладок. При этом штифтовка не должна быть нарушена.
6.12.4 Нагрузка на лапы грузонесущей крестовины должна быть распределена равномерно. Проверка равномерности распределения нагрузки на лапы грузонесущей крестовины осуществляется при выявлении повышенной вибрации крестовины, а также и после каждого снятия крестовины в соответствии с монтажной документацией.
6.12.5 Для прогнозирования технического состояния, определения собственных частот колебаний агрегата в осевом направлении, оценки риска трещинообразования, оценки возможности, целесообразности, сроков и условий продолжения эксплуатации грузонесущей крестовины за пределами назначенного срока службы, в том числе после модернизации и реконструкции гидроагрегата, включающего замену РК, а также в случае замены крепежных элементов грузонесущей крестовины (или крышки турбины при расположении опоры подпятника на ней) проводится определение осевой жесткости грузонесущей крестовины и ГА в целом в соответствии с приложением И.
6.12.6 В гидрогенераторах с электрической изоляцией крестовин величина сопротивления изоляции должна быть не менее 1,0 МОм.
6.12.7 При периодических контролях, техническом обследовании и освидетельствовании крестовин генератора проводится контроль состояния основного металла и сварных швов крестовин с применением неразрушающих методов контроля (ВИК, ПВК или ВТК или МПД, УЗК, ТВ и пр.) в соответствии с В.1, В.2. Объем и методы контроля устанавливаются индивидуальной программой с учетом конструктивных особенностей и ранее выявленных дефектов и повреждений крестовин.
В случае обнаружения дефектов, превышающих нормы оценки качества для данного вида неразрушающего контроля, обоснование возможности и сроков дальнейшей эксплуатации проводится на основании расчетной оценки усталостной прочности и трещиностойкости крестовины, с учетом фактических данных о наработке и механических характеристиках металла, полученных в соответствии с В.З.
6.13 Обобщенный узел
6.13.1 Расчет ИТС ГА по [1] предусматривает оценку ИТС узла, содержащего общие параметры технического состояния, не относящиеся к функциональным узлам (далее — обобщенный узел).
6.13.2 Требования к объемам контроля технического состояния обобщенного узла для последующего определения ИТС представлены в таблице 6.25.
6.13.3 Допустимое значение параметра «срок службы» может быть определено (изменено) на основании комплекса работ по продлению (переназначению) установленного в НТД срока службы с учетом фактических режимов эксплуатации, коэффициента использования ГА, его конструктивных возможностей.
80
Таблица 6.25 — Нормы контроля технического состояния обобщенного узла для последующего определения ИТС
Группа параметров функционального узла1) | Параметр функционального узла1) | Допустимые значения параметра, установленное НТД значение Н | Методика определения фактического значения параметра Ф функционального узла | Способ регистрации результатов контроля | Форма контроля | |
наименование | размерность | |||||
Срок службы | Срок службы | лет | В соответствии с технической документацией на ГА. При отсутствии сведений— в соответствии с ГОСТ 27807: полный срок службы гидротурбин, выпускаемых до 01.01.91, составляет не менее 30 лет, с 01.01.91 — не менее 40 лет | По эксплуатационным данным | Заключение о переназначении (продлении)срока службы или возможности, сроках и условиях дальнейшей эксплуатации. Запись в паспорт гидротурбины | Техническое освидетельствование (с переназначением срока службы) |
Энергетические характеристики | кпд | % | В соответствии с технической документацией на ГА | В соответствии с К.2—К.З | Отчет о проведении испытаний. Запись в паспорт гидротурбины | Техническое обследование, техническое освидетельствование |
Мощность | МВт | В соответствии с технической документацией на ГА | Техническое обследование, техническое освидетельствование | |||
1) В соответствии с [1]. |
ГОСТ Р 55260.3.2—2023
ГОСТ Р 55260.3.2—2023
Приложение А (обязательное)
Методические указания по техническому обследованию узлов гидроагрегатов при их повреждениях
А.1 Общие положения
Анализ аварий и отказов гидросилового оборудования ГЭС показывает, что наиболее повреждаемыми элементами оборудования являются РК гидротурбин, КРК ПЛ-гидротурбин, направляющие подшипники гидротурбин и гидрогенераторов, подпятники гидроагрегатов и маслоприемники ПЛ-гидротурбин. На их долю приходятся порядка 2/3 всех нарушений и практически все аварии. Ниже изложены методические указания по обследованию упомянутых узлов при их повреждениях, а также указан минимальный объем данных по ГА и поврежденному узлу, необходимых для установления причин повреждения.
Основные технические данные по ГЭС, гидротурбинному и гидрогенераторному оборудованию представлены в приложении Г.
А.2 Рабочее колесо и камера рабочего колеса гидротурбины
А.2.1 Общие данные по ГА, рабочему колесу гидротурбины и КРК гидротурбины:
- тип турбины (ПЛ, Пр, Д, РО), тип и исполнение гидрогенератора;
- мощность гидрогенератора, частота вращения, напор ГЭС;
- дата ввода в эксплуатацию ГА;
- сведения о перемаркировке ГА на повышенную мощность, насколько была повышена мощность, дата перемаркировки;
- основные данные РК и КРК:
а) типоразмер турбины;
б) диаметр РК;
в) число лопастей РК;
г) диаметр КРК;
д) толщина стенки КРК;
- выполнение РО РК: литое, сварно-литое, цельное сварно-литое или составное (из половин);
- материал ступицы, обода и лопастей РО РК; наличие защитной облицовки лопастей;
- материал лопастей РК ПЛ- или ПР-типа; наличие защитной облицовки лопастей;
- материал КРК ПЛ- или ПР-гидротурбины: чугунное или стальное литье, стальной прокат и сварка, наличие облицовки из нержавеющей стали и др.;
- повреждения (или нарушения в работе), имевшиеся на данном рабочем колесе и КРК за последние 10 лет, их даты, краткое описание, причины;
- мероприятия, проводившиеся на данном рабочем колесе в процессе эксплуатации в целях повышения его надежности: изменение геометрии лопастей или замена элементов конструкции (подрезка или подварка лопастей, забетонирование отъемного сегмента, замена части лопастей и т. д.), введение дополнительных деталей или устройств (подача воздуха непосредственно к местам кавитации на лопастях, установка антикавитационных планок на лопастях и т. д.) и др.;
- дата последнего ремонта РК и КРК, перечень и результаты работ, проводившихся при этом ремонте (дефектоскопия металла, балансировка РК, если они проводились);
- число часов работы ГА после последнего ремонта РК и/или КРК.
А.2.2 Обстоятельства, предшествовавшие и сопутствовавшие повреждению:
- режим работы ГА перед повреждением и при повреждении. В каких режимах и как длительно ГА работал перед повреждением. Была ли длительная работа в нерасчетных режимах: XX, малые нагрузки, перегрузки, низкие напоры, нерасчетная высота отсасывания и др.;
- какие изменения режимов проводились непосредственно перед повреждением: набор или снятие нагрузки, пуск, останов, сброс нагрузки и т. д. Осуществлялись ли эти операции на автоматическом или на ручном управлении. Указать точное время проведения всех операций и время останова при повреждении;
- каким образом был остановлен ГА при повреждении: действием защиты или оперативным персоналом;
- особенности поведения ГА перед повреждением и при повреждении:
а) имелись ли замечания к системе регулирования («качания» в системе, пульсация давления в маслопроводах, частое включение насосов МНУ и др.);
б) отмечались ли повышенное биение вала гидротурбины и повышенная вибрация узлов гидротурбины;
в) появлялись ли посторонние шумы и стуки в проточной части гидротурбины или в других узлах ГА.
А.2.3 Объем обследований РК при повреждении:
- осмотр всех доступных поверхностей РК и лабиринтных уплотнений (для РО-гидротурбины) с регистрацией явных повреждений и нарушений: обломов кромок лопастей, смятий, вырыва облицовки лопастей, кавитационных повреждений, трещин в основном и наплавленном металле и др.;
82
ГОСТ Р 55260.3.2—2023
- ВИК всех доступных поверхностей РК:
а) указание местоположения, площади и глубины повреждений;
б) определение зазоров и правильности формы (отсутствие овальности) лабиринтных уплотнений для РО-гидротурбины;
в) измерение зазоров между лопастями и КРК ПЛ- или ПР-гидротурбины;
г) проверка действительных геометрических размеров лопастной системы (при необходимости);
- проведение дефектоскопии металла лопастей на входных, выходных и периферийных кромках, в зоне гантельных переходов, а также в подозрительных по результатам ВИК местах, включая обнаруженные трещины на лопастях и других деталях РК с использованием методов МПД, ПВК, травления или других методов;
- обследование крепежа деталей РК (плотность затяжки и состояние болтов крепления лопастей ПЛ-гидротурбин, плотность соединения конуса и обтекателя РК). При необходимости проведение ультразвукового контроля болтов крепления лопастей РК ПЛ-гидротурбины;
- исследование поверхности излома кусков лопастей или болтов крепления лопастей ПЛ-гидротурбины (при наличии) для выявления возможных металлургических дефектов и установления характера разрушения (усталостный, от перегрузки и др.);
- лабораторные исследования металла (при необходимости) для определения его прочностных свойств и соответствия заводским требованиям (химический анализ, определение механических свойств, металлографические исследования и др.).
А.2.4 Объем обследований КРК гидротурбины при повреждениях:
- осмотр всех доступных поверхностей КРК и СП с регистрацией явных повреждений облицовки: вырывов кусков облицовки, вмятин от действия посторонних предметов или от задевания лопастей за камеру, кавитационных разрушений, трещин и др.;
- ВИК всех доступных поверхностей КРК и СП с указанием местоположения, размеров и глубины повреждений облицовки; при сквозном разрушении облицовки или ее вырыве указывают состояние бетона в месте вырыва (глубину вырывания);
- определение мест и размеров отставания облицовки от бетона и наличие пустот за облицовкой путем простукивания или инструментальным способом;
- проведение дефектоскопии металла облицовки в местах наличия трещин и других локальных дефектов по результатам ВИК;
- проведение обследований и анализа поверхности излома металла в местах вырыва облицовки для выявления характера разрушения (ударный, усталостный и пр.). При необходимости производится химический, металлографический и другие анализы металла облицовки;
- определение фактической толщины облицовки КРК в местах повреждения;
- определение формы КРК (выявление местных выступов, впадин или эллипсности) в горизонтальной плоскости по оси поворота лопастей или близкой к ней;
- определение состояния отъемного сегмента КРК ПЛ-гидротурбины:
а) обследование рабочей поверхности отъемного сегмента (со стороны проточной части турбины);
б) обследование крепежа (затяжка и состояние талрепов, домкратов, болтов по периметру);
в) проверка состояния ребер жесткости.
А.З Направляющие подшипники гидротурбины и гидрогенератора
А.3.1 Общие данные по ГА и направляющим подшипникам:
- тип гидротурбины, тип и исполнение гидрогенератора;
- мощность гидротурбины, частота вращения;
- основные данные по поврежденному направляющему подшипнику:
а) тип (кольцевой резиновый на водяной смазке, сегментный резиновый на водяной смазке, кольцевой баббитовый на масляной смазке, сегментный баббитовый на масляной смазке);
б) диаметр расточки вкладышей (сегментов) подшипника; высота кольцевого подшипника, число вкладышей; расположение вкладышей в один или в два яруса по высоте;
в) число и размеры сегментов (в сегментных подшипниках): высота, ширина;
г) тип уплотнения вала над и под направляющим подшипником (торцевой резиновый, торцевой углеграфитовый, воротниковый и др.);
д) величина эксцентриситета сегментов (для сегментных направляющих подшипников);
е) система опирания сегментов в сегментных подшипниках (на сферический вкладыш, на болт со сферической поверхностью, на опору с цилиндрической поверхностью);
ж) способ регулировки зазоров (прокладками, болтовой, клиновой);
и) нормативная величина зазора между валом и вкладышами (сегментами);
к) способ смазки (самоциркуляция масла в ванне, принудительная циркуляция с помощью электронасоса, принудительная циркуляция с помощью трубок Пито и вращающейся маслованны, проточная система и др.);
л) система охлаждения масла в направляющих подшипниках на масляной смазке (с помощью встроенных маслоохладителей, в охлаждающих отсеках обтекателя крышки турбины и др.);
83
ГОСТ Р 55260.3.2—2023
- дата ввода в эксплуатацию данного ГА; дата последнего КР, перечень работ, проводившихся с направляющими подшипниками ГА при этом ремонте (по всем подшипникам);
- повреждения, имевшиеся на данном направляющем подшипнике ранее; краткое описание, причины;
- мероприятия, проводившиеся на данном направляющем подшипнике в целях повышения его надежности (изменение или замена элементов конструкции, изменение системы смазки и охлаждения и др.);
- какие операции и когда производились на данном направляющем подшипнике последний раз (регулировка зазоров, проверка и подтяжка крепежа, ревизия поверхностей трения и др.);
- во скольких сегментах или вкладышах баббитового подшипника установлены термосопротивления и термосигнализаторы. Какова величина уставок на сигнал и на останов ГА;
- какими средствами осуществляется контроль смазки подшипника (расход воды или масла, давление воды или масла в камере подшипника, уровень воды или масла и др.);
- какими средствами и с какой периодичностью осуществляется контроль относительных перемещений вала у направляющего подшипника.
А.3.2 Обстоятельства, предшествовавшие и сопутствовавшие повреждению:
- режим работы ГА перед повреждением и при повреждении. В каких режимах и как длительно ГА работал перед повреждением (включая отклонения уровней бьефов от расчетных по напору и высоте отсасывания);
- какие изменения режимов проводились непосредственно перед повреждением (набор или снятие нагрузки, перевод в режим СК или из режима СК, пуск, останов). Осуществлялись ли эти операции на автоматическом или ручном управлении. Указать точное время проведения всех операций и время останова при повреждении;
- каким образом остановлен ГА при повреждении: действием защиты или оперативным персоналом;
- особенности поведения ГА перед повреждением и во время повреждения: имелись ли замечания к работе системы регулирования, системы автоматики и другим системам. Не отмечалось ли повышенной абсолютной вибрации корпуса подшипника и/или относительной вибрации вала, появления постоянных стуков и шумов в ГА и т. п.;
- каково было значение параметров, характеризующих работу подшипника перед повреждением и при повреждении: относительные вибрации вала, расход воды на смазку и давление воды в камере подшипника на водяной смазке, температуры сегментов и масла подшипника на масляной смазке. Происходило ли изменение параметров быстро, медленно или они были постоянными.
А.3.3 Объем обследования направляющего подшипника при повреждении:
- измерение зазоров между валом и сегментами (вкладышами) перед разборкой подшипника;
- проверка крепления корпуса ТП к крышке гидротурбины и корпусов ГП;
- проверка состояния поверхностей трения сегментов (вкладышей) с отражением в формулярах мест и размеров местных повреждений (трещин, царапин, вырывов и выкрашиваний резины или баббита и др.), степени износа, отставаний резины или баббита от основания;
- проверка состояния облицовки вала с отражением в формуляре местных повреждений, трещин, рисок, обрыва электрозаклепок и т. д.;
- определение степени износа облицовки вала подшипника на водяной смазке и проверка ее эллипсности;
- проверка состояния опорных болтов или опорных вкладышей в сегментных подшипниках (смятие опорных поверхностей, состояние резьбы и пр.);
- проверка состояния уплотнений подшипника: поверхностей трения резинового кольца и вращающегося диска в торцевых уплотнениях, состояние резины и ее крепления в манжетных уплотнениях, состояние элементов углеграфитового уплотнения и др.;
- проверка состояния фильтров в системе смазки резиновых подшипников, величины расхода воды на смазку, состояние запорных и регулирующих устройств, устройств выпуска воздуха из камеры подшипника.
А.4 Маслоприемники
А.4.1 Общие данные по ГА и маслоприемнику:
- тип гидротурбины, тип и исполнение гидрогенератора, расположение направляющего подшипника(-ов) гидрогенератора;
- мощность гидрогенератора, частота вращения;
- основные данные маслоприемника:
а) тип маслоприемника (высокий с внешним расположением маслопроводов; пониженной высоты с внешним расположением маслопроводов; частично утопленный в полости вала с закрытым расположением маслопроводов); для последнего типа указать также типоразмер;
б) давление масла в системе регулирования;
в) внутренний диаметр подводящих маслопроводов;
г) внутренний диаметр сливного(-ых) маслопровода(-ов) из сливной ванны маслоприемника;
д) внешние диаметры штанг маслоприемника;
- дата ввода в эксплуатацию данного ГА; дата последнего ремонта маслоприемника и перечень работ, проводившихся в нем при этом ремонте;
- повреждения, имевшиеся на данном маслоприемнике за последние 10 лет (или нарушения в его работе), их даты, краткое описание, причины;
84
ГОСТ Р 55260.3.2—2023
- мероприятия, проводившиеся на данном маслоприемнике в процессе эксплуатации в целях повышения его надежности (изменение, замена или введение дополнительных элементов конструкции).
А.4.2 Обстоятельства, предшествовавшие и сопутствовавшие повреждению:
- режим работы агрегата перед повреждением и при повреждении. В каких режимах и как длительно агрегат работал перед повреждением;
- какие изменения режимов проводились непосредственно перед повреждением: набор или снятие нагрузки, пуск, останов, режимы испытаний (сброс нагрузки, разобщение комбинаторной зависимости). Осуществлялись ли эти мероприятия на автоматическом или на ручном управлении. Указать точное время проведения всех операций и время останова при повреждении;
- каким образом остановлен ГА при повреждении: действием защиты или оперативным персоналом;
- особенности поведения ГА перед повреждением и при повреждении:
а) имелись ли замечания к системе регулирования («качания», плохой цикл работы насосов МНУ, повышение температуры масла в системе регулирования и др.);
б) наблюдались ли повышенные протечки масла или его выплескивание через сливную ванну маслопри-емника;
в) отмечались ли повышенная вибрация или биения вала гидрогенератора;
г) появлялись ли посторонние шумы и стуки на ГА, в каком месте и др.;
- каково было значение следующих параметров перед повреждением: биения вала гидрогенератора, цикла насосов МНУ, температуры масла в системе регулирования. Происходило ли изменение этих параметров перед повреждением и как (быстро, медленно).
А.4.3 Объем обследования маслоприемника при повреждениях:
- измерение диаметров втулок и штанг; определение зазоров между ними;
- измерение зазоров между сегментами и втулкой ГП;
- обследование втулок маслоприемника с отражением в акте и формуляре плотности их посадки на своих местах, наличия задиров, натиров и других дефектов на поверхности трения и др.;
- обследование штанг, выявление трещин, обломов у фланцевого соединения, плотности крепежа. Выявление состояния поверхностей трения штанг с отражением в акте и формуляре выработки металла, полос бронзы, изменения цвета поверхности и других дефектов;
- выявление состояния узлов механизма обратной связи;
- определение зазоров по лабиринту маслоприемника;
- проверка состояния изоляции маслоприемника от подшипниковых токов.
А.5 Подпятник
А.5.1 Общие данные ГА и ПП:
- тип гидротурбины, тип и исполнение гидрогенератора, расположение ПП, количество и места расположения направляющих подшипников;
- мощность гидрогенератора, номинальная частота вращения;
- основные данные ПП:
а) тип (однорядный, двухрядный, на гидравлической опоре, пружинном основании и т. д.);
б) конструкция сегментов (с баббитовой облицовкой или с ЭМП-покрытием, однослойные или двухслойные); в) число сегментов;
г) радиальный и тангенциальный (по средней линии) размер сегментов;
д) наружный и внутренний диаметры диска;
е) общая нагрузка на подпятник (расчетная и действительная);
ж) удельная нагрузка на сегменты Па (кг с/см );
и) средняя окружная скорость;
к) величина тангенциального эксцентриситета;
л) тип масла в ванне ПП;
- дата ввода в эксплуатацию ГА. Дата установки в ПП ЭМП-сегментов; дата последнего КР. Указание работ, проводившихся в ПП при этом ремонте. Число часов работы и число пусков агрегата с момента монтажа и с момента последнего КР;
- повреждения, имевшиеся на данном ПП ранее, их даты, краткое описание, причины;
- мероприятия, проводившиеся на данном агрегате в целях повышения надежности ПП (изменения элементов конструкции ПП, введение ограничений в режимы работы агрегата и др.);
- во скольких сегментах ПП (и в каких) установлены термосопротивления (для периодической регистрации температуры) и во скольких сегментах — термосигнализаторы (для сигнализации и защиты). Каковы величины уставок на сигнал и останов агрегата;
- проводились ли мероприятия по повышению эффективности термоконтроля ЭМП-сегментов (прорези в ЭМП-покрытии и др.) и когда.
А.5.2 Обстоятельства, предшествовавшие и сопутствовавшие повреждению:
- режим работы ГА перед повреждением и в момент повреждения. Как длительно и при каких режимах ГА работал перед повреждением;
85
ГОСТ Р 55260.3.2—2023
- какие изменения режимов проводились непосредственно перед повреждением (набор или снятие нагрузки, перевод в режим СК или обратно, пуск, останов). Осуществлялись ли эти операции на автоматическом или ручном управлении. Указать точное время проведения всех операций и время отключения и останова агрегата при повреждении ПП. Каким образом остановлен агрегат при повреждении: действием защиты или дежурным персоналом;
- особенности поведения агрегата перед и во время повреждения ПП: имелись ли замечания к работе системы регулирования, автоматики, торможения и другим системам. Не отмечалось ли повышенной вибрации и повышенного биения вала агрегата, появления посторонних стуков и шумов в агрегате, ненормального изменения уровня масла в ванне ПП и т. п.;
- какова была температура сегментов ПП и масла в ванне во всех точках измерения в течение двух суток до повреждения, непосредственно перед повреждением и при повреждении. Каков был характер изменения температуры перед повреждением: медленное повышение, быстрое повышение, постоянная величина. Каковы были значения температуры подпятников других (хотя бы двух соседних) гидроагрегатов ГЭС.
А.5.3 Объем обследования ПП. При обследовании поврежденного ПП должно быть проверено и отражено следующее:
- состояние рабочей поверхности сегментов. Должны быть отражены в формуляре и указаны места и размеры повреждений:
а) подплавлений, выкрашиваний и выпучивания баббита, истирание, натиры, риски и другие дефекты на рабочей поверхности;
б) степень износа рабочей поверхности ЭМП-сегментов по контрольным рискам или по измерениям толщины сегментов в контрольных точках;
в) состояние скосов на набегающей и сбегающей кромках фторопластовой поверхности ЭМП-сегментов;
г) наличие и места отставания баббита от стального основания;
д) нарушение припайки ЭМП-вкладыша к стальному основанию сегмента и другие возможные нарушения;
- состояние зеркальной поверхности диска. Визуальное обследование диска (с отражением наличия рисок, царапин, каверн, помутнения и других дефектов зеркальной поверхности). При необходимости определение шероховатости методом слепков или другим методом. Определение волнистости (макронеровности) зеркальной поверхности диска путем прокрутки или с помощью поверочной линейки;
- состояние прокладок между диском и втулкой (при их наличии). Наличие зазоров между втулкой и диском ПП при поднятом на тормозах и при опущенном роторе путем осмотра и промеров по контуру. Проверка плотности затяжки болтов крепления диска к втулке;
- состояние тарельчатых опор. Обследование в целях выявления наличия или отсутствия трещин на верхней поверхности; определение состояния нижней поверхности в месте контакта с опорным болтом с регистрацией глубины и диаметра вмятины от сферической головки болта. При необходимости проверка на прессе прогиба опор;
- состояние головок опорных болтов. Определение величины смятия сферической поверхности болтов или вкладышей в болты с помощью специального шаблона и щупа. При необходимости проверка твердости головок опорных болтов или вкладышей, определение состояния резьбы болтов и втулок;
- определение в двухрядных подпятниках состояния поверхностей цилиндрических опор и сопряженных с ними поверхностей балансиров;
- наличие вмятин и натиров на упорах, ограничивающих радиальное и тангенциальное смещение сегментов, и на сегментах в местах соприкосновения с упорами. Глубина и расположение вмятин и натиров;
- величина действительных зазоров между сегментами и упорами (в тангенциальном и радиальном направлениях);
- свобода качания сегментов (отсутствие защемления сегментов между упорами), а в двухрядных подпятниках — свобода качания балансиров;
- действительная величина тангенциального и радиального эксцентриситета сегментов и соответствие его нормативным значениям;
- расстояние от зеркальной поверхности диска ПП на гидравлической опоре до основания в фиксированных точках («маяках») для проверки герметичности упругих камер;
- равномерность осадки упругих камер в подпятниках на гидравлических опорах;
- проверка изоляции между диском и втулкой ПП в генераторах подвесного исполнения;
- анализ масла в ванне ПП в целях определения механических примесей, воды и пр.;
- равномерность распределения нагрузки между сегментами ПП;
- контроль прилегания корпуса ПП ко дну маслованны и дна маслованны к опоре.
86
ГОСТ Р 55260.3.2—2023

-8-
эинвнэ Hindu | о V— | |||
s hi ст ГО J0 о £ го го bi | h/h- иек ‘Koioodu ахэонаиэхииУ /вххэфэИ OMHeHBdioX и виивхэн oiuodxnox ou xogBd qxooxmaoWAdi | СО X— | ||
nxdBaBE вахээнвх вхне^о | V— | |||
киненснихвЕ demoH ‘KHhBEMHBJdo ‘вхву | со X— | |||
® i ° § CL С т Ш ® S Ф ° g &5 £ СП | внидЛии | ю X— | ||
BHndum | X— | |||
BHHLftf | СО X— | |||
S о о ф со о с о 1- о | □z c о О о н hi Ф -8-ф Ct | вххефэУ эинвэиио | см X— | 1 |
tfoiaw | X— | 1 | ||
>s co О CO | вххэфэА эинвэиио | о X— | ||
ВИНЭКСНиХВЕ dswoH ‘BMhBEMHBJdo ‘вхву | О) | 1 | ||
h ‘uuodiHox ojetnAt/iqWedu ю nxiogBdBH nwsdg | ОО | 1 | ||
к ‘ииЬвхвЛииэхе bubhbh э nxiogBdBH tmadg | h- | 1 | ||
сяиИвхвЛниэхе a Bt/caa BXBW/BHHauaoxojsn вхву | со | |||
иивхэ BxdB|/\| | ю | |||
dswoH иохэ^оавд | X- | |||
аиэхиаохохЕИ-Ь’оавд | со | |||
Bxcexdah demon | см | 1 | ||
(quBxetf) хнэтеие | X— | 1 |
87
ГОСТ Р 55260.3.2—2023
Приложение Б (обязательное)
Методики контроля геометрических форм и размеров проточной части гидротурбин
Б.1 Общие положения
Б.1.1 Контроль геометрических форм и размеров проточной части гидротурбин следует выполнять при приемке оборудования в монтаж, в процессе монтажа по мере готовности проточной части гидротурбины и подготовки к монтажу РК, перед приемкой ГА в эксплуатацию, а также при необходимости, вызванной неполадками в работе оборудования в период эксплуатации и выявляемой при осмотрах и освидетельствованиях.
Б. 1.2 Определение геометрических форм и размеров проточной части гидротурбин является формой измерительного контроля и выполняется в соответствии с нормативными требованиями к данной форме контроля.
Допускается на стадии эксплуатации проведение контрольных промеров геометрических форм и размеров проточной части гидротурбин силами персонала ГЭС с участием монтажной (ремонтной) организации при соблюдении требований к средствам измерений и необходимой точности измерений в соответствии с проектной документацией или рекомендациями завода-изготовителя.
При наличии технической возможности определение геометрических форм и размеров спиральной камеры, РК, КРК и др. может быть проведено методами лазерного ЗЭ-сканирования при условии обеспечения необходимой точности измерений в условиях ГЭС, особенно при проведении ремонтов без полной разборки ГА.
Б.1.3 Для определения геометрических форм и размеров проточной части применяются:
- прямой метод измерения, при котором предусматривается непосредственное определение искомой величины;
- косвенный метод, позволяющий определить эту величину по результатам измерения другой величины, связанной с искомой определенной зависимостью.
Б. 1.4 Выбор элементов, подлежащих измерению, основан на ограничении проверки небольшого числа параметров, характерных для данного узла.
При обнаружении несоответствия проекту или формуляру характерного параметра, например шага лопастей (характеризующего наклон, угол установки и расстояние в свету), измерения производятся более подробно для определения причины несоответствия. При этом мерное сечение выбирается в плоскости, удобной для измерений.
Б. 1.5 По результатам контроля устанавливают соответствие фактических геометрических размеров требованиям нормативно-технической и конструкторской документации. Допускаемые отклонения измеряемых величин, если иное не отражено в конструкторской документации, рекомендуется принимать в соответствии с [10].
К числу таких отклонений относятся:
- различие углов установки лопастей РК ПЛ-типа;
- несоответствие диаметров РК турбины и КРК;
- различие проходных сечений между лопастями РК;
- несоответствие профиля лопастей РК расчетному;
- несоответствие профиля элементов проточной части турбины расчетному (например, зуба спирали или колена отсасывающей трубы);
- недостаточная чистота обработки поверхностей проточной части (в стыках, неровности металла и бетона и др.).
Б.2 Рабочее колесо радиально-осевого типа
Б.2.1 У РО-гидротурбин измерению подлежат:
- размеры и равномерность зазоров в лабиринтных уплотнениях верхнего обода;
- величина выступа кромок входного сечения РК относительно закладных частей и крышки турбины;
- высотное положение РК.
Б.2.2 Зазор в лабиринтных уплотнениях контролируют по положению лабиринтных колец на верхнем и нижнем ободах РК (вращающихся) по отношению к кольцам в крышке турбины и на фундаментном кольце (неподвижным).
Размер зазора в лабиринтных уплотнениях определяется методом проворота РК на 360° и «в статике».
Отклонение зазоров в лабиринтных уплотнениях РК радиально-осевых турбин после центровки ГА не должно превышать 20 % проектного зазора.
Неконцентричность между собой верхнего и нижнего лабиринтных колец и несоосность их с валом допускается в пределах 10 % от размера одностороннего зазора в лабиринтном уплотнении РК.
Б.2.3 Величина выступа кромок входного сечения РК относительно закладных частей и крышки турбины в зависимости от диаметра РК, соответственно, не должна превышать значений, приведенных в таблице Б.2.1.
Б.2.4 Высотное положение РК в кратере (для вертикальных агрегатов) определяется фактическим положением смонтированных фундаментных и закладных частей. При отсутствии заводских или монтажных норм зазоры
88
ГОСТ Р 55260.3.2—2023
между вращающимися и неподвижными частями гидротурбины могут иметь отклонения от проектных значений в пределах допусков, приведенных в таблице Б.2.1.
Таблица Б.2.1 — Зазоры между вращающимися и неподвижными частями РО-гидротурбин
Проверяемое положение | Место замера | Величина отклонения, ± мм, в зависимости от диаметра РК, м | |||||
2,0 | 4,0 | 6,0 | 8,0 | 9,5 | 10,5 | ||
Высотное положение рабочих колес РО-гидротурбин | Совмещение уплотнительных колец на верхнем ободе РК (вращающегося) и в крышке турбины (неподвижного) | 1,0 | 2,0 | 2,5 | 3,0 | — | — |
Величина выступа кромок входного сечения рабочих колес РО-гидротурбин | Верхняя и нижняя входные кромки РК относительно плоскости крышки турбины | 1,0 | 1,0 | 2.0 | 3,0 | — | — |
Зазоры между рабочим колесом и неподвижными частями гидротурбины и в лабиринтных уплотнениях РО-гидротурбин | В местах, указанных в заводской и монтажной документации | В пределах 20 % от заданного проектного зазора |
Б.2.5 В целях выявления причин отклонений технических параметров агрегата от проектных значений, установления причин повышенных вибраций, ускоренного износа или преждевременных разрушений элементов РК, уточнения оценки ресурса ГА и обоснования замены или реконструкции оборудования дополнительно могут быть определены (см. рисунок Б.2.1):
- расстояние между входными кромками лопастей в горизонтальном сечении по хорде ^;
- расстояние между выходными кромками лопастей в горизонтальном сечении по хорде t2;
- высота входного сечения h^
- высота (площадь) выходного сечения h2,
- толщина лопасти у выходной кромки;
- угол входа/выхода лопасти;
- иные параметры, влияющие на техническое состояние и ресурс РК.
Максимально допустимые отклонения по критерию однородности (отношение измеренного значения к среднему) приведены в [10]. Нарушение критериев неоднородности приводит к неравномерному распределению нагрузок на РК в процессе нормальной эксплуатации.
Б.2.6 Образцы формуляров проведения контроля геометрии РК РО-типа и лабиринтных уплотнений РО-гидротурбин представлены на рисунках Б.2.1 и Б.2.2.
89
ГОСТ Р 55260.3.2—2023
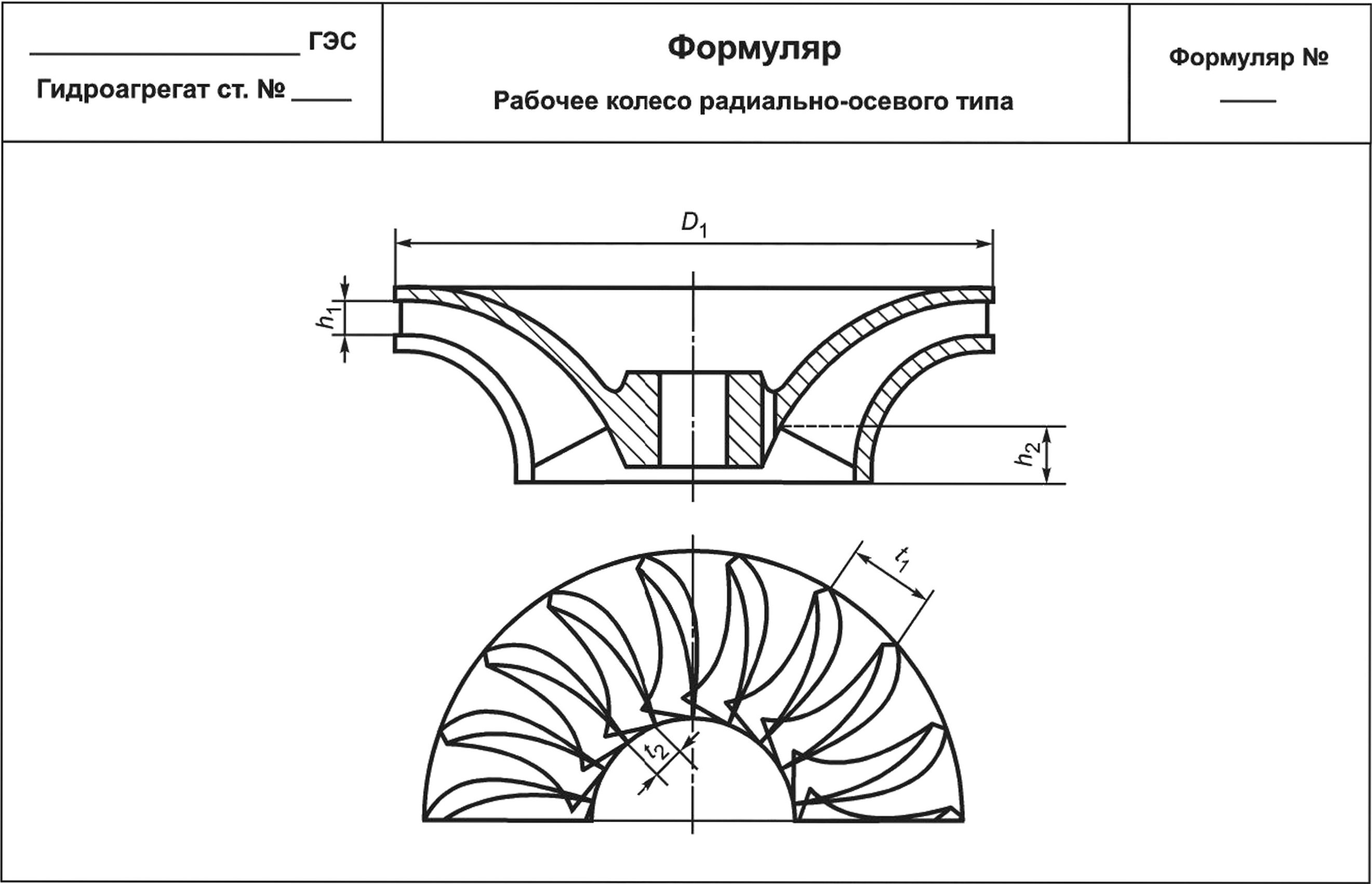
Обозначения | Размеры между лопастями, номер | |||||||||
1—2 | 2—3 | 3—4 | 4—5 | 5—6 | 6—7 | 7—8 | Чертеж N° | |||
^1 | Фактическое | ^ (по чертежу) = | ||||||||
^1 | Фактическое отклонение | допустимое отклонение (по чертежу или НТД) = | ||||||||
f2 | Фактическое | ^2 (по чертежу) = | ||||||||
△f2 | Фактическое отклонение | допустимое отклонение (по чертежу или НТД) = |
Обозначения | Размер по чертежу N° | Фактические размеры по осям | Фактическое максимальное отклонение | Допустимое отклонение по чертежу или НТД | |||
+х | +У | -х | "У | ||||
Л1 | |||||||
^2 |
Замеры производил Дата
Рисунок Б.2.1 — Формуляр проведения контроля геометрии РК РО-типа
90
ГОСТ Р 55260.3.2—2023
_________________ГЭС
Гидроагрегат ст. №
Формуляр
Лабиринтные уплотнения радиально-осевых турбин
Формуляр №
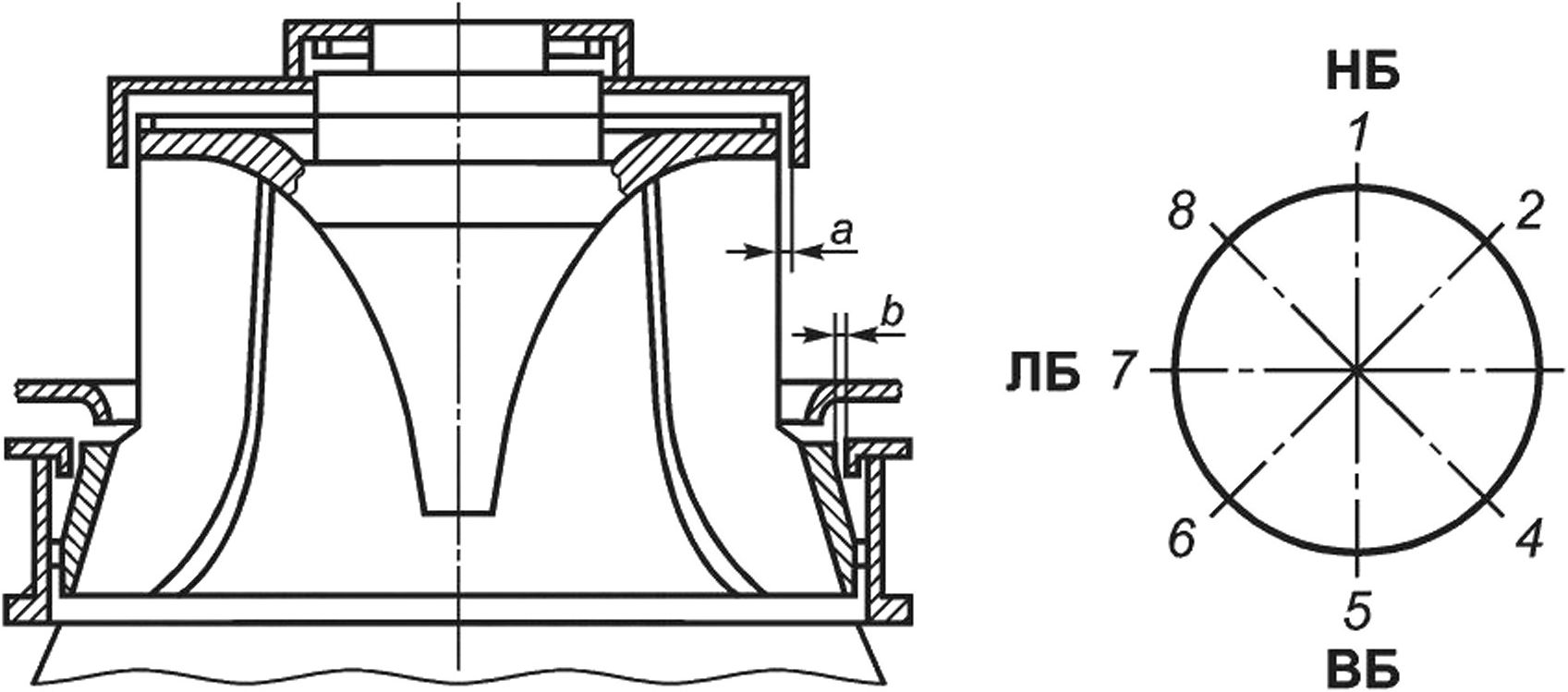
3 ПБ

Рисунок Б.2.2 — Формуляр проведения контроля лабиринтных уплотнений РО-турбин
Б.З Рабочее колесо поворотно-лопастного типа
Б.3.1 У ПЛ-гидротурбин измерению подлежат:
- форма периферийных кромок лопастей;
- форма РК;
- размер и равномерность зазора «камера — лопасть».
Б.3.2 Размер зазора «камера — лопасть» определяется методом проворота РК на 360° и «в статике».
При определении зазора методом проворота количество точек при определении формы РК соответствует количеству лопастей, при определении формы КРК — не менее восьми.
При определении зазора «в статике» фиксируются величины зазоров (по каждой лопасти) при закрепленном положении РК.
Схема измерения зазора представлена на рисунке Б.3.1.
Размер зазора «камера — лопасть» должен соответствовать требованиям конструкторской и/или монтажной документации. При отсутствии соответствующих документов зазор «камера — лопасть» не должен превышать 0,001 от диаметра РК. Отклонения зазора «камера — лопасть» после центровки ГА не должны превышать 20 % от заданного проектного зазора «камера — лопасть».
Зазоры между лопастями РК и КРК ПЛ-гидротурбин (в открытом и закрытом положениях лопастей либо фиксированном положении для гидроагрегатов, переведенных в пропеллерный режим работы) после соединения валов ГА и центрирования могут иметь отклонения в пределах 20 % их номинального значения, установленного заводом-изготовителем.
Б.3.3 Высотное положение РК в кратере (для вертикальных агрегатов) определяется фактическим положением смонтированных фундаментных и закладных частей. Допускаемые отклонения от проектных значений в пределах допусков приведены в таблице Б.3.1.
91
ГОСТ Р 55260.3.2—2023
Таблица Б.3.1 — Зазоры между вращающимися и неподвижными частями гидротурбин
Проверяемое положение | Место замера | Величина отклонения, ± мм, в зависимости от диаметра РК, м | |||||
2,0 | 4,0 | 6,0 | 8,0 | 9,5 | 10,5 | ||
Высотное положение рабочих колес ПЛ-гидротурбин | От верхней плоскости нижнего кольца НА до верхнего торца втулки РК | — | 3,0 | 4,0 | 5,0 | 6,0 | 7,0 |
Б.3.4 В целях выявления причин отклонений технических параметров агрегата от проектных значений, установления причин повышенных вибраций, ускоренного износа или преждевременных разрушений элементов РК, уточнения оценки ресурса ГА и обоснования замены или реконструкции оборудования дополнительно могут быть определены (см. рисунок Б.3.1):
- расстояние между входными кромками лопастей в кольцевом сечении по хорде ^;
- расстояние между выходными кромками лопастей в кольцевом сечении по хорде t2;
- абсолютные габаритные размеры РК по замеру радиального расстояния AR от крайней точки лопасти, лежащей в горизонтальной плоскости, проходящей через ось поворота лопастей;
- угол установки лопастей;
- иные параметры, влияющие на техническое состояние и ресурс РК.
Примечание — Измерения проводятся при максимальном и минимальном углах разворота лопастей.
Максимально допустимые отклонения по критерию однородности (отношение измеренного значения к среднему) рекомендуется принимать в соответствии с рекомендациями [10]. Нарушение критериев неоднородности приводит к неравномерному распределению нагрузок на РК в процессе нормальной эксплуатации.
Б.3.5 Образец формуляра проведения контроля геометрии РК ПЛ-гидротурбин представлен на рисунке Б.3.2, зазора «камера — лопасть» — на рисунке Б.3.3.
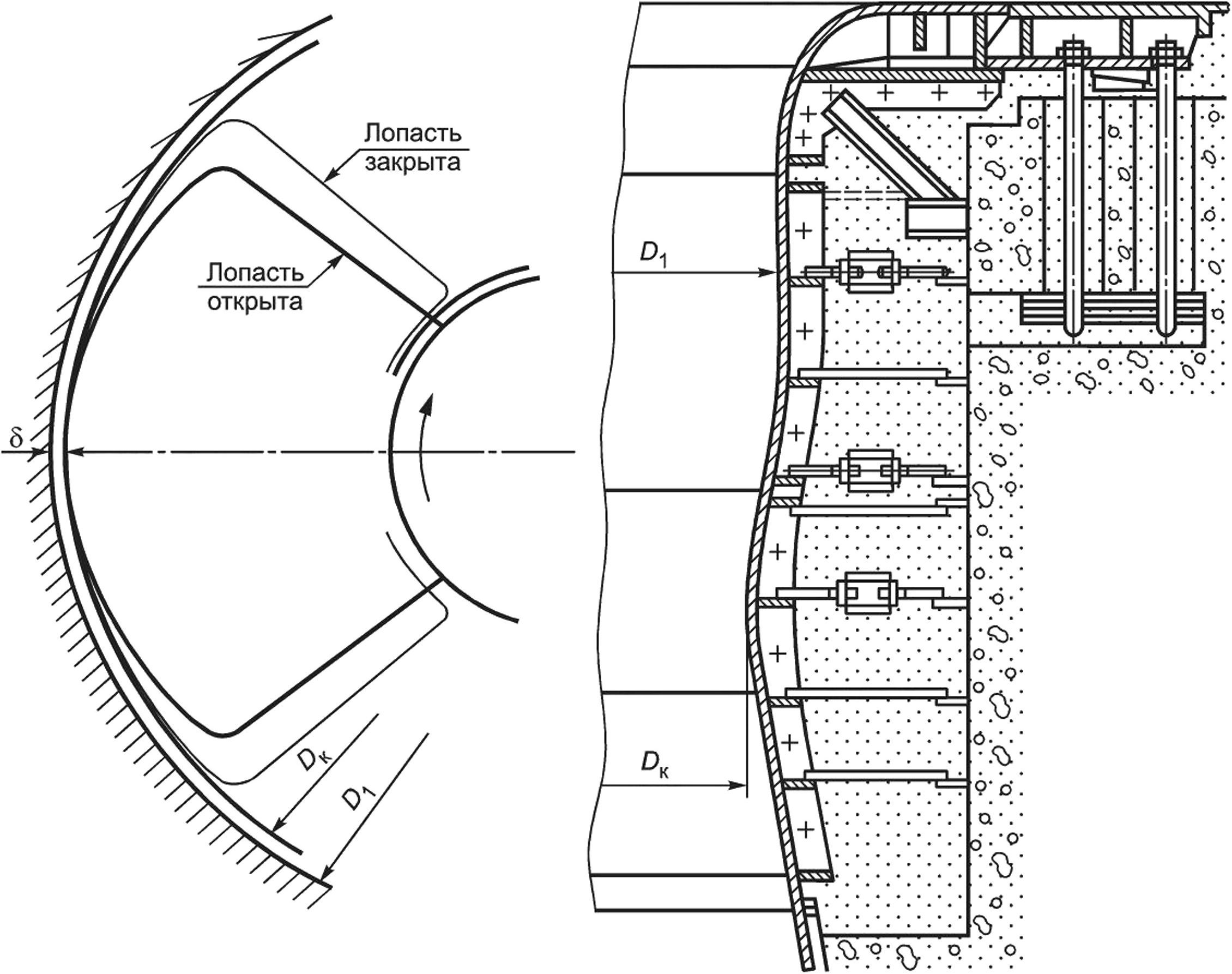
Рисунок Б.3.1 —Схема измерения зазора «камера — лопасть» для гидротурбин поворотно-лопастного типа
92
ГОСТ Р 55260.3.2—2023
ГЭС | Формуляр Рабочее колесо поворотно-лопастного типа | Формуляр № |
Гидроагрегат ст. №____ | ||
Обозначения | Чертеж № | Размер по чертежу | Фактический размер | Фактическое отклонение | Допустимое отклонение |
△Я |
Обозначения | Размеры между лопастями, номер | ||||||
1—2 | 2—3 | 3—4 | А—1 | Допустимое отклонение по чертежу или НТД | |||
'l | По чертежу | ||||||
Фактическое | |||||||
^1 | Фактическое отклонение | ||||||
*2 | По чертежу | ||||||
Фактическое | |||||||
△t2 | Фактическое отклонение |
Замеры производил Дата
Рисунок Б.3.2 — Формуляр проведения контроля геометрии РК поворотно-лопастного типа
93
________________ГЭС Гидроагрегат ст. №____ Угол разворота лопастей______° | Формуляр для определения форм КРК и формы РК (до и после ремонта) | Формуляр №___ |
1. Форма камеры рабочего колеса (сопровождение с лоп. №__, отсчет начат с ВБ)
Точка отсчета | | 1 | 2 | 3 | 4 | 5 | 6 1 7 | 9 | 10 | 11 | 12 | 1 | По чертежу | |
До ремонта | |||||||||||||
Зазор (мм) | | | | | | | | | | | | | | |||||||||||||
После ремонта | |||||||||||||
Зазор(мм) | | | | | | | | | | | | | |
ГОСТ Р 55260.3.2—2023
2. Форма рабочего колеса (от ВБ)
№ лопасти | 1 | 2 | 3 1 4 | | 5 | 1 6 | 7 | 1 | По чертежу |
До ремонта | ||||||||
Зазор (мм) | ||||||||
После ремонта | ||||||||
Зазор (мм) |
3. Зазоры по рабочему колесу «в статике», при этом лопасть №__установлена на ВБ
№ лопасти | 1 | 2 1 3 | 4 | 5 | 6 | 7 | По чертежу |
До ремонта | ||||||
Зазор (мм) | ||||||
После ремонта | ||||||
Зазор (мм) |
Должность | Подпись | Дата | |
Составил | |||
Проверил |
Рисунок Б.3.3 — Формуляр проведения контроля геометрии зазора «камера — лопасть» 5 для ПЛ-гидротурбины
ГОСТ Р 55260.3.2—2023
Б.4 Камера рабочего колеса поворотно-лопастной гидротурбины
Б.4.1 В основу контрольных замеров КРК ПЛ-гидротурбин положены измерения диаметральных размеров, характеризующих соответствие данного сечения правильной окружности.
