ФЕДЕРАЛЬНОЕ АГЕНТСТВО ПО ТЕХНИЧЕСКОМУ РЕГУЛИРОВАНИЮ И МЕТРОЛОГИИ
пнет 683—
2023
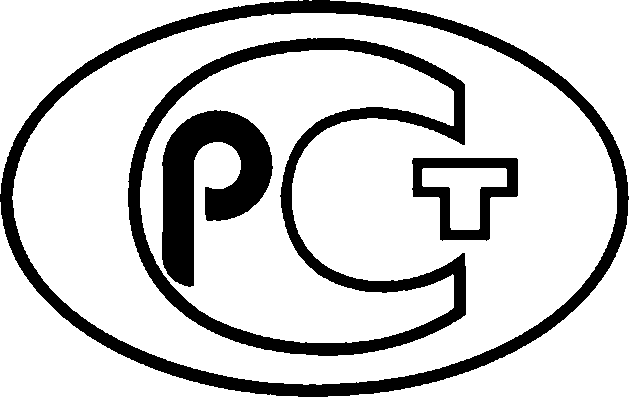
ПРЕДВАРИТЕЛЬНЫЙ НАЦИОНАЛЬНЫЙ СТАНДАРТ РОССИЙСКОЙ ФЕДЕРАЦИИ
Нефтяная и газовая промышленность
СИСТЕМЫ ПОДВОДНОЙ ДОБЫЧИ
Трубы из аустенито-ферритной коррозионно-стойкой стали. Технические условия
Издание официальное
Москва Российский институт стандартизации 2023
Предисловие
1 РАЗРАБОТАН Обществом с ограниченной ответственностью «Газпром 335» (ООО «Газпром 335»)
2 ВНЕСЕН Техническим комитетом по стандартизации ТК 023 «Нефтяная и газовая промышленность»
3 УТВЕРЖДЕН И ВВЕДЕН В ДЕЙСТВИЕ Приказом Федерального агентства по техническому регулированию и метрологии от 13 января 2023 г. № 3-пнст
Правила применения настоящего стандарта и проведения его мониторинга установлены в ГОСТР 1.16—2011 (разделы 5 и 6).
Федеральное агентство по техническому регулированию и метрологии собирает сведения о практическом применении настоящего стандарта. Данные сведения, а также замечания и предложения по содержанию стандарта можно направить не позднее чем за 4 мес до истечения срока его действия разработчику настоящего стандарта по адресу: inf@gazprom335.ru и/или в Федеральное агентство по техническому регулированию и метрологии по адресу: 123112 Москва, Пресненская набережная, д. 10, стр. 2.
В случае отмены настоящего стандарта соответствующая информация будет опубликована в ежемесячном информационном указателе «Национальные стандарты» и также будет размещена на официальном сайте Федерального агентства по техническому регулированию и метрологии в сети Интернет (www.rst.gov.ru)
© Оформление. ФГБУ «Институт стандартизации», 2023
Настоящий стандарт не может быть полностью или частично воспроизведен, тиражирован и распространен в качестве официального издания без разрешения Федерального агентства по техническому регулированию и метрологии
Содержание
1 Область применения
2 Нормативные ссылки
3 Термины и определения
го го
4 Обозначения .........
5 Технические требования
6 Требования безопасности и охраны окружающей среды
7 Правила приемки и методы испытаний
8 Транспортирование и хранение
Библиография
Введение
Настоящий предварительный стандарт разработан в составе комплекса национальных стандартов в области технологий и оборудования для подводной добычи углеводородов, устанавливающих требования к проектированию и строительству систем подводной добычи. Формирование комплекса стандартов систем подводной добычи углеводородов, в соответствии с основами национальной стандартизации и принципами гармонизации документов национальной системы стандартизации с международной, осуществляется на основе применения международных стандартов, отражающих передовой зарубежный опыт, лучшие мировые практики и современные методики проектирования.
Целью разработки настоящего стандарта является установление минимальных требований для труб из аустенито-ферритных нержавеющих сталей, применяемых в системах подводной добычи углеводородов.
ПРЕДВАРИТЕЛЬНЫЙ НАЦИОНАЛЬНЫЙ СТАНДАРТ РОССИЙСКОЙ ФЕДЕРАЦИИ
Нефтяная и газовая промышленность
СИСТЕМЫ ПОДВОДНОЙ ДОБЫЧИ
Трубы из аустенито-ферритной коррозионно-стойкой стали. Технические условия
Petroleum and natural gas industry. Subsea production systems. Austenitic-ferritic corrosion-resistant steel pipes. Specifications
Срок действия — с 2023—06—30 до 2026—06—30
1 Область применения
Настоящий предварительный стандарт распространяется на бесшовные и электросварные прямошовные трубы из аустенито-ферритных нержавеющих сталей, применяемых в системах подводной добычи углеводородов.
2 Нормативные ссылки
В настоящем стандарте использованы нормативные ссылки на следующие стандарты:
ГОСТ 3845 Трубы металлические. Метод испытания внутренним гидростатическим давлением
ГОСТ 6032 (ISO 3651-1:1998, ISO 3651-2:1998) Стали и сплавы коррозионно-стойкие. Методы испытаний на стойкость против межкристаллитной коррозии
ГОСТ 6507 Микрометры. Технические условия
ГОСТ 6996 (ИСО 4136—89, ИСО 5173—81, ИСО 5177—81) Сварные соединения. Методы определения механических свойств
ГОСТ 7565 (ИСО 377-2—89) Чугун, сталь и сплавы. Метод отбора проб для определения химического состава
ГОСТ 8693 (ISO 8494:2013) Трубы металлические. Метод испытания на бортование
ГОСТ 8694 (ISO 8493:1998) Трубы металлические. Метод испытания на раздачу
ГОСТ 8695 (ISO 8492:2013) Трубы металлические. Метод испытания на сплющивание
ГОСТ 9012 (ИСО 410—82, ИСО 6506—81) Металлы. Метод измерения твердости по Бринеллю
ГОСТ 9013 (ИСО 6508—86) Металлы. Метод измерения твердости по Роквеллу
ГОСТ 9454 Металлы. Метод испытания на ударный изгиб при пониженных, комнатной и повышенных температурах
ГОСТ 9940 Трубы бесшовные горячедеформированные из коррозионно-стойкой стали. Технические условия
ГОСТ 9941 Трубы бесшовные холодно- и теплодеформированные из коррозионно-стойкой стали. Технические условия
ГОСТ 10006 (ИСО 6892—84) Трубы металлические. Метод испытания на растяжение
ГОСТ 10243 Сталь. Методы испытаний и оценки макроструктуры
ГОСТ 10692 Трубы стальные, чугунные и соединительные детали к ним. Приемка, маркировка, упаковка, транспортирование и хранение
ГОСТ 11068 Трубы электросварные из коррозионно-стойкой стали. Технические условия
Издание официальное
ГОСТ 11358 Толщиномеры и стенкомеры индикаторные с ценой деления 0,01 и 0,1 мм. Технические условия
ГОСТ 16504 Система государственных испытаний продукции. Испытания и контроль качества продукции. Основные термины и определения
ГОСТ 28548 Трубы стальные. Термины и определения
ГОСТ 30432 Трубы металлические. Методы отбора проб, заготовок и образцов для механических и технологических испытаний
ГОСТ 31458—2015 (ISO 10474:2013) Трубы стальные, чугунные и соединительные детали к ним. Документы о приемочном контроле
ГОСТ 33439 Металлопродукция из черных металлов и сплавов на железо никеле вой и никелевой основе. Термины и определения по термической обработке
ГОСТ 34094 (ISO 6761:1981) Трубы стальные. Отделка концов труб и соединительных деталей под сварку. Общие технические требования
ГОСТ Р 58904 (ISO/TR 25901:2016) Сварка и родственные процессы. Словарь. Часть 1. Общие термины
ГОСТ Р ИСО 4063 Сварка и родственные процессы. Перечень и условные обозначения процессов
ГОСТ Р ИСО 10893-2 Трубы стальные бесшовные и сварные. Часть 2. Автоматизированный контроль вихретоковым методом для обнаружения дефектов
ГОСТ Р ИСО 10893-11 Трубы стальные бесшовные и сварные. Часть 11. Ультразвуковой метод автоматизированного контроля сварных швов для обнаружения продольных и (или) поперечных дефектов
ГОСТ Р ИСО 17659 Сварка. Термины многоязычные для сварных соединений
ГОСТ ISO 10893-10 Трубы стальные бесшовные и сварные. Часть 10. Ультразвуковой метод автоматизированного контроля для обнаружения продольных и (или) поперечных дефектов по всей поверхности
Примечание — При пользовании настоящим стандартом целесообразно проверить действие ссылочных стандартов в информационной системе общего пользования — на официальном сайте Федерального агентства по техническому регулированию и метрологии в сети Интернет или по ежегодному информационному указателю «Национальные стандарты», который опубликован по состоянию на 1 января текущего года, и по выпускам ежемесячного информационного указателя «Национальные стандарты» за текущий год. Если заменен ссылочный стандарт, на который дана недатированная ссылка, то рекомендуется использовать действующую версию этого стандарта с учетом всех внесенных в данную версию изменений. Если заменен ссылочный стандарт, на который дана датированная ссылка, то рекомендуется использовать версию этого стандарта с указанным выше годом утверждения (принятия). Если после утверждения настоящего стандарта в ссылочный стандарт, на который дана датированная ссылка, внесено изменение, затрагивающее положение, на которое дана ссылка, то это положение рекомендуется применять без учета данного изменения. Если ссылочный стандарт отменен без замены, то положение, в котором дана ссылка на него, рекомендуется применять в части, не затрагивающей эту ссылку.
3 Термины и определения
В настоящем стандарте применены термины по ГОСТ 16504, ГОСТ 28548, ГОСТ 33439, ГОСТ Р 58904 и ГОСТ Р ИСО 17659, а также следующий термин с соответствующим определением:
3.1 аустенито-ферритная сталь (austenitic/ferritic stainless steel): Коррозионно-стойкая сталь с двухфазной структурой аустенита и феррита.
4 Обозначения
В настоящем стандарте использованы следующие обозначения:
HBW — твердость металла по Бринеллю при применении шарика из твердого сплава;
HRC — твердость металла по Роквеллу, шкала С;
UNS (unified numbering system) — универсальная система обозначений металлов и сплавов AISI (American Iron and Steel Institute).