Б.4.2 Измерению подлежат:
- форма КРК;
- размер и равномерность зазора «камера — лопасть».
Б.4.3 При выемке РК для определения формы и размеров КРК применяют следующие распространенные методы (рисунок Б.4.1):
- прямой метод измерения от струны, совмещенной с осью ГА, с помощью штихмаса или калиброванной рулетки;
- косвенный метод измерения от поворотного приспособления, базирующегося на стойке, совмещенной с базовой струной с помощью штихмаса или индикатора.
Также возможное определение геометрических форм и размеров КРК проведено методами лазерного ЗО-сканирования.
Б.4.4 Без выемки РК геометрию КРК определяют по результатам проворота фиксированной точкой лопасти РК (рисунок Б.4.2).
Б.4.5 Методики и критерии оценки зазора «камера — лопасть» приведены в Б.3.2.
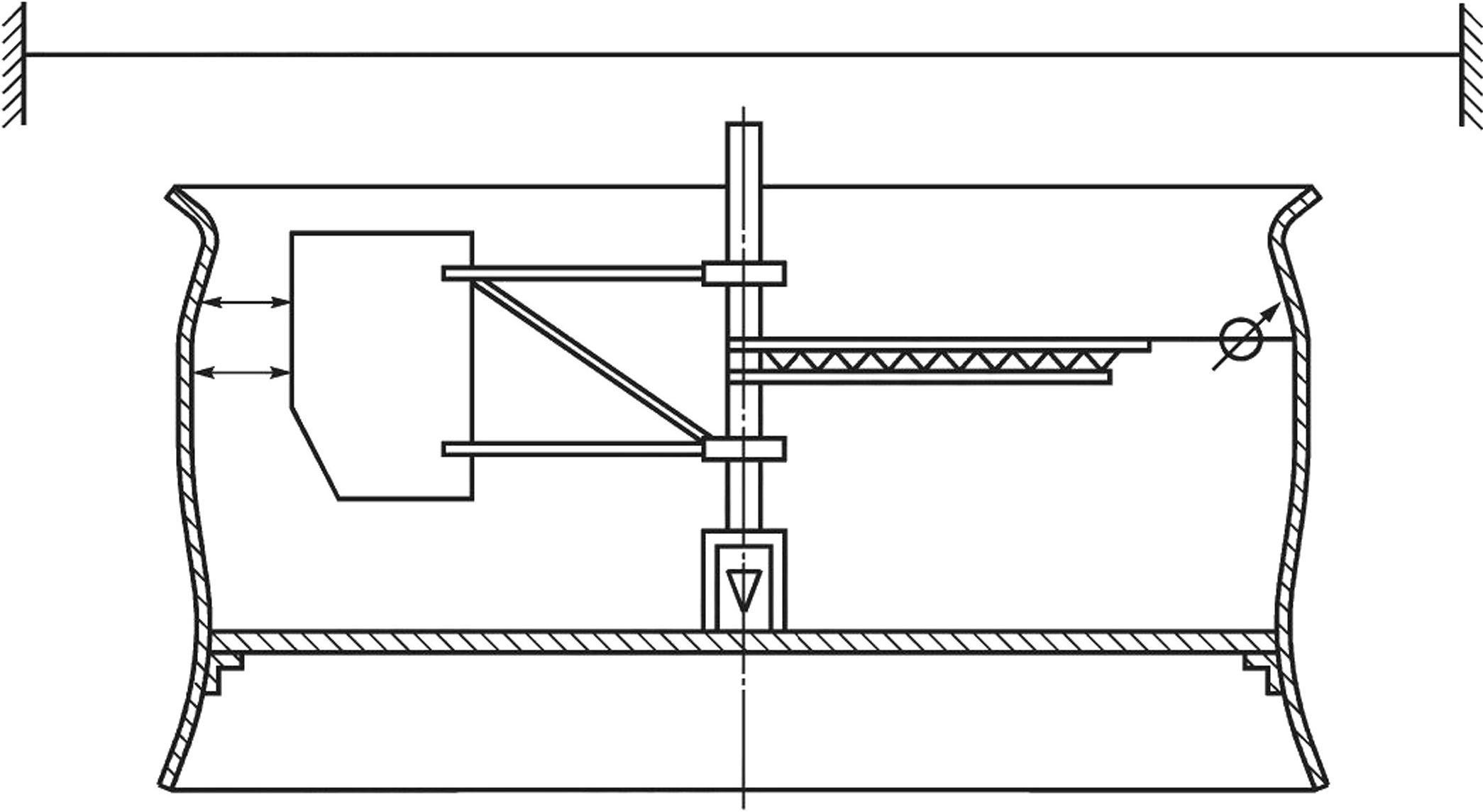
Рисунок Б.4.1 — Проверка размеров КРК с помощью струны
95
ГОСТ Р 55260.3.2—2023
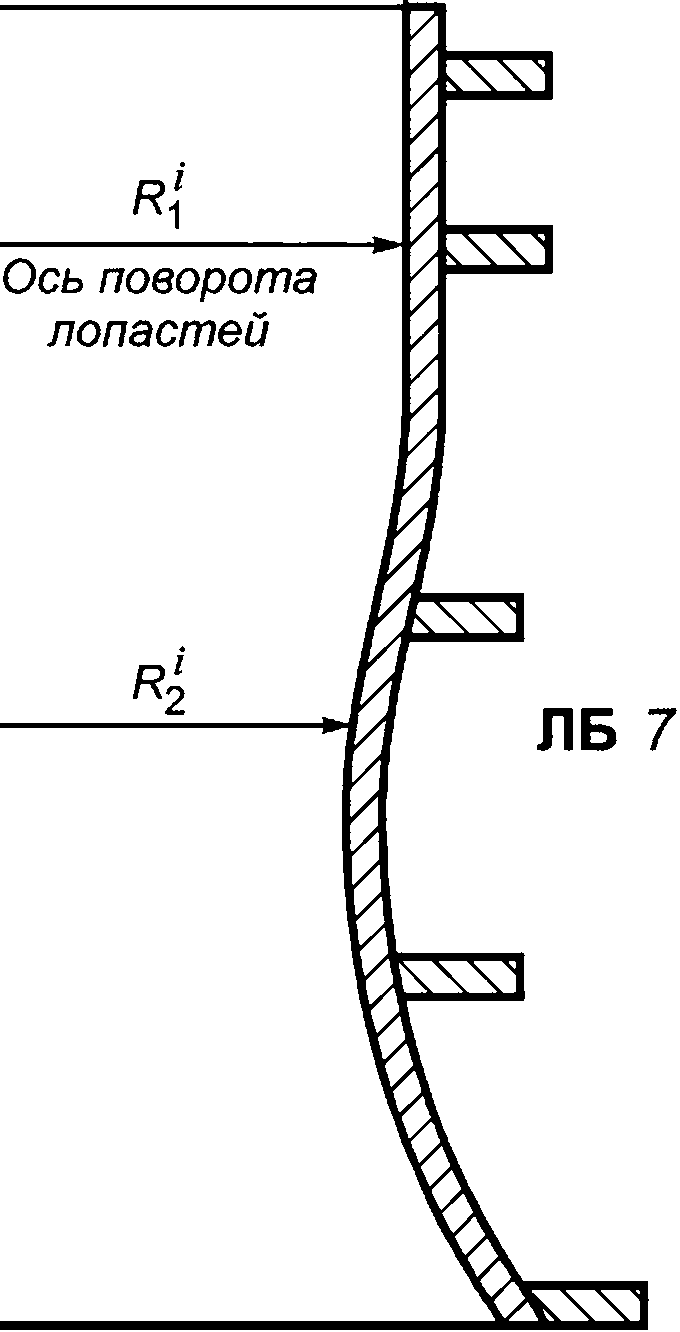
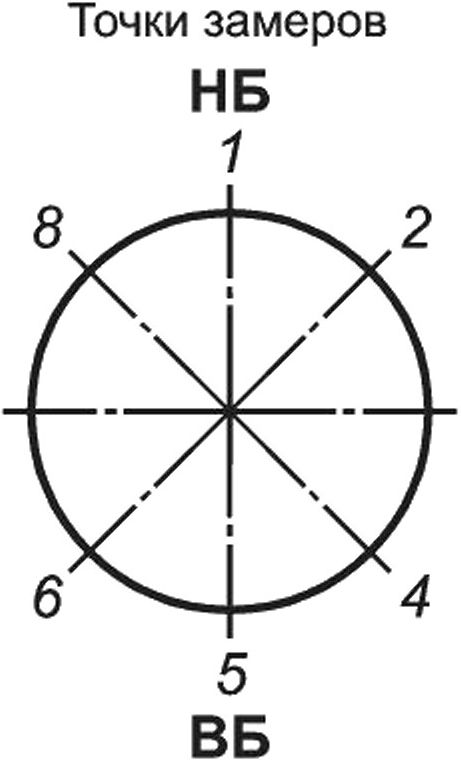
3 ПБ
Точки замеров | Контролируемый параметр, мм | ||||||||
До ремонта | После ремонта | По чертежу № (с указанием допуска) | |||||||
R‘ | «1 | «2 | R1 | «2 | R1 | Ri | «2 | ||
1 | |||||||||
2 | |||||||||
3 | |||||||||
4 | |||||||||
5 | |||||||||
6 | |||||||||
7 | |||||||||
8 |
Рисунок Б.4.2 — Проверка размеров КРК методом проворота РК
Б.5 Спиральная камера
Б.5.1 В данном разделе рассматриваются спиральные камеры таврового или круглого сечения.
Б.5.2 В основе контрольных замеров в спиральной камере лежит проверка взаимно правильного расположения колонн статора и лопаток НА, а также равномерности НА, т. е. относительной разницы расстояний между его лопатками (см. пункт Б.6).
Основными элементами контроля являются подводящая воду часть камеры, статор и НА турбины. При этом уделяется внимание положению зуба спирали.
Б.5.3 Определяющими параметрами являются:
- входное сечение и радиусы спирали спиральной камеры;
- положение колонн статора в плане и их общее положение по отношению к осям х и у;
- расстояние между лопатками, высота и привязка лопаток НА к осям х и у.
96
ГОСТ Р 55260.3.2—2023
Б.5.4 Объем измерений и допуски на установку статоров гидротурбин определяются в соответствии с требованиями [12]. Для статоров с неотъемными колоннами (будь то неразъемная конструкция или конструкция, состоящая из отдельных сегментов) предусматриваются специальные измерения, фиксирующие положение статора в целом относительно осей х и у. Для статоров с отъемными колоннами производятся измерения, фиксирующие положение каждой колонны относительно специальной расчетной окружности, а также относительно радиуса.
Б.5.5 В таблице Б.5.1 приведены допуски на установку статоров, предусмотренные техническими условиями на монтаж гидроагрегатов. Эти же допуски являются определяющими и при контрольных измерениях.
Таблица Б.5.1 — Допуски на установку статоров гидротурбин
Характер отклонения | Отклонение, мм, для диаметра РК, м | |||||
ДО 2,0 | от 2,0 до 3,5 | от 3,5 до 5,5 | от 5,5 ДО 7,5 | от 7,5 ДО 9,5 | от 9,5 до 10,5 | |
Смещение осевых меток на деталях относительно осей гидроагрегата х и у (Ах, Ау) | 2,0 | 2,0 | 2,0 | 3,0 | 5,0 | 5,0 |
Шаг на установочной окружности (по хорде) между колоннами | 8,0 | 8,0 | 10,0 | 12,0 | 15,0 | 15,0 |
Нецилиндричность (расстояние от центральной оси до внутренней расточки детали в местах, заданных формуляром) | 0,5 | 0.8 | 1,0 | 1,2 | 1,5 | 2.0 |
Б.5.6 Спиральная камера таврового сечения
Б.5.6.1 Измерению подлежат (см. рисунок Б.5.1):
- входное сечение турбинного водовода — ширина А в сечении пазов решетки; если имеется разделительный бычок, то измеряются размеры а, Ь и Ду— привязка носка бычка к оси х;
- сечение спирали: радиальный размер 1 (расстояние от внешней окружности установки колонн статора до стенки спирали) и в последующих сечениях — размеры 2, 3 и 4 соответственно по осям х, ху у, ух, вертикальный размер Т (расстояние от потолка до днища спирали) и в последующих сечениях — размеры 2’, 3’ и 4’ по тем же осям.
Б.5.6.2 Измерения вертикальных и горизонтальных размеров спирали производятся с допуском на величину отклонения от геометрической формы в отсасывающих трубах, предусмотренным [12]. При диаметре РК от 2000 мм и выше допустимое значение отклонений для размеров А, а, Ь, Ау, 1—4, 1’—4’ составляет 0,005 проектного размера.
Б.5.6.3 Правильность округления оголовка промежуточного бычка определяется шаблоном, изготовленным по размерам на чертежах проектной документации.
97
ГОСТ Р 55260.3.2—2023
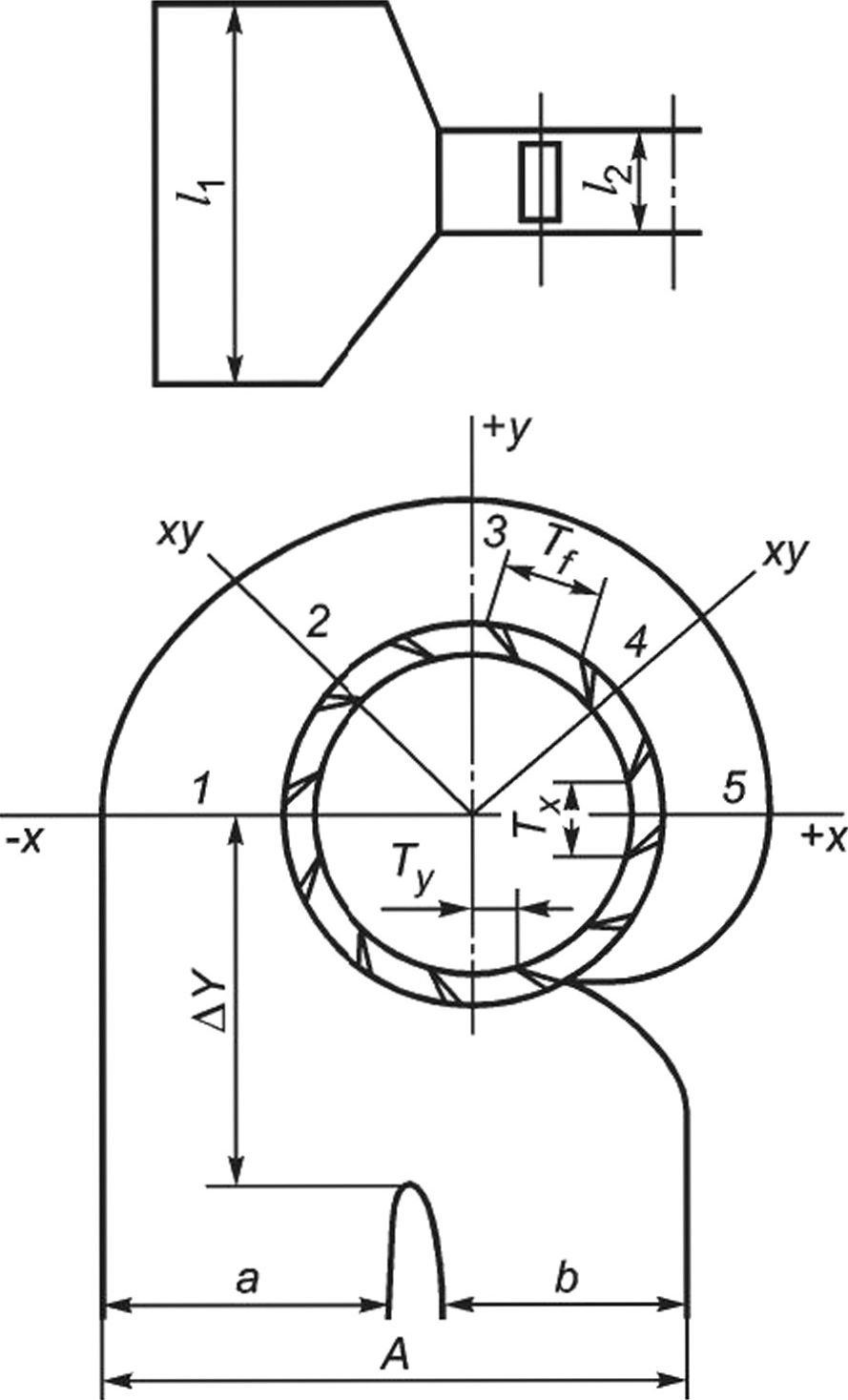
Обозначения | Размер по чертежу № | Фактический размер | Фактическое отклонение | Допустимое отклонение по чертежу или НТД |
А | ||||
а | ||||
b | ||||
△у | ||||
1/1' | ||||
2/2’ | ||||
3/3’ | ||||
4/4’ |
Обозначения | Размеры между колоннами, номер | |||||||||||
1—2 | 2—3 | 3—4 | 4—5 | 5—6 | 6—7 | 7—8 | 8—9 | 9—10 | 10—1 | Допустимое отклонение по чертежу или НТД | ||
тх | По чертежу № | |||||||||||
Фактическое | ||||||||||||
Фактическое отклонение | ||||||||||||
ТУ | По чертежу № | |||||||||||
Фактическое | ||||||||||||
^У | Фактическое отклонение | |||||||||||
По чертежу № | ||||||||||||
Фактическое | ||||||||||||
^f | Фактическое отклонение |
Рисунок Б.5.1 — Контроль геометрии спиральной камеры таврового сечения
98
ГОСТ Р 55260.3.2—2023
Б.5.7 Спиральная камера круглого сечения
Б.5.7.1 Измерению подлежат (см. рисунок Б.5.2):
- в сварных спиралях — сечение спирали: радиальный размер 1 (расстояние от внешней окружности статора до стенки спирали) и в последующих сечениях — размеры 2,3 и т. д. соответственно по осям х, ху, у, ух, в плоскости оси НА; вертикальный размер 1’ и в последующих сечениях — размеры 2’, 3’ и т. д.;
- привязка зуба спирали к оси х— Ту\
- в литых спиралях — расстояние Тх между выходными кромками колонн статора по хорде.
Б.5.7.2 Допуски на измерения:
- нарушение формы сечения сварной спиральной камеры не должно превышать 0,005 размера в данном сечении;
- смещение центральной оси входного сечения спиральной камеры от оси у не должно превышать 12, 18, 25, 30 и 40 мм при диаметре входного сечения спиральной камеры соответственно 2,0; 3,0; 4,5; 6,0 и 8,0 м.
99
ГОСТ Р 55260.3.2—2023
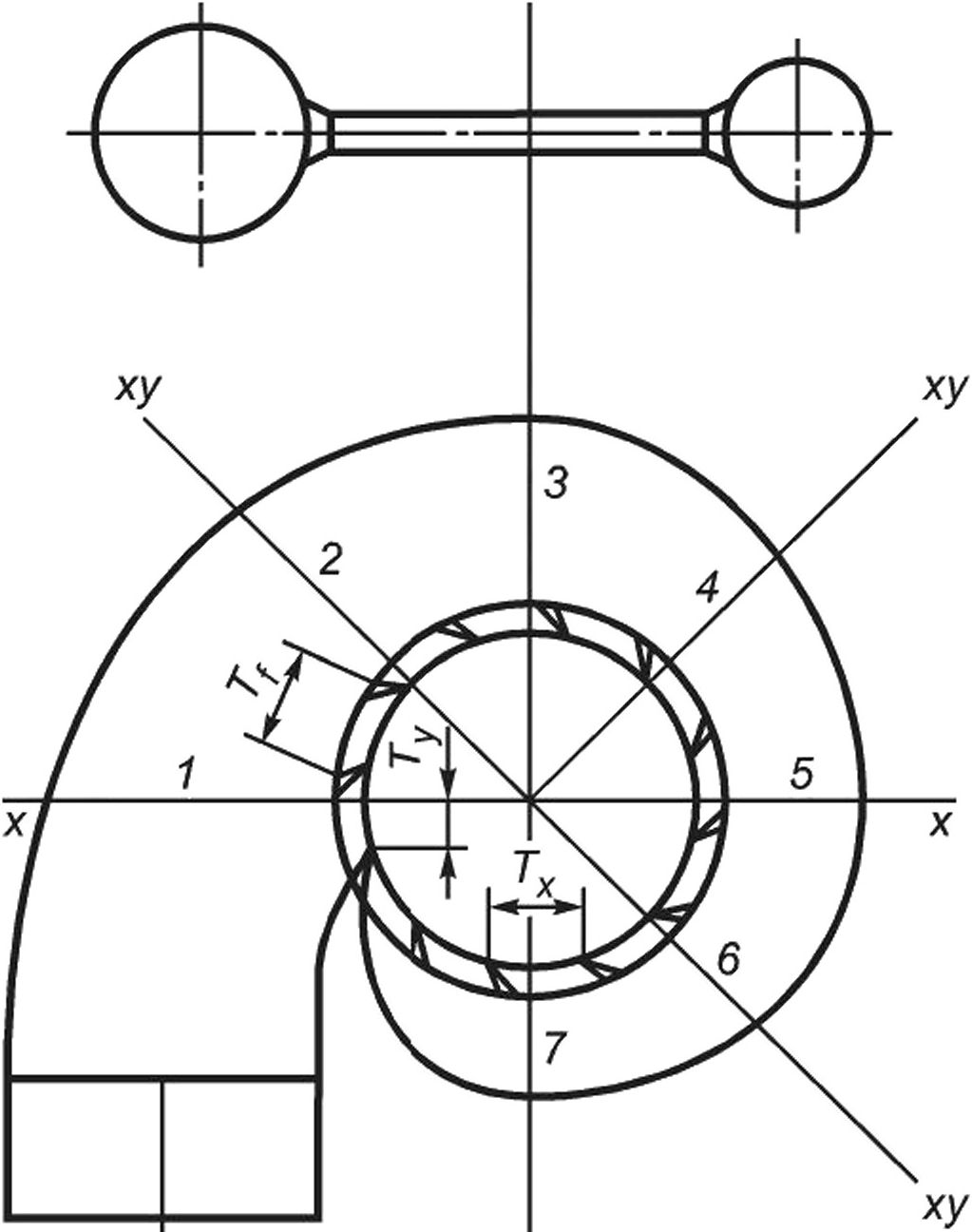
Обозначения | Размер по чертежу № | Фактический размер | Фактическое отклонение | Допустимое отклонение по чертежу или НТД |
1/1’ | ||||
2/2’ | ||||
3/3’ | ||||
4/4’ | ||||
5/5’ | ||||
6/6’ | ||||
7/7’ | ||||
R |
Обозначения | Размеры между колоннами, номер | |||||||||||
1—2 | 2—3 | 3—4 | 4—5 | 5—6 | 6—7 | 7—8 | 8—9 | 9—10 | 10—1 | Допустимое отклонение по чертежу или НТД | ||
тх | По чертежу № | |||||||||||
Фактическое | ||||||||||||
△ Тх | Фактическое отклонение | |||||||||||
т. | По чертежу N° | |||||||||||
Фактическое | ||||||||||||
АТ | Фактическое отклонение | |||||||||||
Tf | По чертежу № | |||||||||||
Фактическое | ||||||||||||
Фактическое отклонение |
Рисунок Б.5.2 — Контроль геометрии спиральной камеры круглого сечения
100
ГОСТ Р 55260.3.2—2023
Б.6 Направляющий аппарат
Б.6.1 Возмущения потока и неравномерность распределения скоростей по периметру НА оказывают влияние на работу ГА в целом, вызывая неравномерность сил, действующих на рабочее колесо турбины.
Б.6.2 Измерению подлежат (см. рисунок Б.6.1):
- расстояние ^ между входными кромками лопаток НА по хорде;
- расстояние t2 между выходными кромками лопаток НА по хорде;
- привязка НКНА к осям у и х;
- высота НА Ьо.
Измерения производятся в любой выбранной горизонтальной плоскости 1-1 при полном открытии НА.
101
ГОСТ Р 55260.3.2—2023
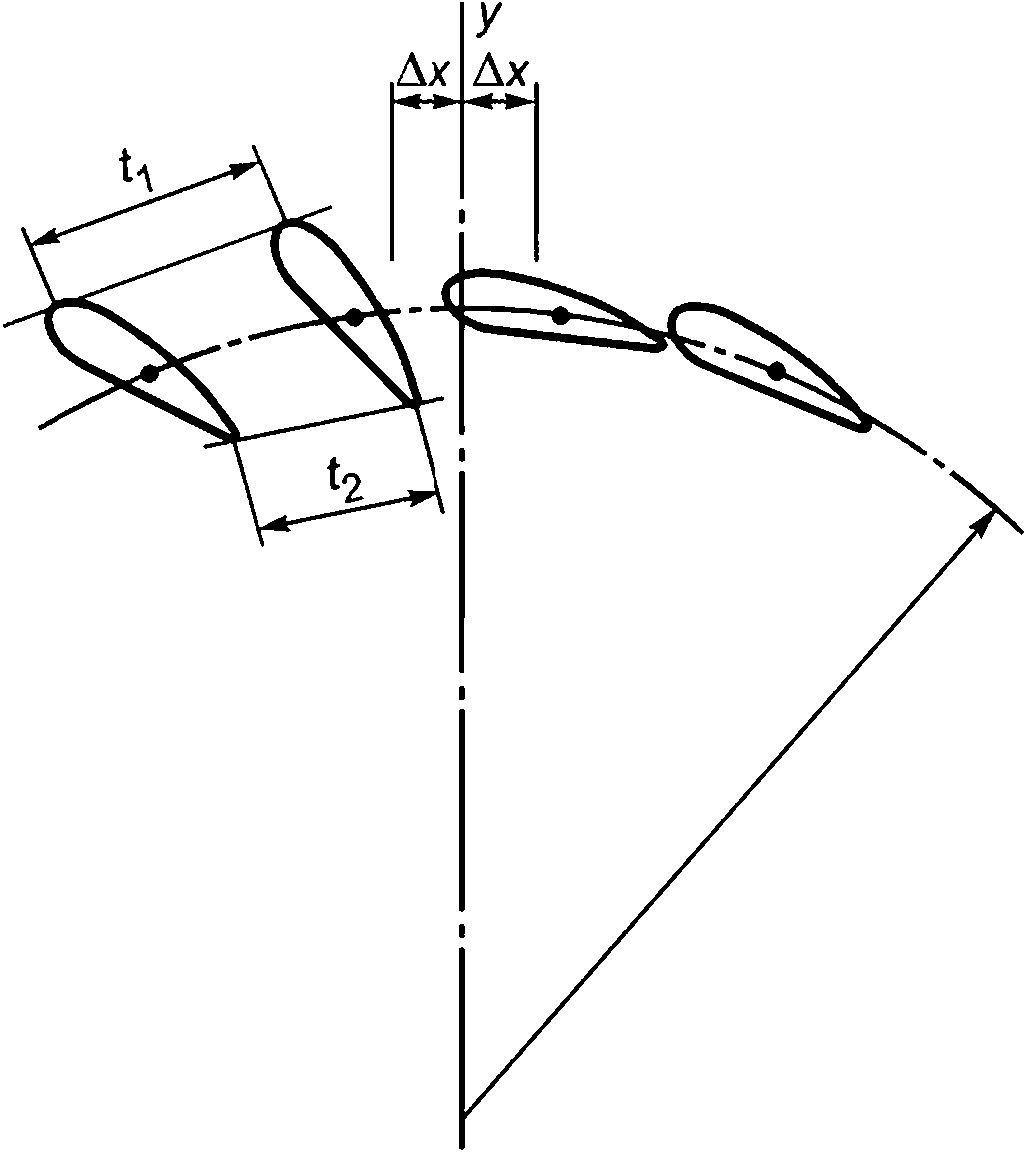
Обозначения | Размер по чертежу № | Фактический размер | Фактическое отклонение | Допустимое отклонение по чертежу или НТД |
Ьп | ||||
Ах | ||||
△у |
Обозначения | Размеры между лопатками направляющего аппарата, номер | |||||||||||||
1—2 | 2—3 | 3—4 | 4—5 | 5—6 | 6—7 | 20—21 | 21—22 | 22—23 | 23—24 | 24—1 | Допустимое отклонение по чертежу или НТД | |||
f1 | По чертежу № | |||||||||||||
Фактическое | ||||||||||||||
△^ | Фактическое отклонение | |||||||||||||
f2 | По чертежу № | |||||||||||||
Фактическое | ||||||||||||||
Ы2 | Фактическое отклонение |
Рисунок Б.6.1 — Проверка равномерности лопаток НА
Б.7 Отсасывающая труба
Б.7.1 В основе контроля отсасывающей трубы лежат измерения размеров, определяющих геометрическую форму и основные сечения трубы.
Б.7.2 Измерению подлежат (см. рисунок Б.7.1):
- размеры а, б, в, г, д, I, h v\ др., определяющие геометрическую форму трубы;
- в отсасывающих трубах с промежуточными бычками размеры геометрического положения бычков относительно стенок и проверяются радиусы округления этих бычков шаблоном, изготовленным по чертежам;
- радиальные размеры /?1 и R2, определяющие нецилиндричность по осям х, ху, у, ух, а также радиусы колена отсасывающей трубы при переходе в горизонтальную часть.
Б.7.3 Допуски на измерения представлены в таблице Б.7.1.
Таблица Б.7.1 — Допуски на монтаж отсасывающей трубы
Характер отклонения | Отклонение, мм, для диаметра РК, м | |||||
ДО 2,0 | от 2,0 до 3,0 | от 3,0 до 5,0 | от 5,0 до 7,5 | от 7,5 до 9,5 | от 9,5 до 10,5 | |
Отклонение высотных размеров | 8 | 10 | 15 | 20 | 25 | 25 |
Нецилиндричность | 5 | 6 | 10 | 15 | 20 | 25 |
Отклонение от геометрической формы (размеры а, б, в, г, д, 1) | Не более 0,1 проектного размера |
Примечание — Допустимые неровности в бетоне должны быть не более 0,5 % D1.
102
ГОСТ Р 55260.3.2—2023

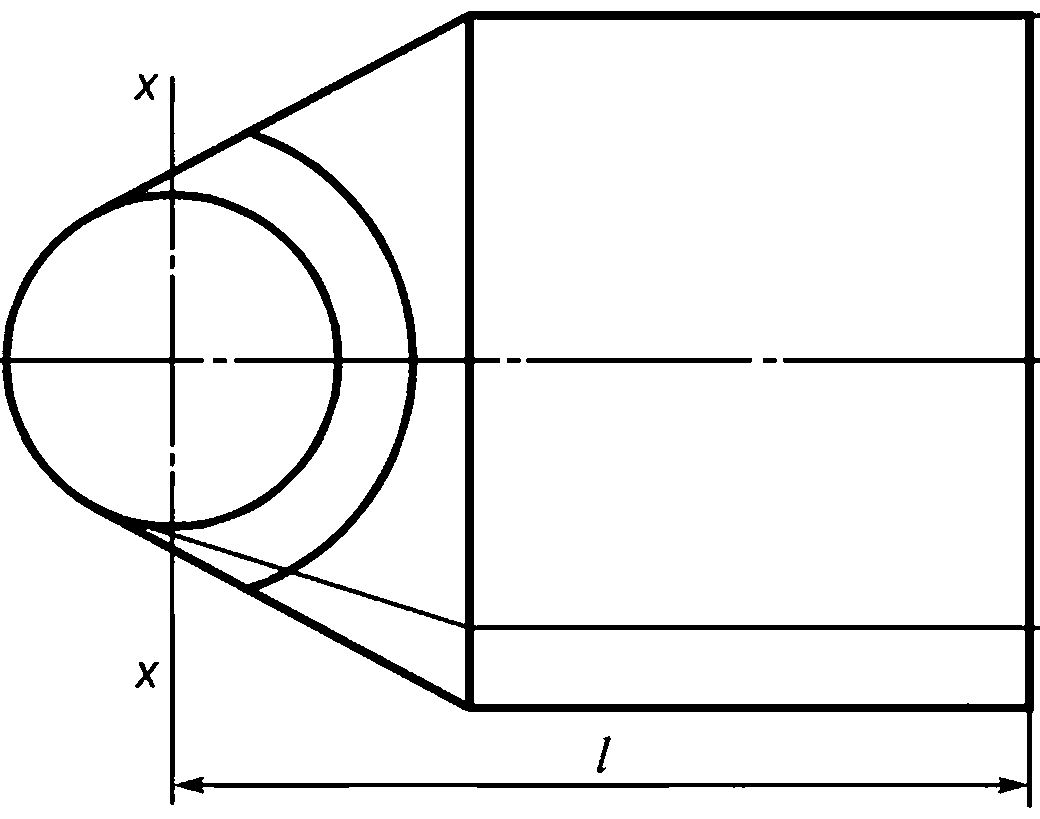
Обозначения | Размер по чертежу № | Фактический размер | Фактическое отклонение | Допустимое отклонение по чертежу или НТД |
а | ||||
б | ||||
в | ||||
г | ||||
О | ||||
1 | ||||
h |
Обозначения | Размер по чертежу № | Фактические размеры по осям | Факти-ческое максимальное отклонение | Допустимое отклонение по чертежу или НТД | |||||||
+У | +у+х | +х | +х-у | -у | -у-х | -х | -х+у | ||||
Рисунок Б.7.1 — Контроль геометрии отсасывающей трубы
Б.8 Закладные части гидротурбины
На обработанных поверхностях закладных частей гидротурбин, подверженных воздействию потока воды, резкие уступы в местах соединений не допускаются. Уступы на необработанных поверхностях должны быть сглажены путем их подрубки, шлифовки или опиловки. Величина сглаженных уступов не должна превышать 5 мм при диаметре РК до 5 м и 8 мм при диаметре РК до 10,5 м. В металлических облицовках указанные уступы не должны превышать 15 % толщины листа.
103
ГОСТ Р 55260.3.2—2023
Приложение В (обязательное)
Методики контроля состояния металла узлов и элементов гидротурбин и механической части генератора
В.1 Общие положения
В.1.1 Визуальный осмотр узлов и элементов гидротурбин и механической части генератора проводится при периодических осмотрах оборудования (см. таблицу 4.1) в периоды плановых и внеплановых ремонтов на выведенном из работы ГА. Осмотр не требует применения аппаратуры и аттестации специалистов.
Осмотр РК, КРК, проточной части, крышки турбины со стороны проточной части требует осушения агрегата. В исключительных случаях (авария, невозможность осушения) допускается осмотр с помощью специальных автономных средств без осушения проточного тракта.
Целью осмотра является обнаружение явных, обнаруживаемых визуально дефектов состояния металла узлов и элементов гидротурбин и механической части генератора: протяженных трещин, значительных кавитационных разрушений, существенного изменения геометрии конструкции и т. д.
В случае обнаружения при осмотрах повреждений необходимо провести восстановительный ремонт или привлечь специализированную организацию для проведения технического обследования с целью принятия решения о возможности дальнейшей эксплуатации.
В.1.2 Контроль состояния металла узлов и элементов гидротурбин и механической части генератора неразрушающими и разрушающими методами в процессе эксплуатации проводится на остановленном ГА при периодическом техническом диагностировании в форме технического обследования или технического освидетельствования.
В.1.3 Контроль состояния металла узлов и элементов гидротурбин и механической части генератора неразрушающими и разрушающими методами проводится по индивидуальной программе, разработанной на основе типовой программы и утвержденной техническим руководителем ГЭС (далее — программа). Индивидуальная программа учитывает конструктивно-технологические и эксплуатационные особенности оборудования, а также ранее проведенные ремонтные работы.
Объем, методы и зоны контроля состояния металла узлов и элементов гидротурбин и механической части генератора могут изменяться в зависимости от формы контроля технического состояния и поставленных задач, в том числе:
- выявление и фиксация эксплуатационных дефектов;
- получение фактических значений параметров функциональных узлов для дальнейшей оценки ИТС в соответствии с [1];
- углубленная оценка фактического технического состояния для определения сроков и объемов необходимого восстановительного ремонта, продления ресурса (срока службы) ГА, обоснования необходимости замены исчерпавших ресурс узлов, проведения реконструкции, модернизации и т. п.).
Основанием для выбора объемов и методов контроля металла узлов и элементов гидротурбин и механической части генератора являются:
- анализ сведений, содержащихся в проектной документации;
- анализ эксплуатационной документации за весь период эксплуатации;
- анализ ремонтной документации за весь период эксплуатации;
- текущее техническое состояние конструкций;
- статистика отказов, повреждений и выявленных дефектов оборудования на данном агрегате и на конструктивно аналогичных узлах других агрегатов при схожих эксплуатационных условиях;
- результаты предыдущих периодических осмотров и контроля, технических обследований и освидетельствований.
К разработке программы целесообразно привлекать специализированные организации, имеющие опыт работы в данной области и владеющие методиками оценки развития дефектов.
Типовые программы контроля состояния металла рабочих колес и камер рабочих колес ПЛ-гидротурбин приведены в В.4 и В.5.
В.1.4 Применяемые методы и объемы контроля должны гарантировать выявление недопустимых дефектов и отклонений в металле и сварных соединениях контролируемого оборудования, в том числе кавитационного, эрозионного, коррозионного, абразивного и усталостного характера, для обеспечения его последующей безопасной и надежной эксплуатации.
Особенности применения различных неразрушающих методов контроля в приложении к контролю состояния металла элементов и узлов гидротурбин и механической части генератора приведены в В.2. При необходимости могут быть использованы иные методы контроля, если они предусмотрены программой.
104
ГОСТ Р 55260.3.2—2023
Разрушающий контроль предусматривает вырезку образцов и последующие лабораторные испытания по определению фактических механических характеристик материала. Основные требования к вырезке образцов и лабораторным испытаниям представлены в В.З.
В.1.5 Неразрушающий контроль оборудования осуществляется:
- лабораторией неразрушающего контроля, аттестованной в установленном порядке в соответствии с [13];
- по наряду-допуску персоналом лаборатории неразрушающего контроля, прошедшим обучение, аттестованным в соответствии с [14] и ГОСТ Р ИСО 9712;
- с использованием аппаратуры, средств контроля, контрольно-измерительного инструмента и стандартных образцов, имеющих технический паспорт и прошедших метрологическую государственную поверку, калибровку или аттестацию в соответствии с установленным порядком;
- с использованием материалов для дефектоскопии (порошки, суспензии, пленка, химические реактивы и пр.), имеющих сертификаты качества, прошедших входной контроль и контроль в процессе эксплуатации в соответствии с установленным порядком.
В.1.6 Разрушающий контроль проводится испытательной лабораторией (испытательным центром), аккредитованной в установленном порядке на соответствующие виды испытаний.
В.1.7 Организация и подготовка оборудования к контролю (вывод из эксплуатации, разборка, устройство лесов, подмостков и ограждений для безопасного проведения работ, освещение и зачистка мест контроля и т. п.) возлагаются на техническое руководство ГЭС.
В.1.8 Технические службы ГЭС должны предоставить на контролируемое оборудование всю необходимую техническую документацию:
- паспорт, исполнительные схемы, сварочные формуляры, чертежи, эскизы;
- сертификаты на основные и сварочные материалы;
- документы о согласовании отступлений от чертежей при сборке и монтаже;
- сведения о наработке и режимах эксплуатации ГА, информацию о количестве пусков/остановов и сбросов нагрузок гидротурбины, продолжительности работы на переходных режимах;
- журнал технического обслуживания;
- сведения о повреждениях, отказах, авариях и проведенных заменах элементов в составе контролируемого оборудования;
- результаты предшествующего контроля;
- информацию о проведенных ремонтах и результатах послеремонтного контроля металла, примененных технологиях ремонта, сварочных, наплавочных материалах и т. п.;
- информацию о принятых технических решениях по устранению дефектов, препятствующих дальнейшей эксплуатации оборудования.
Информация предоставляется за весь период эксплуатации ГА. При отсутствии необходимой документации за весь срок эксплуатации допускается проводить анализ документации для составления программы контроля на основании данных о последнем КР турбины и за последний межремонтный период, но не менее 5 лет.
В.1.9 Если иное не указано в технической документации на ГА, первый контроль металла узлов и элементов гидротурбин и механической части генератора следует выполнить не позднее чем через 8000 ч после начала эксплуатации. Если дефекты не будут обнаружены, то последующие контрольные проверки следует выполнять во время КР гидротурбины не позднее чем через 5—7 лет работы гидротурбины. При необходимости по решению технического руководителя ГЭС периодичность проведения контроля может быть сокращена.
В.1.10 В случае обнаружения по результатам неразрушающего контроля недопустимых дефектов элементов и узлов гидротурбин и механической части генератора необходимо провести восстановительный ремонт или принять техническое решение о возможности, сроках и условиях дальнейшей эксплуатации.
В.2 Контроль состояния металла узлов и элементов гидротурбин и механической части генератора неразрушающими методами
В.2.1 Визуально-измерительный контроль
В.2.1.1 Общие положения
ВИК основного металла и сварных соединений элементов и узлов гидротурбин и механической части генератора выполняют до проведения контроля другими методами.
Контролю подлежат следующие элементы и узлы гидротурбин и механической части генератора:
- рабочее колесо;
- маслоприемник РК гидротурбины ПЛ-типа;
- НА с сервомоторами;
- крышка турбины;
- проточная часть гидротурбины;
- система автоматического управления;
- подшипник направляющий турбинный;
- вал (вал турбины, вал генератора, вал-надставка, остов ротора генератора);
- подшипник опорный генераторный (подпятник) и опорный конус;
105
ГОСТ Р 55260.3.2—2023
- подшипник направляющий генераторный (верхний/нижний);
- крестовина ГА грузонесущая/негрузонесущая.
ВИК проводится в соответствии с ГОСТ Р ИСО 17637, ГОСТ ISO 17635.
В.2.1.2 Цель контроля
Визуальный контроль металла элементов и узлов гидротурбин и механической части генераторов выполняют с целью выявления поверхностных дефектов (трещин, подрезов, прожогов, наплывов, кратеров, свищей, пор, раковин, эрозионно-коррозионных, кавитационных повреждений и других несплошностей, дефектов формы швов) и деформаций.
Измерительный контроль выполняется на участках, проконтролированных визуально.
ВИК также используется для уточнения формы и размеров зазоров, деталей, узлов и элементов гидротурбин и контроля качества исправленных дефектных участков.
В.2.1.3 Нормы оценки качества
По результатам проведения ВИК к дальнейшей эксплуатации без проведения ремонтно-восстановительных работ или принятия технического решения по обоснованию возможности, сроков и условий дальнейшей эксплуатации не допускаются элементы и узлы гидротурбин и механической части генераторов, имеющие следующие дефекты:
- трещины всех видов и всех направлений;
- одиночные механические поверхностные дефекты и включения с характерным размером более 2,5 мм;
- протяженные дефекты любой глубины;
- цепочки дефектов с расстоянием между дефектами менее 25 мм (кроме резьбовой части);
- непровары, наплывы, натеки, брызги металла, прожоги и иные дефекты сварных швов и ремонтных заварок;
- неустраненные эрозионно-коррозионные, кавитационные повреждения и деформации, при которых геометрические размеры контролируемой детали не соответствуют требованиям конструкторской документации или требованиям НТД.
В.2.1.4 Карта контроля
Перед началом проведения контроля необходимо составить карту контроля с указанием:
- наименования объекта контроля;
- перечня необходимых подготовительных и заключительных операций;
- объемов и зон контроля;
- используемых средств контроля;
- НТД по проведению контроля и оценке качества.
В.2.1.5 Периодичность контроля
Периодичность контроля определяется графиками ремонтов в соответствии с ремонтной документацией, но не реже, чем 1 раз в 5—7 лет, если иное не установлено по результатам ранее проведенного технического обследования или технического освидетельствования оборудования.
В.2.1.6 Оформление результатов контроля
По результатам контроля составляется заключение, в котором должно быть указано:
- наименование контролируемого изделия;
- дата проведения контроля;
- карта контроля;
- перечень использованных инструментов с указанием номеров и даты поверки;
- результаты контроля с перечнем обнаруженных дефектов и отклонений с указанием их местоположения и характерных размеров; наиболее характерные или значительные повреждения регистрируются фотографированием с приложением масштабной линейки;
- оценка качества «годен — не годен».
Заключение подписывают начальник лаборатории и проводивший контроль специалист с указанием номера удостоверения и срока действия.
Заключение по результатам контроля регистрируется в журнале учета.
В.2.2 Контроль проникающими веществами
В.2.2.1 Общие положения
ПВК основного металла и сварных соединений узлов гидротурбин и механической части генератора выполняют во время ремонтов после проведения ВИК в соответствии с ГОСТ 18442, ГОСТ ISO 17635 и основными положениями [15].
Объем контроля определяется индивидуальной программой (см. В.1.3) и может быть откорректирован в соответствии с результатами ВИК. Методика ПВК и чувствительность контроля должны соответствовать параметрам, предписанным программой контроля и картой контроля, но быть не ниже второго класса чувствительности.
Если это предусмотрено программой, ПВК может быть заменен МПД или ВТК.
В.2.2.2 Цель контроля
По результатам ПВК выявляют поверхностные трещиноподобные и округлые дефекты, в том числе не выявленные по результатам ВИК.
106
ГОСТ Р 55260.3.2—2023
В.2.2.3 Нормы оценки качества
По результатам проведения ПВК к дальнейшей эксплуатации без проведения ремонтно-восстановительных работ или дополнительного контроля не допускаются элементы и узлы гидротурбин и механической части генератора со следующими обнаруженными дефектами:
- удлиненными индикаторными следами;
- округлыми индикаторными следами с характерным размером более 5 мм;
- при наличии более четырех округлых индикаторных следов, расположенных в линию.
Индикаторным следом округлой формы следует считать рисунок, у которого отношение наибольшего размера проявляющегося следа к его наименьшему размеру меньше или равен трем. В противном случае индикаторный след является удлиненным.
В.2.2.4 Карта контроля
Перед началом проведения контроля необходимо составить карту контроля с указанием:
- наименования объекта контроля;
- перечня необходимых подготовительных и заключительных операций;
- шероховатости поверхности;
- объемов и зон контроля (схем проведения контроля);
- конкретных методов контроля;
- класса чувствительности;
- дефектоскопического набора;
- НТД по проведению контроля и оценке качества.
В.2.2.5 Периодичность контроля
Периодичность контроля определяется графиками ремонтов в соответствии с ремонтной документацией, но не реже, чем 1 раз в 5—7 лет, если иное не установлено по результатам ранее проведенного технического обследования или технического освидетельствования оборудования.
В.2.2.6 Оформление результатов контроля
По результатам контроля составляется заключение, в котором должно быть указано:
- наименование объекта контроля;
- дата проведения контроля;
- карта контроля;
- технологии контроля (метод, набор дефектоскопических материалов, класс чувствительности);
- наименование и тип используемой рецептуры или комплекта реактивов ПВК;
- результаты контроля с перечнем обнаруженных дефектов, выявленных индикаторных следов с указанием их местоположения и характерных размеров; наиболее характерные или значительные повреждения регистрируются фотографированием с приложением масштабной линейки;
- оценка качества «годен — не годен».
Заключение подписывают начальник лаборатории и проводивший контроль специалист с указанием номера удостоверения и срока действия.
Заключение по результатам контроля регистрируется в журнале учета.