5 Технические требования
5.1 Основные показатели
5.1.1 Трубы изготовляют по наружному диаметру и толщине стенки со следующими размерами:
- бесшовные горячедеформированные — по ГОСТ 9940;
- бесшовные холоднодеформированные — по ГОСТ 9941;
- электросварные трубы — по ГОСТ 11068.
5.1.2 По согласованию изготовителя с заказчиком трубы допускается изготавливать по внутреннему диаметру и толщине стенки.
5.1.3 По согласованию изготовителя с заказчиком допускается изготовление труб размерами, не предусмотренными в 5.1.1.
5.1.4 По длине трубы изготовляют:
- немерной длины от 1,5 до 12,5 м;
- мерной длины — в пределах немерной, с предельным отклонением по длине 15 мм. Величина мерной длины должна быть согласована между изготовителем и заказчиком;
- длины, кратной мерной — в пределах мерной длины, с припуском на каждый рез по 5 мм и предельным отклонением по всей длине 15 мм.
По согласованию изготовителя с заказчиком допускается изготовление труб длиной, не предусмотренной настоящим стандартом.
5.2 Сведения, указанные в заказе
5.2.1 В заказе на трубы необходимо указывать следующие сведения:
- вид труб (бесшовные горячедеформированные или холоднодеформированные, сварные) (см. 5.3.1, 5.3.2);
- обозначение настоящего предварительного стандарта;
- размер (наружный или внутренний диаметр и толщину стенки) (см. 5.1.1, 5.1.2);
- вид длины (мерная, кратная или немерная) и длину кратных или мерных труб (см. 5.1.4);
- обозначение стали (см. 5.5.1);
- количество (в метрах, тоннах или штуках).
5.2.2 В заказе на трубы могут быть указаны дополнительные требования:
- размер труб, не предусмотренный настоящим стандартом (см. 5.1.3);
- длина труб, не предусмотренная настоящим стандартом (см. 5.1.4);
- требования к качеству поверхности, не предусмотренные настоящим стандартом (см. 5.4.6);
- исполнение поверхности: механически обработанная наружная поверхность, электрохимически полированные или после термической обработки в безокислительной атмосфере наружная и внутренняя поверхности (см. 5.4.2);
- режим термической обработки, не предусмотренный настоящим стандартом (см. 5.6.3);
- закалка труб на воздухе с принудительным охлаждением аэраторами (см. 5.6.2);
- требования к механическим свойствам металла труб, не предусмотренные настоящим стандартом (см. 5.7.2);
- проведение контроля макроструктуры металла труб и критерии приемки (см. 5.9.1);
- проведение контроля микроструктуры металла труб и нормативные значения контролируемых параметров (см. 5.9.2);
- предельные отклонения внутреннего диаметра (см. 5.12.2);
- требования к овальности, не предусмотренные настоящим стандартом (см. 5.12.4);
- требования к прямолинейности, не предусмотренные настоящим стандартом (см. 5.12.6);
- объем контроля и испытаний, правила проведения повторных испытаний и термообработки, не предусмотренные настоящим стандартом (см. 7.1.2, 7.1.3);
- уровень приемки при ультразвуковом контроле или вихретоковом контроле, не предусмотренный настоящим стандартом (см. 7.11.4);
- на трубах номинальной толщиной стенки 6 мм и более необходимо определить работу удара на образцах с концентратором вида V при температуре испытания минус 46 °C. Средняя величина работы удара, определенная при испытании трех образцов, должна составлять не менее 45 Дж. На одном образце допускается снижение величины работы удара до 35 Дж;
- испытание на ударный изгиб металла бесшовных труб, а также основного металла сварных труб проводят по ГОСТ 9454:
- на поперечных образцах труб диаметром 219 мм и более;
- на продольных образцах труб диаметром менее 219 мм;
- испытание на ударный изгиб металла сварного соединения сварных труб проводят по ГОСТ 6996. Надрез на ударных образцах выполняют перпендикулярно к поверхности исходного проката по центру шва. Образцы для испытаний на ударный изгиб должны быть отобраны от двух труб партии;
- на металле труб следует проводить испытания коррозионной стойкости со следующими критериями приемки:
- отсутствие питтинговой коррозии при 20-кратном увеличении;
- потеря массы менее 4 г/м2;
- испытания коррозионной стойкости допускается выполнть в соответствии с [1], при температуре 50 °C и времени воздействия 24 ч. Травление осуществляется в растворе, содержащем 20 % HNO3 + 5 % HF в течение 5 мин при температуре 60 °C. Испытания на определение коррозионной стойкости следует проводить на одном образце, отобранном от одной трубы партии.
5.3 Способ производства
5.3.1 Трубы изготавливают бесшовными или сваренными автоматизированной сваркой без присадочных материалов.
5.3.2 Бесшовные трубы могут поставляться горячедеформированными или холоднодеформиро-ванными.
5.3.3 Для изготовления сварных труб (продольный сварной шов) допускаются следующие процессы сварки: лазерная (номер процесса «522» согласно ГОСТ Р ИСО 4063) либо аргонодуговая сварка не-плавящимся электродом без использования присадочного материала (номер процесса «142» согласно ГОСТ Р ИСО 4063).
5.4 Качество поверхности
5.4.1 Поверхность труб должна быть обработана травлением, а также очищена от окалины.
5.4.2 По согласованию изготовителя и заказчика трубы поставляют:
- с электрохимически полированной поверхностью;
- с механически обработанной наружной поверхностью после шлифования или точения;
- с поверхностью после термической обработки в безокислительной атмосфере.
5.4.3 Наружная и внутренняя поверхности труб не допускают наличие трещин, плен, рванин, раковин, волосовин, закатов, вмятин, прижогов, травильной сыпи. Допускаются местная зачистка указанных дефектов или сплошная шлифовка, обточка, расточка при условии, что толщина стенки труб не будет выходить за допустимые значения.
5.4.4 Шероховатость в местах зачистки должна быть не более, чем шероховатость остальной поверхности трубы.
5.4.5 Поверхность труб может быть матовой и с цветами побежалости.
5.4.6 По согласованию между изготовителем и заказчиком могут быть установлены другие требования к качеству поверхности.
5.4.7 Наружный грат сварного шва сварных труб необходимо удалить. Высота внутреннего грата сварных труб не должна превышать 0,7 мм. Переход от грата к стенкам трубы должен быть плавным.
5.5 Химический состав
5.5.1 Трубы изготовляют из сталей с химическим составом, указанным в таблице 1.
Таблица 1 — Требования к химическому составу аустенито-ферритных сталей по ковшовой пробе согласно [2]
Обозначение стали | С | Мп | Р | S | Si | Ni | Сг | Мо | N | Си | Другие | |
UNS | AISI | % масс, (не более или в пределах) | ||||||||||
S31200 | — | 0,030 | 2,00 | 0,045 | 0,030 | 1,00 | 5,50—6,50 | 24,0—26,0 | 1,20—2,00 | 0,14—0,20 | — | — |
S31260 | — | 0,030 | 1,00 | 0,030 | 0,030 | 0,75 | 5,50—7,50 | 24,0—26,0 | 2,50—3,50 | 0,10—0,30 | 0,20—0,80 | W 0,10—0,50 |
S31500 | — | 0,030 | 1,20—2,00 | 0,030 | 0,030 | 1,40—2,00 | 4,20—5,20 | 18,0—19,0 | 2,50—3,00 | 0,05—0,10 | — | — |
S31803 | — | 0,030 | 2,00 | 0,030 | 0,020 | 1,00 | 4,50—6,50 | 21,0—23,0 | 2,50—3,50 | 0,08—0,20 | — | — |
S32003 | — | 0,030 | 2,00 | 0,030 | 0,020 | 1,00 | 3,00^,00 | 19,5—22,5 | 1,50—2,00 | 0,14—0,20 | — | — |
S32101 | — | 0,040 | 4,00—6,00 | 0,040 | 0,030 | 1,00 | 1,35—1,70 | 21,0—22,0 | 0,10—0,80 | 0,20—0,25 | 0,10—0,80 | — |
S32202 | — | 0,030 | 2,00 | 0,040 | 0,010 | 1,00 | 1,00—2,80 | 21,5—24,0 | 0,45 | 0,18—0,26 | — | — |
S32205 | 2205 | 0,030 | 2,00 | 0,030 | 0,020 | 1,00 | 4,50—6,50 | 22,0—23,0 | 3,00—3,50 | 0,14—0,20 | — | — |
S32304 | 2304 | 0,030 | 2,50 | 0,040 | 0,040 | 1,00 | 3,00—5,50 | 21,5—24,5 | 0,05—0,60 | 0,05—0,20 | 0,05—0,60 | — |
S32506 | — | 0,030 | 1,00 | 0,040 | 0,015 | 0,90 | 5,50—7,20 | 24,0—26,0 | 3,00—3,50 | 0,08—0,20 | — | W 0,05—0,30 |
S32520 | — | 0,030 | 1,50 | 0,035 | 0,020 | 0,80 | 5,50—8,00 | 24,0—26,0 | 3,00—5,00 | 0,20—0,35 | 0,50—3,00 | — |
S32550 | 255 | 0,040 | 1,50 | 0,040 | 0,030 | 1,00 | 4,50—6,50 | 24,0—27,0 | 2,90—3,90 | 0,10—0,25 | 1,50—2,50 | — |
S32707 | — | 0,030 | 1,50 | 0,035 | 0,010 | 0,50 | 5,50—9,50 | 26,0—29,0 | 4,00—5,00 | 0,30—0,50 | 1,00 | Со 0,5—2,0 |
S32750 | 2507 | 0,030 | 1,20 | 0,035 | 0,020 | 0,80 | 6,00—8,00 | 24,0—26,0 | 3,00—5,00 | 0,24—0,32 | 0,50 | — |
S32760 | — | 0,030 | 1,00 | 0,030 | 0,010 | 1,00 | 6,00—8,00 | 24,0—26,0 | 3,00—4,00 | 0,20—0,30 | 0,50—1,00 | W 0,50—1,00 |
S32808 | — | 0,030 | 1,10 | 0,030 | 0,010 | 0,50 | 7,00—8,20 | 27,0—27,9 | 0,80—1,20 | 0,30—0,40 | — | W 2,10—2,50 |
S32900 | 329 | 0,080 | 1,00 | 0,040 | 0,030 | 0,75 | 2,50—5,00 | 23,0—28,0 | 1,00—2,00 | — | — | — |
S32906 | — | 0,030 | 0,80—1,50 | 0,030 | 0,030 | 0,80 | 5,80—7,50 | 28,0—30,0 | 1,50—2,60 | 0,30—0,40 | 0,80 | — |
S32950 | — | 0,030 | 2,00 | 0,035 | 0,010 | 0,60 | 3,50—5,20 | 26,0—29,0 | 1,00—2,50 | 0,15—0,35 | — | — |