В.2.3 Вихретоковый контроль
В.2.3.1 Общие положения
ВТК основного металла, сварных соединений и ремонтных заварок узлов гидротурбин и механической части генератора выполняют во время ремонтов после проведения ВИК в соответствии с ГОСТ Р ИСО 15549, ГОСТ ISO 17635 и основными положениями [16].
Объем контроля определяется индивидуальной программой (см. В.1.3) и может быть откорректирован в соответствии с результатами ВИК. Методика ВТК и чувствительность контроля должны соответствовать параметрам, предписанным программой контроля и картой контроля.
ВТК допускается не проводить в случае положительных результатов ПВК, если это предусмотрено программой.
В.2.3.2 Цель контроля
По результатам ВТК выявляют поверхностные и подповерхностные дефекты и несплошности металла, в том числе не выявленные по результатам ВИК и ПВК.
В.2.3.3 Нормы оценки качества
По результатам проведения ВТК к дальнейшей эксплуатации без проведения ремонтно-восстановительных работ или дополнительного контроля допускаются элементы и узлы гидротурбин и механической части генератора, если не обнаружены дефекты, имеющие признаки трещины.
В.2.3.4 Карта контроля
Перед началом проведения контроля необходимо составить карту контроля с указанием:
- наименования объекта контроля;
- перечня необходимых подготовительных и заключительных операций;
- требований к контролируемой поверхности (шероховатость);
- объемов и зон контроля (схем проведения контроля);
107
ГОСТ Р 55260.3.2—2023
- перечня средств измерений (дефектоскопов, преобразователей), применяемых образцов, параметров настройки оборудования и шага сканирования;
- НТД по проведению контроля и оценке качества.
В.2.3.5 Периодичность контроля
Периодичность контроля определяется графиками ремонтов в соответствии с ремонтной документацией, но не реже, чем 1 раз в 5—7 лет, если иное не установлено по результатам ранее проведенного технического обследования или технического освидетельствования оборудования.
В.2.3.6 Оформление результатов контроля
По результатам контроля составляется заключение, в котором должно быть указано:
- наименование объекта контроля;
- дата проведения контроля;
- карта контроля;
- тип и заводской номер дефектоскопа;
- тип и заводской номер преобразователя;
- наименование и номер образца, по которому производилась настройка пороговой чувствительности дефектоскопа;
- тип контролируемой поверхности с указанием шероховатости, наличия (толщины) неэлектропроводящих покрытий или их отсутствия;
- результаты контроля с перечнем обнаруженных дефектов с указанием их местоположения и характерных размеров;
- оценка качества «годен — не годен».
Заключение подписывают начальник лаборатории и проводивший контроль специалист с указанием уровня квалификации, номера удостоверения и срока действия.
Заключение по результатам контроля регистрируется в журнале учета.
В.2.4 Ультразвуковой контроль
В.2.4.1 Общие положения
УЗК основного металла, сварных соединений и ремонтных заварок узлов гидротурбин и механической части генератора выполняют во время ремонтов после проведения ВИК в соответствии с ГОСТ Р 55724, ГОСТ Р 55809, ГОСТ ISO 17635, ГОСТ Р ИСО 17640.
Объем контроля определяется индивидуальной программой (см. В.1.3) и может быть откорректирован в соответствии с результатами ВИК и других методов контроля.
Методика УЗК и чувствительность контроля должны соответствовать параметрам, предписанным программой контроля и картой контроля.
В.2.4.2 Цель контроля
Выявить внутренние дефекты, несплошности металла и трещины в резьбовой части крепежных элементов, не доступные для идентификации при проведении других видов контроля.
В.2.4.3 Нормы оценки качества
Результаты контроля состояния основного металла, сварных швов и ремонтных заварок по результатам проведения УЗК считаются удовлетворительными, если:
- не выявлено протяженных несплошностей;
- выявленные непротяженные несплошности являются одиночными;
- минимально фиксируемая эквивалентная площадь выявленного дефекта не превышает 3 мм2 (дефекты меньше 3 мм2 не фиксируют в документации, настройка аппаратуры проведена на дефект размером 3 мм2);
- максимальная эквивалентная площадь выявленного дефекта не превышает 10 мм2;
- максимально фиксируемое количество одиночных несплошностей на длине 100 мм не превышает 10 штук.
В.2.4.4 Карта контроля
Перед началом проведения контроля необходимо составить карту контроля с указанием:
- наименования объекта контроля;
- перечня необходимых подготовительных и заключительных операций;
- требований к контролируемой поверхности (зона зачистки, шероховатость);
- объемов и зон контроля (схем проведения контроля);
- перечня средств измерений (дефектоскопов, преобразователей), применяемых СО и СОП;
- параметров настройки оборудования, чувствительности, шага сканирования, контактной жидкости и т. п.;
- НТД по проведению контроля и оценке качества.
В.2.4.5 Периодичность контроля
Периодичность контроля определяется графиками ремонтов в соответствии с ремонтной документацией, но не реже, чем 1 раз в 5—7 лет, если иное не установлено по результатам ранее проведенного технического обследования или технического освидетельствования оборудования.
В.2.4.6 Оформление результатов контроля
По результатам контроля составляется заключение, в котором должны быть указаны:
- наименование объекта контроля, тип сварного соединения (вид ремонтной заварки);
108
ГОСТ Р 55260.3.2—2023
- дата проведения контроля;
- карта контроля (схемы контроля);
- тип и заводской номер дефектоскопа;
- тип и заводской номер преобразователя;
- рабочая частота;
- инвентарный номер СОП;
- угол ввода ультразвукового луча;
- предельная чувствительность;
- результаты контроля с перечнем обнаруженных дефектов с указанием их местоположения и характерных размеров;
- оценка качества «годен — не годен».
Заключение подписывают начальник лаборатории и проводивший контроль специалист с указанием уровня квалификации, номера удостоверения и срока действия.
Заключение по результатам контроля регистрируется в журнале учета.
В.2.5 Ультразвуковая толщинометрия
В.2.5.1 Общие положения
УЗТ основного металла узлов гидротурбин и механической части генератора выполняют во время ремонтов в соответствии с ГОСТ Р 55614, ГОСТ Р 55809, ГОСТ Р ИСО 16809.
Объем контроля определяется индивидуальной программой (см. В.1.3) и может быть откорректирован в соответствии с результатами ВИК и других видов контроля.
В.2.5.2 Цель контроля
Определить толщину основного металла и зоны возможного расслоения основного металла.
В.2.5.3 Нормы оценки качества
Замеренные величины толщин должны соответствовать требованиям конструкторской документации.
В.2.5.4 Карта контроля
Перед началом проведения контроля необходимо составить карту контроля с указанием:
- наименования объекта контроля;
- перечня необходимых подготовительных и заключительных операций;
- требований к контролируемой поверхности (зона зачистки, шероховатость);
- объемов и зон контроля (схем проведения контроля);
- перечня средств измерений, применяемых СО и СОП;
- параметров настройки оборудования;
- НТД по проведению контроля и оценке качества.
В.2.5.5 Периодичность контроля
Контроль проводится в случае необходимости, например при подозрении на несоответствие фактических толщин проектным параметрам.
В.2.5.6 Оформление результатов контроля
По результатам контроля составляется заключение, в котором должны быть указаны:
- наименование объекта контроля;
- дата проведения контроля;
- карта контроля (схемы контроля);
- тип толщиномера;
- рабочая частота;
- инвентарный номер СОП;
- результаты контроля с указанием соответствия/несоответствия нормативным значениям толщин, указанным в конструкторской или иной технической документации.
Заключение подписывают начальник лаборатории и проводивший контроль специалист с указанием уровня квалификации, номера удостоверения и срока действия.
Заключение по результатам контроля регистрируется в журнале учета.
В.2.6 Магнитопорошковая дефектоскопия
В.2.6.1 Общие положения
МПД основного металла, сварных соединений и ремонтных заварок узлов гидротурбин и механической части генератора выполняют во время ремонтов после проведения ВИК в соответствии с ГОСТ Р 56512, ГОСТ Р ИСО 9934-1, ГОСТ Р ИСО 9934-2, ГОСТ Р 53700, ГОСТ ISO 17638, ГОСТ ISO 17635 и основными положениями [17].
Объем контроля определяется индивидуальной программой (см. В.1.3) и может быть откорректирован в соответствии с результатами ВИК. Методика МПД и чувствительность контроля должны соответствовать параметрам, предписанным программой контроля и картой контроля.
Для обнаружения поверхностных дефектов МПД и ПВК являются взаимозаменяемыми методами контроля. Выбор метода контроля зависит от условий проведения контроля (магнитные свойства контролируемого металла, подготовка поверхности, температура и влажность окружающего воздуха).
109
ГОСТ Р 55260.3.2—2023
В.2.6.2 Цель контроля
По результатам МПД выявляют поверхностные дефекты металла, в том числе не выявленные по результатам ВИК.
В.2.6.3 Нормы оценки качества
Нормы оценки качества при проведении МПД соответствуют нормам оценки качества при проведении ПВК (см. В.2.2.3).
В.2.6.4 Карта контроля
Перед началом проведения контроля необходимо составить карту контроля с указанием:
- наименования объекта контроля;
- перечня необходимых подготовительных и заключительных операций;
- требований к контролируемой поверхности (шероховатость);
- объемов и зон контроля (схем проведения контроля);
- способа контроля;
- перечня средств измерений и параметров настройки оборудования;
- схемы намагничивания;
- напряженности приложенного поля;
- НТД по проведению контроля и оценке качества.
В.2.6.5 Периодичность контроля
Периодичность контроля определяется графиками ремонтов в соответствии с ремонтной документацией, но не реже, чем 1 раз в 5—7 лет, если иное не установлено по результатам ранее проведенного технического обследования или технического освидетельствования оборудования.
В.2.6.6 Оформление результатов контроля
По результатам контроля составляется протокол, в котором должны быть указаны:
- наименование объекта контроля;
- дата проведения контроля;
- карта контроля;
- тип и заводской номер дефектоскопа;
- магнитный индикатор;
- способ контроля;
- схема намагничивания;
- напряженность приложенного поля;
- схема дефектных участков с их координатами;
- результаты контроля с перечнем обнаруженных дефектов с указанием их местоположения и характерных размеров;
- оценка качества «годен — не годен».
Протокол подписывают начальник лаборатории и проводивший контроль специалист, с указанием уровня квалификации, номера удостоверения и срока действия.
Протокол по результатам контроля регистрируется в журнале учета.
В.2.7 Измерение твердости
В.2.7.1 Общие положения
ТВ основного металла, сварных соединений и ремонтных заварок узлов гидротурбин и механической части генератора выполняют во время ремонтов после проведения ВИК. Рекомендуется проводить измерение твердости по Бринеллю в соответствии с ГОСТ 22761, ГОСТ 9012, ГОСТ 8.398 и руководством по эксплуатации прибора.
Объем контроля определяется индивидуальной программой (см. В.1.3) и может быть откорректирован в соответствии с результатами других видов неразрушающего контроля.
В.2.7.2 Цель контроля
Контроль проводится для определения качества сварных соединений, основного металла и наплавок.
В.2.7.3 Нормы оценки качества
Результаты замеров твердости основного металла, сварных соединений и ремонтных заварок должны соответствовать требованиям конструкторской документации, а также нормативным документам, регламентирующим твердость испытуемых материалов.
В.2.7.4 Карта контроля
Перед началом проведения контроля необходимо составить карту контроля с указанием:
- наименования объекта контроля;
- перечня необходимых подготовительных и заключительных операций;
- требований к контролируемой поверхности (шероховатость);
- объемов и зон контроля (схем проведения контроля);
- метода измерения твердости;
- перечня средств измерений (твердомеров) и используемых мер твердости;
- НТД по проведению контроля и оценке качества.
110
ГОСТ Р 55260.3.2—2023
В.2.7.5 Периодичность контроля
Периодичность контроля определяется графиками ремонтов в соответствии с ремонтной документацией, но не реже, чем 1 раз в 5—7 лет, если иное не установлено по результатам ранее проведенного технического обследования или технического освидетельствования оборудования.
В.2.7.6 Оформление результатов контроля
По результатам контроля составляется протокол, в котором должно быть указано:
- наименование объекта контроля;
- дата проведения контроля;
- карта контроля;
- тип прибора и дата поверки;
- метод контроля твердости;
- результаты контроля (среднее значение и разброс по каждой из подготовленных площадок);
- оценка качества — соответствие/несоответствие измеренных значений нормативным значениям, указанным в конструкторской или иной технической документации.
Протокол подписывают начальник лаборатории и проводивший контроль специалист, с указанием уровня квалификации, номера удостоверения и срока действия.
Протокол по результатам контроля регистрируется в журнале учета.
В.З Контроль состояния металла узлов и элементов гидротурбин и механической части генератора разрушающими методами
В.3.1 Специальные обследования с использованием образцов металла проводятся для определения фактических механических характеристик сталей с целью решения вопросов об оценке работоспособности и продлении ресурса гидротурбин и механической части генератора.
В.3.2 Объем разрушающих испытаний определяется программой (см. В.1) и зависит от фактического состояния оборудования и технической возможности вырезки заготовок для образцов и последующего восстановления формы и размеров деталей.
В.3.3 Образцы для испытаний вырезают непосредственно из контролируемого элемента конструкции. Вырезку заготовок для образцов рекомендуется выполнять на металлорежущих станках. Допускается вырезать заготовки кислородной, плазменной, анодно-механической и другими методами резки. При кислородной вырезке заготовок их размеры определяют с учетом припуска на последующую механическую обработку, обеспечивающую отсутствие металла, подвергшегося термическому влиянию при резке в рабочей части образцов.
Размер и количество заготовок образцов определяют исходя из основных положений по проведению соответствующего вида лабораторных испытаний.
В.3.4 Определению подлежат следующие механические характеристики:
- условный предел текучести, временное сопротивление (предел прочности), относительное удлинение и относительное сужение после разрыва по результатам испытаний на растяжение по проекту ГОСТ 1497;
- характеристики сопротивления усталости (кривая усталости, диаграмма предельных напряжений и т. п.) по результатам испытаний на усталость по ГОСТ 25.502;
- скорость роста трещин и характеристики трещиностойкости материала (параметры кинетической диаграммы усталостного разрушения, пороговые и критические значения коэффициента интенсивности напряжений) по результатам испытаний на циклическую трещиностойкость по ГОСТ 25.506.
В.3.5 Если нет других указаний, то испытания проводят не менее, чем на трех образцах. Результаты по всем видам испытаний определяют, как среднее арифметическое результатов, полученных при испытании всех образцов.
В.3.6 Протокол испытаний должен содержать:
- марку металла;
- вид термической обработки (если она выполнялась);
- индекс образца (по клейму);
- тип образца и место его отбора;
- объем испытаний;
- результаты испытаний всех образцов с указанием наличия дефектов в изломе образца.
В.4 Типовая программа контроля состояния металла рабочих колес
В.4.1 Общие положения
РК гидротурбин подвергаются контролю состояния основного и наплавленного металла для выявления повреждений и дефектов, оказывающих влияние на эксплуатационную надежность РК.
Программа контроля состояния металла РК предусматривает применение неразрушающих методов контроля, а также, при необходимости, проведение специальных обследований с использованием образцов металла (разрушающих методов контроля).
ВИК проводится в соответствии с В.2.1 и нормативными документами, регламентирующими данный вид неразрушающего контроля.
111
ГОСТ Р 55260.3.2—2023
ПВК проводится в соответствии с В.2.2 и нормативными документами, регламентирующими данный вид неразрушающего контроля.
ВТК проводится в соответствии с В.2.3, нормативными документами, регламентирующими данный вид неразрушающего контроля, и руководством по эксплуатации приборов.
УЗК проводится в соответствии с В.2.4, нормативными документами, регламентирующими данный вид неразрушающего контроля, и руководством по эксплуатации приборов.
УЗТ проводится в соответствии с В.2.5, нормативными документами, регламентирующими данный вид неразрушающего контроля, и руководством по эксплуатации приборов.
МИД проводится в соответствии с В.2.6, нормативными документами, регламентирующими данный вид неразрушающего контроля, и руководством по эксплуатации приборов.
ТВ проводится в соответствии с В.2.7, нормативными документами, регламентирующими данный вид неразрушающего контроля, и руководством по эксплуатации приборов.
При необходимости уточнения характеристик материала проводят лабораторные испытания с использованием вырезанных образцов металла в соответствии с В.З.
В.4.2 Перечень контролируемых элементов
Контролю подлежат:
а) поворотно-лопастные, пропеллерные и диагональные гидротурбины:
- лопасти РК;
- корпус РК;
- конус обтекателя;
- механизм разворота лопастей (для ПЛ-гидротурбин в случае разборки РК в объеме КР);
- крепежные элементы;
б) радиально-осевые гидротурбины:
- лопасти РК;
- обод РК;
- ступица РК;
- лабиринтные уплотнения.
В.4.3 Характерные дефекты и повреждения
В.4.3.1 Наиболее опасными дефектами и повреждениями, которые оказывают решающее влияние на эксплуатационную надежность РК и, в случае несвоевременного выявления, приводят к значительному увеличению времени, объемов и стоимости необходимого восстановительного ремонта, являются следующие:
- отрыв лопасти РК;
- образование протяженной трещины с дальнейшим обрывом куска металла лопасти РК;
- изменение, относительно проектных, геометрических характеристик РК, в том числе зазоров «камера — лопасть» и зазоров в лабиринтных уплотнениях, в процессе эксплуатации или в результате выполненных ремонтных работ с возможным задеванием лопастей РК о металл неподвижных частей гидротурбины с возможным отрывом лопасти РК;
- глубокие кавитационные повреждения (вплоть до сквозных отверстий);
- разрушение крепежных элементов РК;
- изменение физико-механических свойств металла, связанных с проведением ремонтно-восстановительных работ (сварка, наплавка, термическая обработка) и деградацией свойств материала при длительной эксплуатации в коррозионно-опасной среде (развитие усталостных явлений в металле лопастей, изменение предела коррозионно-усталостной прочности, твердости и т. п.).
В.4.3.2 Наличие трещин и механических повреждений определяется с помощью осмотра и контроля неразрушающими методами в соответствии с В.1—В.2.
Характерные зоны трещинообразования в лопастной системе РК:
- зоны приварки лопасти и околошовная зона у ступицы и обода со стороны входной и выходной кромок для РО рабочих колес;
- в корневом сечении (место сопряжения фланца с пером лопасти ПЛ-турбины), в зоне пересечения периферийного сечения и выходной кромки, в зоне отверстий под болты крепления лопасти к фланцу и в зоне монтажных отверстий для ПЛ рабочих колес.
В.4.3.3 Опасность трещин с точки зрения возможности отрыва куска лопасти определяется на основании оценки усталостной прочности и трещиностойкости лопасти с учетом фактических данных о механических характеристиках металла, полученных в соответствии с В.З.
Оценка усталостной прочности и трещиностойкости проводится расчетными методами путем моделирования процесса накопления усталостных повреждений вплоть до зарождения усталостной трещины и процесса развития трещины до образования магистральной трещины при достижении критического значения величины коэффициента интенсивности напряжений.
Расчеты на усталостную прочность лопастей гидротурбин при номинальном режиме работы ГА регламентируются нормативными документами [18], [19].
112
ГОСТ Р 55260.3.2—2023
Оценку усталостной прочности и трещиностойкости следует проводить с учетом фактических режимов эксплуатации, учитывая фактические наработки в каждом эксплуатационном диапазоне (малая/средняя/большая/ номинальная мощность, XX, работа в режиме СК и т. п.), количество пусков-остановов ГА, время в простоях и ремонтах.
В.4.3.4 Возможность задевания лопастей РК о металл неподвижных частей гидротурбины оценивается на основании фактических данных по размерам и форме зазоров: зазор «камера — лопасть» для ПЛ-турбин и зазор в лабиринтных уплотнениях для РО-турбин.
Величины фактических зазоров определяются в соответствии с методиками, представленными в Б.2, Б.З, Б.4. Допустимые отклонения зазоров от проектных значений представлены в таблицах 6.1 и 6.3.
В.4.3.5 Унос металла от кавитационной эрозии оценивается по величине весовой потери металла, кг, из РК и элементов проточной части за определенное число часов работы в соответствии с гарантиями завода — изготовителя гидротурбин.
В случае отсутствия заводских гарантий по потере металла при кавитационном износе допустимый объем этих потерь должен быть определен в соответствии с ГОСТ Р 55562.
В.4.4 Типовой объем контроля
В.4.4.1 Типовая программа контроля металла РК гидротурбин предусматривает три этапа контроля: первичный визуальный осмотр, уточненный обязательный контроль и дополнительный контроль. Объемы и методы контроля для каждого этапа отражаются в карте зон проведения контроля.
В.4.4.2 Первичный визуальный осмотр проводится с целью уточнения зон проведения контроля, объемов и методов, используемых при уточненном контроле. Первичному визуальному контролю подвергается вся доступная поверхность РК, а именно:
а) для ПЛ-, ПР- и диагональных гидротурбин: лопасти, корпус, конус обтекателя, механизм разворота лопастей (за исключением ПР-гидротурбин), болты крепления лопасти к фланцу (при демонтаже лопасти);
б) для РО-гидротурбин: лопасти, обод, ступица, лабиринтные уплотнения.
В.4.4.3 Уточненный обязательный контроль проводится в соответствии с картой контроля и схемой расположения зон контроля следующими методами и в следующих объемах:
- визуальный контроль поверхности РК— 100 % в доступных местах;
- контроль геометрических характеристик РК, УЗТ лопастей РК — выборочно (по необходимости), включая ИК: выходные кромки для РК РО-типа, выходные и периферийные кромки для РК ПЛ-типа;
- ПВК, МПД или ВТК поверхности лопастей РК:
а) 100 % в зоне галтельных переходов;
б) 100 % в зоне отверстий под болты крепления лопасти, монтажного отверстия и периферийной кромки (для ПЛ-турбин);
в) 30 % длины выходной кромки со стороны периферийной кромки (для ПЛ-турбин);
г) выборочно на поверхностях, наиболее подверженных разрушениям, в зонах повреждения облицовки лопастей и в подозрительных по результатам ВИК зонах;
- ПВК, МПД или ВТК сварных швов РК — выборочно на поверхностях, наиболее подверженных разрушениям, в объеме не менее 10 % протяженности швов;
- ПВК, МПД или ВТК ремонтных заварок РК — 100 %;
- УЗК лопастей РК — выборочно, в зонах ремонтных заварок;
- определение ТВ лопастей РК — выборочно, в зонах наибольших рабочих напряжений и ремонтных заварок;
- лабиринтные уплотнения рабочих колес РО-типа (в случае демонтажа РК): ВИК — 100 %; ПВК, МПД или ВТК — не менее 20 %;
- определение физико-механических и усталостных свойств металла лопастей РК — выборочно (по необходимости на вырезанных образцах);
- ВИК, ПВК, МПД, ВТК, УЗК крепежных элементов — в соответствии с требованиями стандарта организации (при наличии) каждой гидроэлектростанции.
В.4.4.4 Размеры и координаты зон контроля, а также объемы и методы контроля при уточненном обязательном контроле отражаются в карте контроля.
Карта контроля и схема расположения зон заполняются при разработке программы контроля и уточняются по результатам первичного визуального контроля.
В.4.4.5 По результатам первичного визуального контроля, уточненного обязательного контроля, а также с учетом анализа ремонтной и эксплуатационной документации при необходимости уточнения формы и размеров обнаруженных дефектов и повреждений или подтверждения отсутствия дефектов в карту контроля должны быть внесены дополнения, определяющие зоны, объем и методы дополнительного контроля.
В.4.4.6 Форма карты контроля РК ПЛ-гидротурбины представлена на рисунке В.4.1. Расположение зон контроля показано на рисунке В.4.2.
В.4.4.7 Форма карты контроля РК РО-гидротурбины представлена на рисунке В.4.3. Расположение зон контроля показано на рисунке В.4.4.
113
ГОСТ Р 55260.3.2—2023
Карта зон проведения контроля металла рабочего колеса ПЛ-гидротурбины________________ | ||||
Программа № / Шифр___________________ | ||||
Первичный визуальный контроль | ||||
Зона | Размер зоны (мм) или объем контроля | Методы контроля | Примечания | |
Лопасти РК | Рабочая поверхность(Лр) | Вся поверхность | ВИК | По результатам контроля уточняются и дополняются зоны для инструментального контроля, ПВК, МПД, ВТК, УЗК, УЗТ, ТВ |
Тыльная поверхность(Лт) | Вся поверхность | ВИК | ||
Корпус РК | Вся поверхность | ВИК | ||
Конус обтекателя РК | Вся поверхность | ВИК | ||
Механизм разворота лопастей (для ПЛ-гидротурбин при полной разборке РК) | Равномерность углов установки лопастей, наличие люфтов и провисания лопастей, комбинаторная зависимость, перестановочные усилия | Без разборки РК по косвенным признакам | ||
Вся поверхность (рычаги, серьги, цапфы) | ВИК | В случае полной разборки РК | ||
Заглушки болтов крепления лопастей | 100 % | ВИК | Проверка наличия заглушек | |
Уточненный обязательный контроль | ||||
А1р | 400x400 | ВИК, ПВК (или МПД, или ВТК), УЗК, ТВ | ||
А1т | 400x400 | ВИК, ПВК (или МПД, или ВТК), УЗК, ТВ | ||
А2р | 400x400 | ВИК, ПВК (или МПД, или ВТК), УЗК, ТВ | ||
А2т | 400x400 | ВИК, ПВК (или МПД, или ВТК), УЗК, ТВ | ||
АЗр | 300x500 | ВИК, ПВК (или МПД, или ВТК) | ||
АЗт | 300x500 | ВИК, ПВК (или МПД, или ВТК) | ||
А4р | 200xL | ВИК | ||
А4т | 200xL | ВИК | ||
Абр | 200xL | ВИК | ||
А5т | 200xL | ВИК | ||
Абр | 200xL | ВИК | ||
Абт | 200xL | ВИК | ||
А7р | Галтель | ВИК | ||
А7т | Галтель | ВИК | ||
Абр | 300x500 | ВИК | ||
Абт | 300x500 | ВИК | ||
Болты крепления лопастей | В соответствии с требованиями НТД | ВИК, ПВК, МПД, ВТК, УЗК |
Рисунок В.4.1 — Карта зон проведения контроля металла рабочего колеса ПЛ-гидротурбин (лист 1)
114
ГОСТ Р 55260.3.2—2023
Геометрические характеристики | Форма и размеры лопастей, симметричность их расположения, толщина периферийных кромок, размеры и равномерность зазора «камера-лопасть» | Инструментальный контроль, УЗТ | Соответствие проектной документации требованиям НТД | ||||
Физико-механические и усталостные свойства металла лопастей | Выборочно (по необходимости на вырезанных образцах) | Проведение испытаний в соответствии с В.22 | Необходимость вырезки образцов, а также схемы вырезки и объем контроля определяются индивидуальной программой контроля гидротурбины или гидроагрегата при продлении срока службы или обосновании возможности дальнейшей эксплуатации | ||||
Дополнительный контроль | |||||||
С1р | Ремонтная заварка | ВИК, ПВК (или МПД, или ВТК), УЗК, ТВ | |||||
Д1р, Д1т | Зоны деформации | Инструментальный контроль, ВИК, ПВК (или МПД, или ВТК), УЗК, ТВ | |||||
К1р, К2р, КЗт | Зоны высокого кавитационного износа | Инструментальный контроль, ВИК, ПВК (или МПД, или ВТК), УЗК, УЗТ, ТВ | |||||
Организация | Ф.И.О. | Подпись | Дата | ||||
Разработал | |||||||
Утвердил |
А1т — А8т — зоны на тыльной поверхности лопасти; А1р — А8р — зоны на рабочей поверхности лопасти; С1р — зона ремонтного шва на рабочей поверхности (вносится по результатам анализа ремонтных журналов); Д1р, Д1т — зоны деформации, обнаруженные при первичном визуальном контроле и запланированные для проведения дополнительного контроля; К1р, К2р, КЗт — зоны высокого локального коррозионного и эрозионного (кавитационного) износа, выявленные при первичном визуальном контроле и запланированные для проведения уточненного контроля
Рисунок В.4.1 (лист 2)
115
ГОСТ Р 55260.3.2—2023
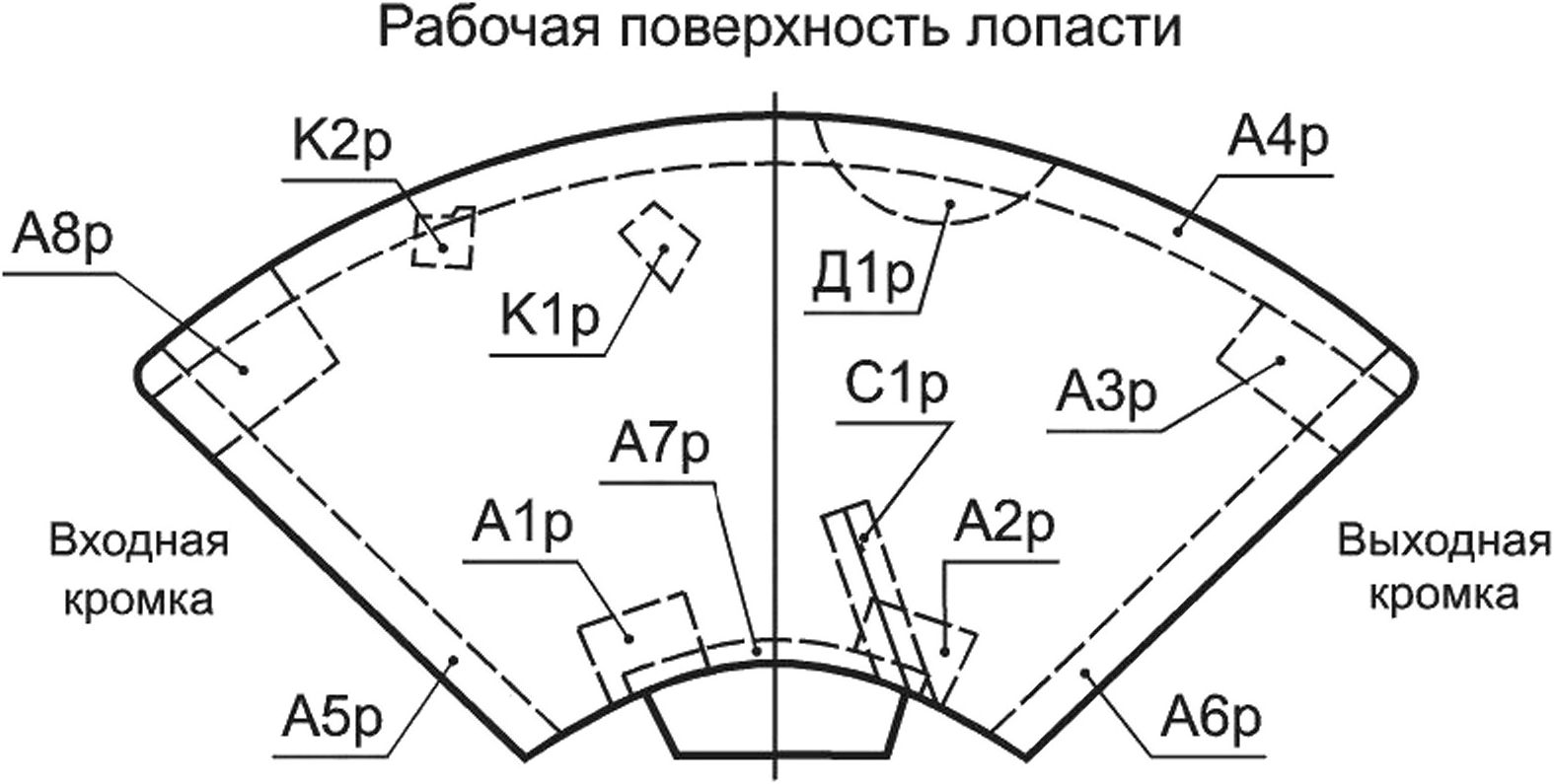
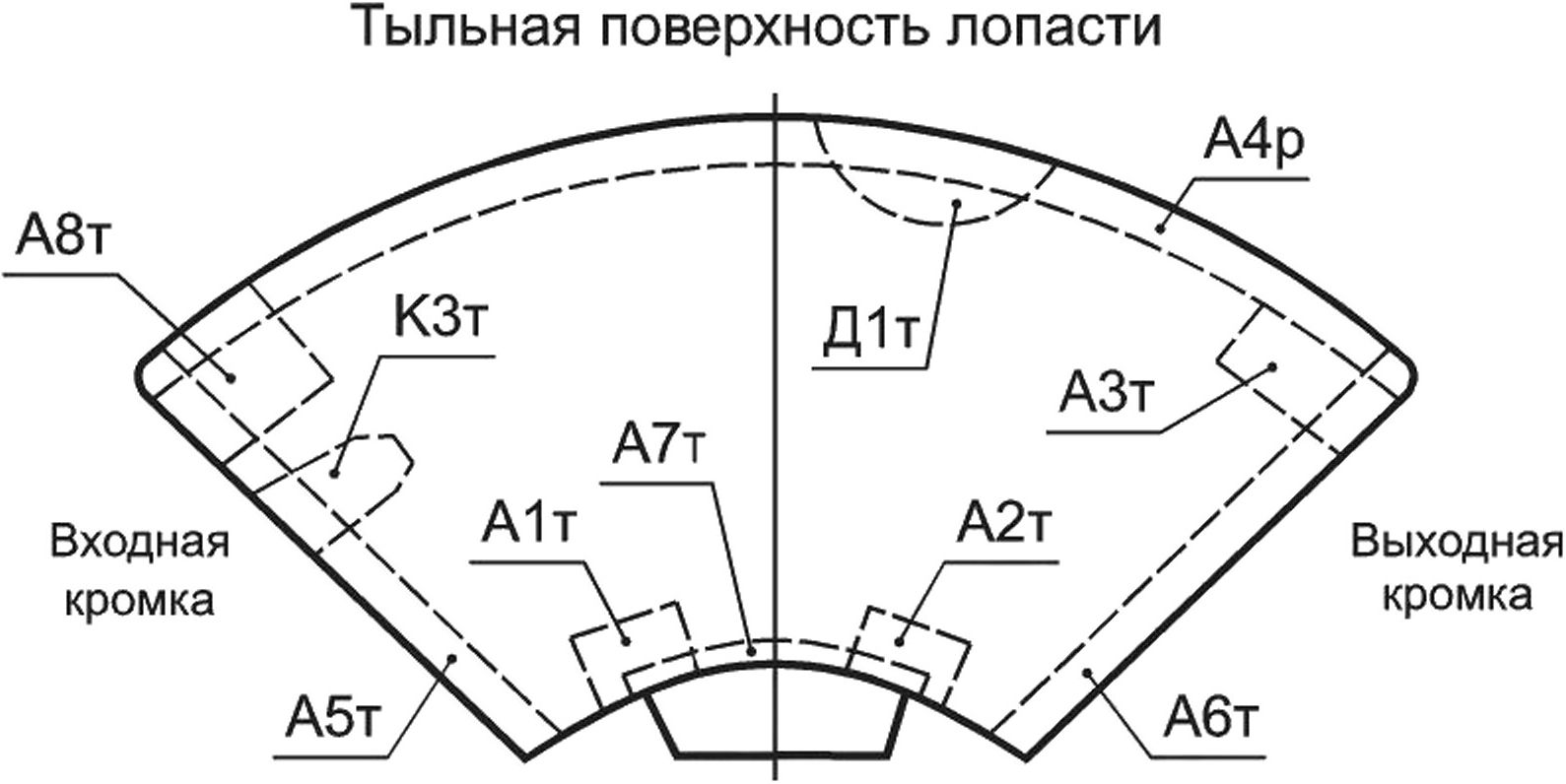
А1р, А1т — зона (400 х 400мм) перехода фланец — перо со стороны входной кромки;
А2р, А2т — зона (400 х 400мм) перехода фланец — перо со стороны выходной кромки;
АЗр, АЗт — зона периферийной и выходной кромки;
А4р, А4т — зона периферийной кромки;
А5р, А5т — зона входной кромки;
Абр, Абт — зона выходной кромки;
А7р, А7т — зона фланец — перо;
А8р, А8т — зона периферийной и входной кромки
Рисунок В.4.2 — Схема расположения зон контроля лопасти ПЛ-гидротурбины
116
ГОСТ Р 55260.3.2—2023
Карта зон проведения контроля металла рабочего колеса РО-гидротурбины_______________ | ||||
Программа № /Шифр___________________ | ||||
Первичный визуальный контроль | ||||
Зона | Размер зоны (мм) или объем контроля | Методы контроля ] | Примечания | |
Лопасти РК | Рабочая поверхность (Лр) | Вся поверхность | ВИК | По результатам контроля уточняются и дополняются зоны для инструментального контроля, ПВК, МПД, ВТК, УЗК, УЗТ, ТВ |
Тыльная поверхность (Лт) | Вся поверхность | ВИК | ||
Обод РК | Вся поверхность | ВИК | ||
Ступица РК | Вся поверхность | ВИК | ||
Лабиринтные уплотнения | 100 % | ВИК | В случае выемки колеса | |
Уточненный обязательный контроль | ||||
А1н | 500x300 | ВИК, ПВК (или МПД, или ВТК) | ||
А1в | 500x300 | ВИК, ПВК (или МПД, или ВТК) | ||
А2н | 500x300 | ВИК, ПВК (или МПД, или ВТК) | ||
А2в | 500x300 | ВИК, ПВК (или МПД, или ВТК) | ||
АЗн | ВИК, ПВК (или МПД, или ВТК) | |||
АЗв | ВИК, ПВК (или МПД, или ВТК) | |||
А4н | 200x200 | ТВ | ||
А4в | 200x200 | ТВ | ||
А5н | 500x300 | ВИК, ПВК (или МПД, или ВТК) | ||
А5в | 500x300 | ВИК, ПВК (или МПД, или ВТК) | ||
Абн | 500x300 | ВИК, ПВК (или МПД, или ВТК) | ||
Абв | 500x300 | ВИК, ПВК (или МПД, или ВТК) | ||
А7н | ВИК | |||
А7в | ВИК | |||
А8н | ВИК |
Рисунок В.4.3 — Карта зон проведения контроля металла РК РО гидротурбины (лист 1)
117
ГОСТ Р 55260.3.2—2023
А8в | ВИК | ||||||
А9н | ВИК, ПВК (или МПД, или ВТК) | ||||||
А9в | ВИК, ПВК (или МПД, или ВТК) | ||||||
Геометрические характеристики | Симметричность расположения лопастей, толщина кромок, размеры и равномерность зазоров между РК и неподвижными частями турбины, а также в лабиринтных уплотнениях | Инструментальный контроль, УЗТ | Соответствие проектной документации и требованиям НТД | ||||
Физико-механические и усталостные свойства металла лопастей | Выборочно (по необходимости на вырезанных образцах) | Проведение испытаний в соответствии с В.22 | Необходимость вырезки образцов, а также схемы вырезки и объем контроля определяются индивидуальной программой контроля гидротурбины или гидроагрегата при продлении срока службы или обосновании возможности дальнейшей эксплуатации | ||||
Дополнительный контроль | |||||||
С1 р | Ремонтная заварка или наплавка | ВИК, ПВК (или МПД, или ВТК), УЗК, ТВ | |||||
Д1р, Д1т | Зоны деформации | Инструментальный контроль, ВИК, ПВК (или МПД, или ВТК), УЗК, ТВ | |||||
К1р, К2р, КЗт | Зоны высокого кавитационного износа | Инструментальный контроль, ВИК, ПВК (или МПД, или ВТК), УЗК, УЗТ, ТВ | |||||
Организация | ФИО. | Подпись | Дата | ||||
Разработал | |||||||
Утвердил |
А1т — А9т — зоны на тыльной поверхности лопасти; А1р — А9р — зоны на рабочей поверхности лопасти; С1р — зона заварки или наплавки на рабочей поверхности (вносится по результатам анализа ремонтной документации); Д1р, Д1т — зоны деформации, обнаруженные при первичном визуальном контроле и запланированные для проведения дополнительного контроля; К1р, К2р, КЗт — зоны высокого локального коррозионного и эрозионного (кавитационного) износа, выявленные при первичном визуальном контроле и запланированные для проведения уточненного контроля
Рисунок В.4.3 (лист 2)
118
ГОСТ Р 55260.3.2—2023
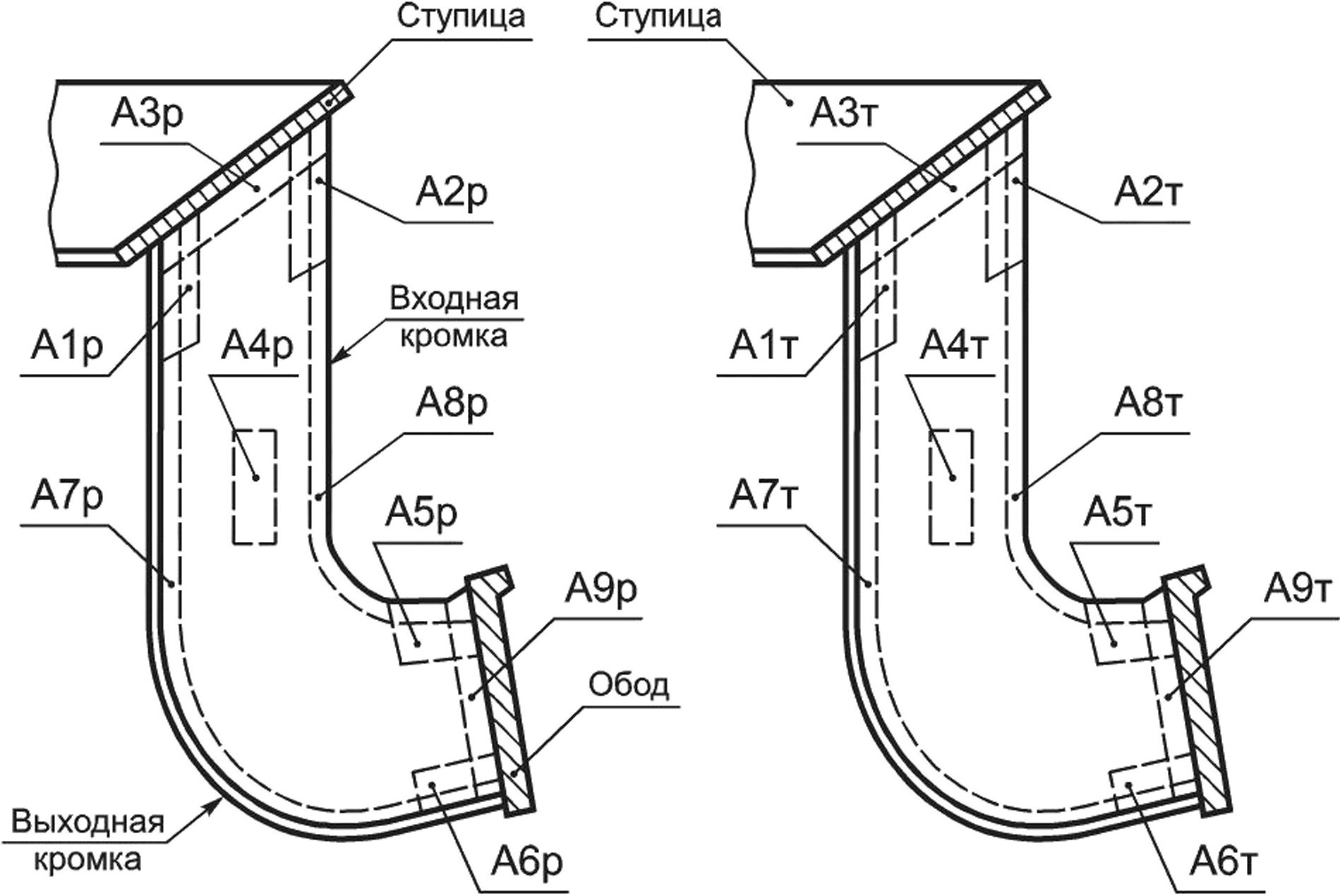
Рабочая поверхность лопасти
Тыльная поверхность лопасти
А1р, А1т — зона (400 * 400 мм) ступица — выходная кромка;
А2р, А2т — зона (400 * 400 мм) ступица — входная кромка;
АЗр, АЗт — зона ступица — лопасть сварное соединение;
А4р, А4т — зона центральная область лопасти;
А5р, А5т — зона (400 * 400 мм) обод — входная кромка;
Абр, Абт — зона (400 х 400 мм) обод — выходная кромка;
А7р, А7т — зона выходной кромки;
А8р, А8т — зона входной кромки;
А9р, А9т — зона обод — лопасть сварное соединение
Рисунок В.4.4 — Схема расположения зон контроля лопасти РО-гидротурбины
В.4.5 Формуляры повреждений РК
При визуальном контроле РК определяются места и виды повреждений металла. Фиксировать эти повреждения необходимо в соответствующих формулярах.
Формуляр повреждений металла лопастей представляет собой схематично представленный вид на рабочую и тыльную поверхности лопасти РК ПЛ-гидротурбины и схематичную развертку лопасти РК РО гидротурбины.
В формуляр вносят зоны механических, эрозионно-коррозионных, кавитационных повреждений, полученные в результате визуального и измерительного контроля металла. Размеры зон кавитационных повреждений — ширина, длина и глубина — записываются в таблицу с номером повреждения. В формуляре предусмотрен столбец для определения объема выборки металла V, см3. На этот же формуляр наносятся обнаруженные трещины и трещиноподобные и округлые дефекты на поверхности РК, отрывы части лопасти, коррозионные и эрозионные повреждения и иные выявленные механические повреждения РК.
Форма формуляра повреждений металла лопастей ПЛ-гидротурбины приведена на рисунке В.4.5, для РО-гидротурбины — на рисунке В.4.6.