S33207 | — | 0,030 | 1,50 | 0,035 | 0,010 | 0,80 | 6,00—9,00 | 29,0—33,0 | 3,00—5,0 | 0,40—0,60 | 1,00 | — |
S39274 | — | 0,030 | 1,00 | 0,030 | 0,020 | 0,80 | 6,00—8,00 | 24,0—26,0 | 2,50—3,50 | 0,24—0,32 | 0,20—0,80 | W 1,50—2,50 |
S39277 | — | 0,025 | 0,80 | 0,025 | 0,002 | 0,80 | 6,50—8,00 | 24,0—26,0 | 3,0—4,00 | 0,23—0,33 | 1,20—2,00 | W 0,80—1,20 |
S82011 | — | 0,030 | 2,00—3,00 | 0,040 | 0,020 | 1,00 | 1,00—2,00 | 20,5—23,5 | 0,10—1,00 | 0,15—0,27 | 0,50 | — |
Примечания 1 Для стали S32750 содержание хрома, молибдена и азота должно быть таким, чтобы выполнялось условие: % Сг + 3,3 • % Мо + 16 • % 2 Для стали S32760 содержание хрома, молибдена и азота должно быть таким, чтобы выполнялось условие: % Сг + 3,3 • % Мо + 16 • % 3 Знак «—» означает, что показатель не нормируют и не определяют. | N >41. N >40. |
ПНСТ 683—2023
5.5.2 Допустимые отклонения массовой доли элементов в химическом составе труб от значений, указанных в таблице 1, приведены в таблице 2.
Таблица 2 — Допустимые отклонения массовой доли элементов в химическом составе труб
Химический элемент | Верхняя предельная массовая доля элемента, % | Допустимые отклонения массовой доли элемента, % |
Углерод | В пределах норм таблицы 1 | +0,010 |
Марганец | До 1,00 включ., более 1,00 | +0,03 ±0,06 |
Фосфор | В пределах норм таблицы 1 | +0,005 |
Сера | До 0,02 включ., более 0,02 | +0,003 +0,005 |
Кремний | До 1,00 включ., более 1,00 | ±0,05 ±0,10 |
Хром | В пределах норм таблицы 1 | ±0,25 |
Никель | До 2,00 включ., более 2,00 до 5,00 включ., более 5,00 | ±0,05 ±0,07 ±0,10 |
Молибден | До 1,75 включ., более 1,75 | ±0,05 ±0,10 |
Медь | До 1,00 включ., более 1,00 | ±0,05 ±0,10 |
Азот | До 0,11 включ., более 0,11 | ±0,01 ±0,02 |
Примечание — Для элементов, массовая доля которых ограничена верхним пределом, применяют только плюсовые предельные отклонения. |
5.6 Термическая обработка
5.6.1 Трубы следует подвергать термической обработке в соответствии с параметрами, приведенными в таблице 3.
5.6.2 Для бесшовных горячедеформированных труб взамен термической обработки с отдельного нагрева, допускается закалка с деформационного нагрева при температуре конца деформации, не менее приведенной в таблице 3.
5.6.3 По согласованию заказчика и изготовителя трубы подвергают термической обработке, режим которой указывают в заказе.
Таблица 3 — Параметры термической обработки
Обозначение стали | Температура нагрева, °C | Способ охлаждения | |
UNS | AISI | ||
S31200 | — | От 1050 до 1100 | Закалка в воде (в т. ч. допускается охлаждение в спреере). По согласованию заказчика и изготовителя — закалка на воздухе с принудительным охлаждением аэраторами |
S31260 | — | От 1020 до 1100 | |
S31500 | — | От 980 до 1040 | |
S31803 | — | От 1020 до 1100 | |
S32003 | — | От 1010 до 1120 | |
S32101 | — | Не менее 1020 | |
S32202 | — | От 1020 до 1080 | |
S32205 | 2205 | От 1020 до 1100 | |
S32304 | 2304 | От 925 до 1050 | |
S32506 | — | От 1020 до 1120 | |
S32520 | — | От 1080 до 1120 | |
S32550 | 255 | Не менее 1040 |
Окончание таблицы 3
Обозначение стали | Температура нагрева, °C | Способ охлаждения | |
UNS | AISI | ||
S32707 | — | От 1080 до 1120 | Закалка в воде (в т. ч. допускается охлаждение в спреере). По согласованию заказчика и изготовителя — закалка на воздухе с принудительным охлаждением аэраторами |
S32750 | 2507 | От 1025 до 1125 | |
S32760 | — | От 1070 до 1140 | |
S32808 | — | От 1050 до 1150 | |
S32900 | 329 | От 925 до 955 | |
S32906 | — | От 1020 до 1150 | |
S32950 | — | От 990 до 1025 | |
S33207 | — | От 1040 до 1140 | |
S39274 | — | От 1025 до 1125 | |
S39277 | — | От 1080 до 1180 | |
S82011 | — | От 1010 до 1120 |
5.7 Механические свойства
5.7.1 Механические свойства при испытании на растяжение и твердость металла труб должны соответствовать значениям, приведенным в таблице 4.