119
ГОСТ Р 55260.3.2—2023
Дата:
Формуляр повреждений металла лопастей ПЛ-гидротурбины ст. №
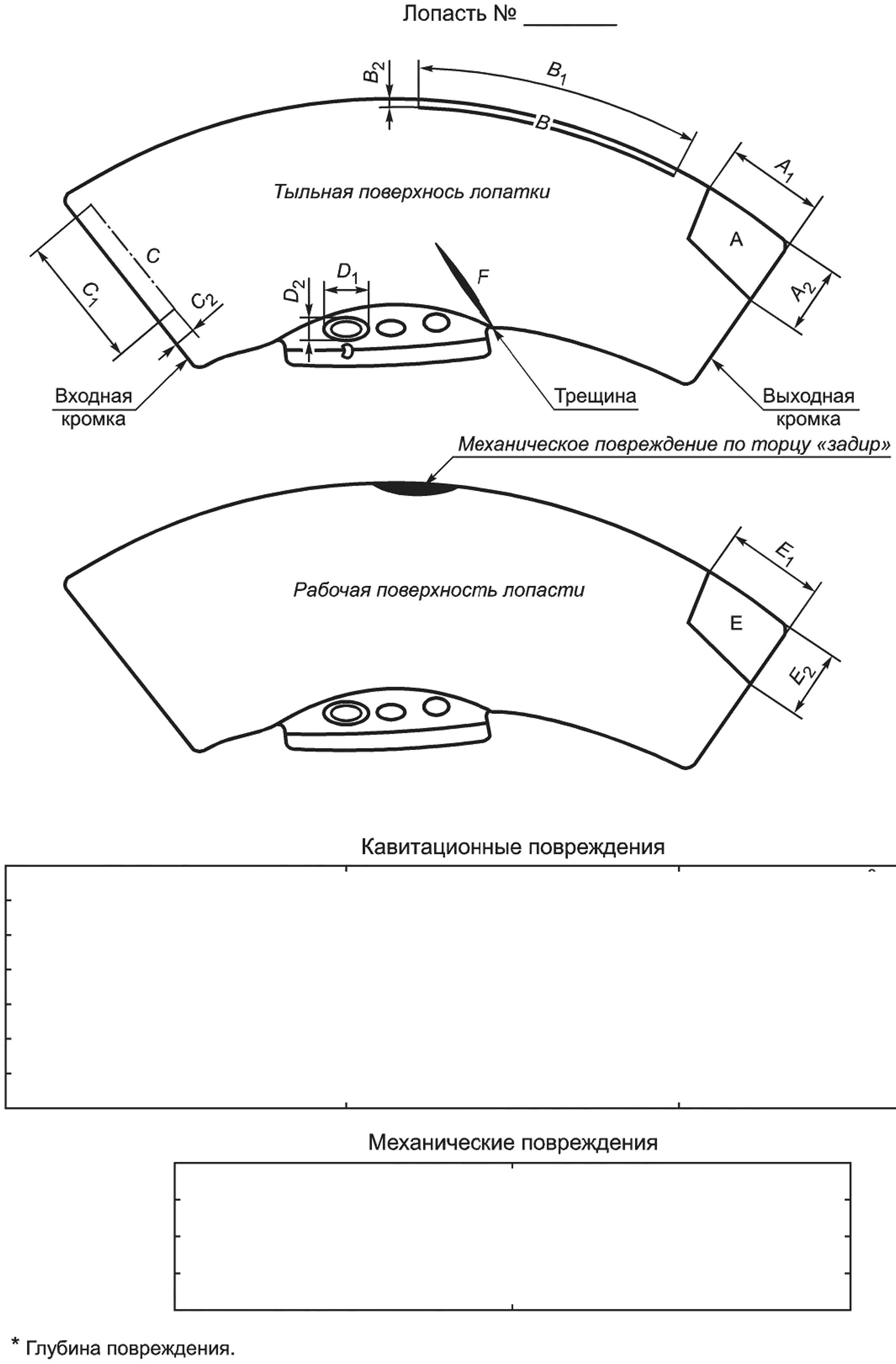
№ | Размеры,см | V, cm3 |
А | А^ х А^ х А^ | |
В | В^ х В2 х В^ | |
С | Cj X С2 X Cg | |
D | D^ х D2 х D3 | |
Е | E1xE2x e3 | |
№ | Характерный размер, см |
Трещина | lF |
Задир | |
Рисунок В.4.5 — Формуляр повреждений металла лопастей ПЛ-гидротурбины
120
ГОСТ Р 55260.3.2—2023
Дата:_____________________________
Формуляр
повреждений металла лопастей ПЛ-гидротурбины ст. №
Лопасть №
Рабочая поверхность лопасти
Тыльная поверхность лопасти
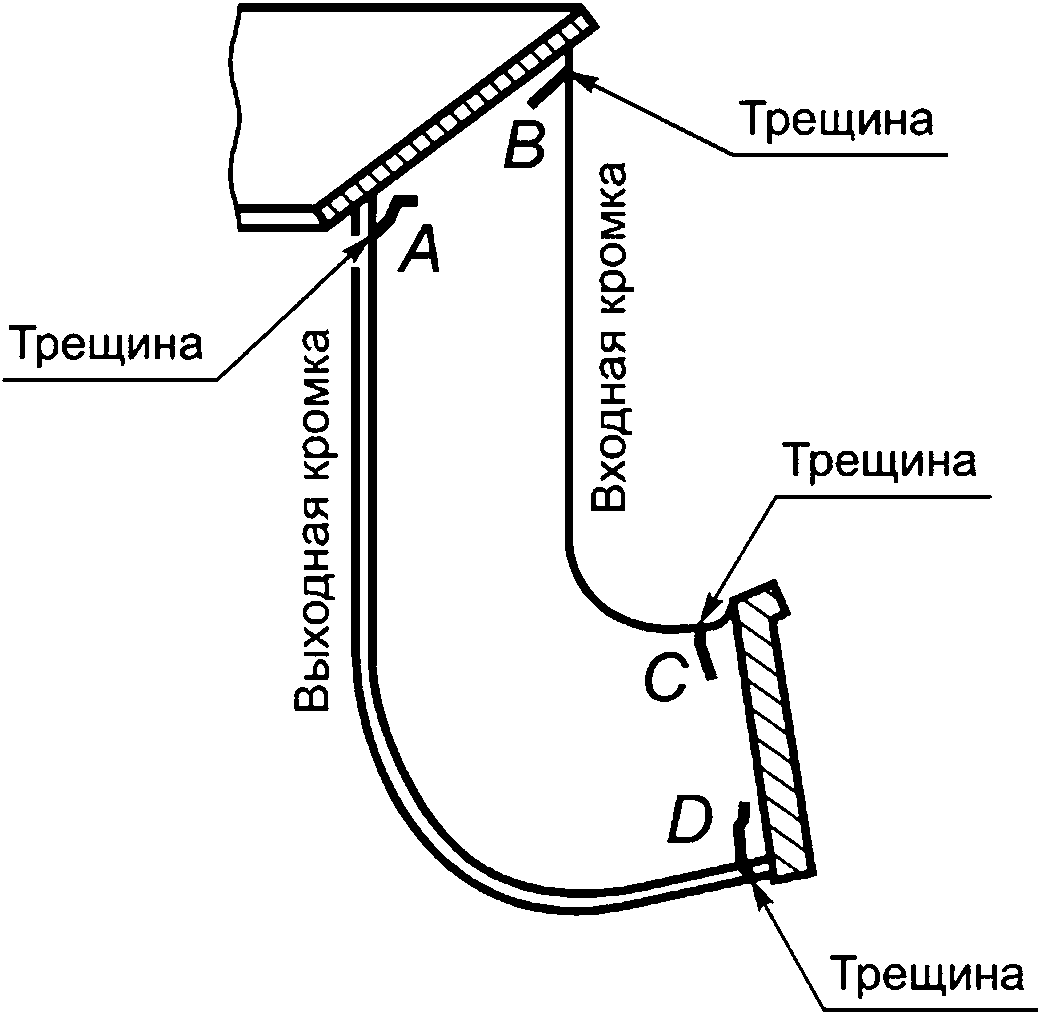
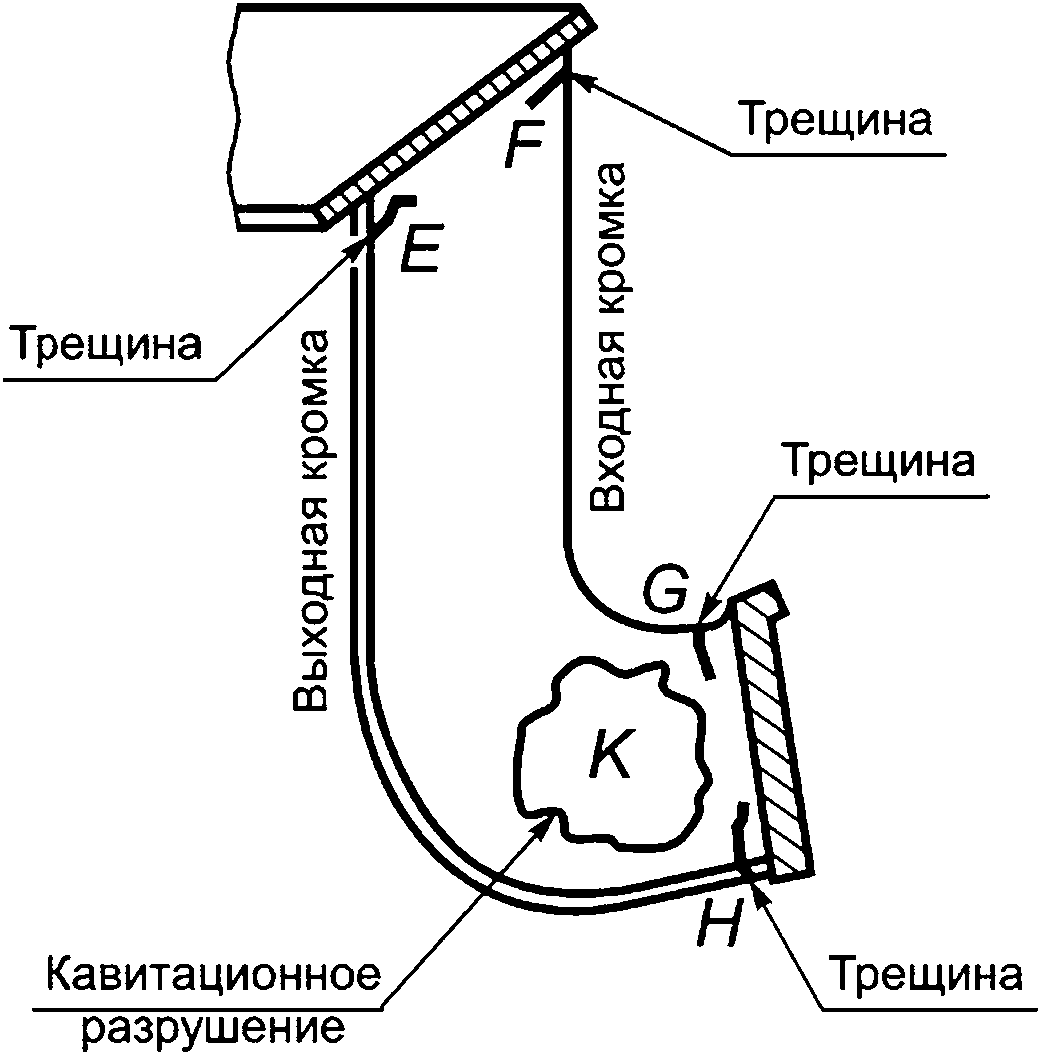
Кавитационные повреждения
№ | Размеры, см | V, см3 |
К | Ку * к2* к£ | |
Механические повреждения
№ | Характерный размер, см |
Трещина А | 1а |
Трещина В | 1в |
Трещина С | 1с |
Трещина D | lD |
Трещина Е | 1Е |
Трещина F | lF |
Трещина G | lG |
Трещина Н | lH |
* Глубина повреждения.
Рисунок В.4.6 — Формуляр повреждений металла лопастей РО-гидротурбины
121
ГОСТ Р 55260.3.2—2023
В.5 Типовая программа контроля состояния металла камер рабочих колес
В.5.1 Общие положения
КРК гидротурбин подвергаются контролю состояния основного и наплавленного металла для выявления повреждений и дефектов, оказывающих влияние на эксплуатационную надежность КРК.
Программа контроля состояния металла КРК предусматривает применение неразрушающих методов контроля, простукивание обечайки КРК молотком (метод свободных колебаний), гидроопробование, а также, при необходимости, проведение специальных обследований с использованием образцов металла (разрушающих методов контроля).
ВИК проводится в соответствии с рекомендациями В.2.1 и нормативными документами, регламентирующими данный вид неразрушающего контроля.
ПВК проводится в соответствии с рекомендациями В.2.2 и нормативными документами, регламентирующими данный вид неразрушающего контроля.
ВТК проводится в соответствии с рекомендациями В.2.3, нормативными документами, регламентирующими данный вид неразрушающего контроля, и руководством по эксплуатации приборов.
УЗК проводится в соответствии с В.2.4, нормативными документами, регламентирующими данный вид неразрушающего контроля, и руководством по эксплуатации приборов.
УЗТ проводится в соответствии с В.2.5, нормативными документами, регламентирующими данный вид неразрушающего контроля, и руководством по эксплуатации приборов.
МПД проводится в соответствии с В.2.6, нормативными документами, регламентирующими данный вид неразрушающего контроля, и руководством по эксплуатации приборов.
ТВ проводится в соответствии с В.2.7, нормативными документами, регламентирующими данный вид неразрушающего контроля, и руководством по эксплуатации приборов.
При необходимости уточнения характеристик материала проводят лабораторные испытания с использованием вырезанных образцов металла в соответствии с В.З.
В.5.2 Перечень контролируемых элементов
Контролю подлежат: облицовка КРК, отъемный сегмент, СП, крепежные элементы.
В.5.3 Характерные дефекты и повреждения
В.5.3.1 Наиболее опасными дефектами и повреждениями, которые оказывают решающее влияние на эксплуатационную надежность КРК и, в случае несвоевременного выявления, приводят к значительному увеличению времени, объемов и стоимости необходимого восстановительного ремонта, являются следующие:
- образование критической трещины с дальнейшим вырывом куска металла облицовки КРК;
- задир облицовки КРК с последующим отрывом металла облицовки;
- наличие пустот за облицовкой или отсутствие сцепления бетона с облицовкой вследствие низкого качества бетона, плохой проработки бетона, усадки бетона, выноса бетона по фильтрационным ходам, фильтрационного и кавитационного выпора облицовки и т. п.;
- недостаточная жесткость конструкции КРК за счет некачественного ее раскрепления в бетонном блоке;
- значительное несоответствие (уменьшение) реальной толщины металла облицовки проектной, полученное в результате обработки КРК на заводе и/или в процессе монтажа на ГЭС для обеспечения допустимого зазора между лопастями РК и облицовкой или уменьшение ее толщины при ремонте, а также за счет выноса металла с больших площадей вследствие кавитационной эрозии;
- стыковое соединение различных участков облицовки не на ребрах жесткости;
- наличие надрезов и иных дефектов металла облицовки;
- наличие трещин в металле до монтажа облицовки в блок ГА, а также после проведения ремонтных работ на облицовке;
- несоответствие физико-механических характеристик металла принятым при проектировании;
- некачественная подгонка листов металла к ребрам жесткости при ремонте;
- непровары стыков листов из-за неполной разделки металла под сварку при проведении ремонтных работ;
- трещины в сварных швах;
- наличие сквозных отверстий в панелях облицовки вследствие некачественной заварки инъекционных отверстий или местных разрушений металла кавитационной эрозией;
- отслоение защитного (противоэрозионного) слоя нержавеющей стали от основного металла облицовки;
- ослабление крепления отъемного сегмента с последующим его сдвигом, деформацией прилегающей металлической облицовки, уменьшением зазора между облицовкой и лопастями турбины вплоть до их отрыва;
- вырыв отъемного сегмента КРК;
- разрушение крепежных элементов КРК.
В.5.3.2 Наличие трещин и механических повреждений определяется с помощью осмотра и контроля неразрушающими методами в соответствии с В.1, В.2.
В.5.3.3 Опасность трещин с точки зрения возможности отрыва куска облицовки КРК определяется на основании оценки усталостной прочности и трещиностойкости камеры с учетом фактических данных о механических характеристиках металла, полученных в соответствии с В.З.
122
ГОСТ Р 55260.3.2—2023
Оценка усталостной прочности и трещиностойкости проводится расчетными методами путем моделирования процесса накопления усталостных повреждений вплоть до зарождения усталостной трещины и процесса развития трещины до образования магистральной трещины при достижении критического значения величины коэффициента интенсивности напряжений.
Оценку усталостной прочности и трещиностойкости следует проводить с учетом фактических режимов эксплуатации, учитывая фактические наработки в каждом эксплуатационном диапазоне (малая/средняя/большая/ номинальная мощность, XX, работа в режиме СК и т. п.), количество пусков-остановов ГА, время в простоях и ремонтах.
В.5.3.4 Возможность задевания лопастей РК о металл неподвижных частей ПЛ-гидротурбины оценивается на основании фактических данных по размерам и форме зазора «камера — лопасть».
Величины фактических зазоров определяются в соответствии с методиками, представленными в Б.З, Б.4. Допустимые отклонения зазоров от проектных значений представлены в таблице 6.3.
В.5.3.5 Интенсивность кавитационной эрозии оценивается по величине весовой потери металла, кг, из элементов проточной части за определенное число часов работы в соответствии с гарантиями завода — изготовителя гидротурбин.
В случае отсутствия заводских гарантий по потере металла при кавитационном износе допустимый объем этих потерь должен быть определен в соответствии с ГОСТ Р 55562.
В.5.4 Типовой объем контроля металла камер рабочих колес ПЛ-гидротурбин
В.5.4.1 Типовая программа контроля металла КРК гидротурбин предусматривает два этапа контроля: первичный визуальный контроль и простукивание, комплексный контроль. Объемы и методы контроля для каждого этапа отражаются в карте зон проведения контроля.
В.5.4.2 Первичный визуальный контроль и простукивание обечайки КРК молотком (метод свободных колебаний) проводится с целью уточнения зон проведения контроля, объемов и методов, используемых при уточненном контроле. Первичному визуальному контролю подвергается вся доступная поверхность КРК. На основании проведенного контроля должен быть составлен формуляр состояния КРК с нанесенными дефектами и оценена необходимость проведения комплексного контроля для определения объема основных текущих ремонтных мероприятий [20].
В.5.4.3 Комплексный контроль проводится в соответствии с картой контроля и схемой расположения зон контроля следующими методами и в следующих объемах:
- контроль геометрических параметров КРК в соответствии с Б.4;
- УЗТ металла КРК для определения разнотолщинности и остаточной толщины стенки обечайки относительно проектной величины после механической обработки секций и длительного воздействия кавитационной и абразивной эрозии, а также коррозии металла на границе металл — бетон опорного конуса КРК, выявления зон расслоения металла согласно В.2.5;
- ультразвуковая дефектоскопия металла КРК для выявления трещин и других дефектов в металле и сварных швах согласно В.2.4;
- магнитные измерения коэрцитивной силы с помощью ММК для оценки НДС стальных конструкций согласно В.5.4.4.4;
- ультразвуковая дефектоскопия бетона для оценки состояния штрабного и монолитного бетона опорного конуса КРК;
- при необходимости оценки состояния металла облицовки КРК проводится макроструктурное и микроструктурное обследование с использованием лабораторного комплекса аналитических приборов и методов.
В.5.4.4 Размеры и координаты зон контроля, а также объемы и методы контроля при комплексном контроле отражаются в карте контроля.
Карта контроля и схема расположения зон заполняются при разработке программы контроля и уточняются по результатам первичного визуального контроля.
В.5.4.4.1 Абразивный, коррозионный и механический износ металла КРК определяют эхоимпульсным методом с использованием серийно выпускаемых дефектоскопов или толщиномеров.
В.5.4.4.2 Скрытые дефекты обнаруживают как эхо-импульсным, так и зеркально-теневым методами с использованием дефектоскопов.
Для УЗК (толщинометрии и дефектоскопии) эхо и зеркально-теневым методами на достоверность и точность результатов при проведении контроля металлической облицовки КРК большое влияние оказывают:
- качество подготовки поверхности, через которую будут вводиться ультразвуковые волны;
- правильный выбор контактной жидкости для обеспечения надежного контакта между ультразвуковым преобразователем и металлом КРК;
- правильный выбор частоты вводимых ультразвуковых волн (и, соответственно, частоты преобразователей) и типа преобразователей (прямой совмещенный, прямой раздельно-совмещенный, наклонный);
- правильная настройка чувствительности приборов.
Качество подготовки поверхности ввода ультразвуковых сигналов должно обеспечить максимальное прохождение сигналов. Для этого поверхность освобождают от неплотно прилегающих наслоений (ржавчина, отстающее защитное покрытие) и сглаживают неровности для обеспечения стабильного акустического контакта. Подготовку
123
ГОСТ Р 55260.3.2—2023
поверхности проводят вручную (шабером, металлической щеткой, наждачной бумагой) или механическим способом (шлифовальной машиной), добиваясь, чтобы параметр шероховатости поверхности по высоте неровностей Rz был не более 50 мкм.
Толщинометрия, осуществляемая приборами, использующими электромагнитноакустический (ЭМА) способ возбуждения и приема сдвиговых колебаний в токопроводящем материале через воздушный зазор или непроводящее покрытие (краска, пленка, загрязнения, коррозия металла и т. д.), позволяют измерять толщину материала от 2 мм до 200 мм (для стали) без зачистки поверхности и без применения контактной жидкости, что является актуальным в условиях обследования металлоконструкций гидротехнических сооружений.
В.5.4.4.3 Поверхностные дефекты позволяет обнаружить также ПВК. При этом определяются конфигурация (форма) и размер (поверхностная протяженность) дефекта (согласно В.2.2).
В.5.4.4.4 Магнитные измерения коэрцитивной силы с помощью ММК для оценки НДС стальных конструкций проводят в соответствии с ГОСТ Р 58599 и руководством по эксплуатации прибора (коэрцитиметра, структуроскопа).
При реализации данного метода используется свойство металла, обусловленное наличием корреляции между магнитными свойствами металла, а именно — величины коэрцитивной силы, от степени деградации металла (зарождение, развитие и накопление микроповреждений в структуре металла).
В реальных условиях эксплуатации металл подвергается, как правило, сложному двух-трехосному нагружению в сочетании с набором факторов деградации, ускоряющих зарождение, развитие и накопление микроповреждений. В случае металлоконструкций КРК это нагружение является совокупностью статического (постоянного гравитационного и медленно меняющегося гидростатического) нагружения и циклического (с разными частотами и амплитудами, включая вибрацию и гидродинамические силы). При всем множестве причин для деградации металла срабатывает важное упрощающее природное свойство коэрцитивной силы, суммирующее это сложное многообразие, состоящее в том, что величина коэрцитивной силы металла непрерывно и заметно, в разы, растет от начального значения, пока металл проходит стадии от состояния поставки до его конечного состояния — разрушения. Начальное и конечное значения коэрцитивной силы у каждой марки металла — это свои характерные константы. Конечное значение при этом не зависит от того, сколько и каких эксплуатационных факторов привели металл к разрушению. Эти две величины коэрцитивной силы — в начальном состоянии (поставки) и в состоянии предразрушения — такие же значимые параметры для каждой марки стали, как, например, предел прочности и предел текучести.
При проведении обследования металла КРК для измерения коэрцитивной силы можно использовать, например, прибор — структуроскоп КРМ-Ц-К2М. Его отличительной особенностью является малая зависимость точности измерения прибором от зазора, возникающего при установке датчика прибора на исследуемую поверхность, те. показания прибора зависят только от свойств металла и не зависят от таких мешающих факторов, как защитное покрытие (краска, пленка, коррозия, загрязнения, шероховатость, кривизна поверхности и т. д.). Допустимый зазор между датчиком прибора и контролируемым металлом — до 6 мм.
В.5.4.4.5 Для УЗТ металла КРК, состоящего из литых обечаек с толщиной основного металла более 50 мм и большим разбросом по толщине (от 70 до 40 мм) частота ультразвуковых волн должна быть не более 2,5 МГц (2,5; 1,8; 1,25).
Донная (обращенная к штрабному бетону) поверхность металла КРК из обычной углеродистой стали, как правило, сильно корродирована, что ослабляет отраженный сигнал. Величина ослабления нестабильна, поэтому рекомендуется настройку чувствительности проводить непосредственно на КРК.
При УЗТ металла КРК с использованием дефектоскопа следует применять прямые раздельно-совмещенные преобразователи.
При использовании этого ультразвукового метода поверхность обследуемого металла должна быть тщательно подготовлена.
При применении для обследования приборов, использующих ЭМА способ возбуждения и приема сдвиговых колебаний, подготовку поверхности можно не проводить.
Проводить толщинометрию и дефектоскопию на участках с наплавкой (особенно отремонтированной) проблематично.
Для сварных КРК с толщиной металла до 40 мм, с относительно гладкой поверхностью и отсутствием ржавчины при толщинометрии следует использовать преобразователи ультразвуковых волн на частоту 5 МГц (10 МГц), которые дают более точный результат, а при дефектоскопии позволяют выявить более мелкие дефекты.
При толщинометрии металла с использованием дефектоскопа следует применять прямые раздельно-совмещенные преобразователи, при дефектоскопии возможно использование как прямых, так и наклонных преобразователей.
Контроль сварных соединений КРК следует проводить в соответствии с ГОСТ Р 55724. Применение ультразвука в целях дефектоскопии сварных швов в обечайках КРК ограничено условиями одностороннего доступа. На практике наиболее часто встречаются следующие схемы сварных соединений:
- стыковые сварные соединения — доступ контроля со стороны сварки;
- тавровые соединения (сварка металла облицовки с ребром жесткости) — контроль сварки осуществляется «вслепую» со стороны листа;
- сварка двух листов облицовки на ребре жесткости —доступ контроля со стороны сварки.
124
ГОСТ Р 55260.3.2—2023
Стыковые сварные соединения контролируют эхо-методом с преобразователем, включенным по совмещенной схеме. При этом для контроля швов толщиной от 10 до 50 мм используют преобразователи с частотой УЗ сигнала 2,5 МГц, размером пьезопластины от 12 до 15 мм и углом наклона от 40° до 50°. Схемы и траектории сканирования выбираются в каждом конкретном случае исходя из условий доступа и могут быть следующими (см. рисунок В.4.7):
- продольное сканирование;
- поперечное сканирование;
- поперечно-продольное сканирование;
- продольно-поперечное сканирование;
- вращательное сканирование в горизонтальной плоскости.
Основные дефекты стыковых сварных соединений: поры, шлаковые включения, непровары, трещины.
Для контроля корня шва и выявления трещин и непроваров в этой зоне шва применяются зеркально-теневой, эхо-зеркальный и эхо методы (см. рисунок В.4.8).
Стыковые сварные соединения на ребре жесткости контролируются по схемам, показанным на рисунке В.4.8. При выравнивании шва шлифмашиной непровар между корнем шва и ребром жесткости контролируется эхо-методом с вводом продольных волн прямой головкой. Тавровые сварные соединения контролируются с поверхности металла облицовки: эхо-методом с вводом продольных волн прямой головкой — для определения непроваров ребра жесткости и металла облицовки и эхо-зеркальным методом — для оценки качества шва.
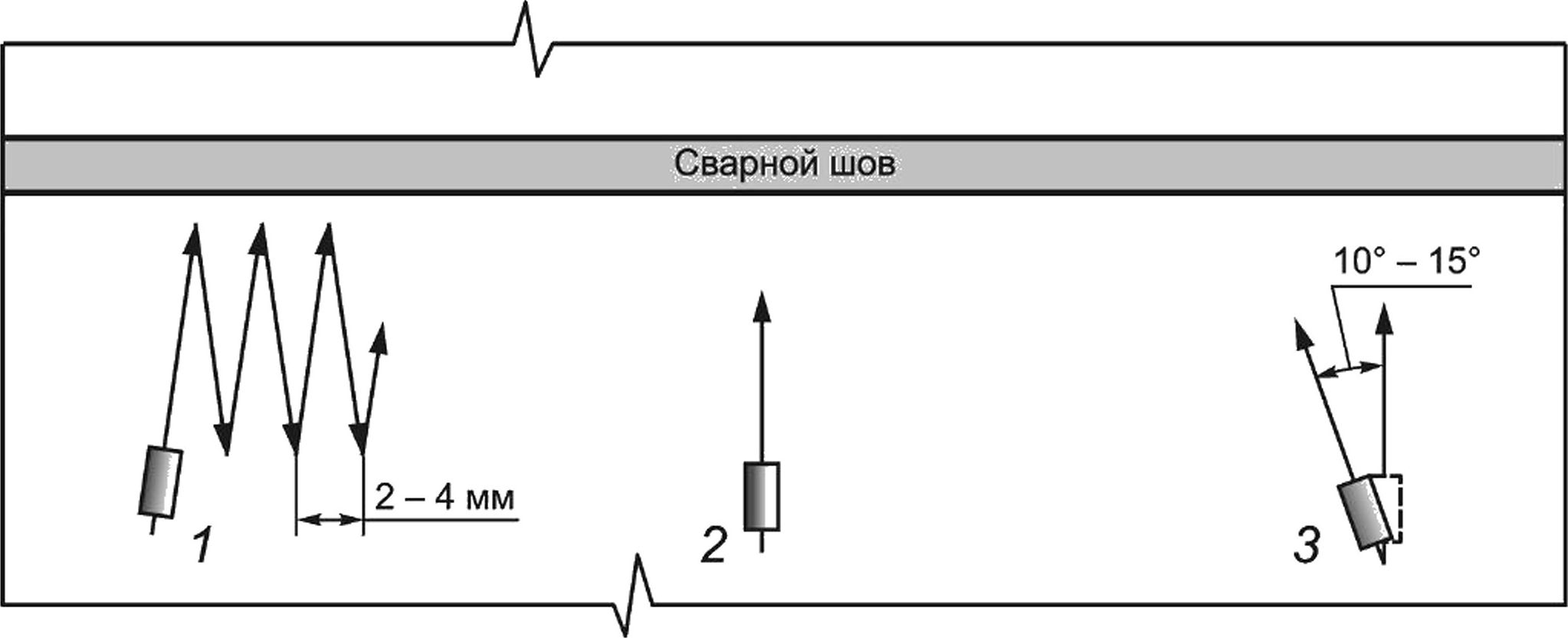
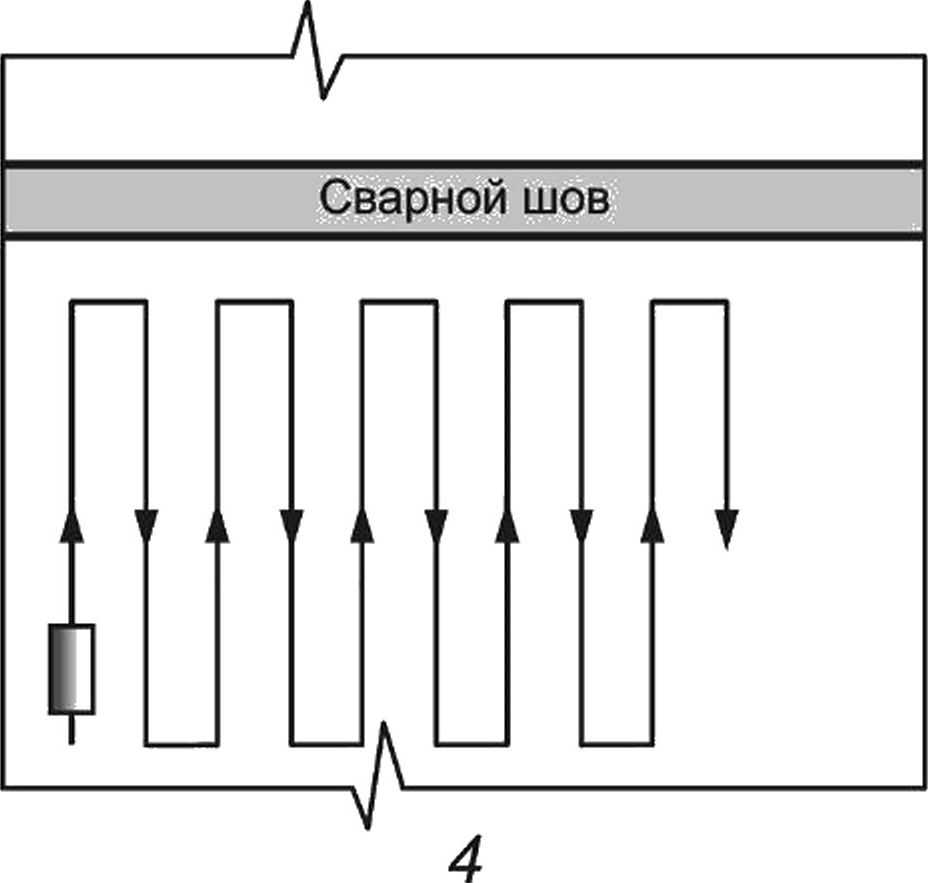
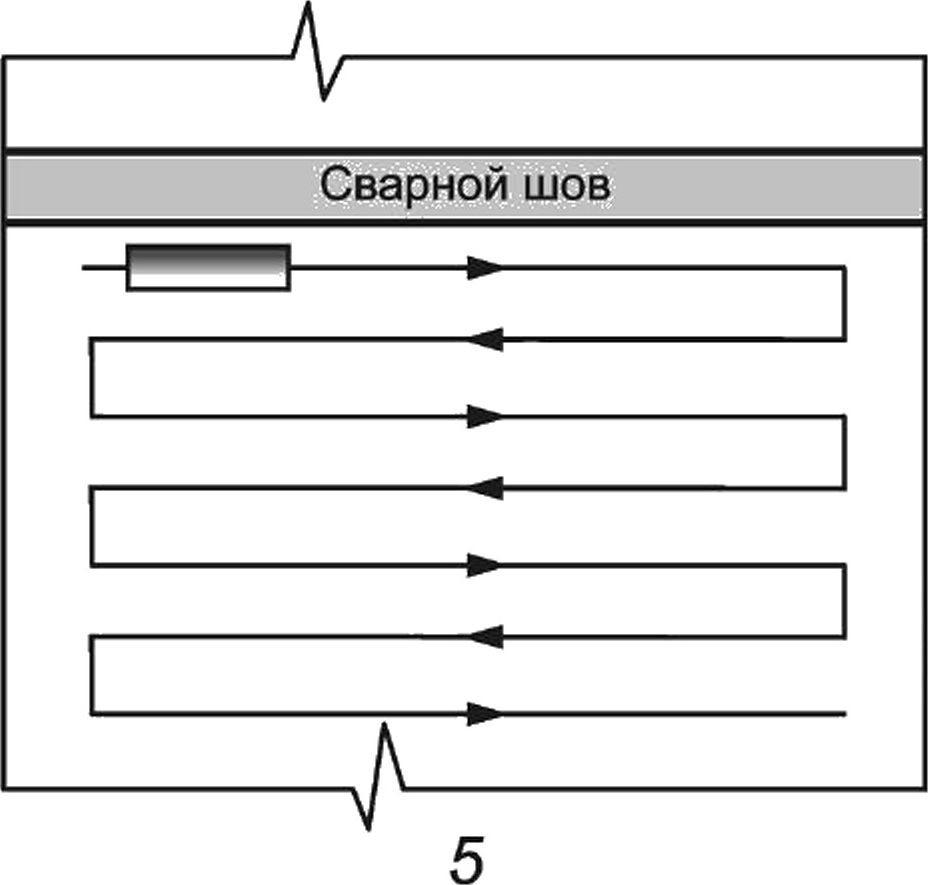
1 — продольное сканирование; 2 — поперечное сканирование; 3 — вращательное сканирование; 4 — поперечно-продольное сканирование; 5 — продольно-поперечное сканирование
Рисунок В.4.7 — Схемы и траектории сканирования сварных швов
125
ГОСТ Р 55260.3.2—2023
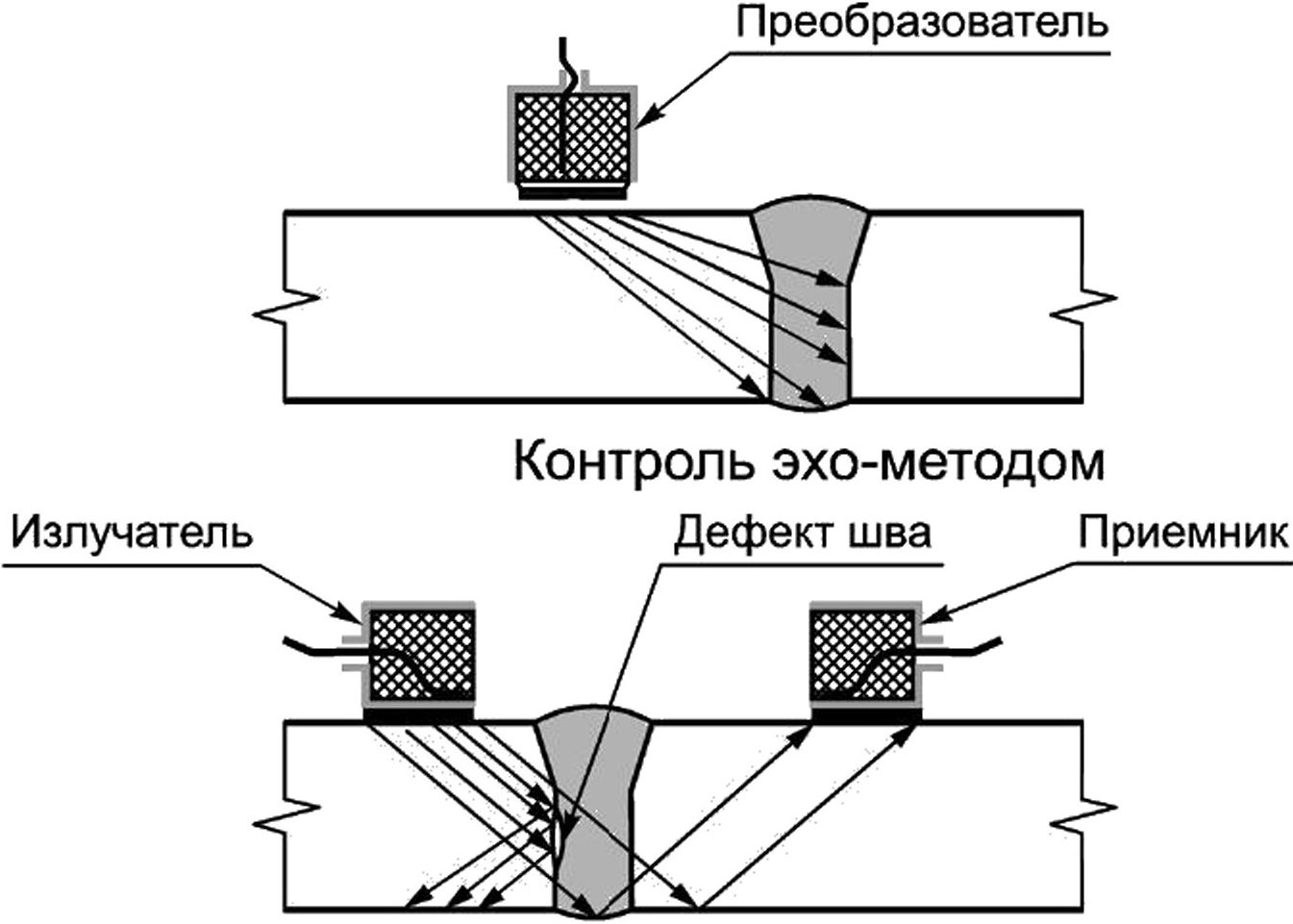
Контроль зеркально-теневым методом
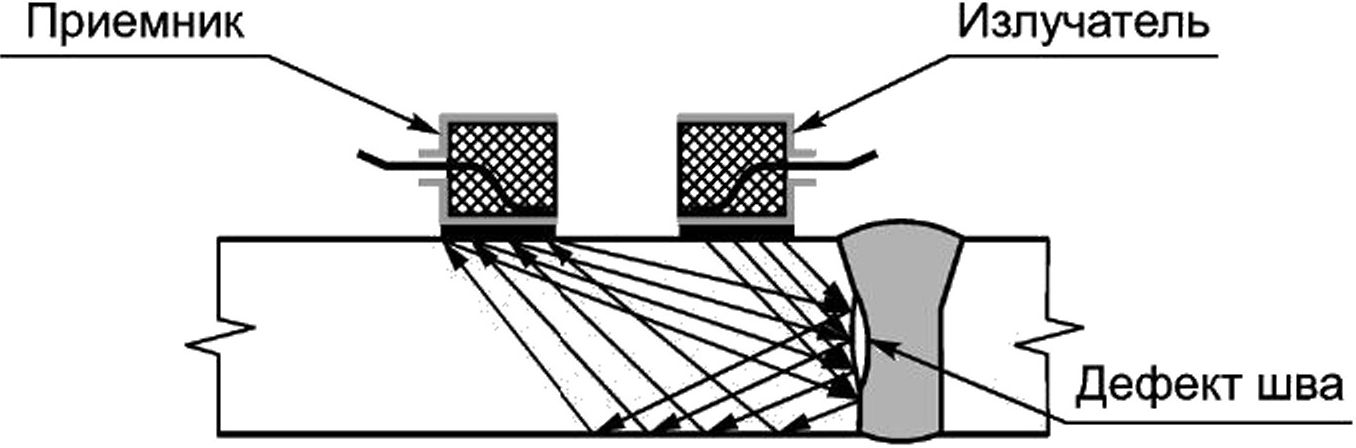
Контроль эхо-зеркальным методом
а) Стыковое сварное соединение
Преобразователь
Излучатель
Приемник

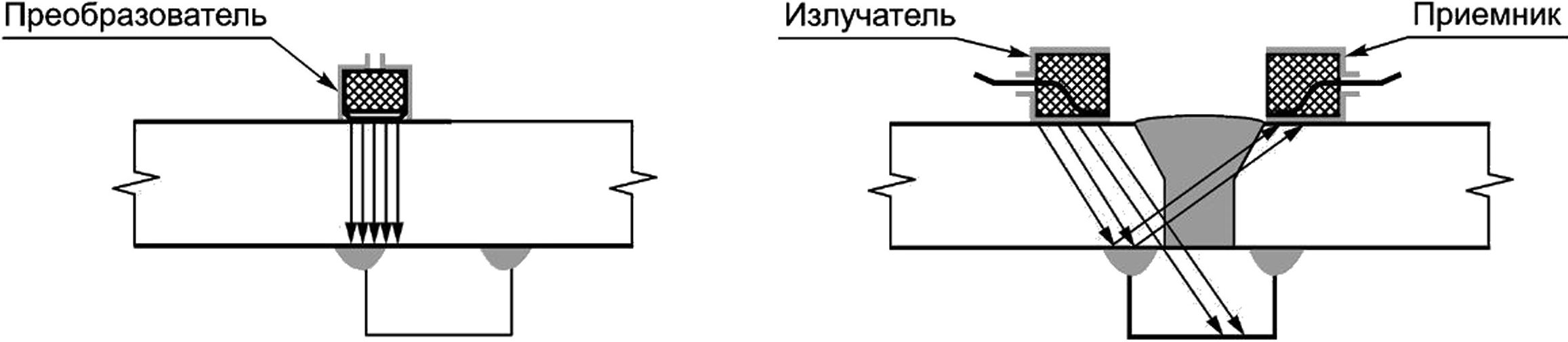
Контроль эхо-методом
Контроль зеркально-теневым методом
б) Стыковое сварное соединение на ребре жесткости
Рисунок В.4.8 — Схемы контроля сварных соединений элементов КРК
В.5.4.4.6 Все обнаруженные дефекты и участки с пониженной, относительно проектной, толщиной металла КРК заносятся в журнал состояния КРК и отмечаются в формуляре состояния.
В.5.4.5 Образцы формуляров контроля КРК представлены на рисунках В.4.9 — В.4.11.
В.5.4.6 Визуальный контроль КРК
Во время визуального контроля оценивается общее внешнее состояние КРК и отъемного сегмента. Выявляются видимые дефекты металла (крупные трещины, нарушение сплошности швов секций обечайки, крупные свищи в металле, отслоения с вырывом металла, сдвиг сегмента и т. д.).
126
ГОСТ Р 55260.3.2—2023
При визуальном контроле обращают внимание на дефекты, образующиеся в результате кавитационной эрозии металла. Наличие трещин в металле определяют с помощью лупы с увеличением от четырех до семи раз. Более тщательное обследование отслоившейся восстановительной наплавки проводится путем ее удаления и оценки состояния основного металла.
Поверхностные дефекты позволяет обнаружить также ПВК или МПД — выборочно на поверхностях, наиболее подверженных разрушениям.
В.5.4.7 Метод свободных колебаний
Простукивание обечайки молотком (метод свободных колебаний) проводится с целью выявления и оконтуривания заоблицовочных полостей и отслоений.
Если обечайка КРК изготовлена из двух металлов, основного и наплавленного, то дефекты наплавки и ее сцепление с основным металлом также определяют методом свободных колебаний (простукиванием).
В.5.4.8 Гидроопробование КРК
Гидроопробование (гидравлические испытания) обечайки КРК рекомендуется проводить перед началом ремонтно-восстановительных работ на обечайке КРК и после завершения сварочных работ (в соответствии с В.5.6).
Гидравлические испытания обечайки КРК предназначены для:
- выявления наличия сквозных трещин и свищей в металле тех участков обечайки, которые расположены в зоне заоблицовочных полостей и отслоений металла от штрабного бетона, обнаруженных при проведении периодического контроля состояния КРК;
- проверки качества сварки после проведения ремонтно-восстановительных работ и контроля отсутствия дефектов, не зафиксированных при периодическом контроле;
- выявления гидравлической связи между отдельными заоблицовочными полостями, обнаруженными при проведении периодического контроля, а также фильтрационных ходов и гидравлической связи полостей с конусом или коленом отсасывающей трубы ГА.
Гидравлические испытания обечайки КРК производятся путем подачи воды от насосной станции в заобли-цовочные полости под давлением, не превышающим допустимое для данной КРК по условиям статической прочности и устойчивости ее обечайки.
Технологическая инструкция проведения гидравлических испытаний КРК соответствует В.5.6.
В.5.5 Формуляры повреждений металла КРК
В.5.5.1 Формуляр зон повреждений металла КРК и примыкающих зон
При составлении формуляра зон повреждений металла КРК и примыкающих зон развертка формуляра делится по горизонтали на зоны, соответствующие количеству лопаток НА, с нанесением секторов КРК, секторов НКНА и СП — толстые линии развертки формуляра.
В вертикальном направлении формуляр поделен на пять областей, что соответствует конструкции самой проточной части агрегата станции, а именно:
- область N° 1 — НКНА;
- область № 2 — верхний пояс КРК без облицовки нержавеющей сталью;
- область N° 3 — верхний пояс КРК с облицовкой нержавеющей сталью;
- область № 4 — нижний пояс КРК с облицовкой нержавеющей сталью;
- область № 5 — СП.
В формуляр вносят зоны повреждений, полученные в результате визуального контроля и с испытанием металлической облицовки методом свободных колебаний (простукиванием).
Простукивание металла проводится в каждом секторе, выявленные дефекты обрисовываются мелом на металле и заносятся в формуляр под своим номером. Размеры — ширина, длина и площадь записываются в таблицу с номером дефекта, трещины фиксируются в формуляре с длиной и глубиной (см. рисунок В.4.9).
Все размеры заносятся в миллиметрах в таблице в формуляре.
В графе «Условные обозначения» указаны возможные виды повреждений металла, а именно:
- отслоение наплавки от основного металла обечайки — это повреждение возможно в областях № 2, № 3, № 4, где имеется наплавка нержавеющей сталью;
- вырыв наплавки от основного металла обечайки, также в областях с наплавкой нержавеющей сталью;
- полость между основным металлом и штрабным бетоном;
- отрыв основного металла от штрабного бетона;
- трещина в металле;
- участок натира металла.
Кавитационные повреждения заносятся в отдельный формуляр (см. рисунок В.4.11).
В.5.5.2 Формуляр толщинометрии металла зон КРК (КРК)
Выборочная толщинометрия металла производится неразрушающими методами ультразвуковой диагностики.
При составлении формуляра толщинометрии металла развертка формуляра делится по горизонтали на зоны, соответствующие количеству лопаток НА, с нанесением секторов КРК, секторов НКНА и СП — толстые линии развертки формуляра.
В вертикальном направлении формуляр поделен на пять областей, что соответствует конструкции самой проточной части агрегата станции, а именно:
127
ГОСТ Р 55260.3.2—2023
- область № 1 — НКНА;
- область № 2 — верхний пояс КРК без облицовки нержавеющей сталью;
- область № 3 — верхний пояс КРК с облицовкой нержавеющей сталью;
- область № 4 — нижний пояс КРК с облицовкой нержавеющей сталью;
- область № 5 — СП.
В формуляр вносят зоны повреждений, полученные в результате визуального контроля и с испытанием металлической облицовки методом свободных колебаний (простукиванием).
Толщинометрия поврежденных зон, где были выявлены отслоение наплавки от основного металла обечайки, вырыв наплавки от основного металла обечайки, отрыв основного металла от штрабного бетона производятся выборочно, без занесения в таблицу, результаты заносятся в формуляр рядом с повреждением.
Выборочная толщинометрия металла неповрежденных зон проводится на каждом секторе под НКНА и строго по осям лопаток НА (вне ребер жесткости).
Пять областей, на которые была поделена развертка проточной части, в свою очередь, поделена на зоны замера толщины металла с восьмью точками «прозвучивания»:
- в области № 1 —точка «прозвучивания» 1 —толщинометрия металла НКНА;
- в области №2 — точка «прозвучивания» 2 — толщинометрия металла КРК;
- в области № 3 — точки «прозвучивания» 3, Зв, Зн, где индексы «в», «н» означают, что измерения в обечайке проводились соответственно выше или ниже оси разворота лопастей турбины;
- в области № 4 — точки «прозвучивания» 41 и 42 — в каждом межреберном пространстве области производится толщинометрия облицовки обечайки КРК;
- в области № 5 — точка «прозвучивания» 5 — толщинометрия металла СП.
Результаты толщинометрии заносят в таблицу формуляра в соответствующую номеру лопатки (по горизонтали) и точке «прозвучивания» (по вертикали) графу. Размеры толщины металла заносятся в миллиметрах (см. рисунок В.4.10).
В.5.5.3 Формуляр кавитационных повреждений металла зон КРК
При составлении формуляра кавитационных повреждений металла развертка формуляра делится по горизонтали на зоны, соответствующие количеству лопаток НА, в данном примере на тридцать две части, с нанесением секторов КРК, секторов НКНА и СП (толстые линии развертки формуляра).
В вертикальном направлении формуляр поделен на пять областей, что соответствует конструкции самой проточной части агрегата станции, а именно:
- область № 1 — НКНА;
- область № 2 — верхний пояс КРК без облицовки нержавеющей сталью;
- область № 3 — верхний пояс КРК с облицовкой нержавеющей сталью;
- область № 4 — нижний пояс КРК с облицовкой нержавеющей сталью;
- область № 5 — СП.
В формуляр вносят зоны повреждений, полученные в результате визуального контроля металла, аналогично как при составлении формуляра повреждений металла.
Размеры — ширина, длина и площадь — записываются в таблицу с номером повреждения, трещины фиксируются в формуляре с длиной и максимальной глубиной.
Все возможные виды кавитационных повреждений указаны на самом формуляре в условных обозначениях (см. рисунок В.4.11).