Таблица 4 — Требования к механическим свойствам при испытании на растяжение и твердости
Обозначение стали | Номинальная толщина стенки | Временное сопротивление, не менее, Н/мм2 | Предел текучести, не менее, Н/мм2 | Относитель-ное удлинение, не менее, % | Твердость1), не более | ||
UNS | AISI | HBW | HRC | ||||
S31200 | — | Для всех толщин | 690 | 450 | 25 | 280 | — |
S31260 | — | Для всех толщин | 690 | 450 | 25 | 290 | 30 |
S31500 | — | Для всех толщин | 630 | 440 | 30 | 290 | 30 |
S31803 | — | Для всех толщин | 620 | 450 | 25 | 290 | 30 |
S32003 | — | Для всех толщин | 690 | 485 | 25 | 290 | 30 |
S32101 | — | До 5 мм включ. | 700 | 530 | 30 | 290 | — |
Более 5 мм | 650 | 450 | 30 | 290 | — | ||
S32202 | — | Для всех толщин | 650 | 450 | 30 | 290 | 30 |
S32205 | 2205 | Для всех толщин | 655 | 450 | 25 | 290 | 30 |
S32304 | 2304 | Для всех толщин | 60022) | 4002) | 25 | 2903) | — |
S32506 | — | Для всех толщин | 620 | 450 | 18 | 302 | 32 |
S32520 | — | Для всех толщин | 770 | 550 | 25 | 310 | — |
S32550 | 255 | Для всех толщин | 760 | 550 | 15 | 297 | 31 |
S32707 | — | Для всех толщин | 920 | 700 | 25 | 318 | 34 |
S32750 | 2507 | Для всех толщин | 800 | 550 | 15 | 300 | 32 |
S32760 | — | Для всех толщин | 750 | 550 | 25 | 310 | 32 |
S32808 | 329 | Для всех толщин | 800 | 550 | 15 | 310 | 32 |
S32900 | — | Для всех толщин | 620 | 485 | 20 | 271 | 28 |
S32906 | — | До 10 мм | 800 | 650 | 25 | 300 | 32 |
10 мм и более | 750 | 550 | 25 | 300 | 32 | ||
S32950 | — | Для всех толщин | 690 | 480 | 20 | 290 | 30 |
S33207 | — | До 4 мм | 950 | 770 | 15 | 336 | 36 |
4 мм и более | 850 | 700 | 15 | 336 | 36 |
Окончание таблицы 4
Обозначение стали | Номинальная толщина стенки | Временное сопротивление, не менее, Н/мм2 | Предел текучести, не менее, Н/мм2 | Относитель-ное удлинение, не менее, % | Твердость1), не более | ||
UNS | AISI | HBW | HRC | ||||
S39274 | — | Для всех толщин | 800 | 550 | 15 | 310 | 32 |
S39277 | — | Для всех толщин | 825 | 620 | 25 | 290 | 30 |
S82011 | — | До 5 мм включ. | 700 | 515 | 30 | 293 | 31 |
Более 5 мм | 655 | 450 | 30 | 293 | 31 | ||
1) Испытания проводят по одному из методов по выбору изготовителя. 2> Для труб наружным диаметром 25 мм и менее нормативное значение временного сопротивления — не менее 690 Н/мм2, предела текучести — не менее 450 Н/мм2. 3) Для труб наружным диаметром 25 мм и менее твердость не нормируют и не определяют. Примечание — Знак «—» означает, что показатель не нормируют и не определяют. |
5.7.2 По согласованию между изготовителем и заказчиком трубы могут быть изготовлены с другими требованиями к механическим свойствам.
5.8 Технологические испытания
5.8.1 Бесшовные трубы диаметром до 150 мм включительно с толщиной стенки не более 10 мм выдерживают испытание на раздачу до увеличения наружного диаметра на 10 % оправкой с углом конусности 30°; допускается применять оправки с углом конусности 6°и 12°.
5.8.2 Электросварные трубы диаметром не менее 25 мм и не более 102 мм выдерживают испытание на бортование с углом отбортовки 90° до получения ширины отгибаемого борта, измеренной от внутренней поверхности трубы, равной 1,5 толщины стенки.
5.8.3 Бесшовные и электросварные трубы наружным диаметром не более 400 мм и с толщиной стенки не более 15 % от наружного диаметра трубы выдерживают испытание на сплющивание до расстояния Н между сплющивающимися плоскостями в миллиметрах, вычисленного по формуле
где S — номинальная толщина стенки трубы, мм;
D — номинальный наружный диаметр трубы, мм.
5.9 Макро- и микроструктура
5.9.1 По согласованию заказчика и изготовителя может быть проведен контроль макроструктуры металла труб. Критерии приемки указывают в заказе (см. 5.2.2).