128
Формуляр повреждений металла камеры рабочего колеса и примыкающих зон
Условные обозначения
129
Х1А
32
ХПБ 32
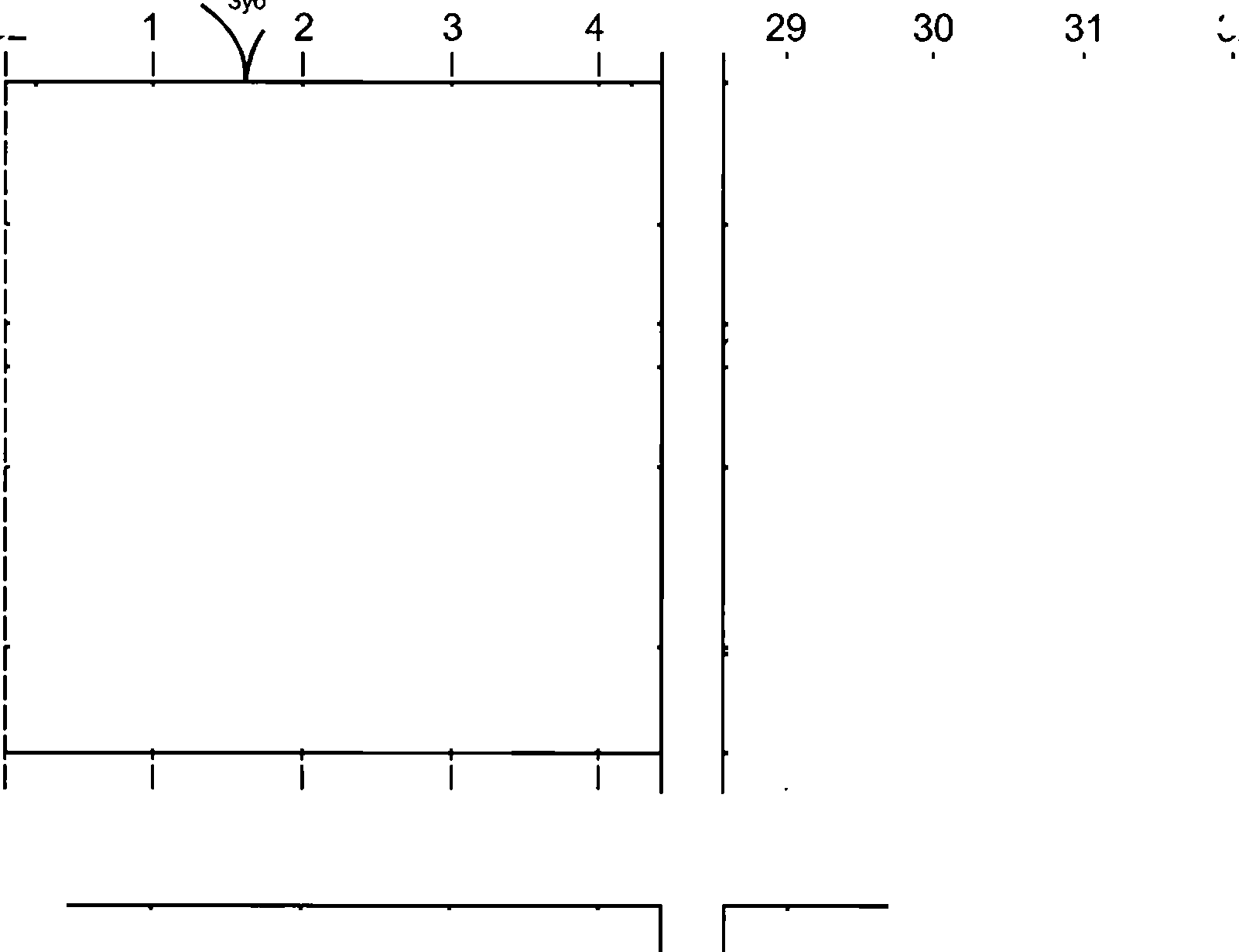
1 1 1 1111 1111 1111 ,211, | |||||
11 ' ль11 | |||||
I— | --1--к — 1 1 | ||||
м | § I 25 | 1 1 1 1 | |||
। 438 ' I ^г | 4 | ||||
1 1 1 1 | |||||
I I 1 I I |
№ дефекта | 32 | 1 | 2 | 3 | 4 |
1 | 438x300=02858 | 165x211=28502 | Длина 650 мм | ||
2 | 256x321=81446 | ||||
3 | 264x202=28851 | ||||
4 | 203x424=65417 | ||||
5 | |||||
6 | |||||
7 | |||||
8 | |||||
9 | |||||
10 |
1111 | ||
1111 1111 1111 1111 1111 | Нижнее кольцо НА М Ж | |
1111 | Верхняя граница заводской облицовки | Камера рабочего колеса | |
В | ||
i i i i iiii iiii | ||
iiii iiii iiii IIII iiii | Нижний пояс КРК | |
1 Нижняя граница'заводской облицовки IIII | Сопрягающий пояс | |
iiii |
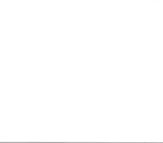
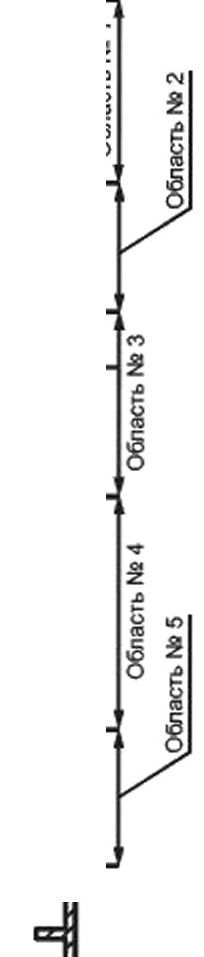
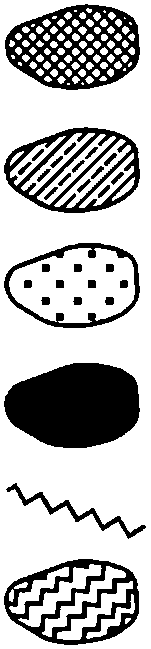
- отслоение наплавки от основного металла обечайки;
- вырыв наплавки от основного металла обечайки;
- полости между основным металлом обечайки и штрабным бетоном;
- вырыв обечайки от штрабного бетона;
- трещина в обечайке;
- участок натира
Примечания:
- в таблице повреждений указываются ширина, длина и приблизительная площадь повреждений в мм, мм2;
- развертка схематически принята цилиндрической;
- нумерация лопаток НА принята по номерам в шахте турбины
Схематический план КРК по оси разворота лопастей
+*ЛБ
29 | 30 | 31 | 32 | № повреждения | Примечание |
Длина 5916 мм | 1 | ||||
2 | |||||
3 | |||||
4 | |||||
5 | |||||
6 | |||||
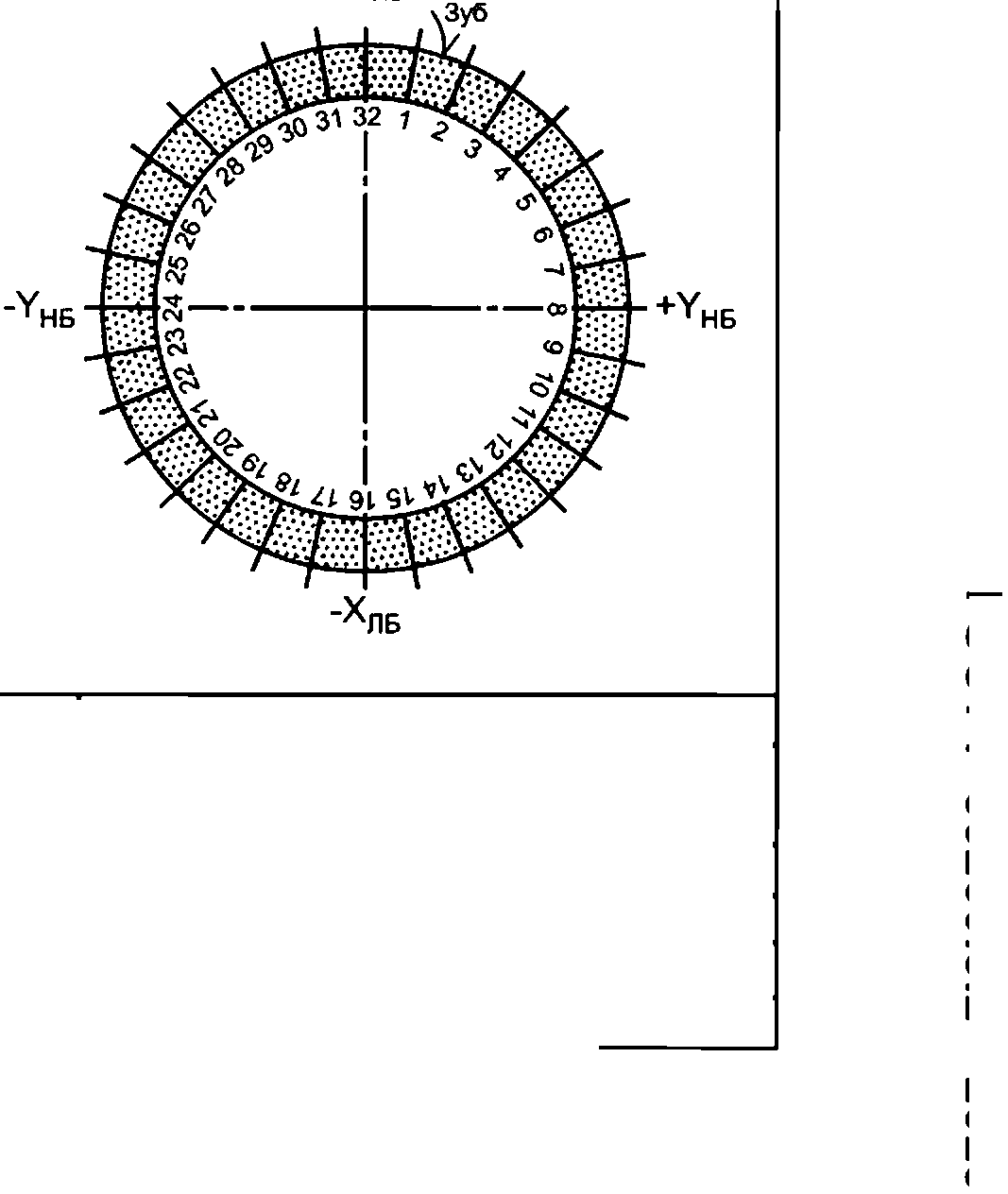
Дата | |||||
Наменование станции | |||||
Замерил | Отчетная документация диагностики металла HKHA. КРК, СП агрегата № | Номер турбины | Лист | ||
Станц. | Заводск. | ||||
Замерил | |||||
Проверил | |||||
Формуляр состояния металла |
Рисунок В.4.9 — Формуляр повреждений металла КРК и примыкающих зон
ГОСТ Р 55260.3.2—2023
130
Формуляр толщинометрии металла камеры рабочего колеса и примыкающих зон
Условные обозначения
Х1А 32
ГОСТ Р 55260.3.2—2023
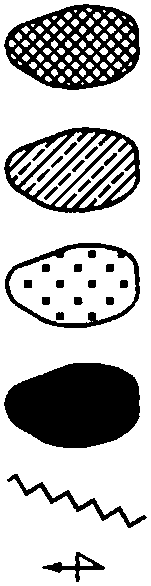
- отслоение наплавки от основного металла обечайки;
ХПБ
32
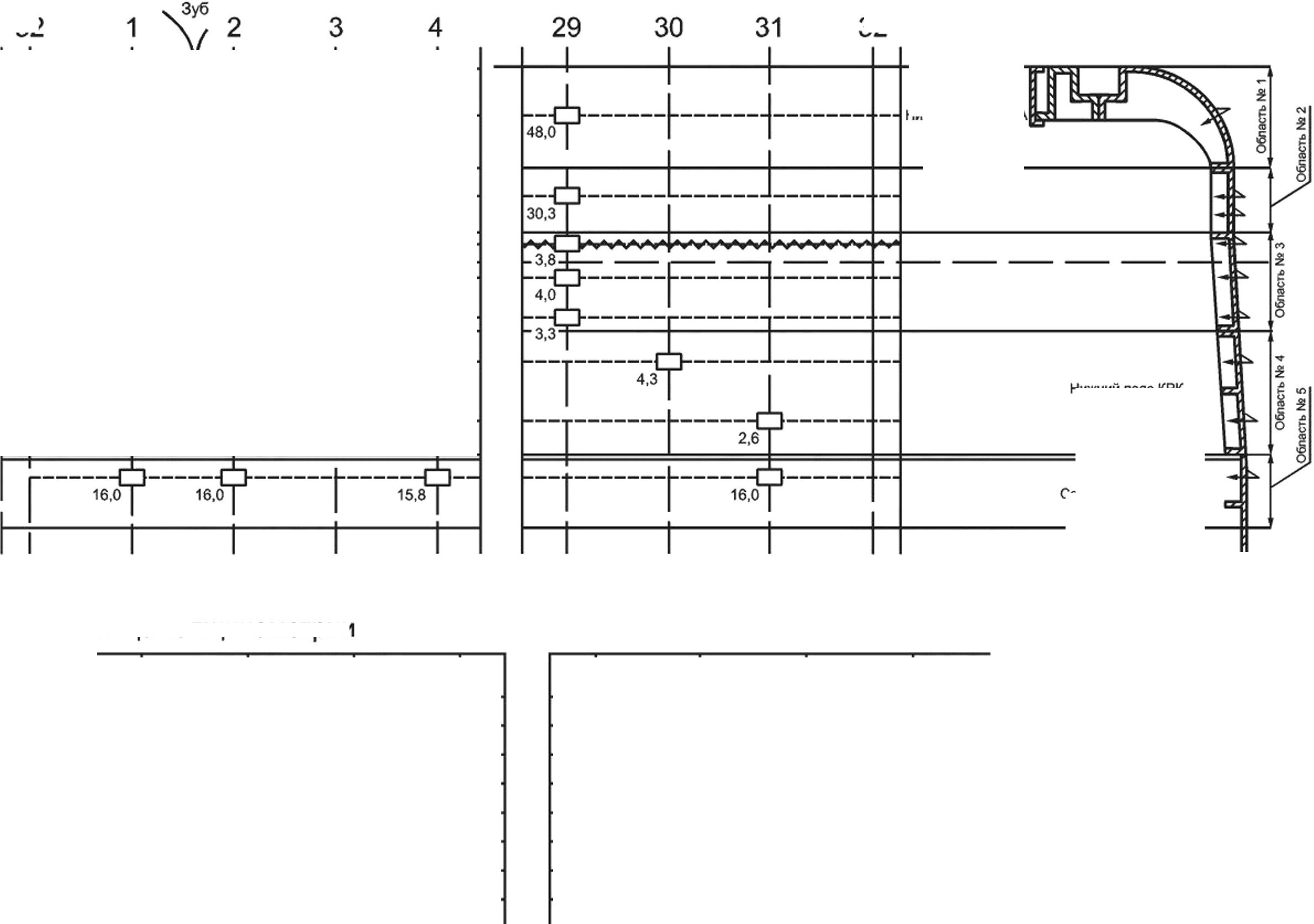
—.А— 38,0 | | — | - | ||||
20,3 | | — | — | ||||
--31 | --2.5 f--- | |||||
4,3 2X5 | I 36 | ц 33 ---Г UL" 2,9 | ]------- | — |
Таблица толщинометрии
№ дефекта | 32 | 1 | 2 | 3 | 4 |
1 | 38.0 | ||||
2 | 20,3 | ||||
Зв | 3,1 | 2.5 | |||
зн | 3.0 | ||||
3 | 2.3 | 2.3 | 2.3 | ||
4, | 4.3 | 3,3 | |||
42 | 2,6 | 2.9 | |||
5 | 16.0 | 16,0 | 15.8 | ||
Нижнее кольцо НА
Камера рабочего колеса
Нижнии пояс КРК
Сопрягающий пояс
29 | 30 | 31 | 32 | № трассы замера толщины металла | Примечание |
1-трасса НКНА | |||||
2-трасса верхнего пояса КРК | |||||
Зв-трасса КРК выше оси разворота лопастей | |||||
Зн-трасса КРК ниже оси РЛ | |||||
3-трасса верхнего пояса КРК | |||||
4,-трасса верхнего пояса КРК | |||||
42-трасса нижнего пояса КРК | |||||
5-трасса сопрягающего пояса | |||||
- вырыв наплавки от основного металла обечайки;
- полости между основным металлом обечайки и штрабным бетоном;
- вырыв обечайки от штрабного бетона;
- трещина в обечайке;
- трасса измерения толщины металла;
□ - точка замера толщины металла
зо.з
Примечания:
- на формуляре все размеры указаны в мм;
- в таблице толщины металла указаны в мм;
- в областях, где были выявлены пустоты или отслоение облицовки, толщина металла измерялась выборочно и указана на самом формуляре;
- развертка схематически принята цилиндрической;
- нумерация лопаток НА
принята по номерам в шахте турбины
Схематический план КРК по оси разворота лопастей
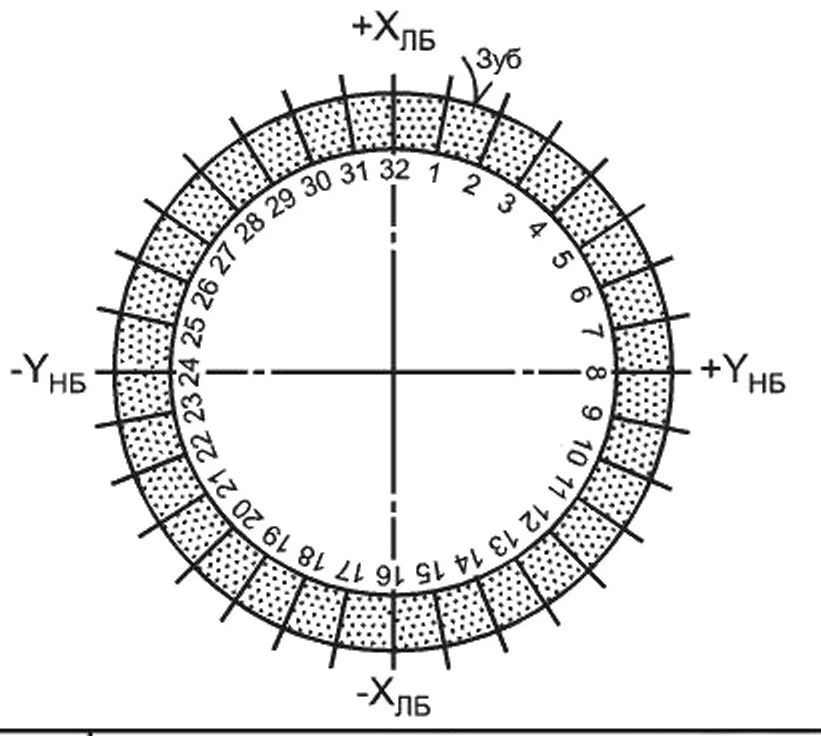
Дата | ||
— | Наменование станции | |
Замерил | Номер турбины Отчетная документация Станц. Заводск. | |
Замерил | диагностики металла НКНА, | |
КРК, СП агрегата № | ||
Проверил | ||
Формуляр состояния металла |
Рисунок В.4.10 — Формуляр толщинометрии металла КРК и примыкающих зон
Формуляр кавитационных повреждений металла камеры рабочего колеса и примыкающих зон
Условные обозначения
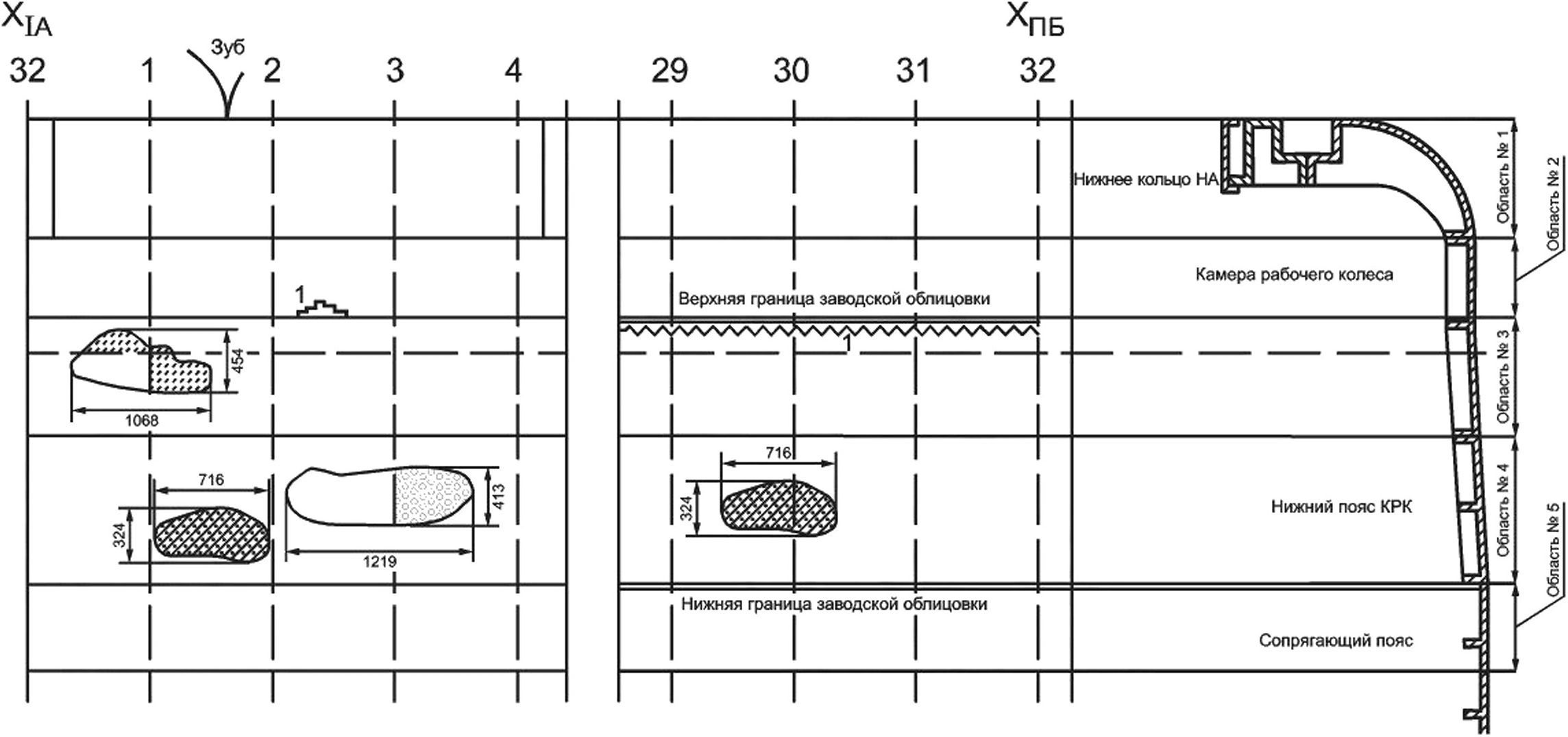
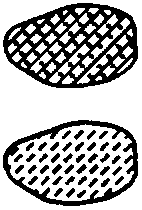
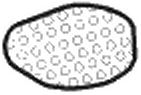
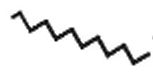
Таблица толщинометрии
№ дефекта | 32 | 1 | 2 | 3 | 4 |
1 | 454x1068-330289 | Длина 672 мм | |||
2 | 324x716-171065 | 413x1219-387 | |||
3 | |||||
4 | |||||
5 | |||||
6 | |||||
7 | |||||
8 | |||||
9 | |||||
10 |
29 | 30 | 31 | 32 | № повреждения | Примечание |
324x716-171066 | 1 | ||||
2 | |||||
3 | |||||
4 | |||||
5 | |||||
6 | |||||
местная равномерная кавитационная эрозия металла;
язвенная, точечная кавитационная эрозия металла;
кавитационные каверны;
- щелевая кавитация в металле
Примечания:
- в таблице повреждений указывается ширина, длина и приблизительная площадь повреждений в мм, мм2;
- развертка схематически принята цилиндрической;
- нумерация лопаток НА
принята по номерам в шахте турбины
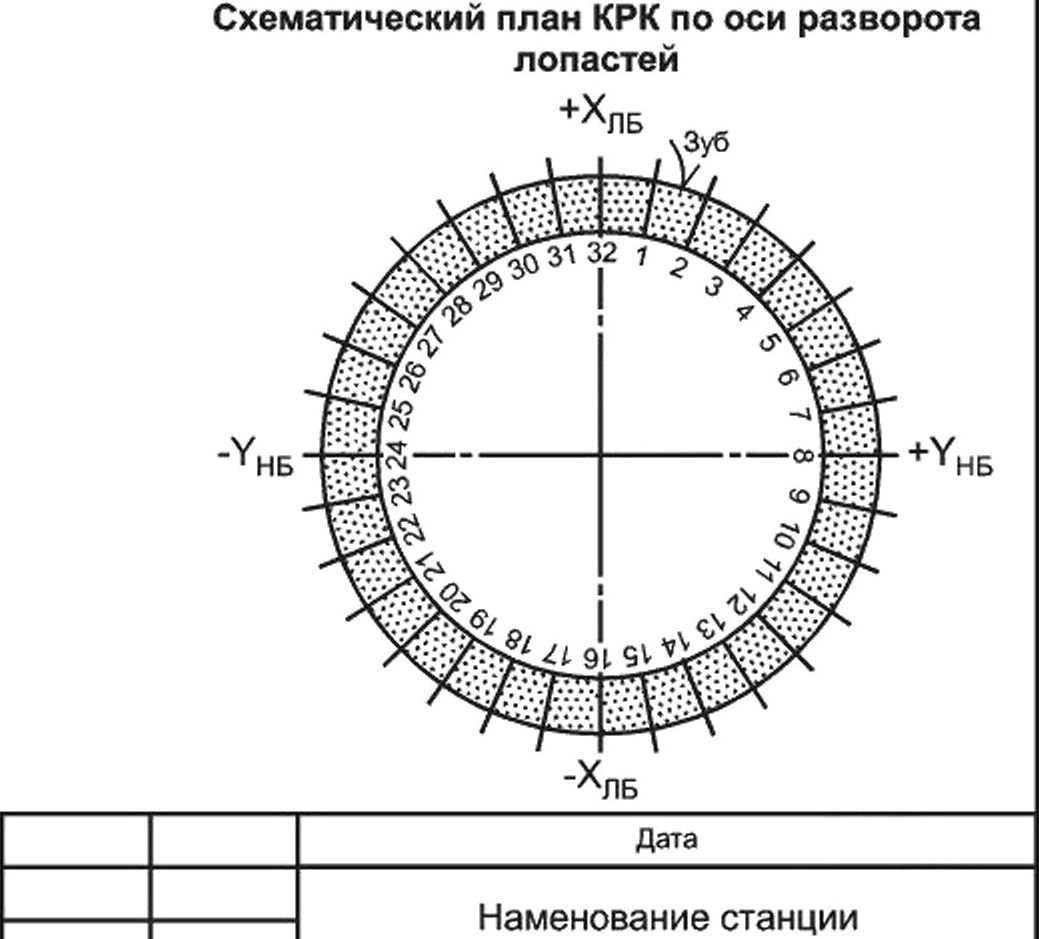
Замерил | Отчетная документация диагностики металла НКНА, | Номер турбины | Лист | ||
Станц. | Заводск. | ||||
Замерил | |||||
КРК, СП агрегата № | |||||
Проверил | |||||
Формуляр состояния металла |
Рисунок В.4.11 — Формуляр кавитационных повреждений металла КРК и примыкающих зон
ГОСТ Р 55260.3.2—2023
ГОСТ Р 55260.3.2—2023
В.5.6 Инструкция по проведению гидравлических испытаний КРК
В.5.6.1 Общие положения
Технологические оборудование, оснастка и приборы, применяемые при гидравлических испытаниях КРК, должны быть аттестованы и допущены к эксплуатации в соответствии с ГОСТ 12.2.003.
В.5.6.2 Подготовка КРК для проведения работ по гидравлическим испытаниям облицовки КРК
Местоположение заоблицовочных полостей, подлежащих заполнению жидкостью, определяется по результатам предварительного обследования КРК (простукиванием, неразрушающими методами ультразвукового контроля и т. п.) и отмечается мелом на поверхности облицовки, а также фиксируется в формуляре состояния закладных частей ГА.
В пределах оконтуренной пустоты в облицовке высверливаются дренажные отверстия. На каждую оконтуренную полость должно быть не менее двух диагонально расположенных отверстий: в нижней и в верхней частях полости (см. рисунок В.4.12).
Дренажные отверстия оборудуют резьбовыми штуцерами внутренним диаметром от 15 до 25 мм.
Для обеспечения возможности герметизации дренажных отверстий на различных стадиях проведения гидравлических испытаний КРК и ремонтно-восстановительных работ, изготавливается соответствующее количество резьбовых пробок (см. рисунок В.4.13).
В.5.6.3 Оборудование для проведения работ по гидравлическим испытаниям облицовки КРК
Для проведения работ по гидравлическим испытаниям облицовки КРК используется следующее (или аналогичное) оборудование:
- центробежный насос, обеспечивающий напор в диапазоне от 15 до 40 м водяного столба и расход в диапазоне от 1,5 до 6,0 м3/час (для обеспечения возможности использования этого же оборудования при проведении операций очистки заоблицовочных полостей рекомендуется использовать насосы, предназначенные для работы с химически активными жидкостями — маркировки типа КС, П);
- сливной бак (буферная емкость) с минимальным объемом от 70 до 80 л;
- шланги с внутренним диаметром от 20 до 25 мм, выполненные из материала, пригодного для работы под давлением, создаваемым используемым насосом при его работе на закрытую задвижку;
- задвижки Ду25 (шаровые или конусные краны) для установки на нагнетательной и сливной магистралях;
- средства двусторонней связи (телефоны, радиосвязь).
В.5.6.4 Порядок проведения работ по гидравлическим испытаниям КРК
В.5.6.4.1 Устанавливают насосную установку и сливной бак (буферную емкость). Рекомендуется установка на отметке входа в шахту турбины.
В.5.6.4.2 С помощью нагнетательного насоса по напорной магистрали подают в заоблицовочную полость воду, которая по сливной магистрали отбирается в буферную емкость (см. рисунок В.4.14). В случае выявления гидравлической связи занапоренной полости с соседними полостями (см. рисунок В.4.12), сообщающиеся отверстия и пустоты отмечают в формуляре состояния закладных частей ГА. Для обеспечения возможности одновременного заполнения водой (занапоривания) гидравлически связанных пустот, пустоты объединяют с помощью установки переходных шлангов или (и) заглушек — окончательное решение о схеме соединения гидравлически связанных пустот принимают на основании фактических данных об их геометрических размерах и местоположении.
В.5.6.4.3 Выявленные в результате гидравлического испытания трещины и свищи в металле облицовки подлежат качественной разделке и заварке электродной массой. После проведения сварочных работ гидравлические испытания должны быть повторены для проверки качества сварки и отсутствия незафиксированных ранее дефектов.
В.5.6.4.4 На основании гидравлических испытаний КРК делают оценки объемов и площади поверхностей заоблицовочных полостей, необходимые для расчета объемов расходных материалов на последующих стадиях производства ремонтно-восстановительных работ.
132
ГОСТ Р 55260.3.2—2023
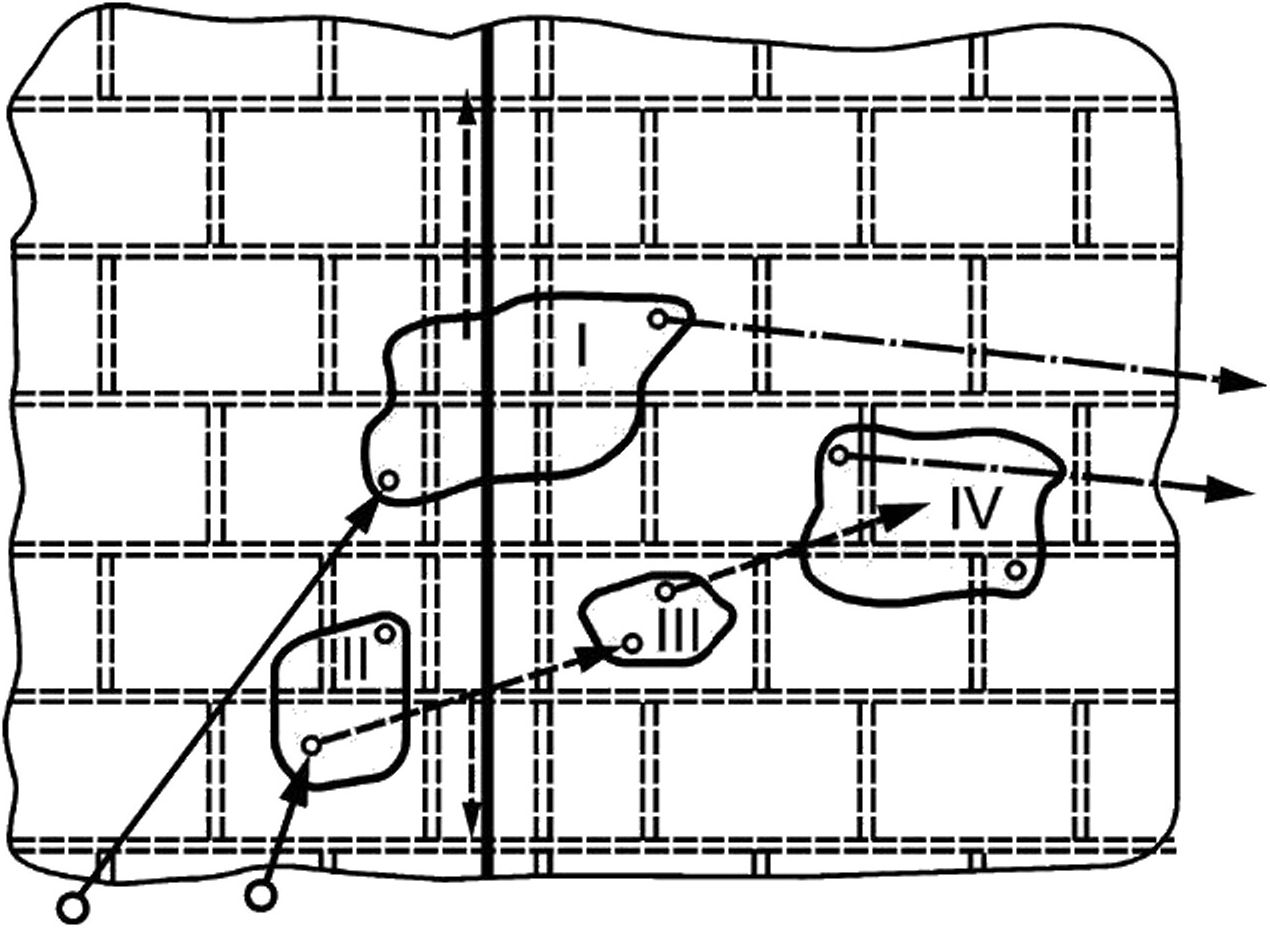
г ] — фрагмент металлической облицовки;
====== — ребра жесткости;
^2^2^ — зоны и номера пустот;
о — дренажное отверстие;
^_^_ — стык секторов КРК;
----► — гидравлическая связь между заоблицовочными полостями или заоблицовочной полостью и стыком секторов КРК;
О—►« — линия подачи воды от насосной установки;
о-----► — линия отвода (слива) воды в буферную емкость
Рисунок В.4.12— Исполнительная схема выявления гидравлической связи
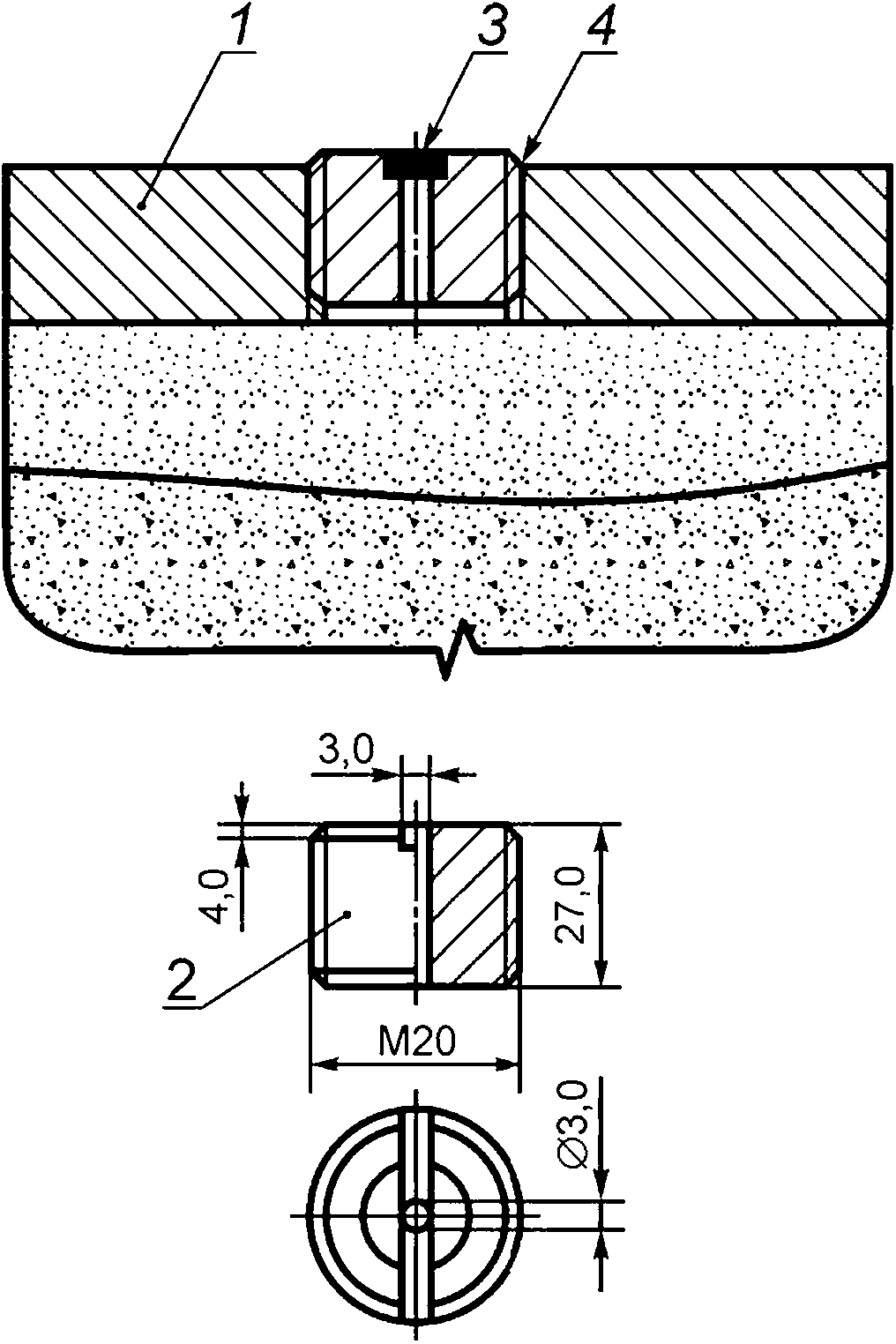
1 — металлическая облицовка; 2 — пробка; 3 — заделка паза и центрального отверстия пробки сваркой; 4 — сварка по контуру отверстия с последующей зачисткой сварного шва
Рисунок В.4.13 — Ликвидация дренажных отверстий в облицовке
133
ГОСТ Р 55260.3.2—2023
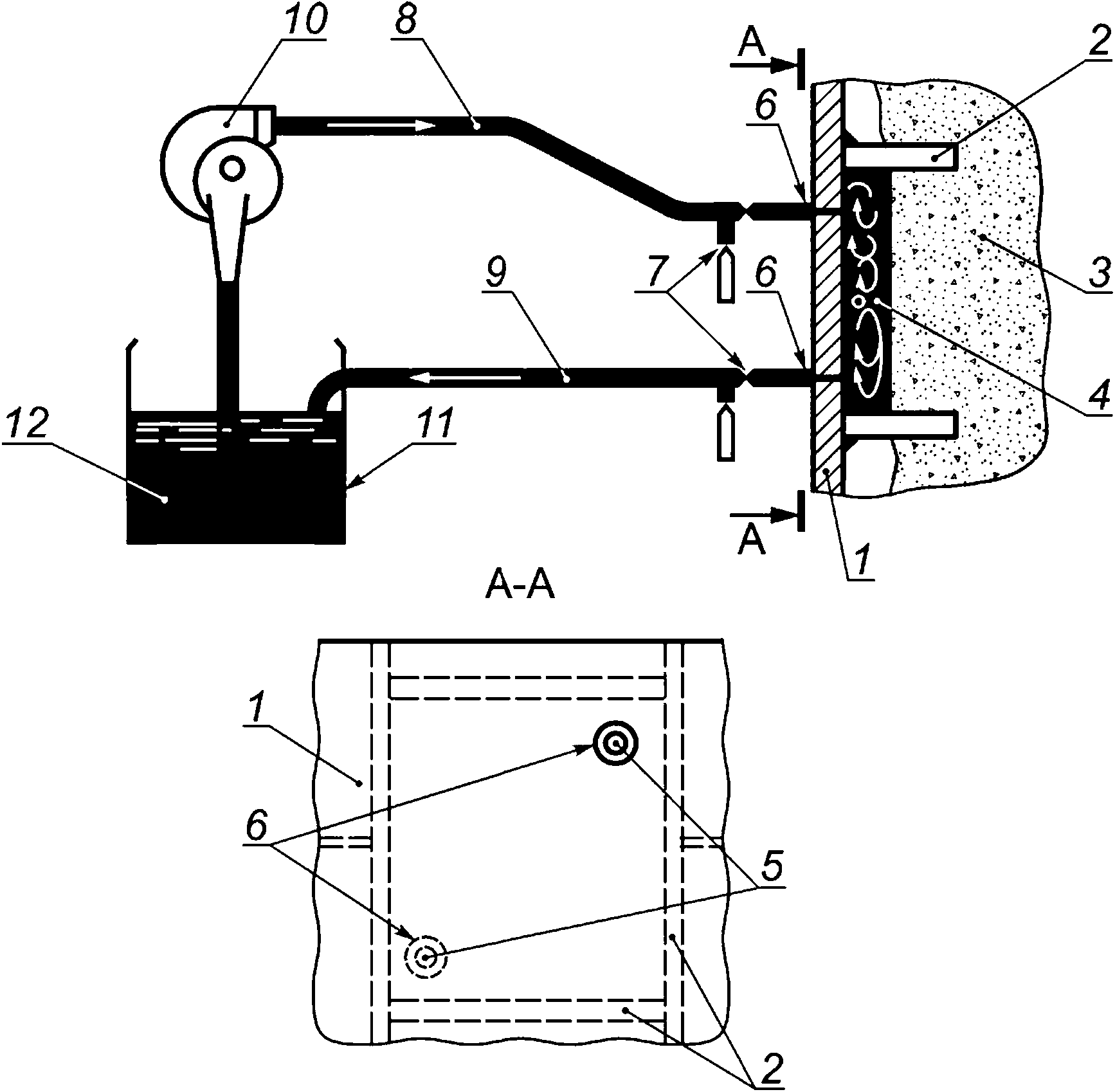
1 — облицовка; 2 — ребра жесткости; 3 — бетон; 4 — заоблицовочная пустота; 5 — дренажное отверстие; 6 — штуцер; 7 — кран-задвижка; 8 — напорный шланг; 9 — сливной шланг; 10 — насос; 11 — буферная емкость; 12 — вода
Рисунок В.4.14 — Проведение гидравлических испытаний КРК
134
ГОСТ Р 55260.3.2—2023
Приложение Г (справочное)
Основные технические данные по ГЭС, гидротурбинному и гидрогенераторному оборудованию
Таблица Г.1
Наименование показателя | Значение |
1 Характеристика ГЭС: состав гидросооружений, длина напорного фронта, расчетные и наиболее характерные напоры, объем водохранилища | — |
2 Установленная мощность ГЭС, МВт | — |
3 Количество гидроагрегатов | — |
4 Первичная схема электрических соединений | — |
5 Характерный режим работы (пиковый, базовый), его изменение во времени | — |
6 Единичная мощность гидроагрегата, МВт | — |
7 Типоразмер турбины | — |
8 Завод — изготовитель турбины | — |
9 Год выпуска турбины | — |
10 Напоры: | — |
- минимальный, м; | — |
- расчетный, м; | — |
- максимальный, м | — |
11 Расход воды через турбину при расчетном напоре, м/с | — |
12 Мощность турбины при расчетном напоре, МВт | — |
13 Требуемая высота отсасывания турбины при расчетном напоре и максимальной нагрузке, м | — |
14 Число лопастей рабочего колеса | — |
15 Число лопаток направляющего аппарата | — |
16 Количество и тип сервомоторов направляющего аппарата | — |
17 Тип направляющего подшипника турбины | — |
18 Тип гидрогенератора | — |
19 Завод — изготовитель гидрогенератора | — |
20 Год выпуска гидрогенератора | — |
21 Номинальная частота вращения ротора, об/мин | — |
22 Напряжение статора, кВ | — |
23 Ток ротора, А | — |
24 Коэффициент мощности | — |
25 Диаметр расточки статора, мм, количество секторов, шт | — |
26 Тип обмотки статора | — |
27 Тип изоляции обмотки статора | — |
28 Число полюсов ротора | — |
135
ГОСТ Р 55260.3.2—2023
Окончание таблицы Г. 1
Наименование показателя | Значение |
29 Тип изоляции обмоток ротора | — |
30 Тип системы охлаждения статора и ротора | — |
31 Тип подпятника (краткое описание) | — |
32 Максимальная нагрузка на подпятник, т | — |
33 Удельная нагрузка на подпятник, МПа | — |
34 Тип подшипников гидрогенератора (краткое описание) | — |
35 Тип системы возбуждения | — |
36 Тип РЧВ | — |
37 Типоразмер МНУ | — |
38 Гарантии регулирования: | — |
- заброс оборотов при сбросе полной нагрузки; | — |
- заброс давления в спиральной камере при сбросе полной нагрузки; | — |
- вакуум в отсасывающей трубе | — |
39 Наличие АСУ ТП | — |
136
ГОСТ Р 55260.3.2—2023
Приложение Д (справочное)
Методики испытания системы регулирования гидротурбин
Д.1 Общие положения
Д.1.1 Функциональные требования к системе регулирования гидротурбины устанавливают на основании требований завода — изготовителя гидротурбины в соответствии с руководством по эксплуатации.
Функциональные требования должны содержать сведения о номинальных, предупредительных и аварийных величинах всех контролируемых технологических параметров и требуемых действиях при их достижении.
Д.1.2 Требования к системе регулирования гидротурбины, обусловленные необходимостью участия гидроагрегатов в автоматическом регулировании режимов энергосистемы, устанавливают в соответствии с ГОСТ Р 55890, ГОСТ Р 56969.
Д.2 Объем испытаний
Д.2.1 При испытаниях системы регулирования независимо от типа регулятора должны быть получены нижеприведенные характеристики.
Д.2.1.1 Под нагрузкой:
- зависимости мощности и угла разворота лопастей РК от открытия НА при действующем напоре;
- цикл работы насосов МНУ при работе на автоматическом и/или ручном управлении в трех-четырех точках эксплуатационной характеристики турбины.
Д.2.1.2 На холостом ходу:
- устойчивость и быстродействие системы регулирования;
- быстродействие (ступенчатое изменение уставки частоты на 1 Гц должно отрабатываться за 20 с при одном перерегулировании до 0,2 Гц);
- соответствие действительной уставки срабатывания защиты от разгона с действием этой защиты на остановку агрегата.
Д.2.1.3 При опорожненной спиральной камере:
- величина люфтов в рычажной или тросовой обратной связи;
- перестановочные усилия сервомоторов НА и РК;
- протечки масла в системе регулирования раздельно по трактам управления сервомоторами НА и РК, а также через аппаратуру МНУ.
Д.2.2 Для ЭГР мертвая зона и среднее положение выходного штока ЭГП должны определяться по статической характеристике и результатам измерения омического сопротивления обмоток катушек ЭГП.
Статическая характеристика зависимости перемещения тела главного золотника от тока разбаланса ЭГП при прямом и обратном ходе должна быть линейной без петли гистерезиса.
Работоспособность ЭГП должна проверяться переводом рукоятки в положение «ручное» — «автомат» и проверкой наличия «оживления».
Д.2.3 Для гидромеханического регулятора частоты вращения
Д.2.3.1 Определению подлежат следующие характеристики регулятора:
- статическая характеристика маятника;
- величина биения штифта маятника;
- соответствие шкал указателей открытия и разворота лопастей действительным значениям;
- время открытия и закрытия НА и лопастей РК;
- величина люфтов в рычажных передачах от сервомотора НА до стакана катаракта;
- время возврата поршня катаракта к среднему положению и значение невозврата;
- величина невозврата в среднее положение главных золотников сервомоторов НА и лопастей РК по окончании переходного процесса регулирования.
Д.2.3.2 Если иное не оговорено в документации завода-изготовителя, должны быть выполнены следующие условия:
- невозврат поршня катаракта в среднее положение (не должен превышать 0,01 мм);
- наличие люфта в приводе пендель-генератора не допускается;
- осевое биение штифта маятника, приведенное к главному золотнику, не должно превышать величину перекрытий (0,35—0,5 мм на строну);
- рукоятки редукторов должны перемещаться без рывков и заеданий;
- время открытия и закрытия НА и лопастей РК, а также начало зоны демпфирования сервомотора НА и время закрытия в зоне демпфирования должны соответствовать требованиям конструкторской документации;
- статическая характеристика зависимости перемещения тела главного золотника от перемещения маятникового рычага при прямом и обратном ходе должна быть линейной без петли гистерезиса;
- положение ролика на кулачке комбинатора должно соответствовать действующему открытию НА и напору;
137
ГОСТ Р 55260.3.2—2023
- время перемещения механизмов изменения мощности и ограничения открытия должно соответствовать паспортным данным;
- время перемещения МИЧО и МОО НА, а также величина крайних и промежуточных значений должны соответствовать паспортным данным;
- последовательность действий механизмов при выполнении операций автоматического пуска агрегата, автоматической остановки, перевода в режим СК, синхронизации и работе в сети, включении в ГРАМ должна соответствовать требованиям конструкторской документации;
- значение люфтов в обратных связях от сервомоторов НА и РК не должны превышать 0,5 %.
Д.2.4 Испытания микропроцессорных электрогидравлических систем регулирования проводятся по методикам завода-изготовителя.
Д.З Испытания исполнительных органов системы регулирования гидротурбин
Д.3.1 Снятие зависимости открытия НА от хода его сервомотора
Д.З.1.1 Испытания необходимо проводить при остановленном агрегате и осушенной спиральной камере турбины.
Перемещение сервомотора следует производить ограничителем открытия ступенями через 10 % от полного закрытия до полного открытия, а затем в обратном направлении. При этом следует измерять положение штока сервомотора и просвет между тремя парами лопаток НА, расположенными через 120° друг от друга в трех точках по высоте лопатки.
По измеренным данным строится зависимость хода НА (средняя из измерений в указанных трех точках) от положения сервомотора.
Д.З.1.2 Из полученной таким образом кривой (см. рисунок Д.3.1) устанавливается характер зависимости и значение мертвого хода в передаче от сервомотора к направляющему аппарату в процентах полного хода сервомотора НА.
Погрешность измерения хода сервомотора ±0,5 мм, погрешность измерения открытия лопаток НА ±0,5 мм.
Допустимый мертвый ход в направляющем аппарате /НА 0,5 % его полного хода.
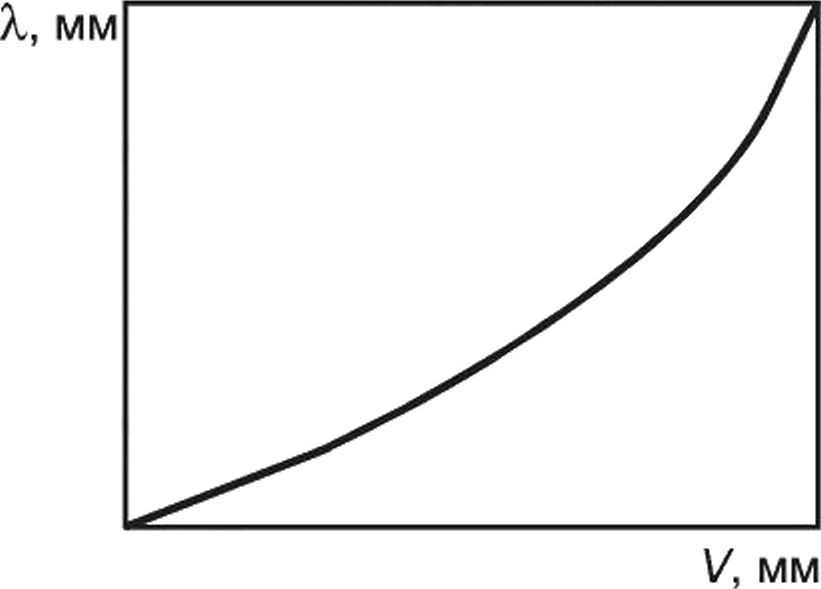
Рисунок Д.3.1 — Кривая зависимости открытия НА от хода штока сервомотора
Д.3.2 Снятие зависимости угла разворота лопастей РК от хода его сервомотора
Д.З.2.1 Испытания необходимо проводить при остановленном агрегате и осушенной спиральной камере.
На втулке РК следует укрепить временную шкалу, отградуированную в градусах.
С помощью механизма ручного управления комбинатора следует произвести перемещение сервомотора РК ступенями через 10 % от полного закрытия до полного открытия, а затем в обратном направлении. При этом следует измерить положение штока сервомотора (по указателю положения лопастей на маслоприемнике) и угол разворота лопастей по временной шкале, установленной на втулке РК.
Д.З.2.2 По измеренным данным необходимо построить зависимость угла разворота лопастей от хода сервомотора лопастей.
Из полученной кривой можно установить характер зависимости и значение мертвого хода в передаче от сервомотора РК к лопастям.
Погрешности измерения хода сервомотора составляют ±0,5 мм, угла лопастей — 0,5.
Допустимый мертвый ход /^ < 1°.
Д.3.3 Проверка комбинаторной связи
Д.З.3.1 Проверку комбинаторной связи ПЛ-гидротурбин можно производить при работе ГА в энергосистеме. Проверка включает в себя определение комбинаторной зависимости, мертвой зоны и зоны неопределенности.
Для определения комбинаторной зависимости следует снять зависимость угла разворота лопастей РК от хода СНА при прямом и обратном ходах. Для этого ограничителем открытия в зоне действия комбинаторной связи надо изменить открытие НА ступенями 5 % — 7 % полного хода при движении его сначала в одном, а затем в другом направлении. При каждом установившемся состоянии системы регулирования произвести измерение открытия НА по шкале сервомотора (в мм) и угла разворота лопастей РК по шкале на маслоприемнике (в градусах), при
138
ГОСТ Р 55260.3.2—2023
достаточной точности штатной шкалы следует произвести дополнительно измерения по миллиметровой линейке. Для определения люфта в обратной связи следует также измерить положение груза обратной связи в колонке регулятора по миллиметровой линейке. Для каждого направления движения НА должно быть получено не менее десяти точек.
Д.3.3.2 По результатам измерений необходимо построить график комбинаторной зависимости и сравнить с заводской или оптимальной комбинаторной зависимостью, определенной в результате натурных испытаний. Нанесение на график точек прямого и обратного ходов позволяет выявить наличие петли гистерезиса.
Мертвую зону в комбинаторной связи следует определять при различных (например, четырех) значениях открытия НА. Для ее определения на золотник сервомотора РК установить индикатор перемещений частого типа. При медленном смещении НА ограничителем открытия в направлении закрытия необходимо наблюдать по индикатору за смещением золотника на закрытие. В момент страгивания поршня сервомотора РК (начинается возврат золотника к среднему положению) измерить значение открытия НА. Затем при медленном перемещении СНА на открытие измерять то открытие, при котором после смещения золотника на открытие начинается его возврат в среднее положение. Разность между двумя измеренными открытиями НА равна значению мертвой зоны. Опыт следует повторить несколько раз. За значение мертвой зоны следует принимать среднее из измеренных. Результат будет тем точнее, чем медленнее будет перемещаться НА. Перемещение следует производить небольшими ступенями с паузами между ними.
Д.3.3.3 Зона неопределенности установки лопастей РК численно равна сумме мертвой зоны и люфта в обратной связи, приведенных к углу разворота лопастей по комбинаторной зависимости. При силах трения, превышающих гидравлические усилия, действующие на лопасти, зона неопределенности может проявляться в статическом отклонении угла разворота лопастей относительно найденной комбинаторной зависимости в пределах зоны.
В противном случае отклонения могут возникать при медленных колебаниях разворота лопастей при неизменном открытии НА.
Д.3.4 Определение перестановочных усилий на сервомоторах
Д.3.4.1 Определение значения перестановочных усилий производится по измерению усилия на штоке сервомотора, которое определяется для одного сервомотора как произведение площади его поршня на перепад давлений в его полостях. При двух сервомоторах площади полостей соответственно суммируются.
В момент страгивания поршня сервомотора можно записать следующие равенства:
- при движении сервомотора в сторону открытия:
PSSno-p3oSn3 = FT+Fr; (Д.1)
- при движении сервомотора в сторону закрытия:
Рз^пз - Ро^по = ^т “ ^г, (Д-2)
где Pq, Рэ — давление в полостях соответственно открытия и закрытия сервомотора при движении сервомотора на открытие;
Ро > Рз — давление в полостях соответственно открытия и закрытия сервомотора при движении сервомотора на закрытие;
Sn0, ^пз — площадь поршня сервомотора соответственно полости открытия и закрытия;
Fr — гидродинамическая сила, направление действия принято в сторону закрытия;
FT — сила трения направлена встречно движению.
Из приведенных равенств следуют выражения для расчета сил трения и гидродинамического воздействия:
^г - 2^° + ^°)^п0 (р° + ^3)^пз)!
(Д-З)
^т - 2((^° ^°)^по “(рз “Рз)^пз j
(Д-4)
Д.3.4.2 Известны два способа измерения перестановочных усилий: страгивания и равномерного движения.
При измерении перестановочных усилий НА способом страгивания на ГА, работающем в энергосистеме, РЧВ необходимо перевести на ручное управление.
Начиная с полного закрытия сервомотор последовательно через 10 % следует устанавливать на определенное открытие. При каждом положении открытия НА следует производить медленное смещение ограничителя открытия в одну сторону и при этом необходимо наблюдать изменения давления в обеих полостях сервомотора.
139
ГОСТ Р 55260.3.2—2023
В момент резкого изменения давления в сторону, противоположную медленному изменению давления, фиксировать значения максимальных отклонений давления в каждой полости в момент времени, предшествовавший указанному толчку давления.
Затем опыт следует повторить при том же открытии НА, но при медленном перемещении ограничителя открытия — в противоположную сторону.
Положение сервомотора можно измерять по шкале указателя на колонке управления. Давление в полостях сервомотора необходимо измерять с помощью манометров класса точности не ниже 0,5.
При оформлении протоколов результатов измерений следуют указывать скорость изменения мощности (изменения открытия или закрытия НА), с которой проводись измерения. Повторные измерения должны выполняться и сравниваться с аналогичными параметрами.
Д.3.4.3 При определении перестановочных усилий на сервомоторе лопастей РК порядок испытаний тот же, что и для сервомотора НА, только управление лопастями осуществляется с помощью механизма ручного управления лопастей.
Д.3.4.4 Измерение перестановочных усилий регулирующих органов методом равномерного движения следует производить следующим образом. С помощью ограничителя открытия сервомотор медленно перемещают с постоянной скоростью, величина которой отражается в протоколе измерений. Время полного смещения сервомотора 1—2 мин. В процессе равномерного перемещения сервомотора через каждые 10 % хода необходимо фиксировать давление в обеих его полостях. Допустимая точность измерений такая же, как указывалось в первом способе.
Допускается проводить измерение при заполненной водой проточной части до уровня НБ при условии согласования этого способа измерений с заводом-изготовителем.
Д.3.4.5 На основании данных испытаний следует построить зависимость перестановочных усилий Fot положения сервомотора у (см. рисунок Д.3.2), по которой определить характер, направление и значения действующих усилий.
Д.3.4.6 При необходимости определения силы трения в регулирующем органе испытания следует проводить без гидродинамического усилия воды. Тогда перестановочные усилия следует определять при опорожненной от воды спиральной камере.
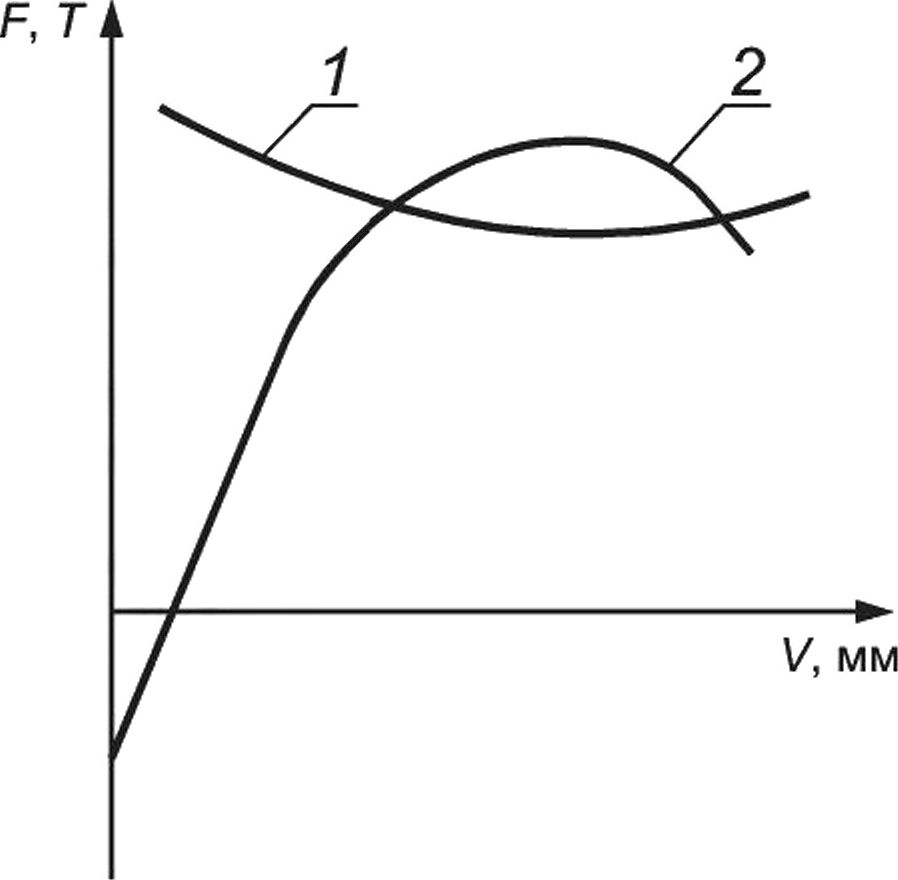
7 — усилие трения; 2 — гидравлическое усилие
Рисунок Д.3.2 — Примерный вид характеристики перестановочных усилий сервомотора НА
140
ГОСТ Р 55260.3.2—2023
Приложение Е (обязательное)
Методика контроля линии валов вертикальных гидроагрегатов
Е.1 Общие положения
Е.1.1 Принятые условные обозначения:
I, II ... XII — точки (риски), обозначающие разбивку окружности вала;
I—V, II—VI, III—VII, IV—VIII —диаметральные плоскости (при разбивке окружности на восемь частей), в которых подсчитываются биения отдельных компонентов линии вала (при разбивке окружности на двенадцать частей наименование плоскостей изменится: I—VII, II—VIII и т. д.);
/г— показания приборов, регистрирующих биение линии вала в зоне ГП (верхнего);
/д — показания приборов, регистрирующих биение по зеркальной поверхности диска ПП;
/ф — показания приборов, регистрирующих биение линии вала по фланцу вала;
/т — показания приборов, регистрирующих биение линии вала в зоне ТП;
△ф — отклонения фланца вала с учетом перемещения в ГП;
△т — отклонения шейки вала в зоне ТП с учетом перемещения в ГП;
бд — торцовое биение (размах) зеркальной поверхности диска ПП в четырех диаметральных плоскостях, где п — от I до IV;
5ф — радиальное биение (размах) фланца вала, где п — от I до IV;
бт — радиальное биение (размах) шейки вала в зоне ТП, где п — от I до IV;
5^/2; 5ф/2 — смещение бьющей точки от оси вращения;
(— расстояние между верхним генераторным подшипником и рассматриваемым сечением (^ и /1);
Д — диаметр расположения на зеркальной поверхности диска ПП, регистрирующего биение прибора;
Дд — диаметр диска ПП;
Докр б — диаметр окружности регулировочных болтов сегментов;
К— излом линии вала;
f— зазор (на диаметр) в ТП;
е — уклон, мм/м.
Е.1.2 Отклонения компонентов линии вала с учетом перемещения в ГП (в тех же точках):
△ф = /ф-'г- (Е-1)
△т = /г-/г- (Е.2)
Е.1.3 Биение (размах) компонентов в диаметральных плоскостях:
^д _ ^д л ^д (л+iv)’ (Е-3)
$Ф “ △фл △ф (n+iv)’ (Е-4)
5Т = ЛТЛ ~ АТ (л + IV)’ (Е-5)
где п — от I до IV (при разбивке окружности на двенадцать частей индекс n+(V изменится на n+V|, а п будет меняться от I до VI).
Е.2 Проверка общей линии валов методом поворота ротора агрегата на 360°.
Е.2.1 Методы поворота роторов ГА
В качестве основного способа поворота ротора ГА рекомендуется применять «крановый» способ с помощью троса, пропущенного через один или два блока и застопоренного за специальные приливы на спицах ротора генератора; в процессе поворота трос последовательно перестропляется. Для небольших ГА указанный трос может быть навит на специальный сварной барабан, прикрепленный к верхнему торцу генераторного вала (см. рисунок Е.2.1).
141
ГОСТ Р 55260.3.2—2023
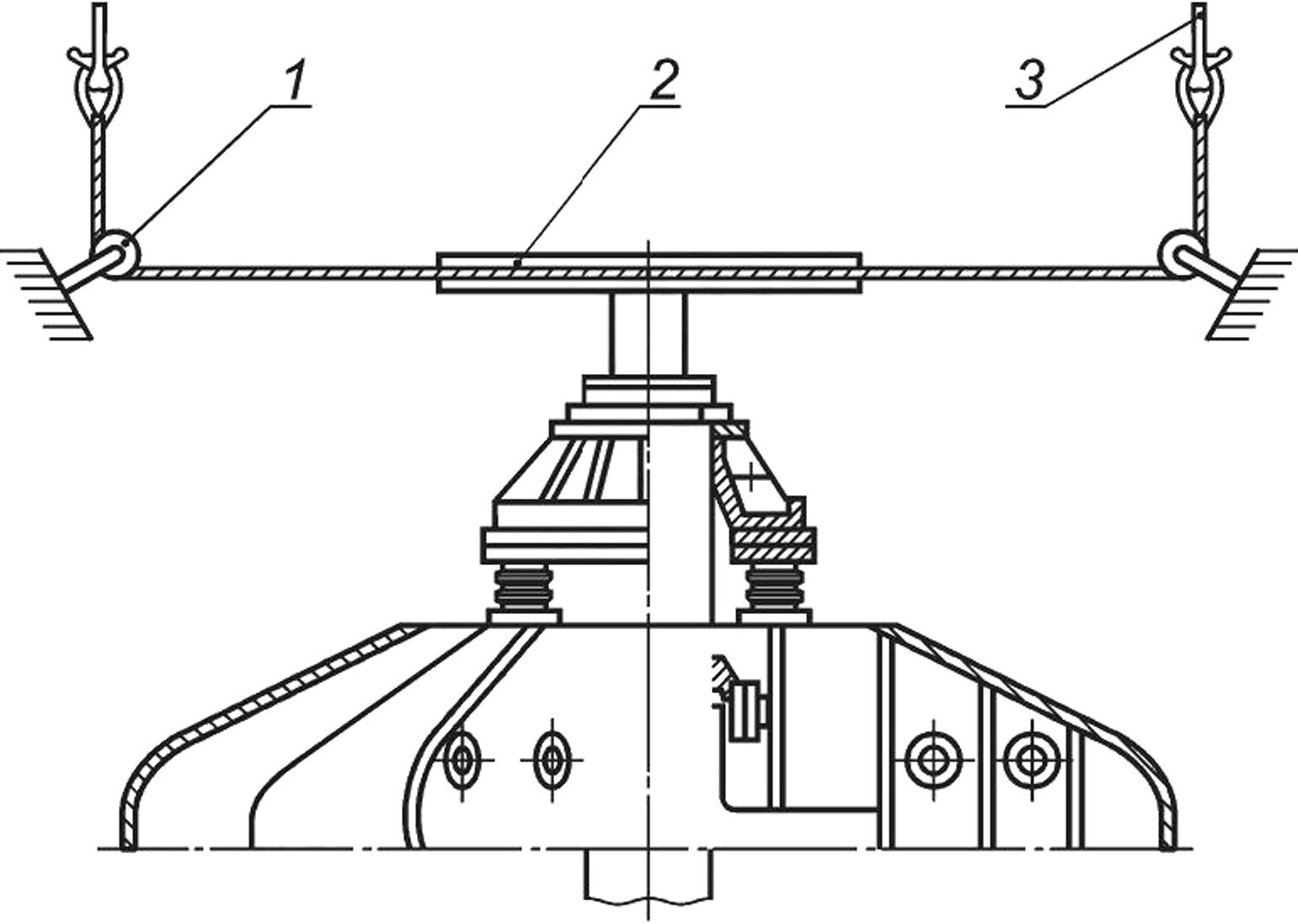
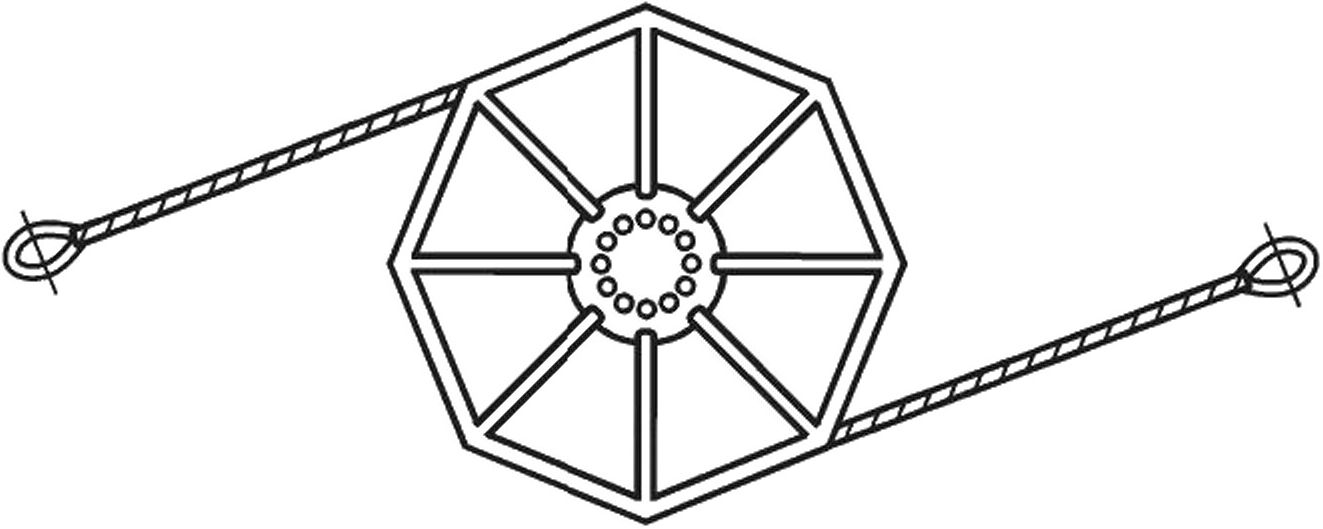
1 — блок; 2 — приспособление для поворота ротора; 3 — гак мостового крана Рисунок Е.2.1 — Схема поворота ротора агрегата
На рисунке Е.2.2 показан простейший способ поворота ротора краном. Недостаток его состоит в несимметричности прилагаемого усилия относительно центра ротора, приводящего к обязательному боковому смещению ротора в пределах зазора в направлявшем подшипнике. На рисунке Е.2.3 представлен симметричный способ поворота, свободный от указанных недостатков и предпочтительный для поворота агрегатов с подпятниками на гидравлической опоре.
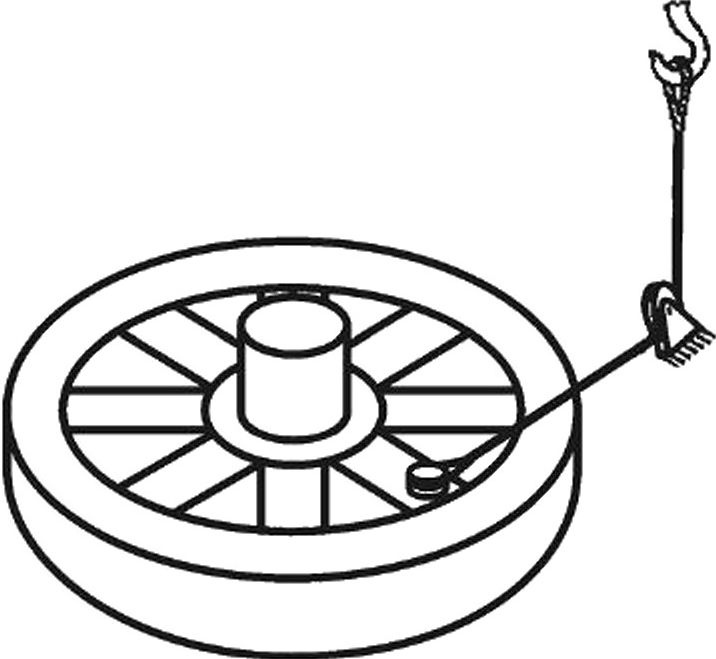
Рисунок Е.2.2 — Несимметричный способ поворота ротора ГА
142
ГОСТ Р 55260.3.2—2023
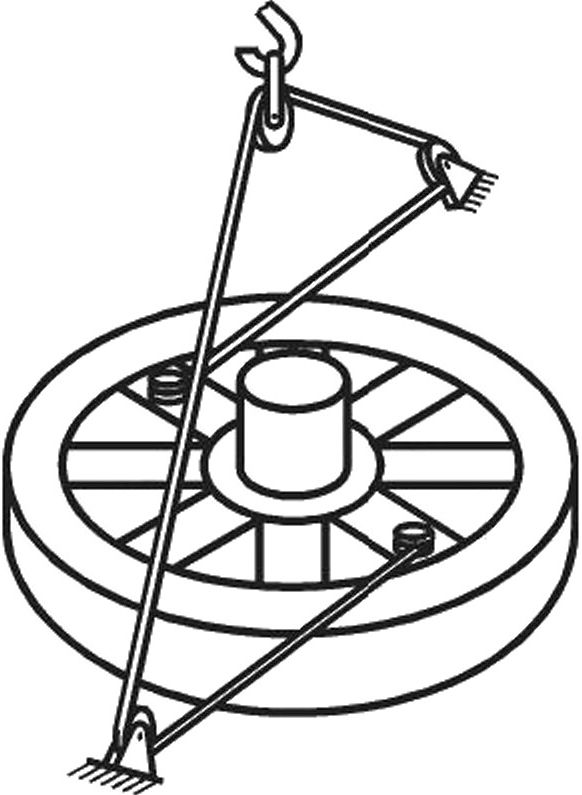
Рисунок Е.2.3 — Симметричный способ поворота ротора ГА
В качестве смазки сегментов баббитового направляющего подшипника и ПП следует применять:
- для легких роторов — свиное несоленое топленое сало;
- для тяжелых — бараний и говяжий жир, смесь свиного топленого сала с хорошо просеянным серебристым графитом.
При температуре воздуха в машинном зале выше 20 °C целесообразно ввести в животный жир порошок дисульфида молибдена (MO2S).
В качестве смазки ЭМП-сегментов ПП можно использовать турбинное масло. Для смазки сегментов перед каждым поворотом ГА поднимается на тормозах и в образовавшийся зазор между зеркальным диском ПП и поверхностью сегмента при помощи масленки подается турбинное масло.
Е.2.2 Проверку общей линии вала ГА следует проводить путем поворота ротора с одним установленным с минимально возможным зазором для поворота подшипником гидрогенератора, наиболее близко расположенным к подпятнику.
Наличие излома линии вала и величины биения контролируют приборами измерения линейных перемещений (бесконтактные приборы дистанционного измерения биения или индикаторы со штативами — по одному на каждое фланцевое соединение валов, шейку турбинного вала, зеркальную поверхность диска ПП (для агрегатов с подпятниками на гидравлической опоре), а также на каждую шейку генераторного вала).
Е.2.3 Окружность вала размечается на восемь равных частей (крупногабаритные роторы размечаются на двенадцать частей) с нанесением через каждые 45° рисок мелом или белой масляной краской на втулку ПП или непосредственно на ротор генератора.
Риски нумеруются от I до VIII против направления вращения ротора. При этом точка I ориентируется по какой-либо детали ротора (чаще всего по нумерованным полюсам). В этом случае угол поворота отсчитывается по числу полюсов ротора генератора, приходящихся на 1/8 часть окружности.
Е.2.4 Измерение и обработка полученных данных
Е.2.4.1 Произвести поворот ротора агрегата с остановами в каждой точке разметки по окружности, снятием показаний всех приборов, регистрирующих биение отдельных компонентов ротора, и записью результатов в карту измерения (см. Е.4.1). При каждом останове ротора обязательно следует ослабить натяжение тягового троса, чтобы не искажалось значение показаний индикаторов. Поворачивание ротора заканчивается при возвращении точки I в исходное положение.
Если показания приборов (индикаторов) вернулись к нулю или разница показаний прибора у шейки ТП (фланца генераторного вала) и прибора у ГП с установленным минимальным для поворота зазором не превышает погрешности измерений, считается, что замеры выполнены правильно. Если же разница показаний приборов превышает величину погрешности измерений, замеры необходимо повторить, так как приборы по какой-то причине сбились. Рекомендуемая величина допустимого отклонения 0,02 мм.
Е.2.4.2 Выявление неперпендикулярности зеркального диска подпятников на гидравлической опоре имеет своеобразные особенности: часть биения диска проявляется, как и для жестких подпятников, в виде радиального биения генераторного вала во фланце; остальная часть сглаживается гидравлическими опорами, что регистрируется установленным к диску дополнительным («торцовым») прибором (индикатором), расположенным в одной вертикальной плоскости с остальными приборами.
Влияние смещенной части веса ГА из-за неперпендикулярности и излома воспринимается дополнительным прибором как появление биения зеркального диска. Это дополнительное биение и следует учитывать в показаниях основных приборов. Общее торцовое биение зеркального диска (по его внешнему диаметру) определяется по формуле
’^fe*^!^ (е6)
при условии отсутствия волнистости рабочей поверхности диска.
143
ГОСТ Р 55260.3.2—2023
Характерным для ГА с ПП на гидравлической опоре следует признать несовпадение показаний приборов после поворота ротора на 360°, в частности невозврат к нулю биения в точке I. Указанное явление имеет место из-за перераспределения соотношения радиальных биений фланца вала и торцевых биений зеркального диска после первого протяжения краном. Поэтому при подсчетах биений отдельных компонентов линии вала по формуле Е.З следует оперировать данными по точке I в самом конце поворота, а не нулевыми в начале отсчета.
Е.2.4.3 Подсчет биений зеркального диска ПП и шейки турбинного вала производится не менее чем в четырех диаметральных плоскостях согласно зависимостям, приведенным в карте измерения (см. Е.4.1). Полное биение зеркальной поверхности диска не должно превышать 0,08 мм для однорядных, 0,12 мм — для двухрядных и гидравлических подпятников; биение шейки турбинного вала не должно превышать величины суммарного (на диаметр) зазора Г в ТП.
Пример подсчета биений представлен непосредственно в карте измерения в Е.4.
Допускаемые значения биения валов приведены в таблице Е.2.1.
Во всех случаях, независимо от допускаемого относительного биения вала, величина абсолютного биения вала у ТП при проверке поворотом ротора ГА на ПП не должна превышать 0,4 мм для ГА с частотой вращения до 250 об/мин и 0,3 мм для ГА с частотой вращения более 250 об/мин.
Таблица Е.2.1 —Допускаемые величины биения вала ГА при проверке поворотом ротора агрегата
Характер биения вала | Место замера | Допускаемое биение вала при частоте вращения гидроагрегата | |||
до 100 об/мин | до 250 об/мин | до 375 об/мин | до 500 об/мин | ||
Относительное биение вала гидротурбины1), мм/м | Шейка вала у ТП | 0,05 | 0,05 | 0,04 | 0,03 |
Относительное биение вала гидрогенератора2), мм/м | Фланец вала генератора | 0,03 | 0,03 | 0,02 | 0,015 |
Абсолютное биение надставки вала генератора, мм | Посадочная шейка для якоря возбудителя | 0,3 | 0,2 | 0,15 | 0,15 |
1) Отношение амплитуды биения вала у ТП к расстоянию между отметками измерения биения у ТП и ГП.
2) Отношение амплитуды биения вала у фланца вала генератора к расстоянию между отметками измерения биения у фланца вала генератора и ГП.
Е.2.4.4 В случае наличия выходящей за пределы допустимого хотя бы одной из указанных величин необходимо построить график состояния линии вала в четырех диаметральных плоскостях (см. рисунок Е.2.4).
График строится в двух масштабах: длина вала /— в уменьшенном, смещение вала от оси вращения 5/2 — в увеличенном.
У осевых линий вала сверху ставится наименование плоскости; положение цифр наименования плоскости относительно оси позволяет ориентировать на графике направление бьющей точки.
Продолжив геометрические линии вала генератора за фланцевые соединения (на графике — пунктиром), определяют величину излома К по расхождению осевых линий валов на длине fT - /ф турбинного вала.
Наибольшая величина Кмакс из всех плоскостей является расчетной для исправления излома в данном фланцевом соединении и указывает плоскость направления излома.
Пример проверки линии валов представлен непосредственно в карте в Е.4.1.
144
ГОСТ Р 55260.3.2—2023
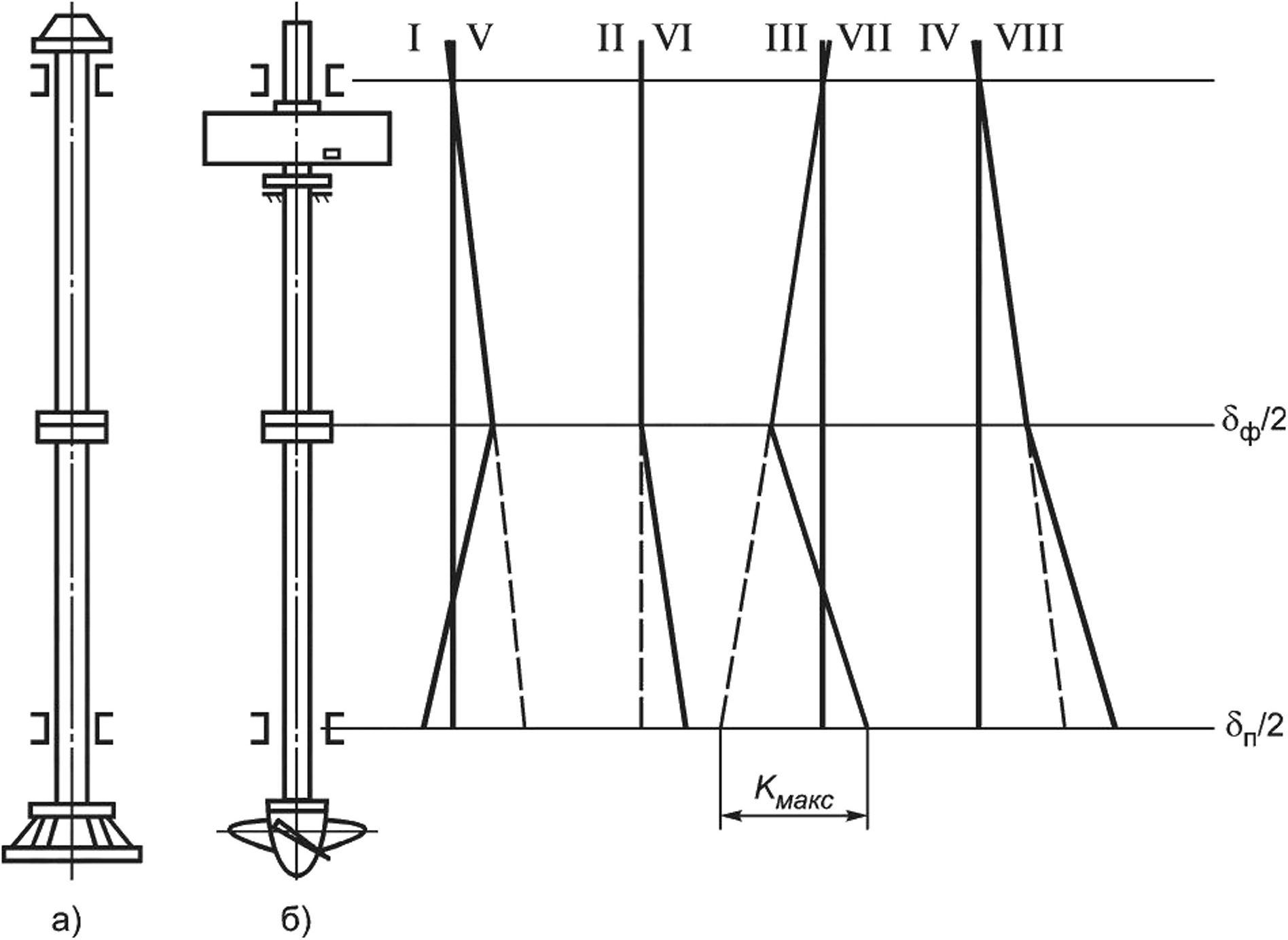
а) гидрогенератор подвесного типа; б) гидрогенератор зонтичного типа
Рисунок Е.2.4 — Пример построения графика состояния линии вала
Е.З Проверка уклона валов
Е.3.1 Проверка уклона валов производится непосредственно вслед за проверкой общей линии валов после устранения неперпендикулярности зеркального диска ПП и излома валов во фланцах.
Е.3.2 Методика проверки уклона вала
В настоящем стандарте не рассматривается широко известная в монтажной практике проверка по четырем струнам из-за ее значительной трудоемкости и невозможности применения к зонтичным ГА с опорой ПП на крышку турбины.
Е.3.2.1 Проверка с помощью микрометрического уровня
Е.3.2.1.1 Используются брусковые или рамные уровни с базой 200 или 250 мм и ценой деления не более 0,02 мм.
В случае проверки по нерабочей поверхности вала необходимо закрепить на генераторном валу (непосредственно над фланцевым соединением) три хомута с расстоянием 350 мм по высоте друг от друга для усреднения показаний по соответствующим сечениям 1,2,3 (см. эскиз карты в Е.4.2) и ослабления тем самым влияния дефектов профиля по высоте вала. Схема крепления с угольником необходима для брускового уровня. Рамный уровень возможно крепить при помощи хомутов непосредственно к валу.
При проверке по хорошо обработанной поверхности (шейке вала) достаточен один хомут.
Е.3.2.1.2 Для фиксации мест установки угольника с уровнем нанести на вал в зоне обозначенных сечений четыре вертикальные линии, соответствующие направлениям осей: +х (ПБ); -х (ЛБ); +у (ВБ); -у (НБ). Нанести также наименования указанных осей (см. рисунок Е.2.5).
Последующие измерения уклона по каждой из этих осей (т. е. с двух сторон вала) предусмотрены в целях устранения влияния погрешности изготовления прямого угла угольника.
145
ГОСТ Р 55260.3.2—2023
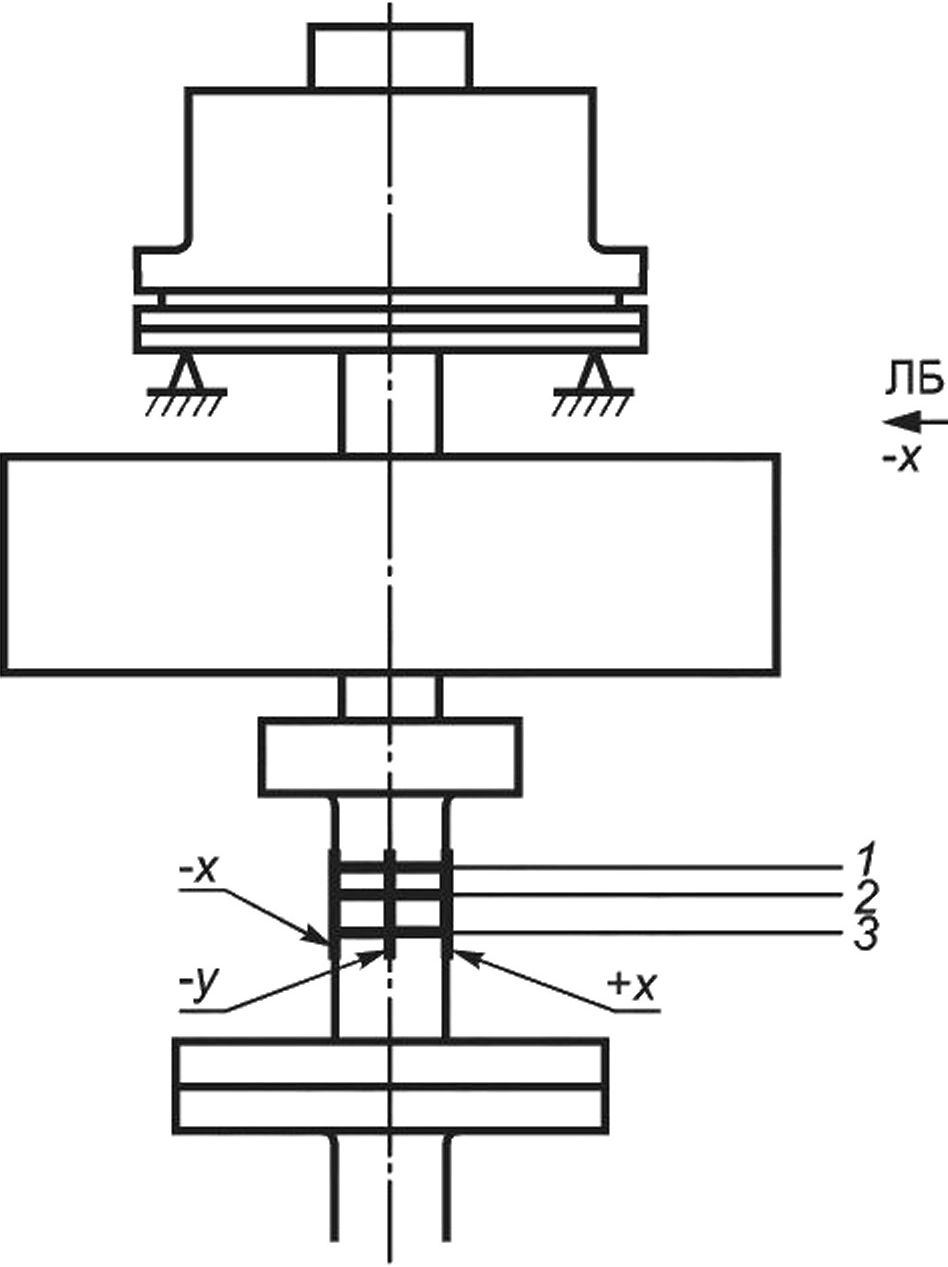
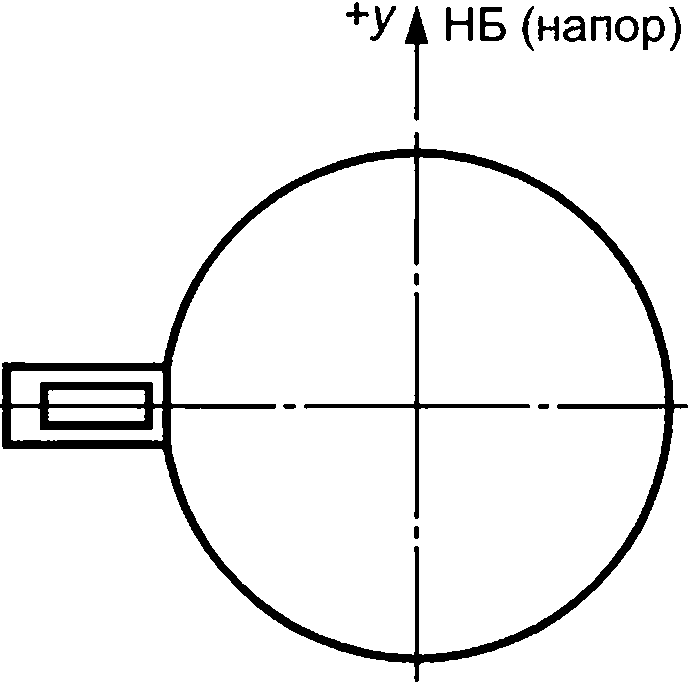
-у | ВБ (напор)
б
ПБ
+х
-х, +х, -у, +у— места закрепления угольника для установки уровня; а — разметка; б — сечение вала в месте установки уровня;
1, 2, 3 — места установки хомутов
Рисунок Е.2.5 — Разметка вала агрегата для проверки уклона уровнем
Е.3.2.1.3 Следует установить угольник (см. рисунок Е.2.6) поочередно на каждый хомут в места его пересечения с обозначенными вертикальными линиями, притягивая его каждый раз к валу стяжным тросиком или другим устройством (см. рисунок Е.2.7).
В каждом из фиксируемых положений необходимо установить на горизонтальную полку угольника брусковый микрометрический уровень, очертить карандашом его положение и произвести измерение уклона.
Следует развернуть уровень на 180°, оставив его на очерченной площадке, и повторить измерение.
Таким образом, всего должно быть проведено двадцать четыре измерения (из них восемь измерений — при проверке по шейке вала), результаты которых следует внести в таблицу карты (см. Е.4). Если результаты измерений в одном из сечений (по одному из хомутов) резко отличаются по значению и знаку от двух других сечений, то следует произвести повторный замер в каком-либо новом сечении.
Е.3.2.1.4 Подсчет уклона производится согласно руководящим указаниям карты измерения.