5.9.2 По согласованию заказчика и изготовителя может быть проведен контроль микроструктуры металла труб.
При проведении контроля микроструктуры определяют следующие параметры:
- содержание феррита;
- содержание карбидов, нитридов, неметаллических включений по границам зерен;
- наличие сигма-фазы;
- расстояние между аустенитными зернами;
- стойкость против межкристаллитной коррозии по ГОСТ 6032.
Нормативные значения параметров микроструктуры указывают в заказе.
5.10 Гидростатические испытания
Трубы должны выдерживать испытание внутренним гидростатическим давлением.
Изготовитель может гарантировать способность труб выдерживать испытательное гидростатическое давление без проведения испытаний.
5.11 Неразрушающий контроль
Трубы подвергают по выбору изготовителя вихретоковому или ультразвуковому контролю.
5.12 Предельные отклонения размеров, формы и длины
5.12.1 Отклонения наружного диаметра и толщины стенки труб не должны превышать предельных отклонений, установленных:
- для горячедеформированных труб в ГОСТ 9940;
- для холоднодеформированных труб в ГОСТ 9941;
- для сварных труб в ГОСТ 11068.
5.12.2 Предельные отклонения по внутреннему диаметру устанавливают по согласованию изготовителя с заказчиком.
5.12.3 Овальность труб не должна выводить наружный диаметр труб за допустимые значения.
5.12.4 Между изготовителем и заказчиком допускается согласование других требований к овальности.
5.12.5 Отклонение от прямолинейности труб на любом участке длиной 1 м должно быть:
-для труб номинальной толщиной стенки до 10 мм включительно — не более 1,5 мм;
- для труб номинальной толщиной стенки более 10 мм — не более 2 мм.
5.12.6 Между изготовителем и заказчиком допускается согласование других требований к отклонению труб от прямолинейности.
5.13 Отделка концов труб
5.13.1 Отделка концов труб соответствует ГОСТ 34094, тип ФБ.
5.13.2 На торцах труб не допускаются заусенцы. При удалении заусенцев на торцах труб допускается образование внутренней и наружной фасок.
5.14 Маркировка
5.14.1 На каждую трубу наружным диаметром 19,0 мм и более должна быть нанесена маркировка, содержащая:
- наименование или товарный знак изготовителя;
- обозначение настоящего предварительного стандарта;
- указание вида трубы (бесшовная «БТ» или сварная «СТ»);
- размер (наружный или внутренний диаметр и толщину стенки);
- мерную длину, если применимо;
- обозначение стали;
- номер плавки.
5.14.2 Маркировка труб наружным диаметром менее 19 мм может быть нанесена, по выбору изготовителя, на каждую трубу или на ярлык, прикрепляемый к пакету труб или ящику с трубами.
5.14.3 Остальные требования к маркировке труб должны соответствовать ГОСТ 10692.
5.15 Упаковка
Упаковка труб соответствует требованиям ГОСТ 10692.
6 Требования безопасности и охраны окружающей среды
Трубы пожаробезопасны, взрывобезопасны, электробезопасны, нетоксичны, не представляют радиационной опасности и не оказывают вреда окружающей среде и здоровью человека при хранении, транспортировании,эксплуатации и утилизации.
7 Правила приемки и методы испытаний
7.1 Правила приемки
7.1.1 Приемку труб осуществляют партиями. Партия состоит из труб одного вида, одной плавки, одного размера, термообработанных по одному режиму или в одной садке. Количество труб в партии должно быть не более 200 штук.
7.1.2 Для подтверждения соответствия требованиям настоящего предварительного стандарта партию труб подвергают приемочному контролю и проведению приемо-сдаточных испытаний.
Если между изготовителем и заказчиком не согласован другой объем приемо-сдаточных испытаний, то испытаниям подвергают:
- контролю химического состава — одну пробу от одной трубы из партии (для сварных труб допускается приемка по данным контроля металла листового/рулонного проката; для бесшовных труб допускается приемка по данным документа о качестве трубной заготовки или документа о приемочном контроле труб, используемых для изготовления труб по настоящему стандарту);
- испытаниям на растяжение — до 3 % труб из партии, но не менее трех труб;
- контролю твердости — по два образца от двух труб из партии;
- контролю качества поверхности (кроме контроля высоты внутреннего грата), размеров, формы, длины, отделки концов — каждую трубу;
- контроль высоты внутреннего грата — от двух труб из партии;
- контролю стойкости к межкристаллитной коррозии до 3 % труб из партии, но не менее четырех образцов с двух труб;
- гидростатическим испытаниям внутренним давлением — каждую трубу;
- неразрушающему контролю — каждую трубу;
- технологическим испытаниям по 5.8;
- контролю макро- и микроструктуры по 5.9.
7.1.3 Остальные правила приемки труб, в том числе, проведение повторных испытаний, соответствуют ГОСТ 10692, если между изготовителем и заказчиком не согласовано иное.
7.1.4 Допускается проведение повторной термической обработки партии с предъявлением ее к приемке, как новой партии.
7.1.5 На принятую партию труб оформляют документ о приемочном контроле по ГОСТ 31458—2015 (подразделы 3.1 или 3.2), содержащий, как минимум, следующее:
- товарный знак и/или наименование изготовителя;
- наименование заказчика;
- номер заказа;
- обозначение настоящего предварительного стандарта;
- вид труб (бесшовные горячедеформированные или холоднодеформированные, сварные);
- размер труб;
- обозначение стали;
- номер партии;
- количество труб;
- результаты контроля и испытаний;
- дату оформления документа.
7.2 Контроль химического состава
7.2.1 Пробы для химического анализа отбирают по ГОСТ 7565.
7.2.2 Химический состав стали определяют стандартными методами химического анализа, применяемыми для легированной стали.
Примечание — Химический состав легированной стали определяют методами химического анализа по стандартам группы «Стали легированные и высоколегированные».
Допускается применение других методов анализа, обеспечивающих необходимую точность определения химического состава.
При возникновении разногласий определение химического состава проводят стандартными методами химического анализа.
7.3 Испытания на растяжение
7.3.1 Образцы для испытаний на растяжение отбирают по ГОСТ 30432.
7.3.2 Испытания на растяжение проводят по ГОСТ 10006 на образцах в виде отрезков труб полного сечения, полосовых образцах или на продольных цилиндрических образцах наибольшего возможного диаметра.
7.4 Контроль твердости
Контроль твердости проводят в соответствии с ГОСТ 9012 или ГОСТ 9013.
7.5 Испытания на раздачу
Испытания на раздачу проводят по ГОСТ 8694.
7.6 Испытание на бортование
Испытание на бортование проводят по ГОСТ 8693.
7.7 Испытания на сплющивание
Испытания на сплющивание проводятся по ГОСТ 8695.
7.8 Контроль макроструктуры и микроструктуры
7.8.1 Контроль макроструктуры проводят по ГОСТ 10243 на протравленном кольцевом поперечном образце.
7.8.2 Контроль микроструктуры проводят по методикам, согласованным между заказчиком и изготовителем.
7.9 Метод контроля качества поверхности, размеров, формы, длины, отделки концов
7.9.1 Контроль размеров, формы, длины проводят универсальными средствами измерений, метрологические характеристики которых обеспечивают необходимую точность измерений. Прямой угол обрезки концов труб не контролируется и определяется конструкцией оборудования для разрезки труб.
7.9.2 Осмотр поверхности труб проводят визуально без применения увеличительных приспособлений. Внутреннюю поверхность контролируют по торцам на видимую длину.
7.9.3 Высоту внутреннего грата измеряют микрометром по ГОСТ 6507 или стенкомером по ГОСТ 11358. Измерение высоты внутреннего грата проводят на расстоянии до 25 мм от торцов труб.
7.10 Гидростатические испытания
Гидростатические испытания проводят в соответствии с ГОСТ 3845 при выдержке не менее 5 с и давлении, рассчитываемом по формуле
Р = 220,6 • t/D, (2)
где Р — испытательное давление, МПа;
t — минимальная, с учетом минусового допуска, толщина стенки, мм;
D — расчетный диаметр трубы, мм, равный:
- при поставке труб по наружному диаметру и толщине стенки — номинальному наружному диаметру, мм;
- при поставке труб по внутреннему диаметру и толщине стенки
D = Овн + 2t, где Овн — номинальный внутренний диаметр, мм.
7.11 Неразрушающий контроль
7.11.1 Ультразвуковой контроль труб проводят по ГОСТ ISO 10893-10, с уровнем приемки U3. Ультразвуковой контроль сварного шва проводят по ГОСТ Р ИСО 10893-11, с уровнем приемки U3.
7.11.2 Вихретоковый контроль проводится по ГОСТ Р ИСО 10893-2, с уровнем приемки ЕЗ.
7.11.3 Между изготовителем и заказчиком может быть согласован другой уровень приемки для ультразвукового или вихретокового методов контроля.
8 Транспортирование и хранение
Транспортирование и хранение труб осуществляют в соответствии с требованиями ГОСТ 10692.
Библиография
[1] ACTMG 48-11
Стандартные методы испытаний нержавеющей стали и родственных сплавов на
коррозионную стойкость с использованием растворов хлористого железа (Standard Test Methods for Pitting and Crevice Corrosion Resistance of Stainless Steels and Related Alloys by Use of Ferric Chloride Solution)
[2] АСТМ A789/A789M-17 Стандартная спецификация на бесшовные и сварные трубы из нержавеющей
ферритной/аустенитной стали для общего применения (Standard Specification for Seamless and Welded Ferritic/Austenitic Stainless Steel Tubing for General Service)
УДК 622.276.04:006.354
OKC 75.020
Ключевые слова: нефтяная и газовая промышленность; системы подводной добычи; коррозионностойкие стали; аустенито-ферритная сталь; трубы электросварные; трубы бесшовные
Редактор Е.Ю. Митрофанова Технический редактор И.Е. Черепкова Корректор М.В. Бучная Компьютерная верстка И.Ю. Литовкиной
Сдано в набор 20.02.2023. Подписано в печать 21.02.2023. Формат 60*8478. Гарнитура Ариал. Усл. печ. л. 1,86. Уч-изд. л. 1,68.
Подготовлено на основе электронной версии, предоставленной разработчиком стандарта
Создано в единичном исполнении в ФГБУ «Институт стандартизации» , 117418 Москва, Нахимовский пр-т, д. 31, к. 2.