146
ГОСТ Р 55260.3.2—2023
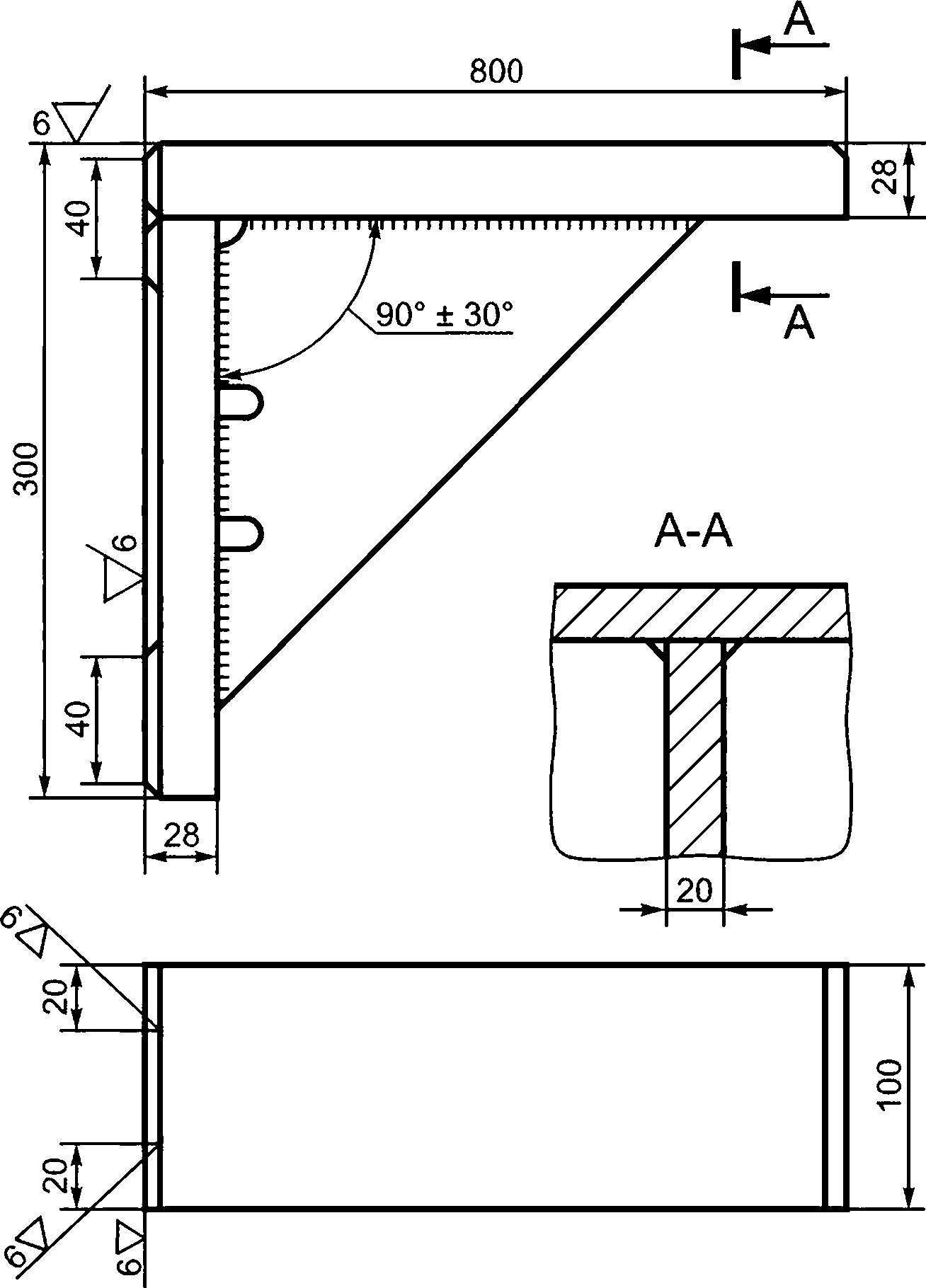
Рисунок Е.2.6 — Угольник для проверки линии валов с помощью брускового уровня
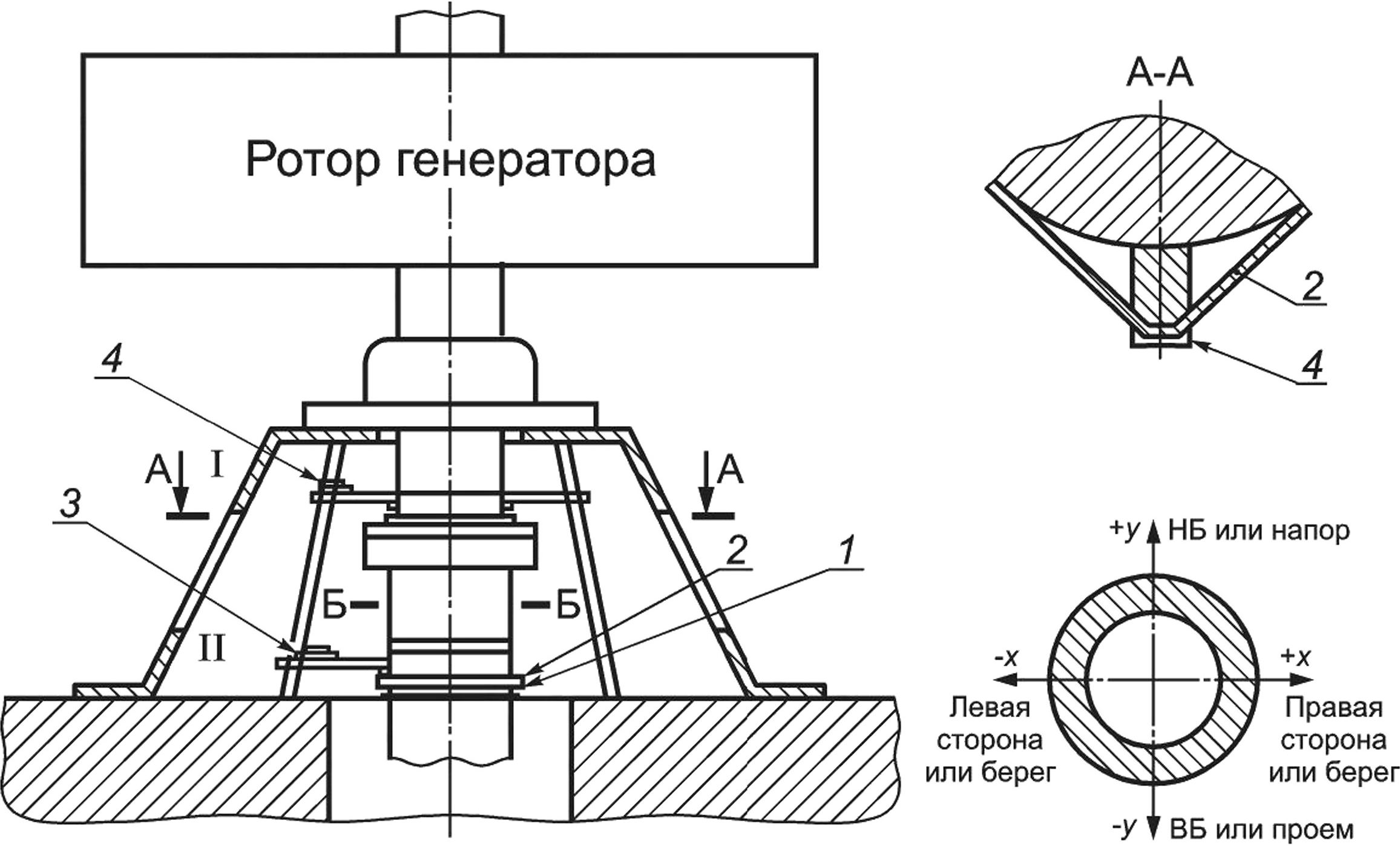
1 — хомут; 2 — стяжной тросик; 3 — уровень; 4 — угольник
Рисунок Е.2.7 — Установка уровня для проверки уклона вала
147
ГОСТ Р 55260.3.2—2023
Усреднение результата измерений 0° и 180° (среднее внутриосевое) проводят алгебраическим сложением показаний и делением суммы пополам. У среднего значения ставится знак большего по абсолютному значению показания.
Аналогичным образом рассчитывается усреднение показаний между положительными и отрицательными осями при получении осевых составляющих уклона ех и еу.
При проверке по нерабочим поверхностям производится усреднение по сечениям 1, 2, 3.
Подсчет завершается переводом результирующей величины уклона из делений шкалы в миллиметры на метр.
Е.3.2.1.5 Пример расчета уклона валов с помощью микрометрического уровня представлен непосредственно в карте измерения в Е.4.2.
Е.3.2.2 Проверка уклона при помощи высокоточного рамочного пузырькового уровня
Проворот вала с закрепленным на нем уровнем и роспуском подшипников позволяет избежать погрешностей, связанных с обработкой поверхности вала, с погрешностью самого уровня.
Е.3.2.2.1 При абсолютно свободном вале (при всех разжатых подшипниках и снятом уплотнении вала турбины) устанавливают на вал высокоточный рамочный уровень с ценой деления 0,02 мм/м при помощи двух хомутов. Установкой прокладок между уровнем и валом следует отрегулировать положение уровня так, чтобы пузырек находился посередине шкалы.
Е.3.2.2.2 Зажимают сегменты ГП и выполняют проворот вала ГА краном по четырем точкам, соответствующим направлению осей +х (ПБ); -х (ЛБ); +у (ВБ); -у (НБ).
В каждой точке выполняют измерение отклонения пузырька, с учетом направления его движения (от вала/к валу). Перед измерениями в каждой точке в обязательном порядке ослабляют натяжение троса и распускают зажатый ГП. После измерения сегменты подшипника опять поджимают к валу для проворота на следующую точку. При возврате на исходную точку контролируют возврат пузырька в исходное состояние.
Е.3.2.2.3 Выполняют расчет уклона вала по методике, приведенной в Е.4.
Е.4 Формуляры (карты контроля)
Примеры
1 Формуляр проверки общей линии валов методом поворота ротора агрегата на 360°.
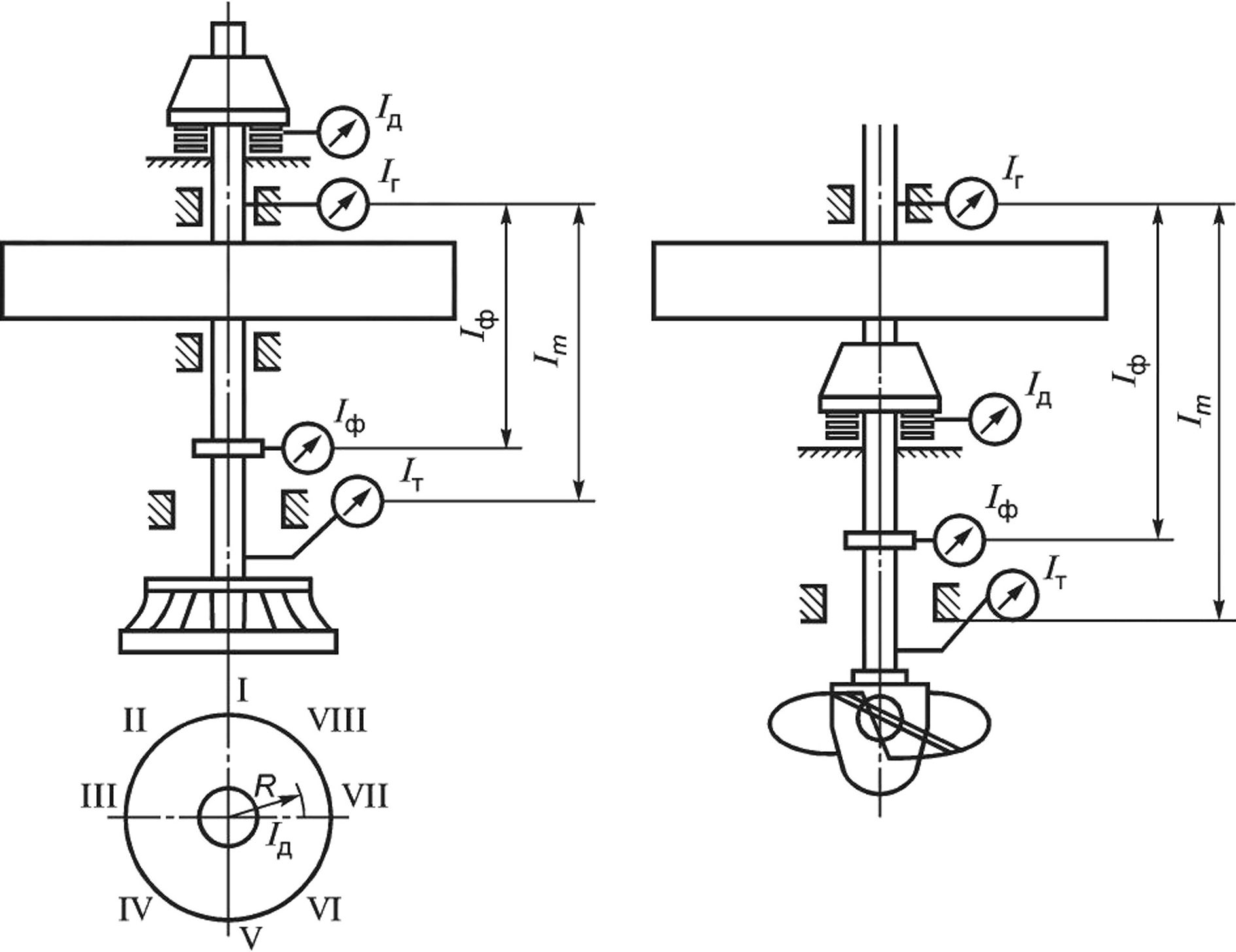
148
ГОСТ Р 55260.3.2—2023
Обозначение приборов и отклонений вала | Показания приборов, регистрирующих биение и подсчет отклонений в точках по окружности | ||||||||
1 | II | III | IV | V | VI | VII | VIII | 1 | |
1г | 0 | +0,02 | +0,015 | +0,010 | +0,010 | -0,005 | +0,012 | +0,028 | +0,03 |
1д* | 0 | -0,06 | -0,05 | 0,00 | +0,02 | +0,01 | +0,03 | +0,01 | -0,02 |
1Ф | 0 | -0,20 | -0,19 | -0,05 | -0,03 | +0,16 | +0,30 | 0,00 | -0,08 |
!т | 0 | -0,21 | -0,35 | +0,18 | +0,01 | -0,23 | -0,18 | -0,11 | +0,07 |
Отклонение шейки вала в зоне ТП Ат = 1т - 1г | 0 | -0,23 | -0,365 | +0,17 | 0,00 | -0,225 | -0,192 | -0,138 | +0,04 |
Отклонение фланцевого соединения Аф = 1ф - 1г | 0 | -0,22 | -0,205 | -0,06 | -0,04 | +0,165 | +0,288 | -0,028 | -0,11 |
Диаметральные плоскости | Биение б, мм | ||||
Фланца вала 5Ф | Шейки ТП бт | Торцовое зеркального диска для ГА с ПП на жесткой опоре е"^%^ | Для ГА с ПП на гидравлической опоре | ||
Торцовое зеркального диска 5д | Полное торцовое я Д 2/ф J | ||||
I—V | -0,07 | +0,04 | — | -0,04 | -0,57 |
H—V! | -0,385 | +0,415 | — | -0,09 | -0,18 |
Ill—VII | -0,517 | +0,368 | — | -0,08 | -0,20 |
IV—VIII | -0,22 | -0,032 | — | -0,01 | -0,06 |
* Измерение биения зеркального диска проводится только для агрегатов с подпятниками на гидравлической основе.
Примечания
1 [SJ^ 0,12, [5m]<f;
2 Подсчет 5П проведен при €ф = 8,8 м; Д = 3,9 м; Дд = 4,0 м; f= 0,2 мм для агрегата с подпятником на гидравлической опоре.
Следует устранить неперпендикулярность зеркального диска в плоскости III—VII и излом валов во фланцах в II—VI.
149
ГОСТ Р 55260.3.2—2023
2 Формуляр проверки уклона линии валов с помощью микрометрического уровня.
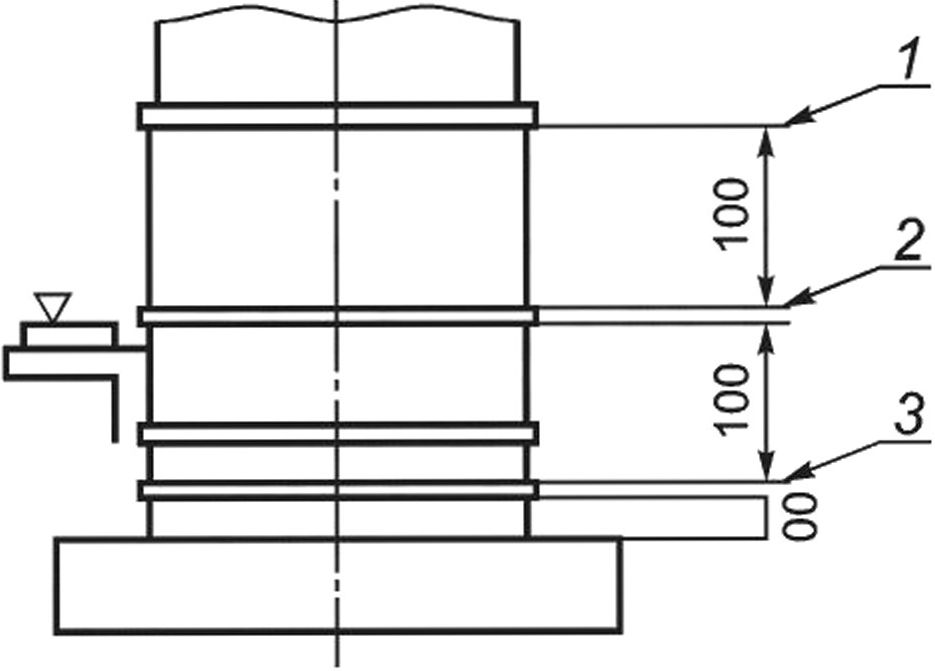
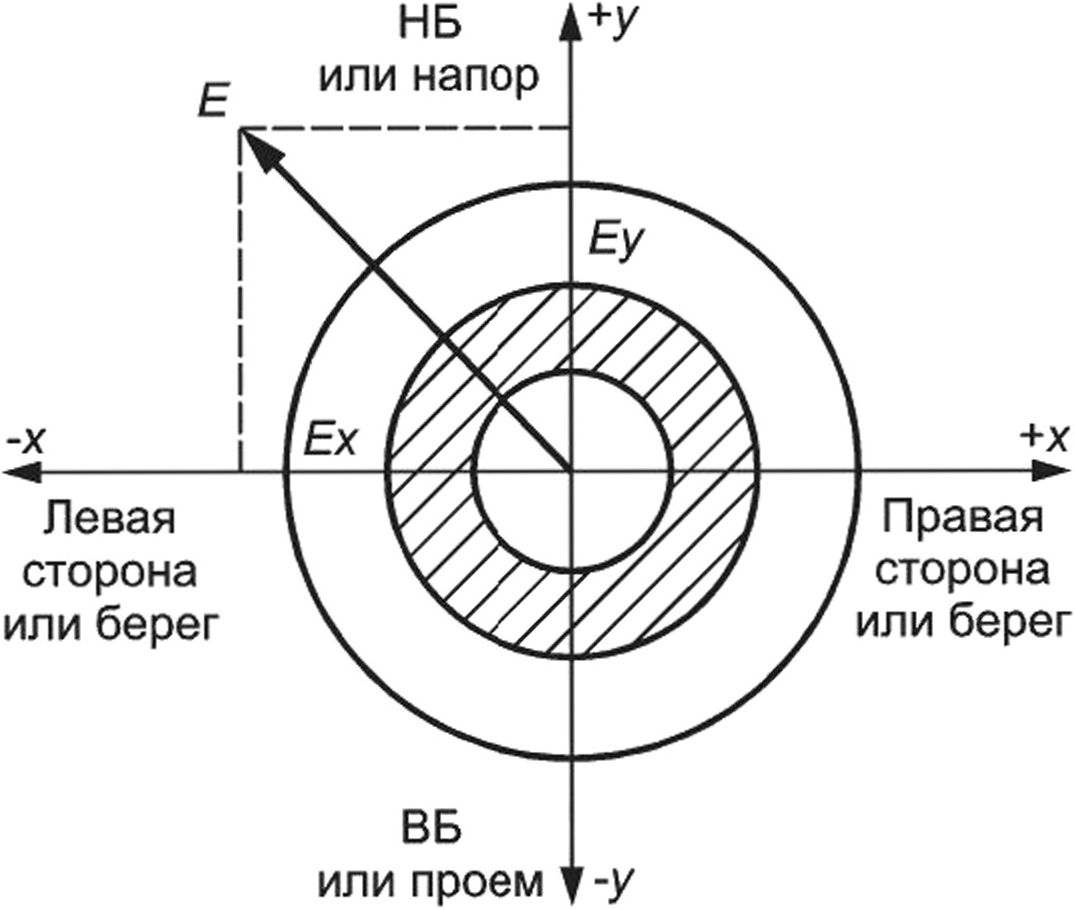
Сечения замеров | Места замеров по окружности вала Положение уровня на плоскости угольника (градусов) | 0 | ■X 180 | 0 | < 180 | 0 | У 180 | + 0 | У 180 |
1 | Показания с исправлением ухода пузырька | -5 | ч— -7 | -70 | ч— -12 | —> +8 | +6 | +76 | +14 |
Среднее внутриосевое | -6 | ч— -11 | —> | —> +15 | |||||
е1х> е1у | -8,5 | —> +11 | |||||||
2 | Число делений с направлением ухода пузырька | <— -3 | ч— -4 | -6 | ч— -7 | —> +2 | -1 | +6 | —> +8 |
Среднее внутриосевое | -3,5 | 4— -6,5 | +0,5 | —> +7 | |||||
е2х’ е2у | <— -5 | +3,75 | |||||||
3 | Деления | ч— -8 | ч— -9 | ч— -9 | ч— -11 | —> +5 | +3 | +10 | —> +12 |
Среднее | ч— -8,5 | ч— -10 | +4 | —> +11 | |||||
е3х> е3у | -9,25 | +7,5 | |||||||
Уклоны еу, еи (в делениях) | ех = -7,58 | еу = +7,42 | |||||||
Уклоны еу, е..(в мм) | ех = -0,76 мм/м | еу = +0,74 мм/м |
150
ГОСТ Р 55260.3.2—2023
Абсолютная величина уклона генераторного вала:
9s^*^s1,0S мм/м.
(Е-7)
Прим е ч а н и я
1 Показания записываются в делениях прибора (цена деления — 0,1 мм/м) с проставлением над цифрой стрелки, указывающей направление ухода пузырька (направление ухода вала). Знак "+" перед цифрой ставится при ориентации этой стрелки по положительной оси и "-” в противном случае. Окончательные результаты составляющих уклонов переводятся в миллиметры на метр.
2 Направление уклона проставляется на принятой системе координат путем построения векторной суммы составляющих ех и е^
3 Данный метод проверки уклона следует принять только после устранения неперпендикулярности зеркала пяты.
151
ГОСТ Р 55260.3.2—2023
Приложение Ж (справочное)
Методика контроля состояния подпятников вертикальных гидроагрегатов
Ж.1 Общие положения
Ж.1.1 Настоящее приложение устанавливает требования к контролю технического состояния подпятников вертикальных ГА всех типов с сегментами, облицованными баббитом, и с эластичными металлопластмассовыми сегментами (ЭМП-сегментами) по результатам технических обследований (испытаний). Технические характеристики, относящиеся к электрической части генератора, оцениваются в соответствии с ГОСТ Р 55260.2.2.
Ж.1.2 Настоящее приложение содержит методические рекомендации по осуществлению технического контроля за состоянием подпятников эксплуатируемых ГА:
- при обычной эксплуатации силами персонала ГЭС;
- в случае повреждений силами персонала ГЭС с привлечением специализированных организаций.
Ж.2 Контроль состояния подпятника при работе ГА
Ж.2.1 Основные контролируемые параметры
При работе ГА должны контролироваться следующие параметры:
- температура сегментов ПП;
- температура и уровень масла;
- наличие потока охлаждающей воды через маслоохладители.
Ж.2.2 Признаки ухудшения состояния ПП:
- повышение температуры сегментов с баббитовым покрытием сверх обычных установившихся значений для данного времени года на 3 °C — 4 °C при сохранении температуры масла на прежнем уровне; в этом случае ГА должен быть остановлен при первой возможности для осмотра ПП и принятия необходимых мер (шабрения сегментов, чистки зеркальной поверхности диска и др.); до вывода в ревизию должно быть максимально ограничено число пусков агрегата и увеличено число измерений температуры (через каждые 2 ч);
- повышение температуры одного или нескольких ЭМП-сегментов в ПП на гидравлической опоре на 4 °C — 5 °C выше обычных установившихся значений температур сегментов и продолжающийся рост температуры, что свидетельствуют о развивающемся повреждении фторопластовой поверхности этих сегментов. В случае отсутствия в этих сегментах термосигнализаторов и при повышении температуры на 10 °C выше первоначального установившегося значения следует остановить агрегат и осмотреть сегменты ПП;
- в ПП с ЭМП-сегментами, имеющими составное исполнение фторопластового покрытия (из двух состыкованных листов фторопласта), возможны повышенные температуры до 15 °C — 20 °C отдельных сегментов, что объясняется неплотностями стыков, в результате чего горячее масло из масляной пленки проходит под фторопластом, вызывая более интенсивный нагрев датчиков температуры, чем на сегментах с плотными стыками фторопластового покрытия. Отрицательного влияния на работу ПП неплотности в стыках не оказывают;
- повышение температуры масла в ванне ПП сверх установившегося значения для данного времени года на 3 °C — 4 °C с последующим повышением температуры сегментов является признаком ухудшения работы маслоохладителей; в этом случае должны быть приняты меры по устранению причин нарушения нормальной работы маслоохладителей (чистка, промыв и др.);
- понижение температуры одного или нескольких сегментов однорядного ПП на жесткой винтовой опоре до значений, близких к температуре масла в ванне (при исправности термоконтроля), свидетельствует о разгрузке этих сегментов, которая может произойти в результате значительных смятий опорных элементов или их разрушений (например, разрушений тарельчатых опор); в ПП с ЭМП-сегментами это может произойти также за счет истирания фторопласта на рабочей поверхности этих сегментов.
Ж.2.3 Контроль уровня масла в ванне ПП
Ж.2.3.1 Контроль уровня масла в ванне ПП должен осуществляться автоматически с подачей сигнала при отклонении уровня от допустимых пределов и визуально по масломерному стеклу.
Ж.2.3.2 Нормальный уровень масла и его предельные значения должны быть нанесены на масломерном стекле и указаны в местной инструкции.
Ж.2.3.3 Уровень масла в ванне ПП должен проверяться оперативным персоналом не реже 1 раза в смену.
Ж.2.3.4 При повышении уровня масла в ванне ПП сверх допустимого значения следует взять пробу масла и, если в нем будет обнаружена вода, остановить ГА для устранения попадания воды в ванну и замены масла. Для ГА с надежно работающими подпятниками при обнаружении небольшого количества воды в масле (следы воды) допускается временная работа при постоянном контроле (2 раза в смену) за состоянием масла.
Ж.2.3.5 При снижении уровня масла в ванне ПП следует взять пробу масла и долить ванну маслом. Для выявления возможной утечки масла через поврежденные трубки маслоохладителей (при самотечной системе технического водоснабжения) необходимо увеличить открытие задвижек на напорных водяных трубопроводах и частич-
152
ГОСТ Р 55260.3.2—2023
но прикрыть задвижки на сливных. Если после этого уровень масла в ванне повысится, то взять пробу масла и при наличии в ней воды действовать согласно Ж.2.3.4. Проверить также плотность закрытия вентилей слива масла.
Ж.2.3.6 Периодически, в соответствии с графиком, установленным на ГЭС, производить отбор и анализ масла из ванны ПП. При несоответствии характеристик масла требованиям ГОСТ 32 или иным нормативным документам, регламентирующим характеристики масла для данного ГА, заменить его.
Ж.2.3.7 На сливных трубопроводах охлаждающей воды из маслоохладителей целесообразно предусмотреть в удобных для наблюдения местах прозрачные вставки или окошки для контроля за движением воды или установить расходомеры.
Ж.2.4 Контроль проседания упругих камер ПП на гидравлической опоре
Ж.2.4.1 Подпятники на гидравлической опоре должны быть оснащены устройствами контроля проседания упругих камер с уставками на сигнал (при проседании на 1 мм больше нормального уровня) и на останов (при проседании на 2 мм больше нормального уровня). Датчики устанавливаются на одной или двух упругих камерах.
Ж.2.4.2 Методы и нормы контроля за герметичностью упругих камер приведены в таблице 6.21.
Ж.2.5 Контроль износа в подпятниках с ЭМП-сегментами
Ж.2.5.1 В ПП с ЭМП-сегментами должен осуществляться контроль износа фторопластовой поверхности по истиранию контрольных кольцевых рисок, нанесенных на четырех сегментах (четырех парах сегментов в двухрядных подпятниках) при изготовлении ЭМП-сегментов на заводе-изготовителе. Первоначальная глубина контрольных рисок указывается на заводском чертеже. Кроме того, целесообразно измерять толщину каждого сегмента не менее чем в четырех точках и данные заносить в формуляр.
Ж.2.5.2 При полном износе контрольных кольцевых рисок дальнейший контроль износа производится путем измерения толщины ЭМП-сегментов не менее чем в четырех фиксированных точках.
При износе фторопласта до выхода на поверхность бронзовой основы ЭМП-сегменты должны быть заменены.
Допускается временная работа при незначительных местных выходах бронзовой проволоки на рабочую поверхность.
Ж.2.6 Отклонения от нормальной работы ПП
В случае появления каких-либо отклонений от нормальной работы ПП, снижения надежности его работы должны быть проведены технические обследования (испытания) с привлечением специализированной организации.
Ж.З Виды натурных испытаний подпятников
Ж.3.1 Испытания, проводимые в целях получения характеристик подпятников
Ж.З.1.1 Испытания, как правило, проводят на одном из первых гидроагрегатов вводимой многоагрегатной ГЭС в целях определения запаса надежности подпятников и при необходимости учета выявленных при испытаниях недостатков и/или особенностей подпятников на последующих гидроагрегатах, а также на гидроагрегатах, оснащенных экспериментальной конструкцией ПП.
Ж.З.1.2 При испытаниях определяют следующие основные характеристики ПП:
- действительную наибольшую нагрузку, действующую на подпятник во время работы ГА;
- значение и характер изменения нагрузки на подпятник при пуске с момента начала открытия НА и до достижения нормальной частоты вращения;
- температуру сегментов ПП при наибольшей на него нагрузке;
- температуру масла в масляной ванне ПП;
- толщину масляной пленки, разделяющей поверхности трения при наибольшей нагрузке на подпятник;
- характер образования масляной пленки, разделяющей поверхности трения при пуске;
- скорость «всплытия» диска пяты над сегментами;
- характер изменения толщины масляной пленки при останове;
- толщину пленки, разделяющую поверхности трения в течение последнего оборота перед остановом;
- потери на трение в ПП.
Ж.З.1.3 Сравнение полученных при испытаниях характеристик ПП с расчетными и нормативными показателями позволят судить о работоспособности конструкции ПП в целом, о запасе ее надежности и ресурсе ГА.
Нормативные значения характеристик приведены в таблицах 6.21, 6.22, конструкторской документации, инструкциях по эксплуатации.
Если для характеристики отсутствуют расчетные и нормативные данные (например, динамика изменения нагрузки на подпятник, характер образования и изменения толщины масляной пленки), следует ее оценивать на основе накопленного опыта испытаний и эксплуатации подпятников.
Ж.З.1.4 Кроме основных характеристик при испытаниях определяют еще и ряд вспомогательных характеристик, таких как величина и характер биения зеркальной поверхности диска, разброс температуры отдельных сегментов, пульсация нагрузки и др., которые позволяют судить о состоянии ПП, о том, как он изготовлен, смонтирован и налажен (см. таблицы 6.21, 6.22).
Ж.3.2 Испытания, проводимые в целях выяснения причин ненадежной работы подпятников
Ж.З.2.1 Ненадежность работы подпятников проявляется в эксплуатации в виде частой повреждаемости сегментов, что вызывает необходимость введения ограничений в режим работы ГА, а также в виде отклонений
153
ГОСТ Р 55260.3.2—2023
его характеристик от нормативных значений (повышенная температура сегментов, большая разница температур отдельных сегментов и др.).
ЭМП-сегменты работают значительно более надежно, чем баббитовые. При условии их качественного изготовления, монтажа в ПП и наладки повреждений подпятников с ЭМП-сегментами сбои в их работе практически не возникают.
Причинами ненадежной работы подпятников как с баббитовыми, так и с ЭМП-сегментами могут быть дефекты конструкции, изготовления, монтажа, недостатки эксплуатации, а также естественное старение.
Ж.3.2.2 Причинами ненадежной работы подпятников могут быть:
- неоптимальная установка тангенциального и радиального эксцентриситетов сегментов;
- неравномерное распределение нагрузки между сегментами;
- высокая волнистость зеркальной поверхности диска;
- недостаточная чистота зеркальной поверхности диска;
- недостаточная эффективность системы охлаждения;
- плохо выбранные пусковые установки турбины (пусковое открытие НА и пусковой угол установки лопастей РК);
- повышенная деформация сегментов и др.
Ж.3.2.3 Испытания в целях выяснения причин ненадежной работы ПП проводятся, как правило, в два или более этапа. На первом этапе определяются те же характеристики ПП, что и при испытаниях по Ж.3.1, и разрабатываются мероприятия по повышению надежности работы ПП. На последующих этапах испытаний проводится проверка разработанных мероприятий.
Ж.3.3 Испытания по сокращенной программе
Ж.3.3.1 Такие испытания проводятся в тех случаях, когда ставится конкретная задача, ограниченная определенными условиями. Например, требуется проверить величину биения зеркальной поверхности диска (с повторными измерениями после исправления, если это потребуется). При таких испытаниях число измеряемых величин и режимов испытаний ограничено. В отдельных случаях даже не требуется разбирать подпятник.
Ж.3.3.2 Испытания по сокращенной программе можно рассматривать как часть испытаний по Ж.3.1, Ж.3.2, методики которых излагаются в настоящем приложении.
Ж.4 Основные требования к проведению натурных испытаний ПП
Ж.4.1 Перед испытаниями ПП, проводимыми в целях получения действительных характеристик или выяснения причин ненадежной работы, необходимо провести тщательный осмотр ПП с измерениями для выяснения его состояния.
Ж.4.2 Объем измерений при испытаниях подпятников
Ж.4.2.1 Наиболее распространенным типом ПП является подпятник на жестких винтовых опорах с однорядным расположением сегментов. Все другие типы подпятников являются разновидностью этого типа. Поэтому основные рекомендации по испытаниям даются вначале для этого типа ПП, а затем указываются особенности испытаний других типов.
Ж.4.2.2 В зависимости от вида испытаний различными являются объем измерений и режимы исследований.
Ж.4.3 Режимы испытаний подпятников
Ж.4.3.1 Испытания проводятся в различных режимах работы ГА. В подпятниках, оснащенных баббитовыми сегментами, особое внимание уделяется пускам как наиболее тяжелым режимам работы для ПП. При испытаниях в целях получения действительных характеристик подпятников проводится серия пусков с различной продолжительностью интервалов между остановами и последующими пусками в такой последовательности:
- пуск после подготовительных работ на сегментах, смазанных салом. Работа на холостом ходу не менее 15 ч. Останов;
- пуск через 6—8 ч после останова. Включение генератора в сеть и плавный набор полной нагрузки. Работа под нагрузкой не менее 3 ч. Останов;
- пуск через 4 ч после останова. Работа под нагрузкой не менее 2 ч. Останов;
- пуск через 2 ч после останова. Работа под нагрузкой не менее 2 ч. Останов;
- пуск через 30 мин после останова. Работа под нагрузкой не менее 2 ч. Останов;
- пуск сразу после останова.
После каждого опыта рассматриваются его результаты, и если они положительные, то проводится следующий опыт.
Ж.4.3.2 После второго или третьего пуска проводятся опыты с различными нагрузками: ступенями (через каждые 10 % мощности ГА) устанавливаются нагрузки от нуля до наибольшей. Каждый режим выдерживается 10—15 мин, после чего проводят измерения.
Ж.4.3.3 Подпятники, оснащенные ЭМП-сегментами, являются значительно более надежными в пусковом и режимном отношениях. Их испытания проводятся в такой последовательности:
- пуск после подготовительных работ. Пуск производится в обычном порядке без смазки сегментов салом. Работа на холостом ходу 4—6 ч. Останов;
- пуск через 2 ч после останова. Работа под нагрузкой не менее 2 ч. Останов;
154
ГОСТ Р 55260.3.2—2023
- пуск сразу после останова и изменение нагрузки ступенями через каждые 10 % мощности ГА от нуля до наибольшей. Каждый режим выдерживается 10—15 мин, после чего производится измерение. Останов;
- пуск сразу после останова и набор номинальной нагрузки. Останов. Режим повторяется 2—3 раза;
- останов агрегата на выбеге без торможения.
После каждого опыта рассматриваются его результаты, и если они положительные, то проводится следующий опыт.
Ж.4.4 Особенности испытаний двухрядных подпятников
В соответствии с конструктивными особенностями двухрядных подпятников (удвоенное число сегментов) при их испытаниях увеличено число измеряемых величин. Все измерения проводят не на одном, а на двух сегментах. На наружном и внутреннем сегментах одной пары измеряется толщина масляной пленки, снимаются температурные поля. Температура в горячей зоне каждого сегмента измеряется на всех наружных и внутренних сегментах. Пульсация усилий измеряется на двух-трех парах сегментов (на внутреннем и наружном сегментах каждой из этих пар). Режимы испытаний двухрядных подпятников как с баббитовыми, так и с ЭМП-сегментами такие же, как и для подпятников с однорядным расположением сегментов.
Ж.4.5 Особенности испытаний подпятников на гидравлической опоре
При испытаниях подпятников на гидравлической опоре, оснащенных как баббитовыми, так и ЭМП-сегментами, должна быть проверена работа системы гидравлического выравнивания нагрузки между сегментами. Проверку проводят сначала перед испытаниями ПП при определении его состояния, а затем на работающем ГА. Для этого одновременно с записью биения зеркальной поверхности диска при прокручивании ротора на сегментах, смазанных салом, регистрируются вертикальные перемещения всех упругих камер (в отдельных случаях, когда упругих камер шестнадцать и более, допустимо осциллографирование половины других камер — через одну). Вертикальные перемещения упругих камер должны составлять не менее 0,8 биения зеркальной поверхности диска. При испытаниях такую же проверку проводят на работающем ГА при нормальной частоте вращения.
Если испытания проводятся для выяснения причин ненадежности работы ПП, то может оказаться необходимым проверить вертикальность опускания всех или части упругих камер при их сжатии во время опускания ротора ГА с тормозов на подпятник. Для этого регистрируется вертикальное перемещение упругой камеры несколькими датчиками или индикаторами, установленными с разных сторон камеры.
Ж.5 Проведение измерений при испытаниях подпятников
Ж.5.1 Измерение нагрузки, действующей на подпятник
Нагрузка, действующая на подпятник, складывается из двух составляющих — массы ротора ГА (постоянная составляющая) и гидравлического осевого усилия (переменная составляющая).
Ж.5.1.1 Масса ротора ГА складывается из масс ротора генератора, вала генератора, РК турбины, вала турбины и других вращающихся частей ГА. Она может быть вычислена по заводским данным, приведенным на чертежах, или определена путем измерений. Перед регулировкой проводят калибровку опорных тарелок ПП на прессе, т. е. определяется зависимость деформации опорных тарелок от нагрузки на них.
Калибровка на прессе должна проводиться в условиях, полностью имитирующих условия работы опорных тарелок в ПП. Должны быть представлены: опорный вкладыш с диаметром сферической головки, равным диаметру сферической головки опорного болта или вкладыша в ПП, реальный сегмент и плита, имеющая такую же толщину, как диск ПП. В случае невыполнения этих условий зависимость деформации опорной тарелки от приложенного к ней усилия будет неодинаковой на прессе и в ПП, и определение массы ротора ГА окажется невозможным (в этих условиях возможно лишь проведение регулировки нагрузки на сегменты без определения абсолютной нагрузки).
При опускании ротора ГА с тормозов на сегменты ПП определяется нагрузка на каждый сегмент. Сумма нагрузок на все сегменты дает массу вращающихся частей агрегата, те. массу ротора агрегата.
При многократных подъемах и опусканиях ротора ГА на тормозах-домкратах и различных высотных положениях регулировочных болтов суммарное значение нагрузки на сегменты, т. е. масса ротора, обычно колеблется в пределах 4 % — 8 % среднего значения, что и определяет точность данного способа.
При таком способе определение значения массы ротора может получиться несколько ниже действительного значения из-за наклона вала и трения в направляющих подшипниках. Кроме того, следует учитывать взвешивающее действие воды на рабочее колесо (Архимедову силу), если КРК заполнена водой.
Если масса ротора ГА определяется при заполненной водой КРК, то это значение массы ротора и берется при вычислении полной нагрузки на подпятник. Если масса ротора ГА определяется при осушенной КРК, то при определении полной нагрузки на подпятник следует уменьшить ее на значение Архимедовой силы (массы воды в объеме РК). Для крупных ПЛ-турбин взвешивающая сила достигает 3 % — 4 % массы ротора агрегата.
Массу вращающихся частей ГА можно также определить измерением с помощью образцового манометра стабильного давления в тормозной системе генератора при взвешенном на тормозах роторе. Зная значение этого давления и общую площадь поршней тормозных цилиндров, легко подсчитать массу вращающихся частей ГА.
При определении массы ротора вышеописанным способом нужно следить за наличием на роторе всех деталей и, если какие-либо из них отсутствуют, учитывать их массу.
Ж.5.1.2 Гидравлическое осевое усилие, действующее на рабочее колесо турбины, может быть измерено различными способами.
155
ГОСТ Р 55260.3.2—2023
Ж.5.1.2.1 Гидравлическое осевое усилие может быть измерено по растяжению вала ГА. При этом способе на вал турбины или генератора ниже ПП наклеиваются тензометры и собираются в измерительную схему. Снятие показаний с вращающихся частей осуществляется с помощью токосъема, установленного в наиболее удобном месте вала турбины или генератора.
Ж.5.1.2.2 Если испытания проводятся на генераторе зонтичного типа или нет возможности наклеить тензометры между ротором генератора и подпятником на подвесном генераторе, то нельзя провести прямую калибровку массой ротора генератора. В этом случае осевое усилие может быть определено с помощью эталонной балки равного сопротивления, на которую наклеены тензометры из той же партии, что наклеены на вал. Тензометры собраны в схему так же, как на валу. Балка подключается к измерительному каналу, на котором регистрируется осевое усилие (на это время тензометры, наклеенные на вал, отключаются). На балке создается прогиб, соответствующий определенному значению напряжения о, и регистрируется отклонение сигнала. Затем создается дисбаланс в схеме путем включения в одно из плеч измерительного моста калибровочного сопротивления (кгс/см2). Определяется, какому значению напряжения (кгс/см2) соответствует калибровочный импульс. В процессе испытаний по этому калибровочному импульсу определяется масштаб записи (кгс/см2). Переход от значения напряжения растяжения вала к осевому усилию Рг, растягивающему вал, производится по формуле
F^a^D^-D^-IO, (Ж.1)
где DH и DB — наружный и внутренний диаметры вала в месте наклейки тензометров.
Ж.5.1.2.3 Гидравлическое осевое усилие может быть измерено по деформации опорных тарелок ПП. При этом способе на все опорные тарелки или их часть наклеиваются тензометры, собирается измерительная схема и производится калибровка опорных тарелок на прессе. Можно калибровать опорные тарелки массой ротора ГА.
Измерение осевого гидравлического усиления при испытаниях ПП этим способом проще, чем по растяжению вала, так как не требуется токосъемное устройство, лучше условия для наклейки и сушки тензометров и т. д. Чувствительность также выше, так как напряжения в опорной тарелке в 3—4 раза больше, чем нормальные напряжения от растяжения вала. Однако измерение осевого гидравлического усилия по деформации опорных тарелок имеет существенный недостаток — при вращении ротора ГА в опорных тарелках возникает пульсация напряжений, вызванная биением зеркальной поверхности диска ПП. Поэтому возникает дополнительная погрешность при определении осевого усилия, так как трудно получить нуль усилия перед пуском: если перед пуском над сегментом, по опорной тарелке которого измеряется осевое гидравлическое усилие, находится выступ зеркальной поверхности диска, то полученное после пуска значение осевого гидравлического усилия будет занижено, если над этим сегментом находится впадина, то значение осевого гидравлического усилия будет завышено. Отклонение может достигать 8 % — 10 % значения осевого гидравлического усилия. Поэтому при измерении осевого гидравлического усилия по деформации опорных тарелок желательно производить замеры одновременно по трем-четырем опорным тарелкам, расположенным на равных расстояниях одна от другой, и брать среднее значение полученного осевого гидравлического усилия.
Ж.5.1.2.4 Гидравлическое осевое усилие может быть измерено по прогибу грузонесущей крестовины. Датчик прогиба должен закрепляться на кронштейне, установленном на фундаменте здания ГЭС, и упираться в крестовину как можно ближе к ее центру. Место на крестовине, в которое упирается головка датчика, должно быть зачищено, не должно иметь заусенцев и рисок. На генераторе подвесного типа датчик можно закрепить на грузе, подвешенном на крюке мостового крана, и упереть в крестовину.
Калибровка прогиба крестовины по усилию производится массой ротора ГА: ротор опускается с тормозов-домкратов на подпятник и регистрируется прогиб крестовины. Считая зависимость прогиба крестовины от приложенного усилия прямолинейной, в дальнейших опытах вычисляется усилие от реакции воды по измеренному прогибу. Значение прогиба крестовины от массы ротора и реакции воды у крупных генераторов достигает 4—5 мм. На такие перемещения должны быть рассчитаны применяемые датчики. Основное неудобство рассмотренного способа измерения заключается в трудности закрепления датчиков неподвижно относительно крестовины.
Ж.5.1.2.5 Гидравлическое осевое усилие может быть измерено по деформации грузонесущей крестовины, на которой размещен подпятник. Для этого на одну из лап крестовины в продольном направлении наклеиваются тензометры сопротивления (рабочие). На компенсационной пластине, закрепленной на крестовине одним концом, наклеиваются компенсационные тензометры. Собирается измерительная схема — мостовая или полумостовая. Калибровка производится массой ротора ГА.
Ж.5.1.2.6 Гидравлическое осевое усилие может быть измерено по деформации опоры пяты. В ГА с подпятниками зонтичного типа при опирании на крышку турбины через промежуточный опорный конус возможно определение осевого гидравлического усилия по деформации этого конуса (опоры пяты). На поверхности опорного конуса наклеиваются тензометры: рабочие — вдоль образующей конуса и компенсационные — на специальной компенсационной пластине, крепящейся одним концом к опорному конусу. Собирается схема и проводится калибровка по усилию массой ротора агрегата, аналогично тому, как это делается в вышеописанных случаях.
156
ГОСТ Р 55260.3.2—2023
Не следует определять гидравлическое осевое усилие по вертикальному перемещению опоры пяты, вызванному прогибом крышки гидротурбины, так как прогиб крышки турбины зависит не только от осевого усилия, передаваемого на нее от ПП через опору пяты, но также и от давления (разрежения) в потоке под крышкой турбины.
Ж.5.1.2.7 Представленные в Ж.5.1 измерения могут быть осуществлены с помощью цифровых средств фиксации и контроля при условии обеспечения необходимой точности измерений.
Ж.5.2 Измерение температуры
Измерение температуры при испытаниях подпятников обычно проводят с помощью термопар. В каждом сегменте устанавливается по одной термопаре в горячей зоне, а в одном или двух сегментах устанавливается по шестнадцать — двадцать термопар для получения температурного поля.
При испытании ПП с баббитовыми сегментами головки термопар размещаются непосредственно в баббите на глубине 2—2,5 мм от уровня рабочей поверхности. Термопары вводятся в слой баббита через отверстия диаметром 3—4 мм с тыльной стороны сегмента, головки термопар плотно прижимаются к баббиту. Для того чтобы термопары плотно держались в отверстиях, они с тыльной стороны расклиниваются. Термопары закладываются в пазы, специально выфрезерованные для этого на тыльной стороне сегментов.
Для получения перепада температур по толщине сегмента с баббитовым покрытием термопары закладываются с тыльной стороны сегмента, для чего сверлятся четыре-пять отверстий глубиной 8—10 мм и в них устанавливается четыре-пять термопар таким образом, чтобы юс головки был плотно прижат к металлу.
Для получения перепада температур по толщине основания сегмента (по толщине подушки) в четырех-пяти точках подушки (если смотреть в плане) устанавливаются термопары на трех уровнях по толщине — всего двенадцать — пятнадцать термопар. Провода от этих термопар удобнее всего выводить в пазы подушек, т. е. к верхней плоскости подушки.
При испытаниях ПП с ЭМП-сегментами измерение температуры производится непосредственно на фторопластовой поверхности в масляном слое, разделяющем поверхности трения. Головки термопар заглубляются на 0,5 мм под уровень рабочей поверхности сегмента. Уплотнение электродов термопар производится с помощью фторопластовых втулок.
Для измерения температуры масла в ванне ПП устанавливаются термопары в различных местах ванны по пути циркуляции масла: над охладителями, под охладителями, в нижней части ванны со стороны выгородки, у входа в межсегментный канал, у выхода из межсегментного канала и т. д. Кроме того, две-четыре термопары устанавливаются на трубках охладителей — на входе и выходе воды.
Ж.5.3 Определение потерь на трение в ПП
Наиболее приемлемым способом определения потерь на трение в ПП является калориметрический метод, т.е. определение потерь, уносимых охлаждающей водой. Для этого необходимо знать расход воды, проходящей через маслоохладители ПП, и температуру воды на входе и выходе из них. Потери Рк, кВт, вычисляют по формуле
PK = 4,19Qyc(T2-T1),
(Ж.2)
где Q — расход воды, л/с;
у — плотность воды, г/см3 (берется для температуры, при которой производятся измерения);
с — удельная теплоемкость воды (практически она составляет 1,0 ккал/(кг-град);
^ и Т2 — температура воды соответственно на входе в маслоохладители и выходе из них, °C.
Измерение температуры воды 7'1 и Т2 должно производиться термометрами с ценой деления 0,1 °C, имеющими поверочные свидетельства с поправками. Термометры устанавливаются в карманы, врезанные в трубопроводы подвода и отвода воды. Измерения производятся в установившемся тепловом режиме. Для увеличения точности измерений целесообразно производить их при пониженном расходе воды, так как при этом увеличивается разница температур воды на входе и выходе.
При определении потерь калориметрическим способом разница температур масла в ванне ПП и воздуха, окружающего масло и ванну, не должна быть больше 5 °C. При большей разнице следует учитывать потери, отводимые через стенки маслованны путем теплопроводности. Для определения этой части потерь необходимо знать температуру внутренней и наружной поверхности стенки маслованны. Потери через стенку маслованны Pcv Вт, вычисляют по формуле
(Ж.З) о
где А — коэффициент теплопроводности материала маслованны, Вт/(мтрад);
/в — средняя температура внутренней поверхности стенки маслованны, °C;
/н — средняя температура наружной стенки маслованны, °C;
б — толщина стенки маслованны, м;
F — общая площадь поверхности стенок маслованны, м.
157
ГОСТ Р 55260.3.2—2023
Температура внутренней и наружной поверхности стенки маслованны должна быть измерена в нескольких местах и должно быть вычислено среднее значение. При измерении температуры поверхности стенки ванны головки термопар или термосопротивления должны быть хорошо изолированы от масла внутри ванны и от воздуха снаружи, т. е. должна измеряться строго температура поверхностей стенки и должно быть исключено влияние температуры масла и воздуха на показания термодатчиков.
Потери на трение в ПП Р определяются как сумма потерь с водой и потерь через стенки маслованны
Р=Р„-РСт (Ж-4)
Ж.5.4 Измерение биения зеркальной поверхности диска
При испытаниях устанавливаются четыре датчика: три — на одном радиусе у наружного края, в середине и у внутреннего края диска и один — на противоположном радиусе у наружного края диска.
Возможно применение бесконтактных датчиков биения зеркальной поверхности диска (например, индуктивных). Они устанавливаются в тех же местах. Зазор между датчиками и зеркальной поверхностью диска на остановленном ГА должен быть не менее 0,8 мм для ПП с сегментами, облицованными баббитом, так как при максимальной нагрузке на подпятник на работающем агрегате возможно опускание диска (ротора агрегата) на величину до 0,7 мм за счет прогиба опорных тарелок и других упругих элементов опорной системы ПП. В жестких однорядных подпятниках зазор должен быть не менее 0,6 мм, в подпятниках на гидравлической опоре — не менее 0,8 мм. В подпятниках с ЭМП-сегментами этот зазор должен составлять не менее 1,0 мм.
Ж.5.5 Определение коэффициента трения в ПП при трогании
Для определения коэффициента трения в ПП в момент трогания необходимо знать нагрузку на подпятник и момент сил сопротивления. Нагрузка на подпятник складывается из массы ротора ГА и осевого гидравлического усилия. Момент сил сопротивления при трогании ротора ГА (т.е. при срыве диска пяты с сегментов) равен моменту приложенных сил и может быть определен по скручиванию вала (крутящего момента на валу).
Кроме осевого гидравлического усилия и крутящего момента на валу необходимо регистрировать момент, когда происходит трогание ротора ГА (с помощью контактной щетки или другим способом).
Коэффициент трения при трогании Г вычисляют по формуле
f-(P2;G)Ry' <ж-5)
где М — крутящий момент при трогании, Н • м;
Р2 — осевое гидравлическое усилие при трогании, Н;
G — масса ротора ГА, Н;
Ry — радиус трения (равен радиусу окружности опорных болтов ПП), м.
Определение напряжений растяжения вала о производится с помощью эталонной балки равного сопротивления, а переход от напряжений к усилию — по формуле (Ж.1). Определение касательных напряжений кручения вала т производится также с помощью эталонной балки равного сопротивления, а переход от деформаций к моменту кручения М, Н ■ м, по формуле
M=Wv10, (Ж.6)
где И/— полярный момент сопротивления, м3
где Он и Овн соответственно наружный и внутренний диаметры вала, м.
При определении коэффициента трения трогания в подпятниках генераторов подвесного типа целесообразно наклеивать тензометры на вал между ротором генератора и подпятником. В этом случае имеется возможность калибрования схемы измерения осевого усилия массой ротора ГА, а записываемый в этом месте вала крутящий момент является непосредственно моментом сил сопротивления в ПП. В момент трогания он достигает наибольшего значения, а затем резко уменьшается. При такой записи не требуется отдельно определять, в какой момент происходит трогание ротора ГА. Точность определения коэффициента трения в этом случае выше.
158
ГОСТ Р 55260.3.2—2023
Приложение И (обязательное)
Методика определения осевой жесткости агрегата
И.1 Осевая жесткость гидроагрегата Сос определяется расчетно-экспериментальным методом. Испытания проводятся на остановленном агрегате, со снятым давлением с водовода. Ротор агрегата постепенно поднимается на тормозах с помощью масляного пресса или тормозных домкратов. В процессе подъема одновременно регистрируются перемещения вала и грузонесущей крестовины (или крышки турбины при расположении опоры подпятника на крышке). Схема измерений на примере нижней грузонесущей крестовины представлена на рисунке И.1.1.
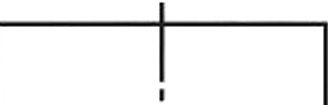
05
СП
у®|
Нижняя крестовина
to ---
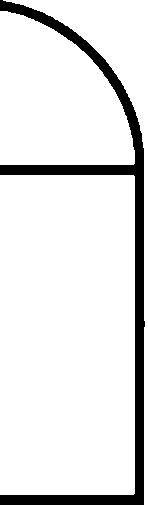
(Т) Датчик перемещения, установленный на вал (работает на увеличение зазора)
(2) Датчик перемещения, установленный на нижней крестовине (работает на увеличение зазора) Рисунок И.1.1 — Схема измерений
И.2 Суммарная осевая жесткость гидроагрегата Сос определяется в соответствии с правилом суммирования двух последовательно соединенных жесткостей: жесткости грузонесущей крестовины Ск (или крышки турбины при опоре на нее подпятника) и жесткости подпятника Сп (опорных болтов и сегментов ПП):
Сос-
QrQi ск+сп
(И.1)
И.З Жесткость грузонесущей крестовины (крышки турбины) Ск определяется по формуле
С _^Р ик~—»
Ук
(И.2)
где Gp — вес ротора гидроагрегата;
ук — вертикальное упругое перемещение грузонесущей крестовины (крышки турбины) в момент ее полной разгрузки при подъеме на тормозах.
В случае невозможности или нецелесообразности проведения испытаний с подъемом ротора на тормозах допускается определение жесткости грузонесущей крестовины численными методами с применением пространственного ЗО-моделирования. При этом особое внимание должно быть уделено условиям опирания грузонесущей крестовины на фундамент.
И.4 Вес ротора гидроагрегата Gp определяется по конструкторской документации или расчетным способом по формуле
159
ГОСТ Р 55260.3.2—2023
Gp=pZT-n—, (И.З)
где р — давление в масляном прессе в момент полной разгрузки грузонесущей крестовины;
ZT — количество тормозов;
dT — диаметр поршня тормоза.
И.4 Жесткость подпятника Сп определяется по формуле
01“’ (И.4)
гдеуп — вертикальное упругое перемещение ПП в момент полной разгрузки грузонесущей крестовины (опоры ПП) при подъеме на тормозах, определяемое как разность перемещения вала и грузонесущей крестовины
Уп = Ув“Ук- (и-5)
Перемещение уп может быть также определено с помощью непосредственных измерений на ПП. Для этого на остановленном гидроагрегате монтируется кронштейн от стенки шахты турбины к опоре подпятника, на который устанавливается датчик перемещений, фиксирующий перемещение опоры подпятника относительно стенки шахты турбины.
И.5 Схема определения величин ув и ук по графику перемещений представлена на рисунке И.5.1, где момент времени ^ соответствует началу подъема ротора, момент времени t2 соответствует полной разгрузке грузонесущей крестовины.
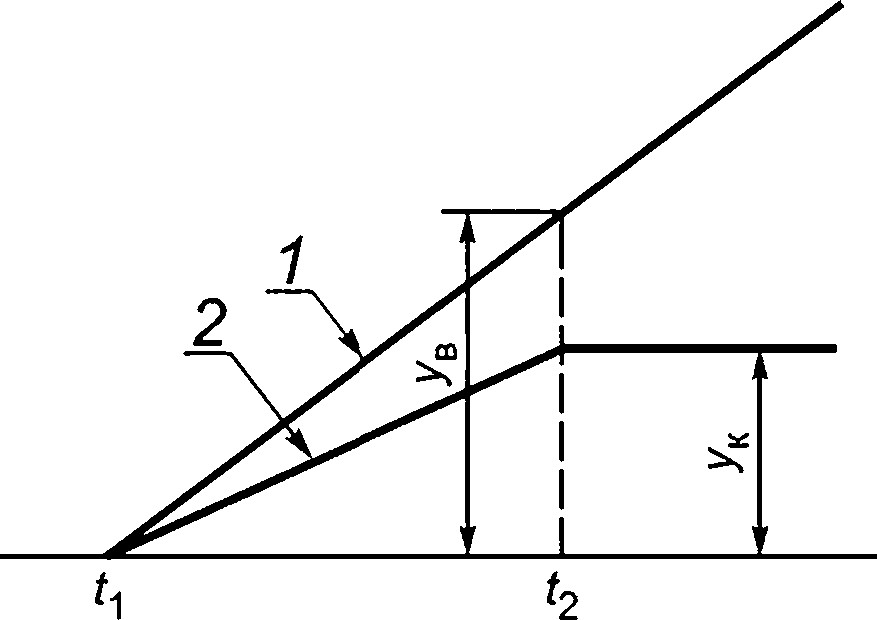
1 — перемещение вала; 2— перемещение грузонесущей крестовины
Рисунок И.5.1 — График подъема ротора на тормозах
И.6 Форма представления результатов измерений и расчета осевой жесткости гидроагрегата представлена в таблице И.5.1.
Таблица И.5.1 — К определению осевой жесткости гидроагрегата
Наименование | Обозначение | Размерность | Значение |
Экспериментальные данные | |||
Перемещение вала | Ув | мм | |
Перемещение грузонесущей крестовины | Ук | мм | |
Расчетные данные | |||
Перемещение подпятника | Уп | мм | |
Жесткость грузонесущей крестовины | Ск | кг/см | |
Жесткость подпятника | сп | кг/см | |
Суммарная осевая жесткость агрегата | Сос | кг/см |
160
ГОСТ Р 55260.3.2—2023
Приложение К (справочное)
Методики проведения натурных испытаний гидроагрегата
К.1 Общие положения
К. 1.1 В данном разделе приведены основные требования к проведению следующих видов натурных эксплуатационных испытаний, используемых для оценки технического состояния гидротурбин:
- энергетические испытания ГА абсолютным методом;
- энергетические испытания ГА индексным методом;
- энергетические испытания по определению оптимальной комбинаторной зависимости ПЛ-гидротурбин;
- исследование вибрационного состояния узлов ГА.
К. 1.2 Основной целью натурных энергетических испытаний ГА является уточнение энергетических характеристик, необходимых для наиболее экономичной эксплуатации ГА. При поставке на ГЭС гидротурбинного оборудования энергетические характеристики выдают заводы-изготовители по результатам пересчета с характеристик модельной гидротурбины. Вследствие не учитываемых при расчете факторов, а также отклонений при изготовлении рабочих колес и проточной части гидротурбины, фактические энергетические характеристики не совпадают с пересчитанными с модельных и могут быть различны для отдельных ГА одной и той же ГЭС. С ростом наработки ГА эти различия могут увеличиваться вследствие неодинакового износа рабочих колес и проточной части, а также ремонтных воздействий (отклонений при восстановлении профилей лопастей).
Натурные энергетические испытания агрегатов могут производиться также:
- для определения эффективности модернизации и ремонтно-восстановительных работ на гидротурбинах;
- определения ограничений максимальной мощности из-за возникновения кавитационных явлений при понижении уровня НБ;
- оптимизации комбинаторной связи ПЛ-гидротурбин.
Эксплуатационные энергетические испытания позволяют получать следующие энергетические характеристики:
- мощностную (зависимость мощности гидротурбины от открытия НА);
- рабочую (зависимость КПД гидротурбины от ее мощности);
- расходную (зависимость расхода воды через гидротурбину от ее мощности);
- эксплуатационную (зависимость КПД турбины от напора и мощности турбины) при проведении испытаний при различных напорах;
- комбинаторную зависимость для ПЛ-гидротурбин.
К. 1.3 Одновременно с энергетическими испытаниями индексным методом целесообразно проводить исследования вибрационного состояния ГА в целях определения на рабочих характеристиках зон, не рекомендуемых и запрещенных для длительной работы ГА.
К.2 Энергетические испытания гидроагрегата абсолютным методом
Испытания проводят в соответствии с требованиями ГОСТ 28842, по рабочей программе. Рабочая программа испытаний утверждается техническим руководителем ГЭС и согласовывается с соответствующим диспетчерским центром. При проведении гарантийных испытаний программу согласовывают также с заводом-изготовителем.
К.2.1 Цель испытаний
Абсолютный метод предусматривает определение фактических (абсолютных) значений КПД, сравнение измеренных значений КПД с гарантированными заводом-изготовителем, определение действительных рабочей и расходной характеристик гидротурбины, тарировка расходомерного створа спиральной камеры гидротурбины.
К.2.2 Периодичность и объем испытаний
К.2.2.1 На гидроэлектростанциях необходимо проводить испытания вновь вводимых (модернизированных) гидротурбин с непосредственным измерением расходов воды через гидротурбину (абсолютным методом) при вводе в эксплуатацию штатных ГА (гидротурбин) после достижения проектного напора и при вводе в работу гидротурбин после модернизации и/или замены элементов гидротурбины или изменения формы проточного тракта.
К.2.2.2 Количество ГА, испытываемых абсолютным методом, рекомендуется принимать в зависимости от количества установленных или модернизированных однотипных ГА:
- до четырех — одного;
- от пяти до десяти — двух;
- от одиннадцати до двадцати и более — трех.
С учетом высокой стоимости и затрат на проведение испытаний абсолютным методом допускается уменьшение количества испытываемых агрегатов по решению технического руководителя ГЭС с согласия завода-изготовителя.
К.2.2.3 При энергетических испытаниях вводимой в эксплуатацию новой или модернизированной гидротурбины с помощью абсолютного метода определяют фактические значения КПД, в т. ч. его максимальное значение, и
161
ГОСТ Р 55260.3.2—2023
максимальную мощность гидротурбины в целях проверки выполнения гарантий завода-изготовителя (гарантийные испытания), оценки эффективности модернизации и оценки фактического состояния гидротурбины.
К.2.3 Методика и условия проведения испытаний
К.2.3.1 Испытания проводят в соответствии с требованиями ГОСТ 28842.
К.2.3.2 В соответствии с ГОСТ 8.439 рекомендуется использовать метод «площадь — скорость», при котором расход гидротурбины определяется интегрированием поля местных скоростей в выбранном для этого створе, измеряемых гидрометрическими вертушками.
Местные скорости измеряются гидрометрическими вертушками, которые могут быть установлены как в закрытом, так и в открытом водоводах. Для снижения погрешности измерений необходимо, чтобы поток в мерном створе удовлетворял требованиям по отсутствию в нем косоструйности, закручивания, несимметричности и повышенной турбулентности.
Проведение энергетических испытаний абсолютным методом на деривационных ГЭС допускает два варианта выбора створа для установки гидрометрических вертушек:
- в напорном трубопроводе;
- в пазах плоских затворов водоприемника.
Использование первого варианта при соблюдении требований ГОСТ 28842 обеспечивает значения погрешности измерения расхода гидротурбины в интервале от ±1,0 % до ±1,5 %; второй вариант при тех же условиях обеспечивает значения погрешности в интервале от ±1,2 % до ±2,0 %.
К.2.3.3 При испытаниях однотипных агрегатов в случае размещения мерного створа во входном сечении водоприемника гидротурбины может применяться упрощенный способ, представляющий собой модификацию метода «площадь — скорость». В этом случае средняя скорость определяется как среднеарифметическое значение скоростей, измеренных в отдельных точках сечения, умноженное на коэффициент коррекции, принимаемый единым для всех однотипных ГА и определяемый по результатам испытаний одного из ГА абсолютным методом.
При применении упрощенного способа испытаний нескольких ГА должны быть соблюдены следующие условия:
- идентичность конструкции и одинаковые размеры входного сечения водоводов;
- фиксированное положение вертушек относительно потока;
- использование одних и тех же вертушек при испытании всех ГА;
- одинаковые режимы работы соседних с испытуемым агрегатов.
Рама для упрощенного способа испытаний должна перекрыть все измерительное сечение водоприемника.
К.2.3.4 Настоящий стандарт допускает возможность применения с этой целью иных методов: например, акустических, гидравлического удара и др., при условии их метрологической аттестации, произведенной в установленном порядке.
К.2.3.5 Испытания рекомендуется проводить при напоре гидротурбины, близком к расчетному.
Испытания всех типов гидротурбин проводят идентично. При этом на ПЛ-гидротурбинах устанавливают комбинаторную связь, соответствующую напору, при котором проводятся испытания.
Для построения эксплуатационной характеристики необходимо иметь результаты испытаний как минимум при трех напорах.
К.2.3.6 При проведении испытаний абсолютным методом должна быть одновременно произведена градуировка расходомерного створа спиральной камеры, которую в последующем используют при проведении испытаний индексным методом.
К.2.3.7 Во время испытаний должны быть приняты меры по поддержанию стабильного режима работы по активной мощности и уровню напряжения на шинах ГЭС.
К.2.4 Порядок проведения испытаний
К.2.4.1 Подготовительные работы:
- изготовление рамной конструкции для установки гидрометрических вертушек;
- монтаж вертушек на раме и разводка кабеля от вертушек до регистрирующего устройства;
- установка при остановленном ГА рамы с вертушками в мерном створе, который выбирается в зависимости от схемы подвода воды к ГЭС либо внутри турбинного трубопровода, либо в водоприемнике;
- проверка и продувка пьезометрических выводов из спиральной камеры, установка и проверка дифманометров и манометров; подключение ваттметра;
- проверка приборов для измерения уровней ВБ и НБ.
К.2.4.2 Проведение измерений:
- на испытуемом агрегате изменяют нагрузку ступенями в 5 % — 7 %. На каждой ступени сохраняют постоянным положение регулирующих органов турбины в течение времени, устанавливаемого рабочей программой испытаний;
- выполняют измерение уровней ВБ и НБ ГЭС, перепада давления и давления на входе в спиральную камеру, активной мощности и положения регулирующих органов, регистрируют показания гидрометрических вертушек.
К.2.4.3 Измерения должны быть проведены не менее чем при десяти различных нагрузках агрегата как для прямого, так и для обратного хода.
162
ГОСТ Р 55260.3.2—2023
Выполнение измерений следует начинать через 2—3 мин после установления нагрузки. При протяженном водоподводящем тракте время выдержки следует увеличить до 5—15 мин. Измерения производят в течение 1—2 мин. При этом определяют среднеинтервальное значение каждого измеряемого параметра.
К.2.4.4 Общая продолжительность испытаний при установке вертушек в трубопроводе составляет 4—6 ч, а при их установке в водоприемнике зависит от числа положений рамы и должно быть уточнено в рабочей программе испытаний.
К.2.4.5 Заключительные операции:
- по окончании испытаний агрегат должен быть остановлен;
- рама с вертушками демонтирована.
К.2.5 Результаты испытаний
К.2.5.1 Оценку технического состояния гидротурбины по результатам энергетических испытаний производят на основании их сравнения с результатами предыдущих испытаний (или заводской эксплуатационной характеристикой):
- по снижению максимального абсолютного КПД;
- изменению формы рабочей характеристики гидротурбины (смещению зоны максимума КПД в сторону больших или меньших мощностей);
- снижению максимальной мощности при том же напоре гидротурбины и открытии НА (для поворотно-лопастных гидротурбин — при отсутствии нарушения комбинаторной связи);
- выявлению во время испытаний при максимальных нагрузках отсутствовавшего ранее «срыва» КПД и мощности.
К.З Энергетические испытания гидроагрегата индексным методом
Испытания индексным методом могут быть применены самостоятельно или совместно с абсолютным методом.
Испытания индексным методом проводят по рабочей программе. Рабочая программа испытаний утверждается техническим руководителем ГЭС и согласовывается с соответствующим диспетчерским центром.
К.3.1 Цель испытаний
Целью энергетических испытаний ГА индексным методом является:
- определение формы рабочей характеристики (при нетарированной спиральной камере) в целях выбора оптимальных режимов работы ГА;
- определение действительных рабочей и расходной характеристик гидротурбины (при тарированной спиральной камере), оценке изменения характеристик действующей гидротурбины в процессе ее эксплуатации;
- проверка гарантий завода по максимальной мощности гидротурбины.
К.3.2 Периодичность и объем испытаний
К.3.2.1 На гидроэлектростанциях необходимо регулярно проводить эксплуатационные энергетические испытания гидротурбин и приемочные испытания вновь вводимых (модернизированных) гидротурбин без непосредственного измерения расходов воды через гидротурбину (индексным методом). Периодичность проведения индексных испытаний определяется условиями эксплуатации. Рекомендуется проведение испытаний индексным методом не реже одного раза в 10 лет, в том числе при вводе гидроагрегатов в работу после КР, связанного с изменениями проточного тракта гидротурбины, при изменении действующих напоров и увеличении мощности гидроагрегата.
К.3.2.2 Испытания индексным методом следует проводить на всех гидроагрегатах ГЭС не менее чем при трех значениях напоров, охватывающих полный диапазон их изменения.
К.3.3 Методика и условия проведения испытаний
К.3.3.1 Испытания должны выполняться в соответствии с требованиями ГОСТ 28842.
К.3.3.2 При индексном методе испытаний измеряется не фактический расход воды, а пропорциональная ему величина. Сущность метода заключается в определении условного или индексного КПД гидротурбины и/или ГА путем измерения фактических значений мощности и напора и условной (индексной) величины расхода воды.
Из-за увеличения погрешности измерения перепада давления индексный метод не рекомендуется применять при расходах гидротурбины менее 50 % от максимального для данного напора.
К.3.3.3 Наибольшее распространение получил способ Винтера-Кеннеди, заключающийся в измерении перепада давления между двумя специально выбранными точками спиральной камеры турбины. При этом принимается, что расход пропорционален корню квадратному из значения перепада давления.
При измерении расхода по способу Винтера-Кеннеди требуется наличие двух пьезометрических выводов в одном и том же радиальном сечении спиральной камеры, расположенном между статорными колоннами. Один вывод размещается на внешнем радиусе спирали, другой — на внутреннем радиусе у статорных колонн. Для повышения надежности измерения перепада обычно размещают несколько пьезометрических выводов.
К.3.3.4 Во время испытаний должны быть приняты меры к поддержанию стабильного режима работы ГЭС по активной мощности. На испытуемом агрегате следует поддерживать постоянное значение coscp = 0.
К.3.3.5 При проведении сравнительных испытаний следует соблюдать условия идентичности: использовать одни и те же пьезометрические выводы из спиральной камеры, одну и ту же измерительную аппаратуру; идентич-
163
ГОСТ Р 55260.3.2—2023
ными должны быть напор и высота отсасывания. Следует также учитывать повышенную погрешность сравнительных испытаний гидротурбин ПЛ-типа с неполноохватной бетонной спиральной камерой.
К.3.4 Порядок проведения испытаний
К.3.4.1 Подготовительные работы:
- проверка и продувка пьезометрических выводов из спиральной камеры турбины, установка и проверка дифманометра и манометров;
- подключение ваттметра для измерения мощности генератора;
- проверка приборов для измерения уровней ВБ и НБ.
К.3.4.2 Проведение измерений:
- на испытуемом агрегате изменяют нагрузку ступенями в 5 % — 7 %;
- на каждой ступени открытие регулирующих органов турбины сохраняют постоянным в течение 3—10 мин, в течение которых выполняют измерение уровней ВБ и НБ, перепада давления и давления на входе в спиральную камеру, активной мощности и положения регулирующих органов.
К.3.4.3 В пределах рабочего диапазона работы турбины устанавливают не менее десяти различных нагрузок.
К.3.4.4 Общая продолжительность испытаний составляет 3—4 ч.
К.3.4.5 Заключительные операции: по завершении испытаний должны быть демонтированы установленные приборы и агрегат сдан оперативному персоналу.
К.3.5 Результаты испытаний
Оценку технического состояния гидротурбины по результатам энергетических испытаний производят на основании их сравнения с результатами предыдущих испытаний (или заводской эксплуатационной характеристикой):
- по снижению максимального относительного КПД;
- по изменению формы рабочей характеристики гидротурбины (смещению зоны максимума КПД в сторону больших или меньших мощностей);
- по снижению максимальной мощности при том же напоре гидротурбины и открытии НА (для ПЛ-гидро-турбин — при отсутствии нарушения комбинаторной связи).
К.4 Определение оптимальной комбинаторной зависимости гидротурбин
Испытания проводят в соответствии с требованиями ГОСТ 28842, по рабочей программе. Рабочая программа испытаний утверждается техническим руководителем ГЭС. При проведении гарантийных испытаний программу согласовывают также с заводом-изготовителем.
К.4.1 Цель испытаний
Целью энергетических испытаний по определению оптимальной комбинаторной зависимости гидротурбин является определение зависимости между открытием НА и углом разворота лопастей РК, обеспечивающей работу гидротурбины при наивысших значениях КПД.
К.4.2 Условия проведения испытаний
Во время испытаний должны быть приняты меры по поддержанию стабильного режима работы гидрогенератора по активной мощности. На испытуемом агрегате следует поддерживать постоянное значение costp. Испытания проводят при работе агрегата под нагрузкой на ручном управлении при разобщенной комбинаторной связи.
К.4.3 Порядок проведения испытаний
К.4.3.1 Подготовительные работы:
- проверка и продувка пьезометрических выводов из спиральной камеры турбины, установка и проверка дифманометра и манометров;
- подключение ваттметра для измерения мощности генератора;
- проверка приборов для измерения уровней ВБ и НБ.
К.4.3.2 Проведение измерений:
- при нескольких постоянных значениях угла разворота лопастей устанавливают различные открытия НА и, наоборот, при нескольких постоянных значениях открытия НА устанавливают различные углы разворота лопастей; каждый установленный режим выдерживают в течение 3—5 мин;
- проводят измерение уровней ВБ и НБ, перепада давления по дифманометру, активной мощности генератора и положения регулирующих органов.
К.4.3.3 Общая продолжительность испытаний составляет 4—6 ч.
К.4.3.4 Заключительные операции
По завершении испытаний должна быть восстановлена комбинаторная связь, демонтированы установленные приборы и агрегат сдан оперативному персоналу.
К.4.4 Результаты испытаний
Эффект оптимизации комбинаторной связи оценивают по разнице в КПД между огибающей и рабочей характеристикой, снятой при установленной комбинаторной связи.
164
ГОСТ Р 55260.3.2—2023
К.5 Методика проведения вибрационных испытаний
К.5.1 Общие положения
К.5.1.1 Вибрационные испытания проводятся по программе, подписанной руководителем испытаний и уполномоченными представителями технических подразделений ГЭС, согласованной при необходимости с территориальным диспетчерским центром и утвержденной техническим руководителем ГЭС.
К.5.1.2 Перед проведением вибрационных испытаний должен быть выполнен визуальный осмотр оборудования на предмет оценки целостности конструкции и наличия видимых дефектов (трещин, расслоений и выкрашивания материала, повышенных люфтов, ослабления крепежа, изменения геометрии или сдвигов отдельных элементов конструкции и пр.). Результаты визуального осмотра фиксируются в соответствии с локальными нормативными актами предприятия (акты, заключения или записи в журнале ремонтов).
К.5.1.3 Оценка вибрационного состояния гидротурбины и механической части генератора осуществляется путем измерения абсолютной вибрации его опорных конструкций и относительных вибраций вала в соответствии с рекомендациями ГОСТ Р ИСО 20816-1, ГОСТ Р ИСО 13373-1, ГОСТ Р ИСО 13373-2, ГОСТ Р ИСО 13373-3, ГОСТ Р 70810.
Оценку вибрационного состояния ГА следует проводить совместно с оценкой вибрации стальных конструкций и лобовых частей обмоток статора в соответствии с ГОСТ Р 55260.2.2.
К.5.2 Контролируемые параметры
К.5.2.1 Контролируемые параметры вибрационного состояния приняты с учетом ГОСТ Р 70810 и представлены в таблицах 6.5, 6.10, 6.11, 6.15—6.17, 6.21,6.24.
К.5.2.2 Для определения общего вибрационного состояния контролю подлежат:
а) осевая абсолютная вибрация:
- крышка турбины;
- грузонесущая крестовины гидрогенератора;
- корпус подшипника, в котором размещен подпятник;
б) радиальная абсолютная вибрация:
- корпус ТП;
- верхняя и нижняя крестовины при размещении в них подшипников;
в) относительные виброперемещения: вал у корпусов направляющих подшипников (виброперемещение вала).
К.5.2.3 В целях уточненной оценки технического состояния или при выявлении неисправностей дополнительно контролируются:
- диск ПП на жесткой опоре (виброперемещение зеркальной поверхности диска ПП);
- упругая камера ПП на гидравлической опоре (просадка и вертикальные колебания упругой камеры);
- крышка турбины в районе лопаток НА относительно стенки шахты турбины в осевом направлении для вертикальных ГА.
К.5.2.4 Контроль осуществляется:
1) для широкополосной вибрации — вибрации в широком диапазоне частот без анализа частотных составляющих и их фаз:
- в диапазоне 0,8—30,0 Гц для абсолютной вибрации;
- в диапазоне 0—20 Гц для относительной вибрации;
2) для отдельных частотных составляющих с учетом фаз (в диапазоне от 0,8 Гц до 200 Гц и выше при необходимости):
- низкочастотные вибрации (ниже 1 Гц);
- оборотная и кратные ей частоты;
- частота осевых колебаний агрегата;
- лопастная частота (произведение количества лопастей РК на оборотную частоту);
- лопаточная частота (произведение количества лопаток НА на оборотную частоту);
- полюсная частота гидрогенератора (100 Гц);
- частоты гидравлических явлений и эффектов (пульсации давления в водоводе, в межлопастных каналах рабочего колеса, высокочастотные колебания, связанные со сходом вихрей Кармана с выходных кромок обтекаемых элементов проточной части и т. п.);
- собственные частоты опорных конструкций и/или основных элементов гидроагрегата.
К.5.2.5 При необходимости объем контроля может быть расширен (включая измерения таких параметров, как пульсации давления, перемещения и деформации узлов и элементов агрегата и т. п.) на основании результатов обследования с выработкой рекомендаций по определению специфических неисправностей оборудования, выявление которых возможно методами вибрационной диагностики.
К.5.2.6 В целях уточненной оценки технического состояния ГА и оценки стабильности агрегата рекомендуется дополнительно использовать векторное представление вибрации или проводить анализ траектории движения вала, который позволяет на крупных ГА с подшипниками скольжения контролировать положение вала внутри подшипника и зазор между подшипником и валом.
165
ГОСТ Р 55260.3.2—2023
Информация об изменении вектора вибрации особенно полезна в целях обнаружения и идентификации изменений динамического поведения ГА. Правильная интерпретация орбиты прецессии вала позволяет понять природу вынуждающих сил.
К.5.2.7 По указанию завода-изготовителя перечень контролируемых параметров может быть изменен.
К.5.3 Критерии оценки
К.5.3.1 Критерий вибрационного состояния — это максимальное значение широкополосной вибрации, полученное в результате измерений на каждом подшипнике или опоре. Критерий вибрационного состояния сравнивают с границами принятых зон вибрационного состояния.
К.5.3.2 Установленные зоны вибрационного состояния предназначены для качественной оценки вибрации машины в установившемся режиме работы на номинальной частоте вращения и принятия решения о необходимых мерах. Числовые значения границ зон определяются на основе опыта эксплуатации.
Границы зон по критерию широкополосной вибрации для неподвижных частей ГА представлены в К.5.8.
К.5.3.3 Основные методы обработки и представления результатов измерений вибрации, анализа вибрационных характеристик в целях вибрационного контроля состояния машин, а также процедуры, применяемые при организации диагностирования машин по параметрам вибрации, представлены в ГОСТ Р ИСО 13373-2 и ГОСТ Р ИСО 13373-3.
К.5.3.4 Для оценки вибрационного состояния в соответствии с рекомендациями ГОСТ Р ИСО 20816-1 используют два типа критериев:
- абсолютное значение контролируемых параметров (Критерий I);
- изменения параметра вибрации (Критерий II).
К.5.3.5 Критерий I — параметр вибрации при номинальной частоте вращения в установившемся режиме работы агрегата.
К.5.3.6 Критерий II — изменения параметра вибрации, тенденция изменения значений по Критерию I, независимо от того, в какую сторону происходит изменение. Данный критерий основан на оценке изменения значения параметра вибрации при работе в установившемся режиме, по сравнению с предварительно заданным опорным значением.
Существенные изменения (увеличение или уменьшение) значения параметра широкополосной вибрации могут потребовать принятия определенных мер даже в том случае, когда в соответствии с Критерием I еще не достигнута граница зоны, когда агрегат может рассматриваться как непригодный для длительной непрерывной работы. При значениях вибрации более 80 % границы зоны «удовлетворительно» по критериям К.5.8.4, а также отклонениях в вибрационных характеристиках по неизвестной причине требуется производить анализ вибрации с целью определения предполагаемой причины изменения вибрационного состояния.
Изменения могут носить скачкообразный характер или постепенно нарастать во времени (наличие тенденции), указывая на возможное возникновение повреждения агрегата, что позволяет прогнозировать техническое состояние в соответствии с ГОСТ Р ИСО 13381-1.
При использовании критерия II важно, чтобы измерения значений параметров вибрации, подлежащих сравнению, проводили при одних и тех же положении и ориентации преобразователя вибрации и приблизительно в одном и том же режиме работы агрегата. Рекомендуется проводить сравнения при близких значениях мощности, открытия направляющего аппарата, величин напоров и глубин отсасывания, температур подшипников, а в случае водяной смазки турбинного подшипника — температурой воды. Следует иметь в виду, что некоторые существенные изменения в состоянии агрегата могут быть обнаружены только при контроле отдельных частотных составляющих.
К.5.4 Средства измерения
К.5.4.1 Аппаратура, используемая для измерения вибрации, должна быть выполнена на базе микропроцессорных устройств с возможностью измерения, записи, анализа вибросигналов по нескольким параллельным каналам с возможностью разложения сигнала в спектр.
К.5.4.2 Основные технические требования к аппаратуре, используемой для измерения вибрации элементов ГА, приведены в ГОСТ Р ИСО 13373-1, ГОСТ Р 70810.
К.5.4.3 Используемая аппаратура должна позволять определять следующие параметры:
- среднее квадратическое отклонение сигнала вибрации;
- размах вибрации за определенный промежуток времени;
- спектральные составляющие сигнала.
К.5.4.4 Используемая аппаратура должна быть аттестована или подвергаться регулярной калибровке.
К.5.5 Периодичность испытаний
К.5.5.1 Измерение вибрации ГА должно проводиться до и после каждого КР с целью уточнения необходимых объемов ремонтных работ и подтверждения эффективности выполненных ремонтов, модернизаций или реконструкций.
К.5.5.2 В межремонтный период необходимость проведения измерений и осмотров устанавливается в зависимости от результатов предыдущих обследований и при возникших предположениях об изменении (ухудшении) вибрационного состояния агрегата.
Решение о проведении внеочередных технических обследований принимает технический руководитель ГЭС.
166
ГОСТ Р 55260.3.2—2023
К.5.6 Условия испытаний
К.5.6.1 Измерения абсолютной и относительной вибрации узлов ГА желательно производить в одних и тех же точках (рекомендуется отмечать их на корпусе ГА краской или маркером) с помощью датчиков с одинаковыми техническими и метрологическими характеристиками, по возможности одними и теми же датчиками.
К.5.6.2 Общие требования к креплению датчиков для измерения абсолютной и относительной вибрации представлены в ГОСТ ИСО 5348, ГОСТ ИСО 10817-1 и ГОСТ Р 70810.
Датчики абсолютной вибрации следует располагать вдали от ребер жесткости конструктивных элементов или в средней части ребер жесткости.
При выборе местоположения датчиков необходимо учитывать опыт эксплуатации ГА. В случаях наблюдения характерных или повторяющихся дефектов (люфтов, снижение жесткостей, креплений и т. п.), наличие которых может быть идентифицировано с помощью результатов вибрационного контроля, следует располагать датчики вибрации (при необходимости устанавливаются дополнительные датчики) таким образом, чтобы иметь возможность определить наличие этих дефектов по результатам вибрационных измерений.
К.5.7 Результаты испытаний
К.5.7.1 Результаты вибрационных испытаний необходимо фиксировать в протоколах с четким указанием места измерения вибрации, применявшейся аппаратуры, параметров вибрации (частота, размахи) и всех параметров режима работы гидрогенератора (активная и реактивная мощности, напряжение и ток статора, ток ротора, температура меди обмотки и сердечника статора, уровни бьефов, открытие НА, углы установки лопастей РК, температуры сегментов подшипников).
К.5.7.2 По результатам измерений вибрации должно быть составлено заключение с оценкой вибрационного состояния ГА и соответствующими рекомендациями.
К.5.8 Оценка уровня вибрации
К.5.8.1 Контроль вибрационного состояния опорных частей и вала ГА должен выполняться при работе ГА в диапазоне установившихся нагрузочных рабочих режимов и в режиме XX. Оценка проводится отдельно для каждого установившегося рабочего режима, разрешенного для длительной эксплуатации ГА. Оценка вибрационного состояния ГА соответствует наихудшей из полученных оценок, при этом для анализа вибрационного состояния следует выбирать участок записи сигнала с наибольшими амплитудами/размахами.
Для режимов работы, на которых не допускается длительная эксплуатация ГА, оценка вибрационного состояния может проводиться по той же методике, но не учитываться в общей оценке вибрационного состояния ГА, что указывается в протоколе вибрационных испытаний.
Измерение вибрационных параметров рекомендуется производить при следующих режимах работы гидроагрегата:
- холостой ход без возбуждения с частотами вращения ротора 0.8, 0.9, 1.0 и 1.1 от номинальной;
- холостой ход с номинальным возбуждением и при номинальной частоте вращения;
- параллельная работа с сетью при нагрузках от нуля до номинальной, изменяемая ступенями по 10—20 % от номинальной нагрузки;
- режим синхронного компенсатора (с камерой рабочего колеса, освобожденной от воды);
- выбег гидроагрегата после отключения от сети из режима синхронного компенсатора при освобожденной от воды камере рабочего колеса; при отсутствии на ГЭС режима синхронного компенсатора с освобожденной от воды камерой рабочего колеса измерения производят при выбеге из генераторного режима.
К.5.8.2 Вибрационное состояние опорных частей и вала ГА в неустановившихся режимах не нормируется.
Из анализа исключаются неустановившиеся (переходные) режимы работы ГА:
- пуск;
- включение в сеть;
- изменение нагрузки;
- короткое замыкание генератора;
- останов;
- перевод из генераторного в режим СК и обратно;
- разгонный режим;
- сброс нагрузки.
К.5.8.3 Контроль значений относительных вибраций ГА следует выполнять сравнением результатов измерения с предельными значениями, установленными в руководстве по эксплуатации, выпущенном заводом — изготовителем гидротурбины и гидрогенератора, или величинами, определенными в ходе натурных испытаний или на основе опыта эксплуатации.
Предельные значения относительной вибрации указывают в стандарте организации ГЭС для каждого из контролируемых узлов.
К.5.8.4 Контроль абсолютных виброперемещений опорных частей, если иное не указано в руководстве по эксплуатации гидротурбины, выполняется по размаху спектральных составляющих виброперемещения в зависимости от частоты в диапазоне частот 1—30 Гц (см. рисунок К.5.1).
При частоте более 30 Гц недопустимым считается размах более 40 мкм, при частоте менее 1 Гц — 180 мкм.
167
ГОСТ Р 55260.3.2—2023
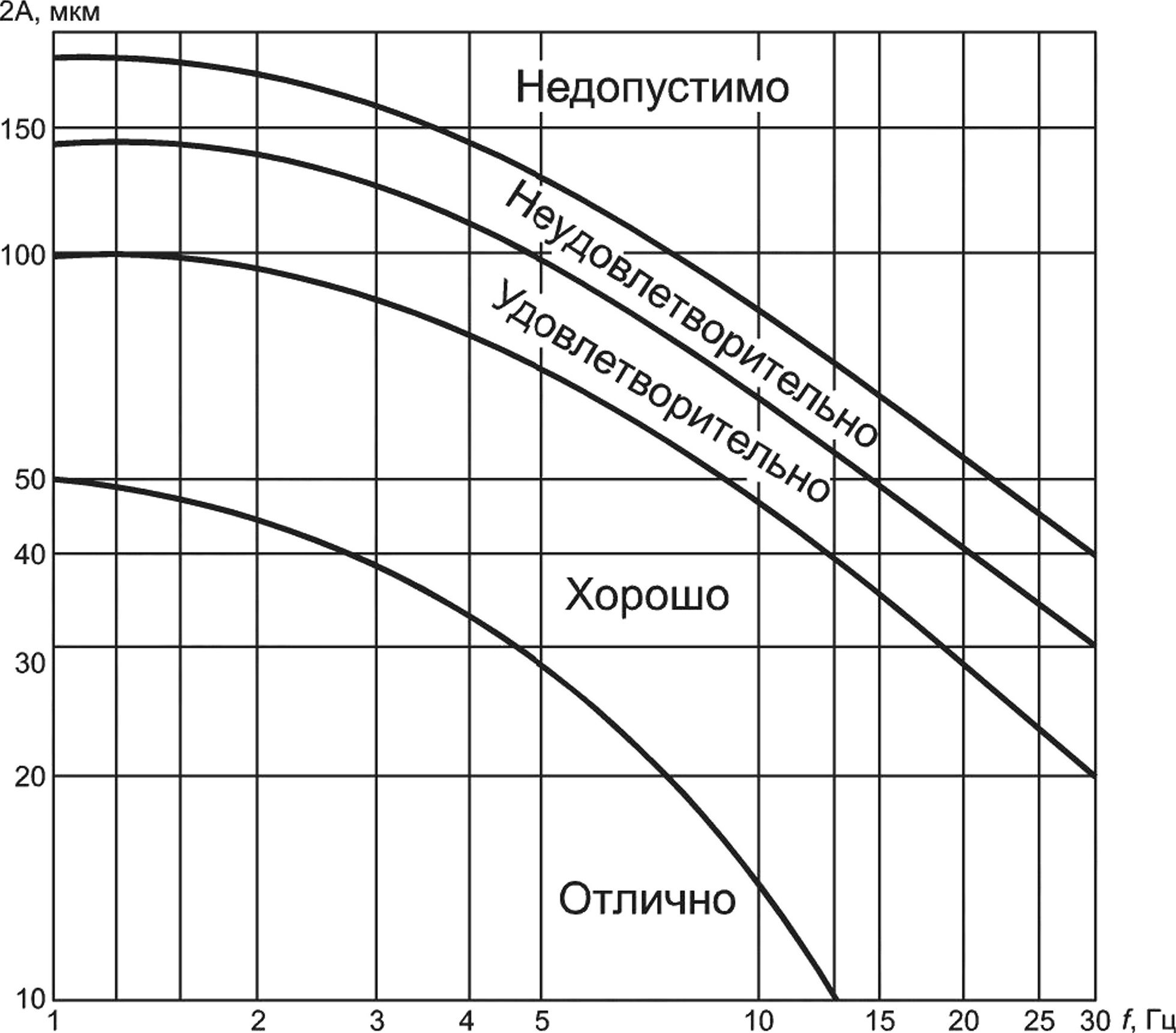
Рисунок К.5.1 — Оценка вибрации опорных конструкций ГА
К.5.8.5 При периодической вибрации оценка проводится по среднему размаху виброперемещения с использованием зависимостей, приведенных на рисунке К.5.1.
Средний размах виброперемещений 2Аср, определенный по отклонению СКО, рассчитывают по формуле
2Acp=2V2CKO. (К.1)
Интервал времени должен быть выбран таким, чтобы на нем было не менее десяти периодов оборотной частоты.
При этом оценка среднего размаха виброперемещения проводится по нормам для низшей из составляющих частот, как правило, оборотной или лопастной. Из всех оценок принимается худшая.
К.5.8.6 При непериодической вибрации оценка вибрационного состояния проводится по среднему размаху и средней частоте с использованием зависимостей, приведенных на рисунке К.5.1. Средний размах определяется по формуле К.1. Среднюю частоту определяют как величину, при которой наблюдается максимальный размах виброперемещений спектральных составляющих. Если это невозможно, допускается среднюю частоту определять как отношение половины числа пиков за выбранный интервал времени к этому интервалу.
В протоколе с результатами контроля вибрации, кроме среднего размаха виброперемещений, должен быть указан также максимальный размах виброперемещений на выбранном интервале времени. Максимальный размах виброперемещений носит информационный характер.
Зачастую непериодический характер вибрации вызван гидродинамическими явлениями в проточной части гидротурбины и может носить определенную периодичность, которую невозможно выявить за 10 оборов ротора гидроагрегата. В этом случае рекомендуется увеличить время измерений и длину обрабатываемого сигнала с обязательным указанием этого в протоколе измерения.
В случаях наблюдения ударов, зафиксированных средствами вибрационного контроля, в протоколе измерений следует указать их количество, максимальный размах виброперемещений и время, в течение которого фиксировались указанные удары. В случае ударных явлений в проточной части гидроагрегата частоты, на которых будут наблюдаться затухания размаха вибрации, будут близки к собственным частотам опорных конструкций гидроагрегата.
168
ГОСТ Р 55260.3.2—2023
К.5.8.7 Типовые решения, принимаемые на основе оценки вибрационного состояния конструктивных узлов ГА, приведены в таблице К.5.1.
Таблица К.5.1—Типовые решения
Оценка вибрационного состояния | Решение |
«Отлично» | Периодичность измерений вибрации не реже одного раза в 6 лет |
«Хорошо» | Периодичность измерений вибрации один раз в 3 года |
«Удовлетворительно» | Периодичность измерений вибрации один раз в год. При значениях вибрации более 80 % границы зоны «Удовлетворительно», а также отклонения в вибрационных характеристиках по неизвестной причине необходимо произвести анализ данных и определить предполагаемую причину изменения вибрационного состояния. При сомнении в достоверности измерений необходимо организовать проведение проверки наличия повышенной вибрации и достоверности измерений |
«Неудовлетворительно» | Устранение повышенной вибрации при первой возможности. До устранения повышенной вибрации проводить контроль вибрации не реже одного раза в 2 месяца. Необходимо уточнить зоны, не рекомендуемые для длительной работы гидроагрегата |
«Недопустимо» | Эксплуатация агрегата без особого разрешения технического руководителя генерирующей компании не допускается. В случае продолжения эксплуатации по решению технического руководителя генерирующей компании необходимо установить зоны, запрещенные для работы ГА |
169
ГОСТ Р 55260.3.2—2023
Библиография
Методика оценки технического состояния основного технологического оборудования и линий электропередачи электрических станций и электрических сетей (утверждена приказом Минэнерго России от 26 июля 2017 г. № 676)
Правила организации технического обслуживания и ремонта объектов электроэнергетики (утверждены приказом Минэнерго России от 25 октября 2017 г. № 1013)
Правила проведения технического освидетельствования оборудования, зданий и сооружений объектов электроэнергетики (утверждены приказом Минэнерго России от 14 мая 2019 г. № 465)
Методические указания по расчету вероятности отказа функционального узла и единицы основного технологического оборудования и оценки последствий такого отказа (утверждены приказом Минэнерго России от 19 февраля 2019 г. № 123)
Правила по охране труда при эксплуатации электроустановок (утверждены приказом Министерства труда и социальной защиты Российской Федерации от 15 декабря 2020 г. № 903н)
Правила технической эксплуатации электроустановок потребителей (утверждены Приказом Минэнерго России от 12 августа 2022 г. № 811)
СО 153-34.20.161—2003 | Рекомендации по проектированию технологической части гидроэлектростанций и гидроаккумулирующих электростанций |
РД 34.11.115—97 РД 34.11.101—96 | Положение о системе калибровки средств измерений в электроэнергетике Методические указания. Планирование работ по метрологическому обеспечению производства в отрасли «Электроэнергетика». Организация и порядок проведения |
МЭК 60193:2019 | Гидравлические турбины, аккумулирующие насосы и турбонасосы. Приемочные испытания на модели (Hydraulic turbines, storage pumps and pump-turbines — Model acceptance tests) |
РД 34.17.415—96 | Инструкция по проведению ультразвукового контроля крепежа энергооборудования |
Технические условия на монтаж гидроагрегатов (утверждены Минэнерго СССР от 30 апреля 1974 г. № 117)
СДАН К-01—2020 | Правила аттестации и основные требования к лабораториям неразрушающего контроля |
СДАН К-02—2020 РД 13-06—2006 | Правила аттестации персонала в области неразрушающего контроля Методические рекомендации о порядке проведения капиллярного контроля технических устройств и сооружений, применяемых и эксплуатируемых на опасных производственных объектах |
РД 13-03—2006 | Методические рекомендации о порядке проведения вихретокового контроля технических устройств и сооружений, применяемых и эксплуатируемых на опасных производственных объектах |
РД 13-05—2006 | Методические рекомендации о порядке проведения магнитопорошкового контроля технических устройств и сооружений, применяемых и эксплуатируемых на опасных производственных объектах |
РД 24.122.14—89 | Методы расчета на прочность рабочих колес гидравлических радиально-осевых турбин |
РД 24.122.15—89 | Методы расчета на усталостную прочность лопастей гидравлических поворотнолопастных турбин |
РД 153-34.2-31.604—2002 | Рекомендации по ремонту и реконструкции камер колес гидроагрегатов с целью повышения их эксплуатационной надежности |
170
УДК 621.224:006.354
ГОСТ Р 55260.3.2—2023
ОКС 27.140
Ключевые слова: гидроэлектростанция, гидроагрегат, гидротурбина, техническое состояние, методики оценки, методы контроля, дефект, трещина
Редактор Е.Ю. Митрофанова Технический редактор И.Е. Черепкова
Корректор Е.Д- Дульнева Компьютерная верстка И.Ю. Литовкиной
Сдано в набор 24.11.2023. Подписано в печать 19.12.2023. Формат 60x84%. Гарнитура Ариал.
Усл. печ. л. 20,00. Уч-изд. л. 17,05.
Подготовлено на основе электронной версии, предоставленной разработчиком стандарта
Создано в единичном исполнении в ФГБУ «Институт стандартизации» , 117418 Москва, Нахимовский пр-т, д. 31, к. 2